Complete Safety Inspector Career Guide
Safety inspectors are the unsung guardians of workplaces, ensuring environments are free from hazards and compliant with critical regulations. They combine meticulous observation with a deep understanding of safety standards, preventing accidents and saving lives across diverse industries. This vital role offers a stable career path for those committed to protecting others and upholding rigorous safety protocols.
Key Facts & Statistics
Median Salary
$79,160 USD
(U.S. Bureau of Labor Statistics, May 2023)
Range: $50k - $120k+ USD (U.S. national range, varies by experience and industry)
Growth Outlook
5%
as fast as average (U.S. Bureau of Labor Statistics, 2022-2032)
Annual Openings
≈17,200
openings annually (U.S. Bureau of Labor Statistics, 2022-2032)
Top Industries
Typical Education
Bachelor's degree in occupational safety and health, engineering, or a related field; some positions may accept an associate's degree or significant relevant experience. Certifications like CSP (Certified Safety Professional) are highly valued.
What is a Safety Inspector?
A Safety Inspector is a specialized professional responsible for ensuring that workplaces comply with health and safety regulations and standards. They systematically identify potential hazards, assess risks, and recommend corrective actions to prevent accidents, injuries, and occupational illnesses. Their core purpose is to protect workers and the public by fostering a safe working environment and ensuring adherence to legal and ethical safety requirements.
This role differs significantly from a Safety Manager, who typically focuses on developing and overseeing an organization's overall safety program, policies, and culture. While a Safety Manager designs the framework, a Safety Inspector is on the front lines, auditing, investigating, and verifying that those policies and regulations are actually implemented and followed in practice. They act as the eyes and ears of safety, providing critical feedback and ensuring ongoing compliance.
What does a Safety Inspector do?
Key Responsibilities
- Conduct thorough on-site inspections of workplaces, machinery, and equipment to identify potential hazards and non-compliance with safety regulations.
- Prepare detailed inspection reports documenting findings, recommended corrective actions, and timelines for remediation.
- Investigate accidents and incidents to determine root causes, prevent recurrence, and ensure proper reporting to regulatory bodies.
- Provide safety training and education to employees and management on best practices, emergency procedures, and regulatory requirements.
- Collaborate with management and employees to develop and implement effective safety programs, policies, and procedures.
- Monitor the implementation of corrective actions and follow up on previous inspection findings to ensure compliance and hazard abatement.
- Stay current with changes in local, state, and federal safety regulations and industry standards to ensure ongoing compliance and best practices are maintained by the organization or client sites.
Work Environment
Safety Inspectors typically work in a dynamic environment, often splitting their time between office duties and extensive field work. Field work involves visiting various industrial sites, construction zones, manufacturing plants, or other workplaces, which may expose them to diverse conditions, including noise, dust, varying temperatures, and heights. They must wear appropriate personal protective equipment (PPE) during these visits.
Collaboration is central to the role, as they frequently interact with management, employees, union representatives, and sometimes regulatory officials. The pace of work can be variable, with routine inspections interspersed with urgent accident investigations or compliance deadlines. While some roles are primarily local, others may require significant travel to different company facilities or client sites. Remote work is generally not feasible for the inspection component of the job, although report writing and administrative tasks can often be done from a home office.
Tools & Technologies
Safety Inspectors regularly use a variety of tools and technologies to perform their duties. They rely on personal protective equipment (PPE) such as hard hats, safety glasses, and high-visibility vests for their own protection during site visits. For documentation and analysis, they use digital cameras, tablets, and laptops to record observations, take photos, and complete inspection checklists.
Software includes specialized safety management systems (SMS) for tracking incidents, managing permits, and scheduling inspections. They also utilize word processing and spreadsheet software like Microsoft Word and Excel for report generation and data analysis. Access to regulatory databases and online resources, such as OSHA (Occupational Safety and Health Administration) or MSHA (Mine Safety and Health Administration) guidelines, is crucial for research and compliance verification.
Safety Inspector Skills & Qualifications
Safety inspectors assess workplaces to ensure compliance with safety regulations and standards. Their qualifications are structured around a blend of formal education, practical experience, and specific certifications. Entry-level positions often require a bachelor's degree in occupational health and safety or a related field, while senior roles may demand a master's or extensive field experience.
Requirements vary significantly by industry sector. Construction safety inspectors need different specialized knowledge than those in manufacturing, healthcare, or oil and gas. Company size also influences needs; larger corporations often have more structured training programs and may prioritize specific certifications, whereas smaller businesses might value broader experience. Geographic location also plays a role, as local and national regulations dictate necessary certifications and knowledge.
While formal education provides foundational knowledge, practical experience and industry-specific certifications are often equally, if not more, critical for career advancement. Certifications like CSP (Certified Safety Professional) or OHST (Occupational Health and Safety Technologist) demonstrate specialized expertise and commitment. The field is evolving with new technologies like drones for inspections and data analytics for hazard identification, making continuous learning essential for maintaining relevance and effectiveness.
Education Requirements
Technical Skills
- OSHA Regulations and Standards (29 CFR 1910 General Industry, 29 CFR 1926 Construction): Deep understanding and practical application of federal safety laws.
- Hazard Identification and Risk Assessment: Ability to systematically identify, analyze, and evaluate workplace hazards and associated risks.
- Incident Investigation and Root Cause Analysis: Proficiency in methodologies like TapRooT, Fishbone Diagram, or Five Whys to determine underlying causes of accidents.
- Safety Management Systems (e.g., ISO 45001, ANSI Z10): Knowledge of implementing, auditing, and maintaining structured safety programs.
- Personal Protective Equipment (PPE) Selection and Use: Expertise in assessing PPE needs, ensuring proper selection, fit, and training.
- Ergonomics Principles: Understanding how to design workplaces to minimize musculoskeletal injuries and improve worker comfort and efficiency.
- Environmental Regulations (e.g., EPA, RCRA): Basic knowledge of environmental compliance related to waste management, air quality, and hazardous materials.
- Fire Safety and Emergency Preparedness: Competence in developing and implementing fire prevention plans, emergency response procedures, and evacuation drills.
- Industrial Hygiene Principles: Familiarity with recognizing, evaluating, and controlling environmental factors or stresses arising in the workplace.
- Data Analysis and Reporting Software (e.g., Microsoft Excel, EHS software): Ability to collect, analyze, and present safety data to identify trends and inform decision-making.
- Auditing and Inspection Techniques: Skill in conducting systematic safety audits, site inspections, and compliance checks.
- Training and Presentation Delivery: Capability to develop and deliver effective safety training programs to various audiences.
Soft Skills
- Observation and Attention to Detail: Critical for identifying subtle hazards, non-compliant conditions, and potential risks that others might overlook during inspections.
- Communication and Interpersonal Skills: Essential for explaining complex regulations, providing clear instructions, and interacting effectively with diverse personnel, from frontline workers to management.
- Problem-Solving and Analytical Thinking: Necessary for evaluating root causes of incidents, developing effective corrective actions, and proposing practical solutions to safety challenges.
- Integrity and Objectivity: Crucial for maintaining impartiality during investigations and inspections, ensuring fair and consistent application of safety standards without bias.
- Conflict Resolution and Persuasion: Important for addressing resistance to safety changes, mediating disagreements, and convincing others to adopt safer practices.
- Adaptability and Resilience: Required to respond to unforeseen hazards, changing regulations, and stressful situations such as accident investigations or emergency responses.
- Documentation and Report Writing: Vital for creating clear, concise, and legally defensible inspection reports, incident analyses, and compliance records.
How to Become a Safety Inspector
Entering the Safety Inspector field offers diverse pathways, ranging from traditional academic routes to vocational training and direct industry experience. A common misconception is that all safety roles require an engineering degree; however, many entry-level positions prioritize practical experience, certifications, and a strong understanding of regulatory compliance. The timeline for entry varies significantly: someone with a related associate's degree or extensive trade experience might secure a role within 6-12 months, while a complete beginner pursuing a bachelor's degree could take 2-4 years.
Geographic location and industry sector heavily influence job availability and specific requirements. Major industrial hubs, construction-heavy regions, and sectors like manufacturing or energy often have a higher demand for Safety Inspectors. Smaller companies may value generalists with broad safety knowledge, while larger corporations or government agencies might seek specialists with certifications in specific areas like OSHA or environmental safety. Networking with professionals in relevant industries and joining safety organizations can provide invaluable insights and open doors to opportunities not publicly advertised.
The hiring landscape increasingly values demonstrable knowledge of regulations, risk assessment skills, and the ability to communicate effectively. While degrees are beneficial, a strong portfolio of practical experience gained through internships, volunteer work, or even safety committee involvement within a current role can be equally compelling. Overcoming barriers to entry often involves prioritizing relevant certifications and gaining hands-on experience, even if initially in a related role, to build a credible foundation for a dedicated Safety Inspector position.
Step 1
Step 2
Step 3
Step 4
Step 5
Step 6
Education & Training Needed to Become a Safety Inspector
Becoming a Safety Inspector involves a blend of formal education and practical experience, with diverse pathways available. Formal degree programs, such as associate's or bachelor's degrees in occupational health and safety, environmental health, or industrial hygiene, typically take 2-4 years and can cost between $20,000 and $100,000+. These programs provide a strong theoretical foundation in regulations, hazard recognition, and risk management. Many employers, especially in government and large corporations, prefer candidates with such degrees, as they demonstrate a comprehensive understanding of the field.
Alternative learning paths, like professional certifications and specialized training courses, offer a more focused and often quicker route into the profession. Certifications from organizations like the Board of Certified Safety Professionals (BCSP) or the National Association of Safety Professionals (NASP) are highly regarded. These programs can range from intensive 1-week courses to self-paced online modules taking several months, with costs typically between $1,500 and $5,000, excluding exam fees. While these options may not carry the same academic weight as a degree, they are crucial for demonstrating specific competencies and are often required even for degree-holders.
The market perception of credentials varies; while a degree offers broad foundational knowledge, certifications prove specialized expertise. Continuous learning is vital for Safety Inspectors due to evolving regulations and technologies. Many roles also require practical experience, often gained through entry-level safety technician positions or internships. Employers seek candidates who combine theoretical knowledge with hands-on problem-solving abilities. The most effective educational investment often combines a relevant degree with industry-recognized certifications, ensuring both a strong knowledge base and practical skills for career advancement.
Safety Inspector Salary & Outlook
Compensation for a Safety Inspector involves numerous variables beyond base salary. Geographic location significantly impacts earnings; major industrial hubs and areas with stringent regulatory environments typically offer higher salaries due to increased demand and cost of living. For instance, inspectors in California or New York generally earn more than those in less populated states, though this can be offset by a higher cost of living in those areas. International markets also show considerable variation, with the provided figures reflecting typical U.S. dollar contexts.
Years of experience, specialized certifications (e.g., OSHA, CSP, CIH), and the specific industry of inspection (e.g., construction, manufacturing, oil and gas, healthcare) create substantial salary differences. A Safety Inspector with expertise in complex hazardous materials or advanced machinery can command premium compensation. Total compensation packages often include performance bonuses, health insurance, retirement contributions like 401(k) matching, and allowances for professional development or equipment. Some roles, particularly in high-risk sectors, may offer hazard pay or additional benefits.
Salary growth in this field is driven by regulatory changes, increased corporate focus on compliance, and a strong safety record. Inspectors who can demonstrate a direct impact on reducing incidents or improving efficiency gain significant negotiation leverage. Remote work is less common for this role due to the hands-on nature of inspections, but some administrative or consulting roles might offer flexibility, potentially influencing geographic arbitrage for certain tasks.
Salary by Experience Level
Level | US Median | US Average |
---|---|---|
Junior Safety Inspector | $52k USD | $55k USD |
Safety Inspector | $68k USD | $70k USD |
Senior Safety Inspector | $82k USD | $85k USD |
Lead Safety Inspector | $97k USD | $100k USD |
Safety Manager | $110k USD | $115k USD |
Director of Safety | $135k USD | $140k USD |
Market Commentary
The job market for Safety Inspectors shows steady growth, driven by increasing regulatory scrutiny and a heightened corporate emphasis on workplace safety across various sectors. The U.S. Bureau of Labor Statistics projects a stable demand for Occupational Health and Safety Specialists, which includes Safety Inspectors, with a growth outlook of about 5% over the next decade. This growth is consistent with the average for all occupations, indicating a reliable career path.
Emerging opportunities for Safety Inspectors include specialized areas such as cybersecurity in industrial control systems, environmental compliance for green energy projects, and advanced safety protocols for automation and robotics in manufacturing. The ongoing digital transformation requires inspectors to understand new technologies and their associated safety risks. There is a consistent demand for qualified professionals, often outpacing the supply of highly specialized candidates, particularly in industries with complex safety requirements like construction and utilities.
Future-proofing considerations for Safety Inspectors involve continuous learning in areas like data analytics for predictive safety, drone technology for remote site inspections, and AI for risk assessment. While automation can streamline some data collection, the critical judgment and on-site verification performed by human inspectors remain indispensable. This profession is relatively recession-resistant as safety compliance is a non-negotiable aspect of business operations, often mandated by law, ensuring consistent demand regardless of economic cycles. Geographic hotspots for employment include major industrial zones, port cities, and areas with significant infrastructure development.
Safety Inspector Career Path
Career progression for a Safety Inspector involves a clear path from hands-on inspection to strategic leadership. Professionals typically begin by mastering technical inspection protocols and regulatory compliance. Advancement often means taking on more complex sites, specialized areas, or leading teams. The field offers both individual contributor (IC) tracks, focusing on deep technical expertise, and management tracks, which involve overseeing teams and developing safety programs.
Advancement speed depends on several factors, including performance, the specific industry (e.g., construction, manufacturing, oil & gas), and company size. Larger organizations or those with higher regulatory scrutiny often present more structured advancement opportunities. Specialization in areas like confined space entry, fall protection, or hazardous materials also accelerates progression. Lateral moves might include transitioning between different industries or moving into related roles like quality assurance or environmental compliance. Continuous learning, staying updated on regulations, and obtaining relevant certifications are crucial for sustained growth.
Networking within industry associations and seeking mentorship from experienced safety professionals significantly aids career development. Building a reputation for thoroughness and effective communication opens doors to leadership roles. Common career pivots include moving into safety training, risk management, or occupational health. Professionals often reach significant milestones by leading major safety audits, implementing company-wide safety initiatives, or achieving certifications like CSP (Certified Safety Professional).
Junior Safety Inspector
0-2 yearsKey Focus Areas
Safety Inspector
2-5 yearsKey Focus Areas
Senior Safety Inspector
5-8 yearsKey Focus Areas
Lead Safety Inspector
8-12 yearsKey Focus Areas
Safety Manager
12-18 yearsKey Focus Areas
Director of Safety
18+ yearsKey Focus Areas
Junior Safety Inspector
0-2 yearsConduct routine safety inspections under direct supervision, primarily focusing on identifying basic hazards and ensuring compliance with established protocols. Assist senior inspectors in data collection and report preparation. Learn to interpret safety checklists and operational procedures for straightforward tasks. Impact is localized to specific work areas or simple projects.
Key Focus Areas
Develop foundational knowledge of OSHA regulations and specific industry safety standards. Focus on mastering inspection techniques, hazard identification, and basic risk assessment. Gain proficiency in documenting findings and preparing preliminary reports. Build strong communication skills for interacting with site personnel.
Safety Inspector
2-5 yearsPerform independent safety inspections across various operational areas, identifying complex hazards and ensuring compliance. Lead initial incident investigations and contribute to the development of corrective action plans. Provide basic safety training to employees. Impact extends to departmental or project-level safety outcomes, working with moderate autonomy.
Key Focus Areas
Deepen expertise in specific safety regulations and industry best practices. Enhance skills in detailed risk assessment, accident investigation, and root cause analysis. Develop the ability to recommend effective corrective actions. Strengthen communication and interpersonal skills for conducting safety briefings and addressing non-compliance.
Senior Safety Inspector
5-8 yearsLead complex safety audits and investigations, often involving multiple departments or high-risk operations. Develop and implement specific safety programs and procedures. Mentor and provide technical guidance to junior inspectors. Act as a subject matter expert on specific safety topics, influencing departmental safety policies. Decisions impact entire sites or major projects.
Key Focus Areas
Master advanced safety management systems and program development. Cultivate strong analytical skills for trend analysis and predictive safety. Develop leadership capabilities, including mentoring junior staff and leading safety committees. Pursue advanced certifications like CSP or industry-specific specializations.
Lead Safety Inspector
8-12 yearsOversee a team of safety inspectors, assigning tasks, providing guidance, and reviewing their work. Lead the implementation of significant safety initiatives and continuous improvement projects. Act as a primary point of contact for regulatory agencies during inspections. Responsible for ensuring consistent application of safety standards across multiple sites or large projects. Decisions have a broad impact on operational safety and compliance.
Key Focus Areas
Focus on strategic planning for safety initiatives and cross-functional collaboration. Develop strong project management and team leadership skills. Enhance communication and presentation abilities for influencing senior management and external stakeholders. Cultivate a proactive approach to safety culture development.
Safety Manager
12-18 yearsManage the overall safety program for a specific division or business unit. Develop and implement safety policies, procedures, and training programs. Oversee the safety department budget and resource allocation. Responsible for regulatory compliance and all incident reporting. Lead the safety team, including hiring, performance management, and professional development. Decisions impact the safety performance and culture of an entire operational area.
Key Focus Areas
Develop comprehensive safety management systems and strategic planning skills. Focus on budget management, resource allocation, and talent development within the safety department. Cultivate strong negotiation and conflict resolution skills for managing complex safety challenges. Enhance executive communication and presentation abilities.
Director of Safety
18+ yearsProvide executive leadership and strategic direction for all safety functions across the entire organization. Establish long-term safety goals, policies, and performance metrics. Responsible for overall regulatory compliance, risk management, and the cultivation of a robust safety culture. Manages a team of safety managers and senior professionals, influencing all levels of the organization. Decisions have a company-wide, strategic impact on safety, reputation, and financial outcomes.
Key Focus Areas
Focus on enterprise-level safety strategy, risk governance, and organizational culture transformation. Develop exceptional leadership, vision-setting, and change management skills. Cultivate strong financial acumen and the ability to integrate safety objectives with overall business strategy. Engage in industry thought leadership and advocacy.
Job Application Toolkit
Ace your application with our purpose-built resources:
Safety Inspector Cover Letter Examples
Personalizable templates that showcase your impact.
View examplesSafety Inspector Job Description Template
Ready-to-use JD for recruiters and hiring teams.
View examplesGlobal Safety Inspector Opportunities
Safety Inspectors ensure compliance with safety regulations across diverse industries globally. This role translates well internationally, with consistent demand for workplace safety expertise in manufacturing, construction, and energy sectors. Cultural norms and specific national legislation significantly influence inspection protocols. Professionals seek international roles for career advancement, exposure to varied industrial practices, and improved compensation. Relevant international certifications, like NEBOSH or OSHA, enhance global mobility.
Global Salaries
Salaries for Safety Inspectors vary significantly by region, reflecting economic conditions and industry demand. In North America, particularly the United States, annual salaries range from $60,000 to $95,000 USD, with higher figures in high-hazard industries like oil and gas. Canadian salaries are comparable, typically $55,000 to $85,000 CAD.
European markets offer competitive compensation. In Germany, a Safety Inspector can expect €50,000 to €75,000 EUR (approximately $54,000 - $81,000 USD), while the UK offers £40,000 to £60,000 GBP (approximately $50,000 - $75,000 USD). These figures often include comprehensive benefits, robust healthcare, and generous vacation time, which can offset slightly lower base salaries compared to the US.
Asia-Pacific regions, such as Australia and Singapore, provide strong earning potential, with salaries ranging from AUD 70,000 to AUD 100,000 (approximately $46,000 - $66,000 USD) and SGD 60,000 to SGD 90,000 (approximately $44,000 - $66,000 USD) respectively. In contrast, Latin American countries like Brazil might offer BRL 80,000 to BRL 120,000 (approximately $16,000 - $24,000 USD), where the lower cost of living provides similar purchasing power.
Salary structures also differ; some countries emphasize base pay, while others include performance bonuses or extensive social security contributions. Tax implications and take-home pay vary widely, with higher tax rates in some European nations compared to lower rates in parts of the Middle East. International certifications and specialized industry experience often lead to higher compensation across all regions.
Remote Work
International remote work for Safety Inspectors is highly limited due to the inherent on-site nature of the role. Physical presence is typically required for inspections, audits, and direct observation of safety protocols. However, some administrative tasks, report writing, policy development, and training roles might be performed remotely.
Digital nomad opportunities are rare for core inspection duties. Companies might offer remote work for global safety management positions that focus on compliance strategy, rather than direct site inspections. Legal and tax implications for the limited remote work available would follow standard international remote work guidelines, requiring careful consideration of tax residency and employer-employee regulations.
Salaries for such limited remote roles may be adjusted based on the inspector's location and the company's global compensation policy. Equipment needs generally include reliable internet and communication tools, but specialized safety equipment is always site-specific. Platforms for international remote safety roles are less common, as most opportunities remain location-bound.
Visa & Immigration
Safety Inspectors seeking international roles typically pursue skilled worker visas. Popular destinations include Canada, Australia, the UK, Germany, and the UAE, all recognizing the profession's importance. Requirements often include a relevant degree or diploma, several years of experience, and sometimes specific certifications like NEBOSH or OSHA. Credential recognition for education is crucial, often requiring evaluation by designated authorities.
Visa application timelines vary, from a few months in countries like Canada to longer periods for complex cases. Many countries have points-based immigration systems where age, education, experience, and language proficiency contribute to eligibility. English language tests (IELTS, PTE) are often mandatory for English-speaking countries.
Intra-company transfers can be an option if an inspector works for a multinational corporation. Some countries offer fast-track programs for in-demand professions, though specific advantages for Safety Inspectors vary by nation. Pathways to permanent residency often exist after several years of skilled employment. Family visas for dependents are usually available once the primary applicant secures their work permit.
2025 Market Reality for Safety Inspectors
Understanding current market conditions is vital for safety inspectors to navigate evolving career landscapes. The field has seen significant shifts from 2023 to 2025, influenced by post-pandemic regulatory changes and the increasing integration of AI in risk assessment.
Broader economic factors, such as industrial growth or contraction, directly impact demand for safety professionals. Market realities for safety inspectors vary considerably by experience level, with senior roles often more secure, and by geographic region, as local industry dictates need. This analysis provides an honest assessment of current hiring realities.
Current Challenges
Safety inspectors face increased competition for fewer entry-level positions, especially in saturated urban areas. Economic slowdowns sometimes lead companies to defer non-critical compliance hires, affecting job availability. Adapting to new technologies and complex regulatory changes also demands continuous learning and upskkilling.
Growth Opportunities
Despite challenges, strong demand persists for safety inspectors specializing in emerging technologies like renewable energy infrastructure or advanced manufacturing. Roles focused on cybersecurity within operational technology environments also present growing opportunities.
Professionals can gain an advantage by acquiring certifications in specific high-risk areas, such as confined space entry or hazardous material handling. Underserved markets, particularly in rapidly industrializing rural regions, offer better opportunities than urban centers. Strong analytical skills and proficiency in data-driven risk assessment provide a competitive edge.
Market adjustments may create openings for inspectors with a deep understanding of evolving regulatory frameworks or those who can integrate AI tools into their inspection protocols. Sectors like healthcare, logistics, and specialized engineering firms continue to show robust demand for dedicated safety oversight. Investing in continuous professional development and niche certifications positions inspectors for long-term career resilience.
Current Market Trends
Hiring for safety inspectors shows steady demand in highly regulated sectors like manufacturing, construction, and energy as of 2025. Companies prioritize risk mitigation and compliance, driving consistent need for these roles. However, the market for less specialized roles faces some saturation.
Economic conditions influence hiring, with a slight slowdown in new construction projects impacting some inspector roles. Despite this, the emphasis on worker safety and environmental protection remains strong, buoyed by regulatory enforcement. Technological advancements, particularly in remote monitoring and AI-powered data analysis, are reshaping the inspector's toolkit. Employers increasingly seek candidates proficient with digital inspection platforms and data analytics tools.
Salary trends for experienced safety inspectors remain stable, reflecting specialized knowledge and certification requirements. Entry-level salaries face more pressure due to increased candidate pools and automation. Geographic variations are significant; high-growth industrial regions often have more openings than areas with declining traditional industries. Remote work is less common for this hands-on role, though some administrative or planning aspects may be done remotely.
Emerging Specializations
The field of safety inspection is undergoing significant transformation, driven by rapid technological advancements and evolving regulatory landscapes. New specialization opportunities are continuously emerging, pushing the boundaries of traditional inspection methods. Understanding these future-oriented career paths is crucial for safety inspectors aiming to position themselves for success in 2025 and beyond.
Early positioning in these emerging areas often leads to premium compensation and accelerated career growth. As industries adopt new technologies and processes, the demand for specialized safety expertise increases, creating valuable niches. While established specializations remain vital, focusing on cutting-edge areas can unlock unparalleled opportunities for professional development and influence.
Many emerging areas, particularly those involving advanced technology, are still in their formative stages but are rapidly gaining traction. They are expected to become mainstream and create significant job opportunities within the next three to five years. Specializing in these cutting-edge fields involves a balance of risk and reward; it requires proactive learning and adaptability, but the potential for leadership and high demand is substantial.
Strategic choices about specialization allow safety inspectors to become indispensable assets in an increasingly complex industrial environment. Focusing on these new frontiers ensures relevance and opens doors to innovative projects and leadership roles. This forward-thinking approach secures a strong competitive advantage in the evolving job market.
Autonomous Systems Safety Inspector
This specialization focuses on inspecting and ensuring the safety of autonomous systems, including self-driving vehicles, drones, and robotic manufacturing lines. It involves assessing software reliability, sensor accuracy, and fail-safe mechanisms, which are critical for preventing accidents in highly automated environments. The complexity of these systems requires a deep understanding of AI ethics, operational design domains, and human-machine interaction.
Hydrogen Energy Safety Inspector
This area involves inspecting and certifying the safety of hydrogen production, storage, and distribution facilities, as well as hydrogen-powered vehicles and industrial equipment. As hydrogen energy gains prominence as a clean fuel source, ensuring its safe handling and infrastructure integrity becomes paramount. Inspectors in this field must understand the unique chemical properties of hydrogen, pressure systems, and specific fire safety protocols.
Advanced Manufacturing Safety Inspector
This specialization focuses on the safety of additive manufacturing processes, commonly known as 3D printing, especially in industrial applications using hazardous materials or producing critical components. It involves inspecting equipment, material handling, ventilation systems, and post-processing safety measures to prevent exposure to fumes, dust, or other byproducts. Ensuring compliance with evolving standards for new manufacturing techniques is key.
Immersive Technology Safety Inspector
This emerging field addresses safety concerns related to virtual reality (VR), augmented reality (AR), and mixed reality (MR) technologies, particularly in industrial training, simulation, and remote assistance applications. Safety inspectors in this area assess ergonomic risks, cybersickness, data privacy implications, and the potential for real-world hazards during immersive experiences. They ensure that these technologies enhance safety without introducing new risks.
Battery Energy Storage Safety Inspector
This specialization involves inspecting and verifying the safety protocols and infrastructure for large-scale battery energy storage systems (BESS), critical for renewable energy grids and electric vehicle charging stations. It includes assessing fire suppression systems, thermal management, electrical hazards, and environmental impact. Given the rapid expansion of renewable energy, ensuring the safe operation of these powerful storage units is vital.
Pros & Cons of Being a Safety Inspector
Making informed career decisions requires a thorough understanding of both the benefits and challenges associated with a profession. The experience of a safety inspector, like any other role, varies significantly based on the industry, company culture, specific specialization (e.g., construction, manufacturing, environmental), and individual personality. What one person considers an advantage, another might see as a challenge. Furthermore, the emphasis on certain pros and cons can shift at different career stages, from an entry-level position to a senior supervisory role. This assessment aims to provide an honest, balanced perspective to help individuals set realistic expectations before committing to a career as a safety inspector.
Pros
- Safety inspectors play a crucial role in preventing accidents, protecting lives, and ensuring workplace well-being, offering a strong sense of purpose and job satisfaction.
- There is consistent demand for safety professionals across various industries, including construction, manufacturing, healthcare, and government, leading to good job security and diverse employment opportunities.
- The role provides opportunities for continuous learning and skill development, as inspectors must master new regulations, technologies, and best practices in safety management.
- Safety inspectors often work independently on site visits and investigations, allowing for a degree of autonomy and the ability to manage their own schedules effectively.
- The profession offers competitive salaries and benefits, especially for experienced and certified inspectors, reflecting the critical nature of their responsibilities.
- Safety inspectors gain broad exposure to different industries and operational processes, providing a unique perspective on how various businesses function and manage risk.
- The work often involves a mix of field visits, office work, and stakeholder engagement, providing variety and preventing the monotony of a purely desk-bound job.
Cons
- Safety inspectors often face high-pressure situations, especially when investigating serious incidents or enforcing compliance with strict deadlines, which can lead to significant stress.
- The job frequently involves extensive travel to various sites, including remote or hazardous locations, requiring time away from home and potentially irregular working hours.
- Safety inspectors may encounter resistance or hostility from individuals or organizations during inspections, particularly when identifying non-compliance or recommending costly changes.
- The role demands continuous education and staying updated on evolving regulations, standards, and technologies, requiring ongoing professional development and training.
- Legal liabilities and potential for litigation exist if an inspector's findings or recommendations are later deemed insufficient or incorrect, placing a heavy responsibility on the individual.
- Some work environments can be physically demanding, requiring prolonged standing, walking, climbing, and exposure to adverse weather conditions or industrial hazards.
- The work can become repetitive, involving adherence to checklists and standardized procedures across numerous inspections, which may not appeal to those seeking highly creative or dynamic roles.
Frequently Asked Questions
Safety Inspectors face distinct challenges in ensuring compliance and mitigating risks across diverse environments. This section addresses the most pressing questions about transitioning into this role, from necessary certifications and physical demands to career progression and work-life balance in a field focused on preventing harm.
What are the essential educational and certification requirements to become a Safety Inspector?
Becoming a Safety Inspector typically requires a high school diploma or GED, though many employers prefer an associate's or bachelor's degree in occupational health and safety, engineering, or a related technical field. Crucially, you will need specific certifications like OSHA 30-Hour or industry-specific credentials, depending on the sector. Experience in a safety-related role or the industry you wish to inspect also significantly enhances your qualifications.
How long does it typically take to become a qualified Safety Inspector if I'm starting from scratch?
The timeline to become job-ready as a Safety Inspector varies. If you are starting with a relevant degree, you might need 6-12 months to gain specific certifications and entry-level experience. For those without a degree, it could take 2-4 years to complete an associate's program and acquire the necessary certifications and practical experience. Networking and hands-on experience through internships or entry-level safety roles significantly accelerate this process.
What are the realistic salary expectations for a Safety Inspector, both entry-level and experienced?
Entry-level Safety Inspectors can expect a starting salary ranging from $45,000 to $60,000 annually, depending on location, industry, and specific qualifications. With experience and specialized certifications, salaries can increase significantly, with experienced inspectors earning $70,000 to $90,000 or more. Factors like working in high-risk industries or for federal agencies often lead to higher compensation.
What is the typical work-life balance like for a Safety Inspector, considering travel and hours?
The work-life balance for a Safety Inspector can vary. Many roles offer standard 9-5 hours, but some positions, especially in construction or manufacturing, may require early mornings, evenings, or occasional weekend work to accommodate operational schedules. Travel is often a significant component, requiring visits to various sites, which impacts personal time. Emergency response situations, though infrequent, can also demand immediate attention outside regular hours.
Is the Safety Inspector role a secure career path with good job stability?
Job security for Safety Inspectors is generally strong and stable. Safety regulations are continuously evolving and becoming stricter across all industries, creating a consistent demand for qualified professionals. Economic downturns may impact specific industries, but the fundamental need for compliance and risk management ensures ongoing opportunities. Specializing in high-demand areas like construction, energy, or environmental safety can further enhance job security.
What are the common career advancement opportunities for a Safety Inspector?
Career growth for Safety Inspectors often involves advancing to senior inspector roles, becoming a safety manager, or specializing in areas like environmental health and safety (EHS), industrial hygiene, or risk management. Many move into consulting, working for private firms that advise companies on safety compliance. Further education, such as a master's degree in occupational safety, and advanced certifications like CSP (Certified Safety Professional) open doors to leadership and executive positions.
What are the biggest challenges or frustrations specific to being a Safety Inspector?
A significant challenge is dealing with resistance from individuals or companies who view safety regulations as burdensome. Inspectors must possess strong communication and negotiation skills to enforce standards effectively without alienating stakeholders. The role also requires meticulous attention to detail, strong analytical abilities to identify hazards, and the capacity to stay updated on complex and frequently changing regulations across multiple industries.
Can Safety Inspectors work remotely, or is it primarily an on-site role?
Remote work is generally not common for Safety Inspectors, as the core function involves on-site inspections and direct observation of workplaces and processes. While some administrative tasks or report writing can be done remotely, the hands-on nature of the job necessitates physical presence. However, some senior roles, consulting positions, or roles focused on policy development might offer more flexibility or a hybrid work model.
Related Careers
Explore similar roles that might align with your interests and skills:
Safety Officer
A growing field with similar skill requirements and career progression opportunities.
Explore career guideSafety Professional
A growing field with similar skill requirements and career progression opportunities.
Explore career guideSafety Supervisor
A growing field with similar skill requirements and career progression opportunities.
Explore career guideHealth and Safety Inspector
A growing field with similar skill requirements and career progression opportunities.
Explore career guideOccupational Safety and Health Inspector
A growing field with similar skill requirements and career progression opportunities.
Explore career guideAssess your Safety Inspector readiness
Understanding where you stand today is the first step toward your career goals. Our Career Coach helps identify skill gaps and create personalized plans.
Skills Gap Analysis
Get a detailed assessment of your current skills versus Safety Inspector requirements. Our AI Career Coach identifies specific areas for improvement with personalized recommendations.
See your skills gapCareer Readiness Assessment
Evaluate your overall readiness for Safety Inspector roles with our AI Career Coach. Receive personalized recommendations for education, projects, and experience to boost your competitiveness.
Assess your readinessSimple pricing, powerful features
Upgrade to Himalayas Plus and turbocharge your job search.
Himalayas
Himalayas Plus
Himalayas Max
Find your dream job
Sign up now and join over 100,000 remote workers who receive personalized job alerts, curated job matches, and more for free!
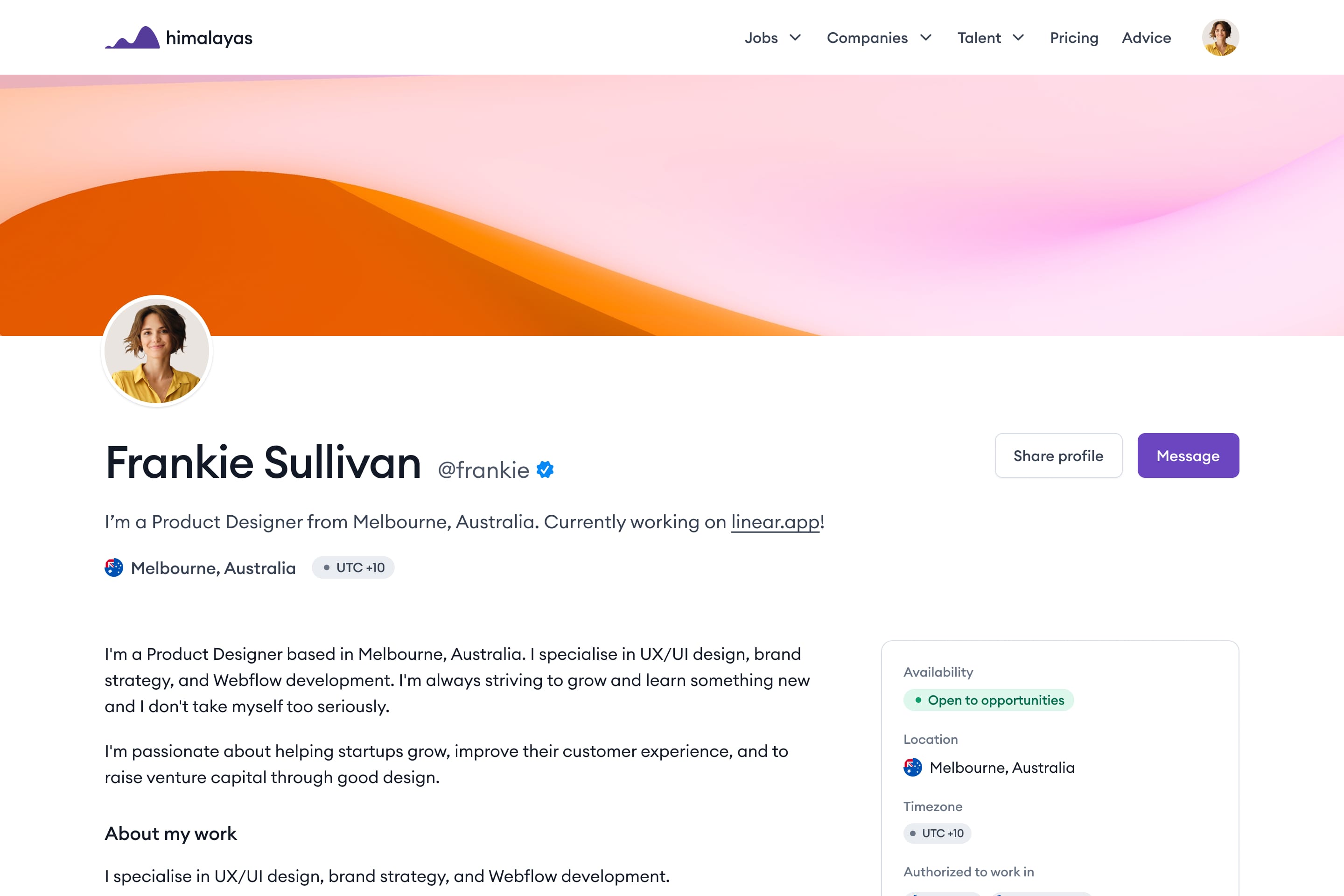