Complete Supply Coordinator Career Guide
A Supply Coordinator ensures a seamless flow of materials and resources, acting as the critical link between procurement, inventory, and operations. This role optimizes supply chains, prevents disruptions, and directly impacts a company's efficiency and profitability by ensuring everything needed is available precisely when required.
You will play a vital role in managing logistics, reducing costs, and supporting production or service delivery, making it a pivotal entry point into the dynamic world of supply chain management.
Key Facts & Statistics
Median Salary
$54,340 USD
(U.S. national median, BLS May 2023)
Range: $35k - $75k+ USD, depending on experience, industry, and location. Senior roles can exceed this.
Growth Outlook
4%
as fast as average (BLS 2022-2032)
Annual Openings
≈48,700
openings annually (BLS 2022-2032)
Top Industries
Typical Education
High school diploma or equivalent, though an associate's or bachelor's degree in supply chain management, logistics, or business is increasingly preferred for advancement.
What is a Supply Coordinator?
A Supply Coordinator is a pivotal professional responsible for the efficient flow of goods, materials, and services within an organization's supply chain. They manage the day-to-day operational aspects of procurement, inventory management, and logistics, ensuring that necessary resources are available when and where they are needed to support business operations.
This role differs from a 'Purchasing Agent' who focuses primarily on sourcing and negotiating contracts, or a 'Logistics Manager' who oversees broader transportation and warehousing strategies. The Supply Coordinator acts as the hands-on implementer, bridging the gap between strategic planning and execution, and ensuring the smooth, continuous operation of the supply pipeline.
What does a Supply Coordinator do?
Key Responsibilities
- Process purchase orders and requisitions for materials, equipment, and services, ensuring compliance with procurement policies and budget constraints.
- Monitor inventory levels and track incoming and outgoing shipments to prevent stockouts and minimize excess inventory holding costs.
- Communicate regularly with suppliers to confirm delivery schedules, resolve discrepancies, and maintain strong vendor relationships.
- Coordinate logistics for the timely receipt and distribution of goods, including scheduling transportation and managing warehousing activities.
- Analyze supply chain data to identify potential risks, optimize processes, and suggest improvements for efficiency and cost reduction.
- Prepare detailed reports on inventory status, purchasing activities, and supplier performance for management review.
- Collaborate with internal departments, such as production, sales, and finance, to align supply chain operations with organizational needs.
Work Environment
Supply Coordinators typically work in an office environment, though some roles may involve time in warehouses or distribution centers. The work often involves a mix of independent data analysis and collaborative problem-solving with internal teams and external suppliers. The pace can be dynamic, particularly when managing urgent orders or resolving supply chain disruptions.
Most positions are full-time, Monday-Friday, though some roles might require occasional flexibility to accommodate international suppliers or critical deliveries. Remote work is increasingly common, but on-site presence may be necessary for roles heavily involved in physical inventory management or direct oversight of logistics operations.
Tools & Technologies
Supply Coordinators regularly use Enterprise Resource Planning (ERP) systems like SAP, Oracle, or Microsoft Dynamics 365 to manage inventory, purchasing, and order fulfillment. They also rely on Warehouse Management Systems (WMS) for tracking goods within storage facilities and Transportation Management Systems (TMS) for logistics planning.
Spreadsheet software such as Microsoft Excel or Google Sheets is essential for data analysis, reporting, and creating forecasts. Communication tools like Slack, Microsoft Teams, and email are vital for coordinating with suppliers and internal teams. Knowledge of business intelligence tools like Tableau or Power BI can be beneficial for advanced data visualization and trend analysis.
Supply Coordinator Skills & Qualifications
A Supply Coordinator's qualifications center on a blend of organizational acumen, logistical understanding, and system proficiency. This role bridges the gap between procurement, inventory, and operations, ensuring a smooth flow of materials and resources. Success hinges on precise execution and proactive problem-solving rather than broad strategic planning.
Requirements for a Supply Coordinator vary significantly based on the industry and company size. In manufacturing or large retail, formal education and specific ERP system experience are often non-negotiable. Smaller businesses or service-based industries might prioritize practical experience and adaptability over a specific degree. The role's entry point typically requires foundational knowledge, while senior coordinator roles demand deeper analytical skills and vendor management experience.
Practical experience often holds more weight than certifications for this position, though certifications in supply chain management (e.g., APICS CSCP or CPIM) can accelerate career progression. Alternative pathways, such as vocational training, relevant internships, or prior experience in warehouse operations, are highly valued. The skill landscape for Supply Coordinators is evolving, with an increasing emphasis on data analysis, digital literacy, and resilience in managing supply chain disruptions. Foundational skills remain critical, but the ability to adapt to new technologies and global complexities is becoming a "must-have."
Education Requirements
Technical Skills
- Inventory Management Systems (e.g., SAP MM, Oracle SCM, Microsoft Dynamics 365, NetSuite)
- Order Processing Software
- Microsoft Excel (intermediate to advanced for data analysis, pivot tables, VLOOKUP)
- Warehouse Management Systems (WMS)
- Logistics and Freight Management Principles
- Basic Data Analysis and Reporting
- Enterprise Resource Planning (ERP) basics relevant to supply chain modules
- Vendor Relationship Management (VRM) software (e.g., CRM for suppliers)
- Material Requirements Planning (MRP) concepts and application
- Procurement and Purchasing Software (e.g., Ariba, Coupa)
- Spreadsheet-based forecasting and demand planning
- Database querying basics (e.g., SQL for pulling reports)
Soft Skills
- Organizational Skills: Essential for managing multiple orders, tracking inventory, and maintaining accurate records efficiently.
- Attention to Detail: Critical for preventing errors in orders, quantities, and delivery schedules, which can lead to costly disruptions.
- Problem-Solving: Important for quickly addressing unexpected issues like delayed shipments, damaged goods, or inventory discrepancies.
- Communication Skills: Necessary for clear interaction with vendors, internal departments, and logistics partners to ensure smooth operations.
- Adaptability: Key for responding to fluctuating demand, supply chain disruptions, and changing operational priorities.
- Time Management: Crucial for prioritizing tasks, meeting deadlines, and ensuring timely material availability for production or sales.
- Proactiveness: Valued for anticipating potential supply issues and taking preventative measures before they escalate.
- Negotiation Skills: Important for discussing terms with suppliers and finding cost-effective solutions for materials and services, particularly in roles with purchasing aspects for small to medium businesses or where the role includes some procurement responsibilities
How to Become a Supply Coordinator
Breaking into a Supply Coordinator role offers multiple pathways, whether you are a recent graduate, a career changer, or transitioning from a related field. Traditional routes often involve a bachelor's degree in supply chain management, logistics, business administration, or a similar discipline. However, many companies now prioritize practical skills and relevant experience, making non-traditional entry points via certifications, vocational training, or internal transfers increasingly viable.
Timeline expectations vary; a complete beginner might need 6-12 months to acquire foundational knowledge and relevant certifications, while someone with transferable skills from operations or administrative roles could transition in 3-6 months. Geographic location and company size also influence entry. Larger corporations in major logistics hubs often seek candidates with formal education or specialized software skills, whereas smaller companies or those in less competitive markets might be more open to individuals with strong organizational abilities and a willingness to learn. Economic conditions can affect hiring speed, but the demand for efficient supply chain operations remains consistent.
Networking and informational interviews are crucial, providing insights into specific industry needs and potential openings that are not widely advertised. Overcoming barriers like a lack of direct experience often involves highlighting transferable skills such as data analysis, problem-solving, communication, and meticulous attention to detail. Focus on building a foundational understanding of inventory management, procurement, and logistics software, as these are universally valued in this role. Your entry strategy should align with your existing background and desired industry sector, whether it is manufacturing, retail, or healthcare logistics.
Understand the core principles of supply chain management, focusing on inventory control, procurement, and logistics. Seek out entry-level courses or online certifications such as the CSCP (Certified Supply Chain Professional) or CLTD (Certified in Logistics, Transportation and Distribution) from APICS, or a basic course in supply chain fundamentals from platforms like Coursera or edX. This foundational knowledge is essential for understanding the flow of goods and information.
Develop proficiency in essential software and tools commonly used in supply coordination. This includes advanced Microsoft Excel for data analysis and reporting, and familiarity with Enterprise Resource Planning (ERP) systems like SAP, Oracle, or NetSuite. Many free tutorials and demo versions are available online to help you gain hands-on experience with these critical applications.
Gain practical experience through internships, volunteer work, or entry-level positions in related fields such as administrative support, warehouse operations, or customer service. Look for opportunities to manage inventory, process orders, or coordinate shipments, even if it is not a dedicated Supply Coordinator role. This hands-on experience demonstrates your ability to apply theoretical knowledge in a real-world setting.
Build a professional network by attending industry events, joining online forums, and connecting with supply chain professionals on LinkedIn. Participate in discussions, ask thoughtful questions, and seek out informational interviews to learn about specific company needs and career paths. A strong network can provide valuable mentorship and lead to job opportunities not publicly advertised.
Craft a compelling resume and cover letter that highlight your relevant skills, certifications, and practical experiences, even if they are from non-traditional roles. Tailor your application to each job description, emphasizing your ability to manage data, optimize processes, and communicate effectively. Develop a strong narrative around your problem-solving abilities and attention to detail.
Prepare thoroughly for interviews by researching common supply chain challenges and practicing your responses to behavioral and situational questions. Be ready to discuss your understanding of inventory management, forecasting, and supplier relationship management, and provide examples of how you have solved problems or improved processes in previous roles. Show enthusiasm for continuous learning and adapting to dynamic supply chain environments.
Step 1
Understand the core principles of supply chain management, focusing on inventory control, procurement, and logistics. Seek out entry-level courses or online certifications such as the CSCP (Certified Supply Chain Professional) or CLTD (Certified in Logistics, Transportation and Distribution) from APICS, or a basic course in supply chain fundamentals from platforms like Coursera or edX. This foundational knowledge is essential for understanding the flow of goods and information.
Step 2
Develop proficiency in essential software and tools commonly used in supply coordination. This includes advanced Microsoft Excel for data analysis and reporting, and familiarity with Enterprise Resource Planning (ERP) systems like SAP, Oracle, or NetSuite. Many free tutorials and demo versions are available online to help you gain hands-on experience with these critical applications.
Step 3
Gain practical experience through internships, volunteer work, or entry-level positions in related fields such as administrative support, warehouse operations, or customer service. Look for opportunities to manage inventory, process orders, or coordinate shipments, even if it is not a dedicated Supply Coordinator role. This hands-on experience demonstrates your ability to apply theoretical knowledge in a real-world setting.
Step 4
Build a professional network by attending industry events, joining online forums, and connecting with supply chain professionals on LinkedIn. Participate in discussions, ask thoughtful questions, and seek out informational interviews to learn about specific company needs and career paths. A strong network can provide valuable mentorship and lead to job opportunities not publicly advertised.
Step 5
Craft a compelling resume and cover letter that highlight your relevant skills, certifications, and practical experiences, even if they are from non-traditional roles. Tailor your application to each job description, emphasizing your ability to manage data, optimize processes, and communicate effectively. Develop a strong narrative around your problem-solving abilities and attention to detail.
Step 6
Prepare thoroughly for interviews by researching common supply chain challenges and practicing your responses to behavioral and situational questions. Be ready to discuss your understanding of inventory management, forecasting, and supplier relationship management, and provide examples of how you have solved problems or improved processes in previous roles. Show enthusiasm for continuous learning and adapting to dynamic supply chain environments.
Education & Training Needed to Become a Supply Coordinator
The educational landscape for a Supply Coordinator emphasizes practical skills and efficient operations rather than advanced theoretical degrees. Many entry-level roles accept candidates with a high school diploma and relevant experience, or an Associate's degree in supply chain management, logistics, or business administration. These 2-year degrees typically cost between $8,000 and $25,000 and provide foundational knowledge in inventory control, procurement, and distribution.
For those seeking to advance or enter larger organizations, a Bachelor's degree in Supply Chain Management or Business Administration is often preferred. These 4-year programs range from $40,000 to $100,000+ at public universities and significantly more at private institutions. They offer a deeper dive into strategic sourcing, global logistics, and supply chain analytics. Completion takes four years for full-time students. Self-study and online certifications, ranging from free resources to programs costing $500-$5,000, can also be effective, especially for career changers or those needing specific skill upgrades, with completion times varying from 3 to 12 months.
Employers value practical experience and certifications. Credentials like the APICS Certified in Production and Inventory Management (CPIM) or Certified Supply Chain Professional (CSCP) enhance a candidate's marketability, demonstrating a commitment to industry best practices. These certifications often require prior experience or a degree. Continuous learning in areas like supply chain software (e.g., SAP, Oracle), data analytics, and lean principles is crucial for career progression, as the field rapidly evolves with technology and global economic shifts. The cost-benefit of a certification often outweighs a full degree for experienced professionals looking to specialize.
Supply Coordinator Salary & Outlook
Compensation for a Supply Coordinator varies significantly based on several key factors. Geographic location plays a crucial role, with higher salaries typically found in major metropolitan areas or regions with significant manufacturing and logistics hubs due to increased cost of living and higher demand for skilled professionals.
Experience levels, specialized skills in inventory management, logistics software proficiency, or specific industry knowledge (e.g., healthcare, automotive) also drive salary variations. Individuals with proven abilities in optimizing supply flows or managing complex vendor relationships often command premium compensation.
Total compensation packages extend beyond base salary, often including performance bonuses tied to efficiency metrics, cost savings, or on-time delivery rates. Benefits such as health insurance, retirement contributions like 401(k) matching, and professional development allowances for certifications (e.g., APICS) add substantial value. Larger companies or those with complex global supply chains tend to offer more robust packages and higher base salaries compared to smaller organizations.
Negotiation leverage comes from demonstrating quantifiable impact on supply chain efficiency or cost reduction. Remote work opportunities are expanding, influencing salary ranges and allowing for geographic arbitrage, though some roles still require on-site presence for physical inventory management. While these figures focus on the USD context, international markets present their own unique compensation structures influenced by local economies and supply chain maturity.
Salary by Experience Level
Level | US Median | US Average |
---|---|---|
Junior Supply Coordinator | $48k USD | $52k USD |
Supply Coordinator | $60k USD | $65k USD |
Senior Supply Coordinator | $73k USD | $78k USD |
Supply Chain Specialist | $84k USD | $89k USD |
Supply Chain Manager | $108k USD | $115k USD |
Market Commentary
The job market for Supply Coordinators shows consistent demand, driven by the increasing complexity of global supply chains and the need for efficient logistics. Current trends emphasize resilience, sustainability, and technological integration, which elevates the role's importance. The growth outlook for supply chain and logistics roles, including coordinators, is projected to be stable, with the U.S. Bureau of Labor Statistics indicating a steady demand over the next decade as businesses continue to optimize their operations.
Emerging opportunities for Supply Coordinators include specializations in e-commerce logistics, reverse logistics, and data analytics for demand forecasting. The adoption of AI and automation tools in warehousing and transportation is transforming the role, requiring coordinators to become more tech-savvy and focused on system management rather than purely manual tasks. This shift creates a need for professionals who can interpret data, manage automated systems, and troubleshoot issues.
Supply and demand dynamics remain relatively balanced, though there is a growing need for candidates with strong analytical and technological skills. The profession is generally recession-resistant, as businesses always require efficient movement of goods, even during economic downturns, though specific industry sectors may experience fluctuations. Geographic hotspots for these roles include major port cities, manufacturing centers, and distribution hubs, particularly in states like California, Texas, and New Jersey. Future-proofing this career involves continuous learning in supply chain software, data science, and agile methodologies.
Supply Coordinator Career Path
Career progression for a Supply Coordinator typically begins with foundational operational tasks, evolving into strategic planning and leadership roles. Individuals generally advance by mastering logistics, inventory management, and vendor relations, demonstrating efficiency and problem-solving skills.
Advancement speed depends on several factors, including individual performance, the complexity of the supply chain, and the company's size and industry. Larger corporations or those with global supply chains often offer more structured and varied advancement opportunities. Lateral movement to roles like Procurement Specialist or Logistics Analyst is common, broadening an individual's expertise.
Professionals often choose between an individual contributor (IC) track, focusing on deep specialization in areas like demand planning or optimization, and a management track, leading teams and overseeing broader supply chain operations. Networking, mentorship, and continuous learning, particularly in supply chain technologies and analytics, are crucial for sustained career growth and opening alternative pathways in related fields like operations consulting or project management.
Junior Supply Coordinator
0-2 yearsSupports the supply chain team by performing essential administrative and operational tasks. Responsibilities include data entry, tracking shipments, verifying inventory counts, and assisting with order processing. Works under direct supervision, with decisions typically limited to routine tasks.
Key Focus Areas
Develop a strong understanding of inventory systems and basic logistics principles. Focus on data entry accuracy, communication skills, and learning internal company policies and procedures. Begin to identify minor process inefficiencies and suggest improvements.
Supply Coordinator
2-4 yearsManages daily supply chain operations, including inventory management, order fulfillment, and coordinating with suppliers and logistics partners. Handles routine issues independently and contributes to process improvements. Works with moderate supervision, impacting departmental efficiency and operational flow.
Key Focus Areas
Master inventory control techniques, demand forecasting basics, and vendor communication. Develop problem-solving skills for routine supply chain disruptions. Enhance analytical skills for reporting and basic performance metrics. Explore supply chain software functionalities.
Senior Supply Coordinator
4-7 yearsOversees specific segments of the supply chain, such as a product category or regional distribution. Identifies and resolves complex logistical challenges, optimizes inventory levels, and manages key vendor relationships. Acts as a subject matter expert, influencing operational decisions and contributing to strategic planning.
Key Focus Areas
Advance in complex problem-solving, risk mitigation, and strategic supplier relationship management. Develop strong negotiation skills and an understanding of global logistics. Focus on data analysis for decision-making and identifying cost-saving opportunities. Begin mentoring junior team members.
Supply Chain Specialist
7-10 yearsActs as a technical expert, analyzing complex supply chain data to identify trends, optimize processes, and implement strategic initiatives. Leads specific projects aimed at improving efficiency, reducing costs, or enhancing supply chain resilience. Provides critical insights that directly influence strategic decisions and operational strategies.
Key Focus Areas
Specialize in areas like demand planning, supply chain analytics, or logistics optimization. Acquire advanced knowledge of supply chain software (e.g., ERP, WMS) and data visualization tools. Focus on project management, cross-functional collaboration, and presenting data-driven recommendations to leadership.
Supply Chain Manager
10+ yearsManages and directs a team of supply chain professionals, overseeing the entire supply chain function or a significant part of it. Develops and implements supply chain strategies, manages budgets, and ensures operational efficiency and compliance. Makes high-level decisions that impact organizational profitability and customer satisfaction.
Key Focus Areas
Develop strong leadership, team management, and strategic planning capabilities. Focus on financial acumen, budgeting, and aligning supply chain operations with overall business goals. Cultivate change management skills and a deep understanding of industry trends and emerging technologies.
Junior Supply Coordinator
0-2 yearsSupports the supply chain team by performing essential administrative and operational tasks. Responsibilities include data entry, tracking shipments, verifying inventory counts, and assisting with order processing. Works under direct supervision, with decisions typically limited to routine tasks.
Key Focus Areas
Develop a strong understanding of inventory systems and basic logistics principles. Focus on data entry accuracy, communication skills, and learning internal company policies and procedures. Begin to identify minor process inefficiencies and suggest improvements.
Supply Coordinator
2-4 yearsManages daily supply chain operations, including inventory management, order fulfillment, and coordinating with suppliers and logistics partners. Handles routine issues independently and contributes to process improvements. Works with moderate supervision, impacting departmental efficiency and operational flow.
Key Focus Areas
Master inventory control techniques, demand forecasting basics, and vendor communication. Develop problem-solving skills for routine supply chain disruptions. Enhance analytical skills for reporting and basic performance metrics. Explore supply chain software functionalities.
Senior Supply Coordinator
4-7 yearsOversees specific segments of the supply chain, such as a product category or regional distribution. Identifies and resolves complex logistical challenges, optimizes inventory levels, and manages key vendor relationships. Acts as a subject matter expert, influencing operational decisions and contributing to strategic planning.
Key Focus Areas
Advance in complex problem-solving, risk mitigation, and strategic supplier relationship management. Develop strong negotiation skills and an understanding of global logistics. Focus on data analysis for decision-making and identifying cost-saving opportunities. Begin mentoring junior team members.
Supply Chain Specialist
7-10 yearsActs as a technical expert, analyzing complex supply chain data to identify trends, optimize processes, and implement strategic initiatives. Leads specific projects aimed at improving efficiency, reducing costs, or enhancing supply chain resilience. Provides critical insights that directly influence strategic decisions and operational strategies.
Key Focus Areas
Specialize in areas like demand planning, supply chain analytics, or logistics optimization. Acquire advanced knowledge of supply chain software (e.g., ERP, WMS) and data visualization tools. Focus on project management, cross-functional collaboration, and presenting data-driven recommendations to leadership.
Supply Chain Manager
10+ yearsManages and directs a team of supply chain professionals, overseeing the entire supply chain function or a significant part of it. Develops and implements supply chain strategies, manages budgets, and ensures operational efficiency and compliance. Makes high-level decisions that impact organizational profitability and customer satisfaction.
Key Focus Areas
Develop strong leadership, team management, and strategic planning capabilities. Focus on financial acumen, budgeting, and aligning supply chain operations with overall business goals. Cultivate change management skills and a deep understanding of industry trends and emerging technologies.
Job Application Toolkit
Ace your application with our purpose-built resources:
Supply Coordinator Resume Examples
Proven layouts and keywords hiring managers scan for.
View examplesSupply Coordinator Cover Letter Examples
Personalizable templates that showcase your impact.
View examplesTop Supply Coordinator Interview Questions
Practice with the questions asked most often.
View examplesSupply Coordinator Job Description Template
Ready-to-use JD for recruiters and hiring teams.
View examplesGlobal Supply Coordinator Opportunities
A Supply Coordinator ensures efficient flow of goods and materials globally. This role involves managing logistics, inventory, and supplier relationships across borders. Global demand for Supply Coordinators remains steady as international trade expands and supply chains become more complex. Professionals often consider international opportunities to experience diverse logistics models and gain exposure to new markets. Understanding regional regulations and cultural nuances is key for success. Certifications like APICS CSCP or ISM CPSM facilitate global mobility, demonstrating a standardized skill set.
Global Salaries
Supply Coordinator salaries vary significantly by region, reflecting economic conditions and cost of living. In North America, a Supply Coordinator can expect to earn between $45,000 and $70,000 USD annually. For example, in the United States, entry-level roles might start at $40,000 USD, while experienced professionals in major logistics hubs like Chicago or Los Angeles can reach $65,000-$75,000 USD. In Canada, salaries often range from CAD $48,000 to CAD $68,000 ($35,000-$50,000 USD).
Europe shows a wide range, from €30,000 to €55,000 ($32,000-$60,000 USD). Germany offers €38,000-€55,000 ($41,000-$60,000 USD), while Eastern European countries like Poland might offer PLN 45,000-70,000 ($11,000-$17,000 USD), which offers strong local purchasing power despite lower USD equivalents. The UK typically sees salaries between £28,000 and £45,000 ($35,000-$56,000 USD).
Asia-Pacific markets like Australia offer AUD $55,000-$75,000 ($36,000-$50,000 USD), while Singapore ranges from SGD $40,000-$65,000 ($30,000-$48,000 USD). In Latin America, salaries are generally lower but offer good local purchasing power. Brazil, for instance, might offer R$40,000-R$70,000 ($8,000-$14,000 USD). These figures are gross salaries; take-home pay varies significantly based on local tax structures and social security contributions. Benefits like health insurance, retirement plans, and vacation time also differ by country, impacting the overall compensation package. International experience can often lead to higher compensation in subsequent roles, as it demonstrates adaptability and global supply chain understanding.
Remote Work
Supply Coordinator roles typically require on-site presence due to physical inventory management and direct interaction with warehouses or shipping partners. However, some aspects, like demand planning, supplier communication, or data analysis, can be performed remotely. The potential for full remote work is limited, but hybrid models are becoming more common, allowing for partial remote work flexibility.
Legal and tax implications for international remote work are complex, requiring employers to navigate different labor laws and tax jurisdictions. Time zone differences can pose challenges for global team collaboration, especially when coordinating across continents. Digital nomad visas are generally less applicable for this role given its operational nature. Companies often prefer to hire Supply Coordinators locally to ensure compliance and efficient operations, but global companies with distributed supply networks might offer some remote flexibility for specific tasks. Salary expectations for remote roles often align with the cost of living in the employee's location, rather than the company's headquarters.
Visa & Immigration
Supply Coordinators seeking international opportunities often pursue skilled worker visas. Popular destinations include Canada, Australia, Germany, and the UK, which have established points-based or employer-sponsored visa systems. Requirements typically include a job offer, relevant work experience, and an educational background in supply chain management, logistics, or business. Many countries require a bachelor's degree, and professional certifications enhance eligibility.
Credential recognition is generally straightforward for standard university degrees. Visa application timelines vary from a few weeks to several months, depending on the country and visa type. For example, Canada's Express Entry system prioritizes skilled workers, while Germany's skilled immigration law facilitates entry for qualified professionals with job offers. Language proficiency, often English or the local language, is a common requirement, usually demonstrated through standardized tests. Pathways to permanent residency exist in many countries after several years of continuous skilled employment. Some roles may qualify for intra-company transfer visas if moving within a multinational corporation, simplifying the process. Family members can typically apply for dependent visas, allowing them to accompany the main applicant.
2025 Market Reality for Supply Coordinators
Understanding current market realities is crucial for any Supply Coordinator aiming for career success. The landscape for this role has evolved significantly from 2023 to 2025. Post-pandemic shifts emphasized supply chain resilience and digital transformation, while the AI revolution introduced new tools and expectations.
Broader economic factors, such as inflation and geopolitical instability, directly impact global trade and inventory management, influencing hiring needs. Market realities for Supply Coordinators vary by experience level; entry-level roles face more competition, while experienced professionals with specialized skills find more opportunities. Geographic region and company size also play a role, with larger enterprises and specific industrial hubs offering more consistent demand. This analysis provides an honest assessment to help you navigate these conditions.
Current Challenges
Supply Coordinator candidates face heightened competition. Automation tools now handle more routine tasks, increasing employer expectations for strategic thinking. Economic uncertainty causes companies to optimize existing supply chains rather than expand them, reducing new openings. Companies seek candidates who bridge traditional supply chain knowledge with data analytics and AI tool proficiency. This creates a skill gap for those lacking modern tech skills. Job search timelines have extended, requiring more persistence.
Growth Opportunities
Despite challenges, strong demand persists for Supply Coordinators skilled in supply chain analytics and digital transformation. Professionals who can implement and manage AI-driven forecasting tools, optimize logistics using data, or navigate complex global trade regulations find excellent opportunities. Roles focused on sustainability in supply chains are also emerging.
Underserved markets exist in regions expanding their manufacturing bases or where companies are investing in resilient, localized supply networks. Developing expertise in specific software platforms, such as SAP SCM, Oracle SCM, or advanced Excel modeling, provides a competitive edge. Certifications in supply chain management (e.g., CSCP, CPIM) combined with practical AI tool experience are highly valued. Market corrections emphasize efficiency, creating opportunities for those who can drive cost savings and process improvements. Industries like healthcare, e-commerce, and renewable energy show consistent demand for skilled supply chain professionals. Strategic investment in continuous learning and adapting to new technologies positions candidates for long-term success.
Current Market Trends
Demand for Supply Coordinators remains steady but is not experiencing rapid growth as of 2025. Companies prioritize efficiency and resilience in their supply chains. Hiring patterns show a strong preference for candidates who understand end-to-end supply chain visibility and risk mitigation. AI integration, particularly in demand forecasting and inventory management, reshapes the role. Coordinators now manage automated systems and interpret AI-generated insights, rather than just executing manual processes.
Economic conditions, including inflation and fluctuating global trade, push companies to optimize existing supply networks. This leads to fewer entirely new positions and more focus on upgrading current teams. Employers seek adaptability and a proactive approach to disruption. Salary trends show modest increases, with higher compensation for those demonstrating strong data analysis skills and experience with supply chain software. Market saturation exists at entry levels, while experienced professionals with specialized tech skills find better opportunities.
Geographic variations are notable; roles are more plentiful in manufacturing hubs and major distribution centers. Remote work for Supply Coordinators is less common compared to other fields, as many tasks require on-site presence or direct interaction with physical inventory and logistics teams. Seasonal hiring patterns align with peak consumer demand periods, such as before major holidays, leading to temporary spikes in activity.
Emerging Specializations
The supply chain landscape is undergoing significant transformation, driven by advancements in technology, evolving global trade dynamics, and increasing demands for sustainability. These shifts are creating entirely new specialization opportunities for Supply Coordinators. Understanding these future-oriented career paths allows professionals to strategically position themselves for next-generation roles.
Early positioning in emerging areas often commands premium compensation and accelerated career growth. While established specializations remain vital, focusing on cutting-edge fields can lead to more impactful roles and leadership opportunities in 2025 and beyond. This strategic choice involves balancing the stability of current roles with the high-reward potential of new frontiers.
Emerging specializations typically take 3-5 years to become mainstream and generate a significant number of job openings. Investing in these areas now provides a competitive advantage as the market matures. However, pursuing cutting-edge fields carries inherent risks; some may not achieve widespread adoption. Careful assessment of trends and continuous learning mitigate these risks, ensuring a rewarding career trajectory.
Blockchain Traceability Coordinator
AI-Driven Supply Optimization Coordinator
Sustainable Supply Chain Coordinator
On-Demand & Additive Manufacturing Supply Coordinator
Cyber-Resilient Supply Chain Coordinator
Pros & Cons of Being a Supply Coordinator
Making informed career decisions requires a clear understanding of both the potential advantages and genuine challenges of a specific profession. A career as a Supply Coordinator offers distinct benefits but also presents unique difficulties. Experiences can vary significantly based on the company's size, industry sector, specific supply chain complexity, and individual personality or preferences. What one person views as a pro, another might see as a con. For instance, a fast-paced environment might be exciting for some but stressful for others. Furthermore, the nature of pros and cons can evolve at different stages of a career, from entry-level to senior roles. This assessment provides an honest, balanced perspective to help set realistic expectations.
Pros
- Stable job market with consistent demand across various industries, as every organization needs effective supply management to function, offering good job security.
- Entry-level accessibility allows individuals to enter the field with a relevant associate's or bachelor's degree, or even through vocational training, making it accessible to a wide range of candidates.
- Develops strong organizational and problem-solving skills by managing inventory, coordinating logistics, and resolving supply chain disruptions, which are highly transferable to other roles.
- Diverse industry exposure is common, as Supply Coordinators are needed in manufacturing, retail, healthcare, and technology, providing opportunities to explore different business environments.
- Clear impact on business operations is evident, as efficient supply coordination directly contributes to cost savings, timely product delivery, and overall customer satisfaction.
- Opportunities for continuous learning arise from exposure to new technologies, global logistics, and evolving market demands, ensuring the role remains dynamic and intellectually engaging.
- Collaborative work environment involves regular interaction with various internal departments and external partners, fostering strong teamwork and networking opportunities.
Cons
- High-pressure environment, especially when dealing with urgent requests or unexpected disruptions in the supply chain, can lead to significant stress and long hours to resolve issues.
- Repetitive tasks are common in daily operations, such as data entry, tracking shipments, and updating inventory, which may lead to monotony for some individuals.
- Limited autonomy often exists as processes are highly structured and dictated by company policies or external vendor agreements, leaving little room for independent decision-making.
- Exposure to external factors like natural disasters, geopolitical events, or economic downturns can directly impact supply stability, creating unpredictable challenges and requiring constant adaptation.
- Career progression can be slow or require further specialization, as many entry-level supply coordinator roles have a defined scope and advancement often necessitates moving into management or analytical positions.
- Communication challenges are frequent, as coordinating with diverse stakeholders including suppliers, internal departments, and logistics providers requires excellent interpersonal skills to navigate potential misunderstandings or conflicts.
- Potential for physical demands exists in roles that require hands-on inventory checks or movement within warehouses, though this varies significantly by company and industry.
Frequently Asked Questions
What are the typical educational and experience requirements for a Supply Coordinator role?
Becoming a Supply Coordinator typically requires a bachelor's degree in supply chain management, logistics, business administration, or a related field. Some entry-level roles may accept an associate's degree with relevant experience or certifications. Practical experience with inventory management software, procurement processes, and basic data analysis is highly beneficial for securing a position.
Can I transition into a Supply Coordinator role without a specific supply chain degree?
You can realistically transition into this field without a specific supply chain degree, especially if you have strong organizational, analytical, and communication skills. Many successful Supply Coordinators come from administrative, retail management, or operations roles. Pursuing certifications like APICS CSCP or CPIM can significantly boost your qualifications and demonstrate commitment to the field.
How long does it typically take to become job-ready as a Supply Coordinator from scratch?
The time it takes to become job-ready varies, but with focused effort, you can prepare for entry-level roles within 6-12 months. This includes gaining foundational knowledge through online courses or certifications, and ideally, securing an internship or a related entry-level position to build practical experience. Networking within the industry also accelerates the process.
What are the salary expectations for an entry-level Supply Coordinator, and how does it grow with experience?
Entry-level Supply Coordinators can expect a salary range of $40,000 to $55,000 annually, depending on location, industry, and company size. With 3-5 years of experience, this can increase to $55,000 to $70,000. Senior or specialized roles, especially in high-demand industries, can command higher salaries, often exceeding $75,000.
What is the typical work-life balance like for a Supply Coordinator?
Work-life balance for Supply Coordinators is generally stable, with most roles being standard Monday-Friday, 9-to-5 positions. However, peak seasons, unexpected supply chain disruptions, or urgent orders may require occasional overtime or flexible hours. Roles in manufacturing or logistics hubs might have less predictable schedules compared to corporate office settings.
What is the job security and market demand for Supply Coordinators?
The job market for Supply Coordinators is stable and growing, driven by the increasing complexity of global supply chains and the need for efficient logistics. Companies across almost all industries require skilled professionals to manage their supply of goods and services. Automation may change some tasks, but the need for human oversight, problem-solving, and relationship management remains strong.
What are the common career growth paths for a Supply Coordinator?
Supply Coordinators have several avenues for career growth. You can advance to Supply Chain Analyst, Procurement Specialist, Logistics Manager, or even Supply Chain Manager. Specialization in areas like strategic sourcing, demand planning, or inventory optimization also opens doors to more senior and specialized roles within larger organizations.
Related Careers
Explore similar roles that might align with your interests and skills:
Supply Chain Coordinator
A growing field with similar skill requirements and career progression opportunities.
Explore career guideSupply Chain Specialist
A growing field with similar skill requirements and career progression opportunities.
Explore career guideSupply Clerk
A growing field with similar skill requirements and career progression opportunities.
Explore career guideSupply Manager
A growing field with similar skill requirements and career progression opportunities.
Explore career guideSupply Planner
A growing field with similar skill requirements and career progression opportunities.
Explore career guideAssess your Supply Coordinator readiness
Understanding where you stand today is the first step toward your career goals. Our Career Coach helps identify skill gaps and create personalized plans.
Skills Gap Analysis
Get a detailed assessment of your current skills versus Supply Coordinator requirements. Our AI Career Coach identifies specific areas for improvement with personalized recommendations.
See your skills gapCareer Readiness Assessment
Evaluate your overall readiness for Supply Coordinator roles with our AI Career Coach. Receive personalized recommendations for education, projects, and experience to boost your competitiveness.
Assess your readinessSimple pricing, powerful features
Upgrade to Himalayas Plus and turbocharge your job search.
Himalayas
Himalayas Plus
Himalayas Max
Find your dream job
Sign up now and join over 100,000 remote workers who receive personalized job alerts, curated job matches, and more for free!
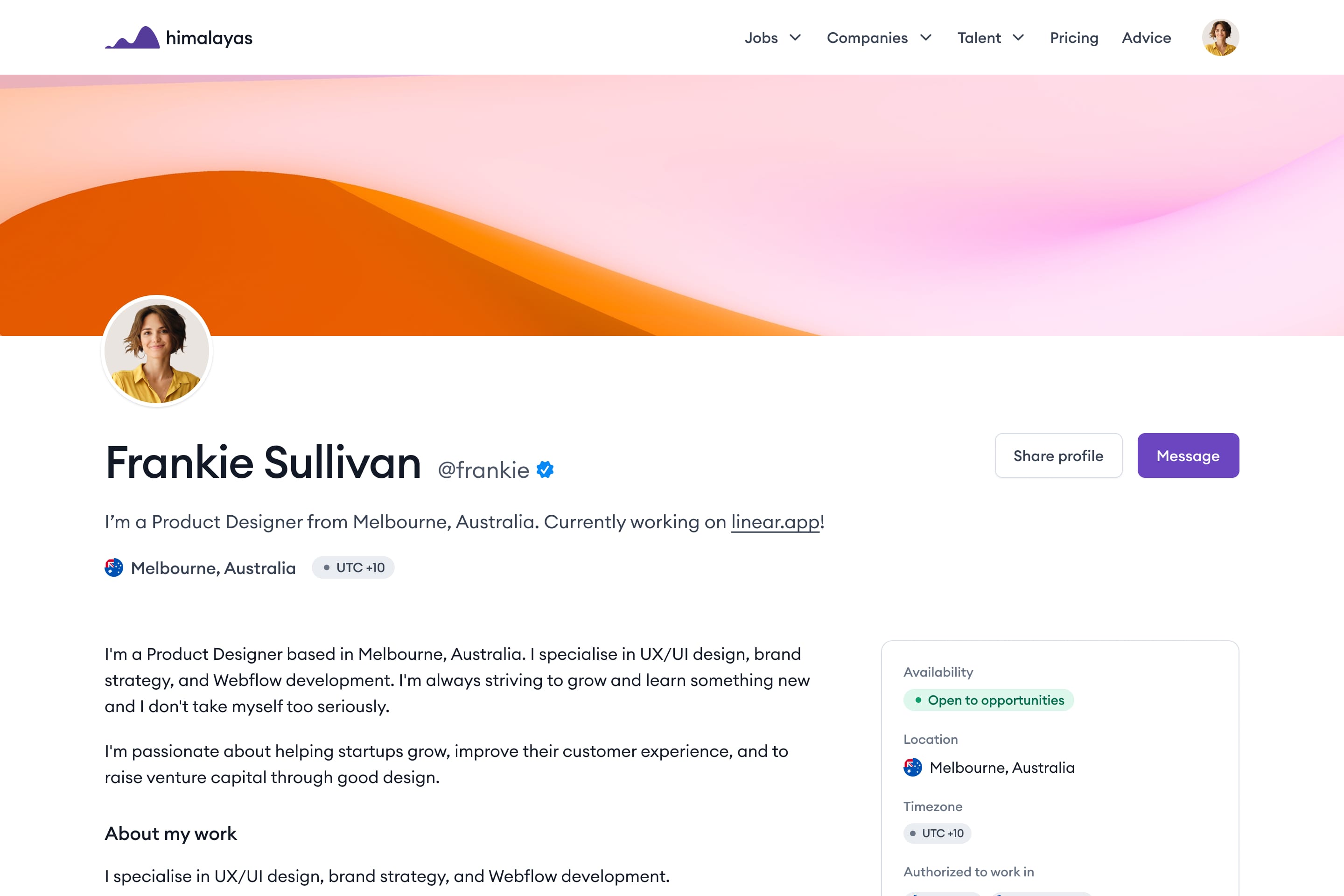