Complete Manufacturing Laborer Career Guide
Manufacturing laborers are the backbone of production, ensuring that raw materials transform into finished goods that power our economy. They perform essential tasks across various industries, from assembling products to operating machinery, directly contributing to output and efficiency. This hands-on role offers a clear path into industrial work, providing tangible skills and a direct impact on product delivery.
Key Facts & Statistics
Median Salary
$38,470 USD
(U.S. Bureau of Labor Statistics, May 2023)
Range: $29k - $55k+ USD, varying significantly by industry and experience
Growth Outlook
5%
as fast as average (U.S. Bureau of Labor Statistics, 2022-2032)
Annual Openings
≈133,900
openings annually (U.S. Bureau of Labor Statistics)
Top Industries
Typical Education
High school diploma or equivalent; on-the-job training is common and often preferred
What is a Manufacturing Laborer?
A manufacturing laborer is a foundational role within a production facility, responsible for the hands-on execution of tasks that keep a manufacturing line running. This role focuses on the physical assembly, operation of basic machinery, and quality control of products, ensuring that goods are produced efficiently and meet specific standards. Unlike a Manufacturing Engineer, who designs and optimizes production processes, or a Machine Operator, who specializes in complex machine setup and troubleshooting, the manufacturing laborer's primary function is direct involvement in the production process.
This position is crucial for the tangible output of any manufacturing operation, whether it involves consumer goods, automotive parts, or industrial equipment. Manufacturing laborers ensure the consistent flow of materials, the proper assembly of components, and the initial quality inspection of finished products. Their work directly impacts production volume and product quality, making them indispensable to the success of a manufacturing plant.
What does a Manufacturing Laborer do?
Key Responsibilities
- Operate production machinery safely and efficiently, following all standard operating procedures and safety protocols.
- Assemble components or products manually, ensuring accuracy and adherence to quality standards.
- Monitor production lines for issues, such as material shortages or equipment malfunctions, and report them promptly.
- Perform quality checks on finished products or components, identifying and removing defective items.
- Load and unload materials, raw goods, or finished products onto conveyors, pallets, or storage areas.
- Maintain a clean and organized work area throughout the shift, complying with 5S principles.
- Package finished products according to specifications, preparing them for shipment or further processing. This includes labeling and stacking.
Work Environment
Manufacturing laborers typically work in a factory or plant setting, which can range from large, open production floors to specialized assembly areas. The environment is often noisy due to machinery and requires adherence to strict safety regulations, including wearing personal protective equipment.
This role involves a high degree of physical activity, including standing for long periods, lifting, bending, and repetitive motions. Shifts often include nights, weekends, or rotating schedules to maintain continuous production. Teamwork and communication with fellow laborers and supervisors are essential, as tasks are often interdependent.
The pace of work can be steady and consistent on an assembly line or variable depending on production demands. While the work is hands-on and often structured, it requires constant attention to detail and safety.
Tools & Technologies
Manufacturing laborers frequently use a variety of hand tools such as wrenches, screwdrivers, and hammers for assembly or adjustments. They also operate power tools like drills, saws, and pneumatic tools for specific tasks. For moving materials, they utilize pallet jacks, hand trucks, and occasionally forklifts, requiring proper certification.
Technology in this role often includes human-machine interfaces (HMIs) on production machines, basic barcode scanners for inventory, and digital scales for weighing products. They also interact with safety equipment such as personal protective equipment (PPE) including safety glasses, gloves, and ear protection.
Communication tools like two-way radios or intercom systems are common for coordinating with supervisors or other team members. Some facilities use basic enterprise resource planning (ERP) systems for tracking production data or work orders.
Manufacturing Laborer Skills & Qualifications
Qualifications for a Manufacturing Laborer prioritize practical aptitude and a strong work ethic over formal academic credentials. Employers highly value hands-on experience in production environments, demonstrating an understanding of safety protocols and operational efficiency. Requirements vary significantly based on the industry sector; for instance, roles in food processing might emphasize hygiene standards, while automotive manufacturing focuses on assembly line precision and material handling.
Seniority levels primarily distinguish between entry-level positions, which require basic physical capabilities and a willingness to learn, and more experienced roles that demand proficiency with specific machinery or processes. Practical experience often outweighs formal education, though vocational training or certifications in areas like forklift operation or basic machinery maintenance can significantly enhance a candidate's appeal. Alternative pathways, such as on-the-job training programs or apprenticeships, are common and provide direct routes into the field for career changers.
The skill landscape for manufacturing laborers is evolving with increased automation. While manual dexterity and physical stamina remain crucial, a growing need exists for laborers who can operate basic machinery, understand digital control panels, and perform routine troubleshooting. Certifications in specific equipment operation, occupational safety (OSHA), or lean manufacturing principles add substantial value, signaling a commitment to safety and efficiency. Geographic variations in requirements often reflect local industry concentrations, with regions strong in heavy manufacturing requiring different skill sets than those focused on light assembly or electronics. Prioritizing safety knowledge and adaptability to new technologies helps laborers remain relevant and advance.
Education Requirements
Technical Skills
- Operation of basic hand and power tools (drills, wrenches, grinders, saws) for assembly or maintenance tasks.
- Material handling and lifting techniques, including proper body mechanics and use of pallet jacks or dollies.
- Quality control and inspection techniques, including visual checks and using basic measuring tools (calipers, tape measures).
- Adherence to Good Manufacturing Practices (GMP) and Standard Operating Procedures (SOPs) for process consistency and product quality.
- Basic machine operation and monitoring, such as presses, conveyors, or packaging equipment, including starting, stopping, and clearing simple jams.
- Inventory management basics, including counting, scanning, and organizing materials and finished products.
- Waste segregation and recycling procedures, ensuring compliance with environmental regulations.
- Lockout/Tagout procedures for safe machine maintenance and preventing accidental startups.
- Basic computer literacy for data entry, accessing work orders, or using simple inventory software.
- Understanding of Lean Manufacturing principles (e.g., 5S, waste reduction) to contribute to efficiency improvements.
Soft Skills
- Adherence to Safety Protocols: This is paramount for a Manufacturing Laborer due to the inherent risks in a factory environment. Strict adherence prevents accidents and ensures a safe workplace for everyone.
- Attention to Detail: Laborers perform repetitive tasks where small errors can lead to product defects or operational inefficiencies. Precision in following instructions and inspecting work is critical.
- Physical Stamina and Endurance: The role often involves prolonged standing, lifting, bending, and repetitive motions. Sustained physical capability throughout shifts is essential for performance.
- Reliability and Punctuality: Manufacturing schedules are tight, and absenteeism or tardiness can disrupt production lines and impact team productivity. Consistent presence is vital.
- Teamwork and Collaboration: Laborers frequently work in teams on assembly lines or in material handling. Effective communication and cooperation with colleagues ensure smooth operations.
- Adaptability to Change: Production demands, equipment, or processes can change rapidly. Laborers must quickly adjust to new instructions, tasks, or work environments.
- Problem-Solving (Basic): Identifying minor issues with equipment, materials, or processes and reporting them promptly or attempting basic fixes can prevent larger disruptions.
- Work Ethic and Initiative: Showing a willingness to take on tasks, learn new skills, and contribute actively to the team's goals goes beyond simply completing assigned duties, demonstrating commitment.
How to Become a Manufacturing Laborer
Entering the manufacturing laborer field offers diverse entry points, primarily focusing on practical skills and reliability rather than extensive formal education. Many individuals secure positions through vocational training, community college programs, or direct entry into entry-level roles that offer on-the-job training. The timeline for entry can range from a few weeks for immediate hires in high-demand areas to several months if specific certifications or apprenticeships are pursued.
Geographic location significantly influences opportunities; major industrial areas and manufacturing hubs will have more openings than rural regions. Company size also plays a role, with larger corporations often having more structured training programs, while smaller businesses might offer quicker entry and a broader range of tasks. Misconceptions often exist that these roles are purely manual; however, many modern manufacturing roles require attention to detail, basic technical literacy, and adherence to safety protocols.
Networking within local industrial parks, attending job fairs, and connecting with staffing agencies specializing in industrial placements are effective strategies. The hiring landscape values candidates who demonstrate a strong work ethic, punctuality, and a willingness to learn. Overcoming barriers often involves showing commitment through reliable attendance and a positive attitude during initial training periods.
Step 1
Step 2
Step 3
Step 4
Step 5
Step 6
Education & Training Needed to Become a Manufacturing Laborer
Becoming a Manufacturing Laborer primarily involves hands-on training and certifications rather than traditional degree programs. While a high school diploma or GED is often a baseline requirement, most essential skills are learned through on-the-job training, vocational programs, or specific industry certifications. Unlike roles requiring extensive theoretical knowledge, this position values practical aptitude, safety adherence, and efficiency.
Formal degree programs, such as a 4-year Bachelor's in Manufacturing Engineering, are generally not necessary for a Manufacturing Laborer and represent a significant overinvestment, typically costing $40,000-$100,000+. Instead, vocational training programs, which might cost $2,000-$10,000 and take 6-18 months, offer a more direct and cost-effective pathway. Shorter, specialized certifications can range from a few hundred dollars to a few thousand, with completion times from a few days to several weeks. Employers highly value credentials like OSHA safety certifications and specific equipment operation licenses, as these directly address workplace safety and productivity needs.
Continuous learning in this field often focuses on new machinery operation, process improvements (like Lean or Six Sigma principles at an introductory level), and updated safety protocols. These are usually offered through employer-sponsored training, community college short courses, or online modules. The market perception for Manufacturing Laborers prioritizes demonstrated skills and a strong work ethic over academic degrees. Practical experience and a proven track record of reliability and skill development are far more impactful for career advancement than advanced academic credentials.
Manufacturing Laborer Salary & Outlook
Compensation for a Manufacturing Laborer varies significantly based on several factors, reflecting the diverse nature of industrial work. Geographic location plays a crucial role; areas with higher costs of living or strong union presence typically offer better wages. For instance, salaries in major manufacturing hubs might differ substantially from those in rural regions, even within the same state.
Experience, specific skills, and the complexity of tasks performed also drive salary differences. Entry-level positions focus on basic tasks, while senior roles often involve operating specialized machinery or performing intricate assembly. Total compensation packages frequently extend beyond base pay, including overtime opportunities, production bonuses, and shift differentials. Many employers also provide comprehensive benefits, such as health insurance, retirement plans, and paid time off, which add significant value to the overall package.
Industry-specific trends influence earning potential. For example, laborers in advanced manufacturing sectors like aerospace or pharmaceuticals may command higher wages due to the precision and specialized knowledge required. Remote work is generally not applicable to this hands-on role. However, the consistent demand for skilled laborers in various industries provides a stable foundation for salary growth through performance and skill acquisition. While the presented figures are in USD, international markets will have their own distinct wage structures based on local economic conditions and labor laws.
Salary by Experience Level
Level | US Median | US Average |
---|---|---|
Entry-Level Manufacturing Laborer | $34k USD | $36k USD |
Manufacturing Laborer | $43k USD | $45k USD |
Senior Manufacturing Laborer | $50k USD | $52k USD |
Lead Manufacturing Laborer | $58k USD | $60k USD |
Manufacturing Supervisor | $72k USD | $75k USD |
Market Commentary
The job market for Manufacturing Laborers is currently stable with a projected slight growth, driven by ongoing industrial production and reshoring efforts in specific sectors. The Bureau of Labor Statistics projects employment of manufacturing production workers to show modest changes over the next decade. Demand remains consistent in industries like automotive, food processing, and general fabrication, where manual operations and machine tending are essential.
Emerging opportunities often involve roles within automated environments, requiring laborers to monitor robotic systems, perform quality control, and conduct routine maintenance. This shift demands a more technologically adept workforce, emphasizing the importance of continuous learning and adaptation. While automation can reduce demand for purely manual tasks, it simultaneously creates new roles for those who can interact with and manage advanced machinery.
The supply of qualified laborers can sometimes lag behind demand, especially for positions requiring specific technical skills or certifications. This imbalance can lead to better wages and job security for skilled individuals. Geographic hotspots for manufacturing include the Midwest and Southern United States, where new plants are frequently established. This profession is relatively recession-resistant as fundamental goods production remains necessary, though economic downturns can temporarily slow demand for specific products. Future-proofing involves acquiring skills in areas like industrial robotics, lean manufacturing principles, and data analysis to adapt to evolving manufacturing processes.
Manufacturing Laborer Career Path
Career progression for a Manufacturing Laborer typically involves a clear path from entry-level tasks to supervisory roles. Advancement is often tied to demonstrated reliability, skill acquisition, and adherence to safety protocols. Individuals can pursue an individual contributor (IC) track, focusing on specialized machine operation or quality control, or transition into management, leading teams and overseeing production.
Factors influencing advancement speed include consistent performance, willingness to learn new machinery or processes, and the company's size and specific industry. Larger corporations might offer more structured pathways and training programs, while smaller manufacturers may provide broader exposure to different aspects of production. Lateral moves might involve shifting between different production lines or departments, gaining diverse operational experience.
Networking within the facility, seeking mentorship from experienced colleagues, and maintaining a strong reputation for diligence are crucial for career growth. Continuous learning, often through on-the-job training or internal certifications for new equipment, marks significant progression. Some laborers might pivot into maintenance, logistics, or quality assurance roles, leveraging their hands-on production knowledge.
Entry-Level Manufacturing Laborer
0-1 yearKey Focus Areas
Manufacturing Laborer
1-3 yearsKey Focus Areas
Senior Manufacturing Laborer
3-5 yearsKey Focus Areas
Lead Manufacturing Laborer
5-8 yearsKey Focus Areas
Manufacturing Supervisor
8-12 years total experienceKey Focus Areas
Entry-Level Manufacturing Laborer
0-1 yearPerform repetitive tasks under direct supervision, such as loading/unloading materials, packaging finished goods, and basic assembly. Follow clear instructions to assist with production processes. Impact is localized to the immediate workstation, ensuring components are ready for the next step. Collaboration involves coordination with immediate team members.
Key Focus Areas
Develop fundamental safety practices and understand basic machine operation. Focus on learning standard operating procedures (SOPs) and material handling techniques. Build consistency in task execution and attention to detail. Seek guidance from experienced team members and actively participate in training.
Manufacturing Laborer
1-3 yearsOperate a range of production equipment, perform quality checks, and troubleshoot minor machine issues. Execute tasks with increasing autonomy and contribute to daily production targets. Decisions focus on optimizing individual workflow and ensuring product quality. Impact extends to the efficiency and output of a specific production line.
Key Focus Areas
Master a variety of production tasks and operate multiple types of machinery safely and efficiently. Improve problem-solving skills for minor operational issues. Understand quality control standards and identify defects. Develop communication skills to coordinate effectively with peers and supervisors.
Senior Manufacturing Laborer
3-5 yearsServe as a subject matter expert for specific equipment or processes, often handling more complex or critical tasks. Provide on-the-job training and guidance to less experienced team members. Make independent decisions regarding immediate operational adjustments to maintain production flow. Impact directly influences the productivity and quality of a section of the manufacturing process.
Key Focus Areas
Acquire expertise in complex machinery and advanced production techniques. Train new or junior laborers on specific tasks and safety protocols. Develop an understanding of lean manufacturing principles and waste reduction. Begin to identify process improvements and contribute to efficiency initiatives.
Lead Manufacturing Laborer
5-8 yearsOversee a small group of laborers, coordinating daily tasks and ensuring production targets are met. Act as the primary point of contact for operational issues within their assigned area. Make quick decisions to address immediate production bottlenecks or safety concerns. Impact spans the output and performance of their direct team, contributing to overall shift goals.
Key Focus Areas
Cultivate strong leadership and communication skills to guide a small team. Learn to interpret production schedules and allocate tasks efficiently. Develop basic troubleshooting skills for team-wide operational issues. Understand metrics related to output, quality, and safety for reporting.
Manufacturing Supervisor
8-12 years total experienceManage a team of manufacturing laborers, overseeing daily operations, production schedules, and quality control. Responsible for team performance, training, and disciplinary actions. Make strategic decisions regarding workflow optimization and resource deployment to meet broader production objectives. Impact directly affects the entire production line's efficiency, safety, and output.
Key Focus Areas
Develop comprehensive team management and motivational skills. Master production planning, scheduling, and resource allocation. Learn to analyze production data to identify trends and implement continuous improvement initiatives. Build conflict resolution and performance management capabilities. Understand and enforce company policies and safety regulations.
Job Application Toolkit
Ace your application with our purpose-built resources:
Manufacturing Laborer Resume Examples
Proven layouts and keywords hiring managers scan for.
View examplesManufacturing Laborer Cover Letter Examples
Personalizable templates that showcase your impact.
View examplesTop Manufacturing Laborer Interview Questions
Practice with the questions asked most often.
View examplesManufacturing Laborer Job Description Template
Ready-to-use JD for recruiters and hiring teams.
View examplesGlobal Manufacturing Laborer Opportunities
A Manufacturing Laborer's role is globally consistent, focusing on manual tasks within production lines across diverse industries. International demand remains stable, particularly in countries with robust manufacturing sectors like Germany, China, and Mexico. Regulatory differences primarily involve safety standards and labor laws. Professionals seek international opportunities for better wages or specific industry exposure. No universal international certifications exist; local vocational training and experience are key.
Global Salaries
Manufacturing Laborer salaries vary significantly worldwide, reflecting local economic conditions and cost of living. In North America, a laborer in the United States might earn $30,000 - $45,000 USD annually, while in Canada, it ranges from $28,000 - $40,000 CAD (approximately $20,000 - $30,000 USD). European wages differ widely; in Germany, a laborer could expect €25,000 - €35,000 (around $27,000 - $38,000 USD), whereas in Poland, it might be PLN 36,000 - PLN 50,000 (about $9,000 - $12,500 USD).
Asia-Pacific markets present a broad spectrum. In Australia, salaries range from AUD 50,000 - AUD 65,000 ($33,000 - $43,000 USD). In contrast, China's manufacturing laborers earn significantly less, typically RMB 40,000 - RMB 60,000 ($5,500 - $8,500 USD) in industrial zones, though purchasing power differs. Latin American countries like Mexico offer MXN 80,000 - MXN 120,000 ($4,500 - $7,000 USD).
Salary structures often include benefits like health insurance and retirement plans, which vary by country. For instance, European countries often have more comprehensive social security contributions impacting take-home pay. Experience and specific skill sets, like operating specialized machinery, can increase compensation globally. Education credential recognition is less critical than practical experience for this role.
Remote Work
International remote work for a Manufacturing Laborer is generally not feasible. This role requires physical presence on a factory floor, operating machinery, assembling products, or moving materials. The core tasks are hands-on and location-dependent.
Digital nomad opportunities or countries with favorable remote work policies do not apply to this profession due to its physical nature. Employers in manufacturing rarely offer international remote work arrangements for production roles. There are no known platforms or companies hiring internationally for remote manufacturing laborer positions.
Salary expectations for this role are tied to the physical location of the factory. Geographic arbitrage is not possible for a manufacturing laborer. Equipment needs involve industrial tools and machinery, which are only available on-site. Internet requirements are minimal for the job itself, but essential for communication with on-site management.
Visa & Immigration
For a Manufacturing Laborer, common visa categories include skilled worker visas or temporary work permits, often tied to specific employer sponsorships. Popular destination countries for manufacturing roles include Germany, Canada, Australia, and parts of the United States. Each country has specific requirements as of 2025.
Germany's 'Skilled Immigration Act' facilitates entry for workers with recognized vocational qualifications, often requiring German language proficiency. Canada's Express Entry system or Provincial Nominee Programs may offer pathways, but typically prioritize higher-skilled trades. Australia's skilled migration program occasionally lists manufacturing roles, requiring skills assessments and English language tests.
Education credential recognition is less stringent for this role than for professional occupations; practical experience and vocational training are more critical. Visa timelines vary from a few months to over a year, depending on the country and visa type. Permanent residency pathways are possible after several years of continuous employment and meeting specific criteria. Family visas for dependents are usually available once the primary applicant secures a work visa.
2025 Market Reality for Manufacturing Laborers
Understanding current market realities for manufacturing laborers is crucial for effective career planning. The sector has undergone significant shifts in recent years, driven by post-pandemic reshoring efforts and accelerated automation.
Broader economic factors, including inflation and supply chain stability, directly influence production levels and, consequently, hiring needs. Market realities can vary significantly based on the specific industry (e.g., automotive vs. food processing), regional industrial density, and the size of manufacturing facilities. This analysis provides an honest assessment of current conditions.
Current Challenges
Manufacturing laborers face increased competition for entry-level roles, partly due to automation handling more repetitive tasks. Economic uncertainty can lead to production slowdowns, reducing the need for temporary or new hires. Additionally, a mismatch between available basic skills and the growing demand for tech-literacy in modern factories presents a hurdle. Job searches can extend several weeks in some regions.
Growth Opportunities
Despite automation, strong demand persists for manufacturing laborers in sectors undergoing expansion, like electric vehicle component production, advanced materials, and medical device manufacturing. These areas often seek individuals capable of adapting to new processes and technologies.
Emerging opportunities exist for laborers willing to cross-train on basic machine operation, quality control software, or inventory management systems. Acquiring certifications in lean manufacturing or safety protocols can significantly enhance a candidate's appeal. Underserved markets, particularly in rural areas near new factory constructions, can offer better entry points.
Laborers who demonstrate reliability, a strong work ethic, and a proactive attitude toward learning new skills hold a competitive advantage. The current market rewards those who view their role as evolving alongside technology. Investing in foundational technical skills, even through short courses, positions individuals for more stable and higher-paying roles within the manufacturing ecosystem.
Current Market Trends
Demand for manufacturing laborers remains steady in 2025, though with shifts in required skills. While foundational tasks still require human input, factories increasingly integrate automation and AI, impacting the nature of entry-level work. This means roles are evolving from purely manual labor to positions requiring more oversight of machinery and basic troubleshooting capabilities.
Economic conditions, particularly supply chain stability and consumer demand for goods, directly influence hiring. Some sectors, like automotive and electronics manufacturing, show consistent need, while others tied to discretionary spending might see fluctuations. Employers increasingly seek candidates with basic digital literacy or a willingness to learn new technologies, even for entry-level floor positions.
Salary trends for manufacturing laborers show modest growth, often tied to regional cost of living and the specific industry. Areas with strong industrial bases, such as the Midwest and parts of the Southeast, offer more consistent opportunities. Remote work is not applicable to this role, making geographic location a primary factor. Seasonal peaks, especially before major retail holidays, can temporarily boost hiring in certain product categories.
Emerging Specializations
The manufacturing landscape is undergoing a profound transformation, driven by advancements in automation, artificial intelligence, and sustainable practices. These technological shifts are not eliminating the need for human labor but rather redefining it, creating new, specialized roles that demand evolving skill sets. Understanding these emerging areas and positioning oneself early is crucial for career advancement in 2025 and beyond.
Early adoption of these specialized skills allows laborers to transition from traditional manual tasks to more complex, value-added roles. This often leads to premium compensation and accelerated career growth, as demand for these next-generation capabilities outpaces supply. While established specializations remain vital, focusing on cutting-edge areas provides a strategic advantage for long-term career resilience and opportunity.
Many emerging areas, particularly those involving advanced robotics or data integration, are currently in a rapid growth phase. They are poised to become mainstream within the next three to five years, creating a significant number of job opportunities. While specializing in new areas carries an inherent risk due to their evolving nature, the potential for substantial rewards in terms of career progression and earning potential often outweighs this uncertainty for proactive professionals.
Robotics Operations & Basic Maintenance Technician
As factories integrate more complex robotic systems, a critical need arises for laborers who can not only operate but also perform basic diagnostics and routine maintenance on these machines. This specialization moves beyond simple button-pushing to understanding robotic movements, sensor data, and basic troubleshooting. It ensures smooth operation and minimizes downtime, which is vital for production efficiency.
Production Data Monitoring Specialist
The rise of the Industrial Internet of Things (IIoT) means that every piece of equipment in a modern factory generates data. Manufacturing laborers specializing in production data monitoring learn to interpret these data streams to identify inefficiencies, predict equipment failures, and optimize workflow. This role shifts focus from purely physical tasks to analytical oversight, using real-time information to improve manufacturing processes.
Sustainable Manufacturing Support
With increasing emphasis on environmental responsibility and resource efficiency, manufacturers are adopting more sustainable production methods. A specialization in sustainable manufacturing support involves understanding and implementing practices like waste reduction, energy conservation, and responsible material handling. This role contributes directly to a company's green initiatives and operational cost savings.
Additive Manufacturing Operator
Additive manufacturing, commonly known as 3D printing, is transforming prototyping and small-batch production. Laborers specializing in additive manufacturing operations manage and operate 3D printers, prepare materials, and perform post-processing tasks. This requires precision and an understanding of different printing technologies and materials, moving beyond traditional subtractive manufacturing processes.
Automated Quality Assurance Technician
Advanced quality control now often involves using sophisticated vision systems, laser scanners, and automated inspection tools. A specialization in advanced quality assurance involves operating and calibrating these tools, interpreting their outputs, and ensuring products meet precise specifications. This moves beyond manual inspection to leveraging technology for higher accuracy and consistency in quality checks.
Pros & Cons of Being a Manufacturing Laborer
Making an informed career choice requires understanding both the positive and challenging aspects of a profession. The experience of a manufacturing laborer, for instance, can vary significantly based on the specific industry, company culture, and the level of automation present in the workplace. Some aspects might be considered advantages by one individual and disadvantages by another, depending on personal values and lifestyle preferences. Additionally, the daily realities and potential for growth may evolve at different career stages. This assessment provides an honest, balanced view to help set realistic expectations for anyone considering this demanding yet vital role.
Pros
Accessible entry-level position with minimal formal education requirements, making it a viable option for individuals looking to enter the workforce quickly.
Hands-on work provides a tangible sense of accomplishment, as laborers directly contribute to the creation of physical products from raw materials.
Skill development in areas like operating machinery, understanding production processes, and adhering to strict quality control standards is continuous on the job.
Steady employment is often available, as manufacturing remains a foundational sector, providing consistent work for those willing to perform manual tasks.
Teamwork and camaraderie are strong, as laborers often work closely with colleagues on production lines, fostering a supportive and collaborative environment.
Opportunities for overtime often exist, allowing individuals to significantly increase their earning potential, especially during peak production periods.
Cons
Physical demands can be significant, leading to fatigue or strain, especially with repetitive tasks or heavy lifting required throughout a shift.
Exposure to hazardous conditions is common, including loud noise, dust, chemicals, or moving machinery, which necessitates strict adherence to safety protocols.
Repetitive tasks can lead to monotony and a lack of intellectual stimulation for some, as the work often involves performing the same actions repeatedly.
Limited career progression opportunities exist within the laborer role itself; advancement typically requires additional training, certifications, or moving into supervisory or specialized technical roles.
Shift work and irregular hours are frequent, as manufacturing plants often operate 24/7, which can disrupt personal life and social schedules.
Job security can be sensitive to economic downturns or automation trends, as manufacturing output fluctuates with demand and technology increasingly replaces manual tasks.
Frequently Asked Questions
Manufacturing Laborers face distinct questions around physical demands, safety, and pathways into steady work without extensive prior experience. This section addresses the most common concerns about entry requirements, daily tasks, and career progression in this hands-on field.
What educational background or certifications do I need to become a Manufacturing Laborer?
Most manufacturing laborer positions do not require a specific degree. A high school diploma or GED is typically sufficient. Employers prioritize a strong work ethic, reliability, and the ability to follow instructions and safety protocols. Some roles might benefit from vocational training in specific industrial processes, but on-the-job training is common.
What does a typical day look like for a Manufacturing Laborer, and what are the physical demands?
Daily tasks for a manufacturing laborer often involve operating basic machinery, assembling components, moving materials, and performing quality checks. You will likely spend significant time on your feet, lifting, bending, and performing repetitive motions. The work environment varies, but it usually involves noise, and potentially dust or specific temperatures, requiring adherence to safety guidelines.
How long does it take to get hired and become proficient as a Manufacturing Laborer without prior experience?
The timeline to become job-ready is relatively short. Many entry-level positions require minimal prior experience, with new hires receiving on-the-job training that can last from a few days to a few weeks. If you possess basic mechanical aptitude and a willingness to learn, you can often secure a position and begin working within a month of applying.
What are the typical salary expectations for an entry-level Manufacturing Laborer, and how does it increase with experience?
Starting salaries for manufacturing laborers can range from minimum wage to around $18-$20 per hour, depending on the industry, location, and specific company. With experience, specialized skills, or certifications (like forklift operation), your earning potential can increase. Overtime opportunities are often available and can significantly boost your income.
What is the work-life balance like for a Manufacturing Laborer, considering typical shift patterns?
Work-life balance for manufacturing laborers often involves shift work, which can include evenings, nights, or weekends, depending on the plant's operational hours. While this provides flexibility for some, it requires careful planning for personal life. Many companies offer stable schedules, but be prepared for potential overtime, especially during peak production periods.
Is the Manufacturing Laborer role secure, or is it at high risk due to automation?
Job security for manufacturing laborers is generally stable, particularly in essential industries or those with high demand for goods. Automation is changing some aspects, but many roles still require human dexterity and problem-solving. Consistent performance, reliability, and a willingness to adapt to new technologies can enhance your job security.
What are the opportunities for career advancement or specialization from a Manufacturing Laborer role?
There are several paths for career growth. You can specialize in operating specific machinery, move into quality control, or become a team lead or supervisor. Further training in areas like maintenance, welding, or advanced manufacturing technologies can also open doors to higher-paying, more skilled positions within the plant or industry.
Related Careers
Explore similar roles that might align with your interests and skills:
Assembly Worker
A growing field with similar skill requirements and career progression opportunities.
Explore career guideFactory Worker
A growing field with similar skill requirements and career progression opportunities.
Explore career guideManufacturing Operator
A growing field with similar skill requirements and career progression opportunities.
Explore career guideProduction Operator
A growing field with similar skill requirements and career progression opportunities.
Explore career guideProduction Worker
A growing field with similar skill requirements and career progression opportunities.
Explore career guideAssess your Manufacturing Laborer readiness
Understanding where you stand today is the first step toward your career goals. Our Career Coach helps identify skill gaps and create personalized plans.
Skills Gap Analysis
Get a detailed assessment of your current skills versus Manufacturing Laborer requirements. Our AI Career Coach identifies specific areas for improvement with personalized recommendations.
See your skills gapCareer Readiness Assessment
Evaluate your overall readiness for Manufacturing Laborer roles with our AI Career Coach. Receive personalized recommendations for education, projects, and experience to boost your competitiveness.
Assess your readinessSimple pricing, powerful features
Upgrade to Himalayas Plus and turbocharge your job search.
Himalayas
Himalayas Plus
Himalayas Max
Find your dream job
Sign up now and join over 100,000 remote workers who receive personalized job alerts, curated job matches, and more for free!
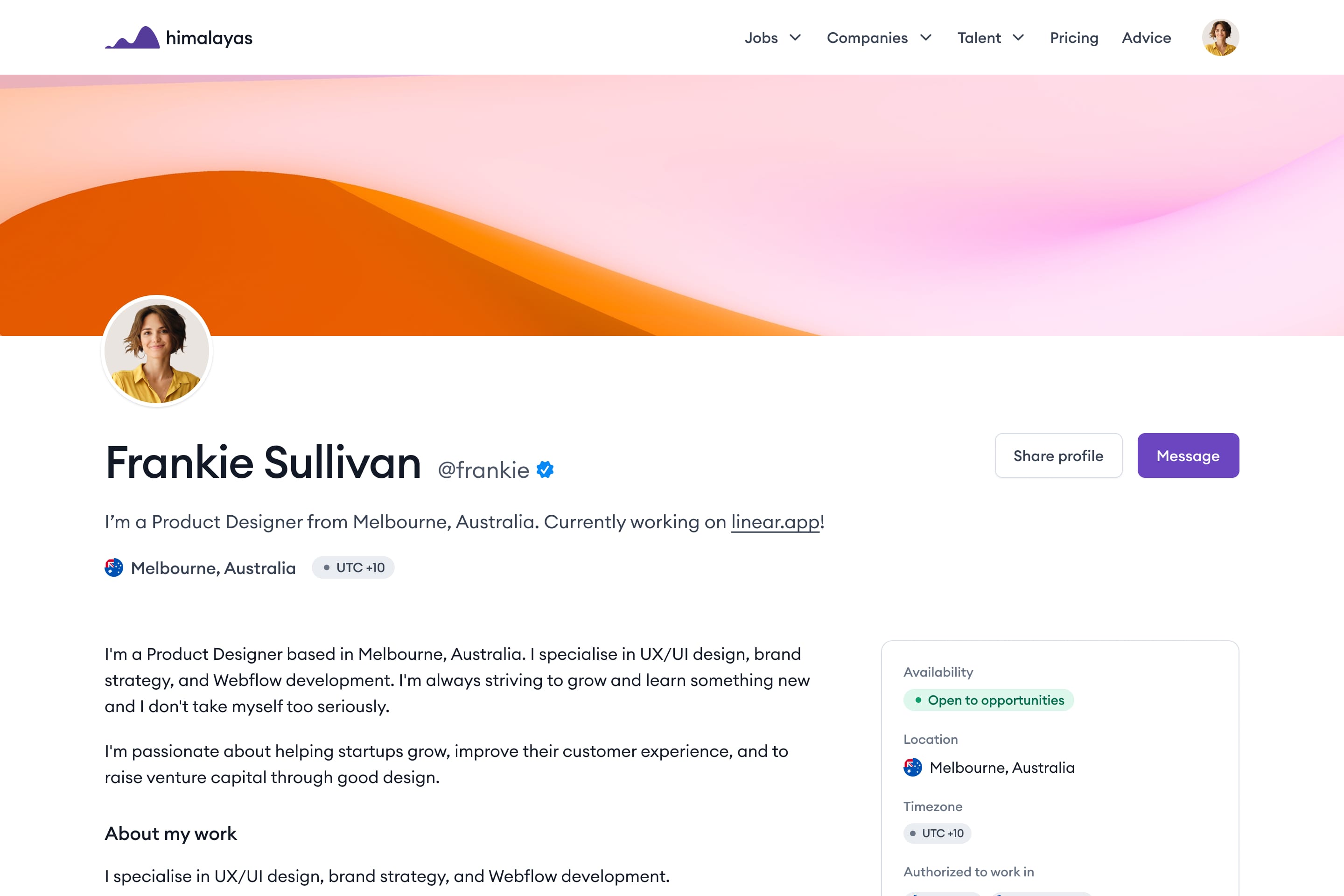