Complete Production Worker Career Guide
Production workers are the backbone of the manufacturing sector, transforming raw materials into finished goods that power economies and everyday life. This hands-on role requires precision, efficiency, and a commitment to quality, offering a direct path to contributing tangible products. You will operate machinery, monitor processes, and ensure products meet rigorous standards, making this a vital and steady career with opportunities for skill development.
Key Facts & Statistics
Median Salary
$38,810 USD
(U.S. national median, BLS, May 2023)
Range: $29k - $55k+ USD
Growth Outlook
1%
as fast as average (BLS, 2022-2032)
Annual Openings
≈170k
openings annually (BLS, 2022-2032)
Top Industries
Typical Education
High school diploma or equivalent, with on-the-job training common; certifications can enhance prospects
What is a Production Worker?
A Production Worker is a frontline manufacturing professional responsible for the hands-on assembly, operation, and quality control of goods within a factory or plant. They are integral to the manufacturing process, ensuring products are made efficiently, correctly, and to specific standards. Their primary focus is on the physical creation and preparation of products for distribution.
This role differs from a Machine Operator, who specializes in running complex, often automated, machinery, and a Quality Control Inspector, who focuses solely on post-production inspection. Production workers often perform a broader range of tasks, including manual assembly, basic machine tending, packaging, and initial quality checks, making them versatile contributors to the entire production line.
What does a Production Worker do?
Key Responsibilities
- Operate and monitor production machinery and equipment according to established procedures and safety guidelines.
- Assemble components or products on an assembly line, ensuring proper fit and adherence to quality standards.
- Inspect finished products for defects, discrepancies, or deviations from specifications, removing non-conforming items.
- Package and label products accurately, preparing them for shipment or further processing.
- Load and unload materials and products from conveyors, machines, or storage areas, using appropriate lifting techniques.
- Maintain a clean and organized work area, following 5S principles to ensure efficiency and safety.
- Perform routine checks and minor adjustments on equipment, reporting any malfunctions or maintenance needs to supervisors.
Work Environment
Production workers typically operate within a manufacturing plant or factory setting. The environment can vary from climate-controlled assembly areas to more industrial spaces with noise, dust, or specific temperature requirements. The work is often performed standing for long periods, with repetitive motions, and may involve lifting or moving materials.
Collaboration occurs within a team on a production line, with workers coordinating tasks to maintain workflow. Shifts are common, including day, evening, and night, sometimes on a rotating basis. The pace of work is generally steady and driven by production targets, requiring focus and attention to detail. Overtime may be necessary to meet demand, but remote work is not possible for this hands-on role.
Tools & Technologies
Production workers primarily use a variety of hand tools such as wrenches, screwdrivers, and pliers for assembly and minor adjustments. They also operate specific machinery relevant to the product being manufactured, which might include presses, drills, automated assembly robots, or packaging machines. Depending on the industry, they may use quality control instruments like calipers, micrometers, or visual inspection tools.
For tracking and communication, they often interact with digital displays on machinery, basic human-machine interfaces (HMIs), and sometimes handheld scanners for inventory management. Personal protective equipment (PPE) like safety glasses, gloves, and hearing protection are essential daily tools. While not deeply technical, understanding basic machine operation and following digital work instructions are key.
Production Worker Skills & Qualifications
A Production Worker operates machinery and performs manual tasks on an assembly line or in a manufacturing plant. This role involves meticulous attention to detail, adherence to safety protocols, and efficient execution of repetitive tasks. The qualification landscape for this position prioritizes practical skills and reliability over extensive formal education.
Requirements for production workers vary significantly by industry sector, company size, and the specific products manufactured. In highly regulated industries like pharmaceuticals or aerospace, stringent quality control and documentation skills are paramount. Conversely, in consumer goods manufacturing, speed and efficiency often take precedence. Geographic location can also influence requirements, with some regions having more specialized manufacturing hubs.
Formal education, such as a high school diploma or GED, serves as a foundational requirement for most entry-level production worker roles. However, practical experience gained through vocational training, on-the-job training, or prior manufacturing roles often carries more weight. Certifications in areas like forklift operation, OSHA safety, or specific machinery operation significantly enhance a candidate's value. The skill landscape is evolving with increasing automation; therefore, an aptitude for learning new technologies and basic machine troubleshooting is becoming more valuable. The balance between breadth and depth of skills leans towards depth in specific operational procedures for a given production line.
Education Requirements
Technical Skills
- Machine operation (e.g., assembly, packaging, cutting machines)
- Quality control inspection (visual and basic measurement tools)
- Material handling and inventory management (e.g., using pallet jacks, hand trucks)
- Basic tool usage (e.g., wrenches, screwdrivers, measuring tapes)
- Reading and interpreting work instructions and blueprints
- Adherence to Good Manufacturing Practices (GMP) or Standard Operating Procedures (SOPs)
- Basic troubleshooting of production equipment
- Data entry for production logs and quality checks
- Waste reduction and efficiency principles
Soft Skills
- Attention to detail: Essential for identifying defects, ensuring product quality, and preventing errors on the production line.
- Adherence to safety protocols: Crucial for maintaining a safe work environment and preventing accidents, which is a top priority in manufacturing.
- Teamwork and collaboration: Necessary for coordinating tasks with colleagues, maintaining workflow, and achieving production targets efficiently.
- Physical stamina and endurance: Required to perform repetitive tasks, stand for long periods, and lift materials throughout a shift.
- Problem-solving (basic): Important for identifying minor equipment malfunctions or production bottlenecks and reporting them effectively.
- Adaptability and flexibility: Key for adjusting to changes in production schedules, product specifications, or new equipment.
How to Become a Production Worker
Entering the production worker field typically involves straightforward pathways, often prioritizing hands-on aptitude and reliability over formal degrees. Many roles are entry-level, requiring a high school diploma or equivalent, with companies providing on-the-job training. Some specialized production lines may seek certifications in safety or specific machinery operation, but these are usually acquired post-hire or through short-term vocational programs.
Realistic timelines for securing a production worker role range from a few weeks to a couple of months, depending on local demand and individual preparedness. Geographic location significantly impacts opportunities; manufacturing hubs will have more openings than rural areas. Also, larger corporations may have more structured hiring processes, while smaller businesses might hire more quickly based on immediate needs.
Common misconceptions include believing extensive prior experience is always necessary or that the work is purely manual. Many modern production environments integrate automation, requiring workers to monitor machines, perform quality control, and troubleshoot. Networking through local job fairs, community colleges, or even direct inquiries at factory gates can often bypass traditional online application processes and accelerate job placement.
Step 1
Step 2
Step 3
Step 4
Step 5
Step 6
Education & Training Needed to Become a Production Worker
Becoming a Production Worker primarily involves practical skills and adherence to safety protocols, rather than extensive formal education. Many roles require only a high school diploma or GED. Employers often prioritize candidates with a strong work ethic, reliability, and the ability to follow instructions precisely. While some manufacturing jobs benefit from technical certifications, a Production Worker's daily tasks focus on operating machinery, assembling products, and quality control, which are typically learned on the job.
Formal degree programs are generally not necessary for entry-level Production Worker positions. Instead, vocational training, community college courses in manufacturing technology, or even specific certifications like OSHA safety training are more relevant. These programs can range from a few weeks to two years, costing anywhere from a few hundred dollars for certifications to $5,000-$15,000 for vocational programs. In contrast, on-the-job training, which is common, offers a no-cost entry point, though it might take 3-6 months to become fully proficient. Employers value practical experience and a demonstrated understanding of production processes over academic credentials.
Continuous learning for Production Workers often involves internal company training on new equipment, safety updates, or lean manufacturing principles. Industry-specific certifications, such as those related to specific machinery or quality management systems, can enhance career progression within a manufacturing plant. These typically require short courses, sometimes paid for by employers. The balance between theoretical knowledge and hands-on experience heavily favors practical application in this field. Educational needs vary by the complexity of the manufacturing process; for instance, roles in advanced manufacturing might prefer some technical schooling, while general assembly roles may not.
Production Worker Salary & Outlook
Compensation for a Production Worker varies significantly based on several factors. Geographic location plays a crucial role, with higher wages typically found in areas with a higher cost of living or strong industrial presence, such as the Midwest or Southeastern manufacturing hubs in the United States. International markets also present diverse salary scales, though figures provided here are in USD.
Experience and specialized skills like operating complex machinery or maintaining quality control systems directly impact earning potential. Total compensation often extends beyond base hourly wages to include overtime pay, production bonuses, and shift differentials for evening or weekend work. Comprehensive benefits packages, including health insurance, paid time off, and retirement plans, add substantial value to the overall compensation.
Industry-specific trends, such as automation adoption or supply chain demands, can influence salary growth. Workers with a proven track record of efficiency, safety compliance, and problem-solving skills often command higher pay. Negotiating leverage comes from demonstrating specific, in-demand technical abilities or leadership potential. Remote work opportunities are minimal for this hands-on role, meaning geographic location remains a primary determinant of compensation.
Salary by Experience Level
Level | US Median | US Average |
---|---|---|
Entry-Level Production Worker | $36k USD | $38k USD |
Production Worker | $43k USD | $45k USD |
Senior Production Worker | $50k USD | $52k USD |
Lead Production Worker | $58k USD | $60k USD |
Production Supervisor | $72k USD | $75k USD |
Production Manager | $90k USD | $95k USD |
Market Commentary
The job market for Production Workers shows steady demand, driven by ongoing manufacturing activities across various sectors, including automotive, food processing, and consumer goods. While automation continues to advance, a significant human element remains essential for machine operation, quality assurance, and assembly tasks. The Bureau of Labor Statistics projects stable employment for production occupations, with some areas experiencing growth due to reshoring initiatives and increased domestic manufacturing.
Emerging opportunities for Production Workers include roles in advanced manufacturing facilities that integrate smart technologies, requiring skills in monitoring automated systems and data interpretation. The supply of qualified candidates often balances with demand, though specific regions may experience shortages for specialized roles. Future-proofing involves continuous learning in areas like lean manufacturing principles, robotics interaction, and digital factory tools.
This profession is generally considered stable, though economic downturns can lead to temporary slowdowns in specific industries. Geographic hotspots for Production Workers are concentrated in industrial corridors and regions with established manufacturing infrastructure. Companies increasingly seek adaptable workers who can cross-train on multiple machines and contribute to continuous improvement processes. The reliance on physical presence means remote work is not a significant factor in market trends for this role.
Production Worker Career Path
Career progression for a Production Worker typically involves a ladder of increasing responsibility, specialization, and leadership within manufacturing or assembly environments. Individuals often start in entry-level roles, mastering specific tasks before moving to more complex operations.
Advancement speed depends heavily on individual performance, a willingness to learn new machinery and processes, and the company's size and industry. Larger corporations might offer more structured pathways and specialized training, while smaller firms could provide broader exposure and faster upward mobility for highly adaptable individuals. Specialization in particular machinery or quality control can create unique advancement opportunities.
Progression often involves a transition from individual contributor roles, focusing on direct production tasks, to supervisory and management positions. These leadership roles require strong communication, problem-solving, and team coordination skills. Networking within the plant and demonstrating reliability are crucial for moving into supervisory roles. Continuous learning, often through internal training or certifications in lean manufacturing or safety, marks significant progression milestones.
Entry-Level Production Worker
0-1 yearKey Focus Areas
Production Worker
1-3 yearsKey Focus Areas
Senior Production Worker
3-5 yearsKey Focus Areas
Lead Production Worker
5-8 yearsKey Focus Areas
Production Supervisor
8-12 yearsKey Focus Areas
Production Manager
12+ yearsKey Focus Areas
Entry-Level Production Worker
0-1 yearPerforms routine tasks on the production line, such as assembling components, packaging products, or operating entry-level machinery under direct supervision. Follows standard operating procedures and contributes to daily output targets. Works as part of a team, with minimal decision-making authority.
Key Focus Areas
Mastering basic production tasks, understanding safety protocols, and developing proficiency with initial machinery. Focus on attention to detail, following instructions, and consistently meeting production quotas. Learning about material handling and basic quality checks is important.
Production Worker
1-3 yearsOperates various pieces of production equipment, performs quality control checks, and assists with machine setup or minor adjustments. Works with moderate supervision and contributes to optimizing line efficiency. May train new entry-level workers on specific tasks and troubleshoot basic problems.
Key Focus Areas
Improving efficiency and speed in assigned tasks, understanding the workflow of the entire production line, and identifying minor operational issues. Developing problem-solving skills for common production challenges and enhancing machine operation proficiency. Cross-training on different stations is beneficial.
Senior Production Worker
3-5 yearsHandles more complex production tasks, operates specialized machinery, and performs advanced quality assurance. Provides guidance and informal training to less experienced workers. Identifies and resolves production bottlenecks, suggesting improvements to processes. Works with minimal supervision and contributes to continuous improvement initiatives.
Key Focus Areas
Becoming proficient in complex machinery operation and troubleshooting. Focusing on process improvement, reducing waste, and maintaining high quality standards. Developing mentorship skills and a deeper understanding of production metrics and goals. Participation in safety committees is common.
Lead Production Worker
5-8 yearsLeads a small team of production workers on a specific line or shift, assigning tasks, monitoring progress, and ensuring production targets are met. Acts as the primary point of contact for operational issues and provides on-the-job training. Reports directly to a supervisor, often making real-time adjustments to maintain flow.
Key Focus Areas
Developing strong leadership and communication skills, understanding production scheduling, and coordinating team activities effectively. Focusing on motivating team members, resolving interpersonal conflicts, and ensuring adherence to safety and quality standards. Learning about inventory management and supply chain basics is key.
Production Supervisor
8-12 yearsManages a section of the production floor, overseeing multiple teams or lines. Responsible for staff scheduling, performance management, and ensuring production goals are achieved efficiently and safely. Troubleshoots major operational issues, implements process improvements, and collaborates with other departments like maintenance and quality control.
Key Focus Areas
Mastering team management, performance evaluation, and conflict resolution. Focusing on optimizing production schedules, implementing lean manufacturing principles, and ensuring compliance with all regulations. Developing strong analytical skills to interpret production data and make informed decisions. Budgeting awareness begins here.
Production Manager
12+ yearsOversees the entire production operation, including planning, directing, and coordinating all manufacturing activities. Responsible for meeting overall production targets, managing budgets, and implementing strategic initiatives to improve efficiency, quality, and cost-effectiveness. Leads supervisory staff and collaborates with senior management on organizational goals.
Key Focus Areas
Developing strategic planning, financial management, and cross-departmental collaboration skills. Focusing on long-term production forecasting, budget management, and implementing large-scale operational changes. Cultivating strong leadership presence and decision-making capabilities in a fast-paced environment. Industry certifications in operations management are highly valued.
Job Application Toolkit
Ace your application with our purpose-built resources:
Production Worker Cover Letter Examples
Personalizable templates that showcase your impact.
View examplesProduction Worker Job Description Template
Ready-to-use JD for recruiters and hiring teams.
View examplesGlobal Production Worker Opportunities
Production workers are essential globally, operating machinery and assembling products across diverse manufacturing sectors. Demand remains steady in industrialized nations and emerging economies, particularly in automotive, electronics, and food processing. Regulatory differences impact safety standards and labor laws internationally. Many production workers consider international roles for better wages or living conditions. No specific international certifications exist; local vocational training and experience are key.
Global Salaries
Salaries for production workers vary significantly by region and industry. In North America, entry-level production workers earn between $30,000 and $45,000 USD annually in countries like the USA and Canada. Experienced workers can reach $55,000 USD. This covers basic living expenses but offers limited discretionary income in major cities.
European salaries range from €20,000 to €40,000 (approximately $21,500-$43,000 USD) in Western European countries like Germany and France. Eastern European nations, such as Poland or Czechia, offer lower ranges, often €10,000 to €20,000 ($10,750-$21,500 USD). Purchasing power parity means lower nominal salaries in Eastern Europe can still provide a decent local living standard.
In Asia-Pacific, Japan and South Korea offer ¥3,000,000-¥5,000,000 (approximately $20,000-$33,500 USD) and ₩30,000,000-₩45,000,000 (approximately $22,000-$33,000 USD) respectively. These salaries are often adjusted for high costs of living in urban centers. Latin American countries like Mexico might offer $8,000-$15,000 USD annually, but with a much lower cost of living.
Salary structures also differ. European countries often include robust social benefits, healthcare, and generous vacation time, which might not be reflected in the base salary. North America might see more performance-based bonuses. Tax implications vary; some countries have higher income taxes but offer more social services, impacting net take-home pay. International experience generally improves compensation, but specific education credentials often matter less than practical skills and certifications like forklift operation or machine maintenance.
Remote Work
International remote work opportunities for production workers are extremely limited. This role is inherently hands-on and requires physical presence on a factory floor or production line. It involves operating machinery, assembling products, and performing quality control tasks that cannot be done off-site.
Digital nomad lifestyles are not applicable to this profession. No companies hire production workers for remote international roles. Salary expectations are tied directly to the local labor market where the physical work occurs.
Practical considerations like equipment, internet, or workspace setup are irrelevant for this role in a remote context. Production workers must be physically present at the work site with the necessary machinery and tools provided by the employer. This profession does not lend itself to geographic arbitrage or international team collaboration in a remote capacity.
Visa & Immigration
Common visa categories for production workers typically fall under skilled or semi-skilled worker programs. Countries with strong manufacturing sectors, like Germany, Canada, and Australia, often have pathways. Requirements usually include a job offer, proof of relevant experience, and sometimes vocational training or specific certifications.
In 2025, Canada's Express Entry system or Provincial Nominee Programs (PNPs) may consider certain production roles if they are in demand. Germany offers skilled worker visas, often requiring recognized vocational qualifications. Australia uses a points-based system, with some manufacturing roles on its skilled occupation lists.
Education credential recognition is less critical than practical skills; however, some countries may require specific trade tests. Visa timelines vary from a few months to over a year. Language requirements are common, particularly for integration; for example, German for Germany or English for Canada/Australia. Pathways to permanent residency exist in many countries after several years of continuous employment and tax contributions.
Family visas are generally possible for spouses and dependent children once the primary applicant secures a work visa. There are no fast-track programs specific to production workers. Applicants should research specific national labor shortages and employer sponsorship options. Some countries may have specific labor agreements for certain industries that could benefit production workers.
2025 Market Reality for Production Workers
Understanding current market conditions is vital for production workers to navigate evolving industry demands. The landscape has shifted significantly between 2023 and 2025, influenced by post-pandemic supply chain adjustments and the accelerating integration of automation and AI. Broader economic factors directly impact manufacturing output and, consequently, job availability.
Market realities vary based on experience level, with skilled machine operators often finding more stable opportunities than entry-level manual laborers. Geographic location, particularly proximity to manufacturing plants, and the size of the company also play a crucial role in job prospects. This analysis provides an honest assessment of current hiring trends and realities in the production worker field.
Current Challenges
Competition for production worker roles remains high, particularly for entry-level positions, as automation increases output expectations per worker. Economic uncertainty leads some manufacturers to delay expansion, limiting new job creation. Skill gaps exist in operating advanced machinery, posing a challenge for those with only basic manual experience.
Growth Opportunities
Despite challenges, strong demand exists for production workers skilled in operating and maintaining advanced machinery. Roles in quality control, machine tending, and basic robotics operation are experiencing growth. Specializations in niche manufacturing, such as aerospace parts or medical devices, also offer more stable employment.
Professionals can gain an advantage by pursuing certifications in industrial automation, lean manufacturing, or specific machine operation. Underserved markets might include regions with new factory investments or smaller, specialized manufacturers seeking reliable, multi-skilled employees. Cross-training in maintenance or quality assurance provides a significant competitive edge.
Market corrections can create opportunities as companies streamline operations, increasing the value of efficient, adaptable workers. Sectors like renewable energy component manufacturing and advanced materials production remain robust. Investing in short-term technical courses or apprenticeships can align skills with current industry needs, improving job prospects and career trajectory.
Current Market Trends
Hiring for production workers shows steady, but not explosive, demand as of 2025. Manufacturers prioritize efficiency, often integrating automation and robotics into production lines. This shifts some manual labor tasks, requiring workers to oversee machinery, monitor quality, and perform maintenance rather than just assembly.
Economic conditions, while stable, still influence production schedules. Some sectors experience growth, such as electric vehicle components and specialized electronics, while others face consolidation. The push for reshoring manufacturing has created some new openings, but these are often balanced by efficiency gains.
Technology trends, particularly generative AI, primarily impact design and planning stages, but automation's influence on the factory floor is significant. Employers increasingly seek workers who can adapt to new digital interfaces and troubleshoot basic machine issues. This means a move away from purely repetitive tasks.
Salary trends for experienced production workers show modest increases, reflecting demand for adaptable skills. Entry-level wages remain competitive due to a larger pool of candidates. Market saturation varies; highly automated plants might have fewer openings but higher skill requirements, while smaller operations might still need more manual roles.
Geographically, opportunities concentrate in manufacturing hubs, such as the Midwest and parts of the Southeast. Remote work is not applicable for this role. Seasonal hiring can occur in industries with peak production cycles, like consumer goods leading up to holidays.
Emerging Specializations
Technological advancements and evolving industry demands are continuously reshaping the landscape for production workers, creating new specialization opportunities. Automation, advanced robotics, and data-driven manufacturing processes are not eliminating jobs but rather transforming them, shifting the focus from manual labor to oversight, programming, and maintenance.
Positioning oneself early in these emerging areas is crucial for career advancement from 2025 onwards. Such foresight allows individuals to gain expertise in high-demand niches, often commanding premium compensation and accelerated career growth compared to traditional production roles.
While established specializations remain vital, the strategic pursuit of cutting-edge areas offers a significant competitive advantage. These emerging fields typically transition from niche to mainstream within five to ten years, creating substantial job opportunities. Understanding this timeline helps professionals balance the risks and rewards of investing in new skill sets.
Specializing in these nascent fields requires a proactive approach to learning and adapting. However, the potential for higher earning potential and greater job security in a rapidly evolving manufacturing environment makes this investment worthwhile. It is about evolving with the industry, not just working within it.
Automated System Operator
Smart Factory Data Monitor
Additive Manufacturing Technician
Automated Quality Control Specialist
Sustainable Production Coordinator
Pros & Cons of Being a Production Worker
Understanding the advantages and challenges of any career is crucial before making a commitment. This is especially true for a Production Worker role, where daily experiences can vary significantly based on the specific industry, company culture, and type of manufacturing process involved. What one person considers a benefit, such as predictable routines, another might find a drawback. Similarly, the physical demands may be manageable for some but challenging for others. Career experiences can also evolve; early-career challenges might lessen with experience, while new ones emerge at senior levels. This assessment provides an honest look at the realistic benefits and genuine difficulties, helping you set appropriate expectations for a career as a Production Worker.
Pros
- Entry-level accessibility means many positions do not require a college degree, making this a viable option for individuals seeking immediate employment.
- Steady employment is often available in industries with consistent demand, providing a reliable income and job stability in many regions.
- Opportunities for acquiring practical skills exist, including operating machinery, quality control, and understanding production processes, which are valuable in various manufacturing settings.
- Structured work environment with clear tasks and responsibilities can provide a sense of routine and predictability for those who prefer consistent daily operations.
- Team-oriented work often involves collaboration with colleagues, fostering camaraderie and a supportive work atmosphere on the production line.
- Tangible output of work provides a sense of accomplishment, as production workers directly contribute to creating physical products that consumers use.
- Overtime opportunities frequently arise, allowing motivated individuals to increase their earning potential significantly, especially during peak production periods.
Cons
- Repetitive tasks can lead to monotony and boredom over long periods, making it difficult to stay engaged with the work.
- Physical demands often involve standing for long hours, lifting heavy objects, and performing repetitive motions, which can lead to fatigue and musculoskeletal issues over time.
- Exposure to noise, dust, chemicals, or extreme temperatures is common in many production environments, potentially posing health risks or requiring specialized protective gear.
- Limited opportunities for upward mobility exist in many production roles, as advancement often requires additional training, certifications, or supervisory experience not always provided.
- Shift work, including nights, weekends, and holidays, is frequently required to maintain continuous production, which can disrupt personal life and social schedules.
- Strict adherence to safety protocols and production quotas is mandatory, creating a high-pressure environment where errors can have significant consequences.
- Job security can be volatile due to automation advancements, economic downturns, or shifts in consumer demand, leading to potential layoffs or factory closures.
Frequently Asked Questions
Production Workers face unique challenges balancing physical demands with attention to detail and safety protocols. This section addresses common questions about entering this role, from required skills and physical stamina to understanding shift work and career progression within manufacturing environments.
What are the basic qualifications needed to become a Production Worker?
Entry-level Production Worker positions typically do not require a college degree. Most employers look for a high school diploma or GED. Essential qualities include reliability, a strong work ethic, the ability to follow instructions precisely, and a commitment to safety. Some roles might require specific certifications, like forklift operation, which employers often provide training for.
How long does it take to become job-ready as a Production Worker?
The time it takes to become job-ready for a Production Worker role is usually short, often just a few weeks of on-the-job training. Most companies provide comprehensive orientation and specific training for their machinery and processes. You can typically start working and earning quickly after being hired, with continuous learning as you gain experience.
What are the typical salary expectations for a Production Worker?
Salaries for Production Workers vary based on industry, location, and experience, but entry-level hourly wages are competitive. Overtime opportunities are common and can significantly boost earnings. Many positions also offer benefits packages, including health insurance and retirement plans, which add to the overall compensation.
What is the work-life balance like for a Production Worker, considering shift schedules?
Work-life balance for Production Workers often involves shift work, including nights, weekends, or rotating schedules, depending on the facility's operational hours. This can affect personal routines, but it also means consistent hours and often set schedules once established. Some roles may offer more traditional daytime hours, so it is important to clarify during the hiring process.
Is the Production Worker role secure, or is it at risk due to automation?
Job security for Production Workers is generally stable, especially in essential manufacturing sectors. Demand for skilled production staff remains consistent as industries require goods to be made. Automation changes some tasks, but it also creates new roles for operating and maintaining advanced machinery, ensuring ongoing opportunities.
What are the career advancement opportunities for a Production Worker?
Production Workers have several avenues for career growth. You can advance to lead positions, quality control roles, or supervisory roles within the production line. Further training in areas like maintenance, machine operation, or specialized manufacturing processes can also open doors to higher-skilled and better-paying technical positions within the company or industry.
What are the main physical demands and safety concerns in this role?
The job involves repetitive tasks and can be physically demanding, requiring standing for long periods, lifting, and operating machinery. Safety is a primary concern, and strict adherence to protocols is essential to prevent injuries. Working in a manufacturing environment also means being exposed to noise, dust, or specific temperatures, depending on the product being made.
Can Production Workers work remotely or have location flexibility?
Remote work is not common for Production Workers because the role requires hands-on involvement with machinery and products on a factory floor. The job is inherently location-dependent, tied to the physical production facility. However, many manufacturing companies have multiple plants, offering potential relocation opportunities if you want to move.
Related Careers
Explore similar roles that might align with your interests and skills:
Factory Worker
A growing field with similar skill requirements and career progression opportunities.
Explore career guideFood Production Worker
A growing field with similar skill requirements and career progression opportunities.
Explore career guideProduction Associate
A growing field with similar skill requirements and career progression opportunities.
Explore career guideProduction Line Worker
A growing field with similar skill requirements and career progression opportunities.
Explore career guideProduction Operator
A growing field with similar skill requirements and career progression opportunities.
Explore career guideAssess your Production Worker readiness
Understanding where you stand today is the first step toward your career goals. Our Career Coach helps identify skill gaps and create personalized plans.
Skills Gap Analysis
Get a detailed assessment of your current skills versus Production Worker requirements. Our AI Career Coach identifies specific areas for improvement with personalized recommendations.
See your skills gapCareer Readiness Assessment
Evaluate your overall readiness for Production Worker roles with our AI Career Coach. Receive personalized recommendations for education, projects, and experience to boost your competitiveness.
Assess your readinessSimple pricing, powerful features
Upgrade to Himalayas Plus and turbocharge your job search.
Himalayas
Himalayas Plus
Himalayas Max
Find your dream job
Sign up now and join over 100,000 remote workers who receive personalized job alerts, curated job matches, and more for free!
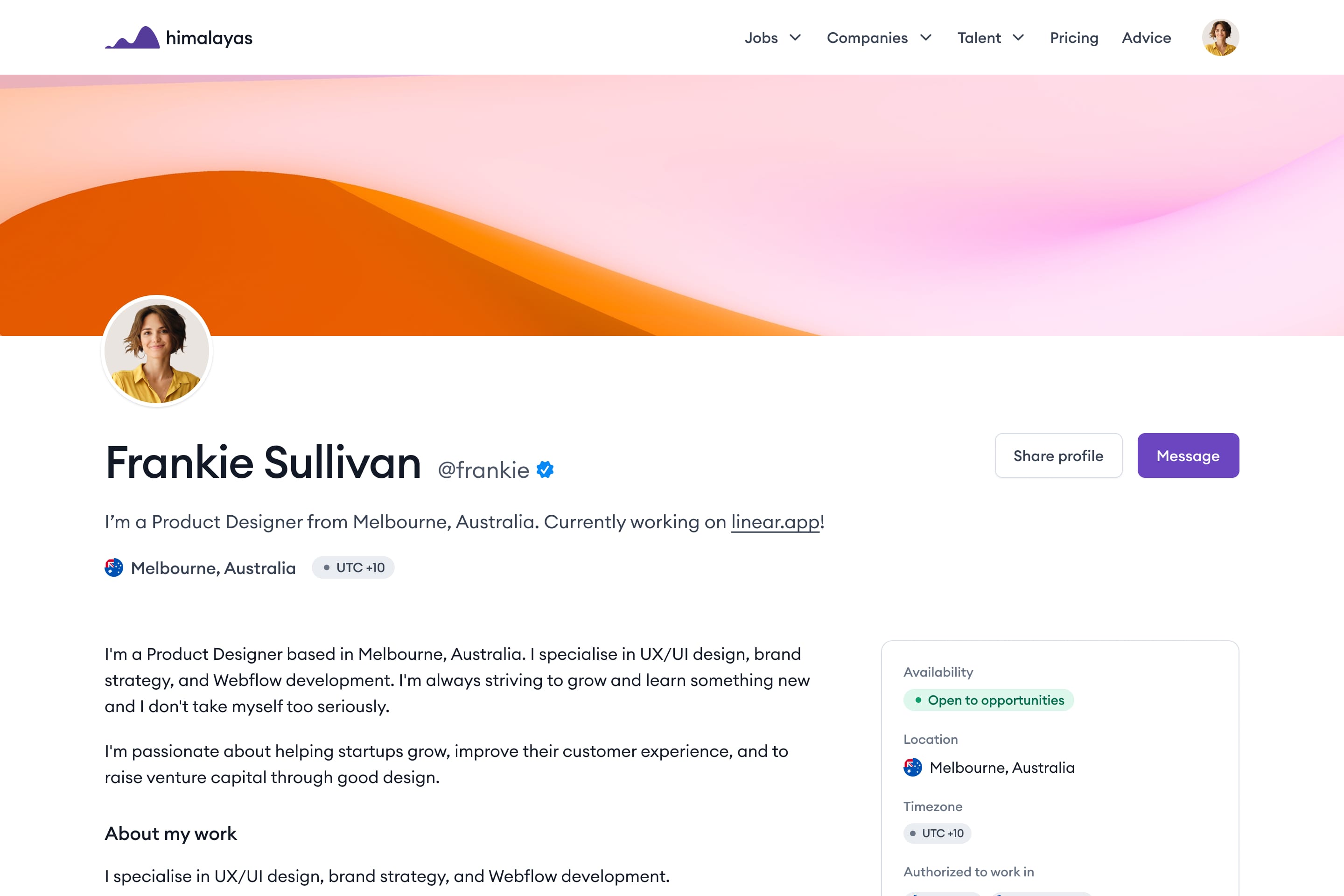