Complete Maintenance Planner Career Guide
Maintenance Planners are the unsung heroes who ensure industrial operations run smoothly, transforming reactive repairs into strategic, scheduled upkeep. They optimize resource allocation and prevent costly downtime, directly impacting a company's bottom line and operational efficiency. This role demands meticulous organization and a keen understanding of mechanical systems, offering a stable and impactful career path in diverse industries.
Key Facts & Statistics
Median Salary
$73,630 USD
(U.S. Bureau of Labor Statistics, May 2023)
Range: $50k - $95k+ USD
Growth Outlook
4%
as fast as average (U.S. Bureau of Labor Statistics, 2022-2032)
Annual Openings
≈30,000
openings annually (U.S. Bureau of Labor Statistics, 2022-2032)
Top Industries
Typical Education
High school diploma or equivalent; associate's degree or vocational training often preferred. Experience in maintenance or a related trade is crucial, and certifications like CMRP (Certified Maintenance and Reliability Professional) enhance prospects.
What is a Maintenance Planner?
A Maintenance Planner is a highly organized professional responsible for optimizing the efficiency and effectiveness of maintenance operations within an organization. They meticulously plan and schedule all necessary resources—labor, materials, tools, and equipment—required to execute maintenance tasks, ranging from routine preventive maintenance to complex repairs and overhauls.
Unlike a Maintenance Supervisor who oversees the execution of work and manages personnel, or a Maintenance Scheduler who focuses solely on the timing of tasks, the Maintenance Planner's core function is to define the 'how' and 'what' of the work. They ensure that when a job is scheduled, all prerequisites are in place, minimizing downtime and maximizing productivity for the maintenance teams.
What does a Maintenance Planner do?
Key Responsibilities
- Develop detailed work plans for maintenance activities, including step-by-step procedures, required labor, materials, and equipment.
- Coordinate with operations, production, and maintenance teams to schedule planned work, minimizing disruption to plant activities.
- Create and maintain a comprehensive catalog of spare parts and critical equipment data, ensuring availability for planned tasks.
- Analyze historical maintenance data and equipment performance to identify trends and improve future planning strategies.
- Generate work orders and requisitions for necessary parts and services, tracking their status from initiation to completion.
- Facilitate pre-job safety briefings and ensure all required permits and safety protocols are integrated into work plans.
- Manage and update the Computerized Maintenance Management System (CMMS) with accurate information on assets, work orders, and maintenance history.
Work Environment
Maintenance Planners typically work in an office setting, often co-located within or near industrial facilities, manufacturing plants, or large institutional campuses. The work environment is collaborative, requiring frequent interaction with maintenance technicians, operations personnel, engineers, and supply chain teams.
While largely desk-bound, the role involves occasional site visits to assess equipment, review job sites, or consult with field teams. The pace of work can be steady with routine planning, but it becomes fast-paced during unexpected breakdowns or critical project deadlines. Most positions follow a standard day shift, but flexibility might be needed to respond to urgent planning needs outside regular hours.
Tools & Technologies
Maintenance Planners heavily rely on Computerized Maintenance Management Systems (CMMS) such as SAP PM, Maximo, Oracle EAM, or Infor EAM for managing work orders, asset data, and scheduling. They also use Enterprise Resource Planning (ERP) systems like SAP or Oracle for procurement and inventory management.
Standard office productivity suites, including Microsoft Excel, Word, and PowerPoint, are essential for reporting, documentation, and presentations. Communication and collaboration tools like Microsoft Teams or Slack facilitate coordination with various departments. Some roles might also involve basic Geographic Information Systems (GIS) for facility mapping or specialized scheduling software for complex projects.
Maintenance Planner Skills & Qualifications
Maintenance planners play a crucial role in optimizing asset performance and operational efficiency. Their qualifications are a blend of technical knowledge, practical experience, and organizational acumen. Entry-level positions may prioritize strong foundational technical skills and a basic understanding of planning software, while senior roles demand extensive experience in complex environments, advanced analytics, and strategic foresight.
Requirements for maintenance planners vary significantly by industry. For instance, a planner in a manufacturing plant needs expertise in specific production machinery, while one in a utility company focuses on infrastructure and regulatory compliance. Company size also impacts requirements; smaller organizations might seek a more hands-on planner, whereas larger enterprises often look for specialists in areas like reliability-centered maintenance or predictive planning. Geographical location can influence specific certifications or safety regulations, particularly in highly regulated sectors.
Formal education, such as an associate's or bachelor's degree in engineering or a related technical field, provides a strong theoretical foundation. However, practical experience, often gained through a background as a skilled tradesperson (e.g., electrician, mechanic), is equally, if not more, valued. Many successful planners transition from maintenance technician roles, bringing invaluable real-world understanding of equipment and processes. Certifications like CMRP (Certified Maintenance and Reliability Professional) or CRL (Certified Reliability Leader) significantly enhance a candidate's profile, demonstrating a commitment to best practices and advanced methodologies. The field is evolving with the rise of IoT and AI, requiring planners to develop skills in data analysis and digital tools to leverage predictive maintenance technologies effectively.
Education Requirements
Technical Skills
- Computerized Maintenance Management System (CMMS) proficiency (e.g., SAP PM, Maximo, Infor EAM, UpKeep)
- Work order management and scheduling principles
- Maintenance Key Performance Indicator (KPI) tracking and reporting
- Spare parts management and inventory control
- Bill of Materials (BOM) creation and management
- Root Cause Analysis (RCA) and Failure Mode and Effects Analysis (FMEA)
- Preventive and predictive maintenance strategies (e.g., vibration analysis, thermography, oil analysis data interpretation)
- Microsoft Excel for data analysis and reporting (advanced functions, pivot tables)
- Basic understanding of mechanical, electrical, and hydraulic systems
- Project management fundamentals (e.g., Gantt charts, critical path method)
- Safety regulations and lockout/tagout procedures (OSHA, industry-specific standards)
- Technical documentation and blueprint reading
Soft Skills
- Organizational skills: Maintenance planners manage multiple tasks, schedules, and resources simultaneously. Strong organization ensures that all components of a maintenance plan are tracked, prioritized, and executed efficiently, preventing delays and optimizing resource allocation.
- Attention to detail: Precise planning requires meticulous attention to every component of a job, including parts, tools, safety procedures, and estimated labor hours. Overlooking small details can lead to significant operational disruptions or safety hazards.
- Problem-solving skills: Planners frequently encounter unexpected issues, such as equipment failures or resource constraints. The ability to quickly analyze problems, identify root causes, and develop effective solutions is critical for minimizing downtime and maintaining productivity.
- Communication skills: Effective communication with maintenance technicians, operations personnel, vendors, and management is essential. Planners must clearly convey job scopes, material requirements, and schedule changes to ensure everyone understands their roles and responsibilities.
- Adaptability: Maintenance environments are dynamic, with priorities shifting due to emergent breakdowns or changes in production schedules. Planners must adapt quickly to new information, revise plans, and reallocate resources to maintain operational flow.
- Time management: Efficiently planning and scheduling maintenance tasks within tight deadlines is a core responsibility. Planners must prioritize urgent tasks, allocate appropriate time, and manage their own workload to ensure timely completion of critical planning activities.
- Negotiation skills: Planners often negotiate with suppliers for parts delivery times or with internal departments for equipment availability. The ability to negotiate effectively ensures timely access to necessary resources and minimizes conflicts.
- Proactive thinking: Identifying potential issues before they become problems, such as anticipating spare part needs or potential equipment failures, is vital for preventing costly downtime. Planners must think ahead to build resilience into maintenance schedules and strategies
How to Become a Maintenance Planner
Breaking into a Maintenance Planner role involves diverse pathways, from hands-on trades experience to formal engineering or supply chain education. While some roles prefer a degree, many value practical experience in maintenance, operations, or inventory management. The timeline to secure a first role varies; a skilled tradesperson with a few years of experience might transition in 3-6 months, whereas someone new to the industrial environment might need 1-2 years to build foundational knowledge and gain relevant certifications.
Entry strategies differ by industry and company size. Large manufacturing plants or utilities often seek candidates with a blend of technical understanding and strong organizational skills. Smaller companies might prioritize someone with a broad understanding of various equipment types. Misconceptions include believing one needs to be a certified engineer; often, strong problem-solving abilities and a methodical approach are more critical. Networking within industrial associations or local manufacturing groups can provide invaluable insights and connections.
The hiring landscape increasingly emphasizes analytical skills and familiarity with Computerized Maintenance Management Systems (CMMS). Companies look for individuals who can optimize workflows, reduce downtime, and manage resources efficiently. Overcoming barriers like a lack of direct planning experience often involves highlighting transferable skills from previous roles, such as project coordination, data analysis, or inventory control, combined with targeted training in maintenance planning principles.
Step 1
Step 2
Step 3
Step 4
Step 5
Step 6
Step 7
Education & Training Needed to Become a Maintenance Planner
The educational landscape for a Maintenance Planner emphasizes practical skills and operational knowledge over traditional academic degrees. While a bachelor's degree in industrial engineering, supply chain management, or a related technical field can provide a strong theoretical foundation, many successful planners come from vocational training programs or have extensive on-the-job experience. Formal degrees typically cost $40,000-$100,000+ and take four years, offering a broad understanding of industrial operations. In contrast, specialized certifications and short courses, ranging from $1,000-$5,000, can be completed in weeks to a few months, focusing directly on maintenance planning software, scheduling techniques, and spare parts management.
Employers often value practical experience and industry-specific certifications from organizations like SMRP or ASQ highly. These credentials demonstrate a focused skill set directly applicable to the role. Continuous learning remains crucial; planners must stay updated on new CMMS (Computerized Maintenance Management Systems) technologies, lean manufacturing principles, and predictive maintenance tools. The blend of theoretical knowledge from degrees and practical application from certifications and experience creates a well-rounded professional.
The specific educational needs for a Maintenance Planner can vary significantly by industry. For instance, a planner in a highly regulated pharmaceutical plant may benefit more from a degree in a relevant engineering discipline, while one in a general manufacturing facility might find a vocational background and specific CMMS training more beneficial. The cost-benefit analysis often favors targeted certifications and continuous professional development, as they offer a quicker return on investment and direct career progression. Quality programs often emphasize hands-on simulation and case studies to bridge the gap between theory and practical application.
Maintenance Planner Salary & Outlook
Compensation for a Maintenance Planner varies significantly based on several factors, extending beyond just base salary. Geographic location plays a crucial role; urban centers and regions with high industrial density often offer higher pay due to increased demand and cost of living. Conversely, rural areas or regions with fewer large-scale industrial operations may present lower compensation.
Experience, specialized skills, and industry certifications dramatically influence earning potential. Planners with expertise in specific CMMS (Computerized Maintenance Management Systems) software, reliability-centered maintenance, or lean manufacturing principles command higher salaries. Total compensation packages frequently include performance bonuses, profit-sharing, and comprehensive benefits such as health insurance, retirement contributions (401k matching), and paid time off. Some roles in high-demand industries might also offer relocation allowances or professional development budgets.
Industry-specific trends also drive salary growth. For example, the manufacturing, utilities, and logistics sectors, which heavily rely on efficient asset uptime, often pay Maintenance Planners more competitively. Salary negotiation leverage increases with proven ability to reduce downtime, optimize resource allocation, and improve maintenance efficiency. Remote work opportunities for Maintenance Planners are less common given the need for on-site presence, but some companies with centralized planning functions might offer hybrid models, impacting geographic salary arbitrage.
While the salary figures provided focus on the USD context, international markets present their own unique compensation structures influenced by local labor laws, economic conditions, and industry prevalence. Understanding these multifaceted elements helps professionals maximize their earning potential in this field.
Salary by Experience Level
Level | US Median | US Average |
---|---|---|
Junior Maintenance Planner | $58k USD | $60k USD |
Maintenance Planner | $72k USD | $75k USD |
Senior Maintenance Planner | $88k USD | $90k USD |
Lead Maintenance Planner | $102k USD | $105k USD |
Maintenance Planning Manager | $120k USD | $125k USD |
Market Commentary
The job market for Maintenance Planners remains stable with a steady demand, driven by industries reliant on operational uptime, such as manufacturing, utilities, transportation, and logistics. The Bureau of Labor Statistics projects consistent growth for maintenance and repair occupations, which indirectly supports the need for skilled planners. Companies increasingly recognize that effective maintenance planning directly impacts profitability, safety, and regulatory compliance, ensuring a continuous need for this role.
Emerging opportunities for Maintenance Planners are linked to the adoption of Industry 4.0 technologies. The integration of IoT, predictive analytics, and AI into maintenance operations creates new specializations in data-driven planning and condition-based maintenance. This shift requires planners to evolve from reactive scheduling to proactive, analytical roles, interpreting data to optimize maintenance strategies. Professionals who can adapt to these technological advancements and integrate new tools into their workflow will find themselves in high demand.
Supply and demand dynamics for skilled Maintenance Planners are relatively balanced, though a shortage exists for those with advanced analytical skills or specific CMMS expertise. The profession is generally recession-resistant as essential industries must maintain operations regardless of economic fluctuations. Geographic hotspots for Maintenance Planners include industrial corridors, major manufacturing hubs, and regions with significant infrastructure projects. Continuous learning in areas like reliability engineering, CMMS software proficiency, and data analysis is crucial for long-term career viability and growth in this evolving field.
Maintenance Planner Career Path
Career progression for a Maintenance Planner typically involves a blend of technical acumen, process optimization, and leadership development. Professionals advance by mastering planning methodologies, improving asset reliability, and integrating maintenance strategies with broader operational goals. Advancement can follow individual contributor (IC) tracks, focusing on specialized planning expertise, or shift towards management, overseeing planning teams and strategic initiatives.
Advancement speed depends on several factors: an individual's performance in reducing downtime and optimizing resources, the specific industry (e.g., manufacturing, energy, logistics), and company size. Larger organizations often have more defined career ladders, while smaller companies might offer broader exposure but fewer formal progression steps. Specialization in areas like predictive maintenance or CMMS administration can accelerate progression, as can demonstrating strong analytical and problem-solving skills.
Lateral moves might include transitioning into reliability engineering or operations management, leveraging a deep understanding of maintenance processes. Networking within industry associations, continuous learning through certifications (e.g., CMRP), and mentorship play crucial roles. Developing a reputation for precision planning and effective resource allocation is vital for reaching higher levels. Common career pivots include moving into supply chain management or project coordination, where planning and logistical skills remain highly relevant.
Junior Maintenance Planner
0-2 yearsKey Focus Areas
Maintenance Planner
2-5 yearsKey Focus Areas
Senior Maintenance Planner
5-8 yearsKey Focus Areas
Lead Maintenance Planner
8-12 yearsKey Focus Areas
Maintenance Planning Manager
12+ yearsKey Focus Areas
Junior Maintenance Planner
0-2 yearsResponsible for basic data entry, work order creation, and scheduling routine maintenance tasks under direct supervision. Assists senior planners with gathering necessary information and preparing simple work packages. Impact is primarily on task-level efficiency and data integrity within the maintenance system.
Key Focus Areas
Develop foundational understanding of CMMS/EAM systems, work order processes, and basic equipment components. Focus on data entry accuracy, adherence to planning standards, and learning from senior planners. Begin to understand the importance of safety protocols and compliance in maintenance operations.
Maintenance Planner
2-5 yearsIndependently plans and schedules routine and corrective maintenance activities for a specific area or asset group. Develops detailed work packages, estimates labor, materials, and equipment. Coordinates with operations and procurement to ensure resource availability. Directly impacts maintenance efficiency and asset uptime for assigned areas.
Key Focus Areas
Master CMMS functionality, develop strong analytical skills for resource allocation, and refine communication abilities for coordinating with technicians and operations. Focus on optimizing planning processes, identifying critical path activities, and contributing to cost-saving initiatives through efficient scheduling. Begin to understand root cause analysis basics.
Senior Maintenance Planner
5-8 yearsLeads the planning and scheduling of complex maintenance projects, including major overhauls and strategic asset improvements. Provides technical guidance to other planners and acts as a subject matter expert for CMMS optimization. Identifies opportunities for process improvements and contributes to maintenance strategy development. Impact extends to overall plant reliability and long-term cost reduction.
Key Focus Areas
Develop advanced planning strategies, including shutdown/turnaround planning and predictive maintenance integration. Focus on leading process improvement initiatives, mentoring junior planners, and enhancing cross-functional collaboration. Cultivate strong problem-solving skills for complex planning challenges and contribute to reliability improvement efforts.
Lead Maintenance Planner
8-12 yearsOversees the entire maintenance planning function for a significant site or multiple asset groups. Develops and implements planning best practices, sets performance metrics, and ensures adherence to safety and compliance standards. Mentors and coaches senior planners, and collaborates extensively with operations, engineering, and supply chain leadership. Impact is on the strategic effectiveness and efficiency of the entire maintenance program.
Key Focus Areas
Focus on strategic planning alignment with business objectives, advanced risk management in maintenance, and fostering a culture of continuous improvement within the planning function. Develop strong leadership skills, including conflict resolution, performance coaching, and strategic communication. Pursue certifications like CMRP or advanced project management.
Maintenance Planning Manager
12+ yearsManages and directs the entire maintenance planning department, including multiple teams and potentially different sites. Establishes departmental goals, budgets, and long-term strategies for maintenance excellence. Responsible for talent development, performance management, and fostering innovation within the planning function. Directly influences organizational profitability through optimized asset performance and reduced operational costs.
Key Focus Areas
Develop executive leadership skills, including strategic visioning, change management, and financial oversight of maintenance operations. Focus on cultivating strong relationships with executive stakeholders, driving organizational change for reliability, and building high-performing teams. Contribute to overall business strategy and capital expenditure planning.
Job Application Toolkit
Ace your application with our purpose-built resources:
Maintenance Planner Resume Examples
Proven layouts and keywords hiring managers scan for.
View examplesMaintenance Planner Cover Letter Examples
Personalizable templates that showcase your impact.
View examplesTop Maintenance Planner Interview Questions
Practice with the questions asked most often.
View examplesMaintenance Planner Job Description Template
Ready-to-use JD for recruiters and hiring teams.
View examplesGlobal Maintenance Planner Opportunities
Maintenance Planners organize and schedule maintenance activities for industrial equipment and facilities worldwide. This role is crucial across manufacturing, energy, and logistics sectors globally. Demand remains stable, with international job markets in 2025 valuing efficiency and preventative strategies. Cultural differences impact safety protocols and operational standards. Professionals seek international roles for diverse industry exposure and specialized project involvement. Certifications like CMRP or CPIM enhance global mobility, demonstrating recognized expertise across borders.
Global Salaries
Maintenance Planner salaries vary significantly by region and industry. In North America, particularly the US and Canada, annual salaries range from 60,000 USD to 90,000 USD, often including comprehensive health benefits and retirement plans. European nations like Germany or the Netherlands offer 45,000 EUR to 70,000 EUR (approximately 48,000 USD to 75,000 USD), with strong social security and longer vacation periods.
Asia-Pacific markets, such as Australia and Singapore, see salaries between 70,000 AUD to 100,000 AUD (roughly 46,000 USD to 66,000 USD), reflecting a higher cost of living in major cities. Latin America, for example, Brazil or Mexico, presents ranges from 25,000 USD to 40,000 USD, where purchasing power parity is often higher despite lower nominal figures. Middle Eastern countries, particularly the UAE or Saudi Arabia, offer competitive tax-free salaries, often from 50,000 USD to 80,000 USD, with housing allowances sometimes included.
Cost of living adjustments are critical; a higher salary in a major city might offer less disposable income than a moderate salary in a less expensive area. Tax implications differ greatly; countries like Germany have higher income tax rates than, for instance, the UAE. Experience and specific industry knowledge, like oil and gas or advanced manufacturing, significantly influence compensation packages internationally. Some multinational corporations use standardized pay scales, but local market conditions always impact final offers.
Remote Work
International remote work for Maintenance Planners is limited but growing, particularly in roles involving strategic planning, software implementation, or data analysis rather than direct site presence. Legal and tax implications require careful consideration; a planner working remotely across borders needs to understand dual taxation agreements and local labor laws. Time zone differences can pose challenges for international team collaboration, especially when coordinating with on-site teams.
Digital nomad opportunities exist for highly specialized planners who can provide consulting services remotely. Countries like Portugal or Estonia offer specific visas for remote workers. Employer policies on international remote work vary widely; some global companies are adopting 'work-from-anywhere' models, while others prefer co-located teams. Remote work can impact salary expectations, as companies may adjust compensation based on the employee's location rather than the company's headquarters. Platforms like LinkedIn and specialized industry job boards list international remote roles. Reliable internet and a dedicated home office setup are essential for productivity.
Visa & Immigration
Maintenance Planners typically qualify for skilled worker visas in many countries. Popular destinations include Canada (Express Entry), Australia (Skilled Migration), and Germany (EU Blue Card). These pathways require a job offer or a skills assessment, often with points-based systems. Educational credential recognition is crucial; applicants may need their degrees assessed by local authorities. Professional licensing is not usually required for planners, but industry-specific certifications are beneficial.
Visa timelines vary from a few months to over a year, depending on the country and specific pathway. The application process generally involves submitting documentation, attending interviews, and sometimes English or local language proficiency tests. Pathways to permanent residency often exist after several years of skilled employment. Specific advantages may arise in countries with high demand for industrial maintenance expertise. Family visas are usually available for spouses and dependent children, allowing them to accompany the main applicant, with varying rights to work or study depending on the country's regulations.
2025 Market Reality for Maintenance Planners
Understanding current market conditions is crucial for maintenance planners to navigate their career paths successfully. The landscape for this role has evolved significantly since 2023, influenced by post-pandemic shifts in supply chains and the rapid integration of AI and automation in industrial operations.
Broader economic factors, such as inflation and capital expenditure trends, directly impact maintenance budgets and, consequently, planning roles. Market realities for planners vary based on experience level, with senior planners in higher demand, and also by geographic region, with industrial hubs offering more opportunities. Company size also plays a role, as larger organizations often have more complex planning needs. This analysis provides an honest assessment of current realities.
Current Challenges
Maintenance planners face increased competition for specialized roles, particularly those requiring advanced CMMS or data analytics skills. Economic uncertainty sometimes leads companies to defer maintenance investments, impacting hiring rates. Entry-level saturation exists in some regions where vocational training is strong but industrial growth is slow. Mismatched skills, especially in predictive maintenance technologies, pose a challenge. Job searches often extend beyond three months as companies seek precise fits.
Growth Opportunities
Despite challenges, strong demand persists for maintenance planners in sectors like manufacturing, energy, and logistics, especially those focused on critical infrastructure. Emerging opportunities lie in roles that integrate predictive maintenance technologies, IoT data analysis, and AI-driven scheduling. Planners who can leverage these tools to forecast equipment failures and optimize resource allocation are highly valued.
Professionals can position themselves advantageously by acquiring certifications in advanced CMMS platforms, data analytics, or specific industry standards like Lean or Six Sigma. Underserved markets, particularly in developing industrial zones or specialized niche manufacturing, may offer less competitive environments. Planners with expertise in reliability engineering or asset performance management gain a significant competitive edge. Strategic career moves now involve focusing on continuous learning in digital tools and embracing a data-centric approach to maintenance planning. Industries prioritizing uptime and efficiency, like pharmaceuticals or data centers, continue to show robust demand for skilled planners.
Current Market Trends
Hiring for maintenance planners remains steady in 2025, driven by the ongoing need for operational efficiency and asset longevity across various industries. Companies prioritize planners who can optimize schedules, manage spare parts, and reduce downtime. The integration of advanced CMMS (Computerized Maintenance Management Systems) and EAM (Enterprise Asset Management) platforms now demands a higher level of technical proficiency.
Economic conditions influence investment in new facilities, which in turn affects the demand for new planning roles. However, existing infrastructure always requires maintenance, ensuring a baseline demand. Generative AI and automation are beginning to impact planning by assisting with data analysis, predictive scheduling, and inventory optimization. This shifts the planner's role towards oversight and strategic decision-making rather than purely manual data entry.
Employers increasingly seek planners with strong analytical skills, experience with data visualization tools, and a proactive approach to maintenance. Salary trends show modest growth, with a premium for those proficient in specific industry software or predictive analytics. Market saturation varies; highly industrialized regions often have more competition, while remote work remains limited for this role due to site-specific requirements. Cyclical patterns in manufacturing or energy can influence hiring, but overall, the demand for effective asset management keeps this role relevant year-round.
Emerging Specializations
The role of a Maintenance Planner is evolving significantly, driven by rapid advancements in technology and shifting industry paradigms. New specialization opportunities are emerging from the integration of artificial intelligence, advanced analytics, and sustainable practices into maintenance operations. Understanding these future-oriented paths allows professionals to strategically position themselves for career advancement in 2025 and beyond.
Early positioning in these emerging areas often commands premium compensation and accelerated career growth. As industries adopt sophisticated tools and methodologies, the demand for planners with specialized expertise in these cutting-edge fields increases. While established specializations remain vital, exploring nascent areas provides a distinct competitive advantage.
Many emerging areas, initially niche, typically become mainstream within three to five years, creating a substantial volume of job opportunities. Investing in these specializations now offers a strong risk-reward balance. The initial investment in acquiring new skills pays off as these areas mature, offering significant long-term career stability and influence within an organization.
AI-Driven Predictive Maintenance Planner
This specialization focuses on integrating AI and machine learning algorithms into maintenance scheduling and resource allocation. AI-driven planning optimizes predictive maintenance schedules, anticipates equipment failures with greater accuracy, and automates parts ordering. This enhances operational efficiency and minimizes downtime by moving beyond traditional reactive or time-based planning.
Maintenance Data Analytics Specialist
This role centers on utilizing advanced data analytics to identify patterns, predict maintenance needs, and optimize asset lifecycle costs. Planners in this area work with large datasets from sensors and operational systems to create sophisticated models. They translate complex data into actionable maintenance strategies, improving decision-making and asset performance across an organization.
Sustainable Maintenance Planner
This specialization focuses on developing and implementing maintenance strategies that reduce environmental impact and improve resource efficiency. Planners in this area consider energy consumption of equipment, waste generation from maintenance activities, and the lifecycle impact of materials. They aim to optimize maintenance for both operational effectiveness and sustainability goals.
Robotics and Automation Maintenance Planner
This emerging area involves planning maintenance activities for highly automated and robotic production environments. It requires understanding the unique maintenance needs of complex robotic systems, AGVs (Automated Guided Vehicles), and integrated automation cells. Planners must coordinate software updates, sensor calibration, and mechanical upkeep for these advanced systems.
Digital Integration Maintenance Planner
This specialization deals with integrating and optimizing the flow of information between various maintenance software systems, including CMMS, ERP, and IoT platforms. The planner ensures seamless data exchange and process automation across different digital tools. This role is crucial for leveraging digital twins and creating a unified digital maintenance ecosystem.
Pros & Cons of Being a Maintenance Planner
Making informed career decisions requires understanding both the benefits and challenges of a specific profession. A career as a Maintenance Planner, for instance, offers distinct opportunities but also presents particular demands.
It is important to recognize that career experiences can vary significantly based on company culture, industry sector (e.g., manufacturing, energy, logistics), and the specific responsibilities of the role. Additionally, the pros and cons may shift at different career stages, with early-career planners focusing on learning and mid-career planners on optimization.
What one person considers an advantage, like a fast-paced environment, another might see as a disadvantage. This assessment aims to provide an honest, balanced perspective to help individuals set appropriate expectations and determine if this path aligns with their personal values and professional aspirations.
Pros
- Maintenance planners play a critical role in operational efficiency, directly impacting productivity and cost savings by ensuring equipment reliability and minimizing downtime, which provides a strong sense of contribution and importance.
- The role demands strong organizational, analytical, and problem-solving skills as planners must optimize schedules, manage resources, and troubleshoot logistical issues, leading to continuous intellectual stimulation and skill development.
- Maintenance planning is essential across various industries, including manufacturing, oil and gas, utilities, and transportation, providing excellent job security and diverse opportunities for employment.
- Maintenance planners often work standard business hours in an office or control room setting, offering a more predictable work-life balance compared to hands-on maintenance technicians who may face more irregular shifts or emergency call-outs.
- The position offers a clear pathway for career advancement into roles such as Reliability Engineer, Maintenance Supervisor, Maintenance Manager, or even Operations Manager, by building a foundational understanding of plant operations.
- Maintenance planners gain a comprehensive understanding of an organization's physical assets and operational processes, which is a valuable skill set highly sought after in various industrial and technical management roles.
- The role allows for significant autonomy in decision-making regarding scheduling, resource allocation, and preventive maintenance strategies, empowering planners to implement their expertise and optimize workflows.
Cons
- Maintenance planners often face intense pressure to minimize downtime and ensure timely repairs, which can lead to high stress levels, especially during critical equipment failures or tight production schedules.
- The role requires meticulous attention to detail and adherence to strict protocols; even minor errors in scheduling or resource allocation can cause significant operational disruptions, leading to accountability and frustration.
- Maintenance planners frequently act as intermediaries between production, maintenance technicians, and parts suppliers, which can involve managing conflicting priorities and navigating interpersonal challenges.
- While some roles offer a standard schedule, maintenance planners may need to be on call or work extended hours during emergencies, unplanned outages, or major turnaround projects to ensure operational continuity.
- Career progression for a dedicated maintenance planner can be limited without transitioning into broader maintenance management, project management, or operational leadership roles, requiring additional skills and experience.
- The work environment often involves being in industrial settings, which can be noisy, dirty, and sometimes hazardous, requiring adherence to strict safety procedures and wearing personal protective equipment.
- Staying current with evolving maintenance technologies, software, and best practices requires continuous learning and professional development, which can be time-consuming and challenging to fit into a demanding work schedule.
Frequently Asked Questions
Maintenance Planners face distinct challenges balancing technical understanding with organizational skills to optimize asset uptime. This section addresses common questions about entering this role, from required skills and career trajectory to managing complex schedules and communicating effectively across teams.
What are the typical entry requirements and educational background for a Maintenance Planner?
A Maintenance Planner typically needs a strong background in maintenance or trades, often with several years of hands-on experience. Many successful planners come from roles like maintenance technician, electrician, or mechanic. While not always mandatory, certifications in maintenance planning or reliability, such as CMRP (Certified Maintenance and Reliability Professional), can significantly enhance your resume and demonstrate specialized knowledge. Some roles may prefer an associate's or bachelor's degree in a technical field or engineering.
How long does it realistically take to become job-ready as a Maintenance Planner if I'm starting from a related field?
The transition time varies based on your existing experience. If you are already a skilled tradesperson, you might transition into a junior planning role within 6-12 months by focusing on planning-specific training and software proficiency. For those new to maintenance, it could take 2-3 years to gain sufficient technical knowledge and practical experience before moving into a planning role. Building a strong understanding of equipment, processes, and safety protocols is crucial.
What are the salary expectations for a Maintenance Planner, and how do they grow with experience?
Maintenance Planners generally earn competitive salaries, reflecting their critical role in operational efficiency. Entry-level positions might start around $55,000 to $65,000 per year, while experienced planners with specialized certifications can earn $75,000 to $95,000 or more annually. Salary can vary significantly based on industry (e.g., manufacturing, oil and gas, utilities), company size, and geographic location. Expect potential for bonuses tied to key performance indicators like reduced downtime or improved maintenance efficiency.
What is the typical work-life balance for a Maintenance Planner, and how demanding is the role?
Work-life balance for Maintenance Planners is generally stable, primarily office-based, and typically follows standard business hours. Unlike technicians, planners are less likely to be called out for emergency repairs during off-hours. However, deadlines for planned shutdowns or critical projects can sometimes require extended hours. The role demands strong organizational skills and the ability to manage multiple priorities, which can sometimes lead to high-pressure periods, but these are usually predictable.
Is the job market for Maintenance Planners stable, and what are the long-term prospects?
The job market for Maintenance Planners is stable and growing, driven by industries' increasing focus on asset reliability and predictive maintenance. Companies across manufacturing, logistics, energy, and infrastructure depend on efficient maintenance to minimize costly downtime. This role is considered essential for operational continuity and cost control, making it a secure career path. As technology advances, the demand for planners proficient in CMMS software and data analysis will continue to rise.
What are the typical career growth opportunities and advancement paths for a Maintenance Planner?
Career growth for Maintenance Planners can lead to various leadership and specialized roles. You might advance to a Senior Maintenance Planner, Maintenance Supervisor, Reliability Engineer, or even Maintenance Manager. Many planners also transition into roles focused on Continuous Improvement, Project Management, or Consulting, leveraging their deep understanding of operational processes and efficiency. Gaining certifications and pursuing further education in engineering or business administration can accelerate this progression.
Can Maintenance Planners work remotely, or is it primarily an on-site role?
While some administrative tasks can be done remotely, the core function of a Maintenance Planner involves close collaboration with maintenance teams, operations, and inventory, often requiring on-site presence. Many organizations prefer planners to be regularly present to conduct field walk-downs, interact with technicians directly, and understand equipment conditions firsthand. Hybrid models are becoming more common, allowing for some remote work, but fully remote positions are rare for this role.
What are some of the biggest daily challenges a Maintenance Planner faces?
A key challenge is balancing proactive planning with reactive demands. Planners must manage unexpected breakdowns and urgent requests while trying to stick to a long-term maintenance schedule. This requires strong prioritization, communication, and adaptability. Another challenge involves securing necessary resources and parts in a timely manner, often requiring meticulous coordination with procurement and vendors. Effectively communicating complex plans to diverse teams, from technicians to management, is also crucial.
Related Careers
Explore similar roles that might align with your interests and skills:
Maintenance Administrator
A growing field with similar skill requirements and career progression opportunities.
Explore career guideMaintenance Coordinator
A growing field with similar skill requirements and career progression opportunities.
Explore career guideMaintenance Manager
A growing field with similar skill requirements and career progression opportunities.
Explore career guideMaintenance Supervisor
A growing field with similar skill requirements and career progression opportunities.
Explore career guideProduction Planner
A growing field with similar skill requirements and career progression opportunities.
Explore career guideAssess your Maintenance Planner readiness
Understanding where you stand today is the first step toward your career goals. Our Career Coach helps identify skill gaps and create personalized plans.
Skills Gap Analysis
Get a detailed assessment of your current skills versus Maintenance Planner requirements. Our AI Career Coach identifies specific areas for improvement with personalized recommendations.
See your skills gapCareer Readiness Assessment
Evaluate your overall readiness for Maintenance Planner roles with our AI Career Coach. Receive personalized recommendations for education, projects, and experience to boost your competitiveness.
Assess your readinessSimple pricing, powerful features
Upgrade to Himalayas Plus and turbocharge your job search.
Himalayas
Himalayas Plus
Himalayas Max
Find your dream job
Sign up now and join over 100,000 remote workers who receive personalized job alerts, curated job matches, and more for free!
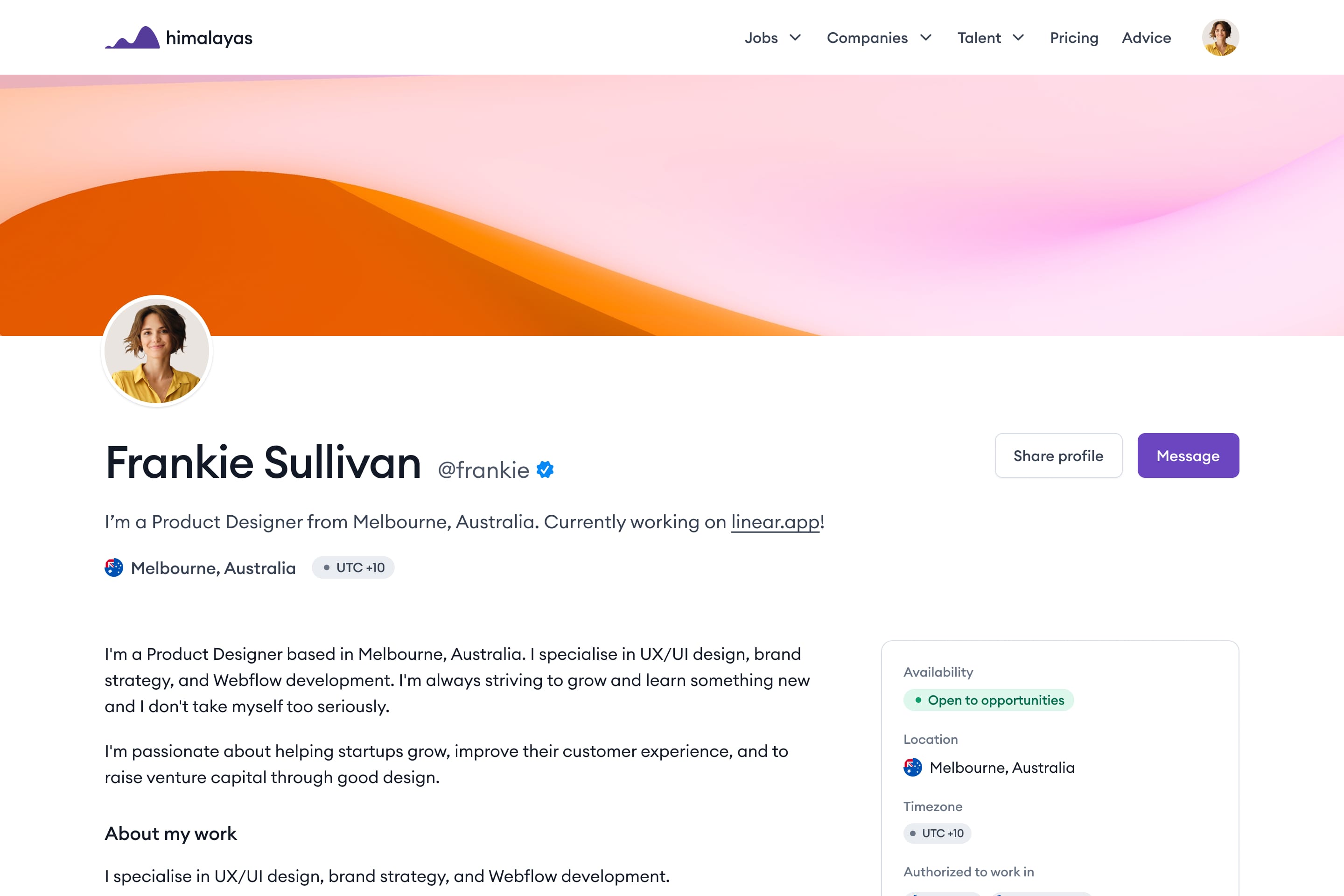