Complete Inventory Control Manager Career Guide
Inventory Control Managers are the strategic backbone of supply chains, ensuring products are exactly where they need to be, when they need to be there, minimizing waste and maximizing efficiency. They optimize stock levels, prevent losses, and implement systems that directly impact a company’s profitability and customer satisfaction.
This critical role demands sharp analytical skills and a knack for logistics, offering a pathway to significant impact within diverse industries.
Key Facts & Statistics
Median Salary
$74,750 USD
(U.S. national median, BLS May 2023)
Range: $45k - $120k+ USD
Growth Outlook
4%
as fast as average (BLS 2022-2032)
Annual Openings
≈35,000
openings annually (BLS)
Top Industries
Typical Education
Bachelor's degree in supply chain management, business, or logistics, though extensive experience with an associate's degree is also common.
What is an Inventory Control Manager?
An Inventory Control Manager is a specialized professional responsible for optimizing the flow of goods within a company, from raw materials to finished products. They ensure accurate, efficient, and cost-effective management of inventory levels, preventing both stockouts and overstock. This role is crucial for maintaining operational efficiency, reducing carrying costs, and supporting sales and production demands.
Unlike a Warehouse Manager who focuses on the physical movement and storage of goods, or a Supply Chain Manager who oversees the entire end-to-end network, the Inventory Control Manager specifically concentrates on the quantity, location, and condition of stock. Their primary goal is to balance product availability with financial prudence, ensuring the right amount of product is in the right place at the right time.
What does an Inventory Control Manager do?
Key Responsibilities
- Develop and implement inventory control procedures to optimize stock levels and minimize waste.
- Monitor inventory accuracy through regular cycle counts and physical inventories, investigating discrepancies.
- Analyze sales data, forecasts, and seasonal trends to determine optimal ordering quantities and reorder points.
- Coordinate with purchasing, warehouse, and sales departments to ensure smooth material flow and order fulfillment.
- Identify and resolve issues related to inventory discrepancies, damaged goods, or slow-moving stock.
- Generate detailed inventory reports and present findings to management, recommending improvements.
- Train and supervise inventory staff on best practices for counting, storing, and tracking materials accurately.
Work Environment
Inventory Control Managers typically work in a dynamic environment, often splitting their time between an office setting and a warehouse or production floor. They spend significant time collaborating with purchasing, logistics, and sales teams, participating in meetings to coordinate supply chain activities. The pace is often fast, especially during peak seasons or when managing unexpected supply chain disruptions. While primarily an on-site role, some larger organizations or those with multiple distribution centers might involve occasional travel. The work schedule is generally standard business hours, but urgent issues or inventory cycles may require flexibility.
Tools & Technologies
Inventory Control Managers primarily use Enterprise Resource Planning (ERP) systems like SAP, Oracle, or NetSuite for comprehensive inventory tracking, order management, and financial integration. They also leverage Warehouse Management Systems (WMS) such as Manhattan Associates or HighJump for precise stock location and movement within the warehouse. Data analysis tools like Microsoft Excel, Google Sheets, or specialized business intelligence (BI) software like Tableau or Power BI help them interpret inventory trends and performance metrics. Barcode scanners and RFID technology are essential for efficient data capture during receiving and shipping. Communication and project management tools like Microsoft Teams, Slack, or Asana facilitate collaboration across departments.
Inventory Control Manager Skills & Qualifications
The Inventory Control Manager role demands a blend of analytical rigor, operational efficiency, and leadership. Qualifications in this field are highly practical, prioritizing demonstrated experience over purely academic credentials, especially at mid to senior levels. Entry-level positions may accept a bachelor's degree with less direct experience, while senior roles often require extensive hands-on management of complex inventory systems.
Requirements vary significantly by company size and industry. Large retail chains or manufacturing companies often seek candidates with experience in sophisticated ERP systems and global supply chains. Smaller businesses might value adaptability and a broader skillset in managing all aspects of warehouse operations. Certifications like APICS CSCP or CPIM add substantial value across all sectors, often substituting for advanced degrees or accelerating career progression.
The skill landscape for Inventory Control Managers is evolving rapidly due to automation, IoT, and advanced analytics. Proficiency in data analysis tools and predictive modeling is becoming a 'must-have,' moving beyond traditional spreadsheet management. While formal education provides foundational knowledge, continuous learning in new technologies and supply chain methodologies is crucial for long-term success in this dynamic role.
Education Requirements
Technical Skills
- Inventory Management Software (e.g., SAP ERP, Oracle SCM, Microsoft Dynamics 365, NetSuite)
- Warehouse Management Systems (WMS) operation and configuration
- Data Analysis and Reporting (Advanced Excel, SQL for querying, Power BI/Tableau for visualization)
- Forecasting and Demand Planning methodologies (e.g., statistical forecasting, moving averages)
- Inventory Optimization Techniques (e.g., ABC analysis, EOQ, safety stock calculation, reorder point setting)
- Cycle Counting and Physical Inventory Procedures
- Supply Chain Metrics and KPIs (e.g., inventory turnover, fill rate, carrying cost, days of supply)
- Barcoding and RFID Technology implementation and utilization
- Logistics and Transportation Management principles
- Lean Inventory and Just-In-Time (JIT) principles
- Enterprise Resource Planning (ERP) system integration with inventory modules
- Compliance with safety regulations and industry standards
Soft Skills
- Analytical Thinking: Essential for identifying inventory discrepancies, forecasting demand, and optimizing stock levels based on complex data.
- Problem-Solving: Critical for resolving inventory issues, managing stockouts or overstock, and improving process inefficiencies.
- Leadership and Team Management: Necessary for overseeing inventory teams, delegating tasks, and fostering a culture of accuracy and accountability.
- Attention to Detail: Paramount for maintaining accurate inventory records, preventing errors, and ensuring compliance with audit requirements.
- Communication Skills: Important for collaborating with purchasing, sales, and warehouse teams, and for reporting inventory status to management.
- Organizational Skills: Key for managing multiple product lines, tracking stock movements, and maintaining a well-ordered warehouse environment.
- Adaptability: Crucial for responding to unexpected supply chain disruptions, market changes, or shifts in demand patterns.
- Negotiation Skills: Useful when working with suppliers or carriers regarding delivery schedules, returns, or inventory discrepancies.
How to Become an Inventory Control Manager
Breaking into an Inventory Control Manager role involves various pathways, depending on your background and the industry. A common misconception is that you need a specialized logistics degree; while helpful, practical experience and certifications often carry more weight. For complete beginners, starting in a warehouse or supply chain operations role provides invaluable foundational experience before transitioning to a management position.
The timeline for entry can range from 1-2 years for those with related experience, to 3-5 years for individuals starting from scratch in entry-level supply chain roles. Entry strategies also vary by company size; larger corporations might prefer candidates with formal degrees or extensive management experience, whereas smaller businesses or startups may prioritize adaptability and hands-on problem-solving skills. Geographic location also plays a role, with more opportunities in logistics hubs or regions with significant manufacturing and distribution.
Networking within the supply chain community, attending industry events, and connecting with mentors can significantly accelerate your career progression. The hiring landscape values a blend of analytical skills, proficiency in inventory management systems, and leadership capabilities. Overcoming barriers to entry often involves demonstrating a strong aptitude for data analysis, process improvement, and a commitment to continuous learning in supply chain best practices.
Step 1
Step 2
Step 3
Step 4
Step 5
Step 6
Step 7
Education & Training Needed to Become an Inventory Control Manager
Becoming an Inventory Control Manager involves a blend of formal education and practical experience. Traditional four-year bachelor's degrees in Supply Chain Management, Logistics, or Business Administration with a concentration in operations are highly valued. These degrees typically cost between $40,000 and $100,000 or more and take four years to complete. They provide a strong theoretical foundation in inventory optimization, warehousing, and supply chain analytics, which is essential for strategic roles.
Alternative pathways include specialized certifications and associate's degrees, which can be more time and cost-efficient. Professional certifications from organizations like APICS (now ASCM) or the Council of Supply Chain Management Professionals (CSCMP) can be completed in 3 to 12 months, costing from $1,000 to $5,000. These certifications focus on practical skills and industry best practices, making candidates immediately hirable for operational roles. Online courses and self-study, ranging from free to a few hundred dollars, offer flexibility but require discipline and may not carry the same weight as formal credentials without accompanying experience.
Employers often prefer candidates with a mix of academic knowledge and hands-on experience, understanding that practical application of inventory principles is crucial. While a degree offers a broad understanding, certifications demonstrate specific expertise. Continuous learning through workshops on new inventory software, data analytics, or lean manufacturing principles is vital for career advancement. The most effective educational investment combines a solid foundational degree or certification with ongoing professional development and significant practical experience in inventory operations.
Inventory Control Manager Salary & Outlook
Compensation for an Inventory Control Manager varies significantly based on several factors. Geographic location plays a major role, with higher salaries typically found in major metropolitan areas or regions with significant logistics and manufacturing hubs due to higher cost of living and increased demand. For instance, salaries in New York or California often exceed those in less populated states.
Years of experience, the complexity of inventory systems managed, and specific industry knowledge also drive salary differences. Professionals specializing in areas like cold chain logistics, high-value goods, or just-in-time (JIT) inventory systems often command higher pay. Skill sets in advanced inventory software (e.g., SAP, Oracle), data analytics, and supply chain optimization are particularly valued.
Total compensation packages extend beyond base salary. They frequently include performance bonuses tied to inventory accuracy, cost reduction, or fill rates. Equity options are less common for this role but can appear at very senior levels in some companies. Comprehensive benefits, such as health insurance, retirement contributions (401k matching), and professional development allowances for certifications like APICS CSCP or CPIM, are standard components.
Company size and industry sector also influence earnings. Larger corporations with complex global supply chains generally offer higher compensation than smaller businesses. The ability to demonstrate quantifiable improvements in inventory turnover, reduction in carrying costs, and optimization of warehouse space provides strong negotiation leverage, regardless of location. Remote work opportunities for this role are limited given the hands-on nature, but hybrid models may adjust salary expectations based on the employer's physical location.
Salary by Experience Level
Level | US Median | US Average |
---|---|---|
Assistant Inventory Control Manager | $60k USD | $65k USD |
Inventory Control Manager | $75k USD | $80k USD |
Senior Inventory Control Manager | $98k USD | $105k USD |
Director of Inventory Control | $128k USD | $135k USD |
VP of Inventory Management | $170k USD | $180k USD |
Market Commentary
The job market for Inventory Control Managers remains stable with a moderate growth outlook, driven by the ongoing need for efficient supply chain operations. E-commerce expansion and increasing consumer demands for faster delivery necessitate precise inventory management, creating continuous demand for skilled professionals. The Bureau of Labor Statistics projects growth for logisticians, a category that includes inventory control managers, at about 4% over the next decade, aligning with the average for all occupations.
Emerging opportunities for Inventory Control Managers are tied to technological advancements. The adoption of AI, machine learning for demand forecasting, and robotic process automation (RPA) in warehouses is transforming the role. Professionals with expertise in implementing and managing these new technologies will find themselves in high demand. This shift emphasizes analytical skills and data interpretation over purely manual tracking.
Supply and demand dynamics for this role are relatively balanced, though a shortage of candidates proficient in advanced analytics and digital inventory platforms exists. This creates a competitive edge for those who can leverage technology to optimize inventory flows and reduce waste. Future-proofing this career involves continuous learning in supply chain technology, data science, and lean inventory principles to adapt to evolving industry standards.
While the role is generally recession-resistant due to its critical function in cost control, economic downturns can lead companies to scrutinize inventory levels more closely, increasing the pressure on managers to achieve efficiency. Geographic hotspots for this role include major distribution hubs and manufacturing centers, such as the Midwest, parts of the South, and coastal port cities. Remote work, while less common, may see a slight increase for strategic planning aspects of the role, though on-site presence remains crucial for operational oversight.
Inventory Control Manager Career Path
Career progression for an Inventory Control Manager typically involves a blend of operational expertise, strategic planning, and leadership development. Professionals advance by demonstrating a deep understanding of supply chain dynamics, optimizing inventory processes, and effectively managing teams. The path often distinguishes between individual contributor roles focused on deep technical inventory management and leadership tracks that oversee broader departmental or organizational inventory strategies.
Advancement speed depends on several factors, including a professional's performance, the complexity of the inventory systems they manage, and the company's size and industry. For instance, a fast-growing retail company might offer quicker advancement than a mature manufacturing firm. Specialization in areas like demand forecasting, warehouse management systems (WMS), or lean inventory principles can accelerate progression. Lateral moves into related supply chain roles, such as logistics management or procurement, are also common for broadening experience.
Building a strong professional network, engaging in continuous learning, and seeking mentorship significantly influence career trajectory. Certifications like APICS CSCP or CPIM are highly valued. Career paths also vary by company type; startups may offer rapid growth and broad responsibilities, while large corporations provide structured paths with more specialized roles. Consulting or agency roles can expose professionals to diverse inventory challenges across multiple clients, enhancing their problem-solving skills and industry reputation.
Assistant Inventory Control Manager
0-3 yearsKey Focus Areas
Inventory Control Manager
3-7 yearsKey Focus Areas
Senior Inventory Control Manager
7-12 yearsKey Focus Areas
Director of Inventory Control
12-18 yearsKey Focus Areas
VP of Inventory Management
18+ yearsKey Focus Areas
Assistant Inventory Control Manager
0-3 yearsOversee daily inventory operations, focusing on accuracy and integrity. This includes managing cycle counts, investigating discrepancies, and ensuring proper stock rotation. The role involves direct supervision of inventory clerks and close collaboration with warehouse supervisors and receiving teams to maintain optimal stock levels and prevent loss.
Key Focus Areas
Develop foundational knowledge in inventory management principles, including cycle counting, ABC analysis, and material handling. Gain proficiency in using inventory management software and data entry. Focus on accuracy, attention to detail, and effective communication with warehouse staff and suppliers. Understand basic supply chain concepts.
Inventory Control Manager
3-7 yearsManage the entire inventory control department, developing and implementing inventory policies and procedures. This role involves setting inventory targets, analyzing stock levels, and optimizing warehouse space. Decision-making authority extends to process improvements, technology adoption, and staffing for the inventory team. The manager reports to supply chain leadership and impacts operational efficiency significantly.
Key Focus Areas
Master advanced inventory optimization techniques, such as demand forecasting, safety stock calculation, and vendor-managed inventory. Enhance analytical skills to interpret inventory data and identify trends. Develop leadership capabilities, including team motivation, performance management, and conflict resolution. Begin strategic planning for inventory reduction and efficiency gains.
Senior Inventory Control Manager
7-12 yearsLead strategic inventory initiatives and oversee multiple inventory control teams or locations. This role involves developing long-term inventory strategies, implementing new technologies, and managing complex projects aimed at improving inventory turns and reducing carrying costs. The manager acts as a key liaison between operations and senior leadership, influencing broad supply chain decisions and impacting overall profitability.
Key Focus Areas
Cultivate expertise in supply chain analytics, predictive modeling, and advanced WMS functionalities. Drive initiatives for continuous improvement and process automation. Focus on cross-functional collaboration with sales, finance, and production to align inventory strategies with business goals. Mentor junior managers and contribute to talent development within the department.
Director of Inventory Control
12-18 yearsDirect the entire inventory control function across an organization, setting the strategic vision and objectives. This position involves developing global inventory policies, managing multi-million dollar inventory budgets, and leading large teams of inventory professionals. The director makes high-level decisions impacting supply chain resilience, cost efficiency, and customer satisfaction, reporting directly to a VP or C-level executive.
Key Focus Areas
Develop executive-level communication and presentation skills. Focus on financial acumen related to inventory valuation, obsolescence, and working capital optimization. Build strong relationships with external partners and lead large-scale supply chain transformation projects. Drive innovation in inventory technology and data utilization.
VP of Inventory Management
18+ yearsHold ultimate responsibility for all inventory management strategies and operations across the enterprise. This executive role involves defining the global inventory vision, influencing company-wide supply chain investments, and ensuring inventory aligns with overall business growth and profitability goals. The VP provides strategic leadership, manages high-level stakeholder relationships, and oversees large departmental budgets, directly impacting the company's financial performance and market position.
Key Focus Areas
Shape the organization's overarching supply chain strategy, integrating inventory management with broader business objectives. Focus on global supply chain risk management, sustainability, and long-term strategic partnerships. Cultivate strong executive presence and influence, driving organizational change and fostering a culture of continuous improvement.
Job Application Toolkit
Ace your application with our purpose-built resources:
Inventory Control Manager Resume Examples
Proven layouts and keywords hiring managers scan for.
View examplesInventory Control Manager Cover Letter Examples
Personalizable templates that showcase your impact.
View examplesTop Inventory Control Manager Interview Questions
Practice with the questions asked most often.
View examplesInventory Control Manager Job Description Template
Ready-to-use JD for recruiters and hiring teams.
View examplesGlobal Inventory Control Manager Opportunities
Inventory Control Managers find global demand across manufacturing, retail, and logistics sectors. Their role ensures efficient supply chains, crucial for international trade and e-commerce growth. Regulatory differences, like customs and import/export laws, directly impact inventory practices worldwide. Professionals seek international roles for diverse supply chain experiences and exposure to new markets. APICS certifications, such as CSCP or CPIM, significantly enhance global mobility.
Global Salaries
Salaries for Inventory Control Managers vary significantly by region and industry. In North America, particularly the United States, annual salaries range from $70,000 to $110,000 USD. Canada offers similar ranges, typically $60,000 to $95,000 CAD. These figures reflect strong purchasing power and access to comprehensive benefits packages.
European markets show diverse compensation. In Germany, a manager earns €55,000 to €85,000 annually, while the UK offers £45,000 to £75,000. These regions have varying social security contributions and healthcare systems that affect net pay. Northern European countries often have higher taxes but robust social benefits.
Asia-Pacific roles in countries like Singapore or Australia pay between $60,000 and $90,000 USD equivalent. Japan's salaries might be ¥6,000,000 to ¥9,000,000, with a higher cost of living. Latin American countries, like Mexico or Brazil, typically offer lower nominal salaries, ranging from $30,000 to $50,000 USD equivalent, but with a proportionally lower cost of living, maintaining a reasonable purchasing power. Experience and company size always influence compensation across all regions.
Remote Work
International remote work for Inventory Control Managers is less common than for purely digital roles, but it is growing. Companies often need on-site presence for physical inventory oversight and team leadership. However, roles focusing on inventory planning, forecasting, and system optimization can support remote or hybrid models. Legal and tax implications for international remote work require careful consideration; employers must comply with local labor and tax laws where the employee resides.
Time zone differences can pose challenges for international team collaboration, requiring flexible working hours. Digital nomad opportunities exist, particularly for consultants or those working with global ERP systems. Some companies with large, distributed supply chains might hire internationally for central planning roles. Salary expectations for remote positions can vary based on the employee's location, sometimes reflecting geographic arbitrage.
Visa & Immigration
Common visa categories for Inventory Control Managers include skilled worker visas or intra-company transfer visas. Popular destination countries like Canada, Australia, Germany, and the UK have specific immigration pathways for skilled logistics and supply chain professionals. Requirements often include a relevant bachelor's degree, several years of experience, and a job offer from a local employer. Education credential recognition may be necessary.
Visa timelines vary from a few weeks to several months, depending on the country and application volume. Language requirements might apply, especially for European countries, necessitating tests like IELTS or Goethe-Institut exams. Some countries offer points-based immigration systems where supply chain experience contributes to eligibility. Spousal and dependent visas are typically available, allowing family members to accompany the main applicant. Professional licensing is generally not required for this role, but industry certifications are beneficial.
2025 Market Reality for Inventory Control Managers
Understanding the current market realities for an Inventory Control Manager is vital for career success. The landscape for this role has evolved significantly since 2023, influenced by post-pandemic supply chain recalibrations and the rapid integration of AI.
Broader economic factors, such as inflation and consumer demand fluctuations, directly impact inventory levels and the strategic importance of this role. Market conditions vary by experience level, with senior roles often more stable, and by geographic region, depending on industrial concentration. This analysis provides an honest assessment to help professionals navigate these changes.
Current Challenges
Inventory Control Managers face increased competition, especially as supply chains normalize and companies optimize existing teams. Market saturation at entry and mid-levels makes distinguishing oneself harder.
Economic uncertainty causes companies to delay hiring or freeze positions. This creates a challenging environment for job seekers.
Growth Opportunities
Despite challenges, strong demand exists for Inventory Control Managers skilled in advanced analytics and technology integration. Companies prioritize professionals who can implement AI-driven forecasting, optimize warehouse automation, and reduce carrying costs through data-driven strategies.
Emerging opportunities include roles focused on sustainable inventory practices, reverse logistics management, and supply chain resilience. Professionals who understand global sourcing complexities and risk management are highly sought after.
Gaining certifications in supply chain management (e.g., APICS CSCP, CPIM) or specialized training in AI/machine learning applications for logistics provides a competitive edge. Underserved markets in developing industrial zones or niche sectors, like cold chain logistics, offer unique prospects.
Market corrections may create opportunities for strategic career moves into companies investing in long-term supply chain optimization. Emphasizing skills in process improvement, cost reduction, and cross-functional collaboration positions candidates advantageously.
Current Market Trends
Hiring for Inventory Control Managers shows a stabilized demand in 2025 after a volatile period. The post-pandemic surge in supply chain roles has leveled off, with companies now focusing on efficiency and optimization rather than rapid expansion.
Generative AI and automation are significantly reshaping the role. Companies seek managers who can implement AI-driven forecasting tools, optimize warehouse automation, and leverage predictive analytics for inventory management. This shifts the focus from manual tracking to strategic oversight and technology integration.
Economic conditions, particularly inflation and consumer spending shifts, influence inventory levels and, consequently, management needs. Some industries, like retail and e-commerce, still experience high turnover and a need for skilled managers. Manufacturing and logistics sectors maintain steady demand for precise inventory control.
Employer requirements now emphasize data analytics, ERP system proficiency (like SAP, Oracle), and a strong understanding of supply chain technology. Candidates with experience in implementing or managing automated inventory systems have a distinct advantage. Salaries show moderate growth, reflecting the demand for specialized skills rather away from generalist roles.
Geographically, demand remains strong in major logistics hubs and manufacturing centers. Remote work for this role is less common due to the hands-on nature of managing physical inventory, though some strategic or analytical positions may offer hybrid options.
Emerging Specializations
The field of inventory control is undergoing a significant transformation, driven by advancements in artificial intelligence, automation, and global supply chain complexities. These technological shifts and evolving market demands are creating entirely new specialization opportunities for inventory control managers. Understanding these emerging areas allows professionals to strategically position themselves for future career advancement and enhanced earning potential.
Early positioning in these emerging specializations, particularly those gaining traction in 2025 and beyond, offers a distinct advantage. Professionals who develop expertise in these cutting-edge niches often command premium compensation due to the scarcity of specialized skills. While established specializations remain vital, focusing on emerging areas provides a pathway to lead innovation and shape the future of supply chain management.
Many emerging areas transition from niche to mainstream within five to seven years, creating a substantial volume of job opportunities. Investing in these areas now offers a favorable risk-reward profile; while some uncertainty always exists with new fields, the potential for significant career growth and impact far outweighs the risks for those committed to continuous learning.
AI-Driven Predictive Inventory Analyst
This specialization focuses on integrating AI and machine learning models into inventory forecasting and optimization processes. Inventory Control Managers in this area analyze vast datasets to predict demand with unprecedented accuracy, identify optimal reorder points, and minimize holding costs. They work with data scientists to deploy predictive analytics solutions that automate decision-making and enhance supply chain resilience.
Automated Warehouse Inventory Specialist
This specialization involves managing inventory within highly automated warehouse environments, including facilities utilizing robotics, automated guided vehicles (AGVs), and drone technology. Inventory Control Managers in this role oversee the seamless interaction between physical stock and automated systems, ensuring data accuracy and operational efficiency. They are responsible for optimizing automated storage and retrieval systems (AS/RS) and managing robotic picking processes to maintain precise inventory levels.
Real-Time Supply Chain Visibility Manager
This role focuses on establishing and maintaining real-time visibility across the entire supply chain, from raw materials to final product delivery. Inventory Control Managers in this area implement IoT sensors, blockchain, and other tracking technologies to monitor inventory movement, condition, and location instantaneously. Their goal is to prevent stockouts, reduce shrinkage, and provide accurate, up-to-the-minute inventory data for strategic decision-making.
Circular Economy Inventory Manager
This specialization addresses the unique challenges of managing inventory for reverse logistics, including returns, repairs, recycling, and product disposition. Inventory Control Managers in this area optimize processes for receiving, assessing, and redirecting returned goods to maximize recovery value and minimize waste. They develop strategies for efficient disposition, whether through refurbishment, resale, or sustainable disposal, ensuring compliance with environmental regulations.
Customization & On-Demand Inventory Coordinator
This emerging area focuses on managing inventory for highly customized or build-to-order products, often in industries like manufacturing or e-commerce. Inventory Control Managers in this specialization develop flexible inventory models that support mass customization without excessive stock holding. They manage component inventory, optimize kitting processes, and coordinate with production to ensure just-in-time availability for unique customer orders, balancing efficiency with bespoke requirements.
Pros & Cons of Being an Inventory Control Manager
Making informed career choices requires understanding both the benefits and challenges of a specific profession. The experience of an Inventory Control Manager can vary significantly based on the company's industry, its size, the specific products handled, and the organizational culture. What one person perceives as an advantage, like structured routines, another might view as a disadvantage. Furthermore, the nature of the role and its demands can evolve as an individual progresses from an early-career position to a more senior management level. This assessment aims to provide an honest and balanced perspective, helping prospective Inventory Control Managers set realistic expectations for a career in this field.
Pros
Inventory Control Managers play a critical role in a company's profitability by optimizing stock levels, which directly impacts efficiency and reduces waste. This direct contribution provides a strong sense of purpose and value within the organization.
There is consistent demand for skilled Inventory Control Managers across various industries, including retail, manufacturing, logistics, and healthcare, providing a stable job market. This broad applicability offers good job security.
The role offers opportunities for developing strong analytical and problem-solving skills, as managers constantly analyze data, identify discrepancies, and implement solutions to optimize inventory flow. This intellectual challenge keeps the work engaging.
Inventory Control Managers often have opportunities to implement new technologies and process improvements, allowing them to drive innovation and efficiency within the supply chain. This aspect provides a chance to make a tangible impact.
Salaries for experienced Inventory Control Managers are competitive, especially in larger organizations or industries with complex supply chains, reflecting the critical nature of the role. There is a clear earning potential as experience grows.
This position often provides a clear path for career advancement into broader supply chain management, operations management, or logistics director roles. Demonstrating success in inventory control can open many doors.
The work often involves a mix of office-based analytical tasks and hands-on engagement in the warehouse or production floor, offering a dynamic environment that avoids being confined to a desk all day. This variety can be appealing.
Cons
Inventory Control Managers often face high pressure during peak seasons or unexpected demand spikes, leading to increased workload and potential overtime to prevent stockouts or overstock. This constant vigilance can be mentally taxing.
The role can become highly repetitive, involving routine checks, data entry, and cycle counts, which may lead to monotony for individuals who prefer dynamic or creative work environments. It requires a strong attention to detail for extended periods.
Success in this role heavily depends on the accuracy of data and the reliability of systems, meaning that errors or system failures can directly impact performance and create significant stress. Troubleshooting discrepancies often falls on the manager.
Career progression within pure inventory control can be somewhat limited, often moving from specialist to manager and then potentially to director, but lateral moves into broader supply chain or operations roles may require additional skill development. The path is often linear.
Inventory Control Managers are frequently on their feet, moving around warehouses or production floors, and may work in environments that are not climate-controlled or are noisy. This physical aspect can be demanding over long shifts.
Managing a diverse team of inventory clerks or associates requires strong interpersonal and leadership skills, as issues like employee turnover, training new staff, and conflict resolution are common challenges. People management is a significant component.
The role requires constant adaptation to new technologies, software systems, and best practices in inventory management, meaning continuous learning is necessary to stay effective. Keeping up with these changes can be a challenge.
Frequently Asked Questions
Inventory Control Managers face distinct challenges balancing supply chain efficiency with cost control and accuracy. This section addresses the most common questions about entering and advancing in this crucial role, from mastering inventory software to managing complex logistics and leading teams effectively.
What educational background or certifications are typically required to become an Inventory Control Manager?
Many Inventory Control Managers start with a bachelor's degree in supply chain management, logistics, business administration, or a related field. However, significant experience in warehouse operations, inventory counting, or logistics can often substitute for a specific degree. Certifications like APICS CSCP or CPIM are highly valued and demonstrate specialized knowledge, boosting your competitiveness for this role.
What is the typical career path to become an Inventory Control Manager, and what are the next steps for advancement?
Career progression often starts from roles like inventory clerk, warehouse associate, or logistics coordinator. With 3-5 years of experience in these operational roles, demonstrating strong analytical and organizational skills, you can typically transition into an Inventory Control Manager position. Further advancement can lead to roles such as Supply Chain Manager, Operations Manager, or Director of Logistics.
What are the salary expectations for an Inventory Control Manager, and how do they vary?
An Inventory Control Manager's salary varies significantly based on industry, company size, location, and experience. Entry-level managerial roles might start around $55,000 to $70,000 annually, while experienced managers in larger corporations or specialized industries can earn $80,000 to $100,000+. Performance bonuses tied to inventory accuracy and cost savings are also common.
What is the typical work-life balance for an Inventory Control Manager, and is remote work possible?
The work-life balance can fluctuate. During peak seasons, inventory audits, or system implementations, long hours may be necessary. However, outside of these periods, a standard 40-50 hour work week is common. The role often requires being on-site at a warehouse or distribution center, limiting remote work options, but some larger companies offer hybrid models for administrative tasks.
Is the role of Inventory Control Manager in high demand, and what is the job security like in this field?
The demand for skilled Inventory Control Managers remains strong across various industries, including retail, manufacturing, e-commerce, and healthcare. As supply chains become more complex and technology-driven, companies increasingly rely on efficient inventory management to reduce costs and improve customer satisfaction. This ensures good job security and consistent demand for qualified professionals.
What are the most critical skills and competencies needed to succeed as an Inventory Control Manager?
Key skills include strong analytical abilities for data interpretation, proficiency with inventory management software (e.g., SAP, Oracle, NetSuite), excellent organizational skills, and attention to detail for tracking stock. Leadership and communication skills are also crucial for managing teams and collaborating with other departments like purchasing, sales, and logistics.
What are the biggest challenges or frustrations that Inventory Control Managers face regularly?
Common challenges include maintaining accurate inventory records, especially with high-volume or perishable goods, managing unexpected supply chain disruptions, and optimizing storage space. You will also deal with balancing customer demand with inventory holding costs and implementing new technologies while managing resistance to change from staff.
What does a typical day look like for an Inventory Control Manager?
A typical day involves monitoring inventory levels, analyzing sales forecasts to predict demand, overseeing cycle counts or physical inventories, and investigating discrepancies. You will also manage a team of inventory clerks, coordinate with suppliers and logistics partners, and generate reports on inventory performance, always looking for ways to improve efficiency and reduce waste.
Related Careers
Explore similar roles that might align with your interests and skills:
Inventory Control Analyst
A growing field with similar skill requirements and career progression opportunities.
Explore career guideInventory Control Specialist
A growing field with similar skill requirements and career progression opportunities.
Explore career guideInventory Control Supervisor
A growing field with similar skill requirements and career progression opportunities.
Explore career guideInventory Controller
A growing field with similar skill requirements and career progression opportunities.
Explore career guideInventory Manager
A growing field with similar skill requirements and career progression opportunities.
Explore career guideAssess your Inventory Control Manager readiness
Understanding where you stand today is the first step toward your career goals. Our Career Coach helps identify skill gaps and create personalized plans.
Skills Gap Analysis
Get a detailed assessment of your current skills versus Inventory Control Manager requirements. Our AI Career Coach identifies specific areas for improvement with personalized recommendations.
See your skills gapCareer Readiness Assessment
Evaluate your overall readiness for Inventory Control Manager roles with our AI Career Coach. Receive personalized recommendations for education, projects, and experience to boost your competitiveness.
Assess your readinessSimple pricing, powerful features
Upgrade to Himalayas Plus and turbocharge your job search.
Himalayas
Himalayas Plus
Himalayas Max
Find your dream job
Sign up now and join over 100,000 remote workers who receive personalized job alerts, curated job matches, and more for free!
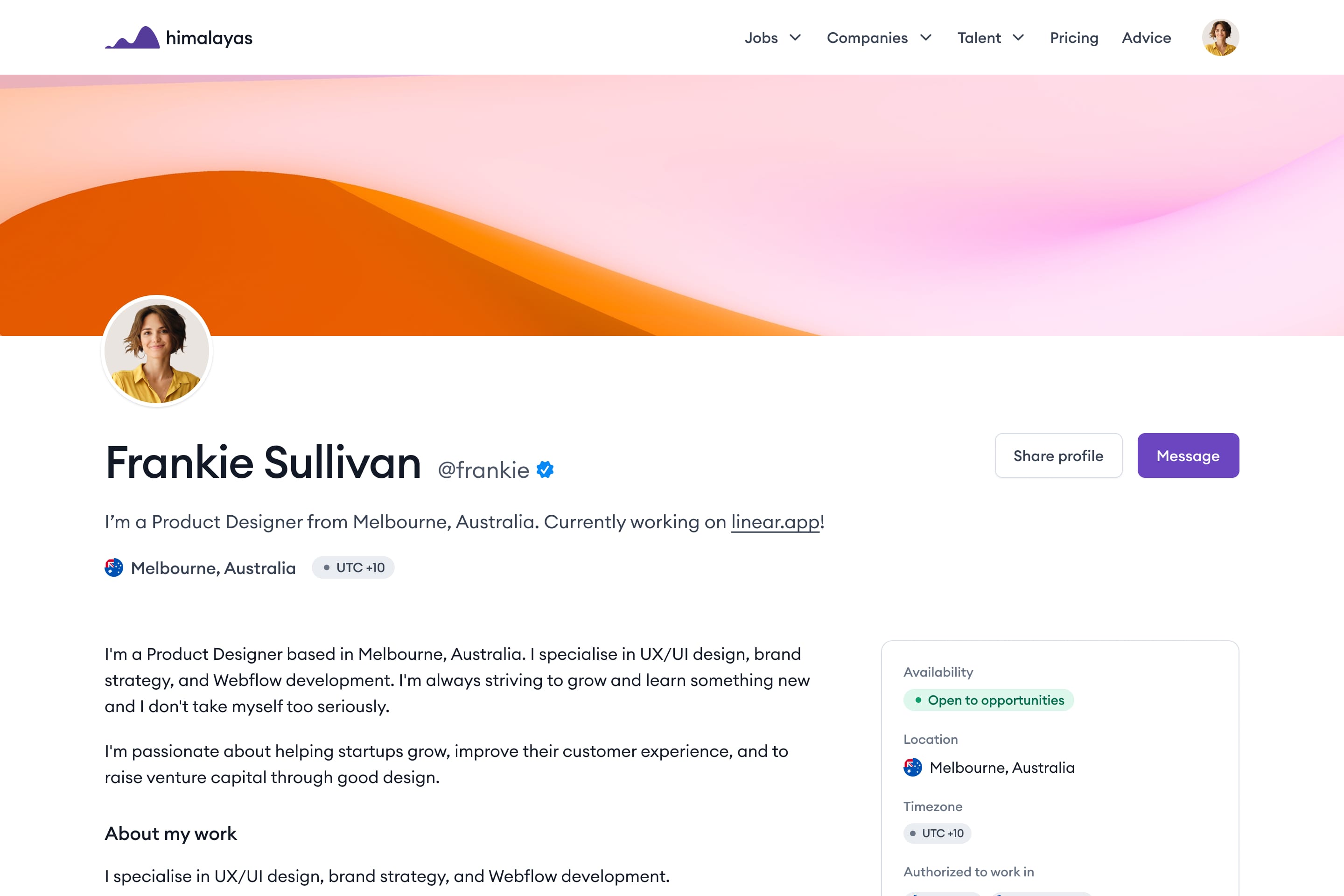