Complete Instrumentation Technician Career Guide
Instrumentation technicians are the unsung heroes of industrial automation, ensuring the precision and reliability of critical control systems that power everything from manufacturing plants to energy grids. They diagnose, calibrate, and maintain complex instruments, directly impacting operational efficiency and safety. This vital role combines hands-on technical skill with problem-solving acumen, offering a stable and rewarding career path in a technology-driven world.
Key Facts & Statistics
Median Salary
$62,320 USD
(U.S. national median, BLS, May 2023)
Range: $45,000 - $90,000+ USD
Growth Outlook
5%
as fast as average (BLS, 2022-2032)
Annual Openings
≈17,400
openings annually (BLS)
Top Industries
Typical Education
Associate's degree in instrumentation technology or a related field, often supplemented by certifications or apprenticeships.
What is an Instrumentation Technician?
An Instrumentation Technician specializes in the installation, calibration, maintenance, and repair of industrial measuring and control instruments. These professionals ensure that automated systems in factories, power plants, and other facilities operate accurately and efficiently. They are crucial for maintaining process control, optimizing production, and ensuring safety in complex industrial environments.
Unlike an Electrician who focuses on power distribution and wiring, or a Mechanic who deals with mechanical components, an Instrumentation Technician's expertise lies specifically in the devices that measure and control variables like pressure, temperature, flow, and level. They bridge the gap between mechanical processes and electronic control systems, ensuring that the data from sensors translates into precise actions by control valves and other actuators.
What does an Instrumentation Technician do?
Key Responsibilities
- Install and calibrate new instrumentation systems, including sensors, transmitters, and control valves, ensuring they meet precise operational specifications.
- Perform routine maintenance and troubleshooting on existing industrial control systems to diagnose and repair malfunctions in pneumatic, electronic, and hydraulic components.
- Conduct preventative maintenance checks on instrumentation, such as loop checks, signal verification, and calibration adjustments, to ensure continuous and accurate operation.
- Interpret and update technical diagrams, schematics, and P&IDs (Piping and Instrumentation Diagrams) to reflect system modifications or repairs.
- Collaborate with engineers and operators to optimize control system performance, identify potential issues, and implement upgrades.
- Document all maintenance activities, calibration results, and repair procedures accurately in maintenance management systems.
- Respond to emergency breakdowns and system failures, quickly identifying root causes and implementing corrective actions to minimize downtime and ensure safety compliance, often under pressure.
Work Environment
Instrumentation Technicians primarily work in industrial settings such as manufacturing plants, power generation facilities, chemical processing plants, and oil and gas refineries. The environment can be noisy, dusty, and may involve working at heights, in confined spaces, or outdoors in varying weather conditions.
Collaboration with engineers, operators, and other technicians is common, often requiring clear communication to resolve complex issues. The work schedule typically involves standard daytime hours, but on-call duties or shift work are frequent for emergency repairs to maintain continuous operations. The pace can vary from routine maintenance to urgent, high-pressure troubleshooting during system failures.
Tools & Technologies
Instrumentation Technicians regularly use a variety of specialized tools and software. They employ calibration devices such as signal generators, multimeters, and pressure calibrators to ensure accuracy. For diagnostics, they rely on oscilloscopes, loop calibrators, and HART communicators.
Their work involves pneumatic and hydraulic tools, along with standard hand tools and power tools for installation and repair. Software applications include Computerized Maintenance Management Systems (CMMS) for logging work orders and maintenance history, as well as proprietary diagnostic software for Programmable Logic Controllers (PLCs) and Distributed Control Systems (DCS). They also work with various sensors, transmitters, and control valves from manufacturers like Emerson, Honeywell, and Siemens.
Instrumentation Technician Skills & Qualifications
Instrumentation Technician qualifications are structured around a strong foundation in electronics, mechanics, and process control. Employers prioritize practical, hands-on experience alongside formal training. Requirements vary significantly based on the industry sector. For example, a technician in a pharmaceutical plant needs different specific certifications than one in an oil refinery or a manufacturing facility.
Entry-level positions often require a technical diploma or associate's degree, combined with relevant internships or apprenticeships. Senior roles typically demand several years of direct experience, specialized certifications, and a proven track record of troubleshooting complex systems. Certifications from organizations like ISA (International Society of Automation) significantly enhance a candidate's profile, demonstrating expertise in specific areas such as Certified Control Systems Technician (CCST).
Formal education provides foundational knowledge, but practical experience often carries more weight in hiring decisions. Alternative pathways like military technical training or extensive vocational programs are highly valued. The field is evolving with increased automation and digitalization, requiring technicians to continuously update their skills in areas like industrial networking, cybersecurity fundamentals, and advanced sensor technologies. A balance between deep specialization in certain instrument types and a broad understanding of various control systems is crucial for career progression.
Education Requirements
Technical Skills
- Calibration and testing of process instruments (pressure, temperature, flow, level, analytical)
- Troubleshooting and repair of control loops (PID controllers, PLCs, DCS systems)
- Reading and interpreting P&ID (Piping and Instrumentation Diagrams) and electrical schematics
- Knowledge of industrial communication protocols (HART, Modbus, Foundation Fieldbus, Profibus)
- Installation and commissioning of field devices and control panels
- Use of specialized calibration equipment (e.g., calibrators, multimeters, oscilloscopes)
- Preventive and predictive maintenance techniques for instrumentation systems
- Basic electrical theory and circuit analysis (AC/DC, Ohm's Law)
- Understanding of control valves, actuators, and positioners
- Familiarity with hazardous area classifications and intrinsic safety principles
- Basic programming or configuration of PLCs (e.g., Rockwell, Siemens) and HMI interfaces
- Data acquisition systems and sensor technologies
Soft Skills
- Problem-solving and diagnostic reasoning: Crucial for identifying and resolving complex issues in control systems and instrumentation quickly and accurately.
- Attention to detail: Essential for precise calibration, wiring, and measurement, ensuring system accuracy and safety in critical industrial environments.
- Safety consciousness: Paramount for adhering to strict safety protocols, especially when working with high voltage, hazardous materials, or pressurized systems.
- Communication and documentation: Important for effectively relaying technical information to engineers, operators, and maintenance teams, and for maintaining accurate records of repairs and calibrations.
- Adaptability and continuous learning: Vital for keeping pace with rapidly evolving technologies and new instrumentation systems in industrial settings.
- Initiative and self-reliance: Necessary for working independently on troubleshooting tasks and finding solutions without constant supervision, particularly in remote or critical environments.
- Team collaboration: Important for coordinating with other technicians, engineers, and production staff to ensure seamless operations and minimize downtime.
- Time management and organization: Essential for prioritizing tasks, managing multiple work orders, and completing calibrations and repairs efficiently to meet production schedules and minimize disruptions.
How to Become an Instrumentation Technician
Breaking into the Instrumentation Technician field offers several pathways, from formal education to on-the-job training, each with varying timelines. For those starting from scratch, pursuing an Associate's degree in Instrumentation, Electronics, or a related engineering technology can take two years and provides a strong theoretical foundation. Alternatively, vocational schools and technical colleges offer focused certificate programs, often completed in 6-12 months, which prioritize hands-on skills directly applicable to the job.
Many entry-level roles value practical experience and certifications over a four-year degree. Apprenticeships, common in industrial sectors, provide paid training and mentorship, typically lasting 3-5 years, and are an excellent way to gain comprehensive skills while earning. Career changers with a background in electrical or mechanical trades may find their transition quicker, potentially requiring only specific instrumentation certifications or a few months of targeted training to bridge skill gaps. The demand for Instrumentation Technicians is strong across various industries like manufacturing, oil and gas, pharmaceuticals, and utilities, meaning opportunities exist in diverse geographic regions and company sizes, from large corporations to smaller local plants.
Understanding the specific industry you wish to enter influences your approach. For example, oil and gas often demand more rigorous safety certifications, while manufacturing might prioritize automation and PLC knowledge. Networking with professionals in the field, attending industry trade shows, and joining professional organizations like the International Society of Automation (ISA) can open doors to mentorship and job opportunities. This field values continuous learning, so demonstrating a commitment to staying current with new technologies and standards is crucial for long-term success.
Step 1
Step 2
Step 3
Step 4
Step 5
Step 6
Education & Training Needed to Become an Instrumentation Technician
Becoming an Instrumentation Technician requires a blend of theoretical knowledge and practical skills. Formal degree programs, typically Associate's degrees in Instrumentation, Electrical, or Mechanical Technology, offer a comprehensive foundation. These 2-year programs often cost between $8,000 and $25,000 annually at community colleges, providing deep understanding of control systems, calibration, and troubleshooting. Graduates from these programs are widely accepted by employers, particularly in large industrial settings, and often have strong job placement rates due to integrated internships and hands-on lab work.
Alternative pathways include vocational training programs, apprenticeships, and specialized certifications. Vocational programs, ranging from 6 to 18 months, focus intensely on specific equipment and industry standards, with costs typically from $5,000 to $15,000. Apprenticeships, often lasting 3-5 years, provide paid on-the-job training combined with classroom instruction, making them a highly cost-effective route. While self-study and online courses can supplement knowledge, direct practical experience with instruments is crucial for this hands-on role. Employers highly value practical experience, often prioritizing candidates with apprenticeship backgrounds or extensive lab work.
Continuous learning is essential for Instrumentation Technicians due to evolving technologies like smart sensors and IoT integration. Staying current involves advanced certifications in specific control systems (e.g., PLC programming, DCS systems) or vendor-specific training. These specialized courses can range from a few hundred to several thousand dollars and typically take days to weeks. The educational investment for this role significantly varies, with formal degrees providing broad career mobility and apprenticeships offering immediate earning potential and practical expertise. Industry-specific certifications from organizations like ISA (International Society of Automation) enhance credibility and demonstrate adherence to quality standards.
Instrumentation Technician Salary & Outlook
Compensation for an Instrumentation Technician varies significantly based on several factors. Geographic location plays a crucial role; areas with a high concentration of industrial facilities, such as the Gulf Coast in the U.S. or major manufacturing hubs, often offer higher salaries due to increased demand and sometimes higher costs of living. Conversely, regions with fewer industrial opportunities may see lower pay scales.
Experience, specialized certifications, and specific skill sets directly impact earning potential. Technicians proficient in advanced calibration techniques, PLC programming, or hazardous environment protocols typically command higher wages. Total compensation extends beyond base salary to include overtime pay, which is common in this role, performance bonuses, and comprehensive benefits packages. These often include health insurance, retirement plans, and allowances for professional development or tool purchases.
Industry-specific trends also influence compensation. Technicians in oil and gas, pharmaceuticals, or aerospace often earn more than those in general manufacturing due to the complexity and criticality of the instrumentation involved. Remote work is rare for this hands-on role, but travel to various sites can sometimes come with per diem rates. When negotiating salary, highlighting specific expertise, proven problem-solving abilities, and relevant certifications provides strong leverage. International markets also present variations, with U.S. figures serving as a benchmark.
Salary by Experience Level
Level | US Median | US Average |
---|---|---|
Junior Instrumentation Technician | $55k USD | $58k USD |
Instrumentation Technician | $69k USD | $72k USD |
Senior Instrumentation Technician | $85k USD | $88k USD |
Lead Instrumentation Technician | $100k USD | $105k USD |
Instrumentation Supervisor | $120k USD | $125k USD |
Market Commentary
The job market for Instrumentation Technicians shows stable demand, driven by the increasing automation across various industries. Projections indicate a steady growth outlook, particularly in sectors adopting advanced manufacturing and process control technologies. The Bureau of Labor Statistics (BLS) forecasts consistent job growth for industrial machinery mechanics, including instrumentation technicians, reflecting the ongoing need for skilled professionals to maintain and troubleshoot complex systems.
Emerging opportunities are appearing in renewable energy, smart manufacturing, and data-driven predictive maintenance. As industries adopt more sophisticated sensors and IoT devices, the role evolves to include data interpretation and network integration. This shift creates a need for technicians with hybrid skills in both traditional instrumentation and IT/data analytics. The supply of qualified technicians often struggles to meet demand, especially for those with specialized certifications in areas like cybersecurity for industrial control systems or specific vendor platforms.
This profession is relatively recession-resistant due to the critical nature of maintaining operational efficiency and safety in industrial plants. Geographic hotspots for instrumentation technicians include Texas, Louisiana, California, and the Northeast U.S., where large chemical plants, refineries, and pharmaceutical manufacturers are concentrated. Future-proofing involves continuous learning, particularly in automation software, industrial networking, and diagnostic tools, to adapt to technological advancements and avoid potential impacts from AI-driven diagnostics.
Instrumentation Technician Career Path
Career progression for an Instrumentation Technician unfolds through increasing technical mastery, problem-solving complexity, and leadership responsibilities. Professionals typically begin by learning foundational skills, then advance to handle more complex systems independently. The pathway often bifurcates into an individual contributor (IC) track, focusing on deep technical specialization, or a management/leadership track, emphasizing team oversight and project coordination.
Advancement speed is influenced by continuous skill development, particularly in advanced control systems and automation. Company size and industry sector also play a role; larger corporations in highly automated industries may offer more structured progression paths. Specialization in specific types of instrumentation, such as pneumatic, hydraulic, or electronic systems, can accelerate career growth, as can obtaining relevant certifications.
Networking within professional organizations and mentorship from experienced technicians are crucial for identifying opportunities and gaining insights. Lateral moves may involve shifting between different industrial environments, like manufacturing, oil and gas, or pharmaceuticals, to broaden experience. Common career pivots include moving into controls engineering, field service engineering, or technical training roles.
Junior Instrumentation Technician
0-2 yearsKey Focus Areas
Instrumentation Technician
2-5 yearsKey Focus Areas
Senior Instrumentation Technician
5-8 yearsKey Focus Areas
Lead Instrumentation Technician
8-12 yearsKey Focus Areas
Instrumentation Supervisor
12+ yearsKey Focus Areas
Junior Instrumentation Technician
0-2 yearsPerforms routine maintenance, calibration, and basic troubleshooting of instrumentation and control systems under close supervision. Assists senior technicians with more complex tasks. Learns to identify common equipment failures and follows established procedures for repairs. Works on individual components or simple systems.
Key Focus Areas
Develop foundational knowledge of instrumentation principles, safety protocols, and basic hand tools. Learn to read schematics and P&IDs. Focus on troubleshooting basic electrical and mechanical issues. Acquire practical experience with calibration procedures and preventive maintenance tasks under direct supervision.
Instrumentation Technician
2-5 yearsIndependently performs maintenance, calibration, and troubleshooting on a variety of instrumentation, including transmitters, sensors, and control valves. Diagnoses and resolves complex issues with minimal supervision. Participates in system startups and commissioning. May provide guidance to junior technicians.
Key Focus Areas
Enhance diagnostic and troubleshooting skills for complex control loops and systems. Master calibration techniques for various instrument types. Develop proficiency in using diagnostic software and advanced test equipment. Begin understanding process control theory and its application.
Senior Instrumentation Technician
5-8 yearsServes as a subject matter expert for complex instrumentation and control systems. Leads diagnostic efforts for challenging system malfunctions. Designs and implements modifications to improve system performance and reliability. Provides technical guidance and mentorship to other technicians. Manages specific projects or system upgrades.
Key Focus Areas
Develop expertise in advanced control strategies, PLC/DCS programming, and network communication protocols. Focus on system optimization and reliability improvements. Cultivate strong analytical and problem-solving skills for complex system failures. Begin mentoring junior staff and leading small projects.
Lead Instrumentation Technician
8-12 yearsCoordinates and oversees the daily activities of a team of instrumentation technicians. Plans and schedules maintenance and calibration tasks. Leads complex installation and commissioning projects. Acts as a primary technical liaison with engineering and operations departments. Ensures compliance with safety and quality standards.
Key Focus Areas
Focus on project management, team coordination, and strategic planning for instrumentation initiatives. Develop leadership skills, including delegation, conflict resolution, and performance feedback. Improve communication skills for interacting with engineering, operations, and management. Understand budgeting and resource allocation.
Instrumentation Supervisor
12+ yearsManages the overall instrumentation department or a significant section of it. Responsible for budgeting, staffing, and performance management of the instrumentation team. Develops and implements maintenance strategies and capital improvement projects. Drives continuous improvement initiatives and ensures adherence to industry best practices and regulatory requirements. Reports directly to operations or engineering management.
Key Focus Areas
Acquire strong managerial competencies, including team development, performance management, and strategic workforce planning. Develop a comprehensive understanding of operational budgets and capital expenditure planning. Focus on long-term system reliability, technology adoption, and continuous improvement methodologies. Build strong cross-functional leadership skills.
Job Application Toolkit
Ace your application with our purpose-built resources:
Instrumentation Technician Resume Examples
Proven layouts and keywords hiring managers scan for.
View examplesInstrumentation Technician Cover Letter Examples
Personalizable templates that showcase your impact.
View examplesTop Instrumentation Technician Interview Questions
Practice with the questions asked most often.
View examplesInstrumentation Technician Job Description Template
Ready-to-use JD for recruiters and hiring teams.
View examplesGlobal Instrumentation Technician Opportunities
Instrumentation technicians maintain and calibrate industrial control systems globally. Their skills are highly transferable across diverse sectors like manufacturing, energy, and pharmaceuticals. International demand for this role remains strong, especially in rapidly industrializing economies and regions with aging infrastructure. Cultural and regulatory differences often affect safety standards and equipment certifications. Professionals seek international roles for higher pay, specialized projects, and diverse experience, with some global certifications like ISA standards aiding mobility.
Global Salaries
Salaries for instrumentation technicians vary significantly by region and industry. In North America, particularly the U.S. and Canada, annual salaries range from $60,000 to $95,000 USD, often higher in oil and gas sectors. Europe sees ranges from €40,000 to €70,000 annually (approximately $43,000-$75,000 USD) in countries like Germany and the Netherlands, with higher costs of living in Western Europe impacting purchasing power.
Asia-Pacific markets, including Australia and Singapore, offer competitive salaries from $70,000 to $100,000 AUD/SGD ($46,000-$74,000 USD), reflecting high demand in mining and advanced manufacturing. Middle Eastern countries, especially Saudi Arabia and UAE, often provide tax-free salaries from $45,000 to $80,000 USD, plus housing and transport allowances, significantly increasing take-home pay.
Latin America's salaries are generally lower, ranging from $25,000 to $45,000 USD in countries like Brazil and Mexico, but the cost of living is also considerably lower, improving local purchasing power. Salary structures globally often include benefits like health insurance and retirement plans, though their scope differs. Tax implications vary widely; for instance, some countries offer lower income tax rates or specific expatriate tax benefits. Experience and specialized skills, such as PLC programming or specific industry certifications, consistently command higher compensation internationally.
Remote Work
International remote work for instrumentation technicians is very limited. This role primarily involves hands-on work with physical equipment, requiring on-site presence for installation, calibration, and maintenance. Therefore, digital nomad opportunities are not applicable for this profession.
However, some aspects like remote diagnostics or software configuration of instrumentation systems might be performed off-site. Such tasks typically support an on-site team or involve highly specialized troubleshooting. Employers generally do not offer fully remote international positions for core instrumentation technician duties. Salary expectations for these limited remote support roles would depend on the specific task and required expertise rather than geographic arbitrage.
Visa & Immigration
Instrumentation technicians typically qualify for skilled worker visas in many countries. Popular destinations include Canada (Express Entry), Australia (Skilled Migration Program), Germany (EU Blue Card), and Middle Eastern nations (employer-sponsored work permits). Requirements often include a relevant diploma or associate degree, several years of experience, and sometimes English or local language proficiency tests.
Credential recognition is crucial; applicants often need their qualifications assessed by a designated body in the target country. Visa processing times vary, from a few months to over a year, depending on the country and application backlog. Pathways to permanent residency often exist after several years of continuous skilled employment.
Specific industry certifications, like those from the International Society of Automation (ISA), can strengthen a visa application. Some countries offer fast-track programs for in-demand trades. Family visas for spouses and dependents are generally available, contingent on the primary applicant's visa approval and sufficient financial means.
2025 Market Reality for Instrumentation Technicians
Understanding current market conditions is crucial for instrumentation technicians navigating their careers. The industry has seen significant shifts since 2023, influenced by post-pandemic reshoring initiatives, supply chain disruptions, and the accelerating integration of AI into industrial automation.
Broader economic factors, such as interest rates and energy prices, directly impact capital investment in new facilities, which in turn affects demand for instrumentation professionals. Market realities for this role vary significantly by experience level, with senior technicians possessing specialized skills remaining in high demand, while entry-level roles face more competition. Geographic location and the size of the employing company also play a major role, as industrial concentration dictates local opportunities. This analysis provides an honest assessment to help set realistic expectations.
Current Challenges
Instrumentation technicians face increased competition, particularly for entry-level roles, as some companies seek to consolidate maintenance functions. Economic slowdowns can delay or halt new industrial projects, directly impacting demand for new installations and commissioning work.
Maintaining up-to-date skills in rapidly evolving digital control systems and AI-driven diagnostics presents a continuous challenge. The job search timeline can extend to several months, especially for specialized roles or in less industrialized regions.
Growth Opportunities
Strong demand persists for instrumentation technicians specializing in advanced automation and predictive maintenance. Emerging roles include those focused on industrial cybersecurity for control systems, data interpretation from smart instruments, and integration of AI-powered diagnostic tools.
Technicians who develop expertise in specific industry standards, such as those for pharmaceutical (GMP) or oil and gas (API) sectors, gain a significant competitive edge. Underserved markets often exist in regions with aging infrastructure requiring modernization, or in newly developing industrial zones. Companies are keen to hire professionals who can optimize existing systems for efficiency rather than just repair them.
Acquiring certifications in specific PLC platforms (e.g., Siemens, Rockwell), SCADA systems, or industrial networking protocols enhances marketability. Pursuing training in data analytics for industrial processes or basic programming for automation scripts can also open new doors. Strategic career moves might involve targeting companies investing heavily in Industry 4.0 technologies or transitioning to roles focused on system integration and optimization rather than routine maintenance. The energy transition also creates opportunities in renewable energy instrumentation.
Current Market Trends
Demand for instrumentation technicians remains steady in critical infrastructure sectors like energy, manufacturing, and pharmaceuticals, but growth has moderated from previous peaks. Companies are prioritizing efficiency and automation, leading to a focus on technicians who can maintain and troubleshoot advanced digital and networked control systems.
The integration of AI and machine learning into predictive maintenance platforms is transforming the role. Technicians now need skills in interpreting data from smart sensors and AI diagnostics, shifting from purely mechanical tasks to more analytical and software-driven responsibilities. This impacts hiring criteria, with employers seeking candidates proficient in PLC programming, SCADA systems, and industrial IoT protocols.
Salary trends show modest growth, with significant premiums for specialists in highly regulated industries or those with expertise in complex DCS (Distributed Control Systems). Market saturation is minimal at the senior level, but entry-level positions often see more applicants due to vocational training programs producing a steady stream of graduates. Remote work is rare for this hands-on role, but regional demand varies; industrial hubs like the Gulf Coast or parts of the Midwest show stronger activity compared to regions with less heavy industry.
Hiring can be cyclical, often tied to project lifecycles and capital expenditure budgets within large industrial companies. New plant constructions or significant upgrades drive temporary surges in demand for installation and commissioning expertise.
Emerging Specializations
The field of instrumentation is undergoing significant transformation, driven by advancements in automation, sensor technology, and data analytics. These technological shifts are not just optimizing existing processes but actively creating entirely new specialization opportunities for Instrumentation Technicians. Understanding and positioning oneself within these emerging areas is crucial for career advancement and securing high-demand roles in 2025 and beyond.
Early adoption and specialization in these cutting-edge fields often lead to premium compensation and accelerated career growth. While established specializations offer stability, emerging areas provide a distinct competitive advantage, placing professionals at the forefront of innovation. These nascent fields, while requiring proactive skill development, transition into mainstream roles with significant job opportunities within the next five to ten years.
Pursuing emerging specializations involves a balance of risk and reward. It demands continuous learning and adaptability, but the payoff includes higher earning potential and greater influence in shaping future industry practices. Strategic investment in these new skill sets ensures relevance and leadership in a rapidly evolving industrial landscape.
Industrial IoT Instrumentation Specialist
The proliferation of IoT devices across industrial settings is creating a demand for technicians who can install, calibrate, and maintain smart sensors and networked control systems. This specialization involves ensuring seamless data flow from physical instruments to cloud platforms, enabling predictive maintenance and real-time operational insights. It requires understanding network protocols and data integrity in addition to traditional instrumentation skills.
Renewable Energy Instrumentation Technician
The increasing focus on renewable energy sources like solar, wind, and geothermal power requires specialized instrumentation expertise. Technicians in this area work with advanced sensors and control systems specific to energy generation, storage, and grid integration. This includes optimizing performance, ensuring safety, and maintaining the complex instrumentation found in large-scale renewable energy facilities.
Robotics and Automation Instrumentation
Advanced robotics and automated manufacturing lines rely heavily on precise instrumentation for operation and quality control. This specialization focuses on integrating, calibrating, and troubleshooting the sensors, actuators, and control feedback loops within robotic systems. It involves working closely with robotic engineers to ensure optimal performance and safety in highly automated environments.
Environmental Compliance Instrumentation Specialist
As industries move towards more sustainable practices, there is a growing need for instrumentation specialists focused on environmental monitoring and compliance. This involves installing, calibrating, and maintaining sensors that measure emissions, water quality, and other environmental parameters. Technicians ensure data accuracy for regulatory reporting and operational efficiency in reducing environmental impact.
AI-Ready Instrumentation Technician
The integration of artificial intelligence and machine learning into industrial control systems is transforming how instrumentation data is used. This specialization involves setting up instrumentation to feed clean, reliable data into AI models for predictive analytics, anomaly detection, and process optimization. Technicians ensure the accuracy and integrity of data streams essential for AI-driven decision-making.
Pros & Cons of Being an Instrumentation Technician
Making informed career decisions requires understanding both the benefits and challenges of a professional path. An instrumentation technician's experience can vary significantly based on the industry, company culture, and specific systems they maintain. This assessment highlights realistic advantages and genuine challenges, helping you set appropriate expectations. Aspects that one person finds appealing, such as hands-on problem-solving, another might find tedious. Similarly, work-life balance and daily tasks can differ at various career stages, from entry-level to senior roles. This balanced view aims to provide a clear picture of what this specialized technical career truly entails.
Pros
- Instrumentation technicians are in consistent demand across various industries, including manufacturing, energy, pharmaceuticals, and utilities, ensuring strong job security and diverse employment opportunities.
- The role offers significant intellectual stimulation through troubleshooting complex electronic, pneumatic, and hydraulic systems, requiring logical thinking and problem-solving skills.
- Instrumentation technicians gain highly specialized and transferable skills in calibration, maintenance, and repair of precision equipment, which are valuable across many technical fields.
- Many positions offer competitive salaries and benefits packages, especially in sectors with critical infrastructure or continuous operations where skilled technicians are essential.
- The job often involves hands-on work with advanced technology, providing a sense of accomplishment from directly impacting operational efficiency and safety.
- Instrumentation technicians typically work in a structured environment with clear procedures, providing a predictable daily routine once systems are stable.
- There are opportunities for continuous professional development through manufacturer training, industry certifications, and on-the-job learning as technology advances.
Cons
- Instrumentation technicians often work in environments with potential hazards like high voltage, pressure systems, or hazardous chemicals, requiring strict adherence to safety protocols and constant vigilance.
- The job frequently involves troubleshooting complex systems, which can be mentally demanding and frustrating when issues are intermittent or difficult to diagnose.
- Many roles require working irregular hours, including evenings, weekends, or on-call shifts, especially in industries like manufacturing or energy where operations run continuously.
- The work can be physically demanding, involving lifting heavy equipment, climbing ladders, working in confined spaces, or standing for long periods.
- Instrumentation technology evolves rapidly, necessitating continuous learning and training to stay updated with new equipment, software, and industry standards.
- Career advancement opportunities may be limited without pursuing further education or specialized certifications, as many roles are highly technical and hands-on.
- The precision required in calibrating and repairing instruments means even small errors can have significant consequences, leading to high-pressure situations and the need for meticulous attention to detail at all times.
Frequently Asked Questions
Instrumentation Technicians face unique challenges maintaining complex control systems across various industries. This section addresses the most common questions about entering this specialized field, from required technical skills and certifications to career advancement and the hands-on nature of the work.
What specific qualifications or certifications do I need to become an Instrumentation Technician?
Most Instrumentation Technician roles require a diploma or associate's degree in instrumentation, electronics, or a related engineering technology field. Some positions accept extensive relevant experience or completion of an apprenticeship program in lieu of a degree. Certifications like ISA's Certified Control Systems Technician (CCST) are highly valued and can significantly boost your employability and demonstrate expertise.
How long does it take to become a qualified Instrumentation Technician if I'm starting from scratch?
Becoming job-ready typically takes 2-4 years, depending on your chosen path. An associate's degree program usually lasts two years, followed by entry-level positions where you gain practical experience. Apprenticeship programs can take 3-4 years but provide hands-on training and often lead directly to employment. The key is consistent practical application of theoretical knowledge.
What are the typical salary expectations for an Instrumentation Technician, both entry-level and experienced?
Starting salaries for Instrumentation Technicians typically range from $45,000 to $60,000 annually, varying by industry, location, and experience. With several years of experience and specialized skills, salaries can increase to $70,000 - $90,000 or more. Overtime opportunities are often available, especially in industrial settings, which can significantly boost overall earnings.
What is the typical work-life balance for an Instrumentation Technician, considering shift work or on-call duties?
Work-life balance can vary significantly. In industrial settings like manufacturing plants or oil and gas, you might work shifts, including nights, weekends, or be on call, especially for critical system maintenance. Other roles, like those in laboratories or less critical facilities, may offer more standard daytime hours. Be prepared for occasional emergency call-outs.
Is the Instrumentation Technician field growing, and what is the job security like?
The job market for Instrumentation Technicians is generally stable and growing, driven by increasing automation across industries. As technology advances, the demand for skilled professionals who can install, calibrate, and maintain complex control systems remains strong. Industries like manufacturing, energy, pharmaceuticals, and utilities consistently need these specialized skills, ensuring good job security.
What are the common career advancement opportunities for an Instrumentation Technician?
Career growth paths for Instrumentation Technicians are robust. You can advance to lead technician roles, specializing in specific types of equipment or systems. Many technicians transition into supervisory positions, maintenance planning, or reliability engineering. Further education can lead to roles as instrumentation engineers, control systems integrators, or technical trainers.
What are the biggest challenges or specific difficulties an Instrumentation Technician faces daily?
A common challenge is adapting to rapidly evolving technologies and complex integrated systems. Technicians must continuously update their skills to work with new software, communication protocols, and smart instrumentation. Troubleshooting intricate intermittent faults also requires strong analytical skills and patience. Working in diverse and sometimes hazardous environments also presents unique safety considerations.
Can Instrumentation Technicians work remotely, or is it primarily an on-site role?
Remote work is generally not common for Instrumentation Technicians because the role is inherently hands-on and requires direct interaction with physical equipment. While some planning, documentation, or diagnostic analysis might be done remotely, the core tasks of installation, calibration, maintenance, and troubleshooting necessitate being on-site. Expect to work primarily at industrial facilities or client locations.
Related Careers
Explore similar roles that might align with your interests and skills:
Automation Technician
A growing field with similar skill requirements and career progression opportunities.
Explore career guideInstrument Engineer
A growing field with similar skill requirements and career progression opportunities.
Explore career guideInstrument Technician
A growing field with similar skill requirements and career progression opportunities.
Explore career guideInstrumentation Engineer
A growing field with similar skill requirements and career progression opportunities.
Explore career guideElectronic Instrument Testing Technician
A growing field with similar skill requirements and career progression opportunities.
Explore career guideAssess your Instrumentation Technician readiness
Understanding where you stand today is the first step toward your career goals. Our Career Coach helps identify skill gaps and create personalized plans.
Skills Gap Analysis
Get a detailed assessment of your current skills versus Instrumentation Technician requirements. Our AI Career Coach identifies specific areas for improvement with personalized recommendations.
See your skills gapCareer Readiness Assessment
Evaluate your overall readiness for Instrumentation Technician roles with our AI Career Coach. Receive personalized recommendations for education, projects, and experience to boost your competitiveness.
Assess your readinessSimple pricing, powerful features
Upgrade to Himalayas Plus and turbocharge your job search.
Himalayas
Himalayas Plus
Himalayas Max
Find your dream job
Sign up now and join over 100,000 remote workers who receive personalized job alerts, curated job matches, and more for free!
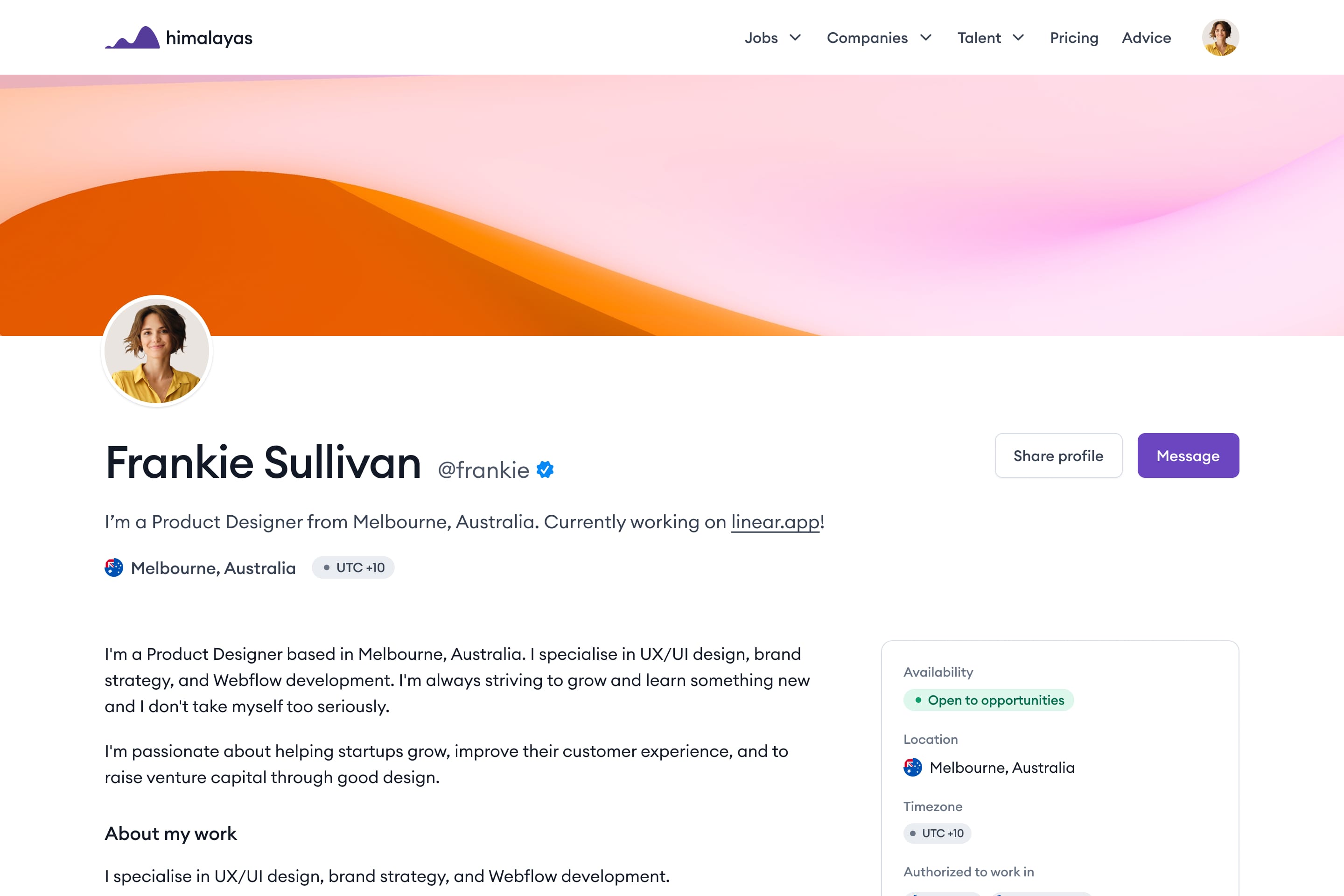