Complete Instrument Technician Career Guide
Instrument Technicians are the unsung heroes maintaining the precision and reliability of complex industrial control systems, ensuring everything from power grids to manufacturing plants operate safely and efficiently.
You diagnose, repair, and calibrate the sensors, transmitters, and automated devices critical to modern industry, offering a hands-on career with direct impact on operational success and safety.
This specialized role combines technical skill with problem-solving, opening doors to diverse sectors seeking expertise in highly automated environments.
Key Facts & Statistics
Median Salary
$73,080 USD
Range: $45k - $100k+ USD
Growth Outlook
6%
as fast as average (2022-2032)
Annual Openings
≈17,200
openings annually
Top Industries
Typical Education
Associate's degree in instrumentation technology or electronics, or completion of an apprenticeship program
What is an Instrument Technician?
An Instrument Technician specializes in the installation, calibration, maintenance, and repair of measurement and control instruments used in industrial processes. These professionals ensure that critical equipment, from temperature sensors and pressure gauges to flow meters and control valves, operates accurately and reliably. Their work is vital for maintaining process efficiency, product quality, and operational safety in complex industrial environments.
This role differs significantly from an Electrician, who primarily focuses on power distribution, wiring, and general electrical systems, or a PLC Programmer, who writes and optimizes the logic for automated control systems. An Instrument Technician bridges the gap between the physical process and the control system, specifically ensuring the integrity and accuracy of the data input (measurements) and the physical output (control actions) of automated processes. They troubleshoot issues with the instruments themselves, rather than the core electrical power or the programming logic.
What does an Instrument Technician do?
Key Responsibilities
- Calibrate and adjust various industrial instrumentation, including transmitters, sensors, and control valves, to ensure accurate readings and proper operation.
- Perform routine preventative maintenance on measurement and control devices to minimize downtime and extend equipment lifespan.
- Diagnose and troubleshoot complex electrical, pneumatic, and electronic instrumentation issues using schematics and diagnostic tools.
- Install new instrumentation systems, including wiring, tubing, and mounting, following engineering specifications and safety protocols.
- Document all maintenance, calibration, and repair activities meticulously in computerized maintenance management systems (CMMS).
- Respond to emergency breakdowns and provide rapid repair to critical process control systems.
- Collaborate with operations and engineering teams to optimize process control strategies and improve system reliability and performance.
Work Environment
Instrument technicians typically work in industrial settings such as manufacturing plants, power generation facilities, oil and gas refineries, chemical plants, and water treatment facilities. The environment can be challenging, involving exposure to varying temperatures, noise, and sometimes hazardous materials, requiring strict adherence to safety protocols.
The role often involves a mix of independent work on specific instruments and close collaboration with operations, maintenance, and engineering teams. Schedules can vary, with some roles being standard day shifts and others requiring on-call duties or rotating shifts to support continuous operations. The pace is often fast, especially when responding to critical equipment failures, demanding quick and accurate problem-solving.
Tools & Technologies
Instrument technicians regularly use a wide array of specialized tools and technologies to perform their duties. They work with precision calibration equipment such as HART communicators, signal generators, multimeters, and pressure calibrators to ensure accuracy. For diagnostics and repair, they utilize oscilloscopes, loop calibrators, and various hand tools like wrenches, screwdrivers, and soldering irons.
Software includes Computerized Maintenance Management Systems (CMMS) like SAP PM, Maximo, or Infor EAM for work order management, scheduling, and historical data tracking. They also interact with Distributed Control Systems (DCS) and Programmable Logic Controllers (PLC) software (e.g., Rockwell Automation, Siemens, Emerson DeltaV) for troubleshooting and system configuration. Understanding of industrial communication protocols like Modbus, Foundation Fieldbus, and Profibus is essential for modern instrumentation.
Instrument Technician Skills & Qualifications
Instrument Technicians play a critical role in ensuring the accuracy, reliability, and safety of industrial control systems. Their qualifications are a blend of formal education, practical experience, and specific certifications. Requirements typically vary significantly by industry sector, with highly regulated industries like pharmaceuticals, oil & gas, and nuclear power demanding more rigorous qualifications and certifications than general manufacturing.
For entry-level positions, a vocational diploma or an associate's degree is often the baseline. However, practical, hands-on experience gained through apprenticeships or military service holds substantial weight, sometimes even more than a four-year degree. Senior roles, particularly those involving complex troubleshooting or system design, may prefer candidates with a bachelor's degree in instrumentation or electrical engineering technology. Certifications from organizations like the International Society of Automation (ISA) are highly valued across all levels, demonstrating specialized knowledge and commitment to the profession.
The skill landscape for Instrument Technicians is continuously evolving with the advent of Industry 4.0 and advanced automation. Traditional mechanical and electrical skills remain foundational, but proficiency in digital communication protocols, PLC programming, and cybersecurity for industrial control systems is increasingly vital. Employers prioritize a balance between deep technical expertise in specific instrumentation types and a broad understanding of integrated control systems. Misconceptions often include underestimating the critical role of data interpretation and diagnostic software, or overemphasizing purely mechanical aptitude without considering the electronic and software components.
Education Requirements
Technical Skills
- Calibration and troubleshooting of process control instrumentation (pressure, temperature, flow, level, analytical)
- Distributed Control Systems (DCS) and Programmable Logic Controllers (PLC) hardware and software diagnostics
- Industrial communication protocols (e.g., HART, Foundation Fieldbus, Profibus, Modbus TCP/IP)
- Electrical wiring, conduit installation, and control panel termination
- Loop checking, commissioning, and startup of new instrumentation systems
- Reading and interpreting Process & Instrumentation Diagrams (P&IDs), electrical schematics, and loop diagrams
- Precision measurement tools and test equipment (multimeters, calibrators, oscilloscopes)
- Preventive and predictive maintenance techniques for instrumentation assets
- Basic understanding of cybersecurity principles for industrial control systems
- Variable Frequency Drives (VFD) installation, configuration, and troubleshooting
- Hydraulic and pneumatic control systems maintenance and repair
- Computerized Maintenance Management Systems (CMMS) operation for work orders and asset tracking
Soft Skills
- Problem-solving and Analytical Thinking: Crucial for diagnosing complex instrument malfunctions, often involving multiple variables like electrical, pneumatic, and communication issues.
- Attention to Detail: Essential for precise calibration, wiring, and configuration of instruments, as even minor errors can lead to significant operational failures or safety hazards.
- Safety Consciousness: Paramount in industrial environments, requiring strict adherence to safety protocols when working with high voltage, hazardous materials, or pressurized systems.
- Technical Communication: Necessary for accurately documenting work, articulating issues to engineers, and explaining procedures to operators, ensuring clear understanding across teams.
- Adaptability and Continuous Learning: The field evolves rapidly with new technologies; technicians must quickly learn new instruments, software, and diagnostic tools.
- Teamwork and Collaboration: Often working as part of a maintenance or operations team, requiring effective coordination with electricians, mechanics, and process engineers.
- Time Management and Organization: Important for prioritizing tasks, managing multiple instrument calibration schedules, and ensuring efficient workflow to minimize downtime.
- Patience and Persistence: Troubleshooting complex intermittent issues often requires methodical, patient investigation and repeated testing until the root cause is identified and resolved.
How to Become an Instrument Technician
Entering the Instrument Technician field offers multiple pathways, whether you are a complete beginner or transitioning from a related trade. While a formal associate's degree in instrumentation, electronics, or a related engineering technology is a common route, many successful technicians begin with vocational training programs, apprenticeships, or military experience. Expect a typical timeline of 1-2 years for vocational training or an associate's degree, followed by a few months for job searching.
The hiring landscape for Instrument Technicians varies significantly by industry and geographic region. For example, oil and gas, manufacturing, and chemical processing hubs often have high demand, offering competitive wages and structured apprenticeship programs. Smaller companies or those in less industrialized areas may prioritize candidates with broader electrical or mechanical skills, rather than specialized instrumentation knowledge. Overcoming barriers often involves gaining practical experience through internships or entry-level helper roles.
Building a strong professional network and seeking mentorship are crucial for navigating this field. Industry connections can open doors to internships, apprenticeships, and job opportunities that are not publicly advertised. Focus on demonstrating practical skills and a commitment to continuous learning, as employers prioritize hands-on capability and problem-solving aptitude over just academic credentials.
Step 1
Step 2
Step 3
Step 4
Step 5
Step 6
Education & Training Needed to Become an Instrument Technician
Becoming an Instrument Technician involves a blend of theoretical knowledge and practical skills, often acquired through various educational pathways. Formal degrees, such as Associate of Applied Science (AAS) in Instrumentation, Industrial Electronics, or Electromechanical Technology, provide a strong theoretical foundation. These 2-year programs typically cost between $10,000 and $25,000 at community colleges, focusing on control systems, calibration, and troubleshooting. Graduates from these programs gain a comprehensive understanding of industrial instrumentation, making them well-prepared for entry-level positions.
Alternative pathways include vocational training programs and apprenticeships. Vocational schools offer focused, hands-on training that can range from 6 months to 18 months, with costs from $5,000 to $15,000. Apprenticeships, often sponsored by companies or unions, combine on-the-job training with classroom instruction. These are typically 3-5 years long and often pay apprentices during their training, making them a cost-effective option. While a degree is valued, employers highly regard hands-on experience and industry certifications like ISA's Certified Control Systems Technician (CCST). Continuous learning is crucial in this field, with new technologies requiring ongoing professional development.
The market perception of credentials varies; while a degree offers a broader understanding, practical experience from vocational training or apprenticeships is often equally, if not more, critical for employer acceptance. Educational needs also depend on the industry and specialization; for instance, process control in oil and gas may demand different expertise than medical instrumentation. Practical experience often outweighs theoretical knowledge in day-to-day operations. Emerging trends include the integration of IoT and automation, which necessitates ongoing training in digital control systems. Investing in specialized certifications or advanced training can significantly enhance career prospects and earning potential, reflecting a strong cost-benefit return for professional growth.
Instrument Technician Salary & Outlook
Compensation for an Instrument Technician varies significantly based on several factors. Geographic location plays a crucial role, with higher salaries typically found in regions with a strong industrial presence, such as the Gulf Coast or areas with extensive manufacturing and energy sectors. Cost of living also impacts these figures; technicians in high cost-of-living areas often command higher wages.
Experience, specialized skills, and certifications directly influence earning potential. Technicians with expertise in complex control systems, calibration, or specific industry equipment (e.g., oil and gas, pharmaceuticals) can negotiate premium compensation. Total compensation extends beyond base salary to include overtime pay, which is common in this field due to maintenance schedules and emergency repairs. Benefits packages, including health insurance, retirement contributions like 401k plans, and paid time off, form a significant part of the overall value.
Industry-specific trends also drive salary growth. The increasing complexity of automated systems and the demand for precision in manufacturing push salaries upward for skilled technicians. Companies in critical infrastructure or highly regulated industries often offer more competitive packages. While remote work is less common for hands-on roles, some senior or supervisory positions may involve remote oversight or planning, impacting location-based salary expectations. International market variations exist, and these figures are primarily benchmarked against the United States Dollar (USD).
Salary by Experience Level
Level | US Median | US Average |
---|---|---|
Junior Instrument Technician | $55k USD | $58k USD |
Instrument Technician | $68k USD | $72k USD |
Senior Instrument Technician | $82k USD | $85k USD |
Lead Instrument Technician | $92k USD | $95k USD |
Instrument Supervisor | $100k USD | $105k USD |
Market Commentary
The job market for Instrument Technicians shows steady demand, driven by the ongoing need to maintain and calibrate complex industrial equipment across various sectors. Industries such as manufacturing, energy (oil, gas, renewables), utilities, and pharmaceuticals heavily rely on precise instrumentation for operational efficiency and safety. The increasing automation of industrial processes means a continuous requirement for skilled technicians to install, troubleshoot, and repair these advanced systems.
The U.S. Bureau of Labor Statistics projects stable growth for industrial machinery mechanics, including instrument technicians, with a focus on specialized roles. Demand is particularly strong in geographic hotspots with significant industrial infrastructure, such as Texas, Louisiana, Pennsylvania, and the Midwest. Emerging opportunities include roles in renewable energy facilities and smart manufacturing plants, where new types of sensors and control systems are being implemented. The aging workforce also creates openings as experienced technicians retire.
Supply and demand dynamics vary by region and specialization. There is often a shortage of highly skilled technicians with expertise in advanced digital control systems or specific proprietary equipment. This imbalance can lead to competitive salaries and signing bonuses for qualified candidates. Future-proofing this career involves continuous learning in areas like industrial internet of things (IIoT), cybersecurity for control systems, and predictive maintenance technologies. While some routine tasks may see automation, the diagnostic and complex problem-solving aspects of an Instrument Technician's role remain essential and largely resistant to full automation, ensuring long-term career viability.
Instrument Technician Career Path
Career progression for an Instrument Technician typically involves a deep focus on technical expertise, safety protocols, and problem-solving. Advancement often follows a path from hands-on execution to leadership and strategic oversight. The core distinction lies between remaining an individual contributor, honing specialized technical skills, or transitioning into management roles that involve team supervision and project coordination.
Advancement speed depends on several factors: the technician's demonstrated proficiency, commitment to continuous learning, and the specific industry (e.g., oil and gas, manufacturing, pharmaceuticals). Larger companies or those with complex instrumentation systems may offer more structured progression paths and specialization opportunities. Lateral movement might involve shifting between different types of instrumentation, such as pneumatic, electronic, or analytical systems, or moving into related fields like process control engineering.
Networking within the industry, securing relevant certifications (e.g., ISA CCST), and mentorship play crucial roles in career acceleration. Technicians often pivot into roles like calibration specialists, field service engineers, or even training instructors as they gain extensive experience. Geographical location can also influence opportunities, with concentrations in industrial hubs offering more diverse career trajectories.
Junior Instrument Technician
0-2 yearsKey Focus Areas
Instrument Technician
2-5 yearsKey Focus Areas
Senior Instrument Technician
5-8 yearsKey Focus Areas
Lead Instrument Technician
8-12 yearsKey Focus Areas
Instrument Supervisor
12+ yearsKey Focus Areas
Junior Instrument Technician
0-2 yearsPerforms routine maintenance, calibration, and repair tasks on industrial instrumentation under direct supervision. Assists senior technicians with troubleshooting and complex installations. Documents work performed and adheres strictly to safety regulations and company procedures.
Key Focus Areas
Develop foundational knowledge of instrumentation principles, calibration techniques, and safety procedures. Master the use of basic test equipment and hand tools. Focus on understanding P&IDs and electrical schematics. Build strong communication skills for effective team collaboration.
Instrument Technician
2-5 yearsExecutes maintenance, calibration, and troubleshooting of a wide range of industrial instruments with minimal supervision. Diagnoses and resolves instrument malfunctions. Participates in commissioning new equipment and performs preventative maintenance tasks. Provides technical support to operations personnel.
Key Focus Areas
Enhance troubleshooting skills for various instrument types, including pneumatic, electronic, and smart instruments. Gain proficiency in configuring and programming control systems. Develop independent problem-solving abilities and a deeper understanding of process control loops. Pursue certifications like ISA CCST Level I.
Senior Instrument Technician
5-8 yearsLeads complex troubleshooting efforts and performs intricate calibrations on critical instrumentation. Provides technical guidance and mentorship to junior and mid-level technicians. Collaborates with engineers on system upgrades and new installations. Takes ownership of significant instrument-related projects.
Key Focus Areas
Master complex control system diagnostics and advanced calibration methods. Develop expertise in a specialized area, such as analytical instrumentation or safety instrumented systems. Begin mentoring junior technicians and contributing to procedure improvements. Focus on project planning and execution skills.
Lead Instrument Technician
8-12 yearsOversees the daily activities of a team of instrument technicians, assigning tasks and ensuring adherence to schedules and quality standards. Acts as the primary technical expert for complex instrument issues and system optimizations. Participates in planning major shutdowns and turnaround activities. Ensures compliance with safety and environmental regulations.
Key Focus Areas
Refine leadership and project management skills. Develop strategic thinking regarding instrumentation lifecycle management and reliability. Focus on optimizing maintenance programs and implementing new technologies. Gain a comprehensive understanding of regulatory compliance and budgeting for instrument-related activities.
Instrument Supervisor
12+ yearsManages the entire instrument department or a significant section, including personnel, budget, and strategic planning for instrumentation assets. Develops and implements maintenance strategies to maximize reliability and efficiency. Leads continuous improvement initiatives and technological adoption. Represents the department in broader organizational meetings.
Key Focus Areas
Develop strong managerial and administrative competencies, including performance management, budgeting, and resource allocation. Cultivate strategic planning abilities for long-term instrumentation needs. Focus on cross-departmental collaboration and stakeholder management. Pursue advanced leadership training or relevant business certifications.
Job Application Toolkit
Ace your application with our purpose-built resources:
Instrument Technician Resume Examples
Proven layouts and keywords hiring managers scan for.
View examplesInstrument Technician Cover Letter Examples
Personalizable templates that showcase your impact.
View examplesTop Instrument Technician Interview Questions
Practice with the questions asked most often.
View examplesInstrument Technician Job Description Template
Ready-to-use JD for recruiters and hiring teams.
View examplesGlobal Instrument Technician Opportunities
An Instrument Technician's skills translate globally, as industries worldwide rely on precise measurement and control systems. There is consistent international demand in sectors like manufacturing, oil and gas, pharmaceuticals, and power generation. Regulatory frameworks and industry standards vary by region, impacting specific calibration and maintenance procedures. International opportunities attract technicians seeking diverse experiences and higher earning potential. Certifications such as ISA (International Society of Automation) designations can enhance global mobility.
Global Salaries
Instrument Technician salaries vary significantly across global markets. In North America, a technician can expect to earn between $60,000 and $90,000 USD annually in the USA, or CAD 70,000 to CAD 100,000 in Canada. These figures reflect strong demand in industrial hubs. European salaries range from €35,000 to €60,000 in Germany, and £30,000 to £50,000 in the UK. Scandinavian countries often offer higher pay, but with a higher cost of living.
In the Middle East, particularly in the oil and gas sectors of Saudi Arabia or UAE, salaries can be very competitive, often ranging from $45,000 to $80,000 USD tax-free, alongside benefits like housing allowances. Asia-Pacific regions show a wider range; Australia offers AUD 70,000 to AUD 110,000, while in Southeast Asia, salaries might be lower, around $20,000 to $40,000 USD, but with a lower cost of living. Latin America sees salaries from $15,000 to $35,000 USD, where purchasing power parity is crucial for comparison.
Salary structures also differ. North America often includes robust health benefits and retirement plans. European compensation may feature more generous vacation time and public healthcare. Tax implications significantly affect take-home pay; for example, Nordic countries have higher income taxes than some Middle Eastern nations. Experience and specialized certifications, like those for hazardous areas (ATEX/IECEx), significantly boost international compensation. Some multinational corporations use standardized pay scales for technicians across their global operations, ensuring a degree of consistency.
Remote Work
International remote work for Instrument Technicians is limited due to the hands-on nature of the role, which requires physical presence for installation, calibration, and maintenance. Most opportunities involve on-site work. However, some specialized roles, such as technical support, remote diagnostics, or system design and documentation, might offer hybrid or partially remote options. These roles often require strong communication skills and deep system knowledge.
Legal and tax implications for any remote work across borders are complex, often requiring a permanent establishment or specific work permits. Time zone differences can pose challenges for international team collaboration. Digital nomad visas are generally not suitable for this profession, as most work is client-site dependent. Employers typically require technicians to be located near their operational sites or client facilities. Remote work does not typically impact salary expectations for hands-on roles, as the value remains tied to on-site service delivery.
Visa & Immigration
Instrument Technicians typically pursue skilled worker visas for international employment. Popular destination countries include Canada (Express Entry), Australia (Skilled Nominated/Sponsored visas), Germany (EU Blue Card/Skilled Immigration Act), and the UK (Skilled Worker visa). Requirements often include a relevant diploma or vocational qualification, several years of experience, and sometimes an employer sponsorship.
Credential recognition is vital; some countries require skills assessments through bodies like Trades Recognition Australia or specific German chambers of commerce. Visa timelines vary, from a few months to over a year. English language proficiency tests (IELTS, PTE) are often mandatory for Anglophone countries. Some countries offer fast-track programs for in-demand trades. Pathways to permanent residency usually involve continuous employment and integration into the local society. Family visas for dependents are generally available once the primary applicant secures their work permit.
2025 Market Reality for Instrument Technicians
Understanding current market conditions is critical for Instrument Technicians navigating career paths. The field has evolved significantly since 2023, influenced by post-pandemic reshoring efforts, supply chain shifts, and the accelerating integration of AI and automation within industrial control systems.
Broader economic factors, such as energy prices and manufacturing output, directly impact investment in industrial infrastructure, which in turn dictates technician demand. Market realities for Instrument Technicians also vary by experience level, with senior specialists in high demand, and by geographic region, often concentrating near industrial plants or energy sites. Company size matters too; larger corporations may offer more specialized roles and advanced training. This analysis provides an honest assessment to guide realistic career planning.
Current Challenges
Instrument Technician roles face increased competition, particularly for entry-level positions, as automation tools streamline some maintenance tasks. Economic uncertainty in manufacturing and processing sectors leads to slower hiring cycles and fewer new projects. A notable skill gap exists for advanced digital instrumentation and AI-integrated systems, creating a barrier for some candidates.
Growth Opportunities
Despite challenges, strong demand exists for Instrument Technicians proficient in advanced diagnostics and digital integration. Emerging opportunities are robust in renewable energy sectors, particularly wind and solar farms, and in smart manufacturing facilities utilizing Industry 4.0 principles. Specializations in cybersecurity for industrial control systems (ICS) or proficiency with specific PLC and DCS platforms offer significant advantages.
Technicians can position themselves advantageously by acquiring certifications in advanced automation, network protocols, and data analysis tools. Underserved markets include critical infrastructure projects in rural areas or regions investing heavily in new industrial parks. Experience with AI-powered predictive maintenance software provides a competitive edge, shifting the role from reactive repair to proactive system management. Market corrections can create opportunities as companies optimize existing assets, increasing the need for skilled maintenance. Investing in training for new technologies like robotics integration or advanced sensor calibration can unlock significant career growth.
Current Market Trends
Demand for Instrument Technicians remains steady but highly specialized as of 2025. Industries like oil and gas, pharmaceuticals, and advanced manufacturing consistently seek skilled technicians for calibration, maintenance, and troubleshooting. The integration of smart sensors, IoT devices, and predictive maintenance software is transforming the role, requiring technicians to possess strong digital literacy alongside traditional mechanical and electrical skills.
Economic conditions influence hiring, with capital expenditure projects slowing in some sectors, yet essential maintenance and upgrades continue. Layoffs in one area often correspond with hiring surges in another due to critical infrastructure needs. Generative AI assists in diagnostics and documentation, but human expertise remains indispensable for hands-on repair and complex system integration. Employers now prioritize technicians who can adapt to evolving automation technologies and understand data analytics for preventative maintenance.
Salary trends show modest growth, with significant premiums for specialists in highly automated or hazardous environments. Market saturation is low for experienced, multi-skilled technicians, but entry-level roles can be competitive. Geographic variations are pronounced; demand is high in industrial hubs and areas with new infrastructure projects, while remote work is generally not applicable to this hands-on profession. Hiring often follows project lifecycles, with peaks during plant commissioning or major upgrade cycles.
Emerging Specializations
The field of Instrument Technician is undergoing significant transformation, driven by rapid advancements in automation, data analytics, and smart technologies. These technological shifts are not merely optimizing existing processes; they are creating entirely new domains for specialization. Understanding and positioning oneself within these emerging areas is crucial for career advancement and securing premium compensation in 2025 and beyond.
Early adoption of skills in these cutting-edge specializations allows professionals to become indispensable experts as industries evolve. While established specializations offer stability, emerging areas often command higher demand and less competition, leading to accelerated career growth. These nascent fields typically take 3-7 years to transition from niche opportunities to mainstream roles with significant job opportunities, providing a strategic window for current professionals to gain expertise.
Pursuing an emerging specialization involves a balance of risk and reward. It requires a commitment to continuous learning and adapting to new paradigms. However, the potential for leadership roles, innovative project involvement, and elevated earning potential far outweighs the initial investment in skill development. Professionals who embrace these future-oriented paths will find themselves at the forefront of industrial innovation.
Industrial IoT Instrument Specialist
The integration of the Internet of Things (IoT) into industrial instrumentation is creating a demand for technicians skilled in managing interconnected sensor networks. These specialists maintain and troubleshoot smart instruments that communicate wirelessly, collect vast amounts of data, and often operate autonomously. Their role is critical in ensuring data integrity and operational efficiency in smart factories and smart infrastructure.
Environmental Instrumentation and Sustainability Technician
With the increasing emphasis on sustainability and energy efficiency, instrument technicians are specializing in optimizing systems for reduced environmental impact. This involves calibrating and maintaining sensors for emissions monitoring, waste heat recovery, and renewable energy integration. They ensure compliance with environmental regulations and contribute to greener industrial operations.
Robotics and Automation Instrument Technician
Advanced robotics and automation are becoming integral to many industrial processes, requiring instrument technicians to specialize in the maintenance and calibration of robotic arms, automated guided vehicles (AGVs), and complex assembly lines. This role involves working with sophisticated servo mechanisms, precision sensors, and integrated control systems to ensure seamless automated operations.
AI-Integrated Instrument Data Technician
The proliferation of artificial intelligence (AI) and machine learning (ML) in predictive maintenance and process optimization creates a need for technicians who can manage and interpret data from smart instruments. These specialists work with AI-driven diagnostic tools, ensuring the accuracy of data fed into algorithms and implementing solutions based on AI-generated insights. They bridge the gap between physical instrumentation and data intelligence.
Industrial Cybersecurity Instrument Specialist
The growing complexity of industrial control networks necessitates instrument technicians who specialize in securing these vulnerable systems. This involves implementing and maintaining cybersecurity measures for industrial control systems (ICS) and supervisory control and data acquisition (SCADA) systems. They protect critical infrastructure from cyber threats by securing instrument communication and data pathways.
Pros & Cons of Being an Instrument Technician
Understanding both the advantages and challenges of a career is crucial for making informed decisions. Career experiences can vary significantly based on company culture, the specific industry sector, the specialization area within the field, and an individual's personal preferences and personality. The pros and cons of a role like an Instrument Technician may also shift at different career stages, from entry-level to senior positions. What one person considers an advantage, such as hands-on problem-solving, another might view as a challenge, like the need for constant vigilance. This assessment aims to provide a realistic, balanced view to help set appropriate expectations for this profession.
Pros
- Instrument technicians are in consistent demand across various industries, including manufacturing, energy, pharmaceuticals, and utilities, ensuring strong job security and diverse employment opportunities.
- The role involves hands-on problem-solving and troubleshooting complex systems, providing intellectual stimulation and a sense of accomplishment when successfully diagnosing and repairing equipment.
- Instrument technicians often receive specialized training and certifications, making their skills highly valuable and transferable across different industrial settings.
- This career typically offers competitive salaries and benefits, reflecting the specialized knowledge and critical nature of maintaining precision equipment in industrial operations.
- The work environment is dynamic, with different challenges and systems to work on daily, which prevents monotony and keeps the job engaging.
- Instrument technicians play a critical role in ensuring the safety, efficiency, and quality of industrial processes, contributing directly to operational success and safety standards.
- There are clear paths for career advancement, allowing experienced technicians to move into supervisory roles, instrumentation engineering, or specialized consulting with additional training or education.
Cons
- Instrument technicians often work in industrial environments such as factories, power plants, or oil rigs, which can involve exposure to noise, hazardous materials, and extreme temperatures, requiring strict adherence to safety protocols.
- The job demands a high level of precision and attention to detail; even minor errors in calibration or repair can lead to significant operational failures or safety hazards, creating constant pressure.
- Maintaining proficiency requires continuous learning as instrumentation technology rapidly evolves, necessitating ongoing training and certification to stay current with new systems and equipment.
- Many roles require working shifts, including nights, weekends, and holidays, especially in 24/7 operational facilities, which can disrupt personal life and social schedules.
- The work can be physically demanding, involving lifting heavy equipment, climbing ladders, working in confined spaces, or standing for long periods, leading to physical strain.
- Troubleshooting complex issues can be mentally taxing and require significant problem-solving skills under pressure, particularly when equipment malfunctions cause production delays.
- Career progression can sometimes be limited to senior technician roles or supervisory positions without further specialized education, which may not appeal to those seeking diverse career paths beyond the technical field itself.
Frequently Asked Questions
What are the typical educational or training requirements to become an Instrument Technician?
Becoming an Instrument Technician typically requires completing a two-year associate's degree in instrumentation, industrial electronics, or a related field. Some entry-level positions are also available through apprenticeships, which can last 3-5 years and combine on-the-job training with classroom instruction. Prior experience in electrical or mechanical trades can also be beneficial for accelerating your learning.
How long does it take to become proficient enough to work as an Instrument Technician?
The time to become job-ready varies based on your chosen path. An associate's degree usually takes two years, followed by entry-level work experience to build proficiency. Apprenticeships can take 3-5 years but provide immediate income and hands-on experience. If you have a strong background in a related trade, you might transition faster, but expect at least 1-2 years of focused training or on-the-job learning specifically for instrumentation.
What are the salary expectations for an entry-level Instrument Technician versus an experienced one?
Starting salaries for Instrument Technicians typically range from $45,000 to $60,000 annually, depending on location, industry, and prior experience. With several years of experience and specialized certifications, salaries can increase significantly, often reaching $70,000 to $90,000 or more. Industries like oil and gas, pharmaceuticals, and manufacturing tend to offer higher compensation due to the complexity and critical nature of their systems.
What is the typical work-life balance like for an Instrument Technician, including hours and work environment?
Work-life balance for Instrument Technicians can vary. Many roles involve standard day shifts in industrial settings. However, some positions, especially in continuous operation plants, may require shift work, including nights, weekends, or on-call duties for emergency repairs. Overtime is common, particularly during plant shutdowns or critical maintenance periods. This career often involves hands-on work in various environments, from control rooms to field locations.
What is the job security and future demand for Instrument Technicians?
The job market for Instrument Technicians remains strong and stable. Industries relying on automated processes, such as manufacturing, energy, chemical, and pharmaceutical, consistently need skilled technicians to maintain their complex control systems. As automation advances, the demand for professionals who can install, calibrate, and troubleshoot these systems is expected to grow. Job security is generally high due to the specialized skills required.
What are the typical career advancement opportunities for an Instrument Technician?
Career growth for Instrument Technicians can lead to several advanced roles. You might specialize in specific types of instrumentation, such as process control, analytical instrumentation, or cybersecurity for industrial control systems. Opportunities also exist to move into supervisory or lead technician roles, instrumentation engineering, or technical training positions. Continuing education and professional certifications are key to advancing your career in this field.
What are the biggest challenges or common frustrations faced by Instrument Technicians?
The primary challenge is keeping up with rapidly evolving technology and complex control systems. Instrument Technicians must commit to continuous learning to master new software, calibration techniques, and diagnostic tools. Working in industrial environments also requires strict adherence to safety protocols and the ability to troubleshoot under pressure. Precision and attention to detail are paramount to avoid costly errors or safety incidents.
Can Instrument Technicians work remotely, or is it primarily an on-site role?
Remote work is generally not common for Instrument Technicians because the role requires hands-on interaction with physical equipment and systems. Most of your work involves calibrating, installing, troubleshooting, and repairing instruments directly on-site in industrial plants, factories, or field locations. While some administrative or planning tasks might be done remotely, the core functions of the job demand a physical presence.
Related Careers
Explore similar roles that might align with your interests and skills:
Equipment Technician
A growing field with similar skill requirements and career progression opportunities.
Explore career guideInstrument Engineer
A growing field with similar skill requirements and career progression opportunities.
Explore career guideInstrumentation Engineer
A growing field with similar skill requirements and career progression opportunities.
Explore career guideInstrumentation Technician
A growing field with similar skill requirements and career progression opportunities.
Explore career guideElectronic Instrument Testing Technician
A growing field with similar skill requirements and career progression opportunities.
Explore career guideAssess your Instrument Technician readiness
Understanding where you stand today is the first step toward your career goals. Our Career Coach helps identify skill gaps and create personalized plans.
Skills Gap Analysis
Get a detailed assessment of your current skills versus Instrument Technician requirements. Our AI Career Coach identifies specific areas for improvement with personalized recommendations.
See your skills gapCareer Readiness Assessment
Evaluate your overall readiness for Instrument Technician roles with our AI Career Coach. Receive personalized recommendations for education, projects, and experience to boost your competitiveness.
Assess your readinessSimple pricing, powerful features
Upgrade to Himalayas Plus and turbocharge your job search.
Himalayas
Himalayas Plus
Himalayas Max
Find your dream job
Sign up now and join over 100,000 remote workers who receive personalized job alerts, curated job matches, and more for free!
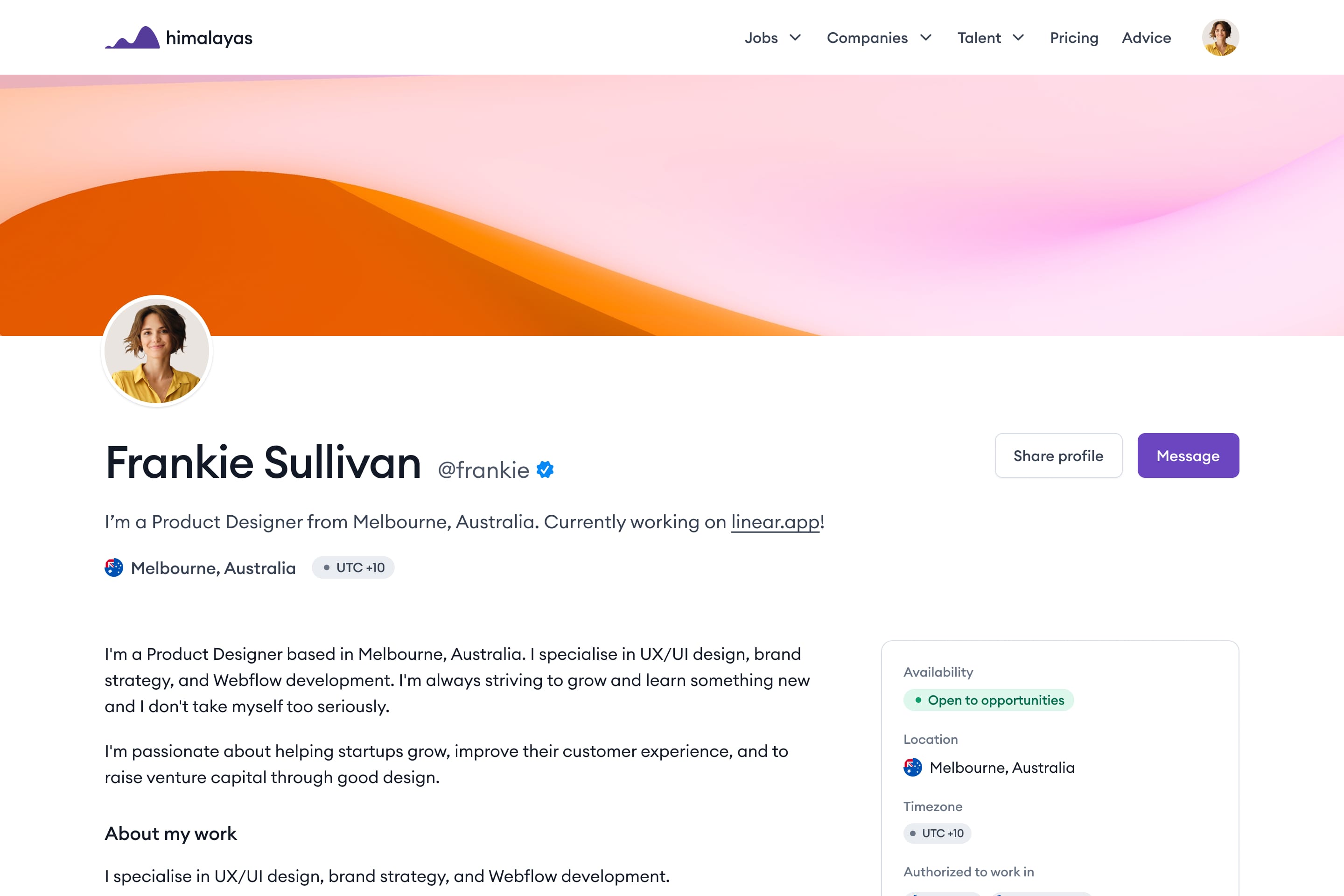