Complete Gear Machinist Career Guide
Gear machinists are the precision artisans who craft the intricate components driving countless machines, from wind turbines to automotive transmissions. They translate engineering blueprints into physical gears, ensuring the exact tolerances critical for mechanical efficiency and longevity. This specialized role requires a keen eye for detail and mastery of advanced machinery, offering a stable career path in manufacturing and engineering.
Key Facts & Statistics
Median Salary
$55,000 USD
(U.S. national median for Machinists, BLS May 2023)
Range: $38k - $75k+ USD (varies by experience, specialization, and region)
Growth Outlook
9%
as fast as average (for machinists and tool and die makers, 2022-2032)
Annual Openings
≈30k
openings annually (across all machinists, tool and die makers, and industrial machinery mechanics and maintenance workers)
Top Industries
Typical Education
High school diploma or equivalent, often followed by a vocational school program, apprenticeship, or significant on-the-job training.
What is a Gear Machinist?
A Gear Machinist is a highly skilled manufacturing professional who specializes in the precision fabrication of gears. This role involves setting up, operating, and maintaining specialized machinery to cut, shape, and grind various types of gears, ensuring they meet exact engineering specifications and strict quality standards. They are critical to industries requiring precise motion control, such as automotive, aerospace, heavy machinery, and robotics.
Unlike general machinists who work on a wide range of components, a Gear Machinist possesses specific expertise in gear geometry, metallurgy, and the unique processes involved in creating gear teeth. They understand the complexities of different gear types—spur, helical, bevel, worm—and the specific machines and tooling required for each, ensuring that gears function efficiently and reliably within mechanical systems. This specialization makes them indispensable for producing the intricate components that drive countless mechanical applications.
What does a Gear Machinist do?
Key Responsibilities
- Interpret engineering blueprints and specifications to determine the precise dimensions, tolerances, and material requirements for various types of gears.
- Set up and operate specialized gear-cutting machines, including hobbing machines, shaping machines, and grinding machines, adjusting settings for speed, feed, and depth of cut.
- Monitor machine operations closely, making fine adjustments to ensure the accurate cutting of gear teeth and maintaining strict quality control throughout the manufacturing process.
- Perform regular inspections of finished gears using precision measuring instruments such as calipers, micrometers, and gear-specific gauges to verify adherence to design specifications.
- Troubleshoot and resolve minor mechanical issues or operational errors with gear-cutting machinery to minimize downtime and maintain production efficiency.
- Maintain a clean and organized work area, adhering to all safety protocols and machine maintenance schedules to ensure a safe and productive environment.
Work Environment
Gear Machinists typically work in manufacturing plants, machine shops, or specialized gear production facilities. The environment can be noisy due to operating machinery and often requires standing for long periods. Safety is paramount, involving the use of personal protective equipment such as safety glasses, ear protection, and steel-toed boots. Collaboration is common, often working with other machinists, quality control inspectors, and engineers to ensure product accuracy. The work schedule usually follows standard shifts, but overtime may be necessary to meet production deadlines. The pace of work is steady and precise, demanding close attention to detail and consistent focus on machine operation and quality.
Tools & Technologies
Gear Machinists primarily use and maintain specialized gear-cutting machines such as hobbing machines, gear shapers, and gear grinding machines. They also work with conventional machine shop equipment like lathes, milling machines, and drill presses for preliminary or finishing work. Precision measuring tools are essential, including micrometers, calipers, bore gauges, depth gauges, and specialized gear inspection tools like gear tooth verniers and run-out indicators. Knowledge of Computer Numerical Control (CNC) programming for automated gear production is increasingly important, requiring familiarity with G-code and M-code, as well as CAD/CAM software for interpreting designs. They also utilize various cutting fluids, coolants, and specific tooling inserts or hobs tailored for different gear profiles and materials.
Gear Machinist Skills & Qualifications
A Gear Machinist specializes in the precise fabrication and modification of gears, which are critical components in countless mechanical systems. This role demands a unique blend of mechanical aptitude, mathematical precision, and attention to detail. Qualifications for a Gear Machinist typically emphasize hands-on experience and specialized training over traditional academic degrees.
Requirements for a Gear Machinist vary significantly by industry sector, company size, and the complexity of the gears produced. For instance, aerospace or medical device manufacturing demands extremely tight tolerances and often requires specific certifications like ISO 9001 or AS9100, alongside extensive practical experience. In contrast, general manufacturing may prioritize production speed and versatility across different machine types. Seniority levels also dictate skill depth; entry-level positions often focus on machine operation and basic quality checks, while experienced machinists handle complex setups, programming, and troubleshooting.
Formal education, such as a vocational degree or apprenticeship, provides a strong foundation, especially for understanding metallurgy and machine mechanics. However, practical experience gained through apprenticeships or on-the-job training is often more highly valued than a university degree in this field. Certifications, like those from the National Institute for Metalworking Skills (NIMS) in areas like 'CNC Machining' or 'Measurement, Materials & Safety,' significantly enhance a candidate's marketability. The skill landscape is evolving with increased automation and CNC technology, making programming and digital inspection skills increasingly vital, shifting from purely manual operations to a blend of manual dexterity and digital proficiency.
Education Requirements
Technical Skills
- CNC Machine Operation and Programming (G-code, M-code) for gear hobbing, shaping, and milling machines
- Manual Machining (Lathes, Milling Machines, Grinders) for material preparation and secondary operations specific to gear blanks
- Gear Hobbing and Shaping Techniques: Setting up and operating hobbing and shaping machines for various gear types (spur, helical, bevel, worm)
- Metrology and Inspection Tools: Proficient use of calipers, micrometers, bore gauges, profilometers, and CMMs for precise gear measurement
- Blueprint Reading and Geometric Dimensioning and Tolerancing (GD&T): Interpreting complex engineering drawings for gear specifications and tolerances
- Material Science Knowledge: Understanding the properties of various metals (steel, aluminum, brass) and their machinability for different gear applications
- Tooling Selection and Sharpening: Choosing appropriate cutting tools (hobs, shaper cutters, milling cutters) and maintaining their sharpness for optimal performance
- Machine Maintenance and Troubleshooting: Performing routine maintenance and diagnosing common mechanical or electrical issues on gear cutting machinery
- Quality Control and Process Improvement: Implementing quality checks and identifying areas for process optimization in gear manufacturing
Soft Skills
- Attention to Detail: Critical for ensuring precise dimensions and surface finishes on gears, where even slight errors can lead to component failure.
- Problem-Solving: Essential for diagnosing machine malfunctions, optimizing cutting parameters, and troubleshooting issues during gear production to maintain quality and efficiency.
- Mechanical Aptitude: Important for understanding how gear cutting machines operate, how tools interact with materials, and the mechanics of gear meshing.
- Patience and Persistence: Necessary for fine-tuning machine setups, especially for complex or difficult-to-machine materials, and for maintaining focus during long production runs.
- Adherence to Safety Protocols: Crucial for operating heavy machinery and handling sharp tools and hot materials safely, preventing workplace accidents.
- Continuous Learning: Important for staying updated with new machining technologies, materials, and gear design principles to improve efficiency and capability.
How to Become a Gear Machinist
Entering the gear machinist field offers multiple pathways, each with distinct timelines and advantages. Traditional routes often involve enrolling in a vocational school or community college program focused on CNC machining, manufacturing technology, or a specialized gear technology curriculum. These programs typically last from six months to two years and provide a strong theoretical and practical foundation. Another common entry point is through apprenticeships, which can range from two to five years. Apprenticeships offer hands-on training while working and earning a wage, making them ideal for those who prefer learning by doing and want to avoid student debt.
For individuals transitioning from other manufacturing roles or with prior machining experience, the timeline for becoming a gear machinist can be shorter, often focusing on acquiring specialized gear-cutting knowledge and operating specific gear machinery. They might pursue short courses or on-the-job training. Geographic location also plays a role; larger industrial centers and manufacturing hubs often have more opportunities and specialized training programs compared to smaller markets. Smaller companies or job shops might be more open to training entry-level machinists, while larger corporations or defense contractors may prefer candidates with formal training or prior experience.
A common misconception is that all gear machining is manual; modern gear manufacturing relies heavily on sophisticated CNC machines and software. While foundational manual machining skills remain valuable, proficiency in computer-aided manufacturing (CAM) and understanding G-code is critical. Networking within local manufacturing associations, attending industry trade shows, and connecting with experienced machinists can open doors to unadvertised opportunities and mentorship. Building a portfolio of precision parts, even from personal projects, can demonstrate commitment and skill to potential employers.
Complete foundational machining education through a vocational school, community college, or a certified apprenticeship program. Focus on courses covering blueprint reading, metrology, materials science, and the fundamentals of manual and CNC machining. This foundational knowledge typically takes 6-24 months and is crucial for understanding precision manufacturing.
Gain practical experience with general machining equipment, such as lathes, mills, and grinders. Seek opportunities for hands-on work, whether through school labs, internships, or entry-level machine operator positions. Proficiency in setting up machines, selecting tooling, and performing quality checks on basic components is essential before specializing in gears.
Acquire specialized knowledge in gear theory, geometry, and specific gear manufacturing processes. This includes understanding different gear types (spur, helical, bevel, worm), gear tooth profiles, and the operation of specialized gear-cutting machines like hobbers, shapers, and grinders. Many vocational programs offer specialized gear technology courses or you may need to seek out specific industry training modules.
Develop proficiency in CNC programming and CAM software relevant to gear manufacturing. Modern gear machinists use CAD/CAM software to design and program complex gear geometries for CNC machines. Practice writing and optimizing G-code, understanding machine offsets, and simulating machining processes to minimize errors and maximize efficiency.
Build a portfolio showcasing your precision machining skills, particularly any gear-related projects or components you have produced. Include detailed documentation of your work, such as blueprints, process sheets, inspection reports, and photographs of finished parts. This portfolio will serve as tangible proof of your capabilities and attention to detail for prospective employers.
Network with professionals in the gear manufacturing industry by attending local trade shows, joining manufacturing associations, or participating in online forums. Connect with experienced gear machinists, supervisors, and recruiters to learn about industry trends and potential job openings. Informational interviews can provide valuable insights and lead to referrals.
Prepare for job applications and technical interviews by practicing common machining questions and understanding specific gear-related terminology. Be ready to discuss your experience with different materials, tooling, and quality control procedures. Highlight your problem-solving skills and your ability to work with tight tolerances, which are critical in gear manufacturing.
Step 1
Complete foundational machining education through a vocational school, community college, or a certified apprenticeship program. Focus on courses covering blueprint reading, metrology, materials science, and the fundamentals of manual and CNC machining. This foundational knowledge typically takes 6-24 months and is crucial for understanding precision manufacturing.
Step 2
Gain practical experience with general machining equipment, such as lathes, mills, and grinders. Seek opportunities for hands-on work, whether through school labs, internships, or entry-level machine operator positions. Proficiency in setting up machines, selecting tooling, and performing quality checks on basic components is essential before specializing in gears.
Step 3
Acquire specialized knowledge in gear theory, geometry, and specific gear manufacturing processes. This includes understanding different gear types (spur, helical, bevel, worm), gear tooth profiles, and the operation of specialized gear-cutting machines like hobbers, shapers, and grinders. Many vocational programs offer specialized gear technology courses or you may need to seek out specific industry training modules.
Step 4
Develop proficiency in CNC programming and CAM software relevant to gear manufacturing. Modern gear machinists use CAD/CAM software to design and program complex gear geometries for CNC machines. Practice writing and optimizing G-code, understanding machine offsets, and simulating machining processes to minimize errors and maximize efficiency.
Step 5
Build a portfolio showcasing your precision machining skills, particularly any gear-related projects or components you have produced. Include detailed documentation of your work, such as blueprints, process sheets, inspection reports, and photographs of finished parts. This portfolio will serve as tangible proof of your capabilities and attention to detail for prospective employers.
Step 6
Network with professionals in the gear manufacturing industry by attending local trade shows, joining manufacturing associations, or participating in online forums. Connect with experienced gear machinists, supervisors, and recruiters to learn about industry trends and potential job openings. Informational interviews can provide valuable insights and lead to referrals.
Step 7
Prepare for job applications and technical interviews by practicing common machining questions and understanding specific gear-related terminology. Be ready to discuss your experience with different materials, tooling, and quality control procedures. Highlight your problem-solving skills and your ability to work with tight tolerances, which are critical in gear manufacturing.
Education & Training Needed to Become a Gear Machinist
Becoming a Gear Machinist requires a blend of theoretical knowledge and hands-on practical skills. Traditional pathways include vocational programs, apprenticeships, and some associate's degrees. Four-year engineering degrees are generally not required for this role, as the focus is on precision manufacturing and machine operation rather than design or advanced materials science. Vocational programs or technical certifications typically cost between $5,000 and $20,000 and can be completed in 6 to 18 months. These programs provide foundational knowledge in blueprint reading, metallurgy, and CNC machine operation, which are critical for gear manufacturing.
Apprenticeships are a highly valued path, often lasting 3 to 5 years, and provide paid on-the-job training combined with classroom instruction. While they do not incur tuition costs, they require a significant time commitment. Employers highly favor candidates with apprenticeship experience due to the practical skills gained. Self-study, through online courses and manuals, can supplement formal training but rarely suffices on its own for entry-level positions due to the need for hands-on machine experience. Quality standards for programs often involve National Institute for Metalworking Skills (NIMS) certifications, which demonstrate proficiency in specific machining areas.
Continuous learning remains important for Gear Machinists, particularly as new technologies like advanced CNC systems and automation emerge. Professional development often involves specialized workshops on new software, materials, or machine maintenance. The market perception strongly favors practical experience gained through apprenticeships or vocational programs with significant lab components. Cost-benefit analysis generally shows that vocational training and apprenticeships offer a high return on investment, leading directly to employment without the higher costs or longer time commitments of traditional degrees. Educational needs vary by the complexity of gears produced; higher precision or specialized materials may require more advanced training.
Gear Machinist Salary & Outlook
Compensation for a Gear Machinist varies significantly based on several critical factors. Geographic location plays a substantial role, as areas with high manufacturing demand or a higher cost of living, such as the Northeast or parts of the Midwest, typically offer better wages than rural regions. The presence of specialized industries like aerospace or automotive manufacturing also drives local salary premiums.
Years of experience dramatically influence earning potential. Entry-level machinists earn less, while those with a decade or more of experience, especially with complex CNC gear cutting machines, command higher salaries. Specialization in specific gear types, materials, or advanced machining techniques like hobbing, shaping, or grinding, also creates significant salary variations. Possessing certifications in areas like GD&T (Geometric Dimensioning and Tolerancing) or advanced CNC programming can further boost compensation.
Total compensation packages often extend beyond base salary. Many employers offer overtime pay, production bonuses, or profit-sharing. Benefits typically include health insurance, paid time off, and 401(k) plans with employer contributions. Some companies may also provide allowances for professional development or tool purchases. Industry-specific trends, such as the adoption of automation or demand from defense contracts, can influence salary growth. Negotiating leverage comes from demonstrating expertise in high-demand machinery or processes, proven precision, and reliability. While remote work is not typical for this hands-on role, some larger companies might offer relocation assistance for highly skilled machinists. Salary figures presented here are primarily in USD, recognizing that international markets will have different compensation structures.
Salary by Experience Level
Level | US Median | US Average |
---|---|---|
Junior Gear Machinist | $45k USD | $48k USD |
Gear Machinist | $57k USD | $59k USD |
Senior Gear Machinist | $70k USD | $72k USD |
Lead Gear Machinist | $82k USD | $85k USD |
Machining Supervisor | $95k USD | $98k USD |
Market Commentary
The job market for Gear Machinists shows a stable outlook, driven by the ongoing need for precision components across various manufacturing sectors. The Bureau of Labor Statistics projects a modest growth for machinists and tool and die makers, including gear machinists, of about 1% from 2022 to 2032. This translates to approximately 18,300 job openings each year, many of which are due to replacing workers who transfer to different occupations or exit the labor force.
Demand drivers include the aerospace, automotive, energy, and heavy machinery industries, all of which rely heavily on custom-made gears for their products. The increasing complexity of modern machinery and the need for higher precision components ensure a steady demand for skilled machinists. Emerging opportunities lie in advanced manufacturing, where machinists operate sophisticated multi-axis CNC machines and work with new materials like composites or advanced alloys. There is a growing need for machinists who can program, set up, and troubleshoot these automated systems.
The supply and demand dynamics for skilled Gear Machinists are relatively balanced, with some regional shortages for highly experienced individuals. Automation and AI are impacting the role by requiring machinists to evolve from manual operators to programmers and supervisors of automated systems. This shift emphasizes problem-solving, quality control, and technical skills over purely manual dexterity. To future-proof their careers, machinists must embrace continuous learning in CNC programming, CAD/CAM software, and advanced metrology. This profession is relatively recession-resistant due to its foundational role in critical infrastructure and product manufacturing. Geographic hotspots for Gear Machinists include traditional manufacturing hubs in the Midwest and Southeast, as well as areas with significant aerospace and defense industries.
Gear Machinist Career Path
Career progression for a Gear Machinist typically follows a structured path focused on increasing technical mastery, problem-solving capabilities, and leadership responsibilities. Initial stages emphasize hands-on skill development and adherence to precision. As a machinist gains experience, the role evolves from executing tasks to optimizing processes and mentoring others.
Advancement in this field depends heavily on demonstrated precision, efficiency, and the ability to work with complex machinery and materials. Specialization in particular gear types, materials (e.g., aerospace alloys), or advanced machining techniques (e.g., 5-axis machining, CNC programming) accelerates progression. Company size and industry also play a role; larger manufacturing firms often have clearer, more stratified paths, while smaller shops might offer broader, but less formal, opportunities.
Career paths can diverge into individual contributor (IC) tracks, where machinists become subject matter experts or highly specialized technicians, or into management tracks, leading to supervisory and leadership roles. Continuous learning, including certifications in specific machinery or quality standards, is vital. Building a reputation for meticulous work and reliability significantly aids advancement within the manufacturing community.
Junior Gear Machinist
0-2 yearsOperates basic gear machining equipment under direct supervision. Performs routine tasks such as loading materials, monitoring machine cycles, and making minor adjustments. Cleans and maintains machinery. Learns to identify quality defects and reports issues to senior machinists or supervisors.
Key Focus Areas
Developing foundational skills in machine operation, tool selection, and material handling. Learning to interpret blueprints, schematics, and technical drawings. Focusing on safety protocols and quality control standards. Building proficiency in measurement tools and basic troubleshooting of common machining issues.
Gear Machinist
2-5 yearsOperates a range of gear machining equipment with minimal supervision, producing gears according to specifications. Performs machine setups, tool changes, and routine maintenance. Conducts in-process quality checks and makes necessary adjustments to maintain tolerances. May assist in training junior machinists.
Key Focus Areas
Mastering various gear machining processes, including hobbing, shaping, and grinding. Improving setup efficiency and reducing cycle times. Developing intermediate troubleshooting skills for machine malfunctions and quality deviations. Beginning to understand G-code and M-code for CNC machines.
Senior Gear Machinist
5-8 yearsIndependently operates and programs complex gear machining centers, handling intricate designs and tight tolerances. Troubleshoots and resolves advanced machine issues, often without assistance. Leads small projects or specific production runs. Provides technical guidance and training to less experienced machinists.
Key Focus Areas
Optimizing machining processes for efficiency and precision, including advanced programming techniques. Developing expertise in complex gear geometries and exotic materials. Mentoring junior and mid-level machinists. Participating in process improvement initiatives and contributing to design for manufacturability discussions.
Lead Gear Machinist
8-12 yearsActs as the primary technical expert and informal team leader on the shop floor. Oversees daily operations for a section of the machining department, ensuring production targets and quality standards are met. Provides advanced technical support and guidance to senior machinists. Troubleshoots complex problems and implements solutions.
Key Focus Areas
Developing leadership skills, including delegation, performance feedback, and conflict resolution. Taking ownership of production schedules and resource allocation. Contributing to strategic planning for equipment upgrades and process enhancements. Building strong communication skills for cross-functional collaboration.
Machining Supervisor
12+ years total experience; 2+ years in a lead roleManages a team of gear machinists, overseeing production schedules, quality control, and personnel development. Responsible for maintaining equipment, optimizing workflow, and ensuring a safe working environment. Collaborates with engineering and production planning to meet organizational goals. Conducts performance evaluations and implements training programs.
Key Focus Areas
Mastering team management, including scheduling, performance reviews, and professional development. Developing strong communication and interpersonal skills to manage a diverse team. Acquiring foundational knowledge of budgeting, inventory management, and lean manufacturing principles. Engaging in strategic planning for the department.
Junior Gear Machinist
0-2 yearsOperates basic gear machining equipment under direct supervision. Performs routine tasks such as loading materials, monitoring machine cycles, and making minor adjustments. Cleans and maintains machinery. Learns to identify quality defects and reports issues to senior machinists or supervisors.
Key Focus Areas
Developing foundational skills in machine operation, tool selection, and material handling. Learning to interpret blueprints, schematics, and technical drawings. Focusing on safety protocols and quality control standards. Building proficiency in measurement tools and basic troubleshooting of common machining issues.
Gear Machinist
2-5 yearsOperates a range of gear machining equipment with minimal supervision, producing gears according to specifications. Performs machine setups, tool changes, and routine maintenance. Conducts in-process quality checks and makes necessary adjustments to maintain tolerances. May assist in training junior machinists.
Key Focus Areas
Mastering various gear machining processes, including hobbing, shaping, and grinding. Improving setup efficiency and reducing cycle times. Developing intermediate troubleshooting skills for machine malfunctions and quality deviations. Beginning to understand G-code and M-code for CNC machines.
Senior Gear Machinist
5-8 yearsIndependently operates and programs complex gear machining centers, handling intricate designs and tight tolerances. Troubleshoots and resolves advanced machine issues, often without assistance. Leads small projects or specific production runs. Provides technical guidance and training to less experienced machinists.
Key Focus Areas
Optimizing machining processes for efficiency and precision, including advanced programming techniques. Developing expertise in complex gear geometries and exotic materials. Mentoring junior and mid-level machinists. Participating in process improvement initiatives and contributing to design for manufacturability discussions.
Lead Gear Machinist
8-12 yearsActs as the primary technical expert and informal team leader on the shop floor. Oversees daily operations for a section of the machining department, ensuring production targets and quality standards are met. Provides advanced technical support and guidance to senior machinists. Troubleshoots complex problems and implements solutions.
Key Focus Areas
Developing leadership skills, including delegation, performance feedback, and conflict resolution. Taking ownership of production schedules and resource allocation. Contributing to strategic planning for equipment upgrades and process enhancements. Building strong communication skills for cross-functional collaboration.
Machining Supervisor
12+ years total experience; 2+ years in a lead roleManages a team of gear machinists, overseeing production schedules, quality control, and personnel development. Responsible for maintaining equipment, optimizing workflow, and ensuring a safe working environment. Collaborates with engineering and production planning to meet organizational goals. Conducts performance evaluations and implements training programs.
Key Focus Areas
Mastering team management, including scheduling, performance reviews, and professional development. Developing strong communication and interpersonal skills to manage a diverse team. Acquiring foundational knowledge of budgeting, inventory management, and lean manufacturing principles. Engaging in strategic planning for the department.
Job Application Toolkit
Ace your application with our purpose-built resources:
Gear Machinist Cover Letter Examples
Personalizable templates that showcase your impact.
View examplesGear Machinist Job Description Template
Ready-to-use JD for recruiters and hiring teams.
View examplesGlobal Gear Machinist Opportunities
Gear machinists operate precision machinery to cut, shape, and finish gears. This specialized trade is globally essential across manufacturing, automotive, aerospace, and energy sectors. International demand remains steady, particularly in industrialized nations with robust manufacturing bases. Professionals often find opportunities in countries prioritizing advanced industrial production. Certifications like ISO 9001 and specific machine operation licenses enhance global mobility.
Global Salaries
Gear machinist salaries vary significantly by region and experience. In North America, a gear machinist earns between $50,000 and $75,000 USD annually in countries like the United States and Canada. Experienced professionals in high-demand areas can reach $80,000 USD. European countries like Germany and Switzerland offer €45,000 to €65,000 (approximately $48,000 to $70,000 USD), reflecting strong manufacturing economies and higher living costs.
Asia-Pacific markets, including Japan and South Korea, typically offer salaries ranging from ¥4,500,000 to ¥7,000,000 JPY (about $30,000 to $47,000 USD) or ₩40,000,000 to ₩60,000,000 KRW (about $29,000 to $44,000 USD). These figures often come with lower living expenses, impacting purchasing power. Latin American countries, such as Brazil or Mexico, present lower nominal salaries, generally $15,000 to $30,000 USD, but with considerably lower costs of living.
Salary structures also differ. European compensation often includes generous vacation time and comprehensive health benefits. North American packages may involve performance bonuses and retirement plans. Tax implications significantly affect take-home pay, with higher income tax rates in many European nations compared to some North American states. International experience and specialized skills in CNC gear cutting or exotic materials can command higher compensation globally.
Remote Work
International remote work for gear machinists is highly limited due to the hands-on nature of the job. This role requires direct interaction with heavy machinery and physical presence in manufacturing facilities. Digital nomad opportunities are not applicable for this specific trade.
However, some related functions, like CAD/CAM programming for gear cutting or virtual machine simulation, might offer limited remote possibilities. These roles are distinct from the primary duties of a gear machinist. Employers typically do not hire gear machinists for international remote work, as the core tasks are performed on-site. Any remote aspect would involve administrative or design tasks, not direct machining.
Visa & Immigration
Gear machinists seeking international work typically apply for skilled worker visas. Countries like Germany, Canada, and Australia often have specific pathways for tradespeople. Requirements generally include recognized qualifications, several years of experience, and a job offer from a local employer.
For example, Canada's Express Entry system or Australia's Skilled Migration program assess points based on age, education, language proficiency, and work experience. Germany's skilled immigration law facilitates visas for those with vocational training and a job contract. Credential recognition for vocational training is crucial; some countries require an assessment of foreign qualifications.
The visa application process usually involves submitting educational documents, work references, and a police clearance certificate. Language proficiency tests, such as IELTS for English or Goethe-Zertifikat for German, are often mandatory. Processing times vary from a few months to over a year. Pathways to permanent residency exist in many developed nations after several years of continuous employment. Family visas for dependents are usually available once the primary applicant secures their work permit.
2025 Market Reality for Gear Machinists
Understanding current market conditions for gear machinists is critical for career success. This field, vital to manufacturing, has seen shifts post-pandemic and with the rise of AI. Broader economic factors directly influence demand for specialized components, impacting job availability and stability. Market realities also vary significantly by a machinist's experience level, geographic location, and the size of the manufacturing firm. This analysis provides an honest assessment of current challenges and opportunities to help you navigate this evolving landscape.
Current Challenges
Gear machinists face increased competition for specialized roles, as some general machining tasks see automation. Economic uncertainty can slow orders for custom gears, impacting job security. The industry also grapples with a generational skill gap, as experienced machinists retire and fewer new candidates enter the field with the necessary precision skills. Finding roles that offer specific gear-cutting experience can be difficult, leading to longer job searches for highly specialized positions. Furthermore, the push for greater efficiency means employers expect machinists to operate advanced CNC gear-cutting machines, requiring continuous learning.
Growth Opportunities
Despite challenges, strong demand persists for gear machinists specializing in high-precision and complex applications. Industries like aerospace, defense, and medical devices consistently need custom gears with tight tolerances, creating stable opportunities. Machinists who cross-train on advanced CNC gear-cutting machines and integrate CAD/CAM skills gain a significant competitive edge. Developing expertise in materials like composites and advanced alloys also opens doors in emerging sectors.
Geographic areas with robust manufacturing ecosystems, particularly those supporting heavy machinery, energy, or specialized component production, often present better prospects. Acquiring certifications in specific gear types or quality control standards enhances marketability. Furthermore, the aging workforce means experienced gear machinists are retiring, creating a vacuum for skilled professionals. This creates opportunities for those willing to pursue apprenticeships or advanced technical training. Strategic career moves involve targeting companies that invest in new manufacturing technologies and offer continuous skill development.
Current Market Trends
Demand for skilled gear machinists remains steady, particularly for those proficient with both traditional and CNC gear-cutting machines. The market prioritizes individuals who can set up, operate, and troubleshoot complex gear manufacturing processes, including hobbing, shaping, and grinding. Companies increasingly seek machinists capable of interpreting intricate blueprints for custom, high-precision gears used in aerospace, automotive, and industrial machinery. While general machining roles face some automation, the specialized nature of gear cutting still requires human expertise for complex geometries and tight tolerances.
Economic conditions influence the sector, with demand fluctuating based on manufacturing output and capital expenditure across industries. The push for electric vehicles, for instance, shifts gear requirements towards different materials and designs, creating new learning curves for machinists. Generative AI and automation are beginning to impact design and quality control in manufacturing, but the hands-on precision of gear cutting remains largely human-dependent for now. Employers now seek machinists who understand CAD/CAM software for programming CNC machines, moving beyond purely manual skills. Salary trends show stability for experienced gear machinists, with a premium on those possessing multi-axis CNC expertise. Market saturation remains low for highly skilled gear specialists, but entry-level positions can be competitive.
Geographically, opportunities concentrate in manufacturing hubs like the Midwest and Southeast United States, as well as regions with strong aerospace and defense industries. Remote work is not applicable to this hands-on role. Seasonal patterns are minimal, but economic downturns can lead to temporary slowdowns in hiring.
Emerging Specializations
The field of gear machining is undergoing a significant transformation, driven by advancements in digital manufacturing, material science, and automation. These technological shifts are not merely optimizing existing processes; they are creating entirely new specialization opportunities for gear machinists.
Understanding and positioning oneself within these emerging areas is crucial for career advancement from 2025 onwards. Professionals who proactively develop skills in these cutting-edge niches often command premium compensation and experience accelerated career growth, as their expertise is in high demand and short supply.
While established gear machining specializations remain important, focusing on emerging areas offers a strategic advantage. These new fields, though sometimes requiring initial investment in learning, promise substantial job opportunities as they transition from niche applications to mainstream industry practices. This transition typically unfolds over the next three to five years, making early adoption highly beneficial.
Pursuing emerging specializations involves a balance of risk and reward. There is an inherent uncertainty in any nascent field; however, the potential for significant impact and leadership roles within the industry often outweighs these considerations for ambitious professionals.
Advanced Robotic Gear Machining Specialist
This specialization focuses on programming and operating multi-axis CNC machines and robotic systems for complex gear geometries. It involves integrating advanced software with machine capabilities to produce gears with highly intricate profiles and tight tolerances, often for aerospace, medical, or high-performance automotive applications. The role requires a deep understanding of CAM software and machine kinematics.
Exotic Material Gear Machinist
This area involves machining gears from novel materials like composites, ceramics, and advanced superalloys, which present unique challenges due to their hardness, abrasiveness, or thermal properties. Machinists in this field must understand material science and adapt tooling, speeds, and feeds to achieve precise results with these challenging substances, often for specialized industrial or defense applications.
Hybrid Additive-Subtractive Gear Production Technician
Specialists in this area utilize additive manufacturing (3D printing) for creating near-net-shape gear blanks, which are then precision-machined to final specifications. This hybrid approach combines the design freedom of additive manufacturing with the precision of subtractive machining, enabling faster prototyping and production of customized gears. This is particularly relevant for unique or low-volume gear sets.
Automated Gear Metrology & Process Control Specialist
This specialization centers on implementing and managing automated quality control systems, such as in-process metrology and optical scanning, to ensure precise gear tolerances. It involves calibrating sensors, interpreting real-time data, and adjusting machining parameters on the fly to maintain quality. This role is crucial for high-volume, zero-defect manufacturing environments.
Digital Twin & Simulation Gear Technologist
This emerging field focuses on using digital twin technology to simulate and optimize gear machining processes virtually before physical production. It involves creating highly accurate digital models of machines, tools, and workpieces to predict performance, identify potential issues, and optimize parameters, significantly reducing setup times and material waste in complex gear manufacturing.
Pros & Cons of Being a Gear Machinist
Understanding both the advantages and challenges of any career is crucial for making informed decisions. The experience of a gear machinist can vary significantly based on the employer's industry, the specific types of gears produced, and the shop's culture. What one person finds appealing, another might see as a drawback, highlighting the importance of personal values and preferences in career satisfaction. Furthermore, the daily realities and long-term prospects can evolve at different stages of a machinist's career, from an apprentice learning the ropes to a seasoned expert. This assessment provides a realistic overview of the benefits and difficulties inherent in the gear machinist profession.
Pros
- Gear machining offers a strong sense of accomplishment, as machinists produce tangible, critical components essential for various industries, from automotive to aerospace.
- There is consistent demand for skilled gear machinists across diverse manufacturing sectors, providing good job security and numerous employment opportunities, even during economic fluctuations.
- The work involves intricate problem-solving and technical precision, offering intellectual stimulation for those who enjoy mechanical challenges and fine-tuning machinery.
- Skilled gear machinists typically command competitive wages, reflecting the specialized knowledge and precision required for the role, with potential for increased earnings through experience and advanced certifications.
- The ability to work with advanced CNC machinery and specialized software allows for continuous skill development in modern manufacturing technologies, keeping the role dynamic.
- Working as a gear machinist provides a clear career path from apprentice to journeyman, with opportunities to specialize further in areas like prototyping, inspection, or specific material machining.
- Gear machinists often work in a structured environment with clear tasks and measurable outcomes, which can appeal to individuals who prefer routine and predictable daily responsibilities.
Cons
- A gear machinist often works in a noisy environment due to the machinery, which can lead to hearing fatigue and long-term hearing damage if proper protection is not consistently used.
- The work frequently involves exposure to coolants, lubricants, and metal shavings, which can cause skin irritation or respiratory issues over time without strict adherence to safety protocols.
- Gear machining requires intense focus and precision for extended periods, leading to mental fatigue and eye strain, especially when working on intricate designs or inspecting finished products.
- The job can be physically demanding, involving standing for long hours, lifting heavy gear blanks or finished components, and repetitive motions, which may contribute to musculoskeletal issues.
- Advancement opportunities for a specialized gear machinist can be limited within a single company unless they transition into supervisory roles, quality control, or highly specialized R&D.
- The cost of specialized training and certifications for advanced gear machining techniques can be substantial, and continuous learning is necessary to keep up with new materials and machining technologies.
- Work schedules can be irregular, with shifts often including nights, weekends, or extended hours during peak production cycles to meet tight deadlines in manufacturing environments, impacting work-life balance at times.
Frequently Asked Questions
Gear Machinists face unique challenges combining precision craftsmanship with advanced machine operation. This section addresses common questions about entering this specialized field, from mastering complex machinery to understanding the industry's demand for skilled professionals.
How long does it take to become a skilled Gear Machinist, starting from no experience?
Becoming a competent Gear Machinist typically requires 2-4 years of dedicated training and on-the-job experience. This usually involves completing an apprenticeship program or a vocational school curriculum focused on machining, followed by specialized training in gear cutting and finishing techniques. Mastery of different gear types and machinery takes consistent practice.
What are the typical education and certification requirements for a Gear Machinist?
Formal education requirements vary, but most entry-level Gear Machinist positions prefer candidates with a high school diploma or GED. Employers highly value vocational training, an associate's degree in machining technology, or completion of an accredited apprenticeship. Certifications in CNC machining or specific gear manufacturing processes also significantly boost your employability.
What are the salary expectations for a Gear Machinist at different experience levels?
Starting salaries for entry-level Gear Machinists can range from $35,000 to $45,000 annually, depending on location and industry. Experienced Gear Machinists with specialized skills and a proven track record can earn $55,000 to $75,000 or more. Overtime opportunities in manufacturing can also significantly increase your overall earnings.
Is the Gear Machinist role secure, or is it at risk from automation and outsourcing?
The demand for skilled Gear Machinists remains steady, particularly in industries requiring high-precision components like aerospace, automotive, and heavy machinery. Automation changes some tasks, but the need for human expertise in setting up, monitoring, and troubleshooting complex gear cutting machines ensures job security. Experienced machinists with advanced CNC skills are especially sought after.
What are the typical career advancement opportunities for a Gear Machinist?
Career growth for a Gear Machinist often involves specializing in advanced CNC programming, becoming a lead machinist, or moving into supervisory or management roles. Some machinists transition into quality control, machine maintenance, or even design engineering positions. Continuous learning and adapting to new technologies are crucial for advancement.
What is the typical work-life balance like for a Gear Machinist?
Work-life balance for a Gear Machinist can vary. Many manufacturing facilities operate on multiple shifts, including evenings or weekends, which might involve irregular hours. However, the work is often stable, and while demanding, it typically offers consistent schedules once you are established. Overtime is common and can impact personal time.
What are the biggest challenges and daily demands of being a Gear Machinist?
Key challenges include mastering complex machinery and software, maintaining extreme precision, and adapting to new materials and manufacturing processes. The work requires significant attention to detail and problem-solving skills to troubleshoot machine issues and ensure product quality. Physical demands, such as standing for long periods and lifting, are also part of the job.
Related Careers
Explore similar roles that might align with your interests and skills:
Lathe Machinist
A growing field with similar skill requirements and career progression opportunities.
Explore career guideManual Machinist
A growing field with similar skill requirements and career progression opportunities.
Explore career guideGear Cutter
A growing field with similar skill requirements and career progression opportunities.
Explore career guidePrecision Machinist
A growing field with similar skill requirements and career progression opportunities.
Explore career guideProduction Machinist
A growing field with similar skill requirements and career progression opportunities.
Explore career guideAssess your Gear Machinist readiness
Understanding where you stand today is the first step toward your career goals. Our Career Coach helps identify skill gaps and create personalized plans.
Skills Gap Analysis
Get a detailed assessment of your current skills versus Gear Machinist requirements. Our AI Career Coach identifies specific areas for improvement with personalized recommendations.
See your skills gapCareer Readiness Assessment
Evaluate your overall readiness for Gear Machinist roles with our AI Career Coach. Receive personalized recommendations for education, projects, and experience to boost your competitiveness.
Assess your readinessLand your dream job with Himalayas Plus
Upgrade to unlock Himalayas' premium features and turbocharge your job search.
Himalayas
Himalayas Plus
Himalayas Max
Find your dream job
Sign up now and join over 100,000 remote workers who receive personalized job alerts, curated job matches, and more for free!
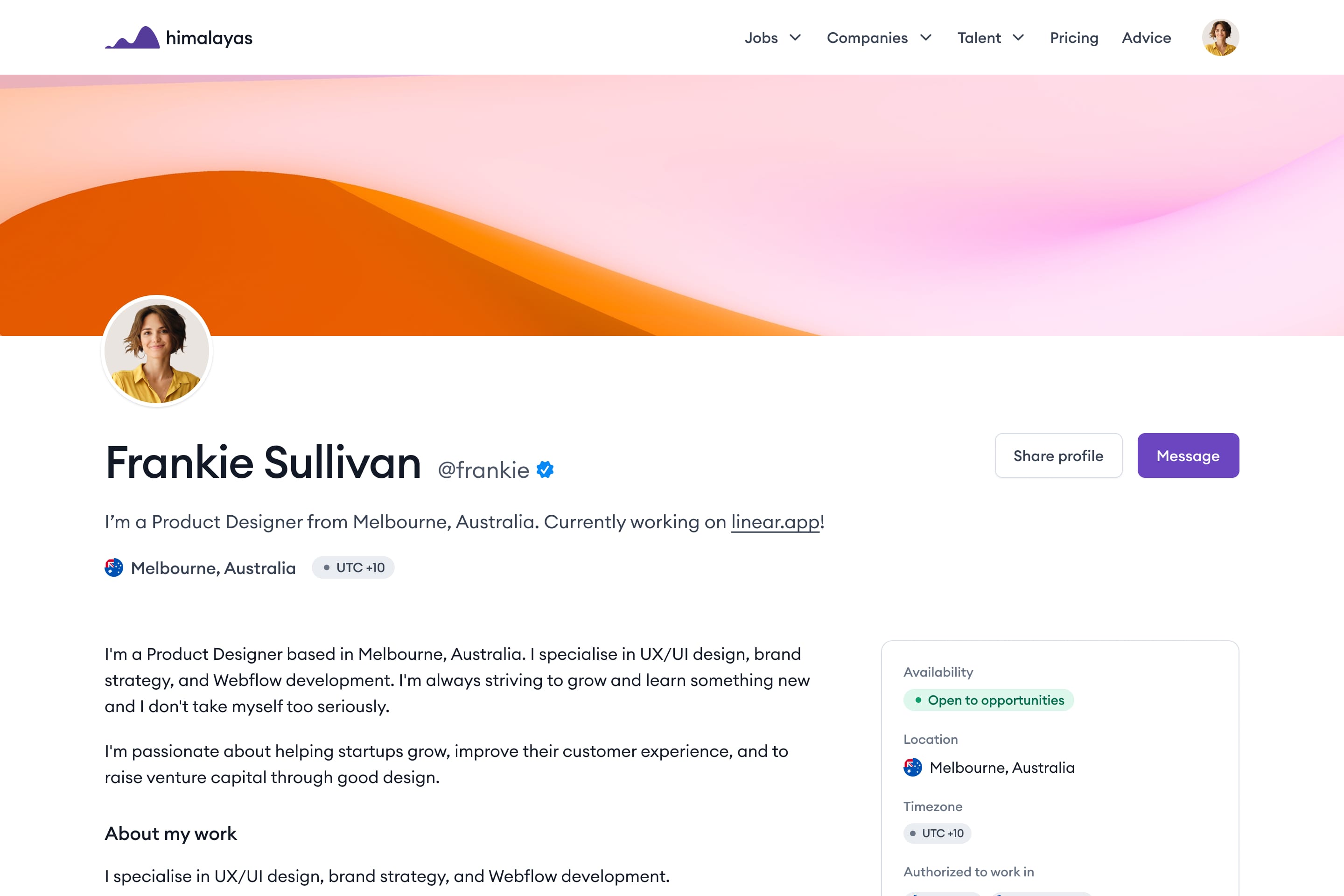