Complete Corrosion Engineer Career Guide
Corrosion engineers are vital guardians of infrastructure, preventing the degradation of materials in critical systems like pipelines, bridges, and manufacturing plants. You'll combine principles of chemistry, metallurgy, and engineering to design solutions that extend asset lifespans, enhance safety, and save industries billions in repair costs. This specialized role offers a unique blend of field work, laboratory analysis, and strategic planning, making it a compelling path for problem-solvers.
Key Facts & Statistics
Median Salary
$102,160 USD
(U.S. national median, May 2023, Source: BLS for materials engineers)
Range: $70k - $150k+ USD
Growth Outlook
1%
slower than average (Source: BLS, 2022-2032 projections for materials engineers)
Annual Openings
≈2,900
openings annually (Source: BLS, 2022-2032 projections for materials engineers, a closely related field)
Top Industries
Typical Education
Bachelor's degree in Materials Science and Engineering, Chemical Engineering, or Mechanical Engineering. Professional certifications like NACE International (now AMPP) certifications are highly valued.
What is a Corrosion Engineer?
A Corrosion Engineer specializes in understanding, preventing, and mitigating the deterioration of materials, primarily metals, due to chemical or electrochemical reactions with their environment. This role is crucial for ensuring the safety, reliability, and longevity of critical infrastructure and industrial assets across sectors like oil and gas, manufacturing, water treatment, and construction. They apply principles of chemistry, materials science, and engineering to protect against economic losses and environmental hazards caused by corrosion.
Unlike a general materials engineer who might focus on material properties for design, a Corrosion Engineer specifically concentrates on the degradation mechanisms and protective measures against corrosion. They also differ from a metallurgist, who primarily studies the physical and chemical behavior of metallic elements and their alloys. Corrosion engineers are the frontline defense against material degradation, implementing practical solutions to extend the life of structures and equipment.
What does a Corrosion Engineer do?
Key Responsibilities
- Conduct thorough inspections of materials and structures to identify signs of corrosion, assessing the extent and type of degradation present.
- Design and implement cathodic protection systems, coatings, and material selection strategies to prevent or mitigate corrosion in various industrial assets.
- Perform root cause analysis on corrosion failures, investigating environmental factors, material properties, and operational conditions to determine failure mechanisms.
- Develop and oversee maintenance programs, including monitoring schedules and repair procedures, to ensure the long-term integrity of infrastructure.
- Prepare detailed technical reports and presentations, documenting inspection findings, proposed solutions, and the performance of corrosion control measures.
- Collaborate with multidisciplinary teams, including mechanical engineers, metallurgists, and operations personnel, to integrate corrosion prevention into project designs.
- Stay current with industry standards, regulations, and emerging technologies in corrosion science and engineering to apply best practices.
Work Environment
Corrosion engineers often split their time between office environments and industrial sites. Office work involves data analysis, report writing, design, and collaboration with project teams. Fieldwork can take them to diverse locations such as oil and gas facilities, chemical plants, water treatment plants, or infrastructure projects, which may involve exposure to various weather conditions and industrial hazards.
The work environment is typically collaborative, involving close interaction with other engineers, technicians, and operational staff. The pace can vary from steady project-based work to urgent responses to integrity issues or failures. Travel is common, especially for consultants or those working across multiple sites. While some roles might offer remote work for analytical tasks, on-site presence for inspections and project oversight remains critical.
Tools & Technologies
Corrosion engineers regularly use a variety of specialized tools and software for analysis and design. They work with electrochemical testing equipment, such as potentiostats and galvanostats, to assess material susceptibility to corrosion. Non-destructive testing (NDT) tools like ultrasonic thickness gauges, eddy current testers, and visual inspection equipment are essential for field assessments.
For data analysis and modeling, they utilize specialized corrosion prediction software, finite element analysis (FEA) tools, and general engineering software like MATLAB or Python for custom scripting. They also rely on standard office productivity suites for reporting and presentations. Familiarity with industry-specific codes and standards from NACE International (now AMPP) and ASTM is crucial, guiding their material selection and design processes.
Corrosion Engineer Skills & Qualifications
A Corrosion Engineer's qualifications are highly specialized, focusing on material science, electrochemistry, and protective measures. Requirements vary significantly based on the industry, such as oil and gas, petrochemicals, infrastructure, or water treatment. Entry-level positions typically require a strong academic foundation, while senior roles demand extensive practical experience and often professional licensure.
Formal education provides the theoretical bedrock, but practical experience in corrosion assessment, mitigation, and failure analysis is equally critical. Certifications from bodies like NACE International (now AMPP) hold substantial weight, often surpassing the perceived value of a master's degree for many roles, especially in the field. These certifications validate specific competencies and practical knowledge, which are highly sought after by employers. Alternative pathways, such as vocational training combined with extensive hands-on experience and certifications, are increasingly accepted, particularly for technician-level roles that may progress into engineering positions.
The skill landscape for Corrosion Engineers is evolving with increased adoption of digital tools, data analytics for predictive maintenance, and advanced materials. Understanding the balance between broad knowledge across various corrosion mechanisms and deep specialization in areas like cathodic protection or coatings is vital for career progression. For instance, an entry-level engineer might need a general understanding of various corrosion types, while a senior engineer often specializes in complex problem-solving for specific material or environmental challenges. Misconceptions often include believing that a degree alone suffices; continuous learning through certifications and practical application is indispensable.
Education Requirements
Technical Skills
- Corrosion mechanisms and types (e.g., galvanic, pitting, crevice, stress corrosion cracking, microbiologically influenced corrosion).
- Materials science and metallurgy (e.g., ferrous and non-ferrous alloys, polymers, composites, their properties and degradation mechanisms).
- Cathodic protection design, installation, and troubleshooting (e.g., sacrificial anodes, impressed current systems, rectifiers, groundbeds).
- Protective coatings and linings (e.g., types, application methods, inspection, failure analysis, surface preparation standards).
- Corrosion monitoring techniques (e.g., ultrasonic testing, eddy current, radiographic inspection, electrochemical noise, corrosion coupons).
- Failure analysis methodologies (e.g., fractography, metallography, chemical analysis, root cause analysis).
- Material selection for corrosive environments (e.g., understanding material compatibility, environmental factors, economic considerations).
- NACE/AMPP standards and industry codes (e.g., NACE SP0169, ISO 12944, API standards, ASME codes).
- Water treatment chemistry and corrosion control in water systems (e.g., cooling water, boiler water, wastewater).
- Corrosion modeling and predictive analytics (e.g., using software tools for corrosion rate prediction, remaining life assessment).
- Non-destructive testing (NDT) methods and interpretation relevant to corrosion assessment.
- Data analysis and reporting (e.g., using statistical tools, spreadsheets, and specialized software for corrosion data management).
Soft Skills
- Problem-solving and analytical thinking: Corrosion Engineers constantly diagnose complex material degradation issues, requiring systematic investigation and root cause analysis.
- Attention to detail: Precise observation of material failures, accurate data collection, and meticulous adherence to standards are critical for effective corrosion prevention.
- Technical communication and documentation: Clearly articulating complex technical information, writing detailed reports, and explaining findings to both technical and non-technical stakeholders are essential.
- Collaboration and teamwork: Working effectively with multidisciplinary teams, including operations, maintenance, and design engineers, is crucial for integrated corrosion management.
- Risk assessment and decision-making: Evaluating the risks associated with corrosion, prioritizing mitigation efforts, and making informed decisions under uncertainty are core responsibilities.
- Adaptability and continuous learning: The field of corrosion engineering is dynamic, with new materials, technologies, and standards emerging. Staying updated is vital for long-term success.
- Stakeholder management: Managing expectations and communicating with clients, regulators, and internal teams regarding corrosion risks and mitigation strategies is important, especially in consulting or project-based roles.
How to Become a Corrosion Engineer
Entering the corrosion engineering field offers multiple pathways, typically revolving around a strong foundation in materials science, chemical engineering, or mechanical engineering. While a traditional bachelor's or master's degree provides a structured learning environment, career changers with related technical backgrounds can transition by focusing on specialized certifications and practical experience. Expect the journey to take 1-2 years for those with a relevant engineering degree seeking entry-level roles, or 2-4 years for individuals building foundational knowledge from scratch.
Entry strategies vary significantly by industry and company size. Large oil and gas companies, utilities, and infrastructure firms often prefer candidates with formal degrees and specific industry certifications like NACE (now AMPP) certifications. Smaller consultancies or specialized manufacturing firms might prioritize practical experience and a strong project portfolio. Geographic location also plays a role; regions with heavy industrial activity, such as the Gulf Coast in the U.S. or specific areas in the Middle East, offer more opportunities but can also have higher competition.
A common misconception is that all corrosion engineering work is hands-on field inspection; in reality, much of the role involves design, analysis, and predictive modeling. Building a strong network within professional organizations like AMPP (Association for Materials Protection and Performance) is crucial, as many opportunities arise through referrals and industry connections. Overcoming barriers to entry often involves demonstrating a clear understanding of corrosion mechanisms, materials selection, and protection methods, even if direct experience is limited. Focus on showcasing problem-solving abilities and a commitment to continuous learning.
Step 1
Step 2
Step 3
Step 4
Step 5
Step 6
Education & Training Needed to Become a Corrosion Engineer
A Corrosion Engineer requires a specialized blend of theoretical knowledge and practical application. Formal education, typically a Bachelor's degree in Chemical Engineering, Materials Science, or Metallurgical Engineering, forms the foundational pathway. These 4-year programs usually cost between $40,000 and $120,000+ for tuition alone, offering a comprehensive understanding of corrosion mechanisms, material selection, and prevention techniques. Master's degrees or Ph.D.s are common for research and development roles, extending the time commitment by 2-5 years and adding significant cost.
Alternative learning paths, while not replacing a foundational degree for entry-level positions, are crucial for specialization and continuous professional development. Industry certifications, such as those offered by NACE International (now AMPP), provide targeted expertise and are highly valued by employers. These certifications can range from a few hundred to several thousand dollars and typically require weeks or months of focused study. Online courses and self-study modules offer flexibility, often costing less than $1,000, but require strong self-discipline and may lack hands-on experience.
Employers highly regard formal degrees for initial hiring, as they demonstrate a broad understanding of engineering principles. Certifications enhance a candidate's profile, signaling specialized competence. Practical experience, gained through internships or entry-level roles, is as vital as theoretical knowledge, allowing engineers to apply classroom learning to real-world scenarios. The field demands continuous learning due to evolving materials, technologies, and environmental regulations. Educational needs vary by specialization, such as pipeline corrosion or marine environments, and seniority levels often require advanced certifications or further academic study. Investing in both formal education and ongoing professional development provides the best long-term career prospects in corrosion engineering.
Corrosion Engineer Salary & Outlook
Compensation for a Corrosion Engineer varies significantly based on several factors, reflecting the specialized nature of the role. Geographic location plays a crucial role; engineers in regions with extensive oil and gas infrastructure, chemical processing plants, or significant utility networks typically command higher salaries due to increased demand and often a higher cost of living. Major industrial hubs in Texas, Louisiana, and California, for example, offer premium compensation compared to areas with less industrial activity.
Experience levels and specialized certifications, such as NACE International (now AMPP) certifications, dramatically influence earning potential. An engineer with expertise in specific materials, cathodic protection, or advanced inspection techniques will earn more than a generalist. Total compensation packages often extend beyond base salary, including performance bonuses, stock options in publicly traded companies, and comprehensive benefits covering health, dental, and vision insurance. Retirement contributions, like 401(k) matching, and allowances for professional development and industry conferences also add substantial value.
Industry-specific compensation trends are also critical. The oil and gas sector historically offers some of the highest salaries for Corrosion Engineers, followed by utilities, manufacturing, and consulting. Larger corporations typically provide more robust compensation and benefits packages than smaller firms. Remote work, while less common for hands-on roles, can impact salary ranges, potentially allowing for geographic arbitrage if the employer is flexible with location. Understanding these components helps maximize earning potential and negotiate effectively, considering both base pay and the full value of the benefits package.
Salary by Experience Level
Level | US Median | US Average |
---|---|---|
Junior Corrosion Engineer | $70k USD | $75k USD |
Corrosion Engineer | $90k USD | $95k USD |
Senior Corrosion Engineer | $120k USD | $125k USD |
Lead Corrosion Engineer | $140k USD | $145k USD |
Principal Corrosion Engineer | $160k USD | $165k USD |
Corrosion Engineering Manager | $175k USD | $185k USD |
Market Commentary
The job market for Corrosion Engineers remains robust, driven by the critical need for infrastructure integrity across various industries. Demand is particularly strong in oil and gas, chemical processing, utilities, and civil infrastructure, where aging assets require continuous monitoring and maintenance. The global push for sustainability and safety regulations further accelerates this demand, as companies aim to prevent costly failures and environmental incidents. We project a steady growth outlook, with an estimated 5-7% increase in job opportunities over the next five to eight years, slightly above the national average for all occupations.
Emerging opportunities for Corrosion Engineers include renewable energy infrastructure, such as offshore wind farms and hydrogen pipelines, which present new materials and environmental challenges. The integration of digital twins, AI-driven predictive analytics, and advanced sensor technologies is also transforming the role, requiring engineers to develop strong data analysis and computational skills. This evolution moves the profession towards more proactive and preventative maintenance strategies, reducing reactive repairs. While automation may handle routine data collection, the interpretive and strategic aspects of corrosion management will remain human-centric.
The supply of qualified Corrosion Engineers often struggles to meet demand, creating a favorable market for skilled professionals. This imbalance is particularly evident for those with specialized certifications or experience in niche areas like protective coatings or materials science. Geographic hotspots for employment include the Gulf Coast region of the U.S., major industrial centers in the Midwest, and increasingly, areas developing new energy infrastructure. The profession is generally recession-resistant, as asset integrity and safety remain paramount regardless of economic cycles, ensuring long-term career viability.
Corrosion Engineer Career Path
Career progression for a Corrosion Engineer involves a clear path from technical specialization to leadership, either within an individual contributor (IC) track or a management track. Initial stages focus on mastering fundamental principles and practical application, then moving towards independent problem-solving and project leadership. Advancement speed depends on factors like industry (oil & gas, chemical, utilities), company size, and the engineer's performance and initiative in pursuing complex challenges.
The IC track typically progresses from Junior to Principal Corrosion Engineer, emphasizing deep technical expertise, specialized knowledge in areas like cathodic protection or materials science, and the ability to solve highly complex corrosion issues. The management track, often branching at the Senior or Lead level, focuses on team oversight, strategic planning, and resource management. Lateral movement into related fields like materials engineering, process safety, or asset integrity management is common, offering diverse professional avenues.
Networking within industry bodies like NACE International (now AMPP), pursuing relevant certifications (e.g., NACE certifications), and continuous learning are vital for career growth. These elements enhance an engineer's reputation and open doors to new opportunities. Company type also influences progression; startups may offer faster advancement but broader responsibilities, while large corporations provide structured paths and specialized roles. Consulting firms often demand diverse technical skills and client management expertise.
Junior Corrosion Engineer
0-2 yearsKey Focus Areas
Corrosion Engineer
2-5 yearsKey Focus Areas
Senior Corrosion Engineer
5-8 yearsKey Focus Areas
Lead Corrosion Engineer
8-12 yearsKey Focus Areas
Principal Corrosion Engineer
12+ yearsKey Focus Areas
Corrosion Engineering Manager
10+ years (with significant leadership experience)Key Focus Areas
Junior Corrosion Engineer
0-2 yearsWorks under direct supervision, assisting senior engineers with data collection, basic calculations, and field inspections. Supports the preparation of technical reports and documentation. Focuses on understanding fundamental corrosion principles and company-specific procedures. Participates in routine monitoring and maintenance activities.
Key Focus Areas
Developing foundational knowledge in corrosion mechanisms, materials science, and basic protective measures. Mastering data collection and analysis techniques. Gaining proficiency with industry standards and software tools. Building effective communication skills for technical reporting and team collaboration.
Corrosion Engineer
2-5 yearsManages assigned corrosion control projects or tasks with moderate supervision. Conducts detailed inspections, performs complex calculations, and analyzes operational data to identify corrosion risks. Develops and recommends solutions for preventing or mitigating corrosion. Collaborates with other engineering disciplines and operations personnel.
Key Focus Areas
Deepening expertise in specific corrosion control methods like cathodic protection, coatings, and inhibitors. Developing problem-solving skills for routine corrosion issues. Improving technical report writing and presentation abilities. Beginning to mentor junior staff and participate in cross-functional team discussions.
Senior Corrosion Engineer
5-8 yearsLeads complex corrosion engineering projects, often with significant financial or operational impact. Provides technical guidance and mentorship to junior team members. Conducts root cause analysis for corrosion-related failures. Develops and implements long-term corrosion management strategies. Acts as a subject matter expert for specific assets or systems.
Key Focus Areas
Mastering advanced corrosion assessment techniques and failure analysis. Developing project management skills, including budgeting and scheduling. Enhancing leadership capabilities through mentoring and guiding project teams. Cultivating strong stakeholder management and negotiation skills. Pursuing specialized certifications (e.g., NACE/AMPP certifications).
Lead Corrosion Engineer
8-12 yearsOversees multiple corrosion engineering projects or a significant program. Leads and coordinates teams of engineers and technicians. Responsible for strategic planning, resource allocation, and ensuring compliance with regulations and standards. Provides expert consultation to internal and external stakeholders. Drives continuous improvement initiatives.
Key Focus Areas
Developing strategic planning and program management skills. Cultivating strong leadership and team coordination abilities. Focusing on risk management and optimization of corrosion control programs across multiple assets. Expanding knowledge of industry best practices and emerging technologies. Enhancing client relationship management and business development skills.
Principal Corrosion Engineer
12+ yearsServes as the ultimate technical authority and expert for corrosion engineering within the organization. Drives the development of company-wide corrosion policies, standards, and best practices. Provides strategic direction on major capital projects and critical asset integrity issues. Mentors senior technical staff and influences organizational strategy. Represents the company in industry forums.
Key Focus Areas
Mastering enterprise-level strategic thinking and long-term asset integrity planning. Developing executive-level communication and presentation skills. Focusing on innovation, research, and development of new corrosion control technologies. Building a strong industry reputation through publications, presentations, and committee involvement. Providing high-level technical mentorship and strategic guidance.
Corrosion Engineering Manager
10+ years (with significant leadership experience)Manages a team or department of corrosion engineers and related technical staff. Responsible for setting departmental goals, managing budgets, and overseeing project portfolios. Develops and implements talent development plans for the team. Ensures the effective application of corrosion engineering principles across the organization. Reports to senior leadership and contributes to overall business strategy.
Key Focus Areas
Developing comprehensive leadership, people management, and organizational development skills. Mastering financial management, budgeting, and resource planning for engineering departments. Focusing on strategic alignment of corrosion engineering with business objectives. Building a strong network of industry contacts and fostering a culture of innovation and safety. Enhancing skills in talent acquisition and performance management.
Job Application Toolkit
Ace your application with our purpose-built resources:
Corrosion Engineer Resume Examples
Proven layouts and keywords hiring managers scan for.
View examplesCorrosion Engineer Cover Letter Examples
Personalizable templates that showcase your impact.
View examplesTop Corrosion Engineer Interview Questions
Practice with the questions asked most often.
View examplesCorrosion Engineer Job Description Template
Ready-to-use JD for recruiters and hiring teams.
View examplesGlobal Corrosion Engineer Opportunities
Corrosion engineers assess and mitigate material degradation across diverse global industries, including oil & gas, infrastructure, and manufacturing. International demand for this specialized role remains robust in 2025, driven by aging infrastructure and sustainability goals. Regulatory frameworks vary by country, impacting material standards and safety protocols. Professionals seek international roles for exposure to unique challenges and advanced technologies, enhancing their expertise. NACE International certifications, like the NACE CIP or CP Specialist, significantly boost global mobility and recognition.
Global Salaries
Corrosion engineer salaries vary significantly by region and experience. In North America, entry-level professionals earn $70,000-$90,000 USD, while experienced engineers command $120,000-$180,000+ USD annually, particularly in states like Texas or Alberta, Canada. These figures reflect high living costs in major industrial hubs but offer strong purchasing power.
Europe presents a diverse salary landscape. In the UK, salaries range from £40,000-£70,000 GBP ($50,000-$88,000 USD), with higher figures in London or for specialized offshore roles. Germany offers €50,000-€85,000 EUR ($54,000-$92,000 USD), often including comprehensive benefits like generous vacation and health insurance, balancing out slightly lower nominal wages with high quality of life. Scandinavian countries like Norway offer high salaries, often exceeding €70,000-€100,000 EUR ($76,000-$108,000 USD), but also feature a high cost of living and significant tax burdens.
Asia-Pacific markets, particularly in Australia and Singapore, offer competitive salaries for experienced corrosion engineers, often ranging from AUD 90,000-AUD 150,000 ($60,000-$100,000 USD) and SGD 70,000-SGD 120,000 ($52,000-$89,000 USD) respectively. The Middle East, especially in Saudi Arabia and UAE, provides tax-free salaries from $80,000-$150,000+ USD, which translates to high take-home pay despite varying local costs. These regions often offer housing and transportation allowances, significantly boosting overall compensation.
Latin America's market is emerging, with salaries in Brazil or Mexico ranging from $30,000-$60,000 USD, reflecting a lower cost of living. International experience and advanced certifications like NACE or AMPP can significantly elevate compensation across all regions, demonstrating a global standard of expertise. Salary structures also differ in terms of pension contributions, bonuses, and severance packages, which are crucial when comparing offers internationally.
Remote Work
International remote work for corrosion engineers is gaining traction, though it is often limited to specific tasks like data analysis, report writing, and consulting. Full-time remote roles are less common due to the hands-on nature of inspections and site visits. Companies increasingly hire for global remote teams to leverage specialized expertise, particularly in software-based corrosion modeling or integrity management systems.
Legal and tax implications of international remote work require careful consideration. Engineers must understand income tax obligations in both their country of residence and the employer's country. Some countries offer digital nomad visas, simplifying long-term stays. Time zone differences can pose challenges for international collaboration, necessitating flexible work schedules. Employers often have specific policies regarding equipment provision and cybersecurity for remote international staff. Salary expectations for remote roles might be adjusted based on the engineer's location and local cost of living.
Visa & Immigration
Corrosion engineers frequently qualify for skilled worker visas in major industrial economies. Popular destinations include Canada (Express Entry), Australia (Skilled Nominated Visa 190, Skilled Independent Visa 189), the UK (Skilled Worker Visa), and the US (H-1B, though highly competitive). Requirements typically include a relevant engineering degree, professional experience, and sometimes English language proficiency (IELTS, TOEFL). Credential recognition by local engineering bodies is often mandatory.
Visa application timelines vary, generally ranging from 3 to 12 months. Intra-company transfers are common for global firms moving corrosion specialists between international offices. Pathways to permanent residency often exist after several years of skilled employment, depending on the country's immigration policies. Some countries, like Australia or Canada, offer points-based systems where specialized engineering skills can earn additional points. Family visas and dependent rights are usually part of skilled worker visa programs, allowing spouses and children to accompany the primary applicant. Specific professional licensing may be required in certain jurisdictions, impacting immediate work eligibility.
2025 Market Reality for Corrosion Engineers
Understanding current market conditions is paramount for corrosion engineers navigating today's job landscape. The field has evolved significantly from 2023 to 2025, influenced by post-pandemic economic adjustments, the AI revolution, and a global pivot towards sustainability.
Broader economic factors, such as inflation and fluctuating energy prices, directly impact capital expenditure on infrastructure projects, which in turn affects hiring in this niche. Market realities for corrosion engineers vary considerably by experience level—entry-level roles are often more competitive than senior specialized positions—and by geographic region, with industrial hubs showing stronger demand. Company size also plays a role, as large corporations often have dedicated departments while smaller firms may outsource.
Current Challenges
Corrosion engineers face increased competition for specialized roles, particularly as some industries like oil and gas experience consolidation or slower growth. Market saturation exists at entry levels, making initial breaks into the field harder without specific internship experience. Economic uncertainty often delays large infrastructure projects, reducing demand for new corrosion prevention initiatives. Integrating advanced AI tools into existing workflows requires new skills, creating a mismatch for some traditional engineers. Remote work normalization means competition now extends beyond local markets, increasing the applicant pool for many positions.
Growth Opportunities
Significant opportunities exist in emerging fields like hydrogen infrastructure, carbon capture and storage (CCS), and offshore wind energy, all of which present unique corrosion challenges requiring specialized engineering solutions. Demand is also strong in traditional sectors for engineers who can integrate advanced digital tools for predictive analytics and remote monitoring of assets. Professionals who combine deep material science knowledge with proficiency in AI/ML applications for anomaly detection and lifetime prediction gain a strong competitive advantage.
Underserved markets include municipal water systems and aging civil infrastructure, where investment in rehabilitation and preventative maintenance is growing. Niche specializations such as microbiologically influenced corrosion (MIC) or high-temperature corrosion in advanced manufacturing also offer excellent prospects. Pursuing certifications from organizations like AMPP (formerly NACE/SSPC) or gaining expertise in sustainable corrosion inhibitors can significantly enhance career prospects. Market corrections might open doors as companies seek to optimize existing assets rather than build new ones, placing greater emphasis on integrity management and failure prevention.
Current Market Trends
Demand for corrosion engineers remains robust in 2025, driven by aging infrastructure and stringent regulatory requirements across various sectors. Companies prioritize asset integrity and lifecycle extension, directly increasing the need for specialized expertise in material degradation and prevention. The energy transition, particularly the shift towards hydrogen and carbon capture technologies, introduces new corrosion challenges, creating specialized demand within these emerging areas. Traditional sectors like oil & gas, water utilities, and manufacturing continue to be significant employers, focusing on maintaining existing assets and optimizing operational efficiency.
Generative AI and advanced analytics are transforming predictive maintenance and material selection in corrosion engineering. Employers increasingly seek candidates proficient in data analysis, machine learning applications for failure prediction, and digital twin technology. This shift means a deeper understanding of computational tools and simulation software is now crucial, alongside traditional metallurgy and electrochemistry. Salary trends show stability for experienced professionals, with a premium on those skilled in novel materials, AI integration, and sustainable corrosion solutions. Entry-level roles face more competition, often requiring candidates to demonstrate practical project experience or certifications in specific NACE/AMPP areas. Geographic variations exist; the Gulf Coast region in the US and the Middle East continue to be strong markets due to high concentrations of oil, gas, and chemical industries. Europe also sees consistent demand, particularly in renewable energy and infrastructure projects. Remote work is less prevalent for hands-on inspection or field-based roles but is common for design, analysis, and consulting positions.
Emerging Specializations
The field of corrosion engineering is undergoing a significant transformation, driven by advancements in materials science, digital technologies, and a growing emphasis on asset longevity and sustainability. New specialization opportunities are rapidly emerging as industries seek more predictive, proactive, and environmentally conscious approaches to corrosion management. Understanding these shifts is crucial for professionals aiming to position themselves at the forefront of the discipline.
Early positioning in these emerging areas offers a distinct advantage for career advancement in 2025 and beyond. These cutting-edge specializations often command premium compensation and accelerate career growth, reflecting the specialized knowledge and skills required. While established areas of corrosion engineering remain vital, focusing on new frontiers allows engineers to solve increasingly complex problems and contribute to next-generation infrastructure.
Many emerging areas, particularly those integrating AI and advanced sensing, are transitioning from research concepts to practical applications. They are expected to generate a substantial number of job opportunities within the next three to five years, as industries fully adopt these innovative solutions. Pursuing these specializations involves a balance of risk and reward; while they promise high growth, they also demand continuous learning and adaptability to evolving technologies.
AI/ML-Driven Predictive Corrosion Analytics
This specialization focuses on integrating artificial intelligence and machine learning algorithms with corrosion data to predict material degradation, optimize maintenance schedules, and identify high-risk assets. It moves beyond traditional empirical models to leverage vast datasets from sensors, inspections, and environmental conditions. AI-driven predictive analytics allows for more precise and cost-effective corrosion control strategies, minimizing unexpected failures and extending asset life.
Smart Sensing & IoT for Corrosion Monitoring
This area involves the development and application of advanced sensor technologies, including IoT devices, embedded sensors, and remote monitoring systems, to provide real-time data on corrosion initiation and progression. These smart monitoring systems enable continuous assessment of asset health, allowing for immediate intervention and reducing the need for manual, intrusive inspections. It is critical for industries with extensive, remote infrastructure like pipelines, offshore platforms, and renewable energy installations.
Corrosion of Advanced & Novel Materials
This specialization centers on designing and implementing corrosion protection strategies for novel materials, particularly those used in extreme environments or emerging technologies such as hydrogen infrastructure, advanced nuclear reactors, and next-generation battery systems. It requires deep knowledge of material science, electrochemistry, and the unique degradation mechanisms of composites, advanced alloys, and functionalized surfaces. This field is crucial for enabling sustainable energy and advanced manufacturing.
Nanotechnology in Corrosion Prevention
This emerging field focuses on the application of nanotechnology to develop highly effective and environmentally friendly corrosion inhibitors, coatings, and self-healing materials. Nanocoatings offer superior barrier properties and enhanced durability, while smart nanomaterials can detect and repair microscopic damage before significant corrosion occurs. This specialization is vital for reducing reliance on traditional, sometimes toxic, corrosion prevention methods and extending the lifespan of critical components.
Digital Twin for Corrosion Management
This specialization applies principles of digital twin technology to create virtual models of physical assets that simulate corrosion behavior in real-time. By integrating sensor data, historical performance, and predictive analytics, a digital twin can accurately represent the current state of corrosion, forecast future degradation, and test different mitigation strategies in a virtual environment. This enhances decision-making for maintenance, design, and operational optimization, particularly for complex, high-value assets.
Pros & Cons of Being a Corrosion Engineer
Understanding both the advantages and challenges of a career is crucial before committing to a path. A corrosion engineer's experience can vary significantly based on the industry, company culture, specific projects, and individual specialization. Factors such as working for an oil and gas giant versus a water treatment plant, or focusing on design versus inspection, will shape daily realities. Additionally, the benefits and drawbacks may shift at different career stages; early career engineers might face steep learning curves, while senior professionals deal with higher stakes and management responsibilities. What one person considers a 'pro,' like extensive travel, another might view as a 'con.' This assessment aims to provide a realistic overview, helping aspiring corrosion engineers set appropriate expectations for this vital and specialized field.
Pros
- High demand across diverse industries ensures strong job security, as sectors like oil and gas, infrastructure, manufacturing, and water treatment constantly require expertise in preventing material degradation.
- The work is intellectually stimulating, involving complex problem-solving by applying principles of chemistry, materials science, and engineering to diagnose failures and design preventative measures.
- Significant impact on safety and sustainability, as effective corrosion control protects critical infrastructure, prevents environmental spills, and extends the lifespan of valuable assets, contributing to public welfare.
- Opportunities for global travel and fieldwork are common, especially in industries with international operations or specialized inspection needs, offering varied experiences and exposure to different environments.
- Competitive compensation packages are typical, reflecting the specialized knowledge and critical role corrosion engineers play in asset integrity and operational efficiency, often including good benefits.
- Continuous learning and professional growth are inherent to the role, as engineers regularly engage with new materials, advanced technologies, and evolving industry standards, fostering ongoing skill development.
- The role offers a blend of theoretical analysis and practical application, allowing engineers to move between laboratory testing, data analysis, and hands-on site inspections, providing a dynamic work experience.
Cons
- Fieldwork often involves exposure to hazardous environments, including industrial sites, offshore platforms, or remote locations, which can pose safety risks and require strict adherence to protocols.
- The work can be highly specialized and niche, potentially limiting career mobility if one wishes to transition to broader engineering roles outside of corrosion prevention.
- Corrosion issues often arise unexpectedly and require urgent attention, leading to unpredictable work schedules, on-call duties, and the need to respond to emergencies outside of standard working hours.
- Continuous learning is essential as materials, coatings, and prevention technologies evolve rapidly, requiring engineers to stay updated through ongoing training and professional development.
- Solving complex corrosion problems can be intellectually demanding and frustrating, as failures can be subtle, multifactorial, and require extensive investigation and testing to diagnose.
- Budgetary constraints can limit the implementation of optimal corrosion prevention strategies, forcing engineers to compromise on solutions or justify significant investments, which can be challenging.
- Legal and regulatory compliance is a significant burden, as corrosion engineers must ensure all designs and maintenance procedures meet stringent industry standards and environmental regulations, carrying high liability.
Frequently Asked Questions
Corrosion Engineers face distinct challenges balancing material science with practical application in harsh environments. This section addresses the most common questions about entering and advancing in this specialized field, from required education to managing safety-critical projects and understanding industry demand.
What educational background and certifications do I need to become a Corrosion Engineer?
Most Corrosion Engineer roles require a bachelor's degree in materials science, chemical engineering, metallurgical engineering, or a related engineering discipline. Some specialized positions, particularly in research or highly complex industries, may prefer a master's degree. Professional certifications, such as those from NACE International (now AMPP), are highly valued and often expected for career progression, demonstrating specialized knowledge in corrosion prevention and control.
What are the typical salary expectations for an entry-level and experienced Corrosion Engineer?
Entry-level Corrosion Engineers can expect to earn a competitive salary, often ranging from $60,000 to $80,000 annually, depending on location, industry, and specific company. With 5-10 years of experience and professional certifications, salaries can increase significantly, reaching $90,000 to $130,000 or more. Senior or principal engineers, especially those in leadership or consulting roles, command even higher compensation.
What is the job security and market demand like for Corrosion Engineers?
The job market for Corrosion Engineers is stable and growing, driven by the critical need to maintain aging infrastructure and industrial assets across various sectors. Industries such as oil and gas, petrochemicals, water treatment, aerospace, and civil infrastructure constantly require experts to prevent material degradation. This consistent demand provides good job security, as corrosion remains a persistent and costly problem globally.
What kind of work-life balance can I expect as a Corrosion Engineer, considering potential field work?
A Corrosion Engineer's work-life balance can vary. Many roles involve standard office hours, but project-based work, particularly in industries like oil and gas or infrastructure, may require occasional travel to sites, extended hours during critical phases, or on-call duties for emergency situations. Field-based roles inherently involve more travel and time away from home. Office-based design or consulting roles often offer more predictable schedules.
What are the typical career progression paths for a Corrosion Engineer?
Career growth for Corrosion Engineers can lead to various specialized paths. You can advance to senior engineering roles, project management, or technical leadership positions overseeing corrosion control programs. Opportunities also exist in research and development, consulting, sales of corrosion-resistant materials or coatings, or even transitioning into broader asset integrity management roles. Continuous learning and obtaining advanced certifications are key for upward mobility.
Is remote work a realistic option for Corrosion Engineers, or is on-site presence usually required?
While some office-based design or consulting roles may offer remote work flexibility, many Corrosion Engineer positions require on-site presence. This is particularly true for roles involving inspections, failure analysis, material testing, or supervising installation of corrosion protection systems. Field work is an inherent part of ensuring the integrity of physical assets. Hybrid models, balancing office and field work, are becoming more common in certain sectors.
What are the biggest challenges or frustrations that Corrosion Engineers typically face in their day-to-day work?
The biggest challenge is often balancing theoretical knowledge with practical application in diverse and often harsh environments. You must understand complex material behaviors, predict degradation mechanisms, and design effective, cost-efficient prevention strategies. Communicating complex technical information to non-technical stakeholders and adapting solutions to evolving regulatory standards also present ongoing challenges.
Related Careers
Explore similar roles that might align with your interests and skills:
Corrosion Technician
A growing field with similar skill requirements and career progression opportunities.
Explore career guideMetallurgical Engineer
A growing field with similar skill requirements and career progression opportunities.
Explore career guidePipeline Engineer
A growing field with similar skill requirements and career progression opportunities.
Explore career guidePiping Engineer
A growing field with similar skill requirements and career progression opportunities.
Explore career guideOxidation Engineer
A growing field with similar skill requirements and career progression opportunities.
Explore career guideAssess your Corrosion Engineer readiness
Understanding where you stand today is the first step toward your career goals. Our Career Coach helps identify skill gaps and create personalized plans.
Skills Gap Analysis
Get a detailed assessment of your current skills versus Corrosion Engineer requirements. Our AI Career Coach identifies specific areas for improvement with personalized recommendations.
See your skills gapCareer Readiness Assessment
Evaluate your overall readiness for Corrosion Engineer roles with our AI Career Coach. Receive personalized recommendations for education, projects, and experience to boost your competitiveness.
Assess your readinessSimple pricing, powerful features
Upgrade to Himalayas Plus and turbocharge your job search.
Himalayas
Himalayas Plus
Himalayas Max
Find your dream job
Sign up now and join over 100,000 remote workers who receive personalized job alerts, curated job matches, and more for free!
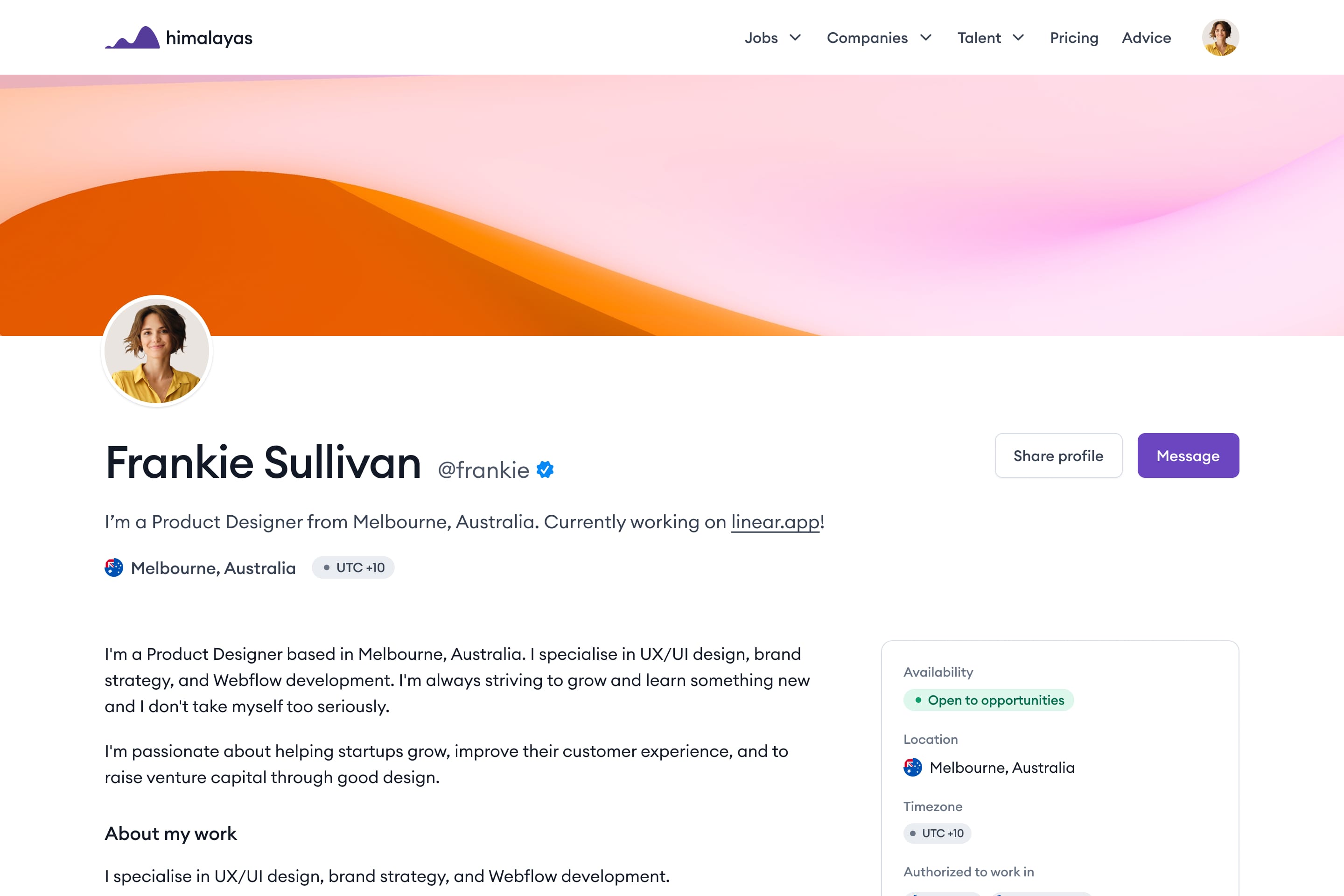