Complete Oxidation Engineer Career Guide
Oxidation engineers stand at the forefront of semiconductor manufacturing, meticulously controlling the growth of thin oxide layers critical for microchip performance. This specialized role combines materials science with process engineering, ensuring the integrity and functionality of every silicon wafer. If you are fascinated by the nanoscale precision required to build the digital world's foundations, this career offers a unique blend of scientific challenge and direct impact on cutting-edge technology.
Key Facts & Statistics
Median Salary
$124,310 USD
(U.S. national median for Semiconductor Process Engineers, BLS, May 2023)
Range: $80k - $180k+ USD
Growth Outlook
16%
much faster than average (for Semiconductor Process Engineers, BLS 2022-2032)
Annual Openings
≈3,200
openings annually (for Semiconductor Process Engineers, BLS)
Top Industries
Typical Education
Bachelor's or Master's degree in Materials Science, Chemical Engineering, Electrical Engineering, or Physics
What is an Oxidation Engineer?
An Oxidation Engineer specializes in the precise growth of thin dielectric films, primarily silicon dioxide, on semiconductor wafers. This critical process, known as oxidation, forms insulating layers essential for transistors, capacitors, and other microelectronic components. They ensure these films have specific electrical and physical properties necessary for device functionality and reliability.
This role differs significantly from a broader Process Engineer, who might oversee multiple steps in the fabrication process. The Oxidation Engineer possesses deep expertise specifically in the thermal and chemical reactions involved in forming these insulating layers, understanding how variations in temperature, gas flow, and pressure affect film quality. They are crucial for advancing transistor technology and improving device performance by perfecting these foundational dielectric layers.
What does an Oxidation Engineer do?
Key Responsibilities
- Develop and optimize oxidation processes for semiconductor manufacturing, focusing on achieving desired film thickness, uniformity, and material properties.
- Conduct experiments and analyze data to understand the kinetics and mechanisms of oxidation reactions, improving process control and yield.
- Design and implement process control strategies using statistical process control (SPC) and fault detection and classification (FDC) to maintain process stability.
- Collaborate with equipment engineers to specify, qualify, and troubleshoot oxidation furnaces and related vacuum systems.
- Perform root cause analysis for process deviations or product defects, identifying and implementing corrective actions to prevent recurrence.
- Document process specifications, operating procedures, and experimental results, ensuring clear communication and knowledge transfer within the team.
- Evaluate new materials and precursors for their suitability in oxidation processes, assessing their impact on device performance and reliability.
Work Environment
Oxidation engineers primarily work in advanced semiconductor fabrication facilities, which are highly controlled cleanroom environments. The work involves a mix of hands-on experimentation in the fab, data analysis at a workstation, and collaborative meetings. They often work closely with process engineers, equipment engineers, and material scientists. The pace can be fast, especially during new product introductions or when troubleshooting urgent process issues. While the role is typically on-site, some flexibility might exist for analytical tasks. Schedules are generally standard business hours, but occasional off-hour support for critical issues or experiments is common.
Tools & Technologies
Oxidation engineers regularly utilize specialized equipment such as horizontal and vertical furnaces, rapid thermal processing (RTP) systems, and plasma-enhanced chemical vapor deposition (PECVD) tools for specific oxidation applications. They work with various gases including oxygen, hydrogen, and inert gases like nitrogen and argon. For process control and data analysis, they use statistical software like JMP or Minitab, alongside custom data analysis scripts often written in Python or MATLAB. They also interact with manufacturing execution systems (MES) and various sensor technologies for real-time process monitoring. Understanding of vacuum systems, gas delivery systems, and cleanroom protocols is essential.
Oxidation Engineer Skills & Qualifications
Oxidation Engineers specialize in designing, optimizing, and maintaining processes involving high-temperature oxidation in semiconductor manufacturing. Their expertise is crucial for creating insulating layers and controlling dopant diffusion on silicon wafers. Qualification requirements for this role prioritize a strong foundation in materials science, chemical engineering, or electrical engineering, often coupled with hands-on experience in a cleanroom environment.
Requirements for Oxidation Engineers vary significantly with seniority. Entry-level positions typically seek candidates with a bachelor's degree and some internship experience, focusing on process monitoring and basic troubleshooting. Senior roles demand advanced degrees, extensive experience with diverse oxidation techniques (e.g., dry, wet, rapid thermal oxidation), and the ability to lead process development, integrate new equipment, and resolve complex yield issues. Company size and specific product lines also influence requirements; larger fabs with diverse product portfolios may require broader expertise, while smaller, specialized firms might seek deep knowledge in niche oxidation processes.
Formal education is highly valued in this field, particularly for theoretical understanding of semiconductor physics and chemistry. Practical experience, however, often carries equal or greater weight, especially for roles involving direct process ownership and improvement. While specific certifications are less common than in IT, participation in industry consortia or specialized training programs focused on semiconductor processing equipment or advanced materials characterization can add significant value. The skill landscape is continuously evolving with demands for higher throughput, thinner gate dielectrics, and integration with novel materials. This necessitates continuous learning in areas like atomic layer deposition (ALD) and advanced metrology techniques. Balancing a deep understanding of oxidation fundamentals with an adaptability to integrate new technologies is critical for career progression.
Education Requirements
Technical Skills
- Semiconductor device physics and materials science fundamentals
- Thermal oxidation processes (dry, wet, rapid thermal oxidation, plasma oxidation)
- Furnace operation and maintenance (e.g., vertical furnaces, RTP systems)
- Thin film deposition techniques (e.g., CVD, PVD, ALD)
- Metrology and characterization techniques (e.g., ellipsometry, SEM, TEM, XPS, SIMS, AFM)
- Statistical Process Control (SPC) and Design of Experiments (DOE)
- Data analysis and statistical software (e.g., JMP, Minitab, Python with NumPy/Pandas)
- Cleanroom protocols and contamination control practices
- Vacuum technology and gas delivery systems
- Process integration principles in semiconductor manufacturing
- Defect analysis and yield improvement methodologies
- Basic programming for automation or data scripting (e.g., Python, MATLAB)
Soft Skills
- Problem-solving and analytical thinking: Essential for diagnosing process deviations, identifying root causes of defects, and developing effective solutions in complex manufacturing environments.
- Attention to detail: Crucial for maintaining precise process control, interpreting subtle data trends, and ensuring product quality in highly sensitive semiconductor fabrication.
- Collaboration and teamwork: Required for working effectively with equipment engineers, process integration engineers, and R&D teams to optimize processes and troubleshoot issues.
- Technical communication: Important for clearly documenting process specifications, writing detailed reports, and effectively conveying complex technical information to diverse audiences, including non-technical stakeholders.
- Adaptability and continuous learning: Necessary to keep pace with rapid technological advancements in semiconductor materials and processing techniques.
- Time management and prioritization: Vital for managing multiple projects, troubleshooting urgent issues, and meeting production deadlines in a fast-paced manufacturing setting.
- Safety consciousness: Paramount for adhering to strict cleanroom protocols, handling hazardous materials, and operating high-temperature equipment safely.
How to Become an Oxidation Engineer
Breaking into the Oxidation Engineer field requires a strong foundation in materials science, chemistry, and process engineering. Traditional entry pathways typically involve a bachelor's or master's degree in these disciplines, often with a specialization in semiconductors or advanced materials. While a formal degree is common, individuals with extensive hands-on experience in related manufacturing environments, particularly those involving high-temperature processes or thin-film deposition, can transition into this specialized role.
The timeline for entry varies significantly based on your starting point. A complete beginner pursuing a relevant degree might expect 4-6 years of academic preparation, followed by 1-2 years in an entry-level process technician or junior engineer role to gain practical experience. Career changers with a strong STEM background could transition in 1-3 years by focusing on targeted certifications, hands-on projects, and networking within semiconductor or advanced manufacturing hubs. Geographic location plays a crucial role; major semiconductor manufacturing regions like Silicon Valley, Arizona, Texas, and parts of Asia offer more opportunities.
Success in this field hinges on combining theoretical knowledge with practical problem-solving abilities. Companies prioritize candidates who can demonstrate an understanding of oxidation mechanisms, equipment operation, and data analysis for process improvement. Networking with professionals at industry conferences, participating in university research projects, and securing internships are vital for gaining visibility and understanding the specific demands of different companies, from large corporations to specialized material science startups. Overcoming barriers often involves proving your practical aptitude through lab work or relevant project experience if your academic background is not directly aligned.
Step 1
Step 2
Step 3
Step 4
Step 5
Step 6
Education & Training Needed to Become an Oxidation Engineer
An Oxidation Engineer specializes in processes involving material oxidation, crucial in semiconductor manufacturing, advanced materials, and chemical engineering. The educational landscape for this role is highly specialized, primarily favoring formal university degrees due to the deep theoretical and practical knowledge required. A Bachelor's or Master's degree in Materials Science, Chemical Engineering, Electrical Engineering, or Physics is typically the foundational requirement, often costing $40,000 to $120,000+ for a four-year program. These degrees provide the essential understanding of thermodynamics, kinetics, material properties, and reactor design, taking four to six years to complete.
Alternative learning paths, such as bootcamps or general online courses, are generally insufficient for an Oxidation Engineer role. While some specialized certifications in semiconductor processing or thin-film deposition might supplement a degree, they do not replace it. These certifications, if available, might cost $1,000-$5,000 and take weeks to months. Employers in the semiconductor industry, in particular, highly value candidates with strong academic backgrounds and often prefer graduate degrees for research and development positions due to the complex, cutting-edge nature of the work.
Practical experience gained through internships, co-op programs, or laboratory work during academic studies is as critical as theoretical knowledge. Continuous learning is vital, involving staying updated on new oxidation techniques, equipment, and materials through industry conferences, journals, and advanced short courses offered by universities or equipment manufacturers. These professional development opportunities can range from a few hundred to several thousand dollars annually. The specific educational needs for an Oxidation Engineer vary by industry, with semiconductor roles demanding more specialized physics and materials knowledge than, for example, corrosion engineering roles, which might lean more on chemical engineering principles. Industry-specific quality standards, such as those related to cleanroom protocols or process control, are often learned on the job or through vendor-specific training.
Oxidation Engineer Salary & Outlook
Compensation for an Oxidation Engineer varies significantly based on several factors, reflecting the specialized nature of this role within semiconductor manufacturing and materials science. Geographic location plays a crucial role; engineers in established tech hubs like Silicon Valley, Austin, or Boston typically command higher salaries due to increased demand and a higher cost of living. Conversely, regions with emerging tech industries may offer slightly lower, but still competitive, compensation.
Experience, specialization within oxidation processes (e.g., wet oxidation, dry oxidation, thermal oxidation, or advanced thin film growth), and specific skill sets in process optimization or equipment management directly impact earning potential. Total compensation extends beyond base salary to include performance bonuses, stock options or equity, comprehensive health and dental benefits, and generous retirement contributions like 401(k) matching. Many companies also provide professional development allowances for conferences or certifications, recognizing the continuous learning required in this field.
Industry-specific trends, such as the increasing demand for advanced semiconductor devices and new material properties, drive salary growth for Oxidation Engineers. Engineers with expertise in novel materials or high-volume manufacturing processes often have stronger negotiation leverage. Remote work is less common for this role due to the hands-on nature of process development and equipment interaction, meaning geographical arbitrage opportunities are limited. International markets also present variations, though the salary figures provided here are in USD and reflect the competitive landscape in the United States.
Salary by Experience Level
Level | US Median | US Average |
---|---|---|
Junior Oxidation Engineer | $80k USD | $85k USD |
Oxidation Engineer | $105k USD | $110k USD |
Senior Oxidation Engineer | $140k USD | $145k USD |
Lead Oxidation Engineer | $170k USD | $175k USD |
Principal Oxidation Engineer | $200k USD | $205k USD |
Market Commentary
The job market for Oxidation Engineers remains robust, driven primarily by the relentless demand for advanced semiconductor devices, microelectronics, and specialized materials. This role is critical in manufacturing processes that require precise control over material properties at the atomic level. The market exhibits steady growth, with projections indicating a continued need for highly skilled engineers in semiconductor fabrication and related industries through 2030, aligning with broader growth in materials science and engineering fields.
Emerging opportunities for Oxidation Engineers include roles in developing next-generation memory technologies, advanced packaging solutions, and novel sensor applications. The push for smaller, more powerful, and energy-efficient electronic components directly translates into a heightened demand for expertise in thin film deposition and controlled oxidation processes. This creates a supply-demand imbalance where qualified engineers are often in high demand, particularly those with experience in atomic layer deposition (ALD) or other advanced deposition techniques.
Technological changes, such as the increasing integration of AI and machine learning for process control and optimization, are transforming the role. Oxidation Engineers who can leverage data analytics to improve yield and efficiency will be highly valued. While automation impacts some aspects of manufacturing, the complex R&D and process troubleshooting inherent to oxidation engineering ensure the role remains largely resistant to full automation. This profession is relatively recession-resistant due to its foundational importance in critical industries, making it a stable career choice. Geographic hotspots continue to be major semiconductor manufacturing hubs globally, with significant opportunities in the U.S., particularly in Arizona, Texas, and New York.
Oxidation Engineer Career Path
Career progression for an Oxidation Engineer typically involves a deep dive into semiconductor fabrication processes, focusing on the controlled growth of silicon dioxide layers. Professionals advance by mastering the intricacies of thin film deposition, thermal processes, and material science, moving from executing established procedures to innovating new techniques.
Advancement can follow either an individual contributor (IC) track, concentrating on technical expertise and innovation, or a management/leadership track, guiding teams and projects. Factors influencing progression include demonstrated technical proficiency, the ability to troubleshoot complex process issues, and success in improving yield or efficiency. Company size, industry sector (e.g., memory, logic, power devices), and economic conditions in the semiconductor market also shape available opportunities and advancement speed.
Lateral movement often involves transitioning to related process engineering roles like Diffusion, CVD, or PVD, or moving into R&D or equipment engineering. Continuous learning through industry seminars, specialized certifications in semiconductor processing, and active participation in professional organizations are crucial for sustained growth. Building a strong professional network and seeking mentorship from experienced engineers significantly aid career trajectory and open doors to advanced roles or specialized projects.
Junior Oxidation Engineer
0-2 yearsKey Focus Areas
Oxidation Engineer
2-5 yearsKey Focus Areas
Senior Oxidation Engineer
5-8 yearsKey Focus Areas
Lead Oxidation Engineer
8-12 yearsKey Focus Areas
Principal Oxidation Engineer
12+ yearsKey Focus Areas
Junior Oxidation Engineer
0-2 yearsExecute standard oxidation recipes and monitor process parameters under direct supervision. Perform routine equipment checks and basic preventative maintenance. Collect and record process data accurately. Support senior engineers in troubleshooting minor process issues and preparing process reports.
Key Focus Areas
Develop foundational knowledge in semiconductor physics, materials science, and cleanroom protocols. Gain proficiency in operating oxidation furnaces and basic process control software. Learn to interpret process data and identify common deviations. Focus on safety procedures and precise execution of work instructions.
Oxidation Engineer
2-5 yearsOperate and optimize various oxidation processes independently, ensuring adherence to specifications. Troubleshoot and resolve complex process excursions and equipment issues. Analyze process data to identify root causes of defects and implement corrective actions. Collaborate with integration and device engineers to meet product requirements.
Key Focus Areas
Master advanced oxidation techniques, including dry, wet, and high-pressure oxidation. Develop strong analytical skills for data interpretation and statistical process control (SPC). Learn to optimize existing processes for improved uniformity, thickness control, and electrical properties. Begin to understand the impact of oxidation on device performance.
Senior Oxidation Engineer
5-8 yearsLead the development and qualification of new oxidation processes and technologies. Drive continuous improvement initiatives for critical oxidation steps, enhancing yield and reliability. Provide expert technical support for complex process issues and equipment upgrades. Design and execute experiments (DOE) to optimize process windows and solve challenging problems.
Key Focus Areas
Specialize in advanced thermal process modeling and simulation. Develop expertise in new material integration for oxidation layers and advanced metrology techniques. Lead process improvement projects, focusing on yield enhancement, cost reduction, and cycle time optimization. Mentor junior engineers and provide technical guidance.
Lead Oxidation Engineer
8-12 yearsOversee a team of Oxidation Engineers, setting technical priorities and managing project timelines. Drive the strategic direction for oxidation process development and integration across multiple product lines. Act as a primary technical liaison with equipment vendors and external research partners. Ensure the successful transfer of new processes from R&D to high-volume manufacturing.
Key Focus Areas
Cultivate strong project management and cross-functional leadership skills. Develop strategic understanding of semiconductor roadmaps and market trends impacting oxidation technology. Guide the technical direction of multiple oxidation projects. Foster innovation within the team and build strong relationships with R&D and manufacturing groups.
Principal Oxidation Engineer
12+ yearsDefine the overall technical vision and strategy for oxidation processes across the company. Lead high-impact, cross-departmental initiatives that significantly advance the state of the art in semiconductor manufacturing. Serve as a top-tier technical expert, advising executive leadership on critical technology investments and strategic partnerships. Represent the company in industry forums and academic collaborations.
Key Focus Areas
Shape the long-term technology roadmap for oxidation within the organization. Drive fundamental research into novel oxidation techniques and materials for next-generation devices. Provide thought leadership in the field, influencing industry standards and best practices. Develop a deep understanding of intellectual property and patent strategies.
Job Application Toolkit
Ace your application with our purpose-built resources:
Oxidation Engineer Resume Examples
Proven layouts and keywords hiring managers scan for.
View examplesOxidation Engineer Cover Letter Examples
Personalizable templates that showcase your impact.
View examplesTop Oxidation Engineer Interview Questions
Practice with the questions asked most often.
View examplesOxidation Engineer Job Description Template
Ready-to-use JD for recruiters and hiring teams.
View examplesGlobal Oxidation Engineer Opportunities
Oxidation engineers apply their specialized knowledge globally across semiconductor, chemical, and materials industries. Demand for their expertise is strong in regions with advanced manufacturing, especially in Asia and North America. Regulatory compliance and specific process standards vary significantly between countries, impacting design and operational practices. Professionals seek international roles for exposure to diverse technologies and cutting-edge research facilities. International certifications, though not strictly standardized, often relate to process safety or quality management, which can enhance global mobility.
Global Salaries
Salaries for Oxidation Engineers vary significantly by region and industry. In North America, particularly the US (Silicon Valley, Arizona), entry-level engineers earn $70,000-$90,000 USD, while experienced professionals can command $120,000-$180,000 USD. This reflects a high cost of living in key tech hubs.
Europe offers diverse ranges. Germany and the Netherlands provide $60,000-$100,000 EUR ($65,000-$110,000 USD), with strong social benefits like extended vacation and comprehensive healthcare. The UK typically sees $50,000-$85,000 GBP ($63,000-$107,000 USD).
Asia-Pacific markets, especially South Korea, Taiwan, and Singapore, show competitive salaries due to their robust semiconductor industries. Experienced engineers can earn $80,000-$150,000 USD in these regions. Japan's salaries range from $60,000-$110,000 USD, with a slightly lower cost of living outside major cities. These regions often have lower overall tax burdens compared to parts of Europe.
Latin America and emerging markets typically offer lower cash compensation, but the purchasing power can be comparable due to significantly reduced living costs. For instance, in Mexico, salaries might range from $30,000-$60,000 USD. Compensation structures also differ; some countries emphasize base salary, while others include substantial performance bonuses or stock options. Tax implications vary widely, impacting net take-home pay, with some European countries having higher income tax rates than North America or Asia. International experience and advanced degrees often lead to higher compensation globally.
Remote Work
International remote work for Oxidation Engineers is limited due to the hands-on nature of their roles, which often involve direct interaction with fabrication equipment and lab environments. Most positions require on-site presence in manufacturing facilities or R&D labs.
However, some aspects, such as process modeling, data analysis, and technical consulting, can be performed remotely. Companies with global operations might employ engineers for remote support or design phases. Time zone differences pose challenges for international team collaboration, requiring flexible working hours.
Digital nomad opportunities are rare for this specific role, as few countries offer specific visas for highly specialized, non-location-independent engineering. When remote work is possible, tax implications and legal compliance for both the employer and employee across borders become complex. Employers often prefer hiring within countries where they have established entities. Salary expectations for remote roles might adjust based on the employee's location and the employer's global compensation strategy.
Visa & Immigration
Oxidation Engineers typically qualify for skilled worker visas in major manufacturing hubs. Popular destinations include the US (H-1B, L-1 for intra-company transfers), Germany (Blue Card), Canada (Express Entry), and Asian countries like Singapore, South Korea, and Taiwan (various employment passes). Educational credential recognition is crucial; degrees in materials science, chemical engineering, or electrical engineering are usually required. Professional licensing is not universally required for this role but can be beneficial.
Visa timelines vary from a few months to over a year, depending on the country and visa type. Applicants usually need a job offer, relevant qualifications, and sometimes English or local language proficiency tests. Pathways to permanent residency often exist after several years of skilled employment. Dependent visas are generally available for spouses and children. Some countries prioritize STEM professionals, potentially offering faster processing or more favorable conditions for highly specialized engineers.
2025 Market Reality for Oxidation Engineers
Understanding current market conditions is crucial for Oxidation Engineers to navigate evolving career landscapes. The field has seen significant shifts from 2023-2025, influenced by post-pandemic supply chain recalibrations and the rapid acceleration of AI in materials science.
Broader economic factors, such as global chip demand and R&D investment, directly impact job availability in this highly specialized area. Market realities vary by experience level, with senior engineers in high demand for complex problem-solving, while entry-level roles face more competition. Geographic location and company size also dictate opportunities, with major semiconductor manufacturers offering the most consistent roles. This analysis provides an honest assessment of current market conditions.
Current Challenges
Oxidation Engineers face increased competition, especially for entry-level roles, as some companies consolidate process teams. Economic uncertainties lead to more conservative hiring in capital-intensive industries like semiconductor manufacturing. A clear skill gap exists between traditional chemical engineering backgrounds and the advanced materials science or AI-driven process optimization skills now in demand.
Growth Opportunities
Strong demand exists for Oxidation Engineers specializing in advanced semiconductor nodes (3nm and below) and novel materials for quantum computing or neuromorphic chips. Emerging roles focus on integrating AI for real-time process optimization and defect reduction in oxidation processes. Professionals can gain an advantage by mastering machine learning applications for process control and predictive analytics.
Underserved markets include niche areas like power electronics and specialized sensor manufacturing, which are experiencing growth. Engineers with expertise in atomic layer deposition (ALD), high-k dielectrics, and ultra-thin film oxidation possess significant competitive advantages. Market corrections can create opportunities for engineers to join companies investing in next-generation technologies. Sectors like electric vehicle battery manufacturing and advanced packaging also remain strong despite broader market challenges, offering new avenues for Oxidation Engineers. Investing in certifications for AI/ML in manufacturing or advanced materials characterization can strategically position candidates.
Current Market Trends
Hiring for Oxidation Engineers shows steady demand within the semiconductor and advanced materials sectors, particularly for roles involving novel device fabrication and material science. Recent industry changes emphasize process miniaturization and enhanced material purity, driven by AI integration for predictive maintenance and process control. Economic conditions, while stable, encourage efficiency, favoring engineers who can optimize existing lines rather than solely design new ones.
Generative AI and advanced simulation tools are transforming process development, reducing the need for extensive physical prototyping and shifting employer requirements towards engineers proficient in these digital tools. Companies now seek Oxidation Engineers with strong data analytics skills, not just traditional chemical or materials engineering expertise. Salary trends remain competitive for specialists in cutting-edge areas like atomic layer deposition (ALD) and advanced thermal oxidation, but market saturation affects generalist roles without specialized skills.
Geographic variations are significant; demand concentrates in established tech hubs like Silicon Valley, Arizona, and parts of Asia, where major fabs operate. Remote work opportunities are limited due to the hands-on nature of process development and equipment oversight. Hiring patterns remain relatively consistent year-round, but major fab expansions or new product cycles can create surges in demand.
Emerging Specializations
The field of Oxidation Engineering is evolving rapidly, driven by advancements in material science, environmental regulations, and the increasing demand for sustainable industrial processes. New specialization opportunities are emerging at the intersection of traditional oxidation chemistry and cutting-edge technologies like artificial intelligence, advanced catalysis, and circular economy principles.
Positioning oneself early in these nascent areas offers significant career advantages for 2025 and beyond. Professionals who develop expertise in these future-oriented niches often command premium compensation and experience accelerated career growth, as their specialized skills address critical industry needs. While established specializations remain vital, exploring emerging areas can unlock pathways to leadership and innovation.
Emerging specializations typically take several years to become mainstream, creating substantial job opportunities. For Oxidation Engineers, this timeline means that investing in these new skill sets now prepares them for a surge in demand in the coming years. There is an inherent risk in specializing in cutting-edge areas due to their novelty, but the potential for high reward—both professionally and financially—is considerable for those who anticipate and adapt to these shifts.
Circular Economy Oxidation Specialist
This specialization focuses on designing and implementing oxidation processes that minimize waste generation and maximize resource recovery, aligning with circular economy principles. It involves developing novel catalytic oxidation methods for converting waste streams into valuable chemicals or energy, moving beyond traditional waste treatment to resource valorization. The emphasis is on process intensification and creating closed-loop systems to reduce environmental impact and improve economic efficiency.
AI-Driven Process Optimization Engineer
This area involves leveraging artificial intelligence and machine learning to optimize oxidation processes for efficiency, selectivity, and safety. Engineers in this field develop predictive models for reaction kinetics, optimize operating conditions in real-time, and design smart control systems for industrial oxidizers. The goal is to enhance process performance, reduce energy consumption, and minimize byproduct formation through data-driven insights and autonomous operation.
Sustainable Environmental Oxidation Engineer
This specialization addresses the critical need for sustainable and environmentally benign oxidation technologies. It involves developing and applying advanced oxidation processes (AOPs) for water and wastewater treatment, air pollution control, and remediation of contaminated sites. The focus is on processes that use minimal energy, produce fewer harmful byproducts, and effectively remove recalcitrant pollutants, ensuring compliance with evolving environmental standards.
Advanced Materials for Oxidation Specialist
This field focuses on the development and application of advanced materials, such as novel catalysts and sorbents, to improve the efficiency and selectivity of oxidation reactions. It includes designing materials with enhanced stability, activity, and regenerability for specific industrial applications like selective oxidation in chemical synthesis or catalytic combustion. Engineers explore nanomaterials, metal-organic frameworks (MOFs), and other cutting-edge materials to achieve superior performance.
Carbon Utilization Oxidation Engineer
This specialization involves designing and implementing oxidation processes for carbon capture, utilization, and storage (CCUS) technologies. It focuses on developing efficient oxidation methods to convert captured CO2 into valuable chemicals or fuels, or to enhance the capture efficiency itself. This area is critical for mitigating climate change and involves integrating oxidation chemistry with large-scale industrial processes aimed at reducing greenhouse gas emissions.
Pros & Cons of Being an Oxidation Engineer
Understanding both the advantages and challenges of a career path is crucial for making informed decisions. The experience of an Oxidation Engineer can vary significantly based on the specific industry, company culture, and the particular processes involved. What one person perceives as a benefit, another might see as a drawback, depending on their personal values, skills, and career aspirations. For instance, the demand for precision might be a pro for detail-oriented individuals but a con for those who prefer less structured work. These dynamics can also shift as an engineer progresses from an entry-level position to a more senior role, where responsibilities and pressures change. This assessment aims to provide a realistic overview to help set appropriate expectations for this specialized engineering field.
Pros
- Oxidation engineers play a critical role in various industries, including semiconductor manufacturing, chemical processing, and wastewater treatment, ensuring high demand for specialized skills.
- The work involves complex chemical and physical processes, offering significant intellectual stimulation through problem-solving and process optimization.
- There are opportunities to work with cutting-edge technologies and contribute to advancements in material science, environmental sustainability, and industrial efficiency.
- Salaries for specialized engineers, such as oxidation engineers, are generally competitive, reflecting the niche expertise and critical nature of their contributions.
- Oxidation engineers often engage in hands-on work, designing, implementing, and monitoring real-world systems, providing a tangible sense of accomplishment.
- The role frequently involves interdisciplinary collaboration with chemists, materials scientists, and other engineers, fostering a rich learning environment and diverse professional interactions.
- Many oxidation processes are vital for environmental protection, such as treating industrial waste, allowing engineers to contribute directly to sustainable practices and public health.
Cons
- Oxidation engineers often work with hazardous chemicals and high temperatures, requiring strict adherence to safety protocols and constant vigilance to prevent accidents.
- The work can be highly repetitive, involving monitoring and maintaining processes that run continuously, which may lead to monotony for some individuals.
- Troubleshooting complex oxidation processes can be challenging and time-consuming, often requiring extensive analysis and experimentation to identify root causes of issues.
- Career advancement opportunities may be limited to specific roles within the oxidation process, making it difficult to transition to other engineering disciplines without additional training.
- The industry can be sensitive to economic downturns, impacting job security or investment in new oxidation technologies during periods of reduced demand or budget cuts.
- Continuous learning is essential to keep up with advancements in oxidation technologies, materials science, and environmental regulations, requiring ongoing professional development.
- Working environments may be noisy, hot, or involve exposure to fumes, necessitating personal protective equipment and potentially impacting long-term comfort and health for some individuals.
Frequently Asked Questions
Oxidation Engineers face distinct challenges in balancing process efficiency with material integrity and environmental compliance. This section addresses common questions about entering this specialized field, from required technical skills to navigating industry-specific regulations and continuous innovation in semiconductor manufacturing.
What educational background and specific qualifications are essential to become an Oxidation Engineer?
An Oxidation Engineer typically needs a Bachelor's or Master's degree in Materials Science, Chemical Engineering, Electrical Engineering, or a related field. Strong foundational knowledge in semiconductor physics, materials characterization, and thermodynamics is crucial. Some roles might prefer candidates with experience in thin-film deposition or process control in a manufacturing environment.
How long does it typically take to become job-ready as an Oxidation Engineer, and what is the career progression timeline?
Entry-level Oxidation Engineer positions can be secured within 1-2 years after graduation, assuming relevant coursework and potentially an internship. Gaining proficiency and becoming a senior engineer might take 5-7 years, as it involves mastering complex process parameters, troubleshooting, and leading improvement projects. Continuous learning is vital due to rapid technological advancements.
What are the salary expectations for an entry-level and experienced Oxidation Engineer?
Starting salaries for Oxidation Engineers can range from $70,000 to $90,000 annually, depending on location, company size, and specific responsibilities. With 5-10 years of experience, a senior Oxidation Engineer can expect to earn $110,000 to $150,000 or more. Compensation often includes bonuses based on performance and company profitability in the semiconductor industry.
What is the job security and market demand for Oxidation Engineers in the coming years?
The demand for Oxidation Engineers remains strong due to the continuous growth of the semiconductor industry and the critical role oxidation processes play in chip manufacturing. As technology advances, new materials and processes emerge, ensuring ongoing opportunities. The field is relatively stable, as oxidation is a fundamental step that cannot be easily automated out of existence.
What is the typical work-life balance like for an Oxidation Engineer, especially during peak periods?
Work-life balance can vary. During process development or troubleshooting critical issues, hours can be long and demanding, sometimes requiring weekend or on-call availability. However, during stable production phases, the work schedule is typically more predictable, often standard business hours. The intensity is often tied to product cycles and manufacturing ramp-ups.
What are the common career growth opportunities and advancement paths for an Oxidation Engineer?
Career growth paths include moving into senior technical roles, specializing in advanced materials or process integration, or transitioning into management positions like process engineering manager or even operations management. Opportunities also exist in research and development, where you can contribute to next-generation semiconductor technologies. Cross-functional project leadership is also a common advancement.
What are the biggest technical challenges and day-to-day problems an Oxidation Engineer faces?
The primary challenges include maintaining ultra-high purity environments, achieving precise film thickness and uniformity across large wafers, and managing defect reduction. Oxidation Engineers must also contend with rapid technological shifts, requiring constant adaptation to new materials and equipment. Troubleshooting complex process deviations while minimizing production impact is also a significant hurdle.
Is remote work a realistic option for an Oxidation Engineer, or is it primarily an on-site role?
Remote work is generally not feasible for an Oxidation Engineer due to the hands-on nature of the role. The job requires direct presence in a cleanroom environment to monitor, adjust, and troubleshoot equipment and processes. While some administrative or data analysis tasks might be done remotely, the core responsibilities demand on-site presence at a fabrication plant.
Related Careers
Explore similar roles that might align with your interests and skills:
Chemical Engineer
A growing field with similar skill requirements and career progression opportunities.
Explore career guideChemical Process Engineer
A growing field with similar skill requirements and career progression opportunities.
Explore career guideProcess Engineer
A growing field with similar skill requirements and career progression opportunities.
Explore career guideCombustion Engineer
A growing field with similar skill requirements and career progression opportunities.
Explore career guideIndustrial Chemist
A growing field with similar skill requirements and career progression opportunities.
Explore career guideAssess your Oxidation Engineer readiness
Understanding where you stand today is the first step toward your career goals. Our Career Coach helps identify skill gaps and create personalized plans.
Skills Gap Analysis
Get a detailed assessment of your current skills versus Oxidation Engineer requirements. Our AI Career Coach identifies specific areas for improvement with personalized recommendations.
See your skills gapCareer Readiness Assessment
Evaluate your overall readiness for Oxidation Engineer roles with our AI Career Coach. Receive personalized recommendations for education, projects, and experience to boost your competitiveness.
Assess your readinessSimple pricing, powerful features
Upgrade to Himalayas Plus and turbocharge your job search.
Himalayas
Himalayas Plus
Himalayas Max
Find your dream job
Sign up now and join over 100,000 remote workers who receive personalized job alerts, curated job matches, and more for free!
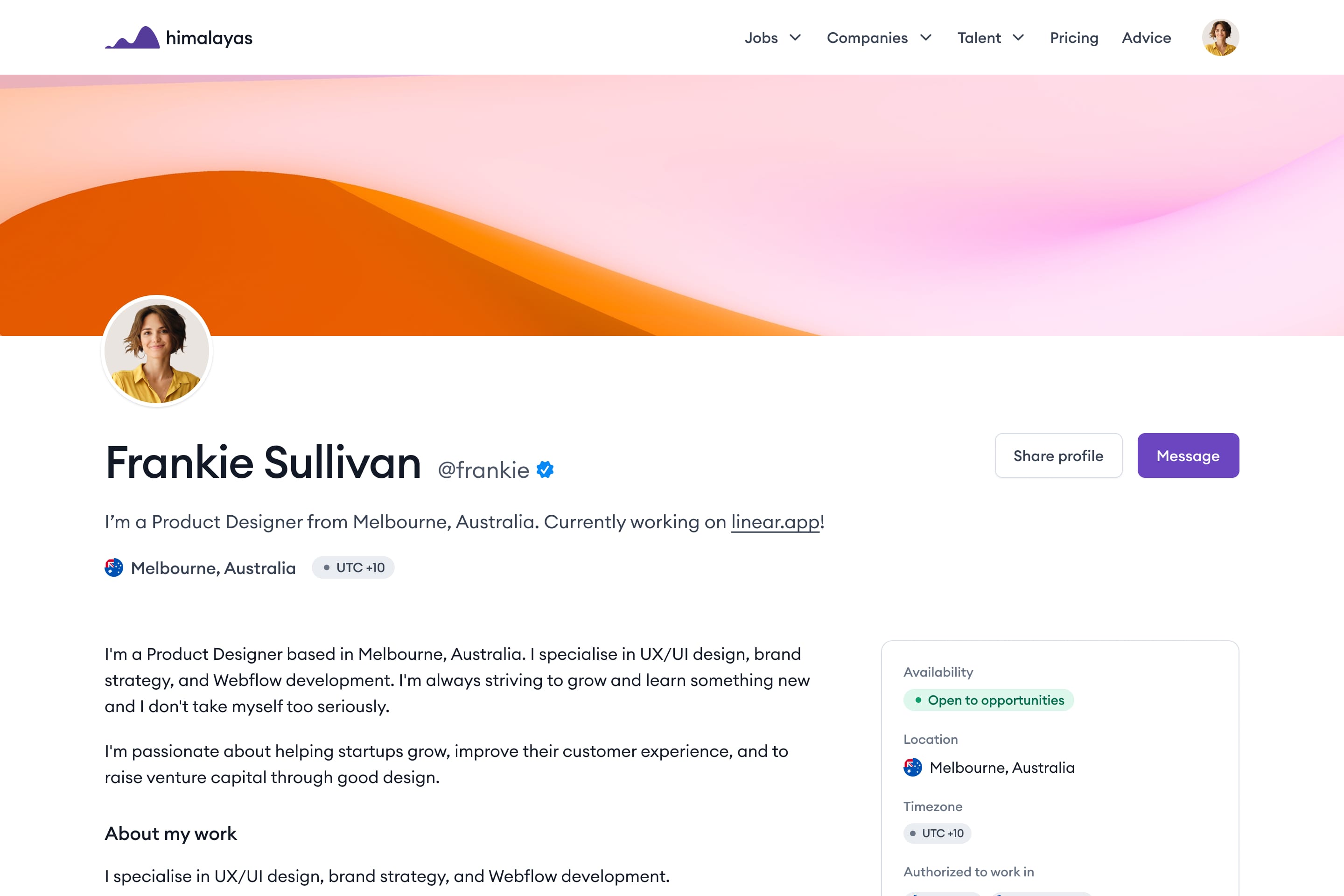