4 Wire Winder Interview Questions and Answers
Wire Winders are skilled workers responsible for winding wire coils used in electrical equipment such as transformers, motors, and generators. They operate specialized machinery, ensure precision in winding, and inspect for quality and consistency. Junior roles focus on learning the machinery and basic tasks, while senior and lead roles involve overseeing operations, troubleshooting issues, and mentoring less experienced workers. Need to practice for an interview? Try our AI interview practice for free then unlock unlimited access for just $9/month.
Unlimited interview practice for $9 / month
Improve your confidence with an AI mock interviewer.
No credit card required
1. Wire Winder Interview Questions and Answers
1.1. Can you describe your experience with winding wire for various applications?
Introduction
This question assesses your technical knowledge and hands-on experience with wire winding, which is crucial for ensuring the quality and efficiency of the winding process.
How to answer
- Start by detailing the types of wire and applications you've worked with
- Explain the techniques and tools you used during the winding process
- Mention any specific challenges you faced and how you overcame them
- Discuss the importance of precision and quality in wire winding
- Share any relevant metrics or outcomes that demonstrate your success
What not to say
- Focusing only on theoretical knowledge without practical experience
- Neglecting to mention safety protocols and quality checks
- Providing vague responses without specific examples
- Underestimating the importance of teamwork in a winding operation
Example answer
“In my previous role at a manufacturing plant, I wound wire for transformers and motors, ensuring precision in the winding process. I used a specialized winding machine, which improved efficiency by 30%. One challenge was maintaining consistent tension; I implemented a monitoring system that reduced defects by 15%. This experience taught me the importance of quality control and teamwork in achieving production goals.”
Skills tested
Question type
1.2. How do you ensure the safety and quality of your work during the wire winding process?
Introduction
Safety and quality are paramount in manufacturing roles, especially in wire winding where improper handling can lead to defects or accidents. This question evaluates your awareness and practices regarding these crucial aspects.
How to answer
- Discuss specific safety protocols you follow in the workplace
- Explain how you conduct quality checks throughout the winding process
- Share how you keep your workspace organized and free of hazards
- Mention any training or certifications you have related to safety
- Provide examples of how you contributed to a culture of safety in your previous roles
What not to say
- Ignoring safety protocols or claiming they are not important
- Failing to provide specific examples of quality control measures
- Suggesting that safety is solely the responsibility of supervisors
- Neglecting to discuss personal accountability in maintaining safety standards
Example answer
“I prioritize safety by following strict protocols, such as wearing protective gear and ensuring my workspace is free from clutter. I conduct regular quality checks, including visual inspections and measurements, to ensure the winding meets specifications. Additionally, I completed a safety training course that emphasized hazard recognition and risk assessment. In my last position, I initiated a weekly safety brief that helped reduce incidents by 20%.”
Skills tested
Question type
2. Senior Wire Winder Interview Questions and Answers
2.1. Can you describe your experience with different types of winding machines and how you've optimized their performance?
Introduction
This question is crucial for a Senior Wire Winder as it assesses both your technical expertise in operating winding machines and your ability to enhance their efficiency, which directly impacts production quality and costs.
How to answer
- Start by mentioning specific winding machines you have worked with (e.g., CNC winders, automatic winders).
- Discuss any optimization techniques you implemented, such as adjusting tension settings or modifying winding patterns.
- Quantify improvements in performance or production output where possible.
- Explain how you stay updated on new technologies or methods in wire winding.
- Mention any training or mentoring you have provided to junior winders.
What not to say
- Vague references to 'just following instructions' without detailing your input.
- Not providing specific examples of optimization or improvement.
- Ignoring the importance of safety or quality standards in your practices.
- Failing to mention teamwork or collaboration with other departments.
Example answer
“At Babcock International, I worked extensively with CNC winding machines, where I optimized the winding process by adjusting the tension settings and implementing a new winding pattern that increased our output by 20%. I also trained junior staff on these techniques, ensuring quality and safety standards were always met.”
Skills tested
Question type
2.2. Describe a challenging situation you faced in your previous role and how you resolved it.
Introduction
This behavioral question evaluates your problem-solving abilities and resilience in overcoming obstacles, which are important traits for a Senior Wire Winder.
How to answer
- Use the STAR method (Situation, Task, Action, Result) to structure your answer.
- Clearly describe the context and the specific challenge you encountered.
- Detail the steps you took to address the issue, including any collaboration with others.
- Discuss the outcome and what you learned from the experience.
- Highlight any changes you made to processes or practices as a result.
What not to say
- Blaming others for the situation without taking responsibility.
- Providing an overly simplistic solution that lacks depth.
- Failing to mention the outcome or results of your actions.
- Describing a situation that doesn't relate to winding or production.
Example answer
“In my previous role at Rolls-Royce, we faced a significant delay in wire production due to a malfunctioning winding machine. I quickly diagnosed the issue as a software glitch and worked with the engineering team to implement a fix. As a result, we reduced downtime by 30% and implemented a preventive maintenance schedule to avoid future issues. This experience taught me the importance of swift action and teamwork.”
Skills tested
Question type
3. Lead Wire Winder Interview Questions and Answers
3.1. Describe a time when you identified a significant issue in the wire winding process and how you resolved it.
Introduction
This question is crucial for evaluating your problem-solving abilities and technical knowledge in wire winding, which are essential for a lead position.
How to answer
- Use the STAR method to structure your answer: Situation, Task, Action, Result.
- Clearly describe the issue you encountered and its impact on production efficiency or product quality.
- Explain the steps you took to analyze the problem and identify the root cause.
- Detail the solution you implemented and how you ensured it was effective.
- Quantify the results of your solution, such as improvements in efficiency, reduction in waste, or enhancement in product quality.
What not to say
- Blaming others for the issue without taking responsibility.
- Providing vague answers without specific examples or measurable outcomes.
- Focusing only on the problem rather than the solution.
- Neglecting to mention teamwork or collaboration if applicable.
Example answer
“At a previous job with Siemens, I noticed a recurring problem where wire breakage was leading to production delays. I conducted a thorough analysis and discovered that the winding tension was set too high. I collaborated with my team to adjust the settings and implemented a regular monitoring system. This change resulted in a 30% reduction in wire breakage and improved our production efficiency by 25%.”
Skills tested
Question type
3.2. How do you ensure that your team adheres to safety and quality standards during the wire winding process?
Introduction
This question evaluates your leadership and commitment to maintaining safety and quality, which are critical in manufacturing roles.
How to answer
- Discuss your approach to training and educating your team on safety and quality standards.
- Explain how you monitor compliance and provide feedback.
- Share specific examples of how you've addressed non-compliance or safety concerns.
- Describe how you foster a culture of safety and quality within your team.
- Discuss any metrics or KPIs you use to measure adherence to these standards.
What not to say
- Implying that safety and quality are not priorities.
- Failing to provide specific examples or experiences.
- Overlooking the importance of team engagement in safety practices.
- Neglecting to mention training or monitoring processes.
Example answer
“In my role at ABB, I implemented a comprehensive safety training program for my team. We hold weekly meetings to discuss safety protocols and review any incidents. I also introduced a quality checklist that must be completed before any winding operation starts. As a result, we achieved a 40% reduction in safety incidents and maintained a 99% quality compliance rate over the last year.”
Skills tested
Question type
4. Wire Winding Supervisor Interview Questions and Answers
4.1. Can you describe a time when you improved the efficiency of the wire winding process?
Introduction
This question assesses your ability to identify inefficiencies and implement improvements, which is crucial for a supervisory role in wire winding.
How to answer
- Use the STAR method to structure your response
- Clearly outline the inefficiency you identified and its impact on production
- Detail the steps you took to analyze the process and propose solutions
- Explain how you implemented the changes and trained your team
- Quantify the results of your improvements, such as reduced waste or increased output
What not to say
- Describing a situation where you made changes without consulting your team
- Focusing only on the problem without detailing the solution
- Neglecting to mention any measurable outcomes from your actions
- Being vague about the steps taken to implement improvements
Example answer
“At ABC Manufacturing, I noticed that our wire winding process was causing a 15% increase in material waste. I conducted a thorough analysis and discovered that we could optimize our winding speed and tension settings. After proposing my findings to management, I led a training session for the team to implement these changes. As a result, we reduced waste by 30% and improved our production output by 20% within three months.”
Skills tested
Question type
4.2. How do you ensure safety compliance in your wire winding operations?
Introduction
Safety is paramount in manufacturing environments, and this question evaluates your commitment to maintaining a safe workplace while supervising wire winding processes.
How to answer
- Discuss your knowledge of safety regulations relevant to wire winding
- Describe specific safety protocols and practices you enforce
- Explain how you train and communicate safety standards to your team
- Provide an example of how you handled a safety incident or concern
- Highlight the importance of a safety-first culture in your team
What not to say
- Suggesting that safety protocols are optional or secondary
- Ignoring the importance of team training on safety standards
- Failing to provide examples of safety compliance measures
- Overlooking the role of continuous monitoring and improvement
Example answer
“In my role at XYZ Industries, I prioritize safety by ensuring all team members are trained on safety protocols, including PPE usage and machine operation guidelines. I conduct weekly safety briefings and encourage open discussions about safety concerns. Last year, when we had a near-miss incident, I led a review of our processes and implemented additional training, which resulted in zero accidents for over six months. Safety is a shared responsibility I promote within the team.”
Skills tested
Question type
Similar Interview Questions and Sample Answers
Simple pricing, powerful features
Upgrade to Himalayas Plus and turbocharge your job search.
Himalayas
Himalayas Plus
Himalayas Max
Find your dream job
Sign up now and join over 100,000 remote workers who receive personalized job alerts, curated job matches, and more for free!
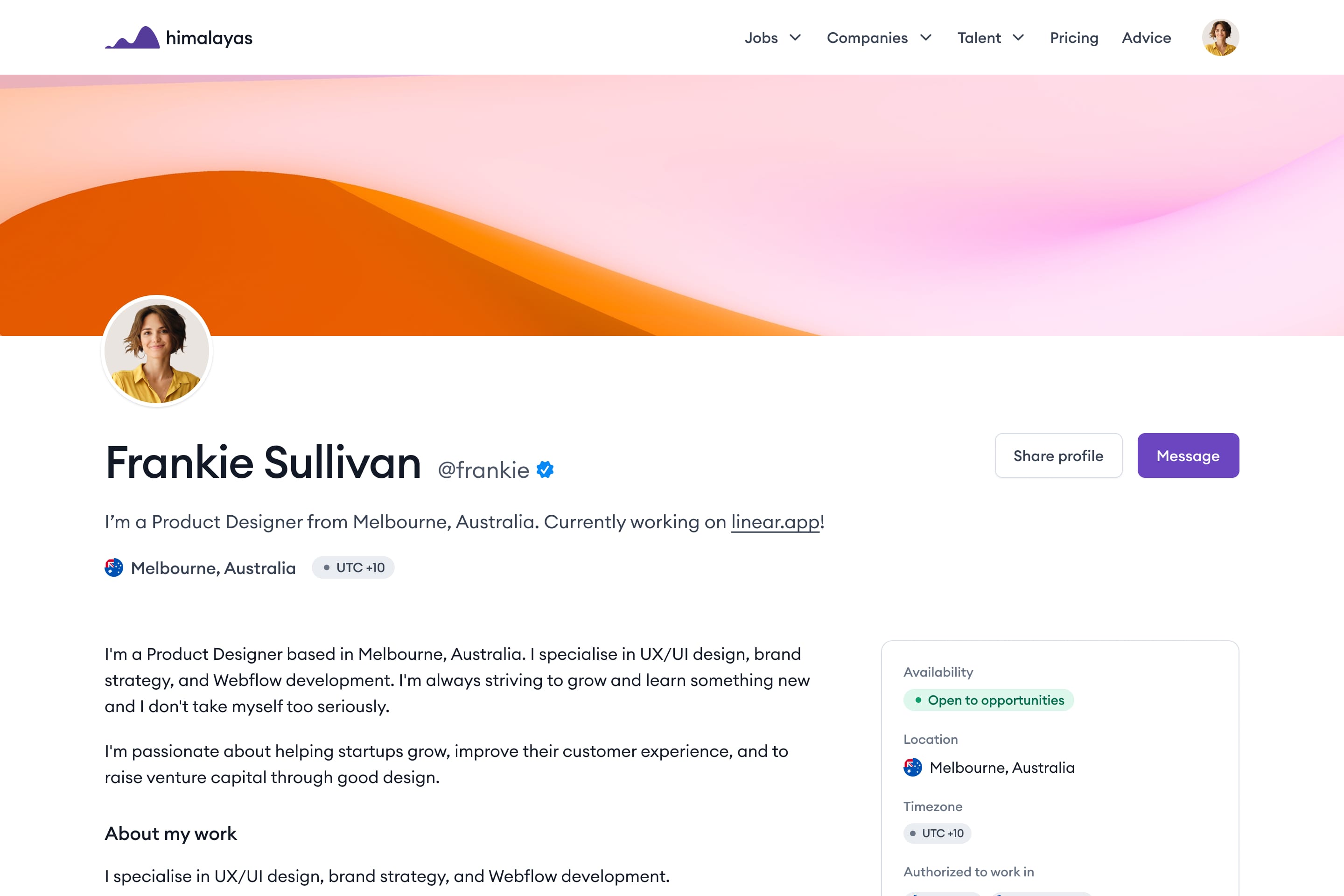