4 Wire Coiler Interview Questions and Answers
Wire Coilers are responsible for operating machinery to wind wire or cable into coils for storage or transport. They ensure proper tension, alignment, and quality of the coiled wire. Junior roles focus on basic machine operation and quality checks, while senior and lead roles involve overseeing operations, troubleshooting equipment, and training team members. Need to practice for an interview? Try our AI interview practice for free then unlock unlimited access for just $9/month.
Unlimited interview practice for $9 / month
Improve your confidence with an AI mock interviewer.
No credit card required
1. Wire Coiler Interview Questions and Answers
1.1. Can you describe your experience with operating a wire coiling machine and the safety protocols you follow?
Introduction
This question is critical as it assesses your technical proficiency and understanding of safety measures, which are paramount in manufacturing roles.
How to answer
- Start by outlining your hands-on experience with different types of wire coiling machines.
- Discuss specific safety protocols you adhere to while operating the machinery.
- Explain how you ensure the quality of the coiled wire during production.
- Mention any relevant training or certifications you have completed.
- Share a specific instance where you identified a safety issue and how you addressed it.
What not to say
- Neglecting to mention any safety protocols or training.
- Focusing only on technical skills without mentioning safety.
- Providing vague answers without specific examples.
- Underestimating the importance of safety in machine operation.
Example answer
“In my previous role at General Cable, I operated various wire coiling machines for over three years. I always follow strict safety protocols, such as wearing protective gear and conducting pre-operation checks. For example, I once identified a potential hazard when I noticed a frayed cable and immediately shut down the machine to address the issue, preventing any accidents. My training in OSHA standards has also reinforced my commitment to safety.”
Skills tested
Question type
1.2. Describe a challenging situation you faced while coiling wire and how you resolved it.
Introduction
This question evaluates your problem-solving skills and ability to work under pressure, which are important in a manufacturing environment.
How to answer
- Use the STAR method to structure your answer: Situation, Task, Action, Result.
- Clearly explain the challenge you faced, including any technical or team-related issues.
- Detail the steps you took to resolve the issue, emphasizing teamwork or individual initiative.
- Highlight the positive outcome and any lessons learned from the experience.
- Mention how you would apply this experience to future challenges.
What not to say
- Blaming others for the problem without taking responsibility.
- Describing a situation without a clear resolution.
- Focusing solely on the problem rather than your actions.
- Lacking a follow-up on the outcome of the situation.
Example answer
“At my previous job with Southwire, we experienced a sudden machine malfunction during a critical production run. I quickly assessed the situation and coordinated with the maintenance team to troubleshoot the issue. By implementing a temporary manual coiling technique while repairs were underway, we managed to meet our deadline. This taught me the importance of flexibility and teamwork in overcoming production challenges.”
Skills tested
Question type
2. Senior Wire Coiler Interview Questions and Answers
2.1. Can you describe a time when you had to troubleshoot a major issue with the wire coiling process?
Introduction
This question assesses your problem-solving skills and technical expertise in handling machinery and processes, which are critical for a Senior Wire Coiler.
How to answer
- Start by briefly explaining the context of the issue you faced
- Detail the specific symptoms of the problem you observed
- Explain the steps you took to diagnose and troubleshoot the issue
- Discuss the solution you implemented and its effectiveness
- Highlight any preventive measures you established to avoid future issues
What not to say
- Avoid vague descriptions without specific details
- Don't focus solely on technical jargon without explaining the impact
- Refrain from blaming others for the issue instead of taking responsibility
- Do not skip over the lessons learned from the experience
Example answer
“At my previous role with a manufacturing company, we encountered a significant slowdown in wire coiling speed. I conducted a thorough inspection and found that the coil tension was set incorrectly. After recalibrating the tension and cleaning the machinery, we restored optimal speed, increasing production efficiency by 20%. I also implemented a new maintenance schedule to ensure we would catch similar issues early in the future.”
Skills tested
Question type
2.2. How do you ensure quality control during the wire coiling process?
Introduction
This question evaluates your understanding and implementation of quality control measures, which are crucial in maintaining product standards.
How to answer
- Describe the quality control measures you have implemented
- Share the specific standards or metrics you monitor during production
- Discuss how you train and guide your team in quality assurance
- Explain the reporting and feedback loop to improve processes
- Mention any tools or technologies you utilize for quality control
What not to say
- Suggesting that quality control is not necessary or can be overlooked
- Failing to provide specific examples of measures you've taken
- Ignoring how team collaboration contributes to quality
- Overemphasizing your role without recognizing the team's efforts
Example answer
“In my previous position at a wire manufacturing facility, I implemented a systematic quality control checklist that included measuring coil diameter and inspecting for defects every 100 meters. I trained my team to follow these guidelines rigorously, and we used software to track and report any deviations. This proactive approach led to a 15% reduction in rework rates and improved customer satisfaction significantly.”
Skills tested
Question type
3. Lead Wire Coiler Interview Questions and Answers
3.1. Can you describe a time when you identified a problem in the wire coiling process and how you resolved it?
Introduction
This question assesses your problem-solving skills and your ability to improve manufacturing processes, which are crucial for a Lead Wire Coiler.
How to answer
- Use the STAR method to structure your response: Situation, Task, Action, Result.
- Clearly describe the specific problem you encountered in the wire coiling process.
- Explain your analysis of the problem and how you determined the root cause.
- Detail the actions you took to resolve the issue, including any collaboration with team members.
- Quantify the results of your actions, such as improvements in efficiency or reduction in defects.
What not to say
- Blaming others for the problem without taking responsibility.
- Providing vague descriptions without specific details.
- Failing to mention the impact of your solution.
- Overlooking the importance of teamwork or collaboration.
Example answer
“At my previous job at Southwire, we noticed an increase in wire defects due to inconsistent coil tension. I led an investigation that revealed the tension calibrations were off due to wear on the machinery. I coordinated with maintenance to recalibrate the machines and trained the team on the importance of monitoring tension during production. As a result, we reduced defects by 30% and improved overall production efficiency.”
Skills tested
Question type
3.2. How do you ensure quality control during the wire coiling process?
Introduction
This question evaluates your understanding of quality assurance in manufacturing and your ability to implement effective control measures.
How to answer
- Discuss the specific quality standards applicable to wire coiling.
- Explain your approach to monitoring and measuring quality during the production process.
- Detail any tools or techniques you implement for quality control, such as inspections or testing methods.
- Share an example of how you handled a quality issue and the steps taken to rectify it.
- Mention the importance of training and updating team members on quality standards.
What not to say
- Suggesting that quality control is not a priority.
- Failing to provide specific examples or methods.
- Ignoring the role of teamwork in maintaining quality.
- Neglecting to mention the importance of continuous improvement.
Example answer
“In my role at General Cable, I implemented a quality control checklist that included regular inspections and tests of the wire samples. I trained my team on the checklist and emphasized the importance of quality in every coil produced. One time, we caught a batch with insulation issues early due to our inspection process, allowing us to address it before it escalated. This proactive approach reduced our return rate by 15%.”
Skills tested
Question type
4. Wire Coiling Supervisor Interview Questions and Answers
4.1. Can you describe a time when you had to improve the efficiency of the wire coiling process?
Introduction
This question assesses your problem-solving skills and ability to enhance operational efficiency, which are crucial for a supervisory role in wire coiling.
How to answer
- Use the STAR method (Situation, Task, Action, Result) to structure your response.
- Clearly describe the initial inefficiencies and their impact on production.
- Detail the specific actions you took to address these inefficiencies, such as implementing new procedures or technology.
- Quantify the results of your efforts, such as increased output or reduced waste.
- Discuss any feedback received from team members or management after the changes were implemented.
What not to say
- Focusing only on the problems without discussing solutions.
- Giving vague answers without measurable outcomes.
- Failing to mention collaboration with team members.
- Not acknowledging any challenges faced during the process.
Example answer
“At my previous job at BHP, we were experiencing a bottleneck in our wire coiling process that reduced productivity by 20%. After analyzing the workflow, I introduced a new scheduling system that prioritized high-demand products. I also trained the team on best practices for machine maintenance. As a result, we increased our production rate by 30% over six months, significantly improving our delivery times and client satisfaction.”
Skills tested
Question type
4.2. How do you ensure safety and compliance in the wire coiling operation?
Introduction
This question evaluates your knowledge of safety regulations and your ability to enforce compliance in a manufacturing environment.
How to answer
- Discuss your understanding of relevant safety regulations and industry standards.
- Explain how you implement safety protocols within your team.
- Provide examples of training sessions or safety drills you have conducted.
- Mention any specific incidents where you successfully improved safety compliance.
- Describe how you encourage a culture of safety among team members.
What not to say
- Ignoring the importance of safety protocols.
- Providing generic answers without specific examples.
- Failing to mention collaboration with safety officers or management.
- Not addressing the consequences of non-compliance.
Example answer
“In my role at Australia Wire Industries, I prioritized safety by conducting monthly training sessions on machine operation and emergency procedures. I also implemented a peer review system, where team members would perform safety checks on each other's workstations. After introducing these measures, we saw a 50% reduction in workplace incidents over the course of a year, which not only improved morale but also ensured compliance with industry regulations.”
Skills tested
Question type
4.3. How would you handle a conflict between team members on the wire coiling floor?
Introduction
This question assesses your conflict resolution skills and ability to maintain a positive work environment, which is vital for a supervisory role.
How to answer
- Describe your approach to understanding the root cause of the conflict.
- Explain how you would facilitate a conversation between the involved parties.
- Discuss the importance of empathy and active listening during conflict resolution.
- Detail how you would ensure that the resolution is fair and maintains team cohesion.
- Mention any follow-up actions you would take to prevent future conflicts.
What not to say
- Avoiding the conflict or hoping it resolves itself.
- Taking sides without hearing both perspectives.
- Not having a clear process for conflict resolution.
- Failing to follow up on the resolution.
Example answer
“When I encountered a conflict between two team members at my previous company, I first met with each of them separately to understand their perspectives. I then facilitated a joint meeting, encouraging open and respectful dialogue. By focusing on the issues rather than personal grievances, we were able to reach a compromise that worked for both parties. Afterward, I checked in with them weekly to ensure the conflict didn’t resurface. This approach not only resolved the issue but also strengthened team dynamics.”
Skills tested
Question type
Similar Interview Questions and Sample Answers
Simple pricing, powerful features
Upgrade to Himalayas Plus and turbocharge your job search.
Himalayas
Himalayas Plus
Himalayas Max
Find your dream job
Sign up now and join over 100,000 remote workers who receive personalized job alerts, curated job matches, and more for free!
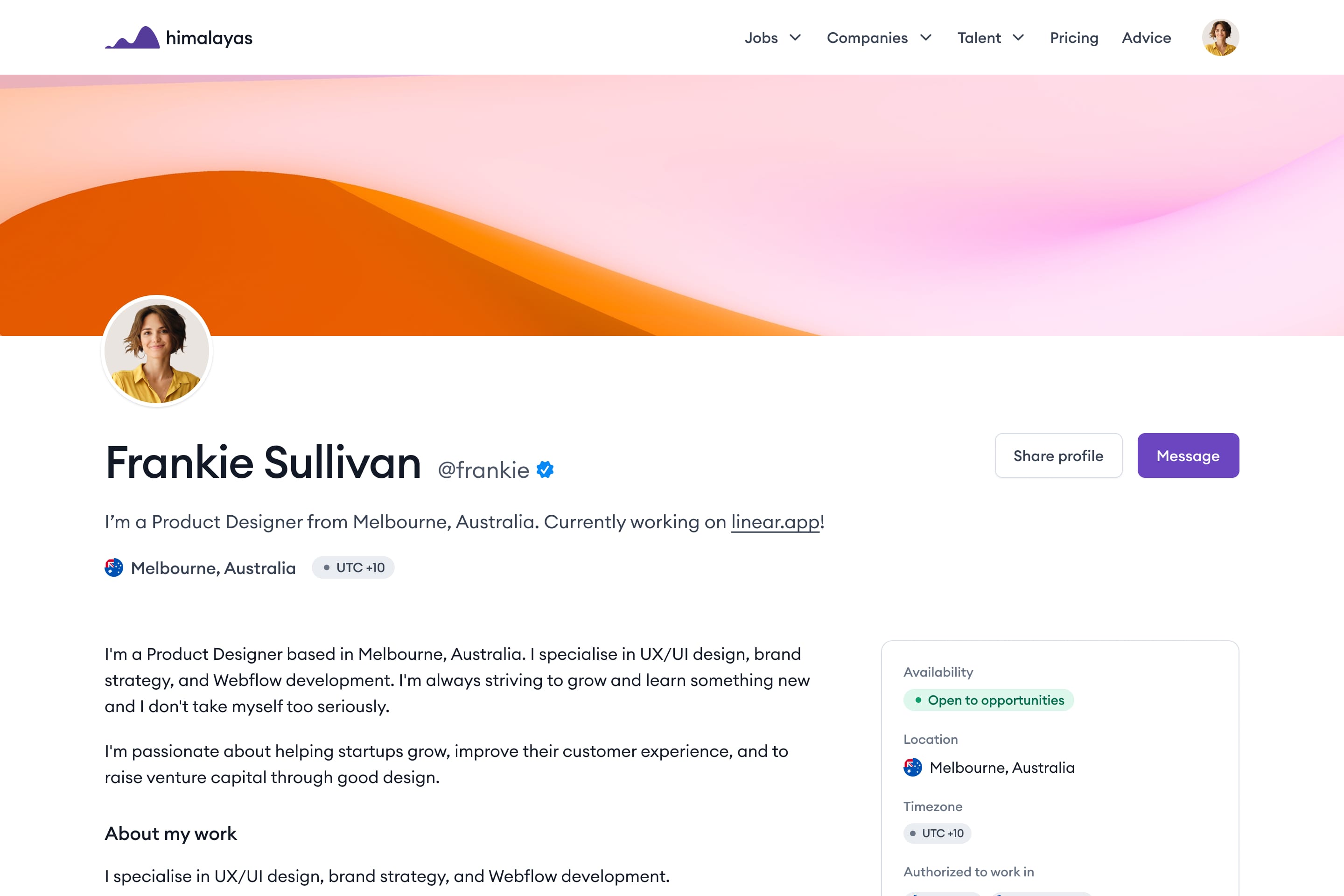