5 Shift Engineer Interview Questions and Answers
Shift Engineers are responsible for maintaining and ensuring the smooth operation of machinery, equipment, and systems during their assigned shifts. They troubleshoot technical issues, perform routine maintenance, and ensure compliance with safety and operational standards. Junior roles focus on learning and assisting with basic tasks, while senior and lead engineers oversee operations, mentor team members, and manage shift-specific challenges. Need to practice for an interview? Try our AI interview practice for free then unlock unlimited access for just $9/month.
Unlimited interview practice for $9 / month
Improve your confidence with an AI mock interviewer.
No credit card required
1. Junior Shift Engineer Interview Questions and Answers
1.1. Can you describe a time when you faced a technical problem during your shift? How did you handle it?
Introduction
This question assesses your problem-solving skills and ability to work under pressure, which are essential for a Junior Shift Engineer.
How to answer
- Use the STAR method to structure your response: Situation, Task, Action, Result.
- Clearly describe the technical problem you encountered and the context around it.
- Explain the steps you took to diagnose and solve the issue.
- Highlight any collaboration with coworkers or supervisors.
- Discuss the outcome and any lessons learned from the experience.
What not to say
- Failing to take responsibility for your role in the situation.
- Providing vague details that do not showcase your involvement.
- Blaming others without acknowledging your own contributions.
- Not discussing how you have improved or what you learned.
Example answer
“During my shift at a manufacturing plant, I noticed a conveyor belt malfunctioning, which was causing delays. I quickly stopped the line and consulted the equipment manual to identify the issue. I discovered a jam caused by a foreign object. After removing it, I tested the system to ensure it was working properly. This not only minimized downtime but also taught me the importance of quick thinking and attention to detail in preventing further issues.”
Skills tested
Question type
1.2. How do you prioritize your tasks during a busy shift to ensure everything runs smoothly?
Introduction
This question evaluates your time management and organizational skills, which are critical for maintaining operational efficiency.
How to answer
- Discuss your approach to assessing task urgency and importance.
- Explain how you might use checklists or digital tools to keep track of tasks.
- Describe how you communicate priorities with your team.
- Share an example of a busy shift and how you managed your tasks effectively.
- Mention any techniques you use to remain flexible in case priorities change.
What not to say
- Claiming you work best without any plan or structure.
- Suggesting you rely solely on others to prioritize tasks.
- Overlooking the importance of teamwork in task management.
- Failing to provide a specific example to illustrate your point.
Example answer
“On a particularly busy shift at a beverage production facility, I faced multiple equipment checks and maintenance tasks. I prioritized based on safety and production impact, using a checklist to track progress. I communicated with my supervisor to ensure we were aligned on urgent tasks, which allowed us to maintain productivity and avoid any safety issues. This experience reinforced the need for organization and clear communication in high-pressure environments.”
Skills tested
Question type
2. Shift Engineer Interview Questions and Answers
2.1. Can you describe a situation where you had to troubleshoot a complex equipment failure during your shift?
Introduction
This question is critical for assessing your technical troubleshooting skills and your ability to remain calm under pressure, which are essential traits for a Shift Engineer.
How to answer
- Use the STAR method to structure your answer (Situation, Task, Action, Result)
- Clearly describe the context of the equipment failure and its possible implications
- Detail the steps you took to diagnose the issue, involving any tools or methods used
- Explain how you collaborated with team members or other departments to resolve the issue
- Quantify the outcome, such as reduced downtime or improved performance
What not to say
- Failing to take responsibility for the issue or blaming others
- Providing vague answers without specific details or metrics
- Overlooking safety protocols during troubleshooting
- Not mentioning any follow-up actions taken to prevent future failures
Example answer
“During my shift at Toyota, we experienced a critical failure in a robotic arm used in assembly. The arm halted production, risking significant delays. I immediately analyzed the error codes and discovered a faulty sensor. I coordinated with the maintenance team to replace it and recalibrated the system. As a result, we resumed operations within two hours, minimizing downtime to just 30 minutes. This experience reinforced my belief in proactive maintenance checks.”
Skills tested
Question type
2.2. How do you prioritize tasks when managing multiple equipment issues during a shift?
Introduction
This question evaluates your organizational and time management skills, which are vital when handling multiple responsibilities and ensuring smooth operations.
How to answer
- Describe your method for assessing the urgency and impact of each issue
- Explain your approach to task delegation if applicable
- Discuss how you communicate priorities with your team
- Share an example of a time you successfully handled multiple tasks
- Mention any tools or systems you use to track and manage tasks
What not to say
- Claiming you handle everything on your own without team input
- Suggesting that you ignore smaller issues in favor of larger ones
- Failing to highlight communication with team members
- Providing an example that lacks a successful outcome
Example answer
“In my role at Hitachi, I often faced multiple equipment issues simultaneously. I prioritize tasks by assessing their impact on production and safety. For instance, if a minor issue could escalate into a major problem, I address it first. I communicate with my team to ensure everyone is on the same page, and we use a shared digital task board to keep track of our progress. This approach helped us reduce response time by 20% during peak hours.”
Skills tested
Question type
3. Senior Shift Engineer Interview Questions and Answers
3.1. Can you describe a complex engineering problem you encountered during a shift and how you resolved it?
Introduction
This question assesses your problem-solving abilities and technical expertise, which are critical for a Senior Shift Engineer who often faces unexpected challenges during operations.
How to answer
- Use the STAR method: Situation, Task, Action, Result.
- Clearly outline the problem, including technical specifications and operational impact.
- Discuss your thought process in diagnosing the issue.
- Detail the specific steps you took to resolve the problem, including collaboration with team members.
- Quantify the results and improvements achieved after your solution was implemented.
What not to say
- Avoid vague descriptions that don’t highlight your specific contributions.
- Don’t focus solely on the technical aspects without mentioning teamwork.
- Refrain from blaming others for the problem without taking responsibility.
- Avoid downplaying the importance of the challenge or the impact of your solution.
Example answer
“During my shift at Sasol, we experienced a sudden drop in pressure in a critical distillation column. I quickly assessed the situation and coordinated with the control room to gather data. After identifying a blocked valve as the issue, I organized a team to safely isolate and clear it. This action restored normal pressure within hours, preventing a potential shutdown, and improved our operational efficiency by 15%.”
Skills tested
Question type
3.2. How do you ensure safety compliance during your shifts, especially under high-pressure situations?
Introduction
Safety is a top priority in engineering roles. This question evaluates your commitment to safety standards and your ability to enforce them under pressure.
How to answer
- Describe your approach to safety protocols and training.
- Share specific examples of how you've maintained safety standards during your shifts.
- Explain how you handle situations where safety may be compromised.
- Discuss your methods for promoting a safety culture among team members.
- Highlight any safety improvements or initiatives you've implemented.
What not to say
- Avoid suggesting that safety is secondary to productivity.
- Don’t ignore the importance of training and compliance.
- Refrain from providing generic answers; focus on specific examples.
- Avoid dismissing past safety incidents instead of learning from them.
Example answer
“At my previous role in a petrochemical plant, I implemented a daily safety briefing that included real-time updates on potential hazards. During a high-pressure situation where equipment failure was imminent, I prioritized the safety of my team by halting operations and conducting a thorough risk assessment. This proactive approach not only ensured compliance but also fostered a culture of safety, leading to a 20% reduction in incidents over six months.”
Skills tested
Question type
4. Lead Shift Engineer Interview Questions and Answers
4.1. Can you describe a time when you encountered a significant operational issue during your shift? How did you handle it?
Introduction
This question assesses your problem-solving abilities and how you manage operational challenges, which are crucial for a Lead Shift Engineer responsible for ensuring smooth operations.
How to answer
- Use the STAR method (Situation, Task, Action, Result) to structure your response
- Clearly describe the operational issue and its potential impact
- Explain the steps you took to address the issue, including team involvement
- Discuss any immediate and long-term solutions you implemented
- Share measurable outcomes or improvements resulting from your actions
What not to say
- Avoid blaming others without taking any responsibility
- Neglecting to mention specific actions you took
- Focusing solely on the problem without discussing solutions
- Failing to reflect on the lessons learned from the experience
Example answer
“During my shift at Renault, we faced a sudden shutdown of a critical assembly line due to a machinery malfunction. I quickly gathered my team to assess the situation and prioritized immediate troubleshooting. We identified a faulty sensor and collaborated with maintenance to replace it. As a result, we minimized downtime to just 45 minutes, allowing us to meet our production targets for the day. This experience taught me the importance of teamwork and swift decision-making under pressure.”
Skills tested
Question type
4.2. How do you ensure safety and compliance standards are met during your shifts?
Introduction
This question evaluates your knowledge and commitment to safety regulations, which are critical in engineering roles, especially in manufacturing environments.
How to answer
- Describe your understanding of safety regulations relevant to your industry
- Explain your approach to training team members on safety protocols
- Detail any safety audits or checks you implement regularly
- Discuss how you handle safety violations or emergencies
- Share examples of how you've improved safety standards in previous roles
What not to say
- Indicating that safety is not a priority during shifts
- Providing vague answers without specific safety measures
- Ignoring the importance of team training on safety
- Failing to mention any personal commitment to safety
Example answer
“At Airbus, I prioritize safety by implementing daily safety briefings at the beginning of each shift, emphasizing the importance of compliance with both internal and external regulations. I conduct regular safety audits and ensure all team members are trained on emergency procedures. After identifying a trend in safety violations, I led an initiative to enhance our training program, resulting in a 30% decrease in incidents over six months. Safety is always at the forefront of our operations.”
Skills tested
Question type
4.3. How do you manage team dynamics during a high-pressure situation?
Introduction
This question assesses your leadership style and ability to maintain team cohesion and productivity under pressure, which is vital for a Lead Shift Engineer.
How to answer
- Describe your leadership philosophy during stressful times
- Explain how you communicate with your team to keep morale high
- Share techniques you use to delegate tasks effectively
- Discuss how you encourage collaboration and support among team members
- Provide examples of successful outcomes from managing high-pressure situations
What not to say
- Claiming you work best alone without team input
- Ignoring the emotional state of the team during pressure
- Failing to mention specific strategies for delegation
- Not recognizing the importance of clear communication
Example answer
“In my role at TotalEnergies, during a high-pressure project deadline, I focused on transparent communication and regular check-ins with my team. I encouraged open dialogue about challenges and delegated tasks based on individual strengths. By fostering a supportive environment, we not only met our deadline but also boosted team morale, with a satisfaction survey indicating a 40% increase in team cohesion. My approach ensures that everyone feels valued and engaged, even in challenging times.”
Skills tested
Question type
5. Shift Engineering Supervisor Interview Questions and Answers
5.1. Can you describe a situation where you had to manage a team during a crisis on the production floor?
Introduction
This question assesses your crisis management skills and ability to lead a team under pressure, which is crucial for a Shift Engineering Supervisor.
How to answer
- Outline the context of the crisis clearly, including the technical issues involved
- Explain your immediate response and how you prioritized tasks
- Discuss how you communicated with your team and ensured everyone's safety
- Detail the steps you took to resolve the issue and any follow-up actions
- Highlight the outcomes and any lessons learned from the experience
What not to say
- Avoid blaming others without taking responsibility
- Do not focus on the technical issues without explaining your leadership approach
- Steer clear of vague descriptions that lack specific actions or results
- Avoid discussing only the negative aspects without highlighting positive outcomes or improvements
Example answer
“During my time at Tata Steel, we faced a significant equipment failure that halted production. I quickly gathered my team, assessed the situation, and delegated tasks, ensuring that we prioritized safety first. I kept everyone informed throughout the process, coordinating with maintenance to expedite repairs. Within two hours, we resolved the issue, minimizing downtime to just one shift. This experience reinforced the importance of effective communication and teamwork in crisis situations.”
Skills tested
Question type
5.2. How do you ensure compliance with safety regulations and maintain a safe working environment for your team?
Introduction
This question evaluates your understanding of safety protocols and your capability to enforce them, a vital aspect of a Shift Engineering Supervisor's role.
How to answer
- Discuss your approach to training and educating team members about safety practices
- Describe how you conduct regular safety audits and inspections
- Explain the importance of leading by example in adhering to safety protocols
- Share any specific initiatives you've implemented to improve safety standards
- Highlight how you handle safety violations or concerns raised by team members
What not to say
- Neglecting to mention specific safety protocols or training methods
- Implying that safety isn't a priority in your supervision
- Avoiding details on how you address violations or enforce compliance
- Overlooking the importance of team engagement in safety practices
Example answer
“At Mahindra & Mahindra, I implemented a 'Safety First' program that included monthly safety training sessions and daily briefings. I conduct regular safety audits and encourage open dialogue about safety concerns. By fostering a culture where team members feel comfortable reporting issues, we reduced safety incidents by 30% in one year. Leading by example and ensuring everyone understands their role in maintaining safety is key to my approach.”
Skills tested
Question type
Similar Interview Questions and Sample Answers
Simple pricing, powerful features
Upgrade to Himalayas Plus and turbocharge your job search.
Himalayas
Himalayas Plus
Himalayas Max
Find your dream job
Sign up now and join over 100,000 remote workers who receive personalized job alerts, curated job matches, and more for free!
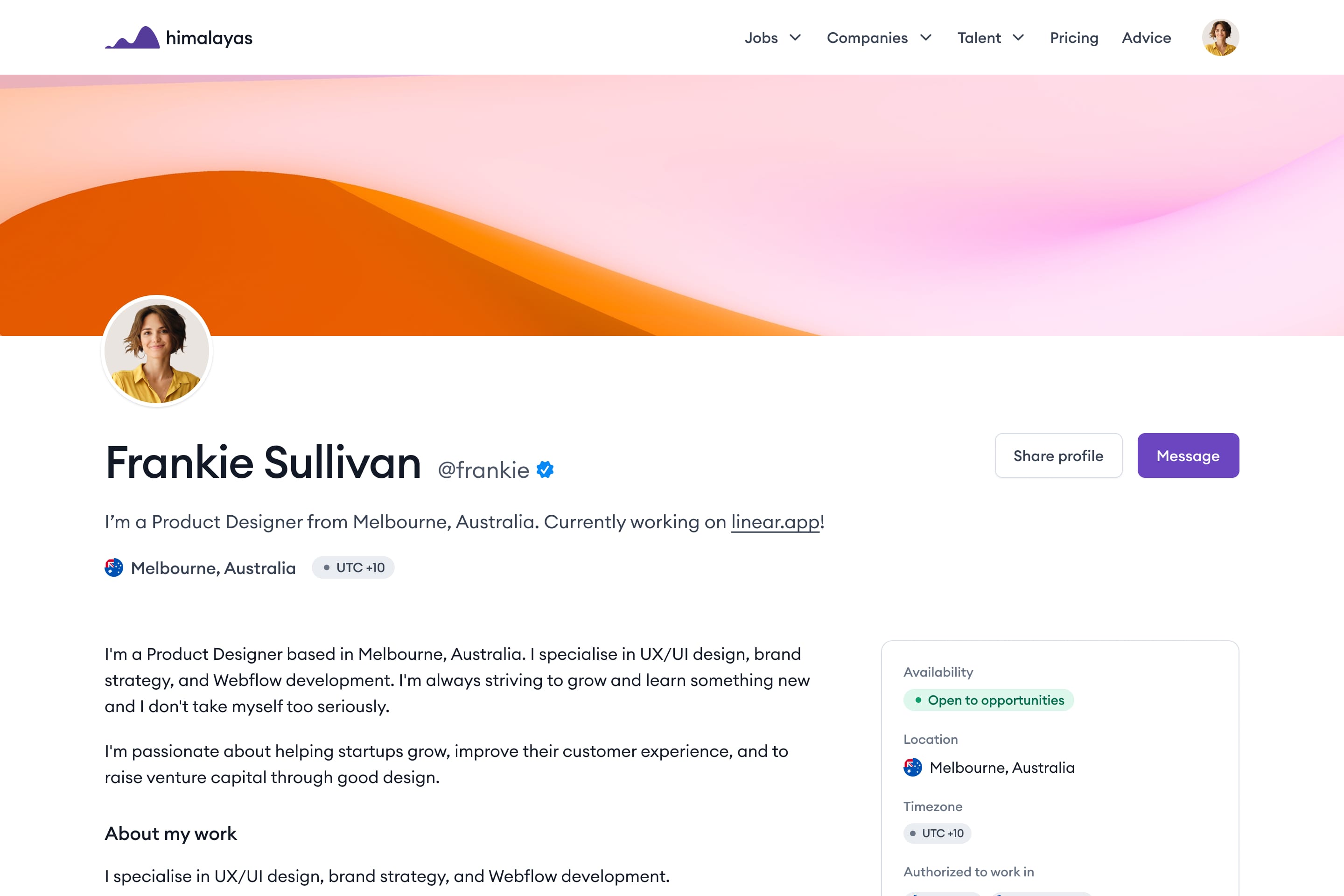