5 Plant Technician Interview Questions and Answers
Plant Technicians are responsible for operating, maintaining, and troubleshooting equipment and systems in industrial or manufacturing plants. They ensure that machinery runs efficiently and safely, performing routine inspections, repairs, and adjustments as needed. Junior technicians focus on learning and assisting with basic tasks, while senior technicians and leads take on more complex responsibilities, including mentoring others and overseeing plant operations. Need to practice for an interview? Try our AI interview practice for free then unlock unlimited access for just $9/month.
Unlimited interview practice for $9 / month
Improve your confidence with an AI mock interviewer.
No credit card required
1. Junior Plant Technician Interview Questions and Answers
1.1. Can you describe a time when you identified a problem in plant operations and how you handled it?
Introduction
This question assesses your problem-solving skills and ability to proactively manage issues within plant operations, which is crucial for a Junior Plant Technician.
How to answer
- Use the STAR method to structure your response: Situation, Task, Action, Result.
- Clearly outline the problem you identified and its implications on operations.
- Describe the steps you took to investigate and address the issue.
- Emphasize your collaboration with other team members or departments.
- Highlight the positive outcome and any lessons learned from the experience.
What not to say
- Avoid vague descriptions that lack specific details about the problem.
- Don't focus only on the negative aspects without mentioning the resolution.
- Refrain from claiming total responsibility without acknowledging teamwork.
- Avoid discussing a problem that had no impact on operations.
Example answer
“During my internship at BASF, I noticed that a conveyor belt was frequently jamming, causing downtime. I first observed the process and then collaborated with my supervisor to investigate the root cause. We discovered that a misalignment in the belt was the issue. We adjusted the alignment and implemented routine checks, which reduced downtime by 30%. This experience taught me the importance of being vigilant and proactive.”
Skills tested
Question type
1.2. How do you prioritize safety in your daily tasks within a plant environment?
Introduction
This question evaluates your understanding of safety protocols and your commitment to maintaining a safe working environment, which is vital in a plant setting.
How to answer
- Discuss any relevant safety training you have completed.
- Explain how you assess risks before starting tasks.
- Describe your approach to following safety protocols and using protective equipment.
- Provide examples of how you have promoted safety among colleagues.
- Emphasize the importance of reporting hazards or unsafe conditions.
What not to say
- Neglecting to mention any safety training or certifications.
- Downplaying the importance of safety in daily operations.
- Failing to provide specific examples of safety practices.
- Suggesting that safety protocols are optional or can be overlooked.
Example answer
“Safety is my top priority in my role. I completed a safety training course at my previous internship, where I learned to conduct risk assessments before starting any task. I always wear the necessary personal protective equipment and encourage my colleagues to do the same. For example, I once noticed a coworker not wearing safety goggles while working with chemicals, and I reminded them of the importance of following safety protocols. This commitment to safety not only protects us but also ensures smooth operations.”
Skills tested
Question type
2. Plant Technician Interview Questions and Answers
2.1. Can you describe a time when you identified a potential safety hazard in the plant and how you addressed it?
Introduction
This question is crucial for a Plant Technician role because safety is a top priority in manufacturing environments. It evaluates your ability to recognize risks and implement effective solutions.
How to answer
- Use the STAR method (Situation, Task, Action, Result) to structure your response
- Clearly describe the safety hazard you encountered and the context
- Explain the steps you took to investigate and assess the risk
- Detail the actions you implemented to resolve the issue or prevent future occurrences
- Share the outcomes, including any improvements in safety metrics or compliance
What not to say
- Minimizing the importance of safety or suggesting it's someone else's responsibility
- Describing a situation without taking ownership of your actions
- Failing to mention the impact of your actions on team safety or productivity
- Neglecting to discuss follow-up measures to ensure the hazard was resolved
Example answer
“At my previous job with Procter & Gamble, I noticed that a machine's safety guard was frequently left open by operators. I immediately reported it and initiated a safety audit that confirmed the risk. I proposed a mandatory safety training session for all operators and implemented a monitoring system to ensure compliance. As a result, we reduced safety incidents by 30% in the following quarter.”
Skills tested
Question type
2.2. What troubleshooting process do you follow when a machine stops functioning correctly?
Introduction
This question assesses your technical problem-solving skills and your systematic approach to troubleshooting machinery, which is essential for a Plant Technician.
How to answer
- Outline your step-by-step troubleshooting process
- Explain how you gather information about the issue, including data from machine logs
- Discuss how you prioritize potential causes based on your experience and knowledge
- Describe any tools or diagnostic software you use during troubleshooting
- Mention how you document the issue and your resolution for future reference
What not to say
- Providing a vague or overly simplistic troubleshooting approach
- Ignoring the importance of documentation or follow-up
- Failing to mention collaboration with other team members when necessary
- Overlooking safety protocols during troubleshooting
Example answer
“When a machine at my previous job at Coca-Cola stopped functioning, I first checked the machine logs for any error codes. Then, I inspected the physical components for wear and tear. Based on my findings, I replaced a malfunctioning sensor that was causing the shutdown. I documented the issue and updated the maintenance logs to help my team address similar problems in the future.”
Skills tested
Question type
3. Senior Plant Technician Interview Questions and Answers
3.1. Can you describe a time when you identified a significant issue in the plant's operations and how you resolved it?
Introduction
This question is crucial for assessing your analytical skills and problem-solving abilities, which are vital for a Senior Plant Technician responsible for maintaining efficient operations.
How to answer
- Use the STAR method (Situation, Task, Action, Result) to structure your response.
- Clearly outline the issue you identified and its potential impact on operations.
- Explain the steps you took to investigate the problem.
- Detail the solution you implemented and how you coordinated with your team.
- Share the measurable outcomes that resulted from your actions.
What not to say
- Focusing only on the problem without discussing the resolution.
- Failing to mention teamwork or collaboration in resolving the issue.
- Overlooking specific metrics or results to demonstrate impact.
- Being vague about your role in the resolution process.
Example answer
“At Toyota, I noticed a recurring issue with a conveyor belt malfunction that slowed down production. I conducted an analysis and found that the belt was misaligned due to wear. I coordinated with the maintenance team to realign and lubricate the system. As a result, we improved production efficiency by 20% and reduced downtime significantly.”
Skills tested
Question type
3.2. How do you ensure compliance with safety regulations in the plant?
Introduction
This question evaluates your knowledge of safety standards and your commitment to maintaining a safe working environment, which is paramount in a plant setting.
How to answer
- Discuss your familiarity with local safety regulations and standards.
- Describe specific safety protocols you implement regularly.
- Explain how you engage your team in safety practices and training.
- Share any past experiences where you improved safety compliance.
- Highlight the importance of a safety-first culture in plant operations.
What not to say
- Claiming safety is solely the responsibility of management.
- Providing vague responses without specific examples.
- Neglecting to mention ongoing training and updates on safety practices.
- Downplaying the importance of safety in day-to-day operations.
Example answer
“In my role at Mitsubishi, I made it a priority to stay updated on safety regulations, ensuring our operations met or exceeded compliance standards. I conducted quarterly safety training for all team members and introduced a safety audit system that identified potential hazards. This proactive approach resulted in a 30% reduction in workplace incidents over a year.”
Skills tested
Question type
4. Lead Plant Technician Interview Questions and Answers
4.1. Can you describe a time when you identified a critical safety issue in the plant and how you addressed it?
Introduction
This question is crucial for a Lead Plant Technician as it assesses your commitment to safety standards and your proactive approach to problem-solving in a high-risk environment.
How to answer
- Start by outlining the specific safety issue you encountered
- Explain the steps you took to assess the severity of the situation
- Detail how you communicated with your team and management about the issue
- Describe the actions you implemented to resolve the problem
- Share the outcome and any improvements in safety protocols that resulted
What not to say
- Minimizing the importance of safety concerns
- Failing to take responsibility or acknowledge oversight
- Describing a situation without detailing your involvement
- Not providing concrete outcomes or changes made
Example answer
“At a chemical plant in Durban, I noticed a potential leak in a storage tank during routine inspections. I immediately halted operations in the area and informed my supervisor. We conducted a thorough assessment and discovered a faulty valve. I coordinated with maintenance to replace the valve and implemented a new inspection schedule. After this incident, we improved our safety training, leading to a 30% reduction in safety incidents over the next year.”
Skills tested
Question type
4.2. How do you ensure that maintenance and operational procedures are followed consistently in the plant?
Introduction
This question evaluates your leadership and organizational skills, which are essential for maintaining high operational standards in a lead technician role.
How to answer
- Describe your strategies for training and educating your team on procedures
- Explain how you monitor compliance and address deviations
- Discuss the importance of documentation and regular audits
- Share examples of how you have improved adherence to procedures in the past
- Emphasize the role of open communication in maintaining standards
What not to say
- Claiming that compliance is solely the responsibility of the operators
- Failing to mention any measures you take for continuous improvement
- Overlooking the importance of training and education
- Describing a lack of monitoring or oversight
Example answer
“I ensure that all maintenance and operational procedures are consistently followed by implementing a structured training program for new hires and conducting regular refresher courses for existing staff. I utilize checklists and conduct weekly audits to ensure compliance. For instance, after noticing some lapses in procedure adherence at my previous job, I introduced a buddy system where experienced technicians mentor newer staff, resulting in a 20% improvement in compliance rates.”
Skills tested
Question type
5. Plant Supervisor Interview Questions and Answers
5.1. Can you describe a time when you had to manage a safety incident in the plant?
Introduction
This question is crucial as safety is a top priority in any manufacturing environment. It helps assess your crisis management skills and your commitment to maintaining safe working conditions.
How to answer
- Use the STAR method (Situation, Task, Action, Result) to structure your response
- Clearly describe the incident and its potential risks
- Explain your immediate actions and decision-making process
- Detail how you communicated with your team and ensured compliance with safety protocols
- Share the outcomes and any changes implemented to prevent future incidents
What not to say
- Downplaying the seriousness of the incident
- Failing to mention the importance of safety protocols
- Not discussing the lessons learned or improvements made
- Blaming others without taking responsibility for team management
Example answer
“In my previous role at a manufacturing facility, we experienced a near miss where a machine malfunctioned during operation. I quickly evacuated the area and conducted a team meeting to assess the situation. We discovered that the equipment had not been maintained properly. I coordinated with maintenance to implement a more rigorous inspection schedule and retrained staff on safety protocols. As a result, we had zero incidents in the following year, reinforcing our safety culture.”
Skills tested
Question type
5.2. How do you ensure that production targets are met while maintaining quality standards?
Introduction
This question evaluates your ability to balance productivity with quality control, which is vital for a plant supervisor.
How to answer
- Describe your approach to setting clear production goals
- Explain how you monitor production processes and quality metrics
- Detail your methods for training and motivating your team
- Discuss how you handle deviations from quality standards
- Share examples of successful initiatives that improved both productivity and quality
What not to say
- Suggesting that quantity is more important than quality
- Failing to provide specific examples of past experiences
- Ignoring the importance of team involvement in quality control
- Overlooking the role of data in monitoring performance
Example answer
“At my last plant, I implemented a dual focus on production targets and quality assurance. I set clear KPIs for both and held weekly meetings to review our progress. During one quarter, we faced quality issues, so I initiated a team retraining on our quality standards, which led to a 20% decrease in defects while still meeting production targets. This experience taught me the importance of integrating quality checks into daily processes.”
Skills tested
Question type
Similar Interview Questions and Sample Answers
Simple pricing, powerful features
Upgrade to Himalayas Plus and turbocharge your job search.
Himalayas
Himalayas Plus
Himalayas Max
Find your dream job
Sign up now and join over 100,000 remote workers who receive personalized job alerts, curated job matches, and more for free!
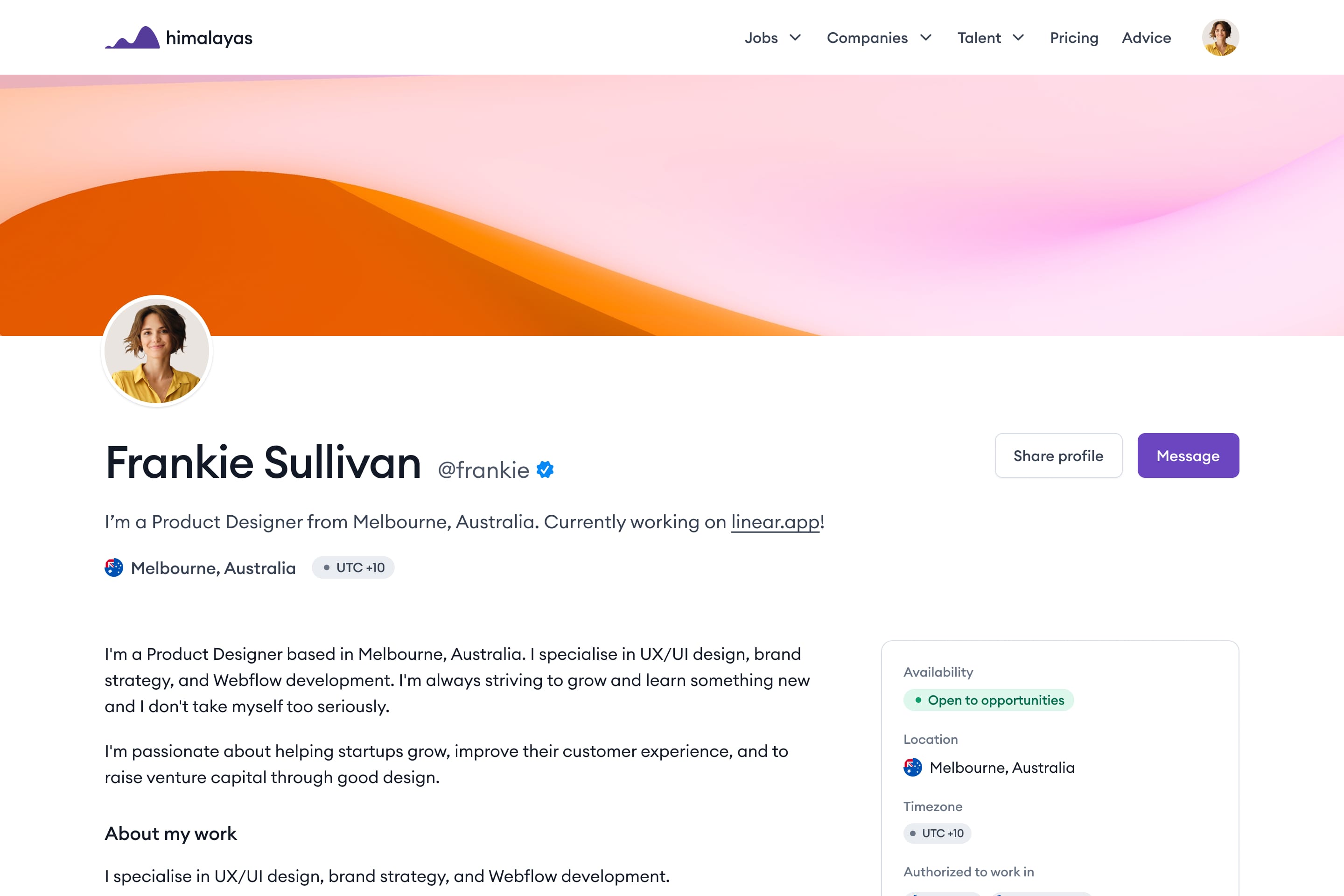