5 Sewing Machine Operator Interview Questions and Answers
Sewing Machine Operators are skilled professionals responsible for operating sewing machines to create, alter, or repair garments and other fabric-based products. They ensure precision in stitching, maintain equipment, and follow patterns or designs to meet production standards. Junior operators focus on learning machine operations and basic tasks, while senior operators and leads oversee complex projects, mentor team members, and ensure quality control in production. Need to practice for an interview? Try our AI interview practice for free then unlock unlimited access for just $9/month.
Unlimited interview practice for $9 / month
Improve your confidence with an AI mock interviewer.
No credit card required
1. Junior Sewing Machine Operator Interview Questions and Answers
1.1. Can you describe your experience operating a sewing machine and any specific techniques you excel in?
Introduction
This question is crucial as it assesses your hands-on experience with sewing machines and your proficiency in various techniques, which are essential for a Junior Sewing Machine Operator role.
How to answer
- Start by outlining your experience with different types of sewing machines and fabrics.
- Mention any specific techniques or styles you are particularly skilled in.
- Include any relevant training or certifications you've received.
- Discuss any projects or tasks where you've successfully applied your skills.
- Highlight any challenges you faced and how you overcame them.
What not to say
- Claiming to have experience with sewing without specifics.
- Failing to mention any particular techniques or styles.
- Being vague about your training or certifications.
- Ignoring the importance of safety and maintenance practices.
Example answer
“I have over two years of experience operating various sewing machines, including industrial and domestic models. I specialize in straight stitching and zigzag techniques, particularly for dressmaking and alterations. I completed a sewing course at a local college, where I learned proper machine maintenance and safety protocols. One of my proudest projects was creating a custom dress for a client, where I navigated some fabric challenges by adjusting my techniques, resulting in a perfectly fitted garment.”
Skills tested
Question type
1.2. Describe a time when you had to follow specific instructions or patterns while sewing. How did you ensure accuracy?
Introduction
This question evaluates your ability to follow detailed instructions and your attention to detail, both critical for ensuring the quality of sewing work.
How to answer
- Use the STAR method to structure your response.
- Describe the specific instructions or patterns you were given.
- Explain the steps you took to ensure accuracy, such as double-checking measurements or using tools.
- Discuss any challenges you faced in following the instructions and how you resolved them.
- Highlight the outcome and how it met the expectations.
What not to say
- Claiming you don't need to follow instructions because you are skilled.
- Providing vague examples without specific steps taken.
- Neglecting to mention any challenges or mistakes.
- Failing to recognize the importance of accuracy in sewing.
Example answer
“In my previous role, I was tasked with sewing a batch of uniforms that required following specific patterns. To ensure accuracy, I meticulously checked the measurements against the specifications and used a fabric marker to outline key points. Despite some initial confusion with the pattern, I consulted with my supervisor for clarification and adjusted my approach accordingly. The final uniforms fit perfectly, and the client was very satisfied with the quality of work.”
Skills tested
Question type
2. Sewing Machine Operator Interview Questions and Answers
2.1. Can you describe a time when you had to troubleshoot a problem with a sewing machine during production?
Introduction
This question assesses your technical knowledge of sewing machines and your problem-solving skills, which are crucial for maintaining production efficiency.
How to answer
- Describe the specific issue you encountered with the sewing machine
- Explain the steps you took to identify the root cause of the problem
- Detail the troubleshooting methods you employed to resolve the issue
- Share the outcome of your actions and how it impacted production
- Highlight any improvements you made to prevent similar issues in the future
What not to say
- Blaming the machine or other team members without taking responsibility
- Providing vague descriptions of the problem without specifics
- Failing to mention the steps taken to resolve the issue
- Ignoring the importance of preventive measures
Example answer
“At a textile factory in Melbourne, I encountered a consistent thread breakage issue while operating an industrial sewing machine. I first checked the thread tension and discovered it was too tight. After adjusting it and ensuring the thread quality was adequate, I continued production. This led to a 30% reduction in downtime, and I implemented regular maintenance checks to avoid future occurrences.”
Skills tested
Question type
2.2. How do you ensure the quality of your sewing work meets production standards?
Introduction
This question evaluates your attention to detail and your understanding of quality control processes within the sewing industry.
How to answer
- Discuss your standard operating procedures when starting a new project
- Explain how you check your work for accuracy and quality throughout the process
- Share any specific quality control measures you implement
- Describe how you handle mistakes or defects when they occur
- Mention any feedback mechanisms you use to improve your work
What not to say
- Claiming that quality control is solely the responsibility of supervisors
- Providing generic answers without specific examples
- Overlooking the importance of continuous improvement
- Failing to acknowledge the impact of quality on customer satisfaction
Example answer
“I always start by reviewing the production specifications and materials before beginning a project. During sewing, I frequently check for alignment and stitch quality, using a ruler to measure as needed. If I notice a defect, I stop immediately to correct it rather than letting it continue. This proactive approach helped maintain our quality rating above 95% at my previous job.”
Skills tested
Question type
3. Senior Sewing Machine Operator Interview Questions and Answers
3.1. Can you describe a time when you identified and resolved a significant issue with a sewing machine during production?
Introduction
This question is crucial for evaluating your problem-solving skills and technical knowledge, which are essential for a Senior Sewing Machine Operator who must ensure smooth operations.
How to answer
- Use the STAR method to structure your response: Situation, Task, Action, Result.
- Clearly describe the issue you faced and its impact on production.
- Detail the steps you took to diagnose the problem and implement a solution.
- Discuss any collaboration with team members or maintenance staff.
- Quantify the results, such as reduced downtime or improved quality.
What not to say
- Blaming the equipment or other team members without taking responsibility.
- Failing to provide specific details about the problem and solution.
- Overlooking the importance of teamwork or communication.
- Neglecting to mention any preventive measures taken afterward.
Example answer
“During my time at a textile factory in Melbourne, we faced recurring thread breakage issues that slowed down production. After analyzing the machine setup, I discovered that improper tension settings were the culprit. I recalibrated the sewing machine and trained my colleagues on proper tension checks. This not only reduced downtime by 30% but also improved our overall fabric quality, leading to fewer returns from clients.”
Skills tested
Question type
3.2. How do you maintain your sewing machines to ensure they operate at peak performance?
Introduction
This question assesses your knowledge of machine maintenance and your commitment to quality production, which is vital for a Senior Sewing Machine Operator.
How to answer
- Discuss your routine maintenance practices, including cleaning and lubrication.
- Explain how you troubleshoot and identify potential issues before they escalate.
- Mention any relevant training or certifications related to machine maintenance.
- Describe how you keep records of maintenance activities.
- Highlight the importance of preventative maintenance in reducing downtime.
What not to say
- Suggesting that maintenance is not part of your role.
- Failing to mention specific maintenance tasks or schedules.
- Neglecting to highlight the importance of machine care.
- Overlooking the role of safety in maintenance operations.
Example answer
“I follow a strict maintenance schedule for all sewing machines, including daily cleaning and weekly lubrication of moving parts. I also conduct monthly inspections to identify potential issues, which helps prevent major breakdowns. I keep detailed maintenance records, which allows me to track performance trends and address any recurring problems proactively. This approach has helped my previous team maintain a production efficiency rate of over 95%.”
Skills tested
Question type
4. Lead Sewing Machine Operator Interview Questions and Answers
4.1. Can you describe a time when you identified a defect in the sewing process and how you addressed it?
Introduction
This question is important as it assesses your attention to detail, problem-solving abilities, and quality control skills in a manufacturing environment.
How to answer
- Use the STAR method (Situation, Task, Action, Result) to structure your response.
- Clearly describe the defect you discovered and its impact on production.
- Detail the steps you took to address the defect, including any collaboration with team members.
- Explain the outcome of your actions, including any improvements in quality or efficiency.
- Reflect on what you learned from the experience and how it has influenced your current practices.
What not to say
- Blaming others for the defect without taking any responsibility.
- Failing to provide a specific example and instead giving a vague response.
- Not mentioning any follow-up actions taken to prevent future defects.
- Overlooking the importance of teamwork in addressing quality issues.
Example answer
“In my previous role at a textiles company, I noticed a recurring issue with stitching quality that was causing returns. I initiated a quality check process and worked with the team to identify the root cause: a misaligned sewing machine. After recalibrating the machines and implementing a checklist for operators, we reduced defects by 30% and improved overall product quality. This experience taught me the importance of proactive quality checks.”
Skills tested
Question type
4.2. How do you ensure that your team meets production deadlines while maintaining quality standards?
Introduction
This question evaluates your leadership and time management skills, which are crucial for a Lead Sewing Machine Operator responsible for both team performance and product quality.
How to answer
- Describe your approach to planning and scheduling production tasks.
- Explain how you communicate expectations and deadlines to your team.
- Discuss the methods you use to monitor progress and address any delays.
- Highlight your strategies for maintaining quality standards while working under pressure.
- Share an example of a time when you successfully balanced deadlines with quality.
What not to say
- Indicating that quality is secondary to meeting deadlines.
- Failing to mention how you support your team during busy periods.
- Only focusing on individual performance rather than team dynamics.
- Not providing a specific example to illustrate your approach.
Example answer
“At my previous job, I implemented a daily briefing to outline goals and deadlines for the team. By using a visual production board, we tracked progress in real-time, which helped identify potential delays early. I also encouraged team members to communicate challenges openly. During peak seasons, this approach allowed us to meet deadlines without compromising our quality standards, reducing rework by 15%.”
Skills tested
Question type
5. Sewing Supervisor Interview Questions and Answers
5.1. Can you describe a time when you improved the efficiency of a sewing production line?
Introduction
This question is crucial for assessing your ability to optimize operations and manage production effectively, which is key for a Sewing Supervisor.
How to answer
- Use the STAR method to structure your response: Situation, Task, Action, Result.
- Clearly describe the inefficiency you identified and its impact on production.
- Explain the steps you took to analyze and address the issue.
- Discuss the changes you implemented and how you involved your team.
- Quantify the results to demonstrate the impact of your improvements.
What not to say
- Blaming team members for inefficiencies without taking responsibility.
- Failing to provide specific examples or metrics.
- Focusing too much on technical aspects without addressing teamwork.
- Overlooking the importance of safety and quality in your improvements.
Example answer
“At my previous job at a textile factory, I noticed that the sewing line was experiencing frequent delays due to inefficient layout. I analyzed the workflow and rearranged the stations to minimize movement and reduce idle time. After implementing these changes, we increased our output by 20% within three months, while also maintaining our quality standards. This experience taught me the importance of continuous improvement and team collaboration.”
Skills tested
Question type
5.2. How do you ensure quality control in the sewing process?
Introduction
This question assesses your understanding of quality assurance practices, which are vital in maintaining the standards of the final product.
How to answer
- Describe your approach to establishing quality control measures.
- Include how you train your team on quality standards.
- Explain the tools or metrics you use to monitor quality.
- Discuss how you handle quality issues when they arise.
- Mention the importance of feedback loops to improve processes.
What not to say
- Suggesting that quality control is solely the responsibility of a separate department.
- Ignoring the role of training and team involvement in quality assurance.
- Failing to address how you respond to quality failures.
- Providing vague answers about quality without specific examples.
Example answer
“In my role as a Sewing Supervisor at a clothing manufacturer, I implemented a continuous quality control process. I trained my team on the importance of checking seams and finishes at each stage, which helped catch errors early. We also introduced a checklist system that improved our defect rate by 15%. When issues arose, I encouraged open communication so we could identify root causes and adapt our processes accordingly.”
Skills tested
Question type
5.3. Describe a situation where you had to manage a conflict within your team. How did you resolve it?
Introduction
Conflict management is an essential skill for a Sewing Supervisor, as it helps maintain a harmonious work environment and boosts team morale.
How to answer
- Use the STAR method to outline the situation clearly.
- Discuss the nature of the conflict and the parties involved.
- Explain the steps you took to mediate and resolve the issue.
- Highlight the positive outcome and any long-term changes made to prevent future conflicts.
- Emphasize the importance of communication and understanding in your approach.
What not to say
- Dismissing the conflict or blaming one party without taking responsibility.
- Failing to acknowledge the impact of unresolved conflicts on team dynamics.
- Describing a situation where you escalated the conflict rather than resolving it.
- Providing an answer that lacks a resolution or positive outcome.
Example answer
“In my previous role, two team members had a disagreement over their sewing techniques, which began to affect their productivity. I arranged a private meeting with both of them to understand their perspectives. We discussed the benefits of each technique and decided to have a skills-sharing session where they could teach each other. This not only resolved the conflict but also improved collaboration in the team. The experience reinforced the value of open dialogue in conflict resolution.”
Skills tested
Question type
Similar Interview Questions and Sample Answers
Simple pricing, powerful features
Upgrade to Himalayas Plus and turbocharge your job search.
Himalayas
Himalayas Plus
Himalayas Max
Find your dream job
Sign up now and join over 100,000 remote workers who receive personalized job alerts, curated job matches, and more for free!
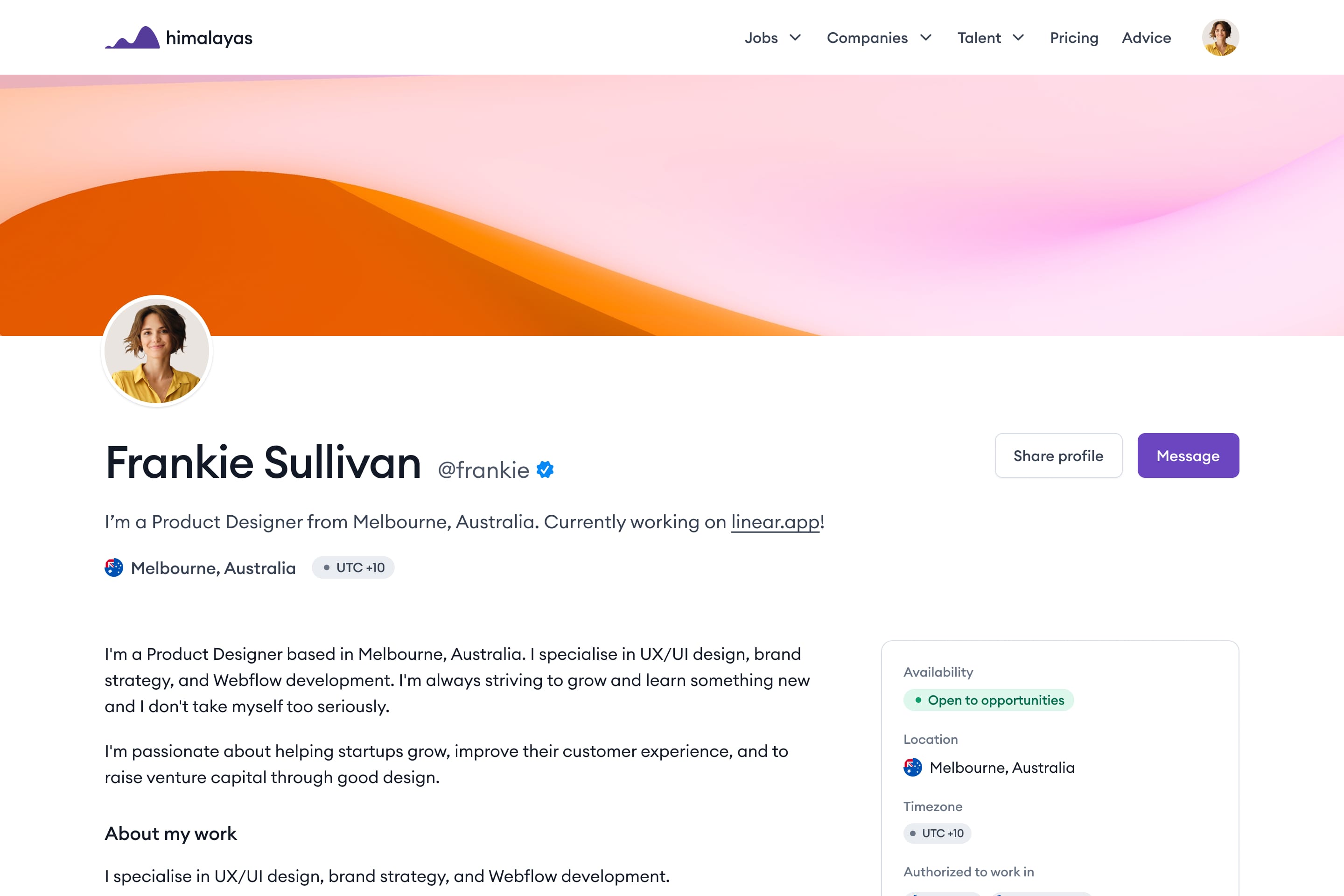