5 Production Technician Interview Questions and Answers
Production Technicians are responsible for operating, maintaining, and troubleshooting equipment in manufacturing or production environments. They ensure that production processes run smoothly, efficiently, and safely. Junior technicians focus on basic tasks and learning the processes, while senior technicians and leads take on more complex responsibilities, including mentoring, overseeing operations, and optimizing workflows. Need to practice for an interview? Try our AI interview practice for free then unlock unlimited access for just $9/month.
Unlimited interview practice for $9 / month
Improve your confidence with an AI mock interviewer.
No credit card required
1. Junior Production Technician Interview Questions and Answers
1.1. Can you describe a time when you identified and resolved a production issue in a timely manner?
Introduction
This question is crucial for assessing your problem-solving skills and ability to work under pressure, which are essential for a junior production technician.
How to answer
- Use the STAR method to structure your response: Situation, Task, Action, Result.
- Clearly outline the production issue you faced and its impact on the workflow.
- Detail the steps you took to resolve the issue, including any tools or techniques you used.
- Quantify the results of your actions, such as time saved or production efficiency improved.
- Reflect on what you learned from the experience and how it helped you grow professionally.
What not to say
- Failing to provide a specific example, which may indicate a lack of experience.
- Describing a situation where you did not take initiative or relied on others to solve the problem.
- Overemphasizing technical jargon without explaining the context.
- Neglecting to mention the outcome or results of your actions.
Example answer
“During my internship at a manufacturing facility, we encountered a significant bottleneck in our assembly line when a key machine malfunctioned. I immediately assessed the situation, identified that a simple calibration was needed, and recalibrated the machine within 30 minutes. This quick fix allowed us to resume production with minimal downtime, improving our output by 15% for that shift. This experience taught me the importance of being proactive and having a solution-oriented mindset.”
Skills tested
Question type
1.2. How do you ensure quality control in your production tasks?
Introduction
This question evaluates your understanding of quality assurance processes, a vital aspect of a production technician's role.
How to answer
- Discuss specific quality control methods you are familiar with, such as checklists or inspection techniques.
- Mention how you document your findings and any corrective actions taken.
- Explain the importance of following standard operating procedures (SOPs) in maintaining quality.
- Share examples of how you have contributed to improving quality in previous roles or projects.
- Highlight your awareness of safety standards and regulations in production.
What not to say
- Suggesting that quality control is not part of your responsibilities.
- Failing to provide specific examples or relying on vague statements.
- Overlooking the importance of teamwork and communication in quality assurance.
- Neglecting to mention safety and compliance aspects.
Example answer
“In my previous role at a packaging plant, I followed a rigorous quality control process that included daily inspections and adherence to SOPs. I used checklists to ensure every product met our quality standards before moving to the next phase. When I identified a recurring issue with packaging integrity, I documented my findings and worked with the team to adjust our processes, which reduced defects by 20%. I understand that quality control is key to maintaining efficiency and customer satisfaction.”
Skills tested
Question type
2. Production Technician Interview Questions and Answers
2.1. Can you describe a time when you identified a flaw in the production process? What steps did you take to address it?
Introduction
This question assesses your attention to detail and problem-solving skills, which are crucial for a Production Technician role, as identifying and resolving issues is key to maintaining production efficiency.
How to answer
- Use the STAR method to structure your response: Situation, Task, Action, Result.
- Clearly outline the specific flaw you identified and its potential impact on production.
- Detail the steps you took to investigate and understand the issue.
- Explain the solution you implemented and how you communicated it to your team or supervisors.
- Quantify the results of your actions, such as improved efficiency or reduced waste.
What not to say
- Avoid vague descriptions without specific examples or metrics.
- Don't focus solely on the problem without discussing your solution.
- Refrain from taking all the credit; mention team involvement if applicable.
- Do not express a lack of initiative or neglect to identify issues.
Example answer
“At a previous role with Nissan, I noticed that the assembly line was experiencing delays due to a recurring issue with a specific machine. I investigated the machine settings and discovered they were incorrectly calibrated. I collaborated with the maintenance team to recalibrate the machine, which improved our production speed by 15% and reduced downtime significantly. This experience reinforced my belief in proactive problem-solving and teamwork.”
Skills tested
Question type
2.2. What safety protocols do you prioritize when working in a production environment?
Introduction
This question helps gauge your understanding of safety standards and practices in a production setting, which is vital to ensure a safe work environment for yourself and your colleagues.
How to answer
- List key safety protocols relevant to the production environment you are familiar with.
- Explain how you ensure compliance with these protocols in your daily tasks.
- Provide examples of how you have contributed to a culture of safety in the workplace.
- Discuss any training or certifications you have related to workplace safety.
- Mention how you keep up-to-date with safety regulations.
What not to say
- Avoid stating that safety is not a priority or that you overlook protocols.
- Don't provide generic answers; be specific about your practices.
- Refrain from downplaying the importance of safety training and compliance.
- Do not claim ignorance of safety regulations.
Example answer
“In my previous position at Jaguar Land Rover, I prioritized wearing personal protective equipment (PPE) and ensuring that all safety guards on machines were in place. I participated in weekly safety meetings and encouraged fellow technicians to report any hazards. Additionally, I completed a health and safety training course, which helped me understand the importance of compliance and risk assessment. This proactive approach contributed to a 20% reduction in workplace incidents in our department.”
Skills tested
Question type
3. Senior Production Technician Interview Questions and Answers
3.1. Can you describe a time when you identified a process inefficiency and how you resolved it?
Introduction
This question assesses your problem-solving abilities and your approach to improving production efficiency, which is critical for a Senior Production Technician role.
How to answer
- Begin by clearly defining the process inefficiency you identified.
- Explain the impact of this inefficiency on production output or quality.
- Detail the steps you took to analyze the situation and propose a solution.
- Describe the implementation of your solution and any challenges faced.
- Share the measurable outcomes of your actions, such as increased efficiency or reduced waste.
What not to say
- Failing to provide a specific example and speaking in generalities.
- Blaming others for the inefficiency without taking ownership.
- Neglecting to mention collaboration with others in the resolution process.
- Overlooking the importance of follow-up to ensure the solution worked.
Example answer
“At Toyota, I noticed that our assembly line had frequent delays due to a slow component delivery process. I analyzed the workflow and discovered that we could rearrange the layout for better accessibility. After discussing with my team and making the adjustments, we reduced assembly time by 20%, resulting in a significant increase in our production rate. This experience taught me the value of continuous improvement.”
Skills tested
Question type
3.2. How do you ensure safety and compliance in the production environment?
Introduction
Safety and compliance are paramount in production roles. This question tests your understanding of safety protocols and your proactive approach to maintaining a safe work environment.
How to answer
- Discuss your knowledge of relevant safety regulations and standards.
- Share specific safety protocols you follow in your daily tasks.
- Describe how you educate and engage your team in safety practices.
- Highlight any initiatives you’ve implemented to improve safety culture.
- Include examples of how you handle safety violations or near misses.
What not to say
- Suggesting that safety is not a priority in your role.
- Failing to mention any specific safety standards or regulations.
- Ignoring the importance of team involvement in safety practices.
- Underestimating the need for regular safety audits.
Example answer
“In my role at Panasonic, I strictly adhere to OSHA regulations and conduct monthly safety training sessions for my team. I implemented a buddy system to ensure that all safety protocols are followed, which has reduced incidents by 30% over the past year. By fostering a culture of safety, I ensure that everyone feels responsible for maintaining a safe work environment.”
Skills tested
Question type
4. Lead Production Technician Interview Questions and Answers
4.1. Can you describe a time when you had to troubleshoot a significant equipment failure on the production line?
Introduction
This question assesses your technical troubleshooting skills and your ability to maintain production efficiency, which are critical in a lead technician role.
How to answer
- Start with a clear description of the equipment and the nature of the failure
- Explain the steps you took to diagnose the issue, including any tools or methods used
- Detail how you communicated with your team and other stakeholders during the process
- Highlight the outcome, including any improvements made to prevent future issues
- Reflect on the lessons learned and how they influenced your approach to maintenance
What not to say
- Failing to mention specific actions taken to resolve the issue
- Blaming the equipment or other team members without taking responsibility
- Providing vague descriptions without technical detail
- Not addressing how the failure impacted production
Example answer
“At a manufacturing plant in São Paulo, we faced a critical failure in our injection molding machine that halted production. I quickly assessed the situation, using diagnostic tools to identify a faulty sensor. I communicated with my team to implement a temporary workaround while I ordered the necessary replacement parts. After the repair, I initiated a review of our maintenance procedures, which led to a 30% reduction in similar failures in the following months. This experience reinforced the importance of proactive maintenance and team communication.”
Skills tested
Question type
4.2. How do you ensure safety and compliance in the production environment?
Introduction
This question evaluates your understanding of safety protocols and regulatory compliance, which are vital for a lead technician overseeing production.
How to answer
- Discuss your familiarity with relevant safety standards and regulations
- Describe the methods you use to enforce safety protocols among the team
- Share examples of safety training you’ve implemented or participated in
- Explain how you monitor compliance and address safety incidents
- Highlight the importance of creating a safety-first culture within the team
What not to say
- Ignoring the importance of safety regulations
- Claiming that safety is solely the responsibility of management
- Providing generic responses without specific examples
- Failing to discuss how you handle safety violations
Example answer
“In my previous role at a textile manufacturing company, I regularly led safety training sessions to ensure all team members understood compliance with regulations like NR-12. I enforced safety protocols by conducting daily audits and encouraging open conversations about safety concerns. After identifying a gap in our machinery safety checks, I implemented a new checklist system that reduced safety incidents by 40%. I believe a proactive approach to safety fosters a strong team culture and enhances overall productivity.”
Skills tested
Question type
5. Production Supervisor Interview Questions and Answers
5.1. Can you describe a time when you improved a production process? What steps did you take to implement this change?
Introduction
This question evaluates your ability to identify inefficiencies, implement improvements, and achieve measurable results, which are critical skills for a Production Supervisor.
How to answer
- Use the STAR method to structure your response: Situation, Task, Action, Result.
- Clearly describe the initial state of the production process and the specific inefficiency you identified.
- Explain the specific steps you took to analyze the process and develop an improvement plan.
- Discuss how you communicated and engaged your team in the change process.
- Quantify the results of your improvement in terms of efficiency, cost savings, or quality enhancement.
What not to say
- Failing to provide a specific example, relying on generic statements.
- Taking sole credit without acknowledging team contributions.
- Neglecting to mention any challenges faced during the implementation.
- Not providing measurable outcomes or improvements.
Example answer
“At Volkswagen, I noticed that our assembly line had a bottleneck at a specific station, leading to delays. I conducted an analysis and found that by training workers on a new tool, we could reduce time spent per unit. I implemented a training program and adjusted workflows accordingly. As a result, we improved our throughput by 25% within three months, which significantly decreased our backlog.”
Skills tested
Question type
5.2. How do you handle conflicts within your production team?
Introduction
This question assesses your conflict resolution skills and ability to maintain a positive work environment, which are essential for effective team management.
How to answer
- Describe your approach to identifying and addressing conflicts early.
- Discuss your communication style in conflict resolution, emphasizing active listening and empathy.
- Share an example where you successfully resolved a conflict, detailing your actions and the outcome.
- Highlight the importance of fostering a collaborative team culture.
- Explain how you follow up to ensure conflicts don't re-emerge.
What not to say
- Dismissing conflict as unimportant or irrelevant.
- Adopting a confrontational approach without seeking resolution.
- Failing to provide a specific example of conflict resolution.
- Ignoring the role of team dynamics in conflict situations.
Example answer
“In my previous role at BMW, I encountered a conflict between two team members who had differing opinions on a production method. I arranged a meeting where both could express their views, encouraging active listening. We then collaboratively explored a hybrid solution that incorporated elements from both sides. This not only resolved the conflict but also strengthened team cohesion, leading to improved collaboration and morale.”
Skills tested
Question type
Similar Interview Questions and Sample Answers
Simple pricing, powerful features
Upgrade to Himalayas Plus and turbocharge your job search.
Himalayas
Himalayas Plus
Himalayas Max
Find your dream job
Sign up now and join over 100,000 remote workers who receive personalized job alerts, curated job matches, and more for free!
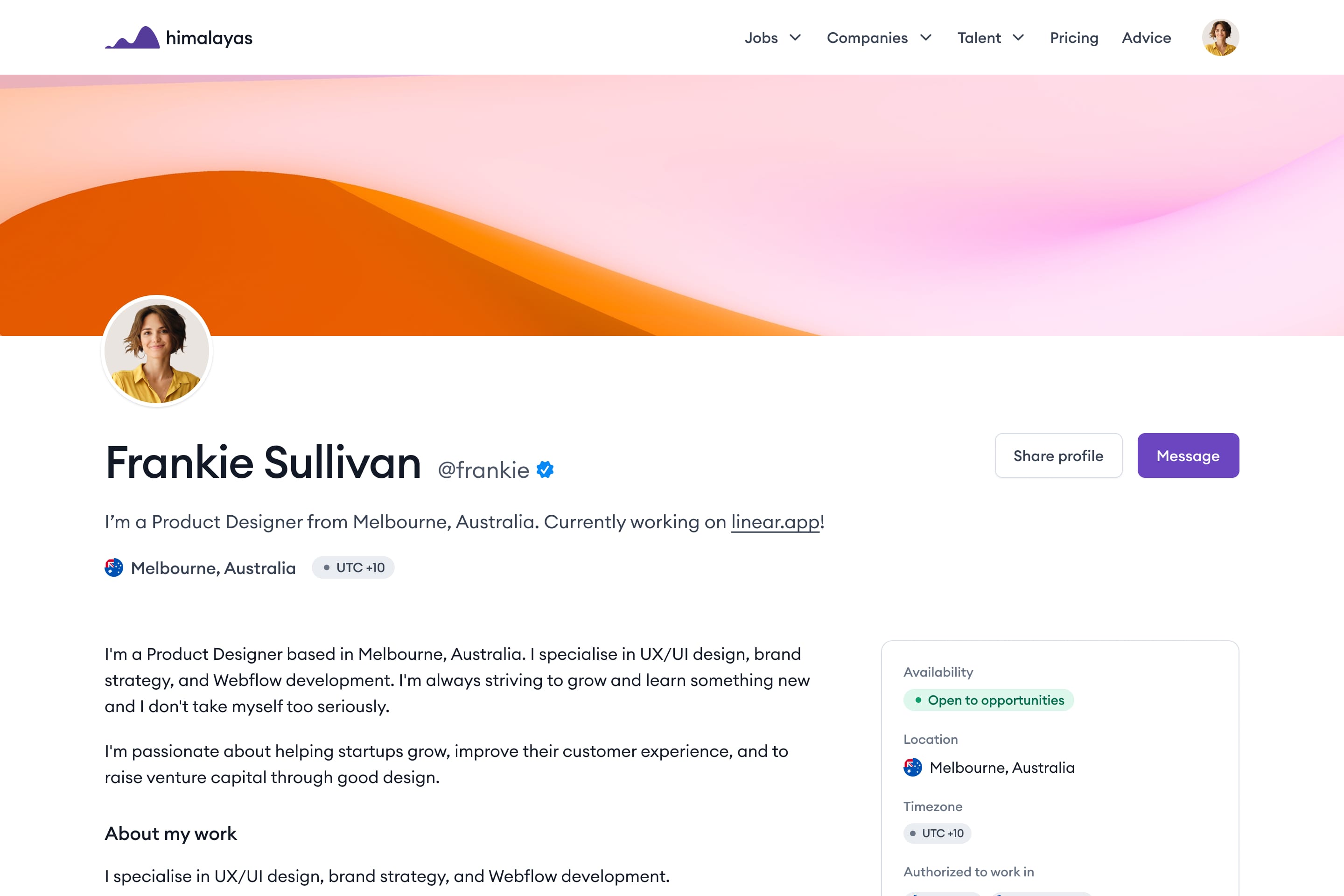