5 Loom Technician Interview Questions and Answers
Loom Technicians are skilled professionals responsible for operating, maintaining, and repairing weaving looms in textile manufacturing. They ensure the machinery runs efficiently, troubleshoot mechanical issues, and perform regular maintenance to minimize downtime. Junior technicians focus on learning the basics of loom operation and maintenance, while senior and master technicians oversee complex repairs, optimize production processes, and may supervise teams. Need to practice for an interview? Try our AI interview practice for free then unlock unlimited access for just $9/month.
Unlimited interview practice for $9 / month
Improve your confidence with an AI mock interviewer.
No credit card required
1. Junior Loom Technician Interview Questions and Answers
1.1. Can you explain the process of setting up a loom for production?
Introduction
This question is crucial for assessing your technical understanding of loom operations, which is fundamental for a Junior Loom Technician role.
How to answer
- Start by outlining the key components involved in loom setup
- Explain the steps taken to prepare the loom for production, including threading and tension adjustments
- Discuss any safety checks or protocols you follow
- Mention the importance of understanding fabric specifications
- Highlight any experience you have with different types of looms
What not to say
- Providing vague answers without technical specifics
- Failing to mention safety protocols
- Overlooking the importance of fabric specifications
- Suggesting you can set up a loom without prior training or supervision
Example answer
“To set up a loom, I first ensure I have the correct warp and weft threads based on the fabric specifications. I begin by threading the warp through the heddles and reed, ensuring proper tension. I also check the shuttle and bobbin setup before starting a test run. Safety checks, like ensuring all guards are in place, are crucial. At my previous role, I was trained on both shuttle and non-shuttle looms, which gave me a solid foundation.”
Skills tested
Question type
1.2. Describe a situation where you identified a problem during the loom operation. How did you resolve it?
Introduction
This question assesses your problem-solving abilities and your capability to respond to operational challenges, which is key for a Junior Loom Technician.
How to answer
- Use the STAR method to structure your response
- Clearly define the problem you encountered during operation
- Explain your thought process in diagnosing the issue
- Detail the steps you took to resolve the problem
- Share the outcome and any lessons learned from the experience
What not to say
- Blaming others for the problem without taking responsibility
- Describing a problem without detailing how you resolved it
- Failing to mention any preventive measures taken afterward
- Overcomplicating the situation without clear resolution steps
Example answer
“During a run at a textile mill, I noticed inconsistent fabric width due to misaligned warp threads. I promptly halted the loom and realigned the threads, ensuring they were evenly tensioned. After running a few test pieces to confirm the fix, we resumed production. This experience taught me the importance of vigilance during operation to prevent larger issues.”
Skills tested
Question type
2. Loom Technician Interview Questions and Answers
2.1. Can you describe your experience with different types of looms and how you determine which one to use for specific projects?
Introduction
This question is crucial for assessing your technical knowledge and practical experience with looms, which is essential for a Loom Technician role.
How to answer
- Begin with a brief overview of your experience with various loom types (e.g., Jacquard, shuttle, non-shuttle).
- Explain the factors you consider when choosing a loom for a project, such as fabric type, design complexity, and project timeline.
- Provide specific examples of projects where you successfully selected and operated the appropriate loom.
- Discuss any challenges faced during loom operation and how you overcame them.
- Highlight any ongoing training or certifications related to loom technologies.
What not to say
- Claiming to have experience with a loom type you are not familiar with.
- Failing to mention specific examples of projects or outcomes.
- Suggesting that loom selection is not important or can be arbitrary.
- Overlooking the importance of fabric characteristics in loom selection.
Example answer
“In my previous role at a textile manufacturing company, I worked extensively with Jacquard and shuttle looms. For a project requiring intricate patterns on silk fabric, I chose a Jacquard loom due to its capability of handling complex designs. This choice allowed us to meet the client's high standards, and the project was completed ahead of schedule, resulting in a 20% increase in customer satisfaction. I continually update my skills through workshops to stay current with new loom technologies.”
Skills tested
Question type
2.2. Describe a time when you encountered a mechanical issue with a loom. How did you troubleshoot and resolve the problem?
Introduction
This question assesses your troubleshooting skills and ability to handle mechanical issues, which are critical for maintaining loom efficiency.
How to answer
- Use the STAR method to structure your response.
- Clearly outline the mechanical issue you faced and its impact on production.
- Detail the steps you took to diagnose the problem, including any tools or techniques used.
- Explain how you resolved the issue and any preventive measures you implemented to avoid recurrence.
- Emphasize collaboration with team members if applicable.
What not to say
- Blaming others for the mechanical issue.
- Failing to demonstrate a structured approach to troubleshooting.
- Neglecting to mention the importance of preventive maintenance.
- Describing a situation without a resolution.
Example answer
“At my previous job, a shuttle loom malfunctioned, causing a halt in production. I quickly assessed the situation and found that the shuttle was misaligned. I used a gauge to check the alignment and recalibrated the mechanism, which fixed the issue. I also implemented a regular alignment check schedule to prevent future occurrences. This experience improved our downtime by 15% over the next quarter.”
Skills tested
Question type
3. Senior Loom Technician Interview Questions and Answers
3.1. Can you describe a complex loom setup that you managed and the challenges you faced?
Introduction
This question assesses your technical expertise and problem-solving skills in handling loom machinery, which is crucial for a Senior Loom Technician role.
How to answer
- Start with a brief overview of the loom setup and its specifications
- Detail the specific challenges you encountered during the setup process
- Explain the steps you took to resolve those challenges effectively
- Include any collaboration with team members or departments to overcome obstacles
- Conclude with the outcome and any improvements made as a result of your actions
What not to say
- Offering vague descriptions without specific details about the loom or challenges
- Failing to mention the resolution process
- Taking all the credit without acknowledging team contributions
- Ignoring the importance of safety and quality standards during the setup
Example answer
“At a textile mill in Singapore, I was responsible for setting up a new jacquard loom for a high-end fabric line. The challenge was integrating the new software with existing equipment, which initially caused synchronization issues. I coordinated with the IT team to troubleshoot the software, adjusting the parameters to ensure smooth operation. As a result, we completed the setup ahead of schedule and improved production efficiency by 20%. This experience reinforced the importance of cross-department collaboration in technical setups.”
Skills tested
Question type
3.2. How do you ensure quality control during the weaving process?
Introduction
This question evaluates your knowledge of quality assurance protocols and your ability to maintain high standards in weaving operations.
How to answer
- Explain your approach to monitoring loom performance and product quality
- Discuss specific quality control measures or tools you utilize
- Share examples of how you've identified and rectified quality issues in the past
- Highlight the importance of training and communication with the team regarding quality standards
- Mention any metrics or KPIs you track to evaluate quality performance
What not to say
- Ignoring the importance of quality control in favor of speed
- Providing generic answers without specific quality measures
- Failing to mention team training or involvement
- Neglecting to discuss the consequences of poor quality on production
Example answer
“In my previous role at a textile factory, I implemented a quality control checklist for every batch produced. I regularly monitored loom performance and conducted visual inspections every hour to catch any defects early. When I noticed a recurring issue with a specific thread tension, I organized a training session for the team to address it. This proactive approach reduced defects by 30% over three months, ensuring we met our quality targets consistently.”
Skills tested
Question type
4. Master Loom Technician Interview Questions and Answers
4.1. Can you describe a situation where you had to troubleshoot a significant issue with a loom machine?
Introduction
This question assesses your technical problem-solving abilities and experience in handling complex machinery, which is crucial for a Master Loom Technician.
How to answer
- Use the STAR method to structure your response: Situation, Task, Action, Result.
- Begin by describing the specific issue you encountered with the loom.
- Explain the steps you took to diagnose the problem, including any tools or methods used.
- Detail the actions you implemented to resolve the issue and any collaboration with team members.
- Conclude with the outcomes of your actions, including improvements in production or efficiency.
What not to say
- Avoid vague responses that don't detail the specific problem or process.
- Steering away from personal ownership of the situation.
- Not mentioning any measurable results or improvements.
- Focusing on just the technical aspects without discussing teamwork or communication.
Example answer
“In my previous role at a textile manufacturing company in Barcelona, we experienced frequent threading issues on one of our looms, which resulted in significant downtime. I conducted a thorough analysis and discovered that the threading guide was misaligned. After realigning it, I retrained the operators on proper threading techniques. As a result, we reduced downtime by 30% and improved overall production efficiency, which reinforced my belief in the importance of proactive maintenance and training.”
Skills tested
Question type
4.2. How do you ensure quality control during the weaving process?
Introduction
This question evaluates your understanding of quality assurance practices and their implementation in the weaving process, which is vital for maintaining product standards.
How to answer
- Describe your approach to quality control and the specific measures you take.
- Discuss the importance of monitoring processes and identifying defects early.
- Explain how you involve your team in maintaining quality standards.
- Share any tools or technology you use to assist in quality control.
- Provide examples of how your quality control measures improved product outcomes.
What not to say
- Claiming that quality control is solely the responsibility of a specific team.
- Failing to mention specific metrics or tools used in quality monitoring.
- Overlooking the importance of ongoing training for team members.
- Ignoring the feedback loop from production to design for quality improvements.
Example answer
“I adopt a proactive approach to quality control by implementing regular checks at each stage of the weaving process. At my last job, I established a set of KPIs to monitor defects and trained my team to identify issues early. We used a digital tracking system that allowed us to pinpoint problems quickly, reducing defect rates by 20%. I believe that quality control is a team effort, and I ensure my team is engaged in maintaining our standards.”
Skills tested
Question type
5. Loom Maintenance Supervisor Interview Questions and Answers
5.1. Can you describe a time when you had to troubleshoot a complex issue with a loom machine?
Introduction
This question assesses your technical problem-solving skills and your familiarity with loom machinery, both of which are crucial for a Maintenance Supervisor role.
How to answer
- Outline the specific issue encountered with the loom machine
- Detail the steps you took to diagnose the problem
- Explain the technical knowledge or tools you utilized in troubleshooting
- Discuss how you communicated with your team during the process
- Highlight the outcome and any improvements made to prevent future issues
What not to say
- Avoid vague descriptions of the problem without specifics
- Do not neglect to mention the importance of teamwork in troubleshooting
- Refrain from taking sole credit for the resolution without acknowledging others
- Don't focus only on technical jargon without explaining your thought process
Example answer
“In my previous role at Textiles de México, we faced a recurring issue with a loom that frequently jammed. I initiated a detailed inspection and discovered that a specific part was misaligned. I collaborated with my team to adjust the settings and implemented a weekly maintenance check for that loom. As a result, we reduced downtime by 30% and improved production efficiency significantly.”
Skills tested
Question type
5.2. How do you prioritize maintenance tasks in a busy production environment?
Introduction
This question evaluates your organizational skills and ability to manage multiple tasks effectively, which are essential for a Maintenance Supervisor overseeing loom operations.
How to answer
- Explain your method for assessing the urgency and impact of maintenance tasks
- Discuss how you communicate priorities to your team
- Detail any tools or systems you use to track maintenance schedules
- Provide an example of a situation where you had to adjust priorities on the fly
- Mention how you ensure minimal disruption to production during maintenance
What not to say
- Focusing solely on reactive maintenance without a proactive strategy
- Ignoring the importance of team input in prioritization
- Failing to mention any tracking or scheduling tools
- Being vague about how you handle unexpected maintenance needs
Example answer
“At Textiles de México, I prioritized maintenance tasks by assessing equipment criticality and production schedules. I used a maintenance management system to track tasks and communicate with my team. For example, when a loom faced a sudden issue, I quickly re-prioritized tasks to address it, ensuring minimal disruption to the production line. This approach helped us maintain a 95% uptime on our equipment.”
Skills tested
Question type
5.3. Describe how you would handle a situation where your team disagrees on the best maintenance approach for a loom.
Introduction
This question tests your leadership and conflict resolution skills, crucial for maintaining a harmonious and productive work environment.
How to answer
- Explain your approach to facilitating open communication among team members
- Discuss how you would gather input from all parties involved
- Detail how you would analyze the different perspectives objectively
- Share how you would ultimately make a decision and communicate it to the team
- Mention any follow-up actions to ensure team cohesion post-decision
What not to say
- Avoid suggesting that you would dismiss team input without discussion
- Do not focus only on your decision-making without acknowledging collaboration
- Refrain from indicating a lack of conflict resolution strategies
- Neglecting to mention the importance of team morale after the decision
Example answer
“In a previous role, my team had differing opinions on whether to replace a loom part or repair it. I organized a meeting where everyone could present their views and data supporting their approach. After listening to all sides, I conducted a cost-benefit analysis and decided to replace the part. I communicated my decision, along with the reasoning, to the team, which helped maintain trust and cohesion. This experience reaffirmed the importance of inclusive decision-making.”
Skills tested
Question type
Similar Interview Questions and Sample Answers
Simple pricing, powerful features
Upgrade to Himalayas Plus and turbocharge your job search.
Himalayas
Himalayas Plus
Himalayas Max
Find your dream job
Sign up now and join over 100,000 remote workers who receive personalized job alerts, curated job matches, and more for free!
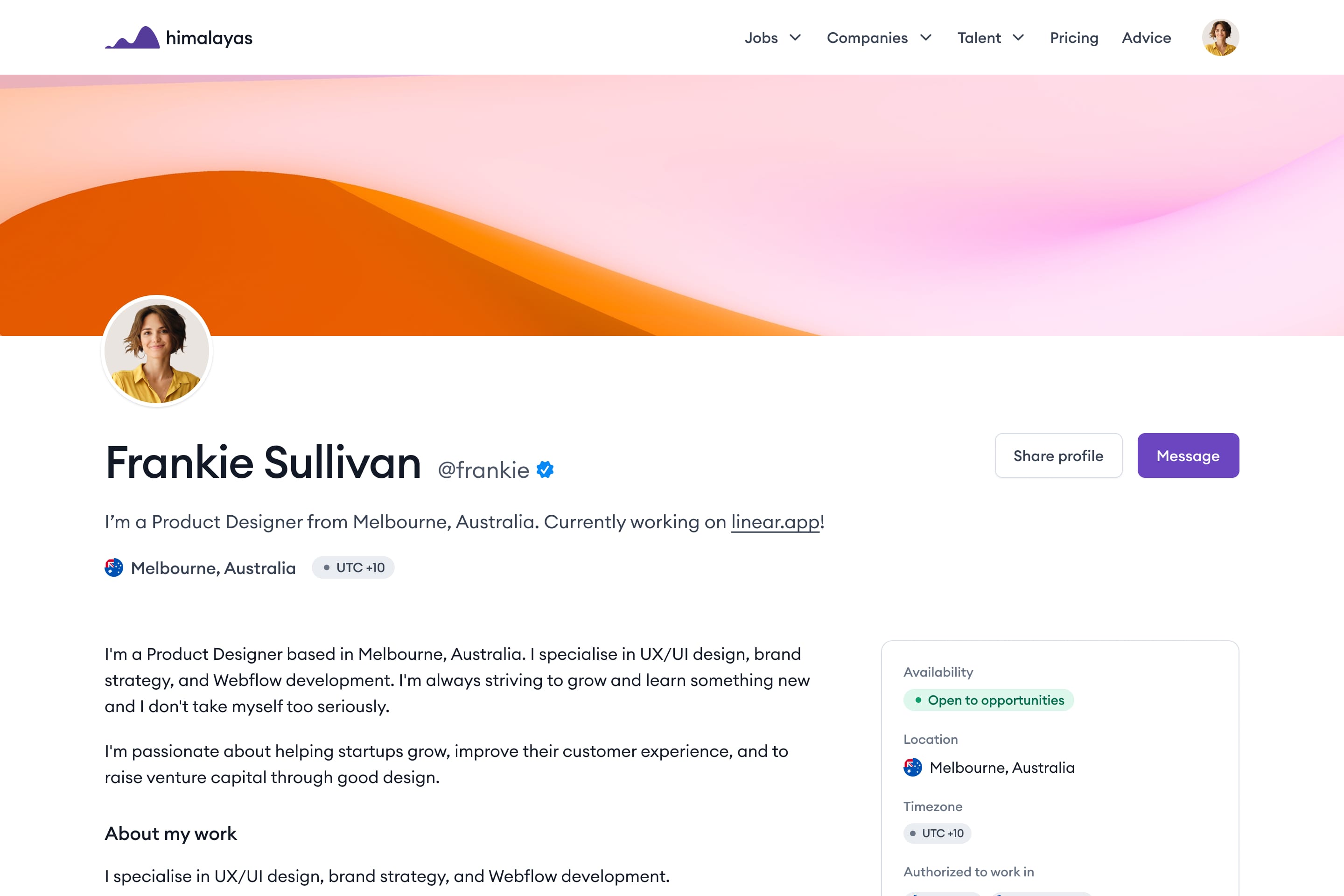