5 Dynamo Repairer Interview Questions and Answers
Dynamo Repairers specialize in diagnosing, repairing, and maintaining dynamo systems, which are essential components in various electrical and mechanical systems. They ensure the efficient functioning of these systems by troubleshooting issues, replacing faulty parts, and performing routine maintenance. Junior roles focus on assisting with basic repairs and learning the trade, while senior and lead roles involve overseeing complex repairs, mentoring junior technicians, and ensuring adherence to safety and quality standards. Need to practice for an interview? Try our AI interview practice for free then unlock unlimited access for just $9/month.
Unlimited interview practice for $9 / month
Improve your confidence with an AI mock interviewer.
No credit card required
1. Dynamo Repair Technician Interview Questions and Answers
1.1. Can you describe a time when you diagnosed a complex issue with a dynamo and how you resolved it?
Introduction
This question is important because diagnosing and resolving issues efficiently is crucial for a Dynamo Repair Technician's role, ensuring equipment reliability and customer satisfaction.
How to answer
- Use the STAR method to structure your response, focusing on the Situation, Task, Action, and Result.
- Clearly describe the technical issue you faced and the context in which it occurred.
- Explain your diagnostic process, including the tools and methods you used to identify the problem.
- Detail the steps you took to resolve the issue and any challenges you faced during the process.
- Quantify the impact of your resolution, such as reduced downtime or cost savings.
What not to say
- Focusing on minor issues that don't demonstrate technical expertise.
- Failing to mention specific diagnostic tools or techniques used.
- Not providing measurable results or outcomes from your actions.
- Avoiding discussions about teamwork or collaboration if applicable.
Example answer
“At a manufacturing facility, we experienced frequent failures in our dynamo systems. I diagnosed the problem as a misalignment in the rotor assembly. Using alignment tools, I adjusted the rotor and replaced worn bearings. This reduced system downtime by 30% and saved the company significant repair costs over the following months. This experience reinforced the importance of thorough diagnostics in maintenance work.”
Skills tested
Question type
1.2. What safety protocols do you follow when repairing dynamos, and how do you ensure compliance?
Introduction
Safety is paramount in repair work, especially with electrical equipment. This question assesses your knowledge of safety procedures and your ability to implement them effectively.
How to answer
- Discuss specific safety protocols you adhere to, such as lockout/tagout procedures.
- Explain how you conduct risk assessments before starting repairs.
- Mention any relevant training or certifications you have in safety practices.
- Describe how you ensure that all team members comply with safety standards.
- Provide an example of a situation where safety protocols prevented an incident.
What not to say
- Implying that safety protocols are optional or can be overlooked.
- Failing to mention specific safety practices or guidelines.
- Not recognizing the importance of team compliance with safety standards.
- Providing vague answers without personal accountability or examples.
Example answer
“I strictly follow OSHA regulations and our company's safety protocols, including lockout/tagout procedures to ensure all equipment is de-energized before repairs. Before each job, I perform a risk assessment and brief my team on potential hazards. Once, during a repair, my adherence to these protocols prevented a serious electrical shock incident. This practice is essential to maintain a safe working environment for everyone.”
Skills tested
Question type
2. Junior Dynamo Repairer Interview Questions and Answers
2.1. Can you describe a situation where you had to troubleshoot a malfunctioning dynamo? What steps did you take?
Introduction
This question assesses your problem-solving skills and technical knowledge in diagnosing issues with dynamos, which is critical for a repairer role.
How to answer
- Start with a brief overview of the situation, including the context of the malfunction.
- Explain the specific symptoms you observed and how they guided your troubleshooting process.
- Detail the steps you took to diagnose the issue, including any tools or techniques you used.
- Discuss how you arrived at the solution and any repairs you performed.
- Conclude with the outcome and what you learned from the experience.
What not to say
- Describing the problem without explaining how you diagnosed it.
- Failing to mention the tools or methods used in troubleshooting.
- Not providing a clear outcome or resolution to the issue.
- Overlooking any teamwork or collaboration involved in the process.
Example answer
“At a local workshop, I encountered a dynamo that was not charging. I first checked the connections and found corrosion on the terminals. After cleaning the connections, I tested the dynamo with a multimeter, which confirmed it was not generating voltage. I then replaced the faulty brushes, and after reassembly, the dynamo functioned properly. This experience taught me the importance of thorough testing and attention to detail.”
Skills tested
Question type
2.2. How do you ensure safety while repairing electrical equipment like dynamos?
Introduction
Safety is paramount in repair work, especially when dealing with electrical components. This question evaluates your understanding of safety protocols and practices.
How to answer
- Discuss general safety practices you follow when working with electrical equipment.
- Mention specific safety gear or tools you use to protect yourself.
- Explain how you assess the work environment for potential hazards.
- Share a specific example of a safety procedure you implemented during a repair.
- Emphasize the importance of adhering to safety regulations and guidelines.
What not to say
- Ignoring the importance of safety in repair work.
- Failing to mention any specific safety equipment used.
- Providing vague answers without concrete examples.
- Suggesting shortcuts or risky behaviors to save time.
Example answer
“I always wear insulated gloves and safety glasses when repairing dynamos. Before starting, I ensure the equipment is disconnected from power sources and check for any exposed wires. During a recent repair, I noticed that the work area was cluttered with tools, so I took the time to organize it to prevent tripping hazards. Following these safety practices not only protects me but also ensures a safer environment for my colleagues.”
Skills tested
Question type
3. Dynamo Repairer Interview Questions and Answers
3.1. Can you explain the process you follow to diagnose and repair a malfunctioning dynamo?
Introduction
This question assesses your technical knowledge and problem-solving skills, which are critical for a dynamo repairer to ensure efficient and safe repairs.
How to answer
- Start by outlining your initial inspection steps to identify symptoms of malfunction
- Discuss the tools and techniques you use for diagnosing issues
- Explain the common problems you encounter and how you address them
- Detail your repair process, including any safety precautions
- Share any follow-up testing or quality checks you perform post-repair
What not to say
- Providing vague details without a clear process
- Ignoring safety protocols in your explanation
- Failing to mention the importance of thorough diagnostics
- Overlooking the need for customer communication regarding repairs
Example answer
“When diagnosing a malfunctioning dynamo, I start with a visual inspection to check for physical damage or loose connections. I then use a multimeter to test the electrical output and resistance levels. Common issues I find include worn brushes or short circuits. For instance, once I repaired a dynamo that was not outputting voltage due to worn brushes. After replacing them, I conducted thorough tests to ensure it was functioning correctly before returning it to the customer, ensuring they understood the repairs made.”
Skills tested
Question type
3.2. Describe a time when you had to work under pressure to meet a tight deadline for a dynamo repair. How did you handle it?
Introduction
This question evaluates your ability to perform under pressure, which is often necessary in repair jobs where downtime can affect productivity.
How to answer
- Set the scene with the context of the repair and the deadline
- Explain the challenges you faced and how they added pressure
- Detail your approach to prioritizing tasks and managing time
- Share the outcome and any feedback from the client
- Reflect on what you learned from the experience
What not to say
- Suggesting that you work best only under pressure without examples
- Describing a situation where you failed to meet the deadline
- Neglecting to mention teamwork or communication if it was relevant
- Focusing too much on the stress rather than the solution
Example answer
“Once, I had to repair a dynamo for a factory that experienced a sudden power outage. The client needed it back in operation within 24 hours. I quickly assessed the issue, prioritized the repair of the rotor and stator, and coordinated with my team to gather the necessary parts. We managed to complete the repair ahead of schedule, and the client was pleased to have minimal downtime. This experience taught me the importance of efficient communication and teamwork under pressure.”
Skills tested
Question type
4. Senior Dynamo Repairer Interview Questions and Answers
4.1. Can you describe a particularly challenging repair you performed on a dynamo and how you approached it?
Introduction
This question is important as it assesses your technical problem-solving skills and hands-on experience with dynamo repairs. Understanding the complexities of past challenges helps gauge your expertise in this specific field.
How to answer
- Start with a brief overview of the dynamo's issue and why it was challenging
- Explain the steps you took to diagnose the problem
- Detail the repair process and any innovative methods you used
- Discuss the outcome, including any metrics or improvements achieved
- Reflect on what you learned from the experience
What not to say
- Providing vague descriptions without specifics of the challenge
- Failing to mention your role in the repair process
- Not discussing the outcome or results of the repair
- Overlooking lessons learned or areas for improvement
Example answer
“I once worked on a dynamo that had persistent overheating issues, affecting its output efficiency. After thorough diagnostics, I discovered a faulty winding insulation. I rewound the coil with high-temperature resistant insulation, which not only resolved the overheating but also improved overall efficiency by 15%. This experience taught me the importance of systematic troubleshooting and continuous learning in my repairs.”
Skills tested
Question type
4.2. How do you ensure safety and compliance when performing repairs on electrical equipment like dynamos?
Introduction
Safety is critical in electrical repair work, and this question evaluates your understanding of safety protocols and compliance measures necessary to prevent accidents and ensure a safe working environment.
How to answer
- Outline specific safety protocols you follow during repairs
- Discuss how you stay updated on safety regulations and standards
- Provide examples of how you've handled safety issues in past repairs
- Explain the importance of using Personal Protective Equipment (PPE)
- Mention training or certifications that enhance your safety knowledge
What not to say
- Downplaying the importance of safety in your work
- Failing to mention specific safety practices or protocols
- Not addressing how you educate others about safety
- Suggesting that safety can be overlooked in favor of speed
Example answer
“In my role, I prioritize safety by adhering to the regulations set by Japan's Electrical Safety Law. Before starting any repair, I conduct a risk assessment and ensure that PPE is worn at all times. I also keep updated with the latest safety training and routinely conduct safety briefings with my team. This commitment to safety has resulted in zero accidents during my tenure.”
Skills tested
Question type
5. Lead Dynamo Repair Specialist Interview Questions and Answers
5.1. Can you describe a time when you had to troubleshoot a complex issue with a dynamo repair? What steps did you take to resolve it?
Introduction
This question assesses your technical expertise and problem-solving skills, which are critical for effectively diagnosing and repairing dynamo systems.
How to answer
- Start by clearly describing the specific issue with the dynamo and its symptoms.
- Outline the diagnostic steps you took to identify the root cause.
- Explain the repair process you implemented, including any tools or techniques used.
- Discuss the outcome and any improvements observed following the repair.
- Reflect on what you learned from the experience that could help in future repairs.
What not to say
- Providing vague descriptions that lack detail about the issue and resolution.
- Focusing solely on technical jargon without explaining the process clearly.
- Not mentioning any collaboration with team members or seeking assistance.
- Neglecting to discuss the impact of the repair on the overall operation.
Example answer
“At my previous job with a manufacturing company, we had a dynamo that intermittently failed to generate power. I began by checking the wiring and connections, discovering a loose terminal. Using a multimeter, I conducted further tests to check for shorts or open circuits. After securing the terminal and replacing a faulty capacitor, the dynamo operated efficiently again. This experience taught me the importance of thorough diagnostics and communication with the team on potential issues.”
Skills tested
Question type
5.2. How do you prioritize tasks when managing multiple dynamo repair projects with tight deadlines?
Introduction
This question evaluates your organizational and time management skills, which are essential when working in a fast-paced repair environment.
How to answer
- Explain your method for assessing the urgency and importance of each project.
- Discuss any tools or systems you use for task management, such as checklists or software.
- Describe how you communicate with team members and stakeholders about priorities.
- Provide an example of a situation where you successfully managed competing deadlines.
- Highlight any adjustments you make when unexpected issues arise.
What not to say
- Suggesting you don't have a system for prioritization.
- Claiming to work best under pressure without demonstrating planning.
- Neglecting to mention collaboration with others in task management.
- Focusing solely on your own workload without considering team dynamics.
Example answer
“In my role at a repair facility, I often had to manage multiple projects. I use a prioritization matrix to evaluate tasks based on urgency and impact. For instance, when two repairs were due on the same day, I communicated with the clients to understand their needs and adjusted my schedule accordingly. This proactive approach allowed me to complete both repairs on time, resulting in positive feedback from both clients and my supervisor.”
Skills tested
Question type
Similar Interview Questions and Sample Answers
Simple pricing, powerful features
Upgrade to Himalayas Plus and turbocharge your job search.
Himalayas
Himalayas Plus
Himalayas Max
Find your dream job
Sign up now and join over 100,000 remote workers who receive personalized job alerts, curated job matches, and more for free!
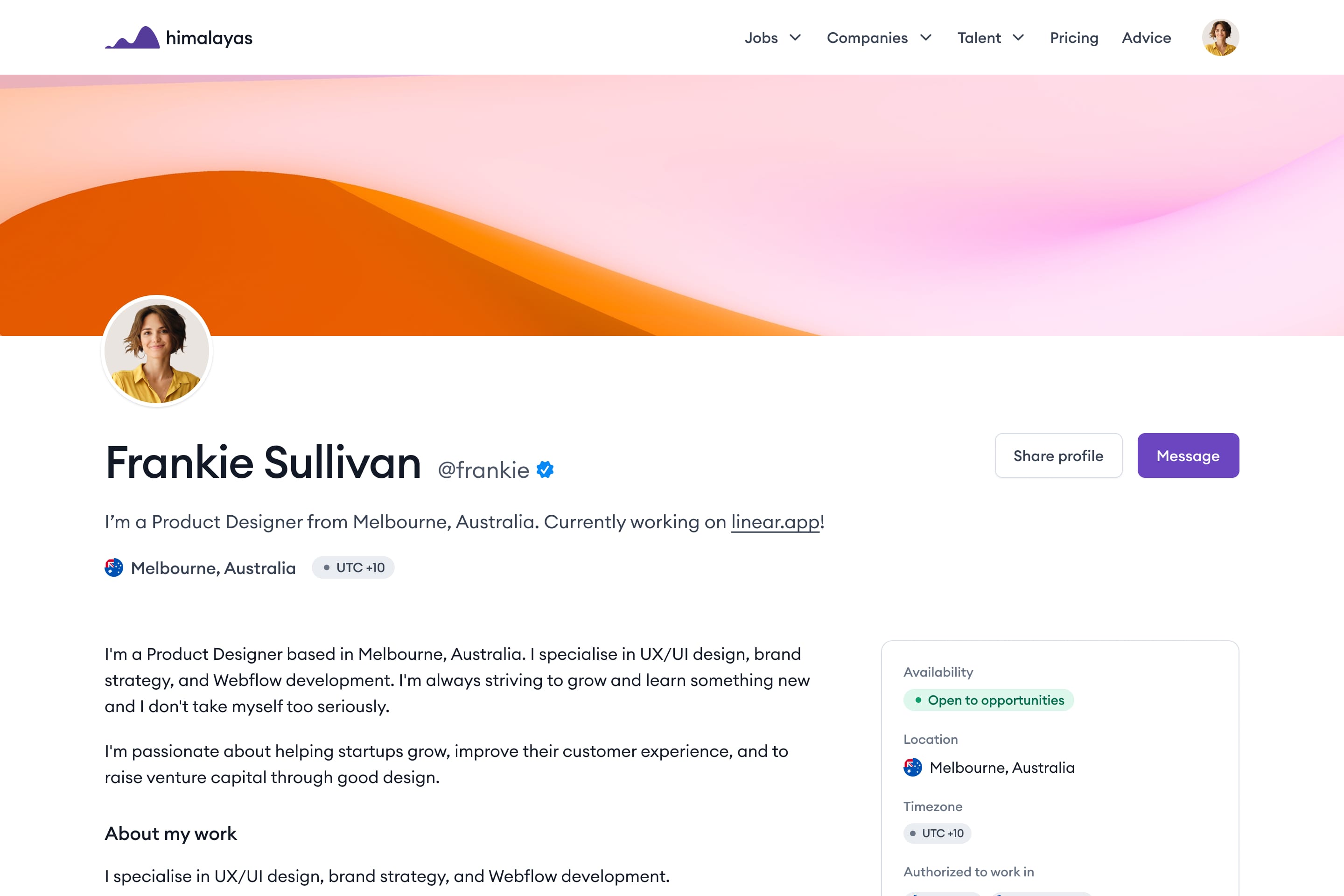