5 Armature Rewinder Interview Questions and Answers
Armature Rewinders specialize in repairing and rewinding the coils of electric motors, generators, and transformers. They diagnose faults, dismantle equipment, and replace or repair damaged windings to restore functionality. Junior roles focus on assisting with basic tasks and learning the trade, while senior and lead roles involve overseeing complex repairs, ensuring quality standards, and mentoring less experienced team members. Need to practice for an interview? Try our AI interview practice for free then unlock unlimited access for just $9/month.
Unlimited interview practice for $9 / month
Improve your confidence with an AI mock interviewer.
No credit card required
1. Junior Armature Rewinder Interview Questions and Answers
1.1. Can you describe a time when you had to troubleshoot a problem during the rewinding process?
Introduction
This question is crucial for understanding your problem-solving skills and ability to work under pressure, which are essential for a Junior Armature Rewinder role.
How to answer
- Use the STAR method (Situation, Task, Action, Result) to structure your response.
- Clearly outline the specific problem you encountered during the rewinding process.
- Detail the steps you took to diagnose the issue and the reasoning behind your approach.
- Explain the solution you implemented and its effectiveness in resolving the problem.
- Highlight any lessons learned that could improve future processes.
What not to say
- Avoid vague descriptions of the problem without context.
- Do not focus solely on the technical details without mentioning your thought process.
- Refrain from placing blame on others or external factors.
- Avoid discussing a failure without mentioning what you learned from it.
Example answer
“During my training at a local motor repair shop, I noticed that a rewound armature was running inconsistently. I suspected an issue with the winding tension. I consulted with my supervisor and conducted a tension test, discovering it was too loose. I adjusted the tension and rewound the armature. After testing, the motor operated smoothly. This experience taught me the importance of meticulous attention to detail and checking my work at every stage.”
Skills tested
Question type
1.2. What safety protocols do you follow while working with electrical components?
Introduction
This question assesses your understanding of safety procedures, which is critical in the rewinding process to prevent accidents and ensure a safe working environment.
How to answer
- Discuss your knowledge of specific safety regulations and protocols related to electrical work.
- Explain how you ensure your own safety and that of your colleagues while performing rewinding tasks.
- Provide examples of safety measures you have implemented or adhered to in previous settings.
- Mention any training or certifications you have received regarding workplace safety.
- Describe the importance of safety in maintaining equipment and preventing injuries.
What not to say
- Neglecting to mention specific safety protocols and regulations.
- Overlooking the importance of safety in the workplace.
- Suggesting that safety measures slow down production.
- Failing to provide examples of past adherence to safety practices.
Example answer
“I strictly adhere to safety protocols such as wearing personal protective equipment, following lockout/tagout procedures, and ensuring my work area is free of hazards. In my previous role, I completed a safety training course that emphasized the importance of identifying electrical hazards. This focus on safety not only protects me but also ensures a safe environment for my coworkers.”
Skills tested
Question type
2. Armature Rewinder Interview Questions and Answers
2.1. Can you explain the process you follow when rewinding an armature?
Introduction
This question is crucial for assessing your technical knowledge and practical skills specific to the role of an armature rewinder, which involves intricate craftsmanship and understanding of electrical components.
How to answer
- Start by outlining the safety precautions you take before beginning the rewinding process.
- Describe the tools and materials you use, and why they are important.
- Detail each step of the rewinding process, including how to remove the old winding, prepare the armature, and apply the new winding.
- Mention any quality checks or tests you perform to ensure the rewinding is successful.
- Conclude with an example of a time when your rewinding process improved performance or solved a specific problem.
What not to say
- Avoid being vague about your process or skipping important steps.
- Do not neglect to mention safety protocols.
- Refrain from using overly technical jargon without explanation.
- Don’t focus solely on one aspect of the job without addressing the complete process.
Example answer
“When rewinding an armature, I start by ensuring my workspace is safe and organized. I use tools like a multimeter to check for any damage and ensure I wear appropriate PPE. I then carefully remove the old winding, taking note of the winding pattern. After cleaning the armature, I select the right gauge wire and begin to wind it, ensuring consistent tension and layering. I conduct a resistance test after rewinding to ensure it meets specifications. At my previous job, this meticulous process led to a 20% increase in efficiency for the motors we serviced.”
Skills tested
Question type
2.2. Describe a challenging situation you faced while rewinding an armature and how you resolved it.
Introduction
This question evaluates your problem-solving abilities and resilience in the face of challenges, which are essential traits for an effective armature rewinder.
How to answer
- Use the STAR method to structure your response: Situation, Task, Action, Result.
- Clearly describe the challenge you faced, including any specific technical issues.
- Explain the actions you took to address the problem, including any adjustments to your process.
- Highlight the outcome of your actions, emphasizing any positive results.
- Reflect on what you learned from the experience and how it improved your skills.
What not to say
- Avoid downplaying the challenge or providing a simplistic solution.
- Do not shift blame to others or external factors.
- Refrain from describing a situation where you did not take action.
- Do not provide a response that lacks a measurable outcome.
Example answer
“Once, I was working on an armature that had a significant short circuit due to improper winding. I immediately diagnosed the issue and realized that the winding was not following the correct pattern. I took the initiative to unwind the faulty section, recalibrated my setup, and rewound it according to the specifications. As a result, the armature not only worked correctly but also increased its performance by 15%. This experience taught me the importance of double-checking my work at every step.”
Skills tested
Question type
3. Senior Armature Rewinder Interview Questions and Answers
3.1. Can you describe a complex rewinding project you've managed, including the challenges you faced?
Introduction
This question evaluates your technical expertise and project management skills in handling complex rewinding tasks, which are crucial for a Senior Armature Rewinder.
How to answer
- Use the STAR method to clearly outline the situation, task, action, and result
- Detail the specific rewinding project, including the type of armature and its application
- Discuss the challenges you encountered, such as material shortages or equipment malfunctions
- Explain the steps you took to overcome these challenges and ensure project success
- Quantify the results, such as time saved or quality improvements
What not to say
- Avoid vague descriptions without specific technical details
- Don't downplay the complexity of the project or the challenges faced
- Refrain from taking sole credit if it was a team effort
- Avoid generalizing your experience without giving concrete examples
Example answer
“At Siemens, I led a project to rewind a series of large armatures for industrial motors. We faced unexpected delays due to a shortage of specific wire gauge required for the job. I coordinated with suppliers to expedite delivery and adjusted our work schedule to minimize downtime. As a result, we completed the project two weeks ahead of the revised timeline, ensuring minimal impact on production schedules.”
Skills tested
Question type
3.2. What techniques do you employ to ensure the quality of your rewinding work?
Introduction
This question assesses your quality control methods and attention to detail, which are critical for maintaining high standards in rewinding processes.
How to answer
- Describe specific quality control processes you follow during rewinding
- Discuss the tools and equipment you use to verify quality
- Explain how you document your quality checks and findings
- Share examples of how your techniques have improved outcomes
- Mention any relevant industry standards or certifications you adhere to
What not to say
- Suggesting that quality assurance is not a priority in your work
- Failing to provide specific examples or methods
- Ignoring the role of team collaboration in quality control
- Avoiding discussion of feedback mechanisms for continuous improvement
Example answer
“I utilize a combination of visual inspections and electrical testing to ensure rewound armatures meet quality standards. I implement a checklist for each stage of the process and document any deviations for follow-up. For instance, at Rolls-Royce, my rigorous quality checks reduced rework by 30%, significantly improving our delivery timelines.”
Skills tested
Question type
4. Lead Armature Rewinder Interview Questions and Answers
4.1. Can you describe your process for diagnosing and repairing a malfunctioning electric motor?
Introduction
This question helps assess your technical expertise and problem-solving skills, crucial for a Lead Armature Rewinder's role.
How to answer
- Outline the steps you take to diagnose the issue, including tools and techniques used.
- Discuss how you gather information about the motor's history and previous repairs.
- Explain your troubleshooting process, including common issues you look for.
- Detail how you document your findings and the repairs made.
- Mention any safety protocols you follow during repairs.
What not to say
- Neglecting to mention specific diagnostic tools or methods.
- Providing an overly simplistic answer without real-world application.
- Ignoring the importance of safety and compliance.
- Failing to acknowledge collaboration with other technicians.
Example answer
“When diagnosing a malfunctioning electric motor, I first gather information on the motor's history and any previous repairs. I use a multimeter to check for continuity and voltage issues, and I listen for unusual sounds when the motor is running. If I identify a short or winding issue, I document my findings and proceed with repair, ensuring to follow all safety protocols. This systematic approach has enabled me to reduce downtime and improve motor performance.”
Skills tested
Question type
4.2. Describe a time when you had to lead a team through a complex rewinding project. What challenges did you face?
Introduction
This question evaluates your leadership skills and ability to manage complex projects, which are key for a Lead Armature Rewinder.
How to answer
- Use the STAR method to structure your response.
- Detail the specific project and its complexity, including any unique challenges.
- Explain your leadership approach and how you motivated the team.
- Discuss how you managed the timeline and resources effectively.
- Highlight the outcome and any lessons learned.
What not to say
- Focusing solely on individual contributions without mentioning the team.
- Neglecting to discuss how you handled specific challenges.
- Providing vague examples with no measurable results.
- Failing to reflect on what you learned from the experience.
Example answer
“In my previous role at GE, I led a team in a complex rewinding project for a large industrial motor. We faced tight deadlines and unexpected supply chain delays. I organized daily stand-up meetings to address issues quickly and kept the team focused on our goals. By reallocating resources and improving our workflow, we completed the project on time, which resulted in a 20% increase in efficiency for our client. This experience taught me the value of proactive communication and adaptability.”
Skills tested
Question type
5. Armature Rewinding Supervisor Interview Questions and Answers
5.1. What strategies do you implement to ensure safe and efficient armature rewinding processes?
Introduction
This question gauges your knowledge of safety protocols and efficiency measures in armature rewinding, which are crucial for maintaining quality and safety in production.
How to answer
- Describe specific safety measures you enforce in the rewinding process
- Explain how you optimize workflow to increase efficiency without compromising quality
- Share examples of tools or technologies you use to monitor and improve processes
- Discuss how you train your team on these strategies
- Consider mentioning any relevant industry standards you adhere to
What not to say
- Ignoring the importance of safety in favor of speed
- Failing to mention team training or communication
- Providing vague strategies without concrete examples
- Neglecting to address equipment maintenance and checks
Example answer
“In my previous role at Schneider Electric, I implemented a strict safety protocol that included daily equipment checks and weekly team training sessions on best practices. To enhance efficiency, I introduced a lean workflow that reduced downtime by 20%, allowing us to meet production targets consistently. I also ensure that all team members are trained on the latest safety standards, which has led to a significant reduction in workplace accidents.”
Skills tested
Question type
5.2. Can you describe a challenging situation you faced while supervising armature rewinding and how you resolved it?
Introduction
This question is important as it assesses your problem-solving skills and ability to handle challenges in a supervisory role, which are critical for maintaining production quality.
How to answer
- Use the STAR method to structure your response
- Clearly describe the challenge and its impact on production
- Detail the steps you took to analyze the problem and implement a solution
- Highlight any collaboration with your team or other departments in resolving the issue
- Share the outcome and what you learned from the experience
What not to say
- Blaming others for the challenge without taking responsibility
- Focusing too much on the problem rather than the solution
- Providing a solution that lacked team involvement
- Failing to mention the importance of learning from the situation
Example answer
“At a previous position at Alstom, we faced a significant drop in quality due to inconsistent rewinding techniques among the team. I organized a root cause analysis and identified gaps in training. I then led workshops to standardize our techniques and implemented a peer review system for quality checks. As a result, our defect rate decreased by 30% in three months, and I learned the importance of continuous team development.”
Skills tested
Question type
Similar Interview Questions and Sample Answers
Simple pricing, powerful features
Upgrade to Himalayas Plus and turbocharge your job search.
Himalayas
Himalayas Plus
Himalayas Max
Find your dream job
Sign up now and join over 100,000 remote workers who receive personalized job alerts, curated job matches, and more for free!
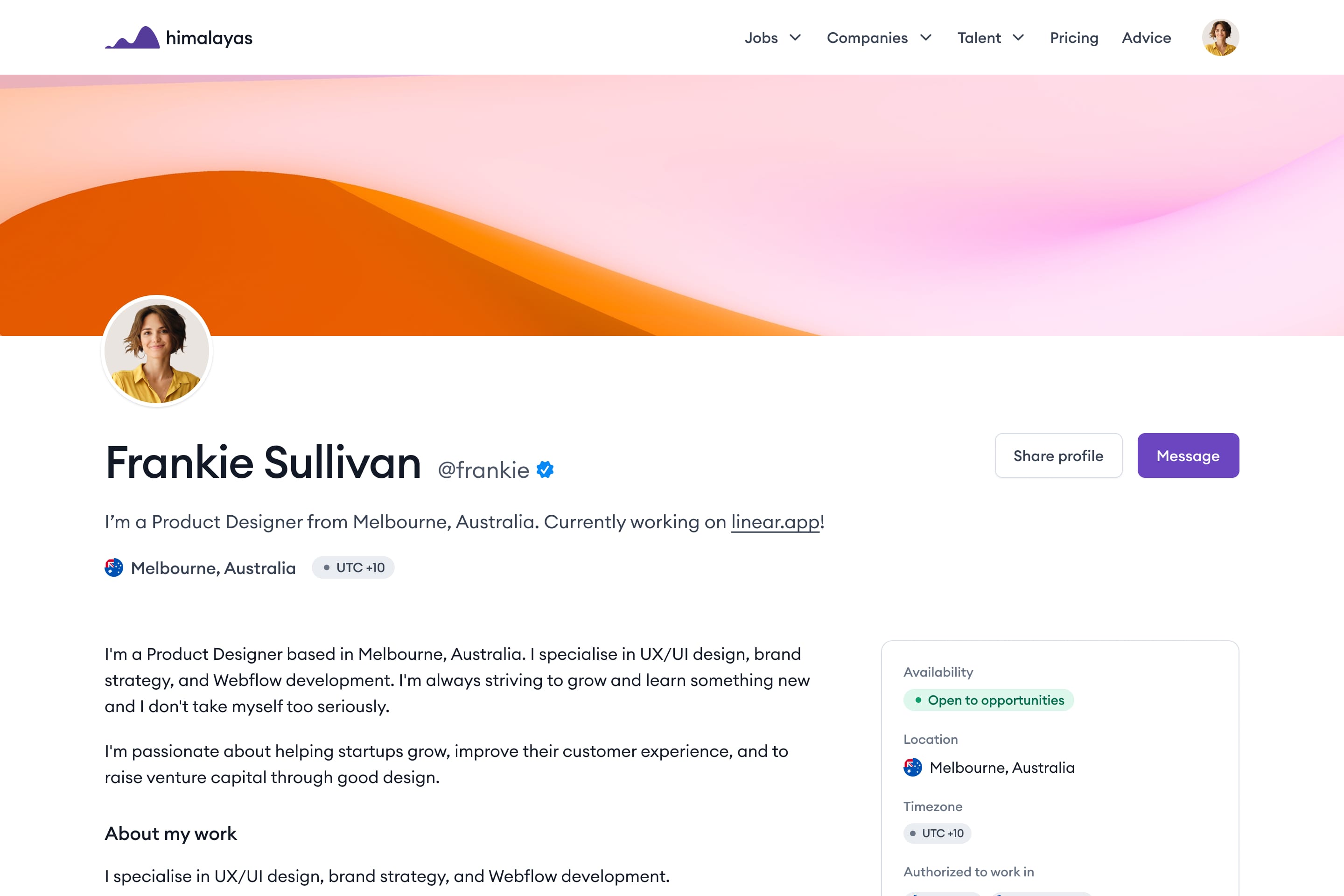