Complete Warehouse Supervisor Career Guide
Warehouse Supervisors are the linchpin of efficient supply chains, orchestrating the movement of goods and managing teams to ensure products reach their destinations on time. This role combines leadership with logistics, offering a dynamic environment where problem-solving and operational excellence directly impact business success. You will optimize workflows, manage inventory, and lead a diverse team, all critical to today's global commerce.
Key Facts & Statistics
Median Salary
$60,420 USD
(U.S. national median, BLS, May 2023)
Range: $40k - $85k+ USD (BLS, May 2023, reflects entry to experienced)
Growth Outlook
4%
as fast as average (BLS, 2022-2032)
Annual Openings
≈140k
openings annually (BLS, 2022-2032)
Top Industries
Typical Education
High school diploma or equivalent, with significant on-the-job experience. Some positions may prefer an associate's degree or postsecondary training in logistics or business.
What is a Warehouse Supervisor?
A Warehouse Supervisor is a frontline leader responsible for the efficient and safe operation of a warehouse facility. They manage the daily flow of goods, from receiving and storage to picking, packing, and shipping, ensuring that products move through the supply chain accurately and on schedule. This role is crucial for maintaining inventory integrity and meeting customer delivery expectations.
Unlike a Warehouse Manager, who focuses on strategic planning, budgeting, and overall facility performance, a Supervisor concentrates on the immediate, day-to-day execution. They directly oversee and motivate a team of associates, address operational bottlenecks, and enforce safety standards. Their primary goal is to optimize productivity and quality at the ground level, ensuring that operational targets are met consistently.
What does a Warehouse Supervisor do?
Key Responsibilities
- Oversee daily warehouse operations, including receiving, stocking, picking, packing, and shipping to ensure efficiency and accuracy.
- Manage and motivate a team of warehouse associates, providing training, performance feedback, and scheduling to optimize productivity.
- Conduct regular inventory counts and reconcile discrepancies to maintain accurate stock levels and prevent loss.
- Implement and enforce safety protocols and procedures to create a secure working environment and comply with regulations.
- Coordinate with transportation and logistics teams to ensure timely delivery and dispatch of goods.
- Analyze operational data and reports to identify areas for improvement and implement process enhancements.
- Troubleshoot and resolve operational issues, such as equipment malfunctions or order discrepancies, to minimize disruptions.
Work Environment
Warehouse Supervisors typically work in a dynamic and often fast-paced warehouse setting, which can be large, open spaces with varying temperatures depending on the goods stored. The environment involves both office work, where they manage administrative tasks and reports, and significant time on the warehouse floor, directly overseeing operations. This role requires frequent standing, walking, and occasional lifting.
Collaboration is constant, involving direct interaction with their team, logistics coordinators, and drivers. The schedule often aligns with operational hours, which might include early mornings, late evenings, or weekend shifts, especially in 24/7 operations or during peak seasons. The pace is generally steady, with bursts of high activity requiring quick problem-solving and decision-making.
Tools & Technologies
Warehouse Supervisors utilize a range of tools and technologies to manage operations effectively. They frequently use Warehouse Management Systems (WMS) like SAP EWM, Oracle WMS Cloud, or Manhattan Associates to track inventory, manage orders, and optimize space.
Handheld scanners and RFID technology are essential for real-time inventory updates and order fulfillment. Forklifts, pallet jacks, and conveyor systems are common material handling equipment they oversee and sometimes operate. Communication tools such as two-way radios, mobile devices, and collaboration software like Microsoft Teams or Slack facilitate team coordination. Data analysis software like Microsoft Excel or specialized reporting tools help them monitor performance and identify trends.
Warehouse Supervisor Skills & Qualifications
A Warehouse Supervisor's qualifications are highly practical, emphasizing hands-on experience and proven leadership over extensive formal education. Employers prioritize candidates who demonstrate a strong understanding of logistics, inventory management, and team oversight. Requirements vary significantly by the size and type of warehouse operation.
For instance, a large e-commerce fulfillment center demands expertise in automated systems and high-volume throughput, often preferring candidates with certifications in lean manufacturing or supply chain management. Conversely, a smaller distribution center might value a supervisor with broad operational knowledge and strong interpersonal skills. Entry-level supervisory roles may accept candidates with a high school diploma and several years of warehouse experience, while senior positions often seek an associate's degree or relevant certifications.
Certifications like OSHA safety training, forklift operation, or specific inventory software proficiency add significant value, often outweighing a bachelor's degree in many hiring scenarios. The industry increasingly values supervisors who can leverage technology for efficiency, such as warehouse management systems (WMS) and data analytics, alongside traditional operational skills. This role requires a balance of operational depth and the ability to adapt to evolving logistical challenges and technological advancements.
Education Requirements
Technical Skills
- Warehouse Management Systems (WMS) proficiency (e.g., SAP EWM, Oracle WMS, Manhattan Associates).
- Inventory Management principles and practices (e.g., FIFO, LIFO, cycle counting, perpetual inventory).
- Material Handling Equipment (MHE) operation and safety (e.g., forklifts, pallet jacks, reach trucks).
- Shipping and Receiving procedures, including documentation (BOLs, packing slips).
- Safety Regulations and Compliance (OSHA, hazmat handling, ergonomic practices).
- Data Entry and basic Spreadsheet Software (Microsoft Excel for tracking and reporting).
- Lean Manufacturing or Six Sigma principles for process optimization.
- Logistics and Supply Chain Fundamentals (e.g., inbound/outbound processes, freight management).
- Quality Control and Inspection protocols for incoming and outgoing goods.
- Basic Maintenance and Troubleshooting of warehouse equipment.
Soft Skills
- Leadership: Essential for motivating and guiding warehouse teams, delegating tasks effectively, and fostering a productive work environment.
- Problem-Solving: Critical for quickly identifying and resolving operational bottlenecks, equipment malfunctions, or inventory discrepancies to maintain workflow.
- Communication: Important for clearly conveying instructions to staff, coordinating with other departments, and providing feedback.
- Time Management: Necessary for prioritizing tasks, managing deadlines, and ensuring efficient loading, unloading, and stocking operations.
- Adaptability: Crucial for responding to unexpected challenges, adjusting to fluctuating demand, and implementing new procedures or technologies.
- Attention to Detail: Vital for accurate inventory counts, proper labeling, and adherence to safety protocols, minimizing errors and losses.
- Decision-Making: Required for making quick, informed choices under pressure regarding staffing, equipment use, and workflow adjustments.
How to Become a Warehouse Supervisor
Entering the warehouse supervisor field offers several pathways, from traditional logistics education to climbing the ranks from a general warehouse associate. The most common route involves gaining hands-on experience in a warehouse environment, often starting in roles like order picker, forklift operator, or shipping/receiving clerk. This practical foundation is crucial for understanding daily operations and the challenges faced by teams.
Timeline expectations vary; someone with prior leadership experience or a related degree might transition into a supervisor role within 6-12 months, while a complete beginner starting as an associate could take 2-3 years to gain the necessary experience and demonstrate leadership potential. Many companies prioritize internal promotions, making it a viable path for dedicated individuals. Geographic location and company size also influence entry; larger distribution centers in logistics hubs offer more opportunities and structured career progression than smaller local warehouses.
Networking within your current company or the broader logistics industry is vital, as many supervisor roles are filled through referrals or internal talent pipelines. Focusing on demonstrating reliability, problem-solving skills, and a proactive attitude towards process improvement will significantly enhance your visibility and chances for promotion. Your ability to manage people and processes effectively, rather than just technical skills, will be the key differentiator.
Step 1
Step 2
Step 3
Step 4
Step 5
Step 6
Step 7
Education & Training Needed to Become a Warehouse Supervisor
Becoming a Warehouse Supervisor typically involves a blend of practical experience and formal education, though the emphasis can vary significantly. Many supervisors begin as warehouse associates and advance through on-the-job training and internal leadership development programs. Formal education, such as an Associate's or Bachelor's degree in Logistics, Supply Chain Management, or Business Administration, can accelerate career progression and open doors to larger organizations or more complex operations. These degrees typically cost between $20,000 and $100,000+ and take 2-4 years to complete.
Alternatively, many aspiring supervisors pursue professional certifications or diplomas from industry associations. These programs focus on specific operational skills like inventory management, safety protocols, and team leadership. Such certifications usually range from $500 to $5,000 and can be completed in a few weeks to several months. Employers often value a combination of practical experience and relevant certifications, as they demonstrate both hands-on capability and foundational knowledge. The market perceives these credentials as highly relevant for immediate application in a supervisory role.
Continuous learning remains crucial for Warehouse Supervisors. The logistics industry constantly evolves with new technologies and best practices, making ongoing professional development essential. This includes training in warehouse management systems (WMS), automation, and lean principles. While a four-year degree provides a broad theoretical base, certifications offer targeted, job-specific skills. Cost-benefit considerations often favor certifications for those already in the field looking to advance quickly, while degrees are beneficial for long-term career growth into senior management roles. Industry-specific accreditations from bodies like the Association for Supply Chain Management (ASCM) or the Warehousing Education and Research Council (WERC) signify program quality and industry relevance.
Warehouse Supervisor Salary & Outlook
Compensation for a Warehouse Supervisor varies significantly based on several factors. Geographic location plays a crucial role, with higher salaries typically found in major metropolitan areas or regions with high costs of living and dense logistics hubs. For instance, supervisors in California or New York often earn more than those in the Midwest or Southern states, even when accounting for purchasing power. This difference reflects local market demand and the concentration of distribution centers.
Years of experience and specialized skills also drive salary variations. A supervisor with extensive experience in automated warehousing systems or hazardous materials handling can command a premium. Total compensation packages frequently extend beyond base salary, including performance bonuses tied to efficiency metrics, overtime pay, and comprehensive benefits. These benefits encompass health insurance, paid time off, and retirement contributions like 401(k) plans, which add substantial value to the overall package.
Industry-specific trends influence pay as well. E-commerce and third-party logistics (3PL) companies often offer competitive wages due to their fast-paced, high-volume environments. Larger companies with more complex operations or multiple facilities generally provide higher salaries and more robust benefits than smaller, independent warehouses. Remote work is rare for this hands-on role, so geographic arbitrage opportunities are limited. However, strong negotiation based on proven leadership, safety records, and efficiency improvements can significantly enhance earning potential.
Salary by Experience Level
Level | US Median | US Average |
---|---|---|
Assistant Warehouse Supervisor | $52k USD | $55k USD |
Warehouse Supervisor | $65k USD | $68k USD |
Senior Warehouse Supervisor | $75k USD | $78k USD |
Warehouse Manager | $90k USD | $95k USD |
Senior Warehouse Manager | $110k USD | $115k USD |
Director of Warehouse Operations | $140k USD | $150k USD |
Market Commentary
The job market for Warehouse Supervisors remains robust, driven by the continued growth of e-commerce and the increasing complexity of global supply chains. The Bureau of Labor Statistics projects a steady demand for logistics and distribution managers, including supervisors, with growth expected to be around 4% from 2022 to 2032. This translates to approximately 16,300 new jobs over the decade. Automation and AI integration are transforming warehouse operations, creating a need for supervisors who can manage advanced robotics, data analytics, and warehouse management systems (WMS).
Emerging opportunities exist in specialized areas such as cold chain logistics, last-mile delivery coordination, and reverse logistics. The demand for skilled supervisors who can optimize efficiency, ensure safety, and lead diverse teams in technology-driven environments outpaces the supply of qualified candidates in many regions. This imbalance often results in competitive compensation and signing bonuses, particularly in areas with high distribution activity.
Future-proofing this career involves continuous learning in supply chain technology, data analysis, and lean management principles. While automation handles repetitive tasks, the need for human oversight, problem-solving, and team leadership remains critical. This role is largely recession-resistant because essential goods still require distribution, even during economic downturns. Geographic hotspots for employment include major port cities, large industrial parks, and areas with significant e-commerce fulfillment centers.
Warehouse Supervisor Career Path
Career progression for a Warehouse Supervisor typically follows a clear path from operational oversight to strategic leadership. Professionals advance by demonstrating strong organizational skills, efficiency improvements, and effective team management. The field offers distinct individual contributor (IC) tracks focused on specialized areas like inventory control or logistics optimization, alongside management tracks that emphasize leading teams and overseeing broader operations.
Advancement speed depends on several factors, including individual performance, the size and complexity of the warehouse, and the industry. Larger companies with multiple distribution centers often present more opportunities for rapid progression due to a greater need for layered management. Specialization in areas like hazardous materials handling or automated systems can also accelerate career growth.
Lateral moves might involve transitioning to roles in supply chain planning, logistics coordination, or even procurement within the broader operations domain. Networking within the industry, pursuing relevant certifications in logistics or supply chain management, and continuous learning about new warehouse technologies are crucial for career acceleration and opening alternative pathways. Strong mentorship also plays a vital role in navigating leadership challenges and strategic decision-making.
Assistant Warehouse Supervisor
1-3 yearsKey Focus Areas
Warehouse Supervisor
3-5 yearsKey Focus Areas
Senior Warehouse Supervisor
5-8 yearsKey Focus Areas
Warehouse Manager
8-12 yearsKey Focus Areas
Senior Warehouse Manager
12-18 yearsKey Focus Areas
Director of Warehouse Operations
18+ yearsKey Focus Areas
Assistant Warehouse Supervisor
1-3 yearsSupport the Warehouse Supervisor in daily operations, ensuring tasks are completed efficiently and according to schedule. Oversee a small team or specific section of the warehouse, such as shipping or receiving. Address immediate operational issues and ensure compliance with safety regulations. Decision-making authority is limited to routine task execution.
Key Focus Areas
Develop foundational skills in inventory management, safety protocols, and basic team coordination. Focus on mastering warehouse management systems (WMS) and standard operating procedures (SOPs). Build effective communication skills with team members and senior staff. Understand the importance of accuracy in all tasks.
Warehouse Supervisor
3-5 yearsDirect daily warehouse activities, including receiving, storage, picking, and dispatch. Manage a team of warehouse associates, assigning tasks, and monitoring performance. Ensure adherence to safety standards, quality control, and inventory accuracy. Make operational decisions to resolve daily challenges and maintain efficiency.
Key Focus Areas
Enhance leadership and problem-solving abilities. Focus on optimizing workflow processes, reducing operational costs, and improving team productivity. Develop skills in performance management, conflict resolution, and effective resource allocation. Begin to analyze operational data for efficiency gains.
Senior Warehouse Supervisor
5-8 yearsOversee a larger or more complex section of the warehouse, or multiple smaller teams. Implement and refine operational procedures to enhance efficiency and productivity. Train and mentor junior supervisors and team leads. Participate in budget planning and resource forecasting. Their decisions significantly impact departmental efficiency.
Key Focus Areas
Master advanced inventory control techniques and logistics planning. Develop strategic thinking to implement process improvements and technological upgrades. Focus on cross-functional collaboration with other departments like transportation and customer service. Cultivate strong analytical skills for performance metrics and reporting.
Warehouse Manager
8-12 yearsManage overall warehouse operations, including budgeting, staffing, and strategic planning. Oversee multiple supervisory teams and functional areas. Implement and manage warehouse technologies, such as automation or advanced WMS. Responsible for achieving key performance indicators (KPIs) and contributing to company-wide logistics strategies.
Key Focus Areas
Develop comprehensive strategic planning and financial management skills. Focus on supply chain optimization, risk management, and vendor relationship management. Cultivate strong leadership in change management and team development across multiple functions. Pursue certifications in logistics or supply chain management.
Senior Warehouse Manager
12-18 yearsProvide leadership and strategic direction for multiple warehouse facilities or a very large, complex single site. Drive significant operational improvements and cost-saving initiatives across the network. Develop and implement long-term operational strategies aligned with company goals. Mentor and develop a team of Warehouse Managers.
Key Focus Areas
Refine executive leadership skills, focusing on cross-regional or multi-site operational excellence. Develop expertise in global logistics, supply chain resilience, and large-scale project management. Engage in high-level strategic partnerships and technology adoption. Focus on continuous improvement methodologies like Lean or Six Sigma.
Director of Warehouse Operations
18+ yearsLead the entire warehouse and distribution network operations for an organization. Responsible for setting the strategic vision for all warehousing activities, optimizing the global supply chain, and ensuring compliance. Oversee major capital investments in infrastructure and technology. A key member of the executive leadership team, influencing overall business strategy.
Key Focus Areas
Master enterprise-level supply chain strategy, including global sourcing, distribution network design, and advanced analytics. Focus on executive leadership, stakeholder management, and driving innovation. Develop expertise in international trade regulations and sustainable logistics practices. Engage in industry thought leadership.
Job Application Toolkit
Ace your application with our purpose-built resources:
Warehouse Supervisor Resume Examples
Proven layouts and keywords hiring managers scan for.
View examplesWarehouse Supervisor Cover Letter Examples
Personalizable templates that showcase your impact.
View examplesTop Warehouse Supervisor Interview Questions
Practice with the questions asked most often.
View examplesWarehouse Supervisor Job Description Template
Ready-to-use JD for recruiters and hiring teams.
View examplesGlobal Warehouse Supervisor Opportunities
Warehouse Supervisor roles universally involve overseeing logistics, inventory, and staff efficiency within distribution centers. Global demand for skilled supervisors remains strong, driven by e-commerce growth and supply chain optimization across North America, Europe, and Asia. Cultural differences in labor laws and operational standards impact daily responsibilities. Professionals consider international roles for career advancement, exposure to diverse logistics models, and higher earning potential in specific markets. No specific international certifications are broadly mandated, but experience with global supply chain software like SAP or Oracle is highly valued.
Global Salaries
Warehouse Supervisor salaries vary significantly by region, reflecting local economies and industry scale. In North America, particularly the US, annual salaries typically range from $55,000 to $75,000 USD, with higher figures in major logistics hubs like California or Texas. Canadian supervisors earn CAD 50,000 to CAD 70,000 (approximately $37,000-$52,000 USD). These figures often include benefits packages, and purchasing power is strong in many US states.
European salaries show wide variation. In Germany, supervisors can expect €40,000 to €60,000 (approximately $43,000-$65,000 USD), while in the UK, salaries are typically £30,000 to £45,000 (approximately $38,000-$57,000 USD). Scandinavian countries might offer similar or slightly higher nominal salaries but have a much higher cost of living. Southern European nations like Spain or Italy generally offer lower nominal salaries, around €25,000 to €40,000 (approximately $27,000-$43,000 USD), though purchasing power can be comparable due to lower living costs.
Asia-Pacific markets present diverse compensation. Australian Warehouse Supervisors earn AUD 60,000 to AUD 85,000 (approximately $40,000-$57,000 USD). In Singapore, salaries range from SGD 45,000 to SGD 65,000 (approximately $33,000-$48,000 USD), but the cost of living is very high. China offers RMB 90,000 to RMB 150,000 (approximately $12,500-$21,000 USD) for local roles, with significant variations based on company size and location. Tax implications and social security contributions differ greatly by country, impacting take-home pay. Experience and specific industry knowledge (e.g., cold chain logistics) significantly influence compensation globally.
Remote Work
International remote work opportunities for a Warehouse Supervisor are extremely limited. This role is inherently hands-on, requiring physical presence to manage staff, inventory, and operations within a specific warehouse facility. Direct oversight of daily processes, equipment, and safety protocols cannot be effectively performed remotely.
Some administrative or planning aspects, such as reporting or scheduling, might be done off-site. However, the core responsibilities demand on-site presence. Digital nomad opportunities are not applicable to this profession. Employers rarely offer fully remote or international remote contracts for this role due to its operational nature. Salary expectations are tied to the local labor market where the warehouse operates. Any remote component would likely be hybrid, requiring regular on-site presence, rather than full international remote work.
Visa & Immigration
Warehouse Supervisors seeking international work typically apply for skilled worker visas. Popular destinations like Canada, Australia, and the UK have points-based systems or employer-sponsored routes. For example, Canada's Express Entry system may consider this role under specific NOC codes, requiring educational credential assessment and English/French language proficiency (IELTS, CELPIP). UK Skilled Worker visas require sponsorship from a licensed employer and meeting salary thresholds. Australia's skilled migration program also considers logistics roles, often requiring specific work experience and skills assessments.
In the US, an H-1B visa is highly competitive and generally focuses on highly specialized occupations, making it less common for a direct Warehouse Supervisor role unless combined with advanced technical skills. Intra-company transfers (e.g., L-1 visa in the US, ICT visa in the UK) are possible if the supervisor works for a multinational company. European Union countries often require an employer to sponsor a work permit, demonstrating a labor market need. Visa timelines vary, from a few months to over a year. Professional licensing is not typically required, but relevant certifications (e.g., forklift operation) are essential. Pathways to permanent residency usually involve sustained employment under a skilled worker visa and meeting specific residency requirements. Family visas allow dependents to accompany the main applicant.
2025 Market Reality for Warehouse Supervisors
Understanding current market conditions is crucial for Warehouse Supervisors. The role has evolved significantly post-pandemic, with shifts in supply chain dynamics and rapid technological adoption.
Economic factors, like inflation and consumer spending patterns, directly influence warehouse activity and hiring needs. Market realities vary by experience level; entry-level roles face different challenges than senior positions. Geographic location and company size also play a substantial role in job availability and compensation. This analysis provides an honest assessment of current market realities for Warehouse Supervisors.
Current Challenges
Warehouse Supervisor candidates face increased competition. Automation and AI tools in logistics demand higher tech literacy, creating skill gaps for some. Economic uncertainty also leads companies to optimize existing staff rather than expand.
Entry-level saturation remains a concern. Job searches can extend from two to five months depending on location and industry specialization.
Growth Opportunities
Strong demand exists for Warehouse Supervisors skilled in automation integration and data-driven decision-making. Emerging opportunities include roles focused on robotics management, supply chain analytics, and sustainable logistics practices.
Professionals can gain an advantage by pursuing certifications in Lean Six Sigma, warehouse automation systems, or supply chain technology. Underserved markets often include regions with new manufacturing or distribution facility investments.
Specific skills like proficiency with warehouse management systems (WMS), experience in implementing automation, and strong team leadership capabilities are highly valued. Market corrections might create opportunities for strategic career moves into companies investing in resilient supply chains. Food and beverage, healthcare, and e-commerce logistics sectors remain robust despite broader market challenges. Investing in advanced training now can significantly boost long-term career prospects.
Current Market Trends
Hiring for Warehouse Supervisors shows steady demand, driven by e-commerce growth and supply chain reshoring. Companies prioritize efficiency and technology integration, impacting job availability and requirements. Economic conditions, while variable, emphasize cost control and optimized operations.
Generative AI and automation tools reshape the supervisor's role. AI-powered inventory management, predictive analytics for logistics, and robotic process automation demand supervisors with strong analytical and tech-savvy skills. Employers seek leaders who can manage automated systems and human teams. Traditional manual oversight roles are declining.
Salary trends show modest growth, but candidates with automation and data analytics experience command higher compensation. Market saturation exists at basic supervisory levels. However, specialized roles in cold chain, hazardous materials, or highly automated facilities see less competition.
Remote work normalization has minimal impact on this inherently on-site role. However, regional variations in market strength persist, with logistics hubs like those near major ports or e-commerce distribution centers showing stronger demand. Seasonal hiring often peaks before major retail holidays, impacting temporary and permanent positions.
Emerging Specializations
The role of a Warehouse Supervisor is evolving rapidly. Technological advancements, particularly in automation, data analytics, and supply chain integration, are creating distinct new specialization opportunities. Understanding these shifts and positioning oneself early in emerging areas is crucial for career advancement from 2025 onwards.
Specializing in these cutting-edge domains often leads to premium compensation and accelerated career growth. While established specializations remain vital, the strategic choice to pursue emerging areas can differentiate professionals significantly. These nascent fields typically move from niche to mainstream within five to ten years, creating substantial job opportunities as they mature.
However, pursuing an emerging specialization involves inherent risk. The field may not develop as anticipated, or the required skills could shift unexpectedly. Balancing this risk with the potential for high reward demands careful assessment of market trends and a commitment to continuous learning. Professionals who proactively adapt will secure leading roles in the next generation of warehouse operations.
Robotics Operations Supervisor
Warehouse Data Analytics Supervisor
Smart Warehouse Systems Supervisor
Cyber-Physical Security Supervisor
Sustainable Logistics Supervisor
Pros & Cons of Being a Warehouse Supervisor
Understanding both the benefits and challenges of any career is crucial before making a long-term commitment. A career as a Warehouse Supervisor offers distinct advantages and presents specific difficulties. Career experiences can vary significantly based on the company's culture, the industry sector (e.g., e-commerce, manufacturing), the size of the warehouse, and individual personality. What one person views as a pro, another might see as a con, depending on their values and lifestyle preferences. Additionally, the nature of the role can evolve at different career stages, with early-career supervisors focusing on hands-on tasks and senior supervisors on strategic planning. This assessment aims to provide an honest, balanced view to help set realistic expectations.
Pros
- Warehouse supervisors gain valuable leadership experience by managing teams, delegating tasks, and fostering a productive work environment, which is highly transferable to other management roles.
- There is consistent demand for skilled warehouse supervisors across various industries, ensuring good job security as logistics and supply chain operations remain essential.
- The role offers a dynamic, fast-paced work environment with new challenges daily, providing intellectual stimulation for those who enjoy problem-solving and operational efficiency.
- Supervisors have a direct impact on operational success, seeing the tangible results of their efforts in efficient material flow, accurate inventory, and timely deliveries.
- With experience, warehouse supervisors can advance into higher-level logistics, supply chain management, or operations management positions within the same or different companies.
- Many entry points exist for this role, including internal promotion from a warehouse associate, vocational training, or a bachelor's degree in logistics or supply chain management.
- The role provides practical, hands-on experience with various technologies, including inventory management systems, automated equipment, and data analytics tools, enhancing technical skills.
Cons
- Warehouse supervisors often work irregular hours, including nights, weekends, and holidays, to oversee shifts and ensure operations run smoothly during peak times.
- The role involves significant physical demands, requiring constant movement, lifting, and standing for extended periods, which can lead to fatigue and physical strain over time.
- Supervisors face high pressure to meet strict deadlines, manage inventory accuracy, and achieve productivity targets, directly impacting company profitability.
- Managing a diverse team of warehouse associates can be challenging, as it requires strong interpersonal skills to handle conflicts, motivate staff, and address performance issues.
- The work environment in a warehouse can be noisy, dusty, and subject to temperature extremes, which may contribute to discomfort or health issues for some individuals.
- Career progression can be limited within a single warehouse, often requiring relocation or a move into more senior logistics management roles to advance significantly.
- Supervisors are frequently on call to address unexpected operational issues, such as equipment breakdowns, staffing shortages, or urgent shipping problems, disrupting personal time.
Frequently Asked Questions
What are the essential qualifications and experience needed to become a Warehouse Supervisor?
You typically need a high school diploma or GED, plus several years of experience in a warehouse or logistics environment. Many employers also prefer candidates with an associate's or bachelor's degree in supply chain management, logistics, or a related field. Demonstrating leadership potential and strong organizational skills during your previous roles is crucial for moving into a supervisory position.
How long does it take to advance from a general warehouse worker to a Supervisor position?
The timeline varies significantly based on your current experience. If you are already working in a warehouse, you might transition into a supervisory role within 2-5 years by taking on leadership responsibilities and pursuing relevant certifications. For someone new to the industry, it could take 5-10 years to gain the necessary operational experience and leadership skills before moving into a supervisory position.
What are the typical salary expectations and benefits for a Warehouse Supervisor?
Salaries for Warehouse Supervisors vary by location, company size, and experience, but generally range from $45,000 to $70,000 annually. Entry-level supervisors might start lower, while experienced supervisors in larger operations or specific industries can earn more. Benefits packages often include health insurance, retirement plans, and sometimes performance-based bonuses.
What is the typical work-life balance like for a Warehouse Supervisor, considering shifts and demands?
The work-life balance can be demanding, as warehouse operations often run 24/7. Supervisors frequently work irregular hours, including nights, weekends, or holidays, especially during peak seasons. While the role demands flexibility, it also offers a dynamic environment where no two days are exactly alike. Planning and delegation are key to managing your time effectively.
Is the role of a Warehouse Supervisor secure, especially with increasing automation in logistics?
Job security for Warehouse Supervisors is generally stable. E-commerce growth and global supply chain demands mean that warehouses remain critical to many businesses. While automation is increasing, the need for human oversight, problem-solving, and team leadership remains essential. Supervisors are crucial for ensuring smooth operations, making the role less susceptible to full automation.
What are the potential career growth opportunities for an experienced Warehouse Supervisor?
There are significant opportunities for career growth. You can advance to roles like Warehouse Manager, Operations Manager, Logistics Manager, or even Supply Chain Director. Pursuing further education, gaining certifications in lean logistics or supply chain management, and consistently demonstrating strong leadership and problem-solving skills will help you climb the career ladder.
What are the biggest day-to-day challenges a Warehouse Supervisor faces?
Common challenges include managing diverse teams, optimizing inventory accuracy, dealing with unexpected supply chain disruptions, and ensuring safety compliance in a fast- paced environment. You will also need to balance productivity targets with quality control and employee well-being. Strong communication and problem-solving skills are essential for navigating these daily challenges effectively.
Can a Warehouse Supervisor role be done remotely, or is it strictly an on-site position?
The Warehouse Supervisor role is primarily on-site due to the hands-on nature of managing physical inventory, equipment, and personnel. While some administrative tasks might be done remotely, the core responsibilities require a constant physical presence in the warehouse. This role typically offers very limited remote work flexibility.
Related Careers
Explore similar roles that might align with your interests and skills:
Distribution Supervisor
A growing field with similar skill requirements and career progression opportunities.
Explore career guideWarehouse Coordinator
A growing field with similar skill requirements and career progression opportunities.
Explore career guideWarehouse Lead
A growing field with similar skill requirements and career progression opportunities.
Explore career guideWarehouse Manager
A growing field with similar skill requirements and career progression opportunities.
Explore career guideWarehouse Operations Manager
A growing field with similar skill requirements and career progression opportunities.
Explore career guideAssess your Warehouse Supervisor readiness
Understanding where you stand today is the first step toward your career goals. Our Career Coach helps identify skill gaps and create personalized plans.
Skills Gap Analysis
Get a detailed assessment of your current skills versus Warehouse Supervisor requirements. Our AI Career Coach identifies specific areas for improvement with personalized recommendations.
See your skills gapCareer Readiness Assessment
Evaluate your overall readiness for Warehouse Supervisor roles with our AI Career Coach. Receive personalized recommendations for education, projects, and experience to boost your competitiveness.
Assess your readinessSimple pricing, powerful features
Upgrade to Himalayas Plus and turbocharge your job search.
Himalayas
Himalayas Plus
Himalayas Max
Find your dream job
Sign up now and join over 100,000 remote workers who receive personalized job alerts, curated job matches, and more for free!
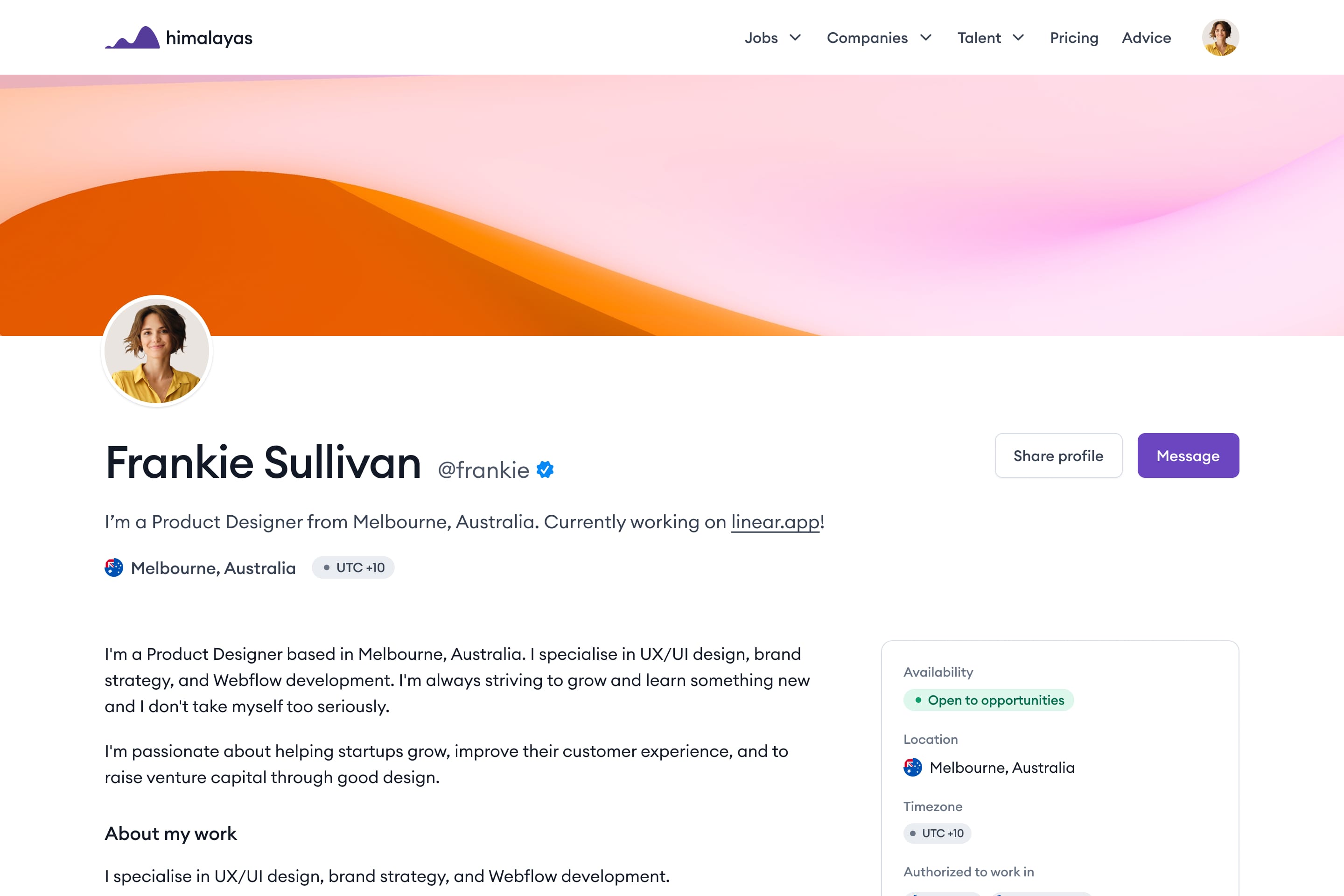