Complete Warehouse Picker Career Guide
Warehouse pickers are the backbone of modern logistics, ensuring countless products move efficiently from storage to shipping. This vital role keeps supply chains flowing, directly impacting how quickly goods reach consumers and businesses.
It offers a clear entry point into the logistics sector, providing opportunities for rapid skill development and career advancement within a growing industry.
Key Facts & Statistics
Median Salary
Range: $29k - $49k+ USD
Growth Outlook
Annual Openings
Top Industries
Typical Education
High school diploma or equivalent; on-the-job training is common
What is a Warehouse Picker?
A Warehouse Picker is a crucial logistics professional responsible for accurately retrieving specific products from warehouse inventory to fulfill customer orders or prepare shipments. This role forms the backbone of order fulfillment, ensuring that the right items are selected in the correct quantities and prepared for the next stage of the supply chain.
Unlike a general warehouse associate who might handle various tasks including receiving, stocking, and shipping, a Warehouse Picker's primary focus is the precise and efficient selection of goods. They differ from a Material Handler, whose role is more about the movement and organization of materials within the facility, rather than the specific selection of items for orders. The picker's efficiency directly impacts delivery times and customer satisfaction, making their attention to detail and speed vital.
What does a Warehouse Picker do?
Key Responsibilities
- Locate and retrieve specific items from warehouse shelves or storage areas according to picking lists or scanner instructions.
- Scan product barcodes and input quantities into inventory management systems to ensure accurate record-keeping.
- Inspect items for damage or discrepancies, reporting any issues to supervisors for resolution.
- Safely operate equipment like pallet jacks or forklifts, if certified, to move products within the warehouse.
- Package picked items securely for shipment, ensuring proper labeling and documentation.
- Organize and replenish stock on shelves, maintaining a clean and efficient work area.
- Collaborate with team members to meet daily picking quotas and maintain workflow efficiency, especially during peak periods.
Work Environment
Warehouse pickers typically work in large, open warehouse facilities that can be noisy due to machinery and activity. The environment varies from climate-controlled to ambient temperatures, depending on the products stored. This role involves significant physical activity, including walking, standing for long periods, bending, lifting, and reaching. Collaboration with other pickers, packers, and supervisors is common, though much of the work is independent. Schedules often involve fixed shifts, including nights or weekends, and can be fast-paced, especially during peak seasons. Some roles might require overtime.
Tools & Technologies
Warehouse pickers primarily use handheld barcode scanners or voice-picking systems to locate and verify items. They often interact with Warehouse Management Systems (WMS) on these devices or through computer terminals for inventory updates and order tracking. Depending on the warehouse, they might operate manual or electric pallet jacks, and if certified, forklifts. Other essential tools include scales for weighing packages, tape dispensers, and various packaging materials like boxes, bubble wrap, and shrink wrap. Safety equipment such as gloves, safety shoes, and reflective vests are also standard.
Warehouse Picker Skills & Qualifications
A Warehouse Picker's qualifications center on efficiency, accuracy, and adherence to safety protocols. Employers prioritize practical experience and a strong work ethic over extensive formal education. For entry-level positions, a high school diploma or GED is typically sufficient, with many companies providing on-the-job training.
Requirements for Warehouse Pickers can vary significantly based on the size of the warehouse, the type of goods handled (e.g., cold storage, hazardous materials, fragile items), and the level of automation. Larger distribution centers often require familiarity with advanced picking technologies like RF scanners or voice picking systems. Smaller operations might still rely on manual processes. The emphasis on speed versus accuracy also shifts; high-volume e-commerce warehouses prioritize speed, while pharmaceutical or high-value goods warehouses demand meticulous accuracy.
Certifications like forklift operation or hazardous material handling are highly valued, indicating a broader skill set and commitment to safety. While formal degrees are not essential, a strong record of reliability and attention to detail is critical for advancement to roles like lead picker or warehouse supervisor. The industry increasingly adopts automation, requiring pickers to adapt to new technologies and integrate with robotic systems. Therefore, a willingness to learn and adapt to new tools is becoming more important.
Education Requirements
Technical Skills
- RF Scanner and Handheld Device Operation (for scanning barcodes and managing inventory)
- Voice Picking Systems Usage (following audio commands for picking tasks)
- Pallet Jack Operation (manual and electric)
- Forklift Operation (e.g., sit-down, stand-up, reach truck, order picker - if certified)
- Inventory Management Software Navigation (basic functions for verifying stock)
- Basic Math Skills (for counting items, calculating quantities, and verifying order totals)
- Warehouse Management System (WMS) Interaction (basic data entry and order status updates)
- Material Handling Equipment Knowledge (understanding different types of equipment and their safe use)
- Order Picking Methodologies (e.g., batch picking, zone picking, wave picking)
- Safety Protocol Adherence (understanding and implementing OSHA and company-specific safety guidelines)
Soft Skills
- Attention to Detail: Essential for accurately identifying products, quantities, and locations, preventing errors in order fulfillment.
- Reliability and Punctuality: Crucial for maintaining operational flow and meeting strict shipping deadlines, as delays impact the entire supply chain.
- Physical Stamina: Necessary for sustained periods of standing, walking, lifting, and bending in a fast-paced environment.
- Teamwork and Collaboration: Important for coordinating with other pickers, packers, and supervisors to ensure smooth workflow and achieve daily targets.
- Problem-Solving: Useful for identifying and addressing discrepancies in inventory, damaged goods, or misplaced items, and escalating issues when necessary.
- Adaptability: Key for adjusting to changing priorities, new picking technologies, or fluctuating order volumes.
- Safety Consciousness: Paramount for adhering to all safety regulations, operating equipment responsibly, and preventing accidents in a busy warehouse setting.
- Time Management: Critical for organizing picking routes and prioritizing tasks to fulfill orders efficiently within designated timeframes, especially in high-volume environments.
How to Become a Warehouse Picker
Becoming a warehouse picker involves straightforward entry pathways, often bypassing the need for extensive formal education or prior experience. Most roles emphasize reliability, physical stamina, and attention to detail. Entry can be swift, with many entry-level positions available for immediate hire, particularly during peak seasons like holidays.
While traditional paths involve applying directly to warehouses or logistics companies, non-traditional entry might include temporary staffing agencies specializing in industrial placements. These agencies often provide a quicker route to gaining initial experience. Geographic location significantly impacts job availability; major distribution hubs and industrial zones offer more opportunities than rural areas.
Misconceptions often include the idea that these roles are purely manual labor; modern warehouses increasingly integrate technology, requiring basic digital literacy for scanning and inventory systems. Networking, though less formal than in other fields, involves building a good reputation with supervisors and peers, which can lead to internal promotions or referrals for better roles.
Step 1
Step 2
Step 3
Step 4
Step 5
Education & Training Needed to Become a Warehouse Picker
Becoming a Warehouse Picker primarily emphasizes practical skills and efficiency, rather than formal academic degrees. Most employers value hands-on experience and a strong work ethic. Traditional 4-year degrees are generally not required or even beneficial for this role, saving individuals significant time and money compared to other professions. Instead, focus on certifications and short-term training.
Alternative learning paths, such as employer-provided on-the-job training, vocational programs, or certifications in areas like forklift operation or safety, are highly relevant. These typically range from a few days to a few weeks, with costs from free (employer-paid) to a few hundred dollars for certifications. Self-study for basic warehouse operations can also be effective, focusing on safety protocols and inventory management principles through online resources. Completion timeframes are short: certifications take 1-5 days, while on-the-job training varies by employer.
Employers prioritize candidates with demonstrable reliability, attention to detail, and a foundational understanding of warehouse safety. Certifications like OSHA 10-Hour General Industry provide a recognized credential that shows commitment to safety. Continuous learning often involves staying updated on new warehouse technologies, such as automated picking systems or inventory software, which employers typically train their staff on. The cost-benefit analysis heavily favors short, practical training and certifications, as they directly enhance employability and efficiency in a warehouse setting without the substantial investment of a degree.
Warehouse Picker Salary & Outlook
Compensation for a Warehouse Picker varies significantly based on several factors beyond just base pay. Geographic location plays a crucial role, with higher wages typically found in major metropolitan areas or regions with higher costs of living and strong logistics industries. Conversely, rural areas or regions with lower demand may offer less.
Experience level, specific skill sets like operating specialized equipment (e.g., forklifts, pallet jacks), and proficiency with warehouse management systems directly influence earning potential. Companies often offer performance-based bonuses for efficiency and accuracy, enhancing total compensation. Overtime hours are also a common way pickers increase their take-home pay.
Beyond base salary, total compensation packages often include health insurance, paid time off, and retirement plan contributions like 401(k)s. Some larger companies or e-commerce giants may offer additional perks or profit-sharing. Unionized warehouses also tend to have structured pay scales and benefit packages.
Industry-specific trends, such as the growth of e-commerce and rapid fulfillment demands, can drive salary growth for skilled pickers. Negotiating leverage comes from demonstrated reliability, high productivity, and a clean safety record. While remote work is not applicable to this hands-on role, the demand for efficient warehouse operations across various industries ensures consistent employment opportunities, though international salary variations mean these figures are specific to the USD context.
Salary by Experience Level
Level | US Median | US Average |
---|---|---|
Junior Warehouse Picker | $33k USD | $35k USD |
Warehouse Picker | $37k USD | $39k USD |
Senior Warehouse Picker | $42k USD | $44k USD |
Warehouse Team Lead | $48k USD | $50k USD |
Warehouse Supervisor | $59k USD | $62k USD |
Market Commentary
The job market for Warehouse Pickers remains robust, largely driven by the continued growth of e-commerce and the increasing complexity of global supply chains. Demand for efficient order fulfillment has intensified, making this role critical across retail, manufacturing, and logistics sectors. The Bureau of Labor Statistics projects employment for material moving machine operators, which includes warehouse pickers, to grow 5% from 2022 to 2032, about as fast as the average for all occupations. This translates to approximately 47,000 new jobs over the decade.
Emerging opportunities for Warehouse Pickers include roles in highly automated warehouses where pickers might interact with robotics and advanced inventory systems, requiring a blend of physical dexterity and technical aptitude. The rise of micro-fulfillment centers in urban areas also creates new, localized job opportunities. Supply often meets demand for entry-level positions, but skilled pickers with certifications in equipment operation or experience with specialized software are highly sought after.
While automation and AI are impacting warehouse operations, the need for human pickers for complex, varied, or delicate items, and for managing exceptions, is likely to persist. The role is generally recession-resistant as consumer goods still need to move, even during economic downturns. Geographic hotspots for these roles include major distribution hubs near large population centers and ports, such as California, Texas, and states in the Midwest and Southeast with significant logistics infrastructure. Continuous learning in new warehouse technologies will be key for career advancement.
Warehouse Picker Career Path
Career progression for a Warehouse Picker typically involves a blend of operational skill mastery, efficiency improvements, and a gradual assumption of leadership responsibilities. Advancement often hinges on consistent performance, accuracy, and a strong understanding of warehouse logistics and safety protocols. The pathway can diverge into individual contributor (IC) tracks focused on specialized picking roles, or management/leadership tracks that oversee teams and entire sections of the warehouse.
Advancement speed depends on factors like the size and automation level of the warehouse, industry demand, and an individual's proactive engagement in learning new systems or equipment. Larger distribution centers may offer more structured paths, while smaller operations might require individuals to take on broader roles sooner. Lateral moves might involve specializing in specific material handling equipment, inventory control, or shipping/receiving roles, broadening a professional's expertise within logistics.
Continuous learning in areas like inventory management software, safety certifications, and equipment operation fuels progression. Networking within the company, demonstrating reliability, and showing initiative to train new hires or improve processes are crucial for standing out. Career pivots from this role often lead to positions in logistics coordination, supply chain analysis, or even operations management, leveraging the foundational knowledge of goods movement and inventory systems.
Junior Warehouse Picker
0-1 yearKey Focus Areas
Warehouse Picker
1-3 yearsKey Focus Areas
Senior Warehouse Picker
3-5 yearsKey Focus Areas
Warehouse Team Lead
5-8 years total experience, 1-3 years in leadershipKey Focus Areas
Warehouse Supervisor
8-12 years total experience, 3-5 years in supervisionKey Focus Areas
Junior Warehouse Picker
0-1 yearPrimarily focuses on accurate and efficient order fulfillment for individual customer orders or bulk shipments. Works under direct supervision, following clear instructions for picking locations and quantities. Handles basic material movement and maintains a clean work area. Contributes to daily operational targets for speed and accuracy.
Key Focus Areas
Develop foundational picking techniques, including efficient route planning and accurate item identification. Master the use of basic warehouse tools like hand scanners and pallet jacks. Focus on adherence to all safety regulations and standard operating procedures. Build a strong understanding of inventory locations and product codes.
Warehouse Picker
1-3 yearsIndependently executes picking tasks, often handling more complex or varied order types. Requires minimal supervision and can troubleshoot minor issues related to inventory or equipment. Contributes to daily team goals and may assist in training new junior pickers on basic tasks. Maintains a high level of productivity and quality.
Key Focus Areas
Refine picking efficiency and accuracy, often exceeding minimum performance metrics. Learn to operate additional equipment like forklifts or reach trucks, if certified. Develop problem-solving skills for common picking discrepancies or inventory issues. Understand basic inventory management principles and how picking impacts stock levels.
Senior Warehouse Picker
3-5 yearsServes as a go-to expert for complex picking challenges and difficult order fulfillment. Provides informal guidance and support to junior colleagues, ensuring adherence to best practices. May participate in quality control checks or assist with inventory audits. Takes initiative in resolving operational bottlenecks and improving team output.
Key Focus Areas
Master advanced picking strategies, including batch picking and zone picking, to optimize workflow. Develop leadership potential by mentoring and guiding less experienced pickers. Gain proficiency in warehouse management systems (WMS) beyond basic scanning. Focus on identifying and suggesting process improvements for efficiency and safety.
Warehouse Team Lead
5-8 years total experience, 1-3 years in leadershipDirectly oversees a small team of warehouse pickers, assigning tasks, monitoring performance, and ensuring daily targets are met. Acts as the primary point of contact for team members, addressing operational issues and providing immediate support. Responsible for training new team members and ensuring compliance with safety and operational policies. Reports team progress and challenges to supervisors.
Key Focus Areas
Develop strong leadership and communication skills to motivate and direct a team. Learn effective delegation, conflict resolution, and performance coaching techniques. Gain a deeper understanding of overall warehouse operations, including inbound, outbound, and inventory control. Focus on data analysis to identify trends and optimize team performance.
Warehouse Supervisor
8-12 years total experience, 3-5 years in supervisionManages a larger section or shift within the warehouse, overseeing multiple teams and team leads. Responsible for optimizing workflows, managing labor resources, and ensuring adherence to key performance indicators (KPIs). Makes decisions regarding staffing, equipment utilization, and operational adjustments to meet business objectives. Collaborates with other departments like logistics and inventory control.
Key Focus Areas
Cultivate strategic planning and resource allocation skills. Develop expertise in budget management, labor forecasting, and advanced WMS functionalities. Enhance problem-solving abilities for systemic operational issues. Focus on continuous improvement methodologies like Lean or Six Sigma to drive overall warehouse efficiency and cost reduction.
Job Application Toolkit
Ace your application with our purpose-built resources:
Warehouse Picker Cover Letter Examples
Personalizable templates that showcase your impact.
View examplesWarehouse Picker Job Description Template
Ready-to-use JD for recruiters and hiring teams.
View examplesGlobal Warehouse Picker Opportunities
Warehouse pickers are essential globally, ensuring supply chain efficiency. This role involves selecting items for orders, a universal need in e-commerce and logistics. Demand remains high worldwide, especially with increasing online retail volumes. While methods vary slightly, the core function is consistent across countries. International opportunities often arise in regions with booming distribution centers or labor shortages. No specific international certifications are typically required, but experience and efficiency are highly valued.
Global Salaries
Warehouse picker salaries vary significantly by region and cost of living. In North America, a picker might earn $30,000 - $45,000 USD annually in the United States, and $35,000 - $50,000 CAD in Canada. These figures often include benefits like health insurance and paid time off. In Western Europe, salaries range from €25,000 - €35,000 EUR in Germany or the Netherlands, offering good purchasing power relative to local costs. The UK sees similar ranges, around £20,000 - £28,000 GBP. These regions generally have robust social benefits and higher minimum wages.
Asia-Pacific countries like Australia offer $45,000 - $55,000 AUD, reflecting higher living costs. Japan's salaries might be ¥2.5M - ¥3.5M JPY annually, with less emphasis on extensive benefits. Latin America typically shows lower nominal salaries, for example, $8,000 - $15,000 USD equivalent in Mexico or Brazil, but local purchasing power can still provide a reasonable living standard. Experience and efficiency directly impact compensation globally.
Tax implications differ widely. European countries often have higher income taxes but provide more public services. North American tax burdens vary by state or province. Take-home pay is always a crucial consideration. Some international companies offer standardized pay scales for similar roles, but local market rates usually dictate picker wages. Overtime pay and performance bonuses are common, increasing overall compensation. Understanding the full compensation package, including non-monetary benefits, is vital for international comparisons.
Remote Work
Warehouse picker roles are inherently physical and require on-site presence. Therefore, international remote work opportunities for this specific position are virtually nonexistent. The core function of picking items from a physical warehouse cannot be performed remotely. Digital nomad visas or remote work policies do not apply to this occupation.
Any remote work for this role would involve administrative or supervisory tasks, which fall outside the scope of a typical 'warehouse picker' job description. Companies hiring internationally for logistics roles would expect pickers to be physically located at their distribution centers. This role does not offer geographic arbitrage potential through remote work.
Visa & Immigration
Immigration for warehouse pickers typically relies on skilled worker visas or general labor programs. Popular destinations include Canada, Australia, and parts of Europe (e.g., Germany, Netherlands) due to labor shortages. Requirements vary; Canada's Express Entry system or Provincial Nominee Programs might be pathways for those with relevant experience, though this role is not always highly ranked. Australia's skilled occupation lists sometimes include logistics roles.
European countries often require a job offer and may have specific visa categories for general labor or seasonal work. Education credential recognition is less critical for this role compared to professional occupations, but basic literacy and numeracy are expected. Visa timelines can range from a few months to over a year. Language requirements are generally minimal for entry-level roles, but basic English or the local language is beneficial for workplace communication.
Pathways to permanent residency are possible but often require several years of continuous employment and meeting specific criteria. Family visas are usually dependent on the primary applicant's visa status. There are typically no profession-specific fast-track programs for warehouse pickers; immigration depends more on general labor market needs and individual country policies. Practical considerations include proving financial stability and securing accommodation upon arrival.
2025 Market Reality for Warehouse Pickers
Understanding current market conditions is crucial for any warehouse picker seeking employment or career advancement. The logistics sector has experienced significant shifts between 2023 and 2025, largely influenced by post-pandemic e-commerce surges, evolving consumer expectations, and the rapid integration of automation and AI.
Broader economic factors, such as inflation and supply chain stability, directly impact warehouse operations and staffing needs. Furthermore, market realities for pickers can vary based on experience level, with specialized roles sometimes offering more stability, and geographic region, as major distribution hubs often have more opportunities than rural areas. This analysis will provide an honest assessment of these realities.
Current Challenges
Warehouse pickers face increased competition from automation and a higher expectation for efficiency, often driven by new AI-powered systems. Entry-level roles, in particular, see significant applicant pools. Economic shifts can quickly impact consumer demand, leading to fluctuating work availability. The need for precise, fast work leaves little room for error.
Growth Opportunities
Despite automation, strong demand exists for pickers willing to adapt to hybrid roles, working alongside robots or managing automated guided vehicles. Specializing in specific inventory systems or operating advanced picking machinery can provide a competitive edge. Warehouses focusing on perishable goods, medical supplies, or high-value items often seek meticulous and reliable pickers.
Geographic areas with new distribution center developments, particularly in logistics corridors, present growing opportunities. Developing proficiency in warehouse management software, data entry accuracy, and basic troubleshooting for picking technology significantly enhances a picker's value. Proactive individuals who demonstrate reliability and a willingness to learn new technologies often find more stable roles and advancement paths. Companies are always looking for pickers who can contribute to overall operational efficiency and reduce errors.
Current Market Trends
Demand for warehouse pickers remains steady, driven by the continued growth of e-commerce and rapid delivery expectations. Companies are investing heavily in automation and AI-driven inventory management, which shifts the picker's role towards operating alongside or overseeing automated systems rather than purely manual tasks. Efficiency metrics are more critical than ever, with performance often tracked digitally.
Economic conditions, while generally stable, can create short-term hiring fluctuations; however, the underlying need for fast order fulfillment keeps the sector resilient. Technology, specifically robotics and AI-powered routing, directly influences daily operations, requiring pickers to adapt to new tools and processes. Employers now seek candidates who are not only physically capable but also tech-savvy enough to interact with handheld devices, scanners, and sometimes basic robotic interfaces.
Salary trends show modest growth, primarily tied to productivity bonuses or specialized shifts, but the market remains highly competitive, especially for entry-level roles. Remote work is not applicable here; all work is on-site. Peak seasons, like holidays, continue to see significant temporary hiring spikes, while off-peak periods may have fewer open positions.
Emerging Specializations
The role of a Warehouse Picker is evolving rapidly, driven by advancements in automation, data analytics, and supply chain optimization. These technological shifts are not eliminating the need for pickers, but rather transforming the skills required and creating new, specialized career paths. Understanding these emerging areas allows professionals to proactively adapt, positioning themselves for future-oriented roles.
Early positioning in these emerging specializations is crucial for career advancement in 2025 and beyond. Professionals who develop expertise in next-generation picking methodologies or technologies often command premium compensation and experience accelerated career growth. While established picking roles remain vital, the highest growth and most rewarding opportunities are increasingly found in these specialized niches.
Many emerging areas transition from niche to mainstream within five to ten years, creating significant job opportunities as industries widely adopt new practices. Pursuing cutting-edge specializations involves a balance of risk and reward. While requiring an investment in new learning, the potential for higher demand and less competition often outweighs the initial uncertainty, offering a clear advantage for those who embrace change.
Robotic Picking System Operator
This specialization focuses on operating and maintaining robotic picking systems, including autonomous mobile robots (AMRs) and collaborative robots (cobots). As warehouses increasingly deploy automated solutions for order fulfillment, pickers will transition from manual tasks to supervising, troubleshooting, and programming these machines. This role ensures the seamless integration of human and robotic workflows, optimizing picking efficiency and accuracy.
Augmented Reality Picker
With the rise of augmented reality (AR) and virtual reality (VR) in logistics, this specialization involves using AR glasses or handheld devices to receive visual picking instructions, navigate warehouses, and identify items with enhanced precision. These tools overlay digital information onto the physical environment, reducing errors and training time while significantly boosting picking speed. This role requires adapting to technology that provides real-time data and guidance.
Data-Driven Picking Optimizer
This role focuses on optimizing picking routes and processes using real-time data from warehouse management systems (WMS) and inventory analytics. Pickers in this specialization analyze data to identify bottlenecks, suggest layout improvements, and implement more efficient picking strategies. They move beyond simply executing tasks to actively contributing to operational intelligence, ensuring maximum throughput and minimal waste.
Specialized Goods Order Fulfillment Picker
This specialization involves managing and picking orders for highly specialized or perishable goods, such as pharmaceuticals, fresh produce, or hazardous materials. It requires adherence to strict regulatory compliance, temperature controls, and specific handling protocols. Pickers in this area need a deep understanding of product-specific requirements and safety standards, ensuring product integrity and regulatory adherence.
Sustainable Picking Specialist
Sustainability in logistics is creating roles focused on optimizing picking to minimize environmental impact. This specialization involves strategies like consolidating orders to reduce packaging, optimizing routes for energy efficiency, and managing reverse logistics for returns and recycling. Pickers contribute to green initiatives by implementing sustainable practices, reducing waste, and improving the overall ecological footprint of warehouse operations.
Pros & Cons of Being a Warehouse Picker
Making informed career decisions requires a clear understanding of both the benefits and challenges associated with a particular path. A career as a warehouse picker, like any profession, offers a unique set of advantages and disadvantages. These experiences can vary significantly based on the specific company culture, the size and type of warehouse, and the individual's personal preferences and physical capabilities. Moreover, the nature of the work might evolve at different career stages, with early experiences potentially differing from those of more seasoned pickers. What one person considers a pro, another might view as a con, highlighting the subjective nature of career satisfaction. This assessment provides an honest, balanced perspective to help you set realistic expectations for this role.
Pros
- Entry into the workforce is relatively easy, as the role typically requires minimal formal education or prior experience, making it accessible for many job seekers.
- Physical activity is a core component of the job, providing a consistent workout during shifts, which can be beneficial for maintaining physical fitness.
- The work environment often fosters a sense of teamwork and camaraderie, as pickers frequently work closely with colleagues to meet daily targets and support each other.
- There is a clear and immediate sense of accomplishment each day as you directly contribute to fulfilling orders and ensuring products reach customers, providing tangible results for your efforts.
- Opportunities for overtime hours are frequently available, especially during peak seasons, allowing pickers to earn additional income.
- The skills learned, such as inventory management, efficient movement, and familiarity with warehouse operations, are transferable to other logistics or supply chain roles.
- Many companies offer basic benefits packages, including health insurance and paid time off, even for entry-level warehouse positions, providing a foundation of support.
Cons
- The work is highly repetitive, involving the same motions and tasks for extended periods, which can lead to monotony and mental fatigue over time.
- Physical strain is a constant factor due to lifting, bending, stretching, and walking for an entire shift, often leading to muscle soreness or chronic pain in the back, shoulders, or feet.
- The pay rate for warehouse pickers is often entry-level, offering limited opportunities for significant wage increases without moving into supervisory or specialized roles.
- Working conditions can be challenging, including exposure to varying temperatures (hot in summer, cold in winter), dust, noise from machinery, and the constant movement of forklifts.
- Job security can be volatile, as demand for pickers often fluctuates with economic cycles and consumer spending, and the role is increasingly susceptible to automation.
- There is often intense pressure to meet strict quotas and performance metrics, which can create a stressful work environment and reduce opportunities for breaks or slower-paced work.
- Shift work, including nights, weekends, and holidays, is common in many warehouses, which can disrupt personal life and make it difficult to maintain a consistent social schedule or family routine.
Frequently Asked Questions
Warehouse Pickers face distinct challenges around physical demands, efficiency, and adapting to technology. This section addresses the most common questions about entering this role, from the daily work environment to career progression and job stability in a rapidly evolving logistics landscape.
What does a Warehouse Picker actually do on a day-to-day basis?
Daily tasks for a Warehouse Picker involve accurately locating and retrieving items from warehouse shelves based on order lists, often using handheld scanners or voice-picking systems. You will then transport these items to a packing or staging area. This role requires attention to detail, efficiency, and often involves walking long distances or operating equipment like pallet jacks.
What qualifications or experience do I need to become a Warehouse Picker?
Entry into a Warehouse Picker role typically does not require a specific degree. Most positions look for a high school diploma or equivalent. Employers prioritize a strong work ethic, physical stamina, attention to detail, and the ability to follow instructions. Some roles may require basic math skills or experience with warehouse equipment, which you can often learn on the job.
How physically demanding is the Warehouse Picker job, and what kind of lifting is involved?
The physical demands of a Warehouse Picker role are significant. You can expect to be on your feet for extended periods, walking many miles each shift, and frequently lifting, bending, and reaching. Some roles may involve lifting heavy items, potentially up to 50 pounds or more, repeatedly. It is important to be in good physical condition and prepared for a physically active job.
What is the typical starting salary for a Warehouse Picker, and how does it progress?
Starting salaries for Warehouse Pickers typically range from $15 to $20 per hour, depending on location, company size, and specific responsibilities. With experience, you can expect to earn more, especially if you gain certifications for operating specialized equipment like forklifts. Overtime opportunities are often available, which can significantly boost your earnings.
What are the career growth opportunities for a Warehouse Picker?
Career growth for a Warehouse Picker often involves moving into more specialized roles like equipment operator, inventory control specialist, or team lead. With further experience and potentially some additional training or certifications, you could advance to a warehouse supervisor or manager position. Many companies also offer internal training programs to help employees develop new skills and advance.
Is the Warehouse Picker role secure, or is it at high risk from automation?
Job security for Warehouse Pickers is generally stable due to the ongoing growth of e-commerce and logistics industries. While automation is increasing in warehouses, human pickers remain essential for complex orders and specialized items. The demand for efficient order fulfillment continues to rise, ensuring a steady need for skilled picking staff.
What is the typical work schedule and work-life balance like for a Warehouse Picker?
Work-life balance as a Warehouse Picker can vary. Many warehouses operate 24/7, offering various shifts including nights, weekends, and holidays. While this provides flexibility for some, it can also mean irregular hours. Overtime is often available, which can affect your personal time but also provides extra income. It is important to confirm typical shift patterns with potential employers.
Related Careers
Explore similar roles that might align with your interests and skills:
Order Picker
A growing field with similar skill requirements and career progression opportunities.
Explore career guideOrder Selector
A growing field with similar skill requirements and career progression opportunities.
Explore career guidePicker
A growing field with similar skill requirements and career progression opportunities.
Explore career guideWarehouse Associate
A growing field with similar skill requirements and career progression opportunities.
Explore career guideWarehouse Selector
A growing field with similar skill requirements and career progression opportunities.
Explore career guideAssess your Warehouse Picker readiness
Understanding where you stand today is the first step toward your career goals. Our Career Coach helps identify skill gaps and create personalized plans.
Skills Gap Analysis
Get a detailed assessment of your current skills versus Warehouse Picker requirements. Our AI Career Coach identifies specific areas for improvement with personalized recommendations.
See your skills gapCareer Readiness Assessment
Evaluate your overall readiness for Warehouse Picker roles with our AI Career Coach. Receive personalized recommendations for education, projects, and experience to boost your competitiveness.
Assess your readinessSimple pricing, powerful features
Upgrade to Himalayas Plus and turbocharge your job search.
Himalayas
Himalayas Plus
Himalayas Max
Find your dream job
Sign up now and join over 100,000 remote workers who receive personalized job alerts, curated job matches, and more for free!
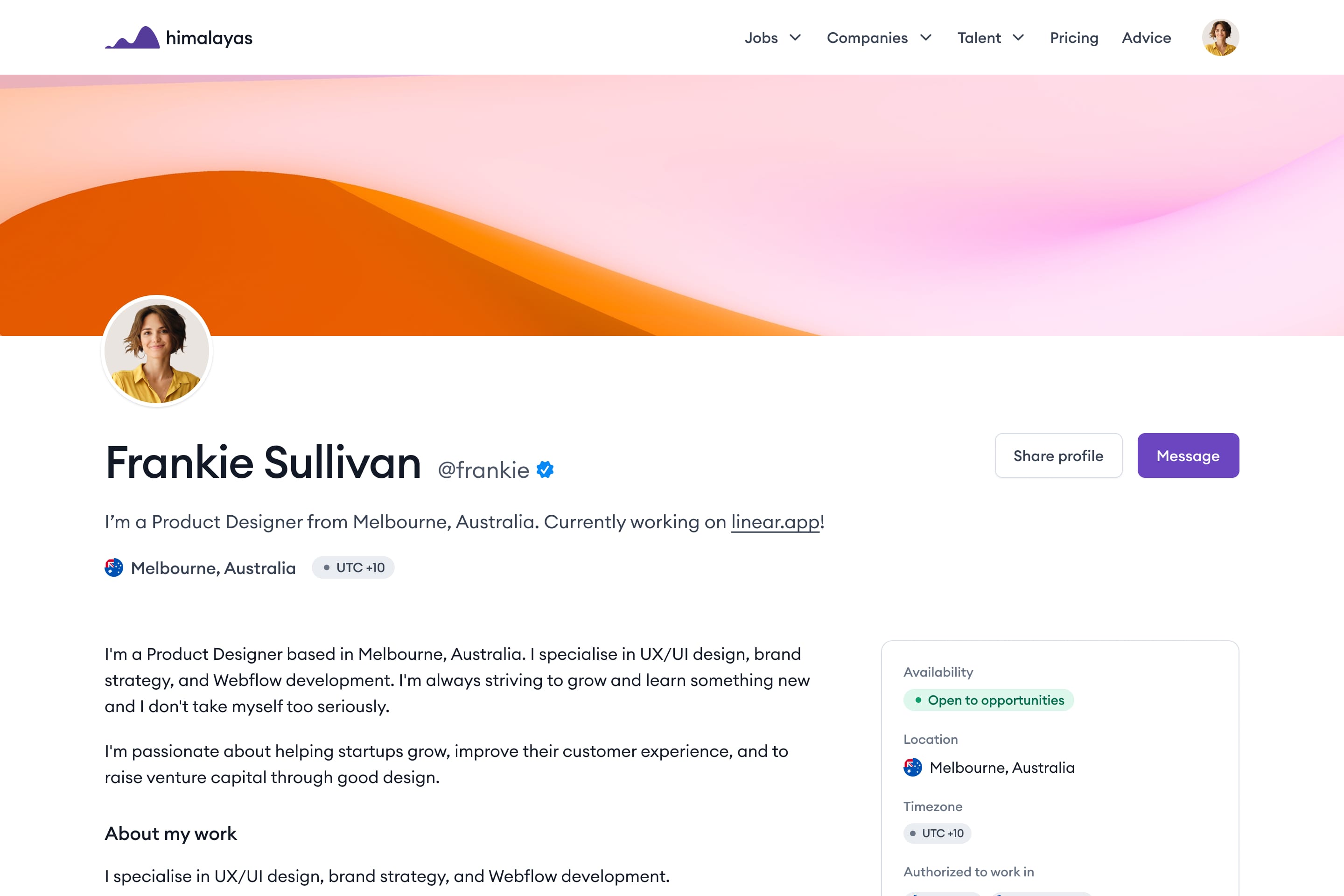