Complete Order Picker Career Guide
Order pickers are the crucial backbone of modern supply chains, meticulously retrieving products from warehouse shelves to fulfill customer orders with speed and accuracy. This role ensures everything from e-commerce packages to retail store shipments arrive correctly, directly impacting customer satisfaction and business efficiency. It's a physically active and detail-oriented position vital to the flow of goods in a rapidly evolving logistics landscape.
Key Facts & Statistics
Median Salary
$37,010 USD
(U.S. national median, BLS, May 2023)
Range: $29k - $49k+ USD (BLS, May 2023)
Growth Outlook
3%
(as fast as average) (BLS, 2022-2032)
Annual Openings
Top Industries
Typical Education
High school diploma or equivalent; on-the-job training is common
What is an Order Picker?
An Order Picker is a logistics professional responsible for accurately locating and retrieving specific products from warehouse inventory to fulfill customer or store orders. This role serves as a critical link in the supply chain, directly impacting delivery speed and customer satisfaction by ensuring the correct items are pulled and prepared for shipment. They navigate large storage facilities, often using technology to guide their path and verify selections.
Unlike a general warehouse associate who might handle various tasks like receiving or loading, an Order Picker specializes specifically in the precise selection and consolidation of goods according to unique order requirements. They are distinct from Inventory Clerks, who focus solely on record-keeping and stock accuracy, as Order Pickers are hands-on in the physical movement of products. Their primary goal is to ensure that every order leaves the warehouse with the right items, in the right quantity, and in good condition.
What does an Order Picker do?
Key Responsibilities
- Locate and retrieve specific products from warehouse shelves or storage areas using picking lists or scanners.
- Operate forklifts, pallet jacks, or other material handling equipment to transport items safely and efficiently.
- Verify product accuracy, quantity, and quality against order specifications before packaging.
- Scan items into inventory systems to maintain accurate stock records and track order progress.
- Package picked items securely for shipment, ensuring proper labeling and documentation.
- Report any damaged goods, inventory discrepancies, or equipment malfunctions to supervisors.
- Perform routine safety checks on equipment and maintain a clean and organized work area to prevent accidents and optimize workflow.
Work Environment
Order pickers typically work in large warehouses, distribution centers, or retail backrooms. The environment can be expansive, often with varying temperatures, especially in facilities handling perishable goods. The work is physically demanding, involving frequent walking, standing, bending, lifting, and repetitive motions. Collaboration with other warehouse staff, including packers, shippers, and inventory control teams, is common. Schedules often involve shifts, including nights, weekends, and holidays, particularly in busy seasons. The pace is generally fast, driven by order volume and delivery deadlines, requiring efficiency and attention to detail.
Tools & Technologies
Order pickers primarily use handheld barcode scanners or voice-picking systems for efficient item location and tracking. They also operate various material handling equipment, such as electric pallet jacks, reach trucks, and forklifts, requiring proper certification and safety training. Warehouse management systems (WMS) guide their workflow, indicating item locations and quantities. Additionally, they use basic packaging tools like tape dispensers, shrink wrap machines, and label printers to prepare orders for shipment. Some roles may involve using radio frequency identification (RFID) readers for advanced inventory management.
Order Picker Skills & Qualifications
Qualifications for an Order Picker primarily revolve around efficiency, accuracy, and reliability within a warehouse or distribution center environment. While formal education is rarely a primary requirement, practical experience and a strong work ethic are highly valued. Requirements vary significantly by company size, the type of goods handled, and the level of automation present.
For entry-level Order Picker positions, employers typically prioritize physical fitness, attention to detail, and the ability to follow instructions precisely. As individuals gain experience, opportunities may arise for roles involving more complex equipment, inventory management systems, or even supervisory duties. Certifications in forklift operation or other material handling equipment significantly enhance an Order Picker's value, especially in warehouses dealing with large or heavy items.
The skill landscape for Order Pickers is evolving with increasing automation. While manual picking remains common, knowledge of warehouse management systems (WMS) and handheld scanning devices is becoming essential. Employers are looking for candidates who can adapt to new technologies and maintain high productivity. Balancing speed with accuracy is a constant challenge and a key differentiator for successful Order Pickers.
Education Requirements
Technical Skills
- Warehouse Management Systems (WMS) Navigation: Ability to use software for locating items, confirming picks, and updating inventory.
- Handheld Scanner Operation: Proficiency in using barcode scanners for accurate item identification and tracking.
- Pallet Jack Operation: Skill in safely operating manual or electric pallet jacks for moving goods.
- Forklift Operation: (If certified) Safe and efficient use of various forklift types for accessing higher shelves or moving heavy loads.
- Inventory Control Principles: Understanding of basic stock rotation (FIFO/LIFO) and inventory accuracy practices.
- Basic Math Skills: Ability to count items accurately and perform simple calculations for order verification.
- Safety Procedures Adherence: Knowledge and strict compliance with warehouse safety rules, including lifting techniques and equipment safety.
- Order Picking Methodologies: Familiarity with common picking methods like batch picking, zone picking, or wave picking.
Soft Skills
- Attention to Detail: Crucial for correctly identifying items, quantities, and ensuring order accuracy, minimizing errors and returns.
- Time Management: Essential for meeting picking quotas and ensuring orders are ready for shipment within tight deadlines.
- Reliability and Punctuality: Companies depend on Order Pickers to be present and on time to maintain operational flow and meet daily targets.
- Physical Stamina: The role often involves prolonged standing, walking, lifting, and bending, requiring good physical endurance.
- Adaptability: Necessary for adjusting to changing priorities, new picking technologies, or different warehouse layouts and product types.
- Following Instructions: Strict adherence to safety protocols, picking procedures, and warehouse rules is paramount for efficiency and safety.
How to Become an Order Picker
Entering the order picker field typically follows a direct and practical pathway, often bypassing the need for extensive formal education. Many individuals secure their first role within weeks to a few months, depending on local demand and their availability. Companies prioritize reliability, a strong work ethic, and the ability to follow instructions accurately over academic credentials.
While traditional routes involve applying directly to warehouses, distribution centers, or retail logistics operations, non-traditional entry can include temp agencies specializing in logistics or even direct hiring events. Geographic location significantly influences opportunities; major metropolitan areas with high consumer demand and robust logistics infrastructure will have more consistent openings than smaller, rural markets. Larger corporations often have more structured hiring processes, while smaller businesses or third-party logistics providers might offer quicker entry.
Misconceptions about this field include the belief that it requires heavy lifting or advanced technical skills. While some roles involve physical activity, many utilize modern equipment for lighter tasks, and the primary technical skill is often basic scanner operation. The hiring landscape values efficiency and attention to detail, making it accessible to a wide range of candidates. Building a network often means connecting with current employees or supervisors during the application process, rather than formal networking events.
Step 1
Step 2
Step 3
Step 4
Step 5
Step 6
Step 7
Education & Training Needed to Become an Order Picker
Becoming an Order Picker primarily focuses on practical skills and on-the-job training rather than formal academic degrees. Most employers value efficiency, attention to detail, and a strong work ethic over university credentials. A high school diploma or GED is often the only educational prerequisite. This contrasts sharply with roles requiring extensive theoretical knowledge.
Alternative learning paths, such as vocational training or certifications in warehouse operations, can enhance a candidate's appeal. These programs, which typically cost between $500 and $2,000, can be completed in a few weeks to a few months. They cover topics like inventory management software, safety protocols, and efficient picking techniques. While not strictly required, they demonstrate a proactive approach to the role and can lead to higher starting wages or faster advancement within a warehouse environment.
Continuous learning for an Order Picker involves staying updated on new warehouse technologies, such as automated picking systems or advanced inventory tracking software. Employers often provide this training internally. The cost-benefit analysis for an Order Picker's education heavily favors short-term, practical training over lengthy, expensive degrees. Investing in a four-year degree for this role would be an inefficient use of time and money, as employers prioritize direct experience and a proven ability to perform the job's physical and logistical demands.
Order Picker Salary & Outlook
Compensation for an Order Picker varies significantly based on several factors beyond just base hourly wages. Geographic location plays a crucial role, with higher cost-of-living areas, particularly major metropolitan centers or regions with high demand for logistics, offering more competitive pay. Conversely, rural or less economically robust areas typically have lower pay scales.
Experience levels directly impact earning potential; entry-level order pickers start at foundational rates, while those with several years of experience, proven efficiency, and specialized skills in operating equipment like forklifts or using advanced inventory systems can command higher wages. Specialization in handling specific types of goods, such as fragile items or cold storage products, can also lead to better compensation. Total compensation packages often extend beyond hourly pay to include overtime opportunities, performance-based bonuses, and sometimes even shift differentials for undesirable hours.
Company size and industry sector also influence pay; larger logistics firms or e-commerce giants often provide more comprehensive benefits, including health insurance, retirement contributions like 401(k) plans, and paid time off, which add substantial value to the overall package. Remote work options are not applicable to this role, as it is inherently on-site. However, the ability to negotiate pay can improve with certifications for equipment operation or a demonstrated history of high productivity and accuracy. International markets will have their own distinct wage structures, so the provided figures are specifically calibrated for the United States dollar (USD) context.
Salary by Experience Level
Level | US Median | US Average |
---|---|---|
Order Picker | $36k USD | $38k USD |
Senior Order Picker | $43k USD | $45k USD |
Lead Order Picker | $50k USD | $52k USD |
Warehouse Supervisor | $62k USD | $65k USD |
Market Commentary
The job market for Order Pickers remains robust, driven by the continued growth of e-commerce and the increasing complexity of global supply chains. Demand for efficient order fulfillment has surged, creating a steady need for skilled individuals in warehousing and distribution centers. The U.S. Bureau of Labor Statistics projects employment of material moving machine operators, which includes order pickers, to grow 6 percent from 2022 to 2032, about as fast as the average for all occupations. This translates to about 68,200 new jobs over the decade, indicating consistent opportunity.
Emerging technologies like warehouse automation and robotics are impacting the role, but not necessarily diminishing demand. Instead, these technologies are transforming the role to require more interaction with automated systems, data input, and problem-solving, rather than purely manual tasks. This shift creates opportunities for order pickers to upskill into roles that involve operating and monitoring automated equipment, enhancing their long-term career viability. While some tasks may be automated, the need for human oversight and intervention, particularly for complex or varied orders, ensures continued relevance.
Geographic hotspots for order picker roles include major logistics hubs near ports, large consumer markets, and intermodal transportation centers. The profession is generally recession-resistant, as consumer demand for goods, even during economic downturns, still requires efficient distribution. Future-proofing involves continuous learning of new warehouse technologies and developing strong problem-solving skills, which will be critical as the industry evolves.
Order Picker Career Path
Career progression for an Order Picker typically involves advancing through increased responsibility, efficiency, and leadership within warehouse operations. This path often distinguishes between individual contributor (IC) growth, focusing on specialized skills and productivity, and management tracks, which involve overseeing teams and broader logistical processes.
Advancement speed depends on several factors: individual performance metrics like pick accuracy and speed, consistent adherence to safety protocols, and a willingness to learn new equipment or processes. Company size and the specific industry (e.g., e-commerce, manufacturing, retail distribution) also influence opportunities, with larger companies often having more defined hierarchical paths. Specialization in areas like hazardous materials handling or operating specific machinery can also accelerate progression.
Lateral movement might involve transitioning to roles like Inventory Clerk, Shipping/Receiving Coordinator, or Forklift Operator, which build on foundational warehouse knowledge. Continuous learning, such as obtaining equipment certifications, and building a reputation for reliability and attention to detail are crucial. Networking within the warehouse team and with supervisors can also open doors to new opportunities or mentorship that aids in career development.
Order Picker
0-2 yearsKey Focus Areas
Senior Order Picker
2-4 yearsKey Focus Areas
Lead Order Picker
4-7 yearsKey Focus Areas
Warehouse Supervisor
7+ years total experienceKey Focus Areas
Order Picker
0-2 yearsAn Order Picker is responsible for accurately and efficiently locating and retrieving items from warehouse shelves based on customer orders. This role involves basic use of scanning equipment and manual handling of goods. They operate under direct supervision, focusing on completing assigned tasks with precision and meeting daily quotas.
Key Focus Areas
Priorities include mastering inventory location systems, improving pick accuracy, and increasing picking speed. Understanding various product types and packaging requirements is essential. Developing strong teamwork and communication skills with colleagues and supervisors is also important.
Senior Order Picker
2-4 yearsA Senior Order Picker consistently demonstrates high levels of accuracy and efficiency, often handling more complex or priority orders. They operate with greater autonomy and may be cross-trained on multiple warehouse zones or product categories. They provide informal guidance to new team members and maintain a high standard for safety and productivity.
Key Focus Areas
Developing expertise in complex picking routes, understanding the flow of goods, and identifying inefficiencies in the picking process. Training on specialized equipment like forklifts or pallet jacks, and obtaining necessary certifications, becomes a key development area. Mentoring new team members on best practices and safety is also important.
Lead Order Picker
4-7 yearsA Lead Order Picker oversees a small team of order pickers, assigning tasks, monitoring performance, and ensuring daily targets are met. They act as a primary point of contact for operational issues, troubleshooting discrepancies and assisting with training. This role involves making real-time decisions to maintain workflow efficiency and ensure team adherence to safety and quality standards.
Key Focus Areas
Key areas include developing strong leadership and communication skills, understanding scheduling and resource allocation, and problem-solving operational bottlenecks. Training in inventory management software and basic reporting is beneficial. Building a foundational understanding of lean warehouse principles to optimize workflows is also critical.
Warehouse Supervisor
7+ years total experienceA Warehouse Supervisor manages a section or shift of the warehouse, overseeing all aspects of picking, packing, shipping, and receiving operations. They are responsible for staff scheduling, performance reviews, and maintaining a safe and productive work environment. This role involves analyzing operational data, implementing process improvements, and ensuring compliance with company policies and regulatory requirements.
Key Focus Areas
Focus shifts to strategic planning, performance management, and continuous improvement initiatives. Developing skills in budgeting, human resource management (hiring, training, disciplinary actions), and advanced logistics software is essential. Understanding supply chain dynamics and implementing new technologies to enhance warehouse efficiency are also critical areas of development.
Job Application Toolkit
Ace your application with our purpose-built resources:
Global Order Picker Opportunities
Order picking is a globally essential role, fundamental to logistics and supply chains in nearly every country. International demand remains stable, driven by e-commerce expansion and efficient inventory management needs as of 2025. This profession translates across borders with universal operational principles, though warehouse technologies and safety regulations vary by region. Cultural differences impact workplace communication and efficiency. Professionals consider international opportunities for better wages, living conditions, or skill development in advanced logistics hubs. No specific international certifications exist, but experience with diverse inventory systems proves beneficial.
Global Salaries
Order picker salaries vary significantly by region and cost of living. In North America, specifically the United States, an order picker can expect to earn between $30,000 and $45,000 USD annually. Canadian salaries are comparable, ranging from CAD 35,000 to CAD 50,000. These figures reflect a higher purchasing power in North America compared to many other regions, though housing costs are often higher.
In Europe, wages differ widely. A picker in Germany might earn €25,000 to €35,000 (approx. $27,000-$38,000 USD), while in Poland, the range is typically PLN 30,000 to PLN 45,000 (approx. $7,500-$11,000 USD). Western European countries generally offer better benefits like paid vacation and robust healthcare, offsetting some wage differences. Eastern European nations offer lower wages but also much lower living costs.
Asia-Pacific regions present diverse pay scales. In Australia, an order picker earns AUD 45,000 to AUD 55,000 (approx. $30,000-$37,000 USD). In contrast, a picker in India might earn INR 150,000 to INR 250,000 (approx. $1,800-$3,000 USD). These figures are adjusted for local purchasing power. Latin America sees lower nominal wages; for instance, in Mexico, a picker might earn MXN 70,000 to MXN 100,000 (approx. $4,000-$6,000 USD). Experience directly influences compensation globally, with specialized skills like operating complex machinery leading to higher pay. Tax implications also vary, impacting take-home pay differently in each country.
Remote Work
Order picking is an inherently physical role, making international remote work or digital nomad opportunities impossible for the core job function. The work requires on-site presence within a warehouse or distribution center to physically handle goods. Therefore, discussions about time zones, international team collaboration, or digital nomad visas are not applicable to this specific profession.
However, some administrative or supervisory roles within logistics operations might offer remote components. These are distinct from the order picker role itself. For the order picker, equipment requirements involve safety gear and warehouse tools, all provided on-site. Internet access is not relevant to the job's execution. Companies hiring order pickers internationally focus on local labor markets, not remote talent pools.
Visa & Immigration
For order pickers, common visa categories include skilled worker visas, though this role often falls under general labor or seasonal worker schemes rather than highly skilled programs. Popular destination countries like Canada, Australia, and parts of Europe (e.g., Germany, Netherlands) may offer pathways for this occupation, often linked to labor shortages in logistics as of 2025.
Requirements typically involve a job offer from a local employer and meeting basic educational or experience thresholds, usually not requiring specific degrees. Credential recognition is generally straightforward, focusing on practical experience over formal licensing. Visa timelines vary, from a few weeks for seasonal work permits to several months for more structured skilled worker programs. Language requirements are minimal for many positions, though basic communication skills are essential.
Pathways to permanent residency are limited for this specific role in most countries, often requiring progression into supervisory or more specialized logistics positions. Family visas for dependents depend on the primary applicant's visa type and duration. It is crucial to verify specific country requirements, as immigration policies for general labor can change frequently based on economic needs.
2025 Market Reality for Order Pickers
Understanding current market conditions for order pickers is vital for career success. The logistics and e-commerce landscape has transformed significantly from 2023 to 2025, influenced by post-pandemic shifts and the accelerating adoption of automation and AI in warehouses.
Broader economic factors, such as consumer spending habits and supply chain stability, directly impact the volume of goods needing picking and distribution. Market realities for order pickers vary by experience level, with entry-level roles facing more competition, and by geographic region, as major distribution centers offer more opportunities. Company size also matters, with larger corporations often having more advanced technological infrastructures. This analysis provides an honest assessment of these realities.
Current Challenges
Order pickers face increased competition, especially for entry-level roles, as automation continues to refine warehouse operations. Economic shifts can lead to fluctuating demand, impacting job security. Some employers also seek candidates with basic tech literacy for handheld scanning devices, creating a small skill gap for those unfamiliar.
Job searches might take longer than expected due to the high volume of applicants for each opening.
Growth Opportunities
Despite automation, strong demand persists for order pickers in specialized segments like cold storage logistics and hazardous materials handling, where human oversight is still critical. Opportunities also emerge in micro-fulfillment centers, which require quick, localized picking for rapid delivery.
Professionals can gain an advantage by mastering modern warehouse technologies, such as advanced scanning equipment and inventory management software. Certifications in forklift operation or hazardous material handling create competitive advantages. Underserved markets might exist in less populated industrial zones seeking to establish new distribution hubs.
Strategic career moves include focusing on companies investing in hybrid automation models, where human pickers collaborate with robots. These roles often require problem-solving skills beyond simple picking. The ongoing growth of e-commerce means sectors like online grocery and specialized retail continue to offer robust opportunities. Timing educational investments in logistics technology or equipment operation can significantly enhance long-term prospects.
Current Market Trends
Hiring for order pickers remains consistent, driven by the ongoing expansion of e-commerce and logistics. Demand for efficient inventory movement is strong, but the nature of the work is evolving. Warehouses are increasingly integrating automation, including robotic picking systems and advanced conveyor belts, which reshapes human roles.
Economic conditions, while stable, emphasize cost efficiency in supply chains. This pressure means employers seek highly productive order pickers. Technology trends, particularly improved warehouse management systems (WMS) and handheld scanners, are now standard tools. Order pickers must use these devices effectively, tracking inventory and optimizing routes.
Employer requirements now often include basic digital literacy alongside physical stamina. Employers prioritize speed and accuracy, with performance metrics closely monitored. Salary trends show modest growth, but the market is becoming more saturated at the entry level, particularly in urban logistics hubs. Remote work is not applicable here, as order picking is a physical, on-site role.
Seasonal hiring spikes, especially during holiday periods, remain a significant pattern, offering temporary and often pathways to permanent roles.
Emerging Specializations
The role of an order picker is evolving rapidly, driven by advancements in automation, data analytics, and supply chain optimization. Understanding these shifts creates new specialization opportunities, allowing professionals to transition from traditional manual tasks to more technologically integrated roles. Early positioning in these emerging areas can significantly enhance career trajectories and earning potential from 2025 onwards.
Specializing in cutting-edge areas often leads to premium compensation and accelerated career growth compared to established paths. While foundational skills remain important, embracing new technologies and methodologies within order picking can unlock next-generation opportunities. This strategic choice balances the risk of early adoption with the reward of becoming an expert in a high-demand, undersupplied niche.
Many emerging specializations begin as niche roles but quickly become mainstream as technology matures and industry adoption increases. Professionals who acquire relevant skills now will be well-prepared when these roles become standard. Investing in these areas helps individuals future-proof their careers and secure a competitive advantage in the evolving logistics and warehousing sector.
Choosing an emerging specialization means anticipating future needs and developing skills that will be critical for tomorrow's operations. This proactive approach ensures relevance and opens doors to leadership positions in technologically advanced environments. The timeline for these areas to generate significant job opportunities is relatively short, often within two to five years, making early investment in skills a wise career decision.
Automated Picking System Operator
Picking Process Data Analyst
Specialized Order Quality Controller
Picking Technology Trainer
Picking Equipment Maintenance Technician
Pros & Cons of Being an Order Picker
Choosing a career path requires a clear understanding of both its appealing aspects and its inherent difficulties. The experience in any career, including an Order Picker, varies significantly based on the employer, the specific industry sector, the level of automation in the warehouse, and an individual's personal preferences and physical capabilities. What one person considers a benefit, another might see as a drawback. For example, a fast-paced environment can be exciting for some but stressful for others. Furthermore, the daily realities and challenges can shift as a career progresses from entry-level to more experienced roles. This assessment aims to provide an honest, balanced perspective on the advantages and challenges of being an Order Picker, helping prospective candidates set realistic expectations.
Pros
Order picker roles typically have low barriers to entry, often requiring no specific degree or extensive prior experience, making them accessible to a wide range of job seekers.
There is consistent demand for order pickers across various industries, including retail, e-commerce, manufacturing, and logistics, providing strong job security.
Many companies offer on-the-job training for new order pickers, allowing individuals to quickly learn necessary skills and become productive without upfront educational costs.
The work environment is often structured and predictable, with clear tasks and routines, which can be appealing for individuals who prefer consistent daily activities.
Order picking provides a good opportunity to stay physically active throughout the workday, as it involves continuous movement, walking, and lifting, which can be a benefit for some.
Some companies offer performance incentives or bonuses for meeting or exceeding productivity targets, providing an opportunity to earn more based on individual effort.
The role offers a sense of accomplishment at the end of each shift, as you can see the direct results of your work in preparing orders for shipment.
Cons
The work is highly repetitive, involving the same motions and tasks for extended periods, which can lead to monotony and boredom over time.
Order pickers often face intense pressure to meet strict quotas and productivity targets, leading to a fast-paced and sometimes stressful environment, especially during peak seasons.
The role typically offers limited opportunities for career advancement within the warehouse, with progression often requiring additional training or moving into supervisory roles.
Many order picker positions involve working non-traditional hours, including early mornings, late nights, weekends, and holidays, which can impact work-life balance and social life.
The job can be physically demanding, requiring prolonged standing, walking, lifting, bending, and carrying heavy items, which increases the risk of fatigue and musculoskeletal injuries.
Working conditions can be challenging, as warehouses may be unheated or uncooled, dusty, noisy, or require working in cold storage, depending on the products handled.
The pay for order picking positions is often at the lower end of the wage scale, with limited potential for significant salary increases without moving into other roles.
Frequently Asked Questions
Order Pickers face distinct challenges around physical demands, efficiency, and accuracy within a fast-paced warehouse environment. This section addresses the most common questions about entering this role, from training and physical requirements to career progression and work-life balance.
What are the basic qualifications and education needed to become an Order Picker?
Entry-level Order Picker roles typically do not require specific academic qualifications. Employers usually look for a high school diploma or equivalent, basic literacy and numeracy skills, and a strong work ethic. Some roles might prefer previous warehouse or manual labor experience, but many companies offer on-the-job training for new hires.
How long does it take to get proficient as an Order Picker, and what does the training involve?
Most new Order Pickers can become proficient within a few weeks to a couple of months, depending on the complexity of the warehouse system and the products. Initial training covers safety protocols, equipment operation like pallet jacks, and the specific software or scanning devices used for picking. Consistent practice and attention to detail are key to increasing speed and accuracy.
What is the typical work schedule and how does it affect work-life balance for an Order Picker?
The work-life balance for an Order Picker can vary significantly based on the employer and industry. Many warehouses operate 24/7, offering various shifts including nights, weekends, and holidays, especially during peak seasons. While some roles offer consistent daytime hours, be prepared for potential shift work or overtime, which can impact personal scheduling.
What are the physical demands of an Order Picker role?
Order Picking is physically demanding, involving standing for long periods, walking several miles daily, bending, lifting, and carrying items ranging from light to moderately heavy. You should be able to lift at least 30-50 pounds regularly. Good stamina, spatial awareness, and hand-eye coordination are important to perform tasks efficiently and safely.
Is the Order Picker role secure, or is it at risk from automation?
The job market for Order Pickers is generally stable, driven by the growth of e-commerce and logistics. While automation is increasing in warehouses, human Order Pickers remain crucial for complex or varied tasks. Job security depends on the company's stability and the local demand for warehouse labor, but the skills are transferable across many industries.
What are the common career advancement opportunities for an Order Picker?
Career growth paths for Order Pickers often lead to roles such as Lead Order Picker, Team Leader, Inventory Clerk, or Warehouse Associate. With additional training and experience, you could advance to Forklift Operator, Shipping and Receiving Clerk, or even Warehouse Supervisor. Many companies encourage internal promotion and provide opportunities for skill development.
What are the salary expectations for an Order Picker, and how does it vary?
Order Pickers typically earn an hourly wage, which can vary based on location, company, and experience. Entry-level wages are often around minimum wage or slightly above, with potential for increases based on performance, tenure, and shift differentials for nights or weekends. Overtime can significantly boost earnings, especially during busy periods like holidays.
Can Order Pickers work remotely, or is it always an on-site role?
Many Order Picker positions are on-site in warehouses or distribution centers. Remote work is not feasible for this role due to the hands-on nature of picking and packing physical goods. Location flexibility is limited to finding employment in areas with high concentrations of warehouses, which are typically near major transportation hubs or industrial zones.
Related Careers
Explore similar roles that might align with your interests and skills:
Order Filler
A growing field with similar skill requirements and career progression opportunities.
Explore career guideOrder Puller
A growing field with similar skill requirements and career progression opportunities.
Explore career guideOrder Selector
A growing field with similar skill requirements and career progression opportunities.
Explore career guidePicker
A growing field with similar skill requirements and career progression opportunities.
Explore career guideWarehouse Picker
A growing field with similar skill requirements and career progression opportunities.
Explore career guideAssess your Order Picker readiness
Understanding where you stand today is the first step toward your career goals. Our Career Coach helps identify skill gaps and create personalized plans.
Skills Gap Analysis
Get a detailed assessment of your current skills versus Order Picker requirements. Our AI Career Coach identifies specific areas for improvement with personalized recommendations.
See your skills gapCareer Readiness Assessment
Evaluate your overall readiness for Order Picker roles with our AI Career Coach. Receive personalized recommendations for education, projects, and experience to boost your competitiveness.
Assess your readinessSimple pricing, powerful features
Upgrade to Himalayas Plus and turbocharge your job search.
Himalayas
Himalayas Plus
Himalayas Max
Find your dream job
Sign up now and join over 100,000 remote workers who receive personalized job alerts, curated job matches, and more for free!
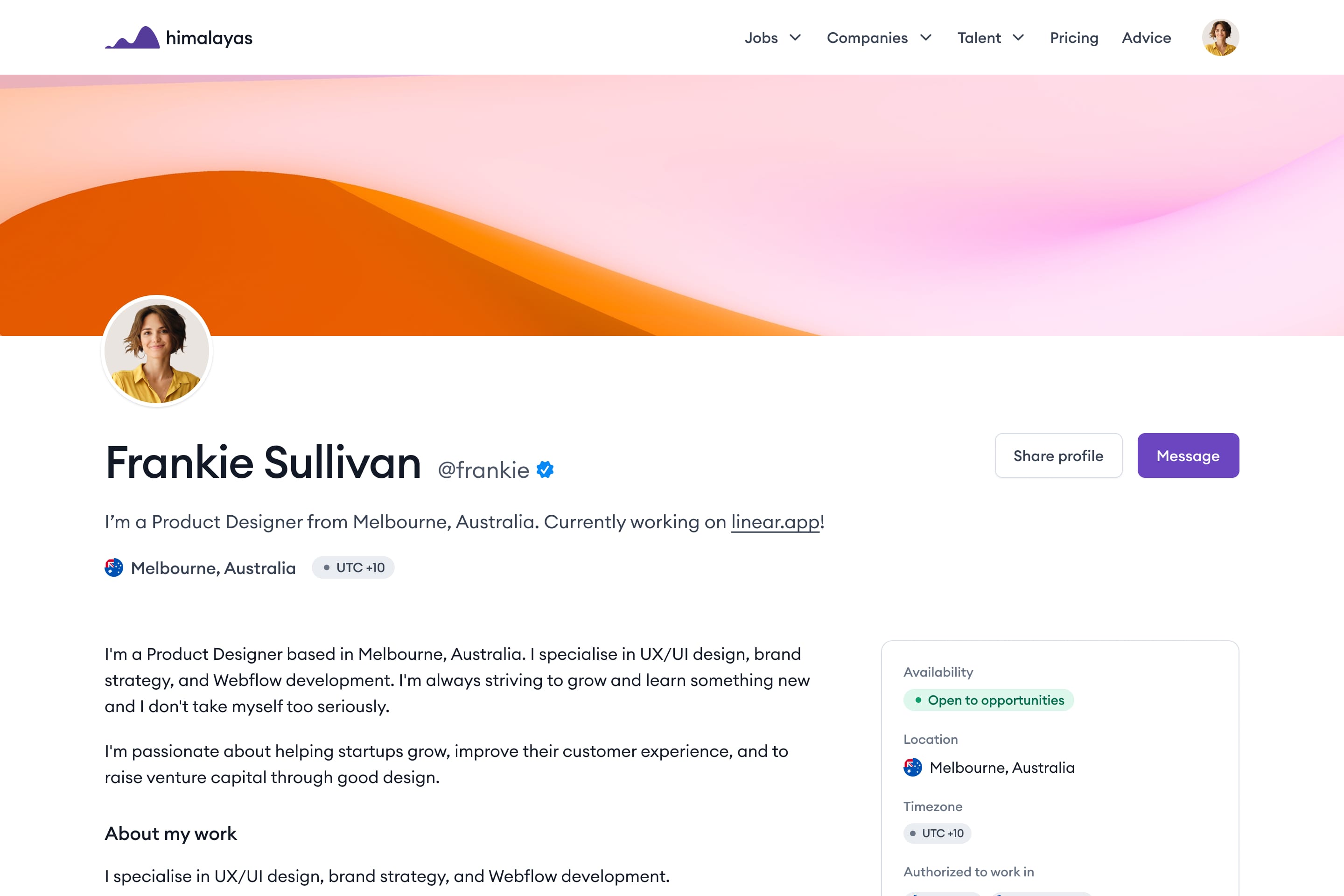