Complete Tool Crib Attendant Career Guide
Tool Crib Attendants play a vital role in industrial and manufacturing settings, ensuring that essential tools and equipment are organized, maintained, and readily available for technicians and production staff. This position is crucial for operational efficiency, minimizing downtime, and preventing costly losses, making you an indispensable part of any busy workshop or factory floor. It is a detail-oriented role that offers a direct impact on productivity and provides a clear pathway into broader supply chain or inventory management careers.
Key Facts & Statistics
Median Salary
$44,480 USD
(U.S. national median, May 2023, BLS)
Range: $30k - $60k+ USD
Growth Outlook
3%
as fast as average
Annual Openings
≈35,000
openings annually
Top Industries
Typical Education
High school diploma or equivalent; some positions prefer vocational training or experience in inventory management.
What is a Tool Crib Attendant?
A Tool Crib Attendant is a specialized inventory and logistics professional responsible for the organized storage, issuance, and maintenance of tools, equipment, and materials within an industrial or manufacturing setting. This role ensures that all necessary operational resources are readily available to production and maintenance teams, minimizing downtime and maximizing efficiency. They act as the central point of control for valuable assets, preventing loss and ensuring proper care.
Unlike a general warehouse associate who handles a wide variety of goods, a Tool Crib Attendant possesses specific knowledge of the tools and equipment used in their particular industry, understanding their function, maintenance needs, and proper handling. They are crucial for operational continuity, as their meticulous management directly impacts a facility's productivity and safety by ensuring the right tools are always on hand and in good working order.
What does a Tool Crib Attendant do?
Key Responsibilities
- Issue tools, equipment, and materials to production and maintenance personnel upon request, ensuring accurate record-keeping for each transaction.
- Receive, inspect, and organize incoming tools and supplies, verifying quantities against purchase orders and noting any discrepancies or damage.
- Maintain a clean, organized, and secure tool crib area, implementing efficient storage solutions for various items.
- Perform regular inventory counts and audits of tools and equipment, identifying low stock levels and initiating reorder requests.
- Conduct routine maintenance and calibration checks on tools, ensuring they are in good working condition before being issued.
- Track tool usage and return dates, following up with personnel to ensure timely returns and accountability.
- Repair minor tool damage or coordinate with maintenance staff for more complex repairs, keeping tools readily available.
Work Environment
Tool Crib Attendants typically work in industrial settings such as manufacturing plants, construction sites, or large maintenance facilities. The environment is often a dedicated storage area, which can be busy and noisy depending on the facility's operations. The role requires a fair amount of standing, walking, and lifting, as attendants handle various tools and parts. Collaboration is constant, as they interact frequently with mechanics, technicians, and production staff. The work schedule usually aligns with facility operating hours, which may include shifts outside of standard business hours, but the pace is generally steady rather than highly variable.
Tools & Technologies
A Tool Crib Attendant primarily uses inventory management software or systems to track tools, including barcode scanners for efficient check-in and check-out processes. They also work with basic hand tools for minor repairs and maintenance, and sometimes operate forklifts or pallet jacks for moving heavier equipment or bulk supplies. Communication tools like two-way radios or internal messaging systems are common for coordinating with shop floor personnel. They also utilize spreadsheets for manual tracking or reporting, and enterprise resource planning (ERP) systems for managing supply chain data.
Tool Crib Attendant Skills & Qualifications
A Tool Crib Attendant's qualifications primarily revolve around practical experience and meticulous organizational skills. Formal education requirements are typically minimal, with a high school diploma or GED often sufficient. Employers prioritize candidates who demonstrate a strong work ethic, attention to detail, and a foundational understanding of various tools and equipment.
Requirements for this role can vary based on the industry and the size of the operation. In large manufacturing plants or aerospace facilities, specific certifications related to safety, hazardous material handling, or specialized equipment operation might be mandatory. Smaller workshops or construction sites might place more emphasis on a candidate's general mechanical aptitude and ability to quickly learn new inventory systems. Geographic location can also influence requirements, with some regions having stricter safety regulations that necessitate additional training.
Practical experience in a warehouse, inventory management, or a related industrial setting often outweighs advanced degrees for this position. While a degree is not typically required, certifications in inventory control software or forklift operation significantly enhance a candidate's appeal. The skill landscape for Tool Crib Attendants is evolving with the increasing adoption of digital inventory systems and automated tracking, requiring a balance between traditional hands-on knowledge and proficiency with modern technology. Prioritizing strong organizational habits alongside basic computer literacy is crucial for success in this role.
Education Requirements
Technical Skills
- Inventory management software proficiency (e.g., SAP, Oracle E-Business Suite, custom CMMS)
- Forklift operation and safety protocols
- Hand tool identification and usage (wrenches, screwdrivers, pliers, hammers)
- Power tool identification and basic operation (drills, saws, grinders)
- Measuring tool proficiency (calipers, micrometers, tape measures)
- Basic computer literacy (Microsoft Office Suite, data entry)
- Barcode scanning and labeling systems operation
- Tool maintenance and minor repair knowledge
- Material handling equipment operation (pallet jacks, dollies)
- FIFO (First-In, First-Out) inventory principles
- Tool calibration awareness and record-keeping
- Personal Protective Equipment (PPE) knowledge and adherence
Soft Skills
- Attention to Detail: Essential for accurately tracking tools, identifying damage, and ensuring correct inventory levels, preventing costly errors.
- Organizational Skills: Critical for maintaining a tidy, efficient tool crib, ensuring tools are easily locatable, and managing inventory flow.
- Reliability and Punctuality: Tools are vital for operations; consistent presence and dependable work ethic ensure production schedules remain uninterrupted.
- Problem-Solving: Needed for troubleshooting missing tools, resolving inventory discrepancies, or finding suitable alternatives when specific tools are unavailable.
- Communication Skills: Important for interacting with technicians and other staff, understanding their tool needs, and providing clear instructions on tool usage or return procedures.
- Customer Service Orientation: Treating internal customers (technicians, engineers) with respect and efficiency, ensuring their needs are met quickly to minimize downtime.
- Adaptability: Adjusting to new inventory systems, tool types, or operational procedures as the facility's needs evolve.
- Safety Consciousness: Consistently adhering to safety protocols for tool handling, storage, and equipment operation to prevent accidents and maintain a safe work environment.
How to Become a Tool Crib Attendant
Becoming a Tool Crib Attendant typically involves practical experience and strong organizational skills rather than a specific degree. Many enter this field directly from high school, trade schools, or previous roles in manufacturing, construction, or logistics. Your entry strategy will vary based on your background; someone with warehouse experience might find a role faster than a complete beginner.
Geographic location and company size significantly impact entry routes. Larger manufacturing plants or construction companies in industrial hubs often have more structured hiring processes and may prefer candidates with some prior inventory management or tool handling experience. Smaller shops or local businesses might offer entry-level roles with on-the-job training, valuing reliability and a willingness to learn above all else.
A common misconception is that this role is purely manual; it increasingly involves digital inventory systems and basic data entry. While formal certifications are not always mandatory, demonstrating proficiency in inventory software or having a forklift certification can significantly boost your candidacy. Networking within local industrial parks or trade communities can also uncover opportunities not widely advertised, as many positions are filled through word-of-mouth.
Step 1
Step 2
Step 3
Step 4
Step 5
Step 6
Education & Training Needed to Become a Tool Crib Attendant
A Tool Crib Attendant's role focuses on managing, issuing, and maintaining tools and equipment within industrial or manufacturing settings. Formal university degrees are generally not required for this position. Instead, the educational ecosystem emphasizes practical skills, inventory management knowledge, and safety protocols.
Many Tool Crib Attendants learn through on-the-job training, often starting in entry-level roles within a warehouse or maintenance department. Vocational schools and community colleges offer programs in logistics, supply chain management, or industrial maintenance that can provide a strong foundation. These programs typically cost between $3,000 and $15,000 and take 6 to 18 months to complete, offering certificates or associate degrees. Online courses and self-study resources for inventory control, OSHA safety, and basic tool identification are also valuable, often costing under $500 and taking a few weeks to months.
Employers highly value practical experience and a strong understanding of inventory software. While a degree is not essential, a certificate in a related field can demonstrate commitment and foundational knowledge, potentially leading to faster advancement or higher starting wages. Continuous learning in areas like new tool technologies, advanced inventory systems, and safety regulations remains important for career progression. Practical experience often outweighs theoretical knowledge for this role, meaning hands-on training and apprenticeships are highly beneficial. Educational needs for a Tool Crib Attendant are quite specific, focusing on operational efficiency and meticulous record-keeping rather than broad academic disciplines.
Tool Crib Attendant Salary & Outlook
Compensation for a Tool Crib Attendant varies significantly based on several factors. Geographic location plays a crucial role; areas with a higher cost of living or strong manufacturing and industrial sectors often offer higher wages. Experience level, specialized knowledge of inventory systems, and proficiency with specific tools or equipment also directly impact earning potential.
Total compensation extends beyond base salary. Many positions include benefits packages such as health insurance, retirement contributions like 401(k) matching, and paid time off. Some companies, especially in manufacturing or logistics, may offer performance-based bonuses or overtime pay, which can substantially increase overall earnings.
Industry-specific trends also influence compensation. For example, a Tool Crib Attendant in aerospace manufacturing might earn more than one in general construction due to the precision and value of the inventory managed. Remote work is generally not applicable for this hands-on role, meaning location-based salaries are the norm. Understanding these components helps in salary negotiation and maximizing earning potential.
Salary by Experience Level
Level | US Median | US Average |
---|---|---|
Tool Crib Attendant | $42k USD | $45k USD |
Senior Tool Crib Attendant | $49k USD | $52k USD |
Tool Crib Supervisor | $57k USD | $60k USD |
Tool Crib Manager | $70k USD | $75k USD |
Market Commentary
The job market for Tool Crib Attendants remains stable, driven by the ongoing need for efficient inventory management in various industrial and manufacturing settings. Demand is consistent in sectors such as automotive, aerospace, construction, and general manufacturing, where precise control over tools and equipment is critical for operational efficiency and cost control.
Growth in this field is steady rather than explosive. Automation and advanced inventory software are influencing the role, shifting some responsibilities from manual tracking to system oversight. This creates opportunities for attendants proficient in digital inventory systems and data analysis.
While not a high-growth occupation, the role is relatively recession-resistant as industries always need to manage their assets. Geographic hotspots for Tool Crib Attendants align with major industrial and manufacturing hubs across the United States. Future-proofing this career involves continuous learning in inventory software, supply chain logistics, and potentially, basic maintenance of tools. The supply of qualified candidates generally meets demand, making specialized skills or experience with high-value tools particularly valuable.
Tool Crib Attendant Career Path
Career progression for a Tool Crib Attendant typically involves increasing responsibility for inventory management, equipment maintenance, and operational efficiency within a tool crib or storeroom environment. Advancement can follow either an individual contributor (IC) track, becoming a highly specialized attendant, or a management/leadership track, overseeing staff and operations.
Advancement speed depends on factors such as performance in maintaining accurate inventory, implementing efficient processes, and demonstrating strong organizational skills. Specialization in certain types of equipment, such as precision tools or heavy machinery components, can also accelerate progression. Company size and industry, whether manufacturing, aerospace, or construction, influence the complexity and scale of tool crib operations, impacting career paths.
Lateral movement opportunities exist within supply chain roles, moving into inventory control, purchasing, or even facilities management. Networking within the industry and actively seeking mentorship from experienced supervisors are crucial for identifying opportunities and gaining insights into best practices. Certifications in inventory management or safety protocols can mark significant professional development, opening doors to more advanced roles.
Tool Crib Attendant
0-2 yearsKey Focus Areas
Senior Tool Crib Attendant
2-5 yearsKey Focus Areas
Tool Crib Supervisor
5-8 yearsKey Focus Areas
Tool Crib Manager
8+ yearsKey Focus Areas
Tool Crib Attendant
0-2 yearsManages the check-in and check-out of tools and equipment, ensuring all items are accounted for and returned in good condition. Performs basic maintenance and cleaning of tools. Assists with organizing the tool crib and maintaining cleanliness. Reports damaged or missing tools to a supervisor. Interacts directly with technicians and other personnel to fulfill tool requests.
Key Focus Areas
Understanding tool identification systems, basic inventory software, and safety protocols for handling various tools. Develop strong organizational skills and attention to detail. Learn to maintain a clean and orderly tool crib environment. Focus on accurate data entry and following established procedures.
Senior Tool Crib Attendant
2-5 yearsOversees daily tool crib operations, including managing inventory levels, performing regular audits, and processing tool requests. Provides guidance to junior attendants and assists with training new staff. Identifies and troubleshoots common tool crib issues. Manages relationships with specific vendors for tool procurement and repair. Ensures compliance with safety regulations and company policies.
Key Focus Areas
Mastering advanced inventory management techniques, including cycle counting and discrepancy resolution. Developing strong communication skills for interacting with suppliers and internal departments. Learning minor tool repair and calibration. Begin mentoring new attendants and identifying areas for process improvement. Understand inventory optimization principles.
Tool Crib Supervisor
5-8 yearsDirects the activities of a team of Tool Crib Attendants, including scheduling, assigning tasks, and overseeing performance. Responsible for maintaining optimal inventory levels, reducing loss, and improving operational efficiency. Manages tool crib budget and coordinates with purchasing for new tool acquisitions. Implements and enforces safety procedures and company policies within the tool crib. Conducts regular inventory audits and prepares reports for management.
Key Focus Areas
Developing leadership and team management skills, including scheduling, performance feedback, and conflict resolution. Learning to analyze inventory data for trends and forecasting needs. Understanding procurement processes and budgeting for tool acquisition. Focus on implementing new technologies or systems to improve efficiency. Cultivate problem-solving and decision-making abilities.
Tool Crib Manager
8+ yearsManages all aspects of tool crib operations across multiple facilities or a large, complex organization. Develops and implements strategic plans for inventory control, tool procurement, and equipment maintenance. Oversees the budget for all tool cribs, ensuring cost-effectiveness and efficiency. Leads and mentors Tool Crib Supervisors, fostering professional development. Establishes key performance indicators (KPIs) and analyzes data to optimize operations. Ensures compliance with all regulatory standards and company policies.
Key Focus Areas
Developing strategic planning and resource allocation skills across multiple tool cribs or larger departments. Mastering advanced supply chain management principles and vendor negotiation. Leading cross-functional projects to integrate tool crib operations with broader organizational goals. Focus on continuous improvement methodologies and leveraging data analytics for strategic decision-making. Building strong relationships with senior leadership and external partners.
Job Application Toolkit
Ace your application with our purpose-built resources:
Tool Crib Attendant Resume Examples
Proven layouts and keywords hiring managers scan for.
View examplesTool Crib Attendant Cover Letter Examples
Personalizable templates that showcase your impact.
View examplesTop Tool Crib Attendant Interview Questions
Practice with the questions asked most often.
View examplesTool Crib Attendant Job Description Template
Ready-to-use JD for recruiters and hiring teams.
View examplesGlobal Tool Crib Attendant Opportunities
A Tool Crib Attendant's role involves managing and distributing tools and equipment in industrial settings. This profession has consistent global demand wherever manufacturing, construction, or maintenance operations occur. While specific regulations vary, the core function remains universal. Professionals consider international roles for better pay, diverse work environments, or to follow large-scale projects. No specific international certifications exist, but experience with various inventory systems is beneficial.
Global Salaries
Tool Crib Attendant salaries vary significantly by region and industry. In North America, a Tool Crib Attendant earns between $35,000 and $55,000 USD annually in the United States, while in Canada, the range is $30,000 to $50,000 CAD (approximately $22,000-$37,000 USD). These figures reflect higher purchasing power due to generally lower cost of living outside major cities where many industrial sites are located.
European salaries differ widely. In Germany, a Tool Crib Attendant might earn €28,000 to €40,000 (approximately $30,000-$43,000 USD), benefiting from strong social benefits and healthcare. In the UK, salaries range from £20,000 to £30,000 (around $25,000-$38,000 USD), with a higher cost of living in southern regions. Asian markets like Singapore offer S$25,000 to S$40,000 (about $18,000-$29,000 USD), but with a much higher cost of living, impacting real income.
Latin American countries typically show lower nominal salaries but higher purchasing power. In Mexico, an attendant earns around MXN 100,000 to MXN 200,000 annually (approximately $5,000-$10,000 USD). Experience with specialized tools or inventory software can influence compensation globally. Tax implications and take-home pay vary significantly; for example, European countries often have higher social security contributions than North America. Vacation time and healthcare benefits also differ by country and employer.
Remote Work
International remote work for a Tool Crib Attendant is generally not feasible. This role requires physical presence to manage, distribute, and track tools and equipment in a specific location. Inventory management, quality control, and direct interaction with workers are core, hands-on responsibilities.
Some administrative tasks, like inventory data entry or ordering, could theoretically be done remotely. However, these form only a small part of the job. Employers prioritize on-site availability for this operational role. Digital nomad opportunities do not apply to this profession. The role's nature inherently demands a physical workspace, making international remote work or global hiring models largely inapplicable.
Visa & Immigration
Visa and immigration pathways for Tool Crib Attendants often fall under general skilled worker categories, rather than profession-specific programs. Countries like Canada, Australia, and Germany have points-based systems or employer-sponsored visas. These visas often require a job offer from an employer demonstrating a need for the position.
Common requirements include proving relevant work experience and sometimes demonstrating English or local language proficiency. Educational credential recognition is less stringent for this role compared to highly regulated professions. The visa application process can take several months, depending on the country and visa type.
Some industrial sectors, especially those with labor shortages, might offer faster processing. Pathways to permanent residency exist in many countries after several years of continuous employment on a skilled worker visa. Family visas allow dependents to accompany the primary applicant. Each country's specific immigration laws and labor market needs in 2025 will dictate the ease of obtaining a work visa for this role.
2025 Market Reality for Tool Crib Attendants
Understanding current market realities for a Tool Crib Attendant is crucial for successful career planning. The landscape has evolved significantly from 2023 to 2025, influenced by post-pandemic supply chain adjustments and the accelerating integration of digital tools.
Broader economic factors, such as industrial output and construction spending, directly impact job availability in this field. Market realities also vary considerably by experience level—entry-level roles face different dynamics than supervisory positions—and by geographic region and company size, from small workshops to large factories. This analysis provides an honest assessment to help job seekers navigate these conditions effectively.
Current Challenges
Securing a Tool Crib Attendant position faces challenges from increased automation in inventory management. Businesses seek to reduce manual oversight, impacting entry-level roles. Competition remains steady for available roles, especially as some manufacturing sectors consolidate operations.
Growth Opportunities
Despite some automation trends, strong demand persists for Tool Crib Attendants in specialized manufacturing and defense industries. These sectors require meticulous inventory control that basic automation cannot yet fully replicate. Emerging opportunities include roles focused on managing advanced tooling for robotics or additive manufacturing.
Professionals can gain an advantage by mastering digital inventory management software and basic data analysis. Underserved markets often appear in rapidly expanding industrial zones outside major metropolitan areas. Skills in predictive maintenance scheduling or basic tool repair provide competitive edges.
Market adjustments might create opportunities for those willing to relocate or specialize in niche equipment. Companies still need reliable personnel to ensure operational continuity and minimize costly downtime. Focusing on industries with high-value tooling can lead to more stable and specialized positions.
Current Market Trends
Hiring for Tool Crib Attendants shows stability in 2025, particularly within industrial manufacturing, construction, and large-scale maintenance operations. Demand centers on facilities requiring precise tracking and issuance of specialized equipment. Companies increasingly prioritize candidates with digital inventory system experience, moving beyond purely manual methods.
Economic conditions influence hiring, with robust infrastructure projects creating consistent need. Conversely, sectors facing slowdowns might see fewer openings. Generative AI and automation are beginning to affect the role, shifting focus from simple check-outs to data entry and system management. Employers now seek individuals who can operate software platforms for inventory, rather than just physical handling.
Salary trends for Tool Crib Attendants remain steady, reflecting the essential but often entry-level nature of the role. Market saturation is low for experienced attendants capable of managing complex digital inventories. Geographic variations are significant; high-demand regions include areas with active manufacturing hubs, large construction projects, or extensive industrial parks. Remote work is not applicable for this hands-on position.
Emerging Specializations
Technological advancement and industry evolution are continually reshaping traditional roles, creating new specialization opportunities even within established fields. For a Tool Crib Attendant, understanding these future-oriented paths is crucial for career advancement in 2025 and beyond. Early positioning in emerging areas often commands premium compensation and offers significant career growth potential, as demand outpaces the supply of specialized skills.
While established specializations offer stability, pursuing emerging areas balances this with strategic foresight. These cutting-edge niches often become mainstream within three to five years, leading to a significant increase in job opportunities. Professionals who adapt early can become leaders in these evolving sectors. However, specializing in nascent fields carries inherent risk, requiring continuous learning and adaptability. The reward for navigating this uncertainty is often a highly valued, future-proofed career path.
The strategic implications of specialization choices are profound. Opting for an emerging area requires investing time in new skill acquisition and staying abreast of technological shifts. This proactive approach ensures relevance and competitiveness in a rapidly changing industrial landscape. It’s about recognizing where the industry is heading and aligning one's skills accordingly, rather than reacting to shifts after they have occurred.
Smart Tooling & IoT Integration Specialist
As manufacturing facilities adopt smart technologies and IoT, the role of a Tool Crib Attendant evolves to include managing interconnected tools and equipment. This specialization focuses on maintaining digital inventories, tracking tool usage patterns via sensors, and integrating data from various smart devices into a centralized system. It ensures optimal tool availability and predicts maintenance needs, minimizing downtime and improving operational efficiency.
Blockchain-Enabled Inventory Management Specialist
With increasing emphasis on supply chain transparency and efficiency, blockchain technology is finding applications in asset tracking. A Tool Crib Attendant specializing in blockchain-enabled inventory management uses distributed ledger technology to create immutable records of tool movements, maintenance history, and ownership. This enhances accountability, reduces fraud, and streamlines audits, offering a high level of security and transparency for critical assets.
Sustainable Tool Lifecycle Manager
Sustainability and circular economy principles are driving demand for responsible material and tool management. This specialization involves tracking the lifecycle of tools from procurement to disposal, focusing on repair, reuse, and recycling. A Tool Crib Attendant in this role optimizes resource utilization, minimizes waste, and ensures compliance with environmental regulations, contributing to a company's green initiatives and reducing operational costs.
On-Demand Tool Fabrication Specialist (3D Printing)
The rise of additive manufacturing, particularly 3D printing, means that many tools or tool components can now be produced on-demand. A Tool Crib Attendant specializing in On-Demand Tool Fabrication manages in-house 3D printing operations for custom tools, jigs, and fixtures. This reduces lead times, cuts costs associated with external procurement, and allows for rapid prototyping and customization, directly impacting production agility.
Automated Tool Handling Systems Operator
As automation becomes prevalent in industrial settings, robotic systems are increasingly used for tasks like tool retrieval, sorting, and inventory counts. A Tool Crib Attendant specializing in Automated Tool Handling Systems oversees the operation, programming, and basic maintenance of these robotic systems. This role ensures the efficient and accurate movement of tools, integrating robotic processes with existing inventory management systems to optimize workflow.
Pros & Cons of Being a Tool Crib Attendant
Understanding both the advantages and challenges of any career is crucial before making a commitment. A tool crib attendant role, like many others, offers distinct benefits alongside specific difficulties. Career experiences can vary significantly based on the company's size, industry sector, and the specific demands of the facility. For instance, working in a large manufacturing plant differs from a smaller repair shop. Furthermore, the pros and cons may shift at different career stages; what seems like a benefit early on might become a challenge later. Some aspects might even be a pro for one person and a con for another, depending on individual preferences for routine, physical work, or social interaction. This assessment provides an honest, balanced view to help set realistic expectations.
Pros
- The role typically offers stable employment with consistent demand in manufacturing, construction, and maintenance industries that rely heavily on organized tool management.
- It provides a clear, structured work environment with well-defined tasks and responsibilities, which can be appealing to individuals who prefer routine and order.
- Entry into this career often requires minimal formal education or specialized certifications, making it accessible to a wide range of job seekers.
- Tool crib attendants gain practical knowledge about a vast array of tools, equipment, and industrial processes, which can be valuable for transitioning into other trades or roles.
- The work is essential to operational efficiency, meaning the role contributes directly to productivity and helps prevent costly downtime, offering a sense of purpose.
- Many positions offer regular daytime hours, especially in smaller operations, providing a predictable schedule that supports work-life balance.
- There is often a strong emphasis on safety protocols, ensuring a secure working environment and fostering a culture of careful handling and organization.
Cons
- The work environment can be physically demanding, requiring frequent lifting, bending, and standing for long periods, which may lead to physical strain over time.
- There is often limited opportunity for significant career advancement within a tool crib attendant role itself, as it is largely an entry-level or support position.
- The job can become monotonous due to the repetitive nature of tasks such as organizing, cataloging, and dispensing tools day after day.
- Exposure to various industrial environments means dealing with noise, dust, and sometimes hazardous materials, requiring adherence to strict safety protocols.
- Pay scales for tool crib attendants are generally modest, and while steady, they may not offer high earning potential compared to skilled trades or management roles.
- Errors in inventory or dispensing can cause significant disruptions to operations, leading to pressure and accountability for accuracy.
- Working hours may include shifts, evenings, or weekends, especially in facilities with continuous operations, impacting work-life balance for some individuals and families.
Frequently Asked Questions
Tool Crib Attendants face distinct challenges around maintaining precise inventory, ensuring tool availability, and managing equipment flow in dynamic industrial settings. This section addresses key questions about entering this role, from required skills to career stability and daily responsibilities.
What are the basic educational and experience requirements to become a Tool Crib Attendant?
Most Tool Crib Attendant positions require a high school diploma or GED. Employers value practical experience in inventory management, warehousing, or mechanics. Some positions may prefer vocational training in a related field or a certification in inventory control, but these are often not mandatory. Attention to detail and organizational skills are more critical than formal degrees.
What does a typical day look like for a Tool Crib Attendant?
Daily tasks for a Tool Crib Attendant involve issuing and receiving tools and equipment, maintaining accurate inventory records, inspecting tools for damage, and performing minor repairs or maintenance. You will also organize and stock the tool crib, ensure safety compliance, and communicate with workers about tool availability. It is a physically active role, involving frequent lifting and moving of items.
What is the typical salary range for a Tool Crib Attendant, especially for someone starting out?
Entry-level Tool Crib Attendants can expect to earn a starting salary that varies significantly by industry, location, and company size, typically ranging from $30,000 to $45,000 annually. With experience, specialized skills, or in unionized environments, this can increase. Overtime opportunities are also common, especially in manufacturing or construction settings, which can boost overall earnings.
Is the job outlook for Tool Crib Attendants stable, or is it a declining field?
The job market for Tool Crib Attendants is generally stable, tied to the health of industries like manufacturing, construction, and automotive. While not a rapidly growing field, the continuous need for equipment management ensures consistent demand. Automation might impact some aspects, but the need for human oversight, inspection, and direct interaction with tools remains. Job security is often good in established companies.
What are the potential career advancement opportunities for a Tool Crib Attendant?
Career growth for Tool Crib Attendants often involves moving into supervisory roles within tool crib operations, becoming a lead attendant, or specializing in purchasing and procurement. Some transition into broader inventory management, warehouse supervision, or even maintenance management positions within the same company. Acquiring certifications in inventory control or logistics can also open up more advanced opportunities.
What kind of work-life balance can I expect as a Tool Crib Attendant?
The work-life balance for a Tool Crib Attendant depends heavily on the industry and specific employer. Many positions are full-time, often working standard shifts, but some industrial settings may require evening, night, or weekend shifts to support 24/7 operations. Overtime is common in busy periods, which can impact personal time. The role is typically on-site and offers little remote work flexibility.
What are the most challenging aspects of being a Tool Crib Attendant?
The biggest challenges often include maintaining highly accurate inventory in a fast-paced environment, dealing with tool loss or damage, and managing requests from multiple departments simultaneously. You also need to stay organized, adapt to new tooling technologies, and ensure compliance with safety regulations. Effective communication and problem-solving skills are crucial for handling these daily pressures.
Related Careers
Explore similar roles that might align with your interests and skills:
Inventory Supervisor
A growing field with similar skill requirements and career progression opportunities.
Explore career guideStockroom Associate
A growing field with similar skill requirements and career progression opportunities.
Explore career guideStockroom Clerk
A growing field with similar skill requirements and career progression opportunities.
Explore career guideStockroom Attendant
A growing field with similar skill requirements and career progression opportunities.
Explore career guideSupply Room Clerk
A growing field with similar skill requirements and career progression opportunities.
Explore career guideAssess your Tool Crib Attendant readiness
Understanding where you stand today is the first step toward your career goals. Our Career Coach helps identify skill gaps and create personalized plans.
Skills Gap Analysis
Get a detailed assessment of your current skills versus Tool Crib Attendant requirements. Our AI Career Coach identifies specific areas for improvement with personalized recommendations.
See your skills gapCareer Readiness Assessment
Evaluate your overall readiness for Tool Crib Attendant roles with our AI Career Coach. Receive personalized recommendations for education, projects, and experience to boost your competitiveness.
Assess your readinessSimple pricing, powerful features
Upgrade to Himalayas Plus and turbocharge your job search.
Himalayas
Himalayas Plus
Himalayas Max
Find your dream job
Sign up now and join over 100,000 remote workers who receive personalized job alerts, curated job matches, and more for free!
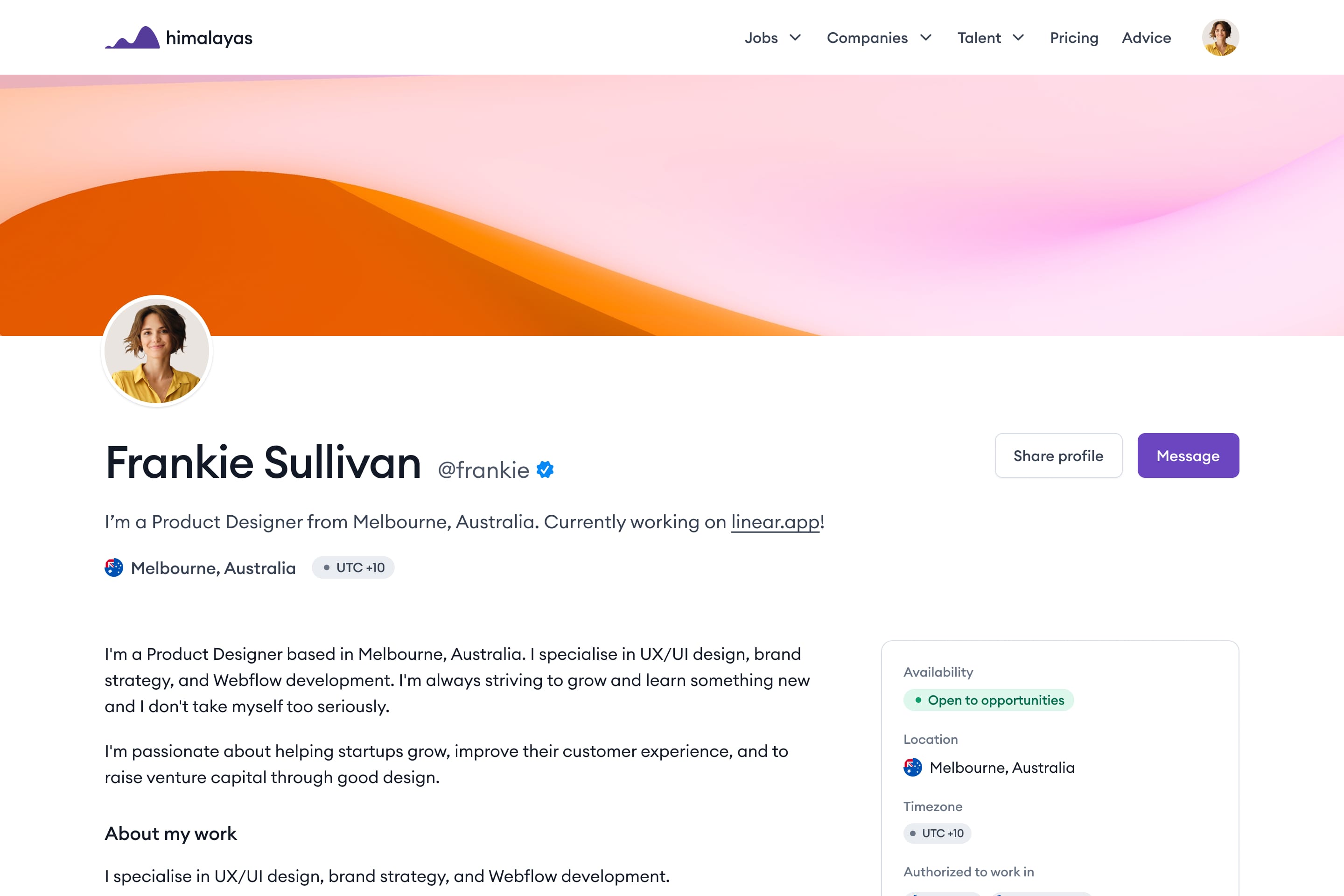