Complete Quality Control Assistant Career Guide
Quality Control Assistants are the vigilant eyes behind product excellence, ensuring everything from pharmaceuticals to manufactured goods meets rigorous standards before reaching consumers. They play a critical role in preventing costly errors and upholding brand reputation, making them indispensable to production lines across diverse industries. This career offers a hands-on path for detail-oriented individuals who enjoy precision and contributing directly to product integrity.
Key Facts & Statistics
Median Salary
$44,790 USD
(U.S. Bureau of Labor Statistics, May 2023)
Range: $30k - $60k+ USD, varying significantly by industry, experience, and location (U.S. Bureau of Labor Statistics)
Growth Outlook
1%
(little or no change) from 2022 to 2032 (U.S. Bureau of Labor Statistics)
Annual Openings
≈10,000
openings annually (U.S. Bureau of Labor Statistics)
Top Industries
Typical Education
High school diploma or equivalent, often with on-the-job training; some positions may prefer an associate's degree or relevant certifications (e.g., ASQ Certified Quality Inspector)
What is a Quality Control Assistant?
A Quality Control Assistant plays a crucial role in ensuring products and processes meet established quality standards throughout the manufacturing lifecycle. They are the frontline defenders of product integrity, primarily responsible for inspecting, testing, and monitoring materials, components, and finished goods. This role focuses on identifying defects and non-conformances, preventing substandard products from reaching customers.
This position differs significantly from a Quality Assurance (QA) Engineer or Manager. While a QA professional designs and implements the overall quality systems and processes, the Quality Control Assistant executes these established procedures. They are the hands-on inspectors and data collectors, whereas QA professionals are more involved in strategic planning, auditing, and continuous improvement of the quality system itself.
What does a Quality Control Assistant do?
Key Responsibilities
- Inspect incoming raw materials and components against specifications to ensure they meet quality standards before production begins.
- Perform in-process checks on products at various stages of manufacturing, identifying and documenting any deviations or defects.
- Conduct final product inspections, including visual checks, measurements, and functional tests, to verify compliance with finished goods criteria.
- Record detailed quality data, including inspection results, defect rates, and non-conformances, into quality management systems.
- Prepare and maintain samples for laboratory analysis, ensuring proper labeling and storage according to established protocols.
- Collaborate with production teams to identify the root causes of quality issues and support the implementation of corrective actions.
- Assist in the calibration and maintenance of inspection equipment, ensuring accuracy and reliability of measurements.
Work Environment
Quality Control Assistants primarily work in manufacturing facilities, laboratories, or warehouses. Their environment can vary from cleanroom settings to noisy production floors. The role often involves standing for extended periods, moving between different inspection points, and sometimes lifting light to moderate weights. Collaboration is frequent with production operators, supervisors, and other quality assurance personnel. Work schedules are typically full-time, often aligning with production shifts, which may include evenings or weekends. The pace is steady and detail-oriented, requiring meticulous attention to process and product quality. While primarily on-site, some roles in larger organizations might involve occasional travel between different plant locations.
Tools & Technologies
Quality Control Assistants regularly use a variety of precision measuring instruments such as calipers, micrometers, gauges, and rulers. They work with visual inspection tools like magnifying lamps and microscopes to detect subtle defects. Data entry and analysis typically involve spreadsheet software like Microsoft Excel and specialized Quality Management Systems (QMS) such as MasterControl or Sparta Systems TrackWise. Depending on the industry, they might also interact with statistical process control (SPC) software, basic laboratory equipment for sample preparation, and enterprise resource planning (ERP) systems like SAP for material tracking. Adherence to industry-specific standards like ISO 9001 and Good Manufacturing Practices (GMP) is fundamental to their daily work.
Quality Control Assistant Skills & Qualifications
A Quality Control Assistant plays a crucial role in maintaining product standards and operational excellence. This position ensures that products or services consistently meet defined specifications and quality benchmarks. Qualification requirements for this role vary significantly based on the industry, company size, and the complexity of the products or processes involved.
For entry-level positions, a strong understanding of basic quality principles often outweighs extensive formal education. Practical experience in manufacturing, laboratory settings, or process adherence is highly valued. Certifications, particularly in quality assurance or specific industry standards, can significantly enhance a candidate's profile, sometimes even serving as an alternative to a traditional degree. Larger corporations or highly regulated industries, such as pharmaceuticals or aerospace, typically demand more formal education, often a Bachelor's degree in a relevant scientific or engineering discipline.
The skill landscape for Quality Control Assistants is evolving with increased automation and data analytics. Proficiency in statistical process control software and data visualization tools is becoming increasingly important. While foundational inspection skills remain critical, the ability to interpret data, identify trends, and contribute to continuous improvement initiatives now differentiates top candidates. This role requires a balance between meticulous attention to detail and a broader understanding of how quality impacts overall business objectives.
Education Requirements
Technical Skills
- Familiarity with Quality Management Systems (QMS) such as ISO 9001.
- Proficiency in using measurement tools (calipers, micrometers, gauges, optical comparators).
- Ability to read and interpret blueprints, schematics, and technical drawings.
- Basic understanding of Statistical Process Control (SPC) and data collection.
- Knowledge of Good Manufacturing Practices (GMP) and Good Laboratory Practices (GLP) where applicable.
- Experience with Non-Conformance Reporting (NCR) and Corrective and Preventive Actions (CAPA) processes.
- Data entry and basic spreadsheet software (e.g., Microsoft Excel) for record keeping.
- Understanding of sampling plans and inspection methodologies (e.g., AQL).
- Ability to perform visual inspections and identify defects.
- Familiarity with safety protocols in a manufacturing or laboratory environment.
Soft Skills
- Attention to Detail: Essential for meticulously inspecting products, identifying flaws, and ensuring compliance with precise specifications.
- Problem-Solving: Important for identifying root causes of quality issues and contributing to effective corrective actions.
- Communication: Necessary for clearly documenting findings, reporting non-conformances, and collaborating with production and engineering teams.
- Organization: Crucial for managing samples, maintaining accurate records, and ensuring traceability of materials and products.
- Integrity: Vital for upholding quality standards impartially and reporting findings accurately, even when they indicate issues.
- Adaptability: Important for adjusting to changes in product specifications, testing procedures, or production schedules.
- Proactiveness: Valued for identifying potential quality risks before they become significant problems.
- Teamwork: Essential for collaborating effectively with production, engineering, and other departments to achieve quality goals and improve processes together.
How to Become a Quality Control Assistant
Breaking into a Quality Control Assistant role often involves a blend of foundational knowledge and practical skills. While a formal science degree is a traditional route, many employers value vocational training, certifications, or even relevant experience in manufacturing or laboratory settings. Your entry strategy might depend on the industry: food and beverage, pharmaceuticals, and manufacturing all have distinct QC needs, impacting the specific skills required and the typical hiring timelines.
Timeline expectations vary; a complete beginner might need 6-12 months for foundational learning and skill development, while someone transitioning from a related field could find a role within 3-6 months. Smaller companies and startups might be more open to candidates with less formal education but strong practical aptitude, whereas larger corporations or highly regulated industries often prefer candidates with specific certifications or associate's/bachelor's degrees. Networking within industry-specific groups, attending local manufacturing or science career fairs, and seeking mentorship can significantly accelerate your job search.
A common misconception is that this role is purely about 'checking boxes'; it involves critical thinking, problem-solving, and meticulous documentation. Your ability to understand processes, identify deviations, and communicate findings clearly is as important as technical skills. Focus on building a profile that highlights your attention to detail, analytical capabilities, and commitment to maintaining standards, which are universally valued across all sectors hiring Quality Control Assistants.
Develop a strong understanding of quality control principles and basic lab safety protocols. Enroll in an introductory course on quality management, often available through community colleges or online platforms like Coursera, which can take 1-3 months. Focus on concepts like Good Manufacturing Practices (GMP) or Good Laboratory Practices (GLP) depending on your target industry.
Acquire fundamental technical skills relevant to common QC tasks, such as basic statistical process control, data entry, and using measurement tools like calipers or pH meters. Practice these skills through virtual simulations, home-based experiments, or by volunteering in a local community lab if available. This practical application solidifies your theoretical knowledge.
Build a portfolio or resume that highlights your attention to detail, accuracy, and any relevant hands-on experience, even if it's from unrelated roles. Document any projects where you meticulously followed instructions, identified errors, or maintained high standards, quantifying your impact where possible. This step is crucial for showcasing your aptitude to potential employers.
Network with professionals in the quality control field by attending virtual industry webinars, joining LinkedIn groups, or reaching out for informational interviews. Many entry-level positions are filled through referrals, and building connections can provide insights into unadvertised opportunities and specific employer needs. Aim to connect with at least 5-10 professionals monthly.
Tailor your resume and cover letter to each specific Quality Control Assistant job description, emphasizing keywords and required skills. Practice common interview questions focusing on problem-solving, attention to detail, and your ability to follow procedures. Be prepared to discuss how your experiences align with the company's quality standards.
Apply for entry-level Quality Control Assistant roles, internships, or apprenticeships. Focus on positions that offer on-the-job training and mentorship, as these are excellent pathways to gain practical experience and solidify your career in the field. Be persistent and learn from each application and interview experience.
Step 1
Develop a strong understanding of quality control principles and basic lab safety protocols. Enroll in an introductory course on quality management, often available through community colleges or online platforms like Coursera, which can take 1-3 months. Focus on concepts like Good Manufacturing Practices (GMP) or Good Laboratory Practices (GLP) depending on your target industry.
Step 2
Acquire fundamental technical skills relevant to common QC tasks, such as basic statistical process control, data entry, and using measurement tools like calipers or pH meters. Practice these skills through virtual simulations, home-based experiments, or by volunteering in a local community lab if available. This practical application solidifies your theoretical knowledge.
Step 3
Build a portfolio or resume that highlights your attention to detail, accuracy, and any relevant hands-on experience, even if it's from unrelated roles. Document any projects where you meticulously followed instructions, identified errors, or maintained high standards, quantifying your impact where possible. This step is crucial for showcasing your aptitude to potential employers.
Step 4
Network with professionals in the quality control field by attending virtual industry webinars, joining LinkedIn groups, or reaching out for informational interviews. Many entry-level positions are filled through referrals, and building connections can provide insights into unadvertised opportunities and specific employer needs. Aim to connect with at least 5-10 professionals monthly.
Step 5
Tailor your resume and cover letter to each specific Quality Control Assistant job description, emphasizing keywords and required skills. Practice common interview questions focusing on problem-solving, attention to detail, and your ability to follow procedures. Be prepared to discuss how your experiences align with the company's quality standards.
Step 6
Apply for entry-level Quality Control Assistant roles, internships, or apprenticeships. Focus on positions that offer on-the-job training and mentorship, as these are excellent pathways to gain practical experience and solidify your career in the field. Be persistent and learn from each application and interview experience.
Education & Training Needed to Become a Quality Control Assistant
The educational path for a Quality Control Assistant emphasizes practical skills over advanced theoretical knowledge. Many roles prioritize a high school diploma or GED, often combined with vocational training or a certificate. Some employers prefer candidates with an Associate's degree in a scientific or technical field, such as Chemistry, Biology, or Manufacturing Technology. Bachelor's degrees are generally not a prerequisite unless the role involves more complex analytical tasks or progression into management.
Formal degree programs, like Associate's degrees, typically cost between $6,000 and $20,000 and take two years to complete. These programs provide a strong foundation in scientific principles and laboratory techniques. Vocational training and certificate programs, often costing $1,000 to $5,000, can be completed in a few months to a year, focusing directly on industry-specific quality control methods. Self-study through online courses or industry guides is also viable, costing from free to a few hundred dollars, with completion times ranging from 3 to 12 months, depending on the learner's dedication.
Employers highly value practical experience and familiarity with industry standards like ISO 9001 or cGMP. While degrees offer a broader theoretical base, certifications from organizations like the American Society for Quality (ASQ) directly demonstrate proficiency in quality control tools and methodologies. Continuous learning through workshops on new testing equipment or updated regulations is crucial for staying current. The best educational investment combines foundational knowledge with hands-on training and specific industry certifications, preparing individuals for immediate contributions in a quality control environment.
Quality Control Assistant Salary & Outlook
Compensation for a Quality Control Assistant varies significantly based on several factors. Geographic location plays a crucial role; areas with a higher cost of living or a strong manufacturing presence typically offer higher salaries. For instance, a Quality Control Assistant in California or New Jersey might earn more than one in a lower cost-of-living state, reflecting regional economic conditions and demand.
Experience, specialized skills, and the specific industry also dramatically influence earning potential. An assistant with experience in highly regulated fields like pharmaceuticals or aerospace, or with certifications in Six Sigma or Lean Manufacturing, can command a premium. Total compensation extends beyond base salary to include performance bonuses, health insurance, retirement plans like 401(k) matching, and opportunities for professional development.
Company size and type of product directly affect pay structures. Larger corporations often provide more comprehensive benefits and higher base salaries compared to smaller businesses. Remote work is less common for this hands-on role, but when available, it can impact salary ranges, sometimes allowing for geographic arbitrage if the employer maintains a national pay scale. Salary negotiation leverage increases with proven experience, a track record of improving quality metrics, and specialized technical skills relevant to the product being inspected. While these figures primarily reflect the US market, international salaries vary widely based on local economies and industry standards.
Salary by Experience Level
Level | US Median | US Average |
---|---|---|
Junior Quality Control Assistant | $36k USD | $38k USD |
Quality Control Assistant | $43k USD | $45k USD |
Senior Quality Control Assistant | $50k USD | $52k USD |
Quality Control Specialist | $58k USD | $60k USD |
Quality Control Supervisor | $72k USD | $75k USD |
Quality Control Manager | $90k USD | $95k USD |
Market Commentary
The job market for Quality Control Assistants shows stable demand, driven by the continuous need for product integrity and regulatory compliance across various industries. Manufacturing, food and beverage, pharmaceuticals, and electronics sectors consistently seek qualified personnel to ensure product quality. Automation and AI are transforming some aspects of quality control, particularly in data collection and preliminary analysis, but the need for human oversight, judgment, and hands-on inspection remains critical.
Projections indicate a steady growth outlook, with the Bureau of Labor Statistics forecasting a modest increase in related occupations. This growth is fueled by consumer demand for high-quality products and stringent industry regulations. Emerging opportunities lie in specialized areas such as advanced materials testing, digital quality assurance, and roles involving data analytics for predictive quality control. The supply and demand dynamics are relatively balanced, with a consistent need for entry-level and experienced professionals in manufacturing hubs.
Future-proofing this career involves continuous learning in new inspection technologies, statistical process control software, and regulatory updates. While generally recession-resistant due to compliance requirements, economic downturns can lead to slower hiring in some manufacturing sectors. Geographic hotspots for Quality Control Assistants include industrial regions in the Midwest, parts of the Southeast, and states with strong pharmaceutical or aerospace industries like California, Texas, and North Carolina. The role is evolving, requiring a blend of hands-on skills and data interpretation capabilities.
Quality Control Assistant Career Path
Career progression for a Quality Control Assistant typically involves a steady accumulation of technical expertise, an understanding of quality standards, and an increasing ability to take on more complex tasks. Professionals often begin with foundational inspection duties and gradually move towards analytical, problem-solving, and leadership responsibilities. This field offers distinct pathways: an individual contributor (IC) track focused on deep specialization and technical mastery, or a management/leadership track centered on team oversight and strategic quality assurance.
Advancement speed depends on several factors, including consistent performance, the complexity of products or processes handled, and the size and industry of the employing company. For instance, a pharmaceutical company might offer a more structured, regulated path compared to a manufacturing startup. Specialization in areas like specific testing methodologies or regulatory compliance can accelerate progression. Lateral moves might involve transitioning into related fields such as process improvement, validation, or regulatory affairs, leveraging a strong understanding of quality systems.
Networking within the industry, participating in professional organizations, and seeking mentorship are crucial for identifying opportunities and gaining insights into best practices. Certifications, such as ASQ (American Society for Quality) certifications, mark significant milestones and demonstrate advanced competency. Continuous learning in new technologies, automation, and evolving quality standards is essential. Career pivots could lead to roles in R&D, product development, or even supply chain management, where quality principles remain highly relevant.
Junior Quality Control Assistant
0-1 yearPerform basic visual inspections and simple measurements of raw materials or finished products under direct supervision. Document findings according to established procedures. Assist senior staff in preparing samples for testing. Work within a defined set of instructions, contributing to the initial checks in the quality process.
Key Focus Areas
Develop foundational understanding of quality standards, documentation practices, and basic inspection techniques. Focus on precision, attention to detail, and adherence to protocols. Build proficiency in using standard measuring tools and recording data accurately. Learn to identify common defects and non-conformances.
Quality Control Assistant
1-3 yearsConduct routine quality checks, inspections, and tests on various products or components with limited supervision. Identify and document non-conformances, initiating corrective action reports. Operate and calibrate standard testing equipment. Collaborate with production teams to address immediate quality issues.
Key Focus Areas
Master a wider range of inspection and testing methods. Improve data analysis skills, including trend identification and basic statistical process control (SPC). Enhance problem-solving abilities for minor non-conformances. Begin understanding the 'why' behind quality procedures and their impact on product integrity.
Senior Quality Control Assistant
3-5 yearsExecute complex testing protocols and conduct thorough investigations into quality deviations. Analyze test results, identify root causes of failures, and recommend corrective actions. Train and guide junior assistants on proper procedures and equipment usage. Take ownership of specific quality assurance processes or product lines.
Key Focus Areas
Refine advanced testing techniques and complex data interpretation. Develop a strong understanding of root cause analysis and corrective/preventive actions (CAPA). Begin mentoring junior team members. Focus on process optimization and contributing to standard operating procedure (SOP) improvements. Consider specific industry certifications.
Quality Control Specialist
5-8 yearsServe as a subject matter expert for specific quality control areas or product categories. Design and implement new testing procedures or quality checks. Lead investigations into significant quality failures and contribute to continuous improvement projects. Analyze complex data to identify trends and proactively prevent issues.
Key Focus Areas
Deepen expertise in specific quality methodologies (e.g., Six Sigma, Lean). Develop strong analytical and problem-solving skills for systemic quality issues. Focus on process improvement initiatives and validation activities. Begin cross-functional collaboration on quality-related projects. Seek advanced certifications relevant to the industry.
Quality Control Supervisor
8-12 yearsOversee a team of Quality Control Assistants and Specialists. Manage daily operations of the QC lab or inspection area, ensuring timely and accurate testing. Review and approve documentation, test results, and non-conformance reports. Participate in audits and ensure adherence to quality management systems.
Key Focus Areas
Develop leadership and team management skills, including scheduling, performance feedback, and conflict resolution. Enhance project management capabilities for quality initiatives. Focus on optimizing workflow and resource allocation within the QC department. Understand and implement regulatory compliance requirements.
Quality Control Manager
12+ yearsLead the entire Quality Control department, setting strategic direction and objectives. Develop and manage the QC budget, resources, and personnel. Establish and maintain the quality management system. Collaborate with senior leadership on product development, manufacturing, and supply chain to ensure overall product quality and compliance.
Key Focus Areas
Cultivate strategic thinking, budget management, and departmental planning skills. Focus on developing and implementing comprehensive quality strategies aligned with business goals. Build strong stakeholder management and communication abilities. Drive continuous improvement and innovation across the entire quality function.
Junior Quality Control Assistant
0-1 yearPerform basic visual inspections and simple measurements of raw materials or finished products under direct supervision. Document findings according to established procedures. Assist senior staff in preparing samples for testing. Work within a defined set of instructions, contributing to the initial checks in the quality process.
Key Focus Areas
Develop foundational understanding of quality standards, documentation practices, and basic inspection techniques. Focus on precision, attention to detail, and adherence to protocols. Build proficiency in using standard measuring tools and recording data accurately. Learn to identify common defects and non-conformances.
Quality Control Assistant
1-3 yearsConduct routine quality checks, inspections, and tests on various products or components with limited supervision. Identify and document non-conformances, initiating corrective action reports. Operate and calibrate standard testing equipment. Collaborate with production teams to address immediate quality issues.
Key Focus Areas
Master a wider range of inspection and testing methods. Improve data analysis skills, including trend identification and basic statistical process control (SPC). Enhance problem-solving abilities for minor non-conformances. Begin understanding the 'why' behind quality procedures and their impact on product integrity.
Senior Quality Control Assistant
3-5 yearsExecute complex testing protocols and conduct thorough investigations into quality deviations. Analyze test results, identify root causes of failures, and recommend corrective actions. Train and guide junior assistants on proper procedures and equipment usage. Take ownership of specific quality assurance processes or product lines.
Key Focus Areas
Refine advanced testing techniques and complex data interpretation. Develop a strong understanding of root cause analysis and corrective/preventive actions (CAPA). Begin mentoring junior team members. Focus on process optimization and contributing to standard operating procedure (SOP) improvements. Consider specific industry certifications.
Quality Control Specialist
5-8 yearsServe as a subject matter expert for specific quality control areas or product categories. Design and implement new testing procedures or quality checks. Lead investigations into significant quality failures and contribute to continuous improvement projects. Analyze complex data to identify trends and proactively prevent issues.
Key Focus Areas
Deepen expertise in specific quality methodologies (e.g., Six Sigma, Lean). Develop strong analytical and problem-solving skills for systemic quality issues. Focus on process improvement initiatives and validation activities. Begin cross-functional collaboration on quality-related projects. Seek advanced certifications relevant to the industry.
Quality Control Supervisor
8-12 yearsOversee a team of Quality Control Assistants and Specialists. Manage daily operations of the QC lab or inspection area, ensuring timely and accurate testing. Review and approve documentation, test results, and non-conformance reports. Participate in audits and ensure adherence to quality management systems.
Key Focus Areas
Develop leadership and team management skills, including scheduling, performance feedback, and conflict resolution. Enhance project management capabilities for quality initiatives. Focus on optimizing workflow and resource allocation within the QC department. Understand and implement regulatory compliance requirements.
Quality Control Manager
12+ yearsLead the entire Quality Control department, setting strategic direction and objectives. Develop and manage the QC budget, resources, and personnel. Establish and maintain the quality management system. Collaborate with senior leadership on product development, manufacturing, and supply chain to ensure overall product quality and compliance.
Key Focus Areas
Cultivate strategic thinking, budget management, and departmental planning skills. Focus on developing and implementing comprehensive quality strategies aligned with business goals. Build strong stakeholder management and communication abilities. Drive continuous improvement and innovation across the entire quality function.
Job Application Toolkit
Ace your application with our purpose-built resources:
Quality Control Assistant Resume Examples
Proven layouts and keywords hiring managers scan for.
View examplesQuality Control Assistant Cover Letter Examples
Personalizable templates that showcase your impact.
View examplesTop Quality Control Assistant Interview Questions
Practice with the questions asked most often.
View examplesQuality Control Assistant Job Description Template
Ready-to-use JD for recruiters and hiring teams.
View examplesGlobal Quality Control Assistant Opportunities
A Quality Control Assistant ensures products meet specified standards, a globally critical role across manufacturing, pharmaceuticals, and food industries. This profession demands meticulous attention to detail, maintaining product integrity worldwide.
Global demand for Quality Control Assistants remains steady, particularly in regulated industries. International opportunities often arise in countries with strong export economies or significant manufacturing bases. Professionals consider international moves for career advancement, exposure to diverse production methods, or better living standards.
Global Salaries
Salaries for Quality Control Assistants vary significantly by region and industry. In North America, particularly the United States, an assistant can expect to earn between $35,000 and $55,000 USD annually. Canadian salaries are similar, ranging from $30,000 to $50,000 CAD, roughly $22,000 to $37,000 USD.
European salaries show wide differences. In Germany, a Quality Control Assistant might earn €30,000 to €45,000 (approx. $32,000-$48,000 USD), reflecting a higher cost of living in major cities. The UK offers £22,000 to £32,000 (approx. $28,000-$40,000 USD). Southern and Eastern Europe generally offer lower compensation, but often with a lower cost of living, leading to comparable purchasing power.
Asia-Pacific markets present diverse ranges. In Japan, salaries could be ¥3.5 million to ¥5 million (approx. $23,000-$33,000 USD), while in Australia, it might be AUD 50,000 to AUD 70,000 (approx. $33,000-$46,000 USD). Latin American countries like Mexico or Brazil typically offer lower nominal salaries, but local purchasing power can be strong. For instance, in Mexico, earnings might be MXN 180,000 to MXN 300,000 (approx. $10,000-$17,000 USD).
Benefits packages also differ; European countries often include more comprehensive healthcare and generous vacation time, while North American packages might emphasize performance bonuses. Tax implications and take-home pay vary based on national tax laws and social security contributions. International experience and specialized certifications, such as ISO 9001, can positively impact compensation and career progression.
Remote Work
International remote work opportunities for Quality Control Assistants are limited due to the hands-on nature of the role. This position often requires physical presence in a manufacturing plant, laboratory, or production facility to perform inspections and tests.
However, some administrative or documentation aspects of quality control might allow for partial remote work. This could involve data analysis, report generation, or standard operating procedure (SOP) development. Full-time digital nomad arrangements are uncommon for this specific role.
Companies with global operations might employ Quality Control Assistants in different countries. This allows for international team collaboration across time zones, but the work remains tied to a physical location. Salary expectations for any rare remote components would likely align with the local market where the assistant is physically located, rather than enabling significant geographic arbitrage.
Visa & Immigration
Common visa categories for Quality Control Assistants often fall under skilled worker visas. Countries like Canada, Australia, and the UK have point-based systems or employer-sponsored visas that may apply. Requirements typically include a job offer, relevant educational qualifications, and proof of experience.
Popular destination countries for manufacturing and quality control roles include Germany, the United States, Canada, and Australia. Specific requirements vary; for instance, Germany's skilled immigration law may require a recognized vocational qualification. Educational credential recognition is crucial; applicants often need their diplomas assessed for equivalency.
Visa timelines vary from a few weeks to several months, depending on the country and visa type. Application processes involve submitting documentation, potentially attending interviews, and sometimes undergoing medical exams. While Quality Control Assistant roles are not typically fast-tracked, consistent employment can lead to pathways for permanent residency in many nations.
Language proficiency tests, such as IELTS for English-speaking countries or Goethe-Zertifikat for Germany, are often required. Family visas and dependent rights usually accompany primary visa applications, allowing spouses and children to join. Employers often assist with initial visa processes for sponsored roles.
2025 Market Reality for Quality Control Assistants
Understanding the current market realities for a Quality Control Assistant is crucial for career success. The landscape for this role has evolved significantly from 2023 to 2025, influenced by post-pandemic shifts in supply chains and the rapid integration of AI and automation in manufacturing.
Broader economic factors, such as inflation and consumer demand, directly impact production volumes, which in turn affect the need for quality control personnel. Market realities also vary by experience level; entry-level roles face different challenges than those requiring specialized technical skills. Geographic location and company size also play a major role, as larger, more technologically advanced firms often have different expectations than smaller operations. This analysis provides an honest assessment to help set realistic expectations.
Current Challenges
Increased automation in quality control processes is a significant challenge, reducing demand for purely manual inspection roles. Many companies now expect Quality Control Assistants to operate sophisticated testing equipment or interpret data, a shift from traditional tasks. Competition is also high for entry-level positions, as the role often serves as a stepping stone. This makes securing a role more difficult without specific technical skills or prior experience.
Growth Opportunities
Despite challenges, significant opportunities exist for Quality Control Assistants willing to adapt. Strong demand persists in highly regulated industries like pharmaceuticals, aerospace, and food safety, where human oversight and compliance knowledge remain indispensable. Emerging opportunities are also found in companies adopting advanced manufacturing techniques, such as additive manufacturing or smart factories, which require new forms of quality assurance.
Professionals can position themselves advantageously by acquiring skills in data analysis, statistical process control (SPC) software, and the operation of automated inspection systems. Certifications in Lean Six Sigma, ISO standards, or specific industry regulations (e.g., GMP for pharma) also provide a competitive edge. Underserved markets might include regions with new manufacturing investments or specialized niche industries requiring meticulous quality checks. Strategic career moves involve targeting companies that invest in advanced QC technology, as these roles often offer growth into Quality Assurance or Process Improvement positions. Focusing on sectors that prioritize compliance and precision, even during economic shifts, can lead to more stable and rewarding career paths.
Current Market Trends
Hiring for Quality Control Assistants in 2025 shows a split market. Traditional manufacturing sectors, especially those with high-volume production, maintain steady but often stagnant demand. However, there is growing demand in specialized areas like pharmaceuticals, medical devices, and advanced electronics, where precision and compliance are paramount. Here, roles require more than just visual inspection; they involve understanding regulatory frameworks and operating complex diagnostic tools.
The integration of AI and automation tools significantly impacts this role. While not displacing all positions, these technologies now handle repetitive inspection tasks. This pushes the Quality Control Assistant role towards more analytical responsibilities, such as data interpretation, root cause analysis of defects, and process improvement. Employers increasingly seek candidates with a blend of hands-on experience and digital literacy. Salaries remain relatively stable but show upward movement for those with specialized skills in automated QC systems or specific industry certifications.
Geographically, demand is strongest in industrial hubs and areas with a high concentration of specialized manufacturing. Remote work is rare for this hands-on role. Economic conditions influence hiring; during downturns, companies often reduce QC staff as production slows, making the market tighter. Conversely, during periods of growth, especially in regulated industries, demand for meticulous QC professionals rises to ensure product integrity and compliance.
Emerging Specializations
Technological advancements and evolving industry standards consistently create new specialization opportunities for Quality Control Assistants. Understanding these future-oriented career paths is crucial for professionals seeking to advance their careers and secure next-generation opportunities. Early positioning in emerging areas, particularly those driven by automation, data analytics, and specialized compliance, can significantly enhance a professional's market value and career trajectory from 2025 onwards.
Specializing in these nascent fields often commands premium compensation and offers accelerated career growth, as demand for these unique skill sets outpaces supply. While established specializations remain vital, a strategic balance between foundational expertise and forward-looking emerging areas positions professionals for long-term success. These emerging specializations typically take 3-5 years to become mainstream and generate a significant volume of job opportunities, making proactive skill development essential now.
Pursuing cutting-edge areas involves a calculated risk, as not all emerging trends fully materialize into widespread roles. However, the potential rewards, including leadership opportunities in new domains and increased earning potential, often outweigh these risks. Professionals who invest in these skills early can become pioneers, shaping the future of quality control rather than merely adapting to it.
AI-Driven Quality Assurance Specialist
IoT Data Quality Monitor
Sustainable Quality Compliance Auditor
Additive Manufacturing Quality Verifier
Pros & Cons of Being a Quality Control Assistant
Understanding both the advantages and challenges of a career is crucial before making a commitment. This is particularly true for a Quality Control Assistant, where daily experiences can vary significantly based on the industry, company size, and specific product being evaluated.
The pros and cons may shift at different career stages; for instance, entry-level roles might focus more on learning foundational processes, while more senior positions could involve complex problem-solving. Some aspects, like the emphasis on precision, might be a positive for detail-oriented individuals but a challenge for others. This assessment provides an honest, balanced view to help set realistic expectations for this role.
Pros
Stable job demand exists across various manufacturing and production sectors, ensuring consistent employment opportunities regardless of specific product trends.
Entry-level positions are often accessible with minimal formal education, providing a viable career path for individuals with a strong work ethic and attention to detail.
Hands-on experience with production processes and quality standards is gained quickly, offering practical skills applicable to many industrial settings.
Contribution to product safety and customer satisfaction provides a sense of purpose, knowing your work directly impacts the reliability and quality of goods.
Opportunities for cross-training in different areas of production or quality assurance often arise, broadening your skill set within the same company.
Structured work environment with clear guidelines and procedures makes daily tasks predictable and easy to learn, reducing ambiguity in responsibilities.
Developing a keen eye for detail and analytical skills is inherent to the role, which are valuable transferable skills for future career growth.
Cons
Repetitive tasks can lead to monotony, as the core duties of inspecting, testing, and documenting follow a strict, unchanging protocol daily.
Exposure to hazardous materials or environments is common in certain industries, requiring strict adherence to safety protocols and potentially leading to health concerns over time.
Limited autonomy and creative input define this role, as Quality Control Assistants follow established procedures without much room for independent decision-making or innovation.
Career progression paths are often narrow, as advancement typically requires further education or specialized certifications to move beyond assistant-level duties.
High attention to detail is constantly required, leading to mental fatigue and stress when errors are missed, potentially impacting product quality or safety.
Pressure to meet production quotas while maintaining quality standards can be intense, creating a challenging balance between speed and precision.
Dealing with defective products or failed tests can be frustrating, especially when identifying the root cause falls outside the Quality Control Assistant's direct control.
Frequently Asked Questions
Quality Control Assistants face distinct challenges ensuring product integrity and compliance with precise standards. This section addresses the most common questions about entering this role, from required skills and daily responsibilities to career progression and the impact of automation on the field.
What are the basic educational and skill requirements to become a Quality Control Assistant?
Most Quality Control Assistant roles require a high school diploma or GED, but many employers prefer candidates with an Associate's degree in a science-related field or a vocational certificate in quality assurance. Prior experience in manufacturing, laboratory settings, or data entry can also be highly beneficial. Strong attention to detail, basic math skills, and the ability to follow precise instructions are essential.
How long does it typically take to become job-ready as a Quality Control Assistant if I'm starting fresh?
The time it takes to become job-ready for a Quality Control Assistant role can vary. If you have a high school diploma and relevant experience, you might be ready in a few weeks with basic training. If you pursue an Associate's degree, it typically takes two years. Vocational programs can range from several months to a year, providing specialized skills quickly. Focus on gaining practical experience through internships or entry-level positions to accelerate your readiness.
What are the typical salary expectations for an entry-level Quality Control Assistant?
Entry-level Quality Control Assistants can expect a starting salary that varies significantly based on industry, location, and specific company. Generally, salaries can range from $35,000 to $45,000 annually. With experience and specialized skills, this can increase. Researching average salaries for your specific region and industry will provide the most accurate expectation.
What is the typical work-life balance like for a Quality Control Assistant, and are long hours common?
Work-life balance for Quality Control Assistants often depends on the industry and company. Many roles are standard 9-to-5, but some manufacturing or production environments may require shift work, including evenings or weekends, to cover continuous operations. Overtime can be common during peak production periods or when addressing quality issues. It is important to clarify the typical schedule during the interview process.
Is the Quality Control Assistant role secure, or is it at risk from automation?
The job security for Quality Control Assistants is generally stable, as quality assurance remains critical across all industries. While automation may change some routine tasks, the need for human oversight, problem-solving, and decision-making in quality processes persists. As long as products are being manufactured or services delivered, there will be a demand for individuals to ensure quality standards are met.
What are the potential career growth opportunities for a Quality Control Assistant?
Career growth for Quality Control Assistants can lead to various advanced roles. Common pathways include becoming a Quality Control Technician, Quality Assurance Specialist, or even a Quality Manager with sufficient experience and further education. Opportunities also exist to specialize in areas like regulatory compliance, process improvement, or specific testing methodologies within your industry.
What are some of the most common challenges or frustrations in the Quality Control Assistant role?
A common challenge is the repetitive nature of some tasks, which requires unwavering attention to detail to avoid missing critical deviations. Another concern is handling pressure during peak production times or when a significant quality issue arises, requiring quick and accurate problem identification. Adapting to evolving quality standards and new technologies also presents a continuous learning challenge.
Can Quality Control Assistants work remotely, or is it primarily an on-site role?
Most Quality Control Assistant roles are on-site, as they often involve hands-on inspection, testing of physical products, or direct monitoring of production lines. Remote work is rare for this specific position due to the nature of the tasks. However, some administrative or data analysis aspects of quality control might offer limited hybrid options in more senior roles.
Related Careers
Explore similar roles that might align with your interests and skills:
Quality Assurance Assistant
A growing field with similar skill requirements and career progression opportunities.
Explore career guideQuality Control Associate
A growing field with similar skill requirements and career progression opportunities.
Explore career guideQuality Control Coordinator
A growing field with similar skill requirements and career progression opportunities.
Explore career guideQuality Control Specialist
A growing field with similar skill requirements and career progression opportunities.
Explore career guideQuality Control Technician
A growing field with similar skill requirements and career progression opportunities.
Explore career guideAssess your Quality Control Assistant readiness
Understanding where you stand today is the first step toward your career goals. Our Career Coach helps identify skill gaps and create personalized plans.
Skills Gap Analysis
Get a detailed assessment of your current skills versus Quality Control Assistant requirements. Our AI Career Coach identifies specific areas for improvement with personalized recommendations.
See your skills gapCareer Readiness Assessment
Evaluate your overall readiness for Quality Control Assistant roles with our AI Career Coach. Receive personalized recommendations for education, projects, and experience to boost your competitiveness.
Assess your readinessSimple pricing, powerful features
Upgrade to Himalayas Plus and turbocharge your job search.
Himalayas
Himalayas Plus
Himalayas Max
Find your dream job
Sign up now and join over 100,000 remote workers who receive personalized job alerts, curated job matches, and more for free!
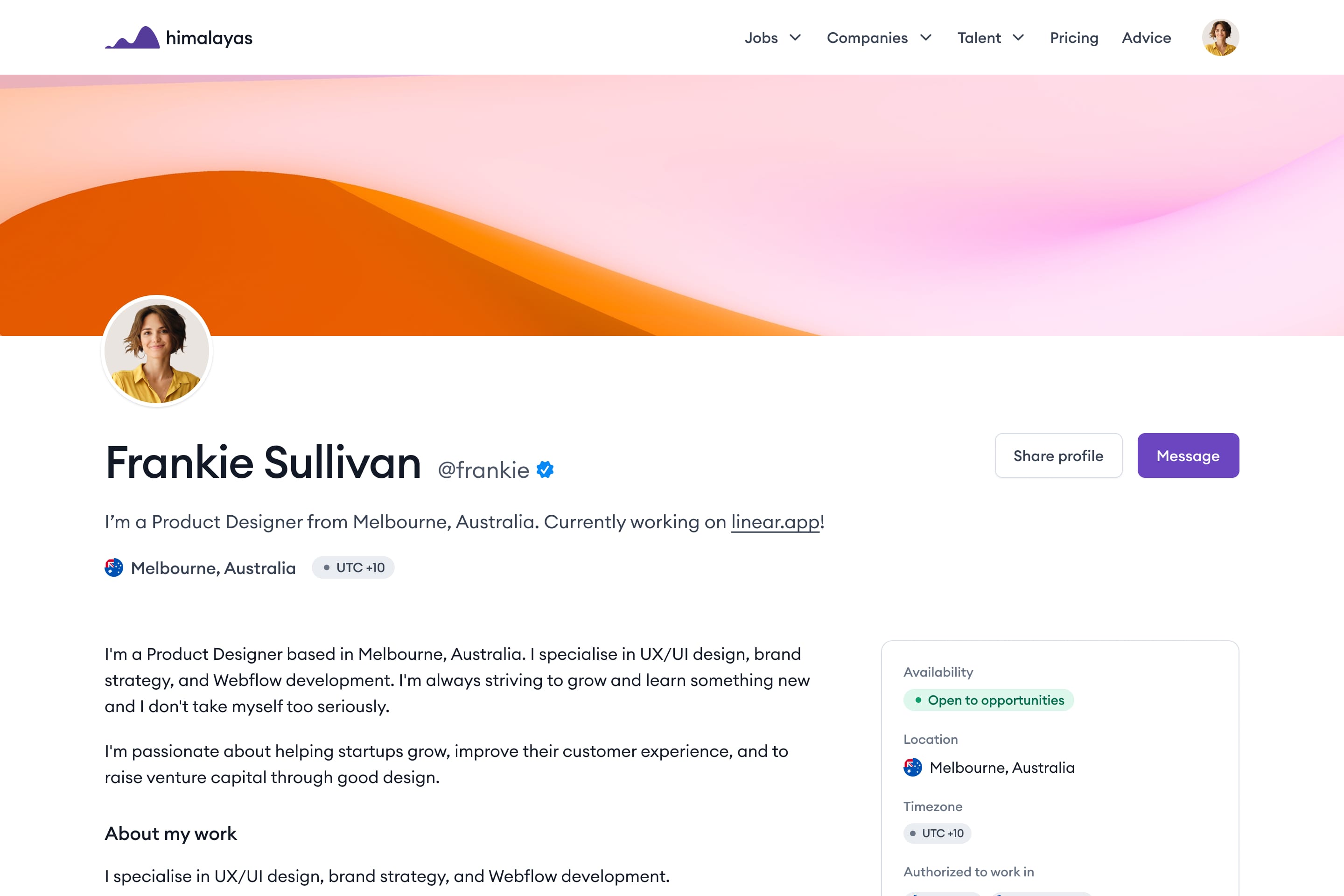