Complete Production Cost Estimator Career Guide
Production Cost Estimators are essential financial strategists, meticulously calculating the resources and expenses needed to bring products or projects to life. They play a critical role in profitability, ensuring companies can accurately bid on projects, manage budgets, and make informed decisions about production feasibility. This career path combines analytical rigor with industry knowledge, offering a stable and impactful role in various sectors.
Key Facts & Statistics
Median Salary
$73,760 USD
(U.S. Bureau of Labor Statistics, May 2023)
Range: $45k - $100k+ USD
Growth Outlook
6%
as fast as average (U.S. Bureau of Labor Statistics, 2022-2032)
Annual Openings
≈22
.2k openings annually (U.S. Bureau of Labor Statistics, 2022-2032)
Top Industries
Typical Education
Bachelor's degree in a related field like construction management, engineering, or finance; some positions accept an associate's degree or extensive experience.
What is a Production Cost Estimator?
A Production Cost Estimator is a specialized professional responsible for forecasting the expenses associated with manufacturing goods. This role involves meticulously calculating the total cost of producing a specific item or completing a production run, encompassing materials, labor, overhead, and other direct and indirect expenses. They provide crucial financial insights that help companies bid on projects, set competitive prices, and manage profitability.
Unlike a general Financial Analyst who might focus on broader company finances, or a Project Manager who oversees project execution, the Production Cost Estimator zeroes in specifically on the granular costs involved in the manufacturing process. Their expertise ensures that production initiatives are financially viable and that the company can accurately predict the financial impact of its manufacturing operations, optimizing resource allocation and identifying areas for cost reduction.
What does a Production Cost Estimator do?
Key Responsibilities
- Analyze blueprints, specifications, and other documentation to prepare time, cost, materials, and labor estimates for production projects.
- Collaborate with engineers, production managers, and sales teams to understand project scope and gather necessary data for accurate estimation.
- Evaluate supplier quotes and negotiate prices for raw materials, components, and outsourced services to optimize production costs.
- Develop and maintain a database of cost information, including historical data, supplier pricing, and labor rates, to improve future estimates.
- Identify potential cost-saving opportunities and recommend alternative materials or production methods without compromising quality or project requirements.
- Prepare detailed cost reports and presentations for management, outlining assumptions, risks, and profitability projections for proposed projects.
- Monitor actual project costs against estimates, identifying variances and adjusting future estimation models for greater accuracy and efficiency.
Work Environment
Production Cost Estimators typically work in a professional office environment, often within a manufacturing plant or corporate headquarters. Their work is primarily analytical and requires significant focus, but it also involves frequent collaboration. They regularly interact with engineers, production supervisors, sales personnel, and procurement teams to gather information and validate assumptions.
The pace of work can vary, with periods of intense deadline pressure when bidding on new projects or evaluating major production changes. While most work is performed during standard business hours, occasional extended hours may be necessary to meet critical deadlines. Remote work is increasingly common, though on-site visits to production floors or supplier facilities may occur periodically.
Tools & Technologies
Production Cost Estimators utilize a variety of software and tools to perform their duties efficiently. They frequently use enterprise resource planning (ERP) systems like SAP or Oracle for integrated data management, alongside specialized estimating software such as Sage Estimating or ProEst. Spreadsheet applications like Microsoft Excel are essential for detailed calculations, data analysis, and creating custom models.
They also work with CAD software (e.g., AutoCAD, SolidWorks) to interpret technical drawings and specifications. Communication and project management tools like Microsoft Teams, Jira, or Asana facilitate collaboration with cross-functional teams. Additionally, they often leverage databases and statistical software to analyze historical cost data and forecast future expenses.
Production Cost Estimator Skills & Qualifications
A Production Cost Estimator plays a crucial role in manufacturing, construction, and service industries by forecasting the costs associated with producing goods or delivering services. This involves analyzing blueprints, specifications, and other data to calculate labor, material, and overhead expenses. The role requires a blend of analytical rigor and industry-specific knowledge, prioritizing accuracy and detail to ensure competitive bidding and profitable project execution.
Requirements for Production Cost Estimators vary significantly based on the industry, company size, and project complexity. In manufacturing, a strong understanding of supply chains and production processes is paramount. Construction requires expertise in building codes and material sourcing. Larger companies often demand more specialized experience and formal education, while smaller firms might value practical experience and a proven track record over academic credentials. Geographic location can also influence requirements, with some regions having specific licensing or certification needs for certain types of estimation.
Formal education, such as a bachelor's degree, often provides a strong foundation, especially for entry-level roles in larger organizations. However, practical experience, particularly in a production or project management capacity, can be equally or more valuable for senior positions. Certifications, like those from the American Society of Professional Estimators (ASPE) or the Association for the Advancement of Cost Engineering (AACE International), significantly enhance credibility and demonstrate a commitment to professional standards. The skill landscape evolves with new technologies like AI-powered estimation software and advanced data analytics, making continuous learning essential to remain competitive.
Education Requirements
Technical Skills
- Cost estimation software (e.g., On-Screen Takeoff, Accubid, Sage Estimating, CostX)
- Blueprint reading and technical drawing interpretation (CAD, BIM software familiarity)
- Microsoft Excel (advanced functions, pivot tables, data modeling)
- Enterprise Resource Planning (ERP) systems (e.g., SAP, Oracle, NetSuite) for data extraction
- Material takeoff and quantity surveying techniques
- Labor cost analysis and productivity rate calculation
- Overhead and indirect cost allocation methods
- Statistical analysis and forecasting techniques
- Supply chain and procurement principles
- Risk assessment and contingency planning for cost estimation
- Database management fundamentals (SQL querying for cost data)
- Industry-specific regulations and standards (e.g., construction codes, manufacturing compliance)
Soft Skills
- Attention to Detail: Essential for scrutinizing specifications, identifying potential hidden costs, and ensuring the accuracy of complex calculations, as even small errors can lead to significant financial discrepancies.
- Analytical Thinking: Crucial for breaking down complex projects into manageable cost components, evaluating various factors (e.g., labor rates, material fluctuations, overhead), and identifying cost-saving opportunities.
- Problem-Solving: Important for addressing unexpected challenges in cost analysis, finding alternative solutions for material sourcing or production methods, and resolving discrepancies in data.
- Negotiation Skills: Key for interacting with suppliers, contractors, and internal stakeholders to secure favorable pricing for materials and services, directly impacting project profitability.
- Communication Skills: Vital for clearly presenting complex cost breakdowns, defending estimates to management or clients, and effectively collaborating with engineering, sales, and production teams.
- Time Management: Necessary for handling multiple projects simultaneously, meeting tight deadlines for bids, and ensuring estimates are delivered promptly to support business operations.
- Adaptability: Important for adjusting to changing project scopes, market conditions, and technology advancements that influence cost factors and estimation methodologies.
- Ethical Judgment: Crucial for maintaining integrity in cost reporting, ensuring fair and accurate estimates, and avoiding conflicts of interest in supplier relationships.
How to Become a Production Cost Estimator
Breaking into a Production Cost Estimator role involves various pathways, depending on your background and the industry you target. While a traditional degree in engineering, finance, or business administration is common, practical experience in manufacturing, construction, or a related trade can also provide a strong foundation. The timeline for entry can range from 6 months for those with direct industry experience and a strong quantitative background to 2 years for complete beginners who need to build foundational skills and a professional network.
Entry strategies vary significantly by company size and geographic location. Larger corporations might prefer candidates with formal degrees and certifications, offering structured training programs. Smaller firms or specialized agencies often prioritize hands-on experience and a proven ability to analyze complex data quickly. Networking within industry associations and seeking out mentorship are crucial, as many opportunities are filled through referrals rather than public job postings.
A common misconception is that this role is purely about number crunching; however, it deeply involves understanding production processes, supply chain dynamics, and market conditions. Building a portfolio of hypothetical or real-world cost analyses, even from personal projects, can significantly enhance your candidacy. This demonstrates your analytical capabilities and practical understanding, which is often more valuable than just academic qualifications.
Develop a strong foundation in mathematics, statistics, and financial accounting. Consider taking online courses or community college classes in these subjects if your background is not quantitative. Understanding these core principles is essential for accurately calculating costs and analyzing variances in production.
Gain practical experience in a production or manufacturing environment, even in an entry-level capacity. This could involve roles in quality control, inventory management, or as a production assistant. Direct exposure to the operational processes, materials, and labor involved in production provides invaluable context for accurate cost estimation.
Master essential software and tools relevant to cost estimation, such as Microsoft Excel for complex data analysis, enterprise resource planning (ERP) systems like SAP or Oracle, and specialized estimation software used in your target industry. Proficiency in these tools is often a non-negotiable requirement for employers.
Build a portfolio of sample cost estimation projects, even if they are hypothetical or based on publicly available data. For example, estimate the cost of producing a common household item, a small construction project, or a service. Document your assumptions, methodologies, and the breakdown of costs to showcase your analytical process.
Network with professionals in manufacturing, construction, and supply chain management by attending industry events, joining online forums, and connecting on platforms like LinkedIn. Informational interviews can provide insights into specific industry needs and potential job opportunities, often leading to referrals.
Prepare a targeted resume and cover letter highlighting your quantitative skills, practical experience, and software proficiencies. Customize each application to align with the specific industry and company requirements. Practice answering questions about your analytical process, problem-solving skills, and ability to handle complex data during interviews.
Step 1
Develop a strong foundation in mathematics, statistics, and financial accounting. Consider taking online courses or community college classes in these subjects if your background is not quantitative. Understanding these core principles is essential for accurately calculating costs and analyzing variances in production.
Step 2
Gain practical experience in a production or manufacturing environment, even in an entry-level capacity. This could involve roles in quality control, inventory management, or as a production assistant. Direct exposure to the operational processes, materials, and labor involved in production provides invaluable context for accurate cost estimation.
Step 3
Master essential software and tools relevant to cost estimation, such as Microsoft Excel for complex data analysis, enterprise resource planning (ERP) systems like SAP or Oracle, and specialized estimation software used in your target industry. Proficiency in these tools is often a non-negotiable requirement for employers.
Step 4
Build a portfolio of sample cost estimation projects, even if they are hypothetical or based on publicly available data. For example, estimate the cost of producing a common household item, a small construction project, or a service. Document your assumptions, methodologies, and the breakdown of costs to showcase your analytical process.
Step 5
Network with professionals in manufacturing, construction, and supply chain management by attending industry events, joining online forums, and connecting on platforms like LinkedIn. Informational interviews can provide insights into specific industry needs and potential job opportunities, often leading to referrals.
Step 6
Prepare a targeted resume and cover letter highlighting your quantitative skills, practical experience, and software proficiencies. Customize each application to align with the specific industry and company requirements. Practice answering questions about your analytical process, problem-solving skills, and ability to handle complex data during interviews.
Education & Training Needed to Become a Production Cost Estimator
Becoming a Production Cost Estimator requires a blend of analytical skills and industry-specific knowledge. Formal university degrees, such as a Bachelor's in Construction Management, Engineering, or Business with a focus on supply chain or operations, provide a strong theoretical foundation. These programs typically span four years and can cost between $40,000 and over $150,000, depending on the institution. They are often perceived as the most robust credential by larger corporations, offering in-depth understanding of production processes, materials, and financial modeling.
Alternative learning paths include specialized certifications, online courses, and self-study. Certifications in cost estimating or project management, often offered by professional associations, can be completed in 6-12 months and range from $1,000 to $5,000. These are highly valued for demonstrating specific competencies and are excellent for professionals looking to upskill or transition. While some employers prefer a degree, practical experience combined with a relevant certification can be equally compelling, especially in smaller to mid-sized firms.
Continuous learning is crucial for Production Cost Estimators. Industry trends, material costs, and technology evolve rapidly, requiring ongoing professional development. This includes workshops on new software, seminars on lean manufacturing, or advanced courses in data analytics. The cost-benefit analysis favors a structured approach: a degree for foundational knowledge and long-term career growth, and certifications for targeted skill enhancement and immediate career impact. Practical experience through internships or entry-level roles is vital, as theoretical knowledge alone does not suffice for accurate cost estimation in real-world production environments.
Production Cost Estimator Salary & Outlook
Compensation for a Production Cost Estimator varies significantly based on several key factors. Geographic location plays a crucial role; estimators in high cost-of-living areas or regions with robust manufacturing and construction industries typically command higher salaries. For instance, salaries in major metropolitan areas often exceed those in rural regions, reflecting local market demand and economic activity.
Years of experience and specialized industry knowledge dramatically influence earning potential. An estimator with expertise in complex manufacturing processes or large-scale construction projects can negotiate a premium. Total compensation extends beyond base salary, often including performance bonuses tied to accuracy and project savings, profit-sharing, and comprehensive benefits packages covering health, dental, and retirement contributions. Some roles might also offer professional development allowances for certifications or advanced training.
Industry-specific trends, such as supply chain volatility or technological advancements in estimation software, can drive salary growth. Companies value estimators who can accurately forecast costs, mitigate risks, and contribute to project profitability. Remote work opportunities also impact salary ranges, allowing some professionals to leverage geographic arbitrage, earning competitive salaries while residing in lower cost-of-living areas. These figures are generally in USD, though international markets will have their own distinct compensation structures.
Salary by Experience Level
Level | US Median | US Average |
---|---|---|
Junior Production Cost Estimator | $58k USD | $62k USD |
Production Cost Estimator | $75k USD | $78k USD |
Senior Production Cost Estimator | $92k USD | $95k USD |
Lead Production Cost Estimator | $110k USD | $115k USD |
Cost Estimation Manager | $130k USD | $135k USD |
Market Commentary
The job market for Production Cost Estimators remains stable with a steady demand, particularly in sectors experiencing growth such as advanced manufacturing, infrastructure development, and renewable energy. The U.S. Bureau of Labor Statistics projects a modest growth outlook for cost estimators, driven by the ongoing need for accurate financial planning in various industries. Companies continue to rely on precise cost projections to remain competitive and manage complex projects efficiently.
Emerging opportunities for Production Cost Estimators include specialization in sustainable building practices, digital construction, and the integration of artificial intelligence and machine learning tools for predictive analytics. These technological shifts are transforming the role, requiring estimators to adapt to new software and data analysis techniques. The ability to utilize Building Information Modeling (BIM) and other advanced estimation platforms is increasingly valued.
Supply and demand dynamics are relatively balanced, though a shortage of highly skilled estimators with specific industry experience or advanced technological proficiency can create competitive compensation packages. This role is generally resilient to economic downturns, as cost control remains critical even during periods of slow growth. Geographic hotspots for employment include industrial hubs and regions with significant infrastructure projects. Future-proofing this career involves continuous learning in new technologies, understanding global supply chain complexities, and honing analytical and negotiation skills.
Production Cost Estimator Career Path
Career progression for a Production Cost Estimator typically involves a clear path from foundational support roles to strategic leadership positions. Individuals generally start by assisting senior estimators, then advance to managing their own projects, and ultimately lead teams or entire departments. This progression demands a deep understanding of manufacturing processes, material costs, labor rates, and overheads, along with a keen eye for detail and strong analytical skills.
Advancement speed depends on several factors, including an individual's performance, the complexity of projects handled, and the specific industry. Estimators in high-volume, complex manufacturing environments often gain diverse experience more quickly. Specialization, such as expertise in specific materials or production technologies, can also accelerate progression. Moving from an individual contributor (IC) track, focused on direct estimation work, to a management track, which involves leading teams and strategic planning, marks a significant pivot. Lateral moves to roles like project management, supply chain analysis, or financial analysis are also common, leveraging an estimator's quantitative and process-oriented skills.
Company size significantly influences career paths. Larger corporations offer more structured progression paths and opportunities for specialization, while smaller companies or startups might provide broader responsibilities earlier, though with less formal advancement structures. Networking within the manufacturing and supply chain communities, seeking mentorship from experienced professionals, and maintaining an industry reputation for accuracy and reliability are crucial for long-term career growth. Certifications in cost engineering or project management, along with continuous learning about new production technologies and market trends, mark key milestones and enhance an estimator's value. Economic conditions and industry-specific demand for manufactured goods also influence opportunities.
Junior Production Cost Estimator
0-2 yearsAssist senior estimators by gathering data, inputting information into cost models, and preparing preliminary reports. Responsibilities include researching material prices, obtaining vendor quotes, and organizing documentation. Work is closely supervised, with a focus on learning established procedures and quality control.
Key Focus Areas
Develop foundational understanding of blueprints, specifications, and basic costing principles. Focus on data entry accuracy and learning various estimation software tools. Build strong communication skills for interacting with suppliers and internal teams. Understand the impact of different material types and manufacturing processes on cost.
Production Cost Estimator
2-5 yearsPrepare detailed cost estimates for production projects independently, from initial concept to final manufacturing. Manage multiple estimation projects simultaneously, ensuring accuracy and adherence to deadlines. Collaborate with engineering, purchasing, and production teams to validate assumptions and gather necessary data.
Key Focus Areas
Master various estimation methodologies, including parametric, analogous, and bottom-up costing. Enhance negotiation skills with suppliers and subcontractors. Develop a deeper understanding of overhead allocation and profit margin analysis. Begin to identify cost-saving opportunities and process improvements within production.
Senior Production Cost Estimator
5-8 yearsLead complex and high-value production cost estimation projects, often involving new product lines or significant process changes. Review and validate estimates prepared by junior colleagues, ensuring consistency and adherence to company standards. Present cost analyses and recommendations to cross-functional teams and management.
Key Focus Areas
Refine complex cost modeling and scenario analysis skills. Provide guidance and mentorship to junior estimators. Develop strong analytical capabilities to identify cost drivers and implement value engineering initiatives. Focus on improving estimation processes and accuracy across the department.
Lead Production Cost Estimator
8-12 yearsOversee a team of Production Cost Estimators, allocating projects and ensuring timely and accurate delivery of estimates. Act as a subject matter expert for complex costing challenges and provide technical guidance. Implement best practices and standardized procedures across the estimation function.
Key Focus Areas
Develop strong leadership and team coordination skills. Focus on strategic cost planning and long-range forecasting. Cultivate expertise in advanced data analytics and predictive modeling for cost estimation. Drive continuous improvement initiatives for the entire estimation process.
Cost Estimation Manager
12+ years total experienceLead the entire Cost Estimation department, setting strategic direction, developing policies, and managing budgets. Responsible for the accuracy and reliability of all production cost estimates, directly impacting profitability and business decisions. Recruit, train, and mentor a team of estimators, fostering a culture of continuous improvement and analytical excellence.
Key Focus Areas
Focus on strategic business acumen, financial planning, and risk management related to production costs. Develop strong leadership skills for managing a diverse team and influencing organizational strategy. Cultivate a broad understanding of supply chain dynamics, global economics, and market trends impacting production costs.
Junior Production Cost Estimator
0-2 yearsAssist senior estimators by gathering data, inputting information into cost models, and preparing preliminary reports. Responsibilities include researching material prices, obtaining vendor quotes, and organizing documentation. Work is closely supervised, with a focus on learning established procedures and quality control.
Key Focus Areas
Develop foundational understanding of blueprints, specifications, and basic costing principles. Focus on data entry accuracy and learning various estimation software tools. Build strong communication skills for interacting with suppliers and internal teams. Understand the impact of different material types and manufacturing processes on cost.
Production Cost Estimator
2-5 yearsPrepare detailed cost estimates for production projects independently, from initial concept to final manufacturing. Manage multiple estimation projects simultaneously, ensuring accuracy and adherence to deadlines. Collaborate with engineering, purchasing, and production teams to validate assumptions and gather necessary data.
Key Focus Areas
Master various estimation methodologies, including parametric, analogous, and bottom-up costing. Enhance negotiation skills with suppliers and subcontractors. Develop a deeper understanding of overhead allocation and profit margin analysis. Begin to identify cost-saving opportunities and process improvements within production.
Senior Production Cost Estimator
5-8 yearsLead complex and high-value production cost estimation projects, often involving new product lines or significant process changes. Review and validate estimates prepared by junior colleagues, ensuring consistency and adherence to company standards. Present cost analyses and recommendations to cross-functional teams and management.
Key Focus Areas
Refine complex cost modeling and scenario analysis skills. Provide guidance and mentorship to junior estimators. Develop strong analytical capabilities to identify cost drivers and implement value engineering initiatives. Focus on improving estimation processes and accuracy across the department.
Lead Production Cost Estimator
8-12 yearsOversee a team of Production Cost Estimators, allocating projects and ensuring timely and accurate delivery of estimates. Act as a subject matter expert for complex costing challenges and provide technical guidance. Implement best practices and standardized procedures across the estimation function.
Key Focus Areas
Develop strong leadership and team coordination skills. Focus on strategic cost planning and long-range forecasting. Cultivate expertise in advanced data analytics and predictive modeling for cost estimation. Drive continuous improvement initiatives for the entire estimation process.
Cost Estimation Manager
12+ years total experienceLead the entire Cost Estimation department, setting strategic direction, developing policies, and managing budgets. Responsible for the accuracy and reliability of all production cost estimates, directly impacting profitability and business decisions. Recruit, train, and mentor a team of estimators, fostering a culture of continuous improvement and analytical excellence.
Key Focus Areas
Focus on strategic business acumen, financial planning, and risk management related to production costs. Develop strong leadership skills for managing a diverse team and influencing organizational strategy. Cultivate a broad understanding of supply chain dynamics, global economics, and market trends impacting production costs.
Job Application Toolkit
Ace your application with our purpose-built resources:
Production Cost Estimator Resume Examples
Proven layouts and keywords hiring managers scan for.
View examplesProduction Cost Estimator Cover Letter Examples
Personalizable templates that showcase your impact.
View examplesTop Production Cost Estimator Interview Questions
Practice with the questions asked most often.
View examplesProduction Cost Estimator Job Description Template
Ready-to-use JD for recruiters and hiring teams.
View examplesGlobal Production Cost Estimator Opportunities
Production Cost Estimators analyze manufacturing processes and material costs globally. This role is crucial in competitive international markets, with high demand in regions with strong manufacturing sectors like Asia and Europe. Professionals understand diverse regulatory frameworks and supply chain logistics, enabling them to optimize production expenses across borders. International certifications in cost management enhance global career prospects.
Global Salaries
Production Cost Estimator salaries vary significantly by region and industry. In North America, particularly the U.S., annual salaries typically range from $60,000 to $95,000 USD, reflecting a higher cost of living. Canadian estimators earn between $55,000 and $85,000 CAD (approximately $40,000-$62,000 USD).
European salaries differ by country. In Germany, a major manufacturing hub, estimators earn €50,000 to €75,000 EUR (approximately $54,000-$81,000 USD). The UK sees ranges of £40,000 to £60,000 GBP (approximately $50,000-$75,000 USD). Eastern European countries offer lower nominal salaries, for example, Poland at PLN 70,000 to PLN 120,000 (approximately $17,500-$30,000 USD), but purchasing power parity can make these competitive locally.
Asia-Pacific markets present diverse compensation. Australian estimators typically earn AUD 70,000 to AUD 100,000 (approximately $46,000-$66,000 USD). In China, salaries are lower, often RMB 150,000 to RMB 250,000 (approximately $21,000-$35,000 USD), but reflect a much lower cost of living. Salary structures also differ; European countries often include more robust social benefits and vacation time compared to North America. Tax implications significantly affect take-home pay, with some European nations having higher income tax rates. Experience and specialized industry knowledge directly influence compensation in all markets.
Remote Work
Production Cost Estimators often find remote work opportunities, especially in industries with digitalized workflows. Many companies, particularly those with global supply chains, hire estimators to work from various locations. Legal and tax implications require careful consideration; individuals must understand tax residency rules and potential dual taxation agreements. Time zone differences can pose challenges for international team collaboration, necessitating flexible work schedules.
Digital nomad visas are emerging in countries like Portugal and Estonia, offering pathways for estimators to live and work remotely for foreign companies. Some companies offer geo-adjusted salaries, meaning compensation aligns with the cost of living in the estimator's location, rather than the employer's headquarters. Platforms like LinkedIn and specialized industry job boards often list international remote roles. Reliable internet, a dedicated workspace, and appropriate software are essential for successful remote work.
Visa & Immigration
Production Cost Estimators typically qualify for skilled worker visas in many countries. Popular destinations include Canada, Australia, Germany, and the UK. These nations often require a job offer, relevant experience, and sometimes, a recognized degree or professional qualification. For instance, Canada's Express Entry system assesses points for age, education, experience, and language proficiency. Germany's Blue Card requires a university degree and a minimum salary.
Credential recognition is important; some countries may require an assessment of foreign qualifications. Visa application timelines vary, generally taking from a few months to over a year. Pathways to permanent residency often exist after several years of skilled employment. English language proficiency tests, like IELTS or TOEFL, are commonly required for English-speaking countries. For non-English speaking countries, basic proficiency in the local language can be beneficial for integration but is not always a strict visa requirement. Intra-company transfers are also common for estimators working for multinational corporations.
2025 Market Reality for Production Cost Estimators
Understanding current market conditions is vital for Production Cost Estimators navigating career paths. The field has seen significant shifts since 2023, influenced by global economic volatility and rapid technological advancements like AI.
Broader economic factors, such as inflation and interest rate changes, directly impact project viability and material costs, fundamentally altering an estimator's daily work. Market realities for this role also vary by industry, with construction differing from manufacturing, and by company size, where large corporations may have specialized teams versus smaller firms needing versatile estimators. This analysis provides an honest assessment of these dynamics.
Current Challenges
Significant competition faces Production Cost Estimators, particularly for remote roles, as companies seek to optimize budgets by requiring fewer on-site personnel. Economic slowdowns directly reduce project pipelines, leading to fewer estimation needs. Automation in initial project scoping also shifts the demand for human estimators towards more complex, custom projects, requiring higher-level analytical skills.
Growth Opportunities
Despite challenges, strong demand exists for Production Cost Estimators specializing in niche areas like sustainable manufacturing, circular economy projects, or custom, high-complexity engineering. These roles require deep domain knowledge that AI tools cannot yet replicate fully.
Professionals can gain a competitive edge by mastering advanced data analytics tools and integrating AI-driven insights into their workflows. Certifications in specific industry standards or project management also enhance marketability. Underserved markets in emerging economies or specialized sectors like aerospace and defense often present better opportunities due to unique regulatory and technical requirements.
Estimators who can consult on cost-saving strategies, rather than just report numbers, are increasingly valuable. Developing skills in value engineering, supply chain optimization, and risk management transforms the role into a strategic business partner. Investing in continuous learning about new materials and manufacturing processes positions estimators for long-term career growth, especially as industries evolve rapidly.
Current Market Trends
Demand for Production Cost Estimators remains stable, but the nature of the role is evolving. Companies increasingly value estimators who understand advanced manufacturing techniques and global supply chain intricacies. The post-pandemic era emphasized resilient supply chains, making estimators with experience in diverse material sourcing and logistics highly sought after.
Generative AI tools are changing how initial estimates are produced, automating routine calculations and data aggregation. This means estimators now focus more on risk analysis, value engineering, and strategic cost reduction rather than just number crunching. Employers prioritize candidates who can interpret complex data sets and provide strategic insights, moving beyond basic spreadsheet proficiency.
Salaries for experienced estimators are growing, especially for those in specialized fields like renewable energy or advanced robotics manufacturing. However, entry-level positions face more competition as automation handles simpler tasks. Remote work is common for this role, expanding the talent pool but also increasing competition across geographic boundaries. Seasonal fluctuations often align with project lifecycles, with higher demand during planning phases and year-end budget finalizations.
Emerging Specializations
The role of a Production Cost Estimator is evolving rapidly, driven by advancements in digital technologies and a global emphasis on sustainability. Traditional estimation methods are being augmented, and sometimes replaced, by data-driven approaches that offer greater precision and foresight. Understanding these shifts is crucial for professionals aiming to future-proof their careers.
Early positioning in emerging specializations offers significant advantages for career advancement in 2025 and beyond. These cutting-edge areas often command premium compensation due to the specialized knowledge and skills required. While established specializations remain vital, focusing on emerging fields allows estimators to become pioneers, shaping new industry standards and practices.
Many emerging areas, particularly those integrating AI or sustainability metrics, are transitioning from niche interests to mainstream requirements. This shift creates a substantial number of job opportunities as industries recognize the competitive edge these capabilities provide. However, pursuing these areas involves a balance of risk and reward; while the potential for growth is high, it requires continuous learning and adaptation to evolving tools and methodologies.
The timeline for emerging areas to become mainstream varies, but many show signs of significant adoption within three to five years. Strategic estimators should identify these trends early, investing in skill development now to capitalize on future demand. This proactive approach ensures relevance and leadership in a dynamic professional landscape.
Sustainability-Driven Cost Estimator
This specialization focuses on estimating costs for products and processes designed with environmental impact and circular economy principles in mind. It involves assessing the entire lifecycle cost, from sustainable material sourcing and energy-efficient production to end-of-life recycling or disposal. As regulatory pressures and consumer demand for eco-friendly products grow, estimators who can accurately model these complex costs become indispensable for businesses pursuing green initiatives and achieving carbon neutrality.
AI-Powered Predictive Estimator
This area involves leveraging AI and machine learning algorithms to analyze vast datasets and predict production costs with unprecedented accuracy. Estimators in this field develop, train, and refine predictive models, moving beyond traditional spreadsheet-based calculations. They identify hidden cost drivers, optimize resource allocation, and forecast market fluctuations, providing strategic insights that minimize waste and maximize profitability. This shift from reactive to proactive estimation is transforming decision-making processes.
Advanced Manufacturing Cost Analyst
Specializing in the cost estimation of advanced manufacturing processes, such as additive manufacturing (3D printing), robotics, and automation, is becoming critical. This involves understanding the unique material, energy, and labor costs associated with highly automated or novel production techniques. Estimators must account for factors like machine uptime, raw material purity, and post-processing requirements, which differ significantly from conventional manufacturing. Their expertise enables companies to scale new production methods efficiently and cost-effectively.
Digital Supply Chain Cost Modeler
This specialization focuses on estimating costs within highly integrated, digitally connected supply chains. It involves analyzing the financial implications of IoT-enabled tracking, blockchain for transparency, and real-time data analytics across the entire supply network. Estimators here assess the costs and benefits of digital transformation initiatives, including potential savings from optimized logistics, reduced inventory, and improved demand forecasting. They play a key role in making smart factory and supply chain digitization projects financially viable.
Industrial Cybersecurity Cost Estimator
This emerging field focuses on estimating the costs associated with implementing and maintaining cybersecurity measures within production environments. As operational technology (OT) networks become increasingly interconnected, the financial risks of cyberattacks on production lines, intellectual property, and data integrity escalate. Estimators must assess the costs of security hardware, software, audits, training, and potential downtime from breaches. This specialized knowledge helps organizations budget effectively for robust industrial cybersecurity defenses.
Pros & Cons of Being a Production Cost Estimator
Making an informed career choice requires understanding both the benefits and challenges of a profession. The experience of a Production Cost Estimator can vary significantly based on the industry, company culture, and specific projects undertaken. What one person considers a pro, another might see as a con, influenced by personal values and lifestyle preferences. This assessment aims to provide a realistic overview, acknowledging that early career stages might present different challenges and opportunities compared to mid or senior-level positions. By examining both the upsides and the difficulties, job seekers can set appropriate expectations and determine if this career path aligns with their aspirations and capabilities.
Pros
Production Cost Estimators are in high demand across diverse industries such as manufacturing, construction, and engineering, ensuring strong job security and a wide range of employment opportunities.
The role requires analytical thinking and problem-solving skills to break down complex projects into quantifiable components, offering intellectual stimulation for those who enjoy detailed analysis and logical challenges.
Gaining deep insight into various production processes, materials, and labor requirements across different projects provides a comprehensive understanding of operational efficiency and business economics.
Accurate cost estimates directly contribute to a company's profitability and competitiveness, offering a tangible sense of impact and value to the organization's financial success.
The ability to work independently on detailed analyses is often a core component of the role, providing autonomy and the chance to manage one's own workload effectively.
Opportunities exist for continuous professional development through learning about new materials, technologies, and production methods, keeping the role dynamic and preventing stagnation.
Many roles offer stable work hours, typically adhering to standard business hours, which can contribute to a predictable work-life balance compared to roles with frequent travel or unpredictable schedules.
Cons
Working as a Production Cost Estimator often involves tight deadlines, especially when bids are competitive or project timelines are aggressive, leading to periods of high stress and pressure to deliver accurate figures quickly.
Requires meticulous attention to detail; even small errors in calculations, material quantities, or labor rates can significantly impact the overall estimate, potentially leading to financial losses for the company or lost bids.
The role can be repetitive, involving similar calculation methods and data analysis for various projects, which might become monotonous for individuals seeking more dynamic or creative work.
Market fluctuations in material costs, labor rates, and supply chain availability constantly change, requiring estimators to continuously update their knowledge and data sources, which can be time-consuming and challenging.
There is a significant responsibility to ensure estimates are both competitive and profitable; misjudging market conditions or internal capabilities can directly affect a company's success or failure in securing contracts.
Dealing with incomplete or ambiguous project specifications from clients or internal teams is common, necessitating frequent clarification and making accurate estimation more difficult and time-consuming.
Career progression might be limited to senior estimating roles or moving into project management; the specialized nature of the role means horizontal shifts into other departments can be less straightforward without additional training.
Frequently Asked Questions
Production Cost Estimators face unique challenges in balancing detailed material and labor costs with market fluctuations and project timelines. This section addresses the most pressing questions about entering this specialized role, from necessary analytical skills to understanding industry-specific software and career progression.
What educational background and experience are typically required to become a Production Cost Estimator?
Entry into production cost estimating often requires a bachelor's degree in a field like engineering, construction management, finance, or business administration. Many successful estimators also have backgrounds in manufacturing, supply chain, or project management, bringing practical experience to the role. Strong analytical skills and attention to detail are more critical than a specific degree.
How long does it take to become job-ready as a Production Cost Estimator if I'm starting from scratch?
Becoming proficient as a Production Cost Estimator can take 1-3 years of dedicated learning and on-the-job experience. Initial training focuses on understanding industry standards, software proficiency, and cost breakdown methodologies. Gaining expertise in specific production processes and developing a keen eye for potential cost drivers takes more time. Many estimators start in related roles, gaining practical experience before specializing.
What are the typical salary expectations for a Production Cost Estimator at different career stages?
Salaries for Production Cost Estimators vary significantly by industry, experience, and location. Entry-level positions might range from $45,000 to $65,000 annually. Mid-career estimators with 5-10 years of experience often earn between $60,000 and $90,000, while senior or specialized estimators can exceed $100,000. These figures depend on the complexity of projects and the size of the company.
Is the job market for Production Cost Estimators stable, or is it prone to significant fluctuations?
The job market for Production Cost Estimators remains stable, driven by the continuous need for accurate budgeting and financial planning across manufacturing, construction, and other production-heavy industries. Economic fluctuations can impact project volumes, but the core function of cost control ensures ongoing demand. Companies always seek to optimize expenses, making this a valuable and secure role.
What is the typical work-life balance like for a Production Cost Estimator, especially during busy periods?
Production Cost Estimators often work standard office hours, typically 40 hours per week. However, workload can increase significantly during peak bidding periods or when tight project deadlines approach. This might require occasional overtime to ensure accurate and timely submissions. The role balances routine tasks with periods of intense focus and pressure.
What are the typical career progression opportunities for a Production Cost Estimator?
Career growth paths for Production Cost Estimators include advancing to Senior Estimator, Chief Estimator, or moving into project management, procurement, or financial analysis roles. Some estimators specialize in specific industries or complex project types. Developing strong leadership, negotiation, and communication skills opens doors to management positions overseeing estimation teams.
What are the biggest challenges or frustrations that Production Cost Estimators commonly face in their role?
The biggest challenge for Production Cost Estimators is often managing uncertainty and external variables that impact costs, such as material price volatility, labor availability, and unforeseen design changes. It requires constant vigilance and adaptability to provide accurate estimates in dynamic environments. Communicating complex cost breakdowns to non-technical stakeholders also presents a regular challenge.
Related Careers
Explore similar roles that might align with your interests and skills:
Construction Estimator
A growing field with similar skill requirements and career progression opportunities.
Explore career guideCost Estimator
A growing field with similar skill requirements and career progression opportunities.
Explore career guideProject Estimator
A growing field with similar skill requirements and career progression opportunities.
Explore career guideConstruction Job Cost Estimator
A growing field with similar skill requirements and career progression opportunities.
Explore career guideJob Estimator
A growing field with similar skill requirements and career progression opportunities.
Explore career guideAssess your Production Cost Estimator readiness
Understanding where you stand today is the first step toward your career goals. Our Career Coach helps identify skill gaps and create personalized plans.
Skills Gap Analysis
Get a detailed assessment of your current skills versus Production Cost Estimator requirements. Our AI Career Coach identifies specific areas for improvement with personalized recommendations.
See your skills gapCareer Readiness Assessment
Evaluate your overall readiness for Production Cost Estimator roles with our AI Career Coach. Receive personalized recommendations for education, projects, and experience to boost your competitiveness.
Assess your readinessLand your dream job with Himalayas Plus
Upgrade to unlock Himalayas' premium features and turbocharge your job search.
Himalayas
Himalayas Plus
Himalayas Max
Find your dream job
Sign up now and join over 100,000 remote workers who receive personalized job alerts, curated job matches, and more for free!
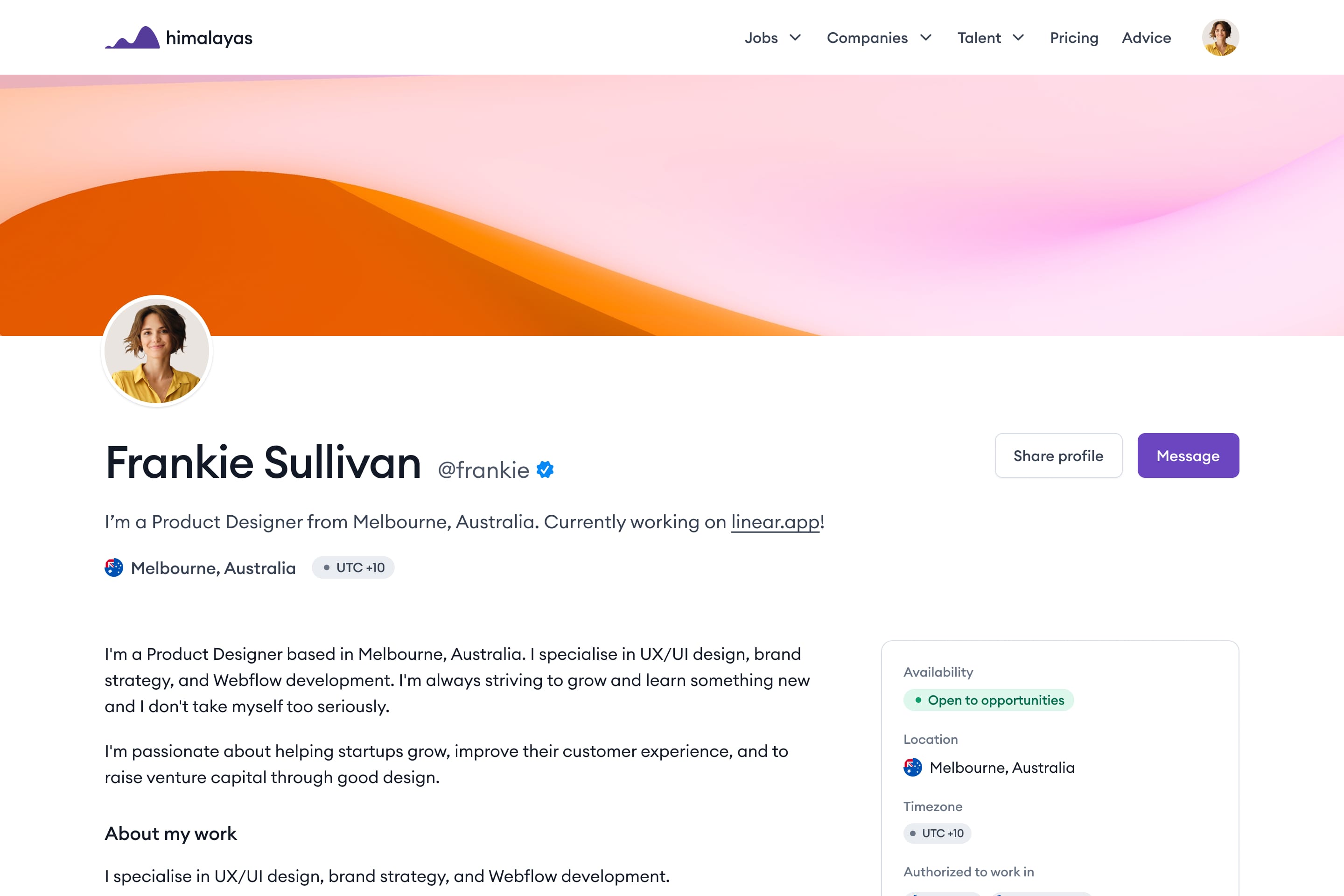