Complete Production Control Coordinating Clerk Career Guide
Production control coordinating clerks are the unsung heroes of manufacturing, ensuring every component and process aligns to meet production targets efficiently. They orchestrate the flow of materials and information, preventing bottlenecks and keeping operations running smoothly. This role offers a vital entry point into industrial operations, blending administrative precision with real-time problem-solving to optimize output.
Key Facts & Statistics
Median Salary
$50,210 USD
(U.S. national median, BLS, May 2023)
Range: $35k - $70k+ USD
Growth Outlook
Annual Openings
≈34k
openings annually (BLS, 2022-2032)
Top Industries
Typical Education
High school diploma or equivalent; some postsecondary education or related experience preferred
What is a Production Control Coordinating Clerk?
A Production Control Coordinating Clerk serves as a vital link in the manufacturing supply chain, ensuring that production processes run smoothly and efficiently. This role focuses on the administrative and logistical coordination required to move raw materials through production to finished goods. They are responsible for monitoring schedules, tracking inventory, and facilitating communication between different departments to prevent delays and optimize output.
Unlike a Production Scheduler who designs the overall production plan, or a Materials Planner who focuses solely on procuring raw materials, the Coordinating Clerk executes and monitors these plans at an operational level. They troubleshoot day-to-day issues, update records, and ensure that the right materials are available at the right time for production to proceed without interruption. This role is crucial for maintaining production flow and meeting delivery targets.
What does a Production Control Coordinating Clerk do?
Key Responsibilities
- Monitor production schedules and material requirements to ensure timely completion of orders.
- Track the flow of materials through various production stages, updating inventory and production records.
- Communicate with production supervisors, purchasing, and shipping departments regarding schedule changes or material shortages.
- Prepare and distribute production work orders, routing sheets, and other necessary documentation.
- Resolve discrepancies in material availability or production progress by coordinating with relevant teams.
- Maintain accurate records of production output, material usage, and finished goods inventory.
- Assist in identifying bottlenecks or inefficiencies in the production process and suggest improvements to the Production Control Manager or Supervisor.
Work Environment
Production Control Coordinating Clerks typically work in an office setting within a manufacturing or production facility. Their environment is often fast-paced and requires constant communication with various departments, including the production floor, purchasing, and shipping.
Collaboration is key, as they frequently interact with team members to resolve issues and coordinate activities. The work schedule is usually full-time during regular business hours, but occasional overtime may be necessary to meet production deadlines or address urgent issues. The role demands attention to detail and the ability to manage multiple priorities in a dynamic environment.
Tools & Technologies
Production Control Coordinating Clerks primarily use Enterprise Resource Planning (ERP) systems like SAP, Oracle NetSuite, or Microsoft Dynamics 365 to manage production data, inventory, and scheduling. They also frequently utilize Material Requirements Planning (MRP) software to plan and control material flows.
Spreadsheet software such as Microsoft Excel or Google Sheets is essential for tracking, reporting, and basic data analysis. Communication tools like email, Microsoft Teams, or Slack facilitate daily interactions. Depending on the industry, they might also use specific manufacturing execution systems (MES) or warehouse management systems (WMS) to monitor real-time production and inventory movements.
Production Control Coordinating Clerk Skills & Qualifications
The Production Control Coordinating Clerk plays a critical role in ensuring the smooth flow of manufacturing operations. This position primarily focuses on the administrative and coordination aspects of production, differing from a Production Planner who strategizes, or a Production Supervisor who manages personnel. Success in this role hinges on meticulous attention to detail, strong organizational abilities, and the capacity to manage multiple data streams efficiently.
Requirements for this role vary significantly based on the industry and the size of the manufacturing facility. In large-scale automotive or aerospace manufacturing, the emphasis shifts towards enterprise resource planning (ERP) system proficiency and strict adherence to regulatory compliance. Smaller operations might prioritize adaptability and a broader range of administrative capabilities. Experience often outweighs formal education, especially for entry-level positions, though a vocational certificate or an Associate's degree can accelerate career progression. Many individuals enter this field with strong administrative backgrounds and acquire industry-specific knowledge on the job.
The skill landscape for Production Control Coordinating Clerks is evolving with increased automation and data analytics. While foundational administrative skills remain crucial, a growing demand exists for proficiency in digital tools and data interpretation. Certifications in supply chain management or production control, while not always mandatory, significantly enhance a candidate's profile and demonstrate a commitment to professional development. Understanding the balance between immediate operational needs and long-term production schedules is vital for prioritizing learning efforts.
Education Requirements
Technical Skills
- Enterprise Resource Planning (ERP) Systems (e.g., SAP, Oracle, Microsoft Dynamics) for data entry and report generation
- Inventory Management Software for tracking parts and materials
- Microsoft Excel for data analysis, reporting, and basic spreadsheet manipulation (formulas, pivot tables)
- Production Scheduling Software (e.g., MES systems) for monitoring and updating production progress
- Data Entry and Management for maintaining accurate records of production orders, inventory levels, and shipments
- Documentation and Record Keeping for maintaining compliance records, work orders, and production logs
- Basic understanding of manufacturing processes and terminology (e.g., Bill of Materials, lead times, work orders)
- Quality Control Procedures for ensuring accuracy in documentation and material handling
- Email and Calendar Management for coordinating with various departments and external vendors
- Database Querying (basic SQL or similar) for extracting specific production data
- Barcode Scanning and Labeling Systems for inventory and production tracking
- Supply Chain Basics for understanding material flow from procurement to finished goods
Soft Skills
- Organizational Skills: Manages multiple tasks, documents, and schedules efficiently to maintain order in complex production environments.
- Attention to Detail: Identifies discrepancies in production schedules, inventory reports, and material lists, preventing costly errors.
- Problem-Solving: Addresses immediate operational issues, such as missing parts or scheduling conflicts, by finding practical, quick solutions.
- Communication Skills: Clearly conveys information to production teams, suppliers, and management regarding schedules, delays, and material needs.
- Adaptability: Adjusts quickly to changes in production demands, material availability, or unexpected operational disruptions.
- Time Management: Prioritizes tasks effectively to meet critical production deadlines and ensure timely material flow.
- Customer Service Orientation: Supports internal stakeholders (e.g., production lines, planning department) with a helpful and responsive attitude.
- Proactiveness: Identifies potential issues before they escalate, such as impending material shortages or schedule clashes, and takes preventative action.
How to Become a Production Control Coordinating Clerk
Entering the Production Control Coordinating Clerk field offers multiple pathways, catering to individuals with diverse backgrounds. While some roles might prefer an associate's degree in business or supply chain management, many entry-level positions prioritize practical administrative skills, attention to detail, and a strong work ethic. You can often break into this field through internal promotions from roles like administrative assistant or inventory clerk, or by applying directly to companies that value on-the-job training.
The timeline for entry varies; a complete beginner might secure a role within 3-6 months by focusing on skill acquisition and targeted applications. Career changers with transferable skills in data entry, scheduling, or logistics could find opportunities within 2-4 months. Geographic location and industry sector also play a significant role; manufacturing hubs or large logistics centers will have more openings than smaller markets. Companies of all sizes, from small local factories to large multinational corporations, employ Production Control Coordinating Clerks, each offering different work environments and advancement opportunities.
A common misconception is that extensive manufacturing experience is always necessary. While helpful, many employers seek candidates who are highly organized, proficient with office software, and eager to learn industry-specific processes. Building a strong resume that highlights your organizational abilities, data management skills, and problem-solving aptitude is crucial. Networking within local manufacturing or supply chain communities can also uncover hidden opportunities and provide valuable insights into specific company needs.
Step 1
Step 2
Step 3
Step 4
Step 5
Step 6
Education & Training Needed to Become a Production Control Coordinating Clerk
The Production Control Coordinating Clerk role primarily focuses on administrative and organizational tasks within a manufacturing or production environment. This position involves managing production schedules, tracking inventory, and coordinating material flow. Formal four-year degrees in supply chain management or business administration are beneficial, typically costing $40,000-$100,000+ over four years, but are not always mandatory. Many employers accept candidates with a high school diploma supplemented by specific certifications or relevant work experience.
Alternative learning paths, such as vocational training, community college associate degrees, or specialized certifications, offer more direct routes into this role. Associate degrees in logistics or production management typically cost $5,000-$15,000 and take two years. Online courses and self-study options, focusing on inventory management software or production planning basics, can range from free to a few hundred dollars, completed in 6-18 months. These alternatives often prioritize practical skills over theoretical knowledge, which employers value for this hands-on position.
Employer acceptance of credentials varies; larger corporations might prefer an associate's degree or a certification, while smaller businesses may prioritize experience. Continuous learning in areas like lean manufacturing principles, enterprise resource planning (ERP) systems, or advanced Excel skills is crucial for career advancement. Practical experience, even through internships or entry-level roles, often outweighs theoretical knowledge in this field. Industry-specific certifications, such as those from APICS, enhance credibility and demonstrate a commitment to professional standards. These certifications typically require a few months of study and cost $500-$1,500.
Production Control Coordinating Clerk Salary & Outlook
Compensation for a Production Control Coordinating Clerk varies significantly based on several key factors. Geographic location plays a crucial role; areas with higher costs of living or a strong manufacturing presence typically offer higher salaries. For instance, clerks in major industrial hubs like the Midwest or Southeast may see different pay scales compared to those in less industrialized regions.
Experience levels dramatically impact earning potential. Entry-level clerks earn less than those with several years of specialized experience in complex production environments. Furthermore, specific skill sets, such as proficiency with advanced Enterprise Resource Planning (ERP) systems or supply chain management software, can command premium compensation.
Total compensation packages extend beyond base salary. They often include performance bonuses, which are common in manufacturing to incentivize efficiency and on-time delivery. Benefits such as health insurance, retirement contributions like 401k matching, and paid time off are standard. Some companies also offer professional development allowances for certifications in areas like Lean Manufacturing or Six Sigma, enhancing long-term career value.
Industry-specific trends also shape salaries. Clerks in high-demand, precision manufacturing sectors, such as aerospace or medical devices, might earn more due to the stringent requirements and value of their coordination. Company size also matters; larger corporations often have more structured pay scales and comprehensive benefits. While remote work is less common for this role due to the hands-on nature of production coordination, some administrative tasks might be flexible, but core functions require on-site presence. International variations mean salaries provided are in USD, and local market conditions globally will differ significantly.
Salary by Experience Level
Level | US Median | US Average |
---|---|---|
Junior Production Control Coordinating Clerk | $38k USD | $42k USD |
Production Control Coordinating Clerk | $52k USD | $55k USD |
Senior Production Control Coordinating Clerk | $65k USD | $68k USD |
Lead Production Control Coordinator | $75k USD | $78k USD |
Market Commentary
The job market for Production Control Coordinating Clerks shows stable demand, primarily driven by the ongoing need for efficient manufacturing and supply chain operations. As of 2025, the outlook for this role is steady, with projected growth closely tied to the health of the manufacturing sector. The Bureau of Labor Statistics (BLS) indicates a moderate growth rate for production and operating occupations, which includes this role, as companies continue to optimize their output.
Emerging opportunities for these clerks stem from increased adoption of advanced manufacturing technologies, including automation and IoT. This requires clerks to adapt to digital systems that track production in real-time, shifting their focus from manual data entry to data analysis and system oversight. Proficiency in these digital tools creates a competitive advantage.
The supply and demand dynamics for this role are generally balanced. While the manufacturing sector faces some labor shortages in skilled trades, the administrative and coordination aspects of this role remain essential. Future-proofing involves continuous learning in new software platforms and understanding lean manufacturing principles. Automation, while impacting some manual tasks, is more likely to augment the clerk's role by providing better data, rather than fully replacing it.
This profession is relatively resilient, as manufacturing is a foundational economic activity, though it can be sensitive to economic downturns that impact consumer demand. Geographic hotspots for these roles align with manufacturing centers across the U.S., such as the industrial Midwest, parts of the Southeast, and specific West Coast regions with strong aerospace or technology manufacturing. The role's evolution requires clerks to become more analytical and technologically proficient to maintain relevance.
Production Control Coordinating Clerk Career Path
Career progression for a Production Control Coordinating Clerk typically involves a deep immersion into operational logistics and supply chain intricacies. Professionals advance by mastering inventory management, scheduling, and data analysis, moving from support functions to more autonomous and strategic roles. Advancement often hinges on an individual's ability to optimize processes, reduce waste, and improve efficiency across production workflows.
Progression can follow either an individual contributor (IC) track, focusing on specialized expertise and complex problem-solving, or a management track, emphasizing team leadership and broader operational oversight. Factors influencing advancement speed include demonstrated performance in meeting production targets, the ability to implement process improvements, and successful cross-functional collaboration. Company size and industry sector also play a role; larger corporations might offer more structured advancement paths, while smaller firms could provide quicker opportunities for broader responsibility.
Lateral movement opportunities exist within related fields such as supply chain analysis, logistics management, or procurement, allowing for diverse skill development. Networking with peers, mentors, and industry professionals is crucial for identifying new opportunities and staying current with best practices. Certifications in supply chain management or lean manufacturing can significantly bolster a clerk's profile and accelerate progression.
Junior Production Control Coordinating Clerk
0-2 yearsThis entry-level role supports the production control team by performing routine administrative and data entry tasks. Responsibilities include maintaining inventory records, processing material requests, and assisting with basic production schedule updates. The clerk operates under close supervision, ensuring data integrity and adherence to established procedures.
Key Focus Areas
Key development areas include mastering inventory tracking systems, understanding basic production scheduling principles, and developing strong data entry accuracy. Focus on foundational communication skills to interact with production teams and suppliers effectively. Learning to identify and report discrepancies in material flow is also critical.
Production Control Coordinating Clerk
2-4 yearsA Production Control Coordinating Clerk independently manages specific segments of the production schedule and inventory. This role involves coordinating material delivery, monitoring production progress against plans, and resolving minor logistical issues. They ensure timely availability of components and finished goods, contributing directly to operational flow.
Key Focus Areas
Develop proficiency in production planning software and advanced inventory management techniques. Enhance problem-solving skills to address scheduling conflicts and material shortages proactively. Strengthen communication and negotiation abilities for effective coordination with internal departments and external vendors.
Senior Production Control Coordinating Clerk
4-7 yearsThe Senior Production Control Coordinating Clerk takes ownership of complex production control functions, including master scheduling and capacity planning. This role involves analyzing production data to identify trends, forecast demand, and implement process improvements. They act as a key liaison between production, purchasing, and sales departments, ensuring alignment of operational goals.
Key Focus Areas
Cultivate advanced analytical skills to identify bottlenecks and optimize production processes. Focus on strategic planning for material procurement and production capacity. Develop leadership qualities by mentoring junior staff and leading small process improvement initiatives. Pursue certifications in supply chain or operations management.
Lead Production Control Coordinator
7+ yearsA Lead Production Control Coordinator oversees a team of clerks and coordinators, managing critical production control functions. This role involves developing and implementing production schedules, optimizing inventory levels, and driving continuous improvement initiatives. They provide expert guidance, resolve complex operational challenges, and ensure the efficiency and effectiveness of the entire production control process.
Key Focus Areas
Emphasize strategic leadership, team management, and cross-functional project leadership. Develop expertise in lean manufacturing principles and supply chain optimization. Focus on building strong relationships with senior management and key stakeholders, contributing to long-term operational strategy and continuous improvement culture.
Junior Production Control Coordinating Clerk
0-2 years<p>This entry-level role supports the production control team by performing routine administrative and data entry tasks. Responsibilities include maintaining inventory records, processing material requests, and assisting with basic production schedule updates. The clerk operates under close supervision, ensuring data integrity and adherence to established procedures.</p>
Key Focus Areas
<p>Key development areas include mastering inventory tracking systems, understanding basic production scheduling principles, and developing strong data entry accuracy. Focus on foundational communication skills to interact with production teams and suppliers effectively. Learning to identify and report discrepancies in material flow is also critical.</p>
Production Control Coordinating Clerk
2-4 years<p>A Production Control Coordinating Clerk independently manages specific segments of the production schedule and inventory. This role involves coordinating material delivery, monitoring production progress against plans, and resolving minor logistical issues. They ensure timely availability of components and finished goods, contributing directly to operational flow.</p>
Key Focus Areas
<p>Develop proficiency in production planning software and advanced inventory management techniques. Enhance problem-solving skills to address scheduling conflicts and material shortages proactively. Strengthen communication and negotiation abilities for effective coordination with internal departments and external vendors.</p>
Senior Production Control Coordinating Clerk
4-7 years<p>The Senior Production Control Coordinating Clerk takes ownership of complex production control functions, including master scheduling and capacity planning. This role involves analyzing production data to identify trends, forecast demand, and implement process improvements. They act as a key liaison between production, purchasing, and sales departments, ensuring alignment of operational goals.</p>
Key Focus Areas
<p>Cultivate advanced analytical skills to identify bottlenecks and optimize production processes. Focus on strategic planning for material procurement and production capacity. Develop leadership qualities by mentoring junior staff and leading small process improvement initiatives. Pursue certifications in supply chain or operations management.</p>
Lead Production Control Coordinator
7+ years<p>A Lead Production Control Coordinator oversees a team of clerks and coordinators, managing critical production control functions. This role involves developing and implementing production schedules, optimizing inventory levels, and driving continuous improvement initiatives. They provide expert guidance, resolve complex operational challenges, and ensure the efficiency and effectiveness of the entire production control process.</p>
Key Focus Areas
<p>Emphasize strategic leadership, team management, and cross-functional project leadership. Develop expertise in lean manufacturing principles and supply chain optimization. Focus on building strong relationships with senior management and key stakeholders, contributing to long-term operational strategy and continuous improvement culture.</p>
Job Application Toolkit
Ace your application with our purpose-built resources:
Production Control Coordinating Clerk Resume Examples
Proven layouts and keywords hiring managers scan for.
View examplesProduction Control Coordinating Clerk Cover Letter Examples
Personalizable templates that showcase your impact.
View examplesTop Production Control Coordinating Clerk Interview Questions
Practice with the questions asked most often.
View examplesProduction Control Coordinating Clerk Job Description Template
Ready-to-use JD for recruiters and hiring teams.
View examplesGlobal Production Control Coordinating Clerk Opportunities
The Production Control Coordinating Clerk role translates globally, focusing on optimizing manufacturing workflows and inventory. International demand remains steady, particularly in industrializing economies and regions with robust manufacturing sectors like Southeast Asia and Central Europe. Cultural nuances affect supply chain communication, and regulatory differences impact inventory management. Professionals consider international roles for diverse industry exposure and career advancement. Certifications in supply chain management or logistics enhance global mobility.
Global Salaries
Salaries for a Production Control Coordinating Clerk vary significantly by region and cost of living. In North America, specifically the US, annual salaries range from $40,000 to $60,000 USD, while in Canada, they typically fall between $35,000 and $55,000 CAD ($26,000-$40,000 USD). European markets offer diverse ranges. In Germany, expect €30,000 to €45,000 ($32,000-$48,000 USD), reflecting a higher cost of living. The UK sees salaries from £25,000 to £38,000 ($31,000-$47,000 USD).
Asia-Pacific countries present a broader spectrum. In Australia, salaries are around AUD 50,000 to AUD 70,000 ($33,000-$46,000 USD). In Japan, a similar role might pay ¥3.5 million to ¥5 million ($24,000-$34,000 USD), often with generous benefits like housing allowances or transportation. Latin America, such as Mexico, offers lower nominal salaries, typically MXN 180,000 to MXN 300,000 ($10,000-$17,000 USD), but purchasing power can be higher.
Salary structures also differ; North America often includes health benefits and 401k plans, while many European countries provide comprehensive public healthcare and more vacation days. Tax implications vary, impacting take-home pay. For example, high taxes in Scandinavian countries mean lower net pay but access to extensive social services. International experience and specialized education can increase earning potential, though direct international pay scales are uncommon for this role.
Remote Work
International remote work opportunities for a Production Control Coordinating Clerk are limited but emerging. This role often requires physical presence to manage inventory and production lines directly. However, some companies with distributed manufacturing or supply chains might hire remote clerks for data analysis, scheduling, or supplier coordination. Legal and tax implications of cross-border remote work are complex, requiring careful consideration of payroll, social security, and local tax laws for both employer and employee.
Time zone differences present a challenge for international team collaboration, especially with real-time production issues. Digital nomad visas are an option in countries like Portugal or Spain, but the core job function often ties clerks to a specific facility. Employers with global operations may offer international remote roles, but these are typically for higher-level management positions. Remote work can affect salary expectations, as companies might adjust pay based on the employee's location and local cost of living. Reliable internet and a dedicated workspace are essential.
Visa & Immigration
Common visa categories for a Production Control Coordinating Clerk include skilled worker visas or general work permits, depending on the destination country's immigration policies. Popular destinations like Germany, Canada, and Australia have specific requirements for demonstrating a skills shortage or employer sponsorship. For instance, Canada's Express Entry system may consider this role under specific NOC codes, requiring credential evaluation and language proficiency tests.
Education credential recognition is crucial; applicants often need a diploma or degree in supply chain, logistics, or business administration. Professional licensing is generally not required for this specific clerical role. Visa timelines vary widely, from a few weeks to several months, depending on the country and application volume. Pathways to permanent residency exist in many countries, often tied to continuous employment and meeting specific residency periods. Language requirements, such as English for Canada or German for Germany, are standard for professional integration. Family visas or dependent rights are usually part of the primary applicant's work visa. Some countries offer fast-track programs for in-demand skills, but this role is less commonly on such lists.
2025 Market Reality for Production Control Coordinating Clerks
Understanding current market conditions for a Production Control Coordinating Clerk is vital for career planning. The landscape for this role has evolved significantly since 2023, influenced by post-pandemic supply chain recalibrations and the ongoing integration of automation.
Broader economic factors, such as inflation and manufacturing output fluctuations, directly affect job availability and stability in this field. Market realities vary by the specific industry, company size, and geographic location, with larger manufacturing operations often offering more structured opportunities. This analysis provides an honest assessment of these dynamics, helping you navigate your career path realistically.
Current Challenges
Competition for Production Control Coordinating Clerk roles has intensified. Many entry-level positions face saturation, making it harder for new entrants to secure roles.
Economic uncertainty causes companies to optimize existing staff, leading to fewer new hires. This role also faces pressure from automation of routine tasks, requiring clerks to adapt quickly.
Growth Opportunities
Despite challenges, strong demand exists for Production Control Coordinating Clerks who master new technologies. Roles emphasizing data analysis, predictive scheduling, and system optimization are growing. Companies seek clerks capable of managing complex ERP systems and leveraging real-time inventory data.
Professionals can gain an advantage by acquiring certifications in supply chain management software or production planning tools. Underserved markets, particularly in emerging industrial zones or specialized manufacturing sectors, may offer less competition. Clerks with strong communication skills, able to bridge gaps between production, logistics, and sales teams, are highly valued.
Strategic career moves involve specializing in niche manufacturing, such as aerospace or medical devices, where precision and compliance are paramount. These sectors often maintain stable demand regardless of broader economic shifts. Investing in continuous learning for new production methodologies and AI-driven planning tools positions individuals for long-term success.
Current Market Trends
Hiring for Production Control Coordinating Clerks shows stable demand in manufacturing and logistics sectors as of 2025. Companies still need human oversight for complex scheduling and material flow, even with increased automation. Recent shifts emphasize efficiency and real-time data management in supply chains.
The integration of AI and advanced planning software affects this role. Clerks now spend less time on manual data entry and more on interpreting system outputs and resolving exceptions. This demands stronger analytical and problem-solving skills, shifting employer requirements.
Economic conditions, particularly fluctuating consumer demand and supply chain disruptions, directly impact production schedules. This creates a need for clerks who can adapt quickly to changes and manage unforeseen issues. Salary trends remain steady, with slight increases for those demonstrating proficiency with new planning tools.
Geographically, demand remains strongest in industrial hubs and areas with significant manufacturing presence. Remote work for this role is uncommon due to the hands-on nature of coordinating physical production and materials. Seasonal hiring patterns align with production cycles, often peaking before major retail periods.
Emerging Specializations
The manufacturing and logistics landscape is undergoing rapid transformation, driven by advancements in automation, data analytics, and supply chain digitization. These shifts are creating entirely new specialization opportunities for Production Control Coordinating Clerks, moving beyond traditional inventory and scheduling tasks. Understanding these emerging areas allows professionals to strategically position themselves for career advancement and increased earning potential in 2025 and beyond.
Early positioning in these cutting-edge specializations often leads to premium compensation and accelerated career growth. While established specializations remain vital, focusing on emerging niches allows clerks to become indispensable assets in evolving production environments. These new areas typically become mainstream within three to five years, creating significant job opportunities for those with foresight and specialized skills.
Pursuing emerging specializations involves a balance of risk and reward. While the demand for these skills grows, the specific requirements may evolve rapidly. However, the potential for high impact and leadership roles in next-generation production control systems significantly outweighs the inherent uncertainties. Clerks who embrace continuous learning and adapt to new technologies will thrive in these forward-looking roles.
Real-time Production Data Analyst Clerk
This specialization focuses on optimizing production flows and material handling using real-time data from IoT sensors on the factory floor. Production Control Coordinating Clerks in this area analyze data streams to identify bottlenecks, predict equipment failures, and adjust schedules dynamically. They play a crucial role in maintaining continuous, efficient operations within smart manufacturing environments.
Supply Chain Resilience Clerk
As supply chains become increasingly complex and vulnerable to disruptions, this specialization focuses on identifying potential risks within the production schedule and material supply. Production Control Coordinating Clerks in this role develop contingency plans, monitor geopolitical and environmental factors, and work to minimize the impact of unforeseen events on manufacturing output. They ensure production resilience and continuity.
Sustainable Production Coordinator Clerk
This area involves coordinating production schedules and material movements with a focus on minimizing waste, reducing energy consumption, and optimizing resource utilization throughout the manufacturing process. Production Control Coordinating Clerks specializing here track environmental metrics, ensure compliance with sustainability standards, and contribute to the company's green initiatives. They help implement circular economy principles within production.
Automated System Integration Clerk
With the rise of collaborative robots (cobots) and automated guided vehicles (AGVs) on the factory floor, this specialization focuses on integrating and coordinating these automated systems into the production schedule. Production Control Coordinating Clerks in this area manage the interaction between human workers and robotic assets, optimizing their deployment for maximum efficiency and safety. They ensure seamless automation integration.
AI-Enhanced Scheduling Clerk
This specialization focuses on using advanced planning and scheduling (APS) software, often powered by AI, to create highly optimized production schedules. Production Control Coordinating Clerks in this role input complex constraints, interpret AI-generated recommendations, and fine-tune schedules for optimal resource allocation and delivery timelines. They leverage technology to achieve superior scheduling precision.
Pros & Cons of Being a Production Control Coordinating Clerk
Embarking on a career path requires a clear-eyed understanding of both its appealing aspects and its inherent difficulties. The experience within any profession, including that of a Production Control Coordinating Clerk, can vary significantly based on factors such as the company's culture, the specific industry sector, and the individual's personality and preferences. What one person perceives as a benefit, another might see as a challenge. Furthermore, the pros and cons of a role can evolve as one progresses through different career stages. This assessment provides an honest, balanced perspective on the realities of being a Production Control Coordinating Clerk, helping aspiring professionals set realistic expectations and make informed decisions about their career trajectory.
Pros
- This role offers excellent entry-level opportunities within the manufacturing and logistics sectors, often requiring only a high school diploma or an associate's degree, making it accessible for many.
- Production Control Coordinating Clerks gain valuable hands-on experience in supply chain management, inventory control, and production scheduling, building a foundational understanding of operational processes.
- The position provides a direct impact on operational efficiency, as effective coordination ensures smooth production flow and timely delivery of goods, leading to a sense of accomplishment.
- There is consistent demand for these skills across various industries, from automotive to food production, offering job security and diverse employment opportunities.
- The role involves significant interaction with various departments, including production, sales, purchasing, and shipping, fostering strong communication and teamwork skills.
- This position allows for the development of strong organizational skills, attention to detail, and problem-solving abilities as clerks manage complex schedules and react to unexpected issues.
- For those interested in a career in operations or supply chain, this role serves as a practical stepping stone, providing a real-world understanding of the challenges and coordination required in manufacturing.
Cons
- The role can be repetitive, as many tasks involve routine data entry, tracking, and communication, which may lead to monotony over time.
- There is often limited upward mobility directly within this specific role; career advancement usually requires moving into broader supply chain, logistics, or management positions.
- Production Control Coordinating Clerks frequently face high-pressure situations, especially when production schedules are tight or unexpected issues arise that threaten deadlines.
- The job often requires working irregular hours, including early mornings, late evenings, or occasional weekends, to align with production shifts and ensure timely material flow.
- This position typically offers lower salary potential compared to roles requiring specialized technical skills or advanced degrees within the manufacturing sector.
- The work environment can be noisy and physically demanding, as it often involves spending time on the production floor, near machinery, or in warehouse settings.
- Dealing with frequent changes to production plans, material shortages, or shipping delays can be stressful and requires constant adaptation and problem-solving under pressure, which is not always within the clerk's control, leading to frustration from other departments and leadership for issues that are not the clerk's fault, yet they are the single point of contact for the problem as it arises and is being fixed, making them the target of complaints that they must absorb and handle professionally without becoming defensive, even when the situation is not their fault. Instead, they must be the calm in the storm, the one who can take the heat and keep a cool head while working to resolve the issue for the greater good of the company and its customers, even when it is not their fault, but the fault of another department or supplier, or even a customer, but they must still be the one to deal with the complaints and work to resolve the issue, and then communicate the resolution to all parties involved, including the complaining parties, and do so in a way that is professional and calm, and does not make the complaining party feel as if they are being blamed, but rather that the clerk is working to resolve the issue for them, and that they are being heard and understood, even when the issue is not the clerk's fault, but the fault of another department or supplier, or even a customer, but they must still be the one to deal with the complaints and work to resolve the issue, and then communicate the resolution to all parties involved, including the complaining parties, and do so in a way that is professional and calm, and does not make the complaining party feel as if they are being blamed, but rather that the clerk is working to resolve the issue for them, and that they are being heard and understood, even when the issue is not the clerk's fault, but the fault of another department or supplier, or even a customer, but they must still be the one to deal with the complaints and work to resolve the issue, and then communicate the resolution to all parties involved, including the complaining parties, and do so in a way that is professional and calm, and does not make the complaining party feel as if they are being blamed, but rather that the clerk is working to resolve the issue for them, and that they are being heard and understood, even when the issue is not the clerk's fault, but the fault of another department or supplier, or even a customer, but they must still be the one to deal with the complaints and work to resolve the issue, and then communicate the resolution to all parties involved, including the complaining parties, and do so in a way that is professional and calm, and does not make the complaining party feel as if they are being blamed, but rather that the clerk is working to resolve the issue for them, and that they are being heard and understood, even when the issue is not the clerk's fault, but the fault of another department or supplier, or even a customer, but they must still be the one to deal with the complaints and work to resolve the issue, and then communicate the resolution to all parties involved, including the complaining parties, and do so in a way that is professional and calm, and does not make the complaining party feel as if they are being blamed, but rather that the clerk is working to resolve the issue for them, and that they are being heard and understood.
Frequently Asked Questions
Production Control Coordinating Clerks face distinct challenges balancing meticulous data entry with dynamic production scheduling. This section addresses common uncertainties about managing inventory, optimizing workflows, and ensuring timely material flow to keep manufacturing lines running efficiently.
What are the entry-level requirements for a Production Control Coordinating Clerk position?
A high school diploma or GED is typically the minimum educational requirement for a Production Control Coordinating Clerk. Many employers prefer candidates with an associate's degree in business, logistics, or supply chain management, or relevant vocational training. Practical experience in an office or manufacturing environment, especially with inventory or data entry, is highly valued and can often substitute for formal education.
How long does it take to become job-ready as a Production Control Coordinating Clerk, especially if I'm new to the field?
Becoming proficient enough for an entry-level Production Control Coordinating Clerk role can take 3-6 months if you focus on acquiring relevant software skills and understanding basic production processes. If starting with no prior office or manufacturing experience, allow 6-12 months to gain foundational knowledge and practical exposure through internships or entry-level administrative roles. Certifications in supply chain fundamentals or specific ERP systems can accelerate your readiness.
What are the typical salary expectations for a Production Control Coordinating Clerk, and what benefits are common?
Starting salaries for Production Control Coordinating Clerks generally range from $35,000 to $45,000 annually, depending on location, industry, and company size. With 3-5 years of experience, this can increase to $45,000-$60,000. Senior or specialized roles, especially those involving complex ERP system management, can command higher salaries. Benefits packages typically include health insurance, retirement plans, and paid time off.
What is the typical work-life balance like for a Production Control Coordinating Clerk?
Work-life balance for Production Control Coordinating Clerks is generally stable, primarily involving standard business hours, Monday through Friday. Overtime may be necessary during peak production periods, year-end inventory, or unexpected supply chain disruptions. The role is often office-based, though some time may be spent on the production floor for coordination, making it less physically demanding than direct production roles.
Is the role of a Production Control Coordinating Clerk secure, or is it at risk from automation?
The job outlook for Production Control Coordinating Clerks remains stable, as manufacturing and logistics companies consistently need professionals to manage production flow and inventory. Automation may change some tasks, but the need for human oversight, problem-solving, and coordination of complex supply chains ensures continued demand. Professionals with strong analytical skills and experience with advanced planning software will have the best job security.
What are the typical career growth opportunities and advancement paths for a Production Control Coordinating Clerk?
Career growth for a Production Control Coordinating Clerk can lead to roles such as Production Planner, Inventory Control Specialist, or Logistics Coordinator. With further experience and potentially additional certifications, you might advance to Supply Chain Analyst, Operations Supervisor, or even Production Manager. Many take on project management responsibilities for system implementations or process improvements, broadening their skill sets.
What are the biggest day-to-day challenges or stressors unique to this role?
The primary challenge for a Production Control Coordinating Clerk is managing unexpected disruptions, such as material shortages, equipment breakdowns, or sudden changes in production schedules. This requires quick thinking, excellent communication skills, and the ability to adapt plans on the fly. Maintaining accurate inventory records and coordinating effectively across multiple departments are also ongoing challenges that demand meticulous attention to detail.
Can a Production Control Coordinating Clerk work remotely, or is it primarily an on-site role?
Production Control Coordinating Clerks primarily work on-site in manufacturing plants, warehouses, or corporate offices that oversee production. The role requires direct interaction with production teams, warehouse staff, and suppliers, making it less suitable for fully remote work. Some companies may offer hybrid options where administrative tasks can be done remotely, but the core coordinating functions necessitate a physical presence.
Related Careers
Explore similar roles that might align with your interests and skills:
Production Clerk
A growing field with similar skill requirements and career progression opportunities.
Explore career guideProduction Scheduler
A growing field with similar skill requirements and career progression opportunities.
Explore career guideProduction Control Clerk
A growing field with similar skill requirements and career progression opportunities.
Explore career guideProduction Control Coordinator
A growing field with similar skill requirements and career progression opportunities.
Explore career guideProduction Control Technologist
A growing field with similar skill requirements and career progression opportunities.
Explore career guideAssess your Production Control Coordinating Clerk readiness
Understanding where you stand today is the first step toward your career goals. Our Career Coach helps identify skill gaps and create personalized plans.
Skills Gap Analysis
Get a detailed assessment of your current skills versus Production Control Coordinating Clerk requirements. Our AI Career Coach identifies specific areas for improvement with personalized recommendations.
See your skills gapCareer Readiness Assessment
Evaluate your overall readiness for Production Control Coordinating Clerk roles with our AI Career Coach. Receive personalized recommendations for education, projects, and experience to boost your competitiveness.
Assess your readinessSimple pricing, powerful features
Upgrade to Himalayas Plus and turbocharge your job search.
Himalayas
Himalayas Plus
Himalayas Max
Find your dream job
Sign up now and join over 100,000 remote workers who receive personalized job alerts, curated job matches, and more for free!
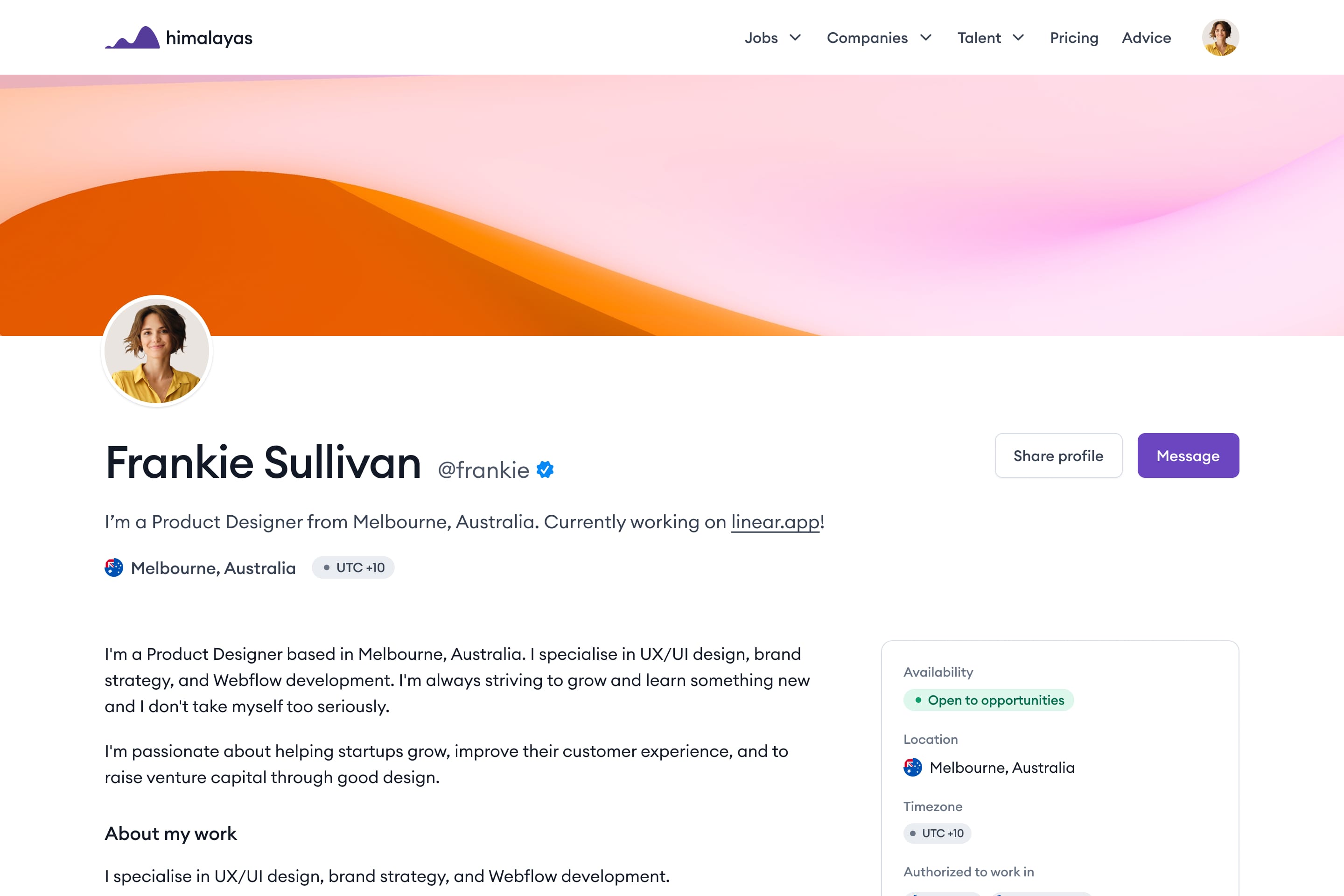