Complete Numerical Control Machine Operator Career Guide
Numerical Control Machine Operators are the skilled artisans of modern manufacturing, transforming raw materials into precision components using computer-controlled machinery. They are crucial for industries from aerospace to medical devices, ensuring the accuracy and quality essential for complex products. This role offers a hands-on career where you blend technical expertise with problem-solving, building the foundational parts that drive innovation.
Key Facts & Statistics
Median Salary
$50,000 USD
Range: $35k - $70k+ USD
Growth Outlook
Annual Openings
≈11,800
openings annually
Top Industries
Typical Education
High school diploma or equivalent; often requires on-the-job training, vocational school, or an apprenticeship
What is a Numerical Control Machine Operator?
A Numerical Control Machine Operator sets up, operates, and maintains computer-controlled machines that cut, shape, and form metal, plastic, or other materials with high precision. This role is fundamental to modern manufacturing, producing everything from aerospace components to medical devices and consumer goods. They translate engineering designs into physical products by overseeing automated machining processes.
This role differs significantly from a traditional Machinist, who often relies more on manual machine operation and hands-on adjustments. While both work with machine tools, the CNC Operator's primary focus is on programming, monitoring, and fine-tuning automated systems, ensuring the machine executes complex instructions with minimal human intervention. They ensure the machine produces parts according to exact specifications, often involving intricate designs and tight tolerances.
What does a Numerical Control Machine Operator do?
Key Responsibilities
- Interpret blueprints and engineering drawings to determine machine setup, sequence of operations, and tooling requirements.
- Load raw materials, such as metal, plastic, or wood, into the machine, ensuring proper alignment and secure clamping.
- Select and load appropriate cutting tools, ensuring they are sharp and correctly installed in the machine's tool changer.
- Monitor machine operations, observing for issues like tool wear, material defects, or programming errors, and making necessary adjustments.
- Perform quality checks on finished parts using precision measuring instruments like calipers, micrometers, and gauges to verify dimensions and tolerances.
- Adjust machine controls to compensate for tool wear or material variations, maintaining part quality and production efficiency.
- Perform routine maintenance on CNC machines, including cleaning, lubricating, and inspecting components for wear or damage, to ensure optimal performance and longevity.
Work Environment
Numerical Control Machine Operators typically work in manufacturing plants, machine shops, or industrial settings. The environment can be noisy due to machinery and may require standing for long periods. Safety is a primary concern, and operators wear personal protective equipment (PPE) such as safety glasses, hearing protection, and steel-toed boots. While operating machines, they often work independently, but collaboration with supervisors, engineers, and quality control personnel is common for troubleshooting and process improvement.
Schedules often involve shifts, including evenings or weekends, to maintain continuous production. The pace is steady, requiring consistent attention to detail and adherence to safety protocols. Some environments may be temperature-controlled, while others might be subject to the ambient conditions of the factory floor.
Tools & Technologies
Numerical Control Machine Operators routinely use a variety of specialized tools and technologies to perform their duties. They work directly with Computer Numerical Control (CNC) machines, which include lathes, mills, grinders, and routers. Proficiency with the machine's control panel and human-machine interface (HMI) is essential for programming and operation.
Precision measuring instruments are critical for quality control, such as calipers, micrometers, height gauges, and bore gauges. Operators also use hand tools for machine setup and maintenance, including wrenches, screwdrivers, and mallets. Material handling equipment like forklifts or hoists may be necessary for loading large workpieces. They also interact with Computer-Aided Manufacturing (CAM) software interfaces to load programs and understand machining processes.
Numerical Control Machine Operator Skills & Qualifications
A Numerical Control (NC) Machine Operator's qualification landscape emphasizes practical expertise and precision. Employers prioritize a blend of mechanical aptitude, technical literacy, and a commitment to safety. While formal education provides a strong foundation, hands-on experience operating specific NC machines and working with various materials often carries more weight, especially for entry-level positions.
Requirements for NC Machine Operators vary by industry, company size, and the complexity of the parts produced. Larger manufacturing firms or those in aerospace and medical device sectors typically seek candidates with more certifications or specialized training in advanced machining techniques. Smaller shops might value versatility across different machine types. Geographic location also plays a role; regions with strong manufacturing bases often have more structured apprenticeship programs.
Certifications from organizations like the National Institute for Metalworking Skills (NIMS) significantly enhance a candidate's profile, demonstrating a standardized level of competency. These certifications often prove more valuable than a general associate's degree for direct employment. The skill landscape for NC operators is evolving with the increasing integration of Computer Numerical Control (CNC) and automation. Operators must adapt to reading more complex G-code and M-code, performing minor programming edits, and understanding sensor feedback. Maintaining a balance between traditional machining knowledge and embracing digital manufacturing tools is crucial for career progression.
Education Requirements
Technical Skills
- Blueprint and technical drawing interpretation (GD&T - Geometric Dimensioning & Tolerancing)
- Measurement tools proficiency (calipers, micrometers, height gauges, bore gauges)
- Machine setup and fixturing (vise, clamps, chucks, collets)
- Tooling selection and installation (end mills, drills, inserts, turning tools)
- Material properties knowledge (metals, plastics, composites)
- Basic G-code and M-code understanding (for manual data input or minor edits)
- Machine operation and monitoring (feed rates, spindle speeds, depth of cut)
- Preventative machine maintenance and lubrication
- Quality control and inspection processes (first-piece inspection, in-process checks)
- Troubleshooting machine alarms and production deviations
- Workholding strategies and optimization
- Basic computer literacy for machine interface navigation and data entry
Soft Skills
- Attention to Detail: Essential for precise measurements, reading blueprints, and identifying minute machine errors that could lead to costly defects.
- Problem-Solving: Operators must diagnose machine malfunctions, adjust parameters to correct quality issues, and troubleshoot unexpected outcomes during production runs.
- Safety Consciousness: Critical for adhering to strict safety protocols, operating heavy machinery responsibly, and preventing accidents in a high-risk environment.
- Mechanical Aptitude: Important for understanding how machines work, performing basic maintenance, and making minor adjustments to tooling and fixturing.
- Adaptability: Necessary to adjust to changing production schedules, different material properties, and new machine technologies or software updates.
- Communication: Operators need to clearly report machine issues, production anomalies, and maintenance needs to supervisors or maintenance teams.
- Patience: Often required when setting up complex jobs, waiting for long machining cycles, or troubleshooting persistent issues without rushing.
- Diligence: Operators must consistently monitor machine performance, maintain cleanliness, and document production accurately over long shifts to ensure quality and efficiency.
How to Become a Numerical Control Machine Operator
Entering the Numerical Control (NC) Machine Operator field offers several practical pathways, ranging from vocational training to on-the-job apprenticeships. While a formal degree is not typically required, specialized training in machine operation, blueprint reading, and computer numerical control (CNC) programming fundamentals significantly shortens the entry timeline. Beginners might expect a 6-12 month period to gain foundational skills and secure an entry-level position, while those transitioning from related manufacturing roles could find opportunities within 3-6 months.
Entry strategies vary by industry and company size. Larger manufacturing plants or aerospace companies often prefer candidates with formal certifications or apprenticeship experience due to the precision and complexity of their operations. Smaller job shops or custom fabrication facilities may be more open to hiring individuals with strong mechanical aptitude and a willingness to learn on-site, offering a faster route to gaining practical experience. Geographic location also plays a role; industrial hubs will have more openings and diverse training programs.
A common misconception is that NC machine operation is solely manual labor; in reality, it requires a blend of technical skill, problem-solving, and attention to detail for programming and monitoring automated processes. Building a basic understanding of G-code and M-code, even through online resources, can provide a significant advantage. Networking within local manufacturing communities, attending industry job fairs, and connecting with trade school instructors can also uncover opportunities not widely advertised.
Develop foundational mechanical and mathematical skills by taking introductory courses in shop math, blueprint reading, and basic mechanics. Many community colleges or vocational schools offer these courses, which provide a critical understanding of precision measurement and material properties. This foundational knowledge is essential before moving to machine-specific training.
Complete a specialized NC Machine Operator training program or apprenticeship. These programs, typically lasting 6-18 months, cover machine setup, operation, safety protocols, and introductory G-code/M-code programming. Look for programs with hands-on lab work, as practical experience is highly valued by employers.
Obtain relevant certifications such as the National Institute for Metalworking Skills (NIMS) credentials in machining or measurement, materials, and safety. These industry-recognized certifications validate your skills and demonstrate a commitment to professional standards, making you a more attractive candidate to employers.
Gain hands-on experience through internships, entry-level positions, or personal projects. Seek out opportunities where you can operate actual NC machines, troubleshoot minor issues, and contribute to production runs. Even volunteering at a local maker space or building small projects can demonstrate practical aptitude.
Create a professional resume highlighting your training, certifications, and any practical experience, even if it's from school projects or personal endeavors. Include a cover letter that expresses your enthusiasm for the manufacturing industry and your specific interest in NC machine operation roles. Tailor your application to each job posting.
Actively network within the local manufacturing community by attending industry events, job fairs, or connecting with professionals on platforms like LinkedIn. Informational interviews with experienced operators or shop managers can provide insights into specific company needs and potential unadvertised openings. Many entry-level positions are filled through referrals.
Prepare for interviews by reviewing common technical questions related to machine operation, safety, and blueprint reading. Be ready to discuss your problem-solving skills and demonstrate your mechanical aptitude. Follow up promptly after interviews to reiterate your interest and thank the hiring manager for their time.
Step 1
Develop foundational mechanical and mathematical skills by taking introductory courses in shop math, blueprint reading, and basic mechanics. Many community colleges or vocational schools offer these courses, which provide a critical understanding of precision measurement and material properties. This foundational knowledge is essential before moving to machine-specific training.
Step 2
Complete a specialized NC Machine Operator training program or apprenticeship. These programs, typically lasting 6-18 months, cover machine setup, operation, safety protocols, and introductory G-code/M-code programming. Look for programs with hands-on lab work, as practical experience is highly valued by employers.
Step 3
Obtain relevant certifications such as the National Institute for Metalworking Skills (NIMS) credentials in machining or measurement, materials, and safety. These industry-recognized certifications validate your skills and demonstrate a commitment to professional standards, making you a more attractive candidate to employers.
Step 4
Gain hands-on experience through internships, entry-level positions, or personal projects. Seek out opportunities where you can operate actual NC machines, troubleshoot minor issues, and contribute to production runs. Even volunteering at a local maker space or building small projects can demonstrate practical aptitude.
Step 5
Create a professional resume highlighting your training, certifications, and any practical experience, even if it's from school projects or personal endeavors. Include a cover letter that expresses your enthusiasm for the manufacturing industry and your specific interest in NC machine operation roles. Tailor your application to each job posting.
Step 6
Actively network within the local manufacturing community by attending industry events, job fairs, or connecting with professionals on platforms like LinkedIn. Informational interviews with experienced operators or shop managers can provide insights into specific company needs and potential unadvertised openings. Many entry-level positions are filled through referrals.
Step 7
Prepare for interviews by reviewing common technical questions related to machine operation, safety, and blueprint reading. Be ready to discuss your problem-solving skills and demonstrate your mechanical aptitude. Follow up promptly after interviews to reiterate your interest and thank the hiring manager for their time.
Education & Training Needed to Become a Numerical Control Machine Operator
Becoming a Numerical Control (NC) Machine Operator primarily involves practical skills and hands-on training, distinguishing it from roles requiring extensive theoretical knowledge. Formal degree programs are less common and often unnecessary for entry-level positions. Instead, individuals typically pursue vocational training, apprenticeships, or specialized certifications. These alternative paths are often more cost-effective and time-efficient than traditional four-year degrees, which might cost $40,000-$100,000+ and take four years. Vocational programs or technical schools range from $5,000-$20,000 and can be completed in 6-24 months. Apprenticeships, often paid, offer on-the-job training and classroom instruction over 2-4 years, with minimal direct cost to the apprentice.
Employers highly value practical experience and certifications from recognized industry bodies. A certificate from a technical college or completion of an apprenticeship signals a candidate's readiness for the role. Self-study with online courses can supplement training but usually requires hands-on practice to be effective, often taking 6-18 months to build foundational skills. Continuous learning remains important, especially with advancements in NC technology and automation. Staying current with new software and machine types through short courses or manufacturer-specific training enhances long-term career prospects.
The educational needs for an NC Machine Operator vary by the complexity of the machines and the industry. Operating basic NC machines might only require a high school diploma and on-the-job training, while programming and setting up advanced CNC (Computer Numerical Control) machines often necessitates a technical certificate or associate's degree. Practical experience is paramount; employers often prioritize candidates with proven machine operation skills over those with only theoretical knowledge. Look for programs with strong connections to local manufacturing companies and high job placement rates, as these indicate direct pathways to employment.
Numerical Control Machine Operator Salary & Outlook
Compensation for Numerical Control (NC) Machine Operators varies significantly based on several factors. Geographic location plays a crucial role; areas with a higher cost of living or strong manufacturing sectors often offer higher wages. Experience level is paramount, with earnings increasing substantially as operators gain proficiency and specialize in complex machinery or materials.
Total compensation extends beyond base salary. Many positions include overtime pay, which can significantly boost annual earnings, especially in high-production environments. Benefits packages typically include health insurance, retirement contributions like 401(k)s, and paid time off. Some companies also offer performance bonuses or profit-sharing, particularly in industries with tight production deadlines or high-value outputs.
Specialized skills, such as advanced programming knowledge, multi-axis machine operation, or expertise with specific control systems (e.g., Fanuc, Siemens), command premium compensation. Companies with larger operations or those in specialized industries like aerospace or medical device manufacturing may offer more competitive salaries and benefits. Remote work is not applicable for this hands-on role, but operators may find opportunities in different regions based on manufacturing hubs. While figures are presented in USD, international markets also show variations driven by local industrial demand and labor costs.
Salary by Experience Level
Level | US Median | US Average |
---|---|---|
Junior Numerical Control Machine Operator | $42k USD | $45k USD |
Numerical Control Machine Operator | $52k USD | $55k USD |
Senior Numerical Control Machine Operator | $65k USD | $68k USD |
Lead Numerical Control Machine Operator | $75k USD | $78k USD |
CNC Supervisor | $85k USD | $88k USD |
CNC Manager | $100k USD | $105k USD |
Market Commentary
The job market for Numerical Control (NC) Machine Operators shows steady demand, driven by the ongoing need for precision manufacturing across various industries. The U.S. Bureau of Labor Statistics projects little to no change in employment for machinists and tool and die makers, which includes NC operators, from 2022 to 2032. Despite this, a consistent need exists as experienced operators retire and industries continue to automate and expand production capabilities.
Emerging opportunities for NC Machine Operators often involve advanced manufacturing techniques, such as additive manufacturing integration and operating machines with robotic loading/unloading systems. Proficiency in CAD/CAM software and understanding Industry 4.0 concepts, like data analytics for machine performance, are becoming increasingly valuable. The demand for highly skilled operators capable of setting up, programming, and troubleshooting complex multi-axis CNC machines remains strong.
Supply and demand dynamics vary by region; some areas with robust manufacturing bases face shortages of skilled operators, leading to competitive wages and incentives. Automation and AI primarily impact the repetitive tasks, increasing the need for operators who can manage and optimize automated systems rather than just operate machines. This role is generally recession-resistant, as manufacturing remains essential even during economic downturns. Geographic hotspots for NC operators include states like Michigan, Ohio, Texas, and California, due to their strong automotive, aerospace, and general manufacturing industries.
Numerical Control Machine Operator Career Path
Career progression for a Numerical Control Machine Operator typically involves a deep focus on technical mastery, precision, and efficiency in operating CNC machinery. Advancement often starts with foundational training and moves towards specialized programming, machine maintenance, and ultimately, leadership roles. The field offers clear pathways for both individual contributor (IC) and management tracks, allowing operators to either become highly specialized technical experts or to lead teams and manage operations.
Advancement speed depends on several factors, including an operator's consistent performance, their willingness to learn new technologies and programming languages, and the specific industry. For example, aerospace or medical device manufacturing often demands higher precision and offers opportunities for specialized skill development. Lateral movement can involve transitioning between different types of CNC machines (e.g., milling to turning) or moving into quality control, CAD/CAM programming, or even design roles. Company size also impacts progression; larger corporations may have more structured career paths and management opportunities, while smaller shops might offer broader exposure to different machine types and more rapid skill diversification.
Continuous learning is critical, with new software and machine capabilities emerging regularly. Obtaining certifications in specific CNC programming languages (like G-code, M-code) or machine operation techniques can significantly boost an operator's profile. Networking within the manufacturing community and seeking mentorship from experienced operators or supervisors helps identify best practices and potential opportunities. Career pivots might include moving into roles like Manufacturing Engineer, Process Improvement Specialist, or even technical training, leveraging the deep understanding of machine capabilities and production processes gained as an operator.
Junior Numerical Control Machine Operator
0-2 yearsOperate specific CNC machines under direct supervision, focusing on loading materials, initiating programs, and performing basic quality checks. Follow established procedures for routine machine operation and minor troubleshooting. Impact is primarily on individual task completion and adherence to production schedules.
Key Focus Areas
Develop foundational understanding of machine safety protocols, basic G-code and M-code commands, and interpreting blueprints. Focus on tool identification, material handling, and quality inspection using basic measurement tools. Seek mentorship from senior operators to understand machine setup nuances and common operational challenges.
Numerical Control Machine Operator
2-5 yearsIndependently operate and set up various CNC machines, including tool changes, offsets, and program adjustments. Perform in-process quality inspections and troubleshoot common machine alarms or minor production issues. Contribute to optimizing machine efficiency and reducing scrap rates, with impact on individual machine output.
Key Focus Areas
Master advanced G-code and M-code programming for complex geometries and multiple machine axes. Develop expertise in tool path optimization, fixture design, and advanced material properties. Focus on independent problem-solving and process improvement for specific machine operations.
Senior Numerical Control Machine Operator
5-8 yearsServe as a subject matter expert for specific CNC machines or complex parts, providing technical guidance to peers. Troubleshoot intricate machine issues, optimize existing programs for efficiency, and participate in new product prototyping. Take ownership of specific production runs, ensuring high-quality output and minimal downtime. Impact extends to team-level problem-solving and process refinement.
Key Focus Areas
Specialize in advanced programming techniques for complex parts or multi-axis machines. Develop strong analytical skills for root cause analysis of production issues and process bottlenecks. Begin mentoring junior operators and contribute to training programs. Explore CAM software proficiency and DFM (Design for Manufacturability) principles.
Lead Numerical Control Machine Operator
8-12 yearsLead a small team of CNC operators, assigning tasks, monitoring progress, and providing on-the-job training. Oversee machine maintenance schedules and ensure adherence to safety and quality standards across multiple machines. Act as the primary point of contact for technical issues and process improvements for a specific shift or production line. Impact directly affects team productivity and adherence to production targets.
Key Focus Areas
Develop strong leadership and communication skills, focusing on delegation, scheduling, and conflict resolution within a team. Gain proficiency in production planning software and inventory management principles. Understand lean manufacturing principles and continuous improvement methodologies.
CNC Supervisor
12-18 yearsSupervise an entire shift or a dedicated cell of CNC operations, managing operator performance, scheduling, and resource allocation. Implement process improvements, ensure compliance with production goals, and manage departmental budgets. Make critical decisions regarding production priorities and personnel management. Impact extends across the entire production area, influencing overall output and efficiency.
Key Focus Areas
Master project management principles, budget oversight, and performance management for a larger team. Develop strategic planning skills related to machine utilization, capital equipment acquisition, and workforce development. Gain a comprehensive understanding of quality management systems (e.g., ISO standards).
CNC Manager
18+ yearsManage the entire CNC department or a significant portion of the manufacturing facility, overseeing multiple supervisory teams and production lines. Develop and implement long-term operational strategies, manage large budgets, and make decisions on technology investments. Responsible for achieving overall production targets, quality standards, and cost efficiencies. Impact is at the organizational level, influencing company-wide manufacturing strategy and profitability.
Key Focus Areas
Cultivate strong business acumen, including financial analysis, supply chain management, and long-term strategic planning for manufacturing operations. Develop advanced leadership skills for managing multiple departments and complex projects. Focus on fostering a culture of innovation and continuous improvement.
Junior Numerical Control Machine Operator
0-2 yearsOperate specific CNC machines under direct supervision, focusing on loading materials, initiating programs, and performing basic quality checks. Follow established procedures for routine machine operation and minor troubleshooting. Impact is primarily on individual task completion and adherence to production schedules.
Key Focus Areas
Develop foundational understanding of machine safety protocols, basic G-code and M-code commands, and interpreting blueprints. Focus on tool identification, material handling, and quality inspection using basic measurement tools. Seek mentorship from senior operators to understand machine setup nuances and common operational challenges.
Numerical Control Machine Operator
2-5 yearsIndependently operate and set up various CNC machines, including tool changes, offsets, and program adjustments. Perform in-process quality inspections and troubleshoot common machine alarms or minor production issues. Contribute to optimizing machine efficiency and reducing scrap rates, with impact on individual machine output.
Key Focus Areas
Master advanced G-code and M-code programming for complex geometries and multiple machine axes. Develop expertise in tool path optimization, fixture design, and advanced material properties. Focus on independent problem-solving and process improvement for specific machine operations.
Senior Numerical Control Machine Operator
5-8 yearsServe as a subject matter expert for specific CNC machines or complex parts, providing technical guidance to peers. Troubleshoot intricate machine issues, optimize existing programs for efficiency, and participate in new product prototyping. Take ownership of specific production runs, ensuring high-quality output and minimal downtime. Impact extends to team-level problem-solving and process refinement.
Key Focus Areas
Specialize in advanced programming techniques for complex parts or multi-axis machines. Develop strong analytical skills for root cause analysis of production issues and process bottlenecks. Begin mentoring junior operators and contribute to training programs. Explore CAM software proficiency and DFM (Design for Manufacturability) principles.
Lead Numerical Control Machine Operator
8-12 yearsLead a small team of CNC operators, assigning tasks, monitoring progress, and providing on-the-job training. Oversee machine maintenance schedules and ensure adherence to safety and quality standards across multiple machines. Act as the primary point of contact for technical issues and process improvements for a specific shift or production line. Impact directly affects team productivity and adherence to production targets.
Key Focus Areas
Develop strong leadership and communication skills, focusing on delegation, scheduling, and conflict resolution within a team. Gain proficiency in production planning software and inventory management principles. Understand lean manufacturing principles and continuous improvement methodologies.
CNC Supervisor
12-18 yearsSupervise an entire shift or a dedicated cell of CNC operations, managing operator performance, scheduling, and resource allocation. Implement process improvements, ensure compliance with production goals, and manage departmental budgets. Make critical decisions regarding production priorities and personnel management. Impact extends across the entire production area, influencing overall output and efficiency.
Key Focus Areas
Master project management principles, budget oversight, and performance management for a larger team. Develop strategic planning skills related to machine utilization, capital equipment acquisition, and workforce development. Gain a comprehensive understanding of quality management systems (e.g., ISO standards).
CNC Manager
18+ yearsManage the entire CNC department or a significant portion of the manufacturing facility, overseeing multiple supervisory teams and production lines. Develop and implement long-term operational strategies, manage large budgets, and make decisions on technology investments. Responsible for achieving overall production targets, quality standards, and cost efficiencies. Impact is at the organizational level, influencing company-wide manufacturing strategy and profitability.
Key Focus Areas
Cultivate strong business acumen, including financial analysis, supply chain management, and long-term strategic planning for manufacturing operations. Develop advanced leadership skills for managing multiple departments and complex projects. Focus on fostering a culture of innovation and continuous improvement.
Job Application Toolkit
Ace your application with our purpose-built resources:
Numerical Control Machine Operator Resume Examples
Proven layouts and keywords hiring managers scan for.
View examplesNumerical Control Machine Operator Cover Letter Examples
Personalizable templates that showcase your impact.
View examplesTop Numerical Control Machine Operator Interview Questions
Practice with the questions asked most often.
View examplesNumerical Control Machine Operator Job Description Template
Ready-to-use JD for recruiters and hiring teams.
View examplesGlobal Numerical Control Machine Operator Opportunities
Numerical Control Machine Operators translate engineering designs into machine instructions, operating CNC machinery globally. This role sees consistent demand across manufacturing sectors worldwide, driven by automation and precision requirements.
Cultural differences impact workplace safety standards and training methodologies, while regulatory frameworks dictate equipment certifications. Professionals seek international roles for higher wages, advanced technology exposure, and diverse industry experience. International certifications like ISO 9001 compliance demonstrate global readiness.
Global Salaries
Salaries for Numerical Control Machine Operators vary significantly by region. In North America, particularly the United States and Canada, annual salaries range from $45,000 to $70,000 USD. This reflects a strong manufacturing base and demand for skilled labor. European countries like Germany and Switzerland offer €40,000 to €65,000 (approximately $43,000-$70,000 USD), often with comprehensive benefits packages and generous vacation time.
Asia-Pacific markets, such as Japan and South Korea, typically offer ¥3.5 million to ¥5.5 million (around $23,000-$36,000 USD) and ₩35 million to ₩55 million (about $25,000-$40,000 USD), respectively. While these figures may seem lower, purchasing power parity often means a comparable standard of living given local cost of living. In Latin America, for instance, Mexico or Brazil, salaries might be $15,000 to $30,000 USD, but living costs are substantially lower.
International salary structures often include varying social security contributions, healthcare provisions, and pension schemes, affecting net take-home pay. For example, some European countries have higher income taxes but provide extensive public services. Experience and specialized machine certifications significantly impact compensation globally, with operators proficient in multi-axis or advanced CAD/CAM systems commanding higher pay. There are no standardized international pay scales for this role, but multinational manufacturers often align pay within their global operations.
Remote Work
Direct remote work for Numerical Control Machine Operators is generally not feasible, as the role requires hands-on operation of machinery. However, some aspects, like programming or simulation, can be performed remotely. This creates limited digital nomad opportunities for operators with strong programming skills.
Companies might hire operators for remote programming tasks, sending files to on-site technicians for execution. This arrangement necessitates robust internet and secure file transfer. Time zone differences can pose challenges for real-time collaboration with production teams. Employers typically do not offer international remote work for the core operational duties of this role. Salary for remote programming might be lower than on-site operational roles, reflecting the reduced physical presence and direct machine responsibility.
Visa & Immigration
Numerical Control Machine Operators often qualify for skilled worker visas in countries with strong manufacturing sectors. Popular destinations include Germany (Skilled Immigration Act), Canada (Express Entry), Australia (Skilled Nominated visa), and the United States (H-2B or E-3 for Australians). Requirements typically include a relevant vocational qualification or significant work experience.
Credential recognition is crucial; applicants may need to have their educational background assessed. English language proficiency (e.g., IELTS, PTE) is often a requirement for English-speaking countries. Visa processing times vary, ranging from a few months to over a year. Some countries offer pathways to permanent residency after several years of skilled employment. Family visas for dependents are generally available once the primary applicant secures their work visa.
2025 Market Reality for Numerical Control Machine Operators
Understanding the current market reality for Numerical Control Machine Operators is crucial. The manufacturing landscape has evolved significantly since 2023, shaped by post-pandemic reshoring efforts and the accelerating impact of AI on industrial processes.
Broader economic factors, such as supply chain stability and industrial output, directly influence job availability. Market realities also vary by experience level; entry-level positions face different challenges than senior roles. Geographic location and the size of the manufacturing firm also play a role. This analysis provides an honest assessment of current conditions.
Current Challenges
Numerical Control Machine Operators face increased competition. Automation and advanced AI tools require operators to handle more complex setups, reducing demand for basic machine tending roles. This also means fewer entry-level positions exist compared to previous years.
Economic uncertainty in manufacturing sectors, particularly automotive and aerospace, directly impacts hiring for these roles. Job seekers often find longer search times due to these factors.
Growth Opportunities
Strong opportunities exist for Numerical Control Machine Operators who specialize in advanced manufacturing. Roles involving complex 5-axis machining, additive manufacturing integration, or working with exotic materials are in high demand. These specialized areas often pay more and offer greater job security.
Operators who gain expertise in AI-driven CAM software, predictive analytics, or robotic cell integration hold a significant competitive advantage. Employers seek individuals who can optimize machine performance using data and advanced software, not just run programs. This skillset bridges the gap between traditional machining and Industry 4.0.
Underserved markets include defense manufacturing and medical device production, which often require high precision and specialized certifications. Investing in certifications for specific machine types or advanced software suites can open doors. Despite overall market challenges, sectors focused on high-precision, low-volume production continue to thrive, offering stable career paths.
Current Market Trends
Demand for Numerical Control Machine Operators remains steady but highly specialized in 2025. Employers prioritize candidates with strong programming skills and experience with multi-axis machines. The rise of automation, especially generative AI in CAD/CAM software, means operators now oversee more complex, integrated systems rather than just tending individual machines.
Economic shifts have led to some consolidation in smaller manufacturing firms. Larger, more technologically advanced facilities are hiring, but they seek operators who can troubleshoot, optimize code, and perform preventative maintenance. This shifts the role from purely operational to a blend of technician and programmer.
Salary growth for basic machine operation roles has slowed. However, operators skilled in advanced CNC programming, robotic integration, or specialized materials (e.g., composites, exotic metals) command higher wages. Market saturation exists for operators with only basic G-code knowledge. Geographic variations are significant; areas with strong aerospace, defense, or medical device manufacturing show higher demand, while traditional industrial regions might see slower growth.
Technology trends like digital twins and predictive maintenance are changing daily tasks. Operators need to interpret data from sensors and integrate new software updates. Remote work is almost non-existent for this hands-on role, emphasizing local market conditions.
Emerging Specializations
Technological advancements and evolving manufacturing processes are continuously reshaping career landscapes, creating entirely new specialization opportunities. For a Numerical Control Machine Operator, understanding these shifts is crucial for long-term career growth. Early positioning in emerging areas allows professionals to become subject matter experts as these niches mature, often commanding premium compensation and accelerated career progression.
While established specializations remain vital, exploring cutting-edge areas can unlock significant future potential. Emerging specializations typically gain significant traction and create widespread job opportunities within the next three to five years. This timeline allows for strategic skill development and early adoption.
Pursuing an emerging specialization involves a balance of risk and reward. While it offers the chance to be at the forefront of innovation and benefit from high demand, it requires adaptability and a commitment to continuous learning. However, the potential for increased earnings and leadership roles in these nascent fields often outweighs the initial uncertainty.
Robotic Integration Specialist
The integration of advanced robotics with CNC machining systems is creating a demand for operators who can program, oversee, and troubleshoot robotic arms that load, unload, and inspect parts directly on CNC machines. This specialization moves beyond traditional machine operation to include automation cell management, significantly increasing efficiency and precision in manufacturing environments. Operators in this role ensure seamless interaction between the CNC machine and robotic peripherals.
CNC Data Analytics Operator
With the rise of Industry 4.0, data analytics is becoming critical for optimizing machine performance and predictive maintenance. Numerical Control Machine Operators specializing in data-driven operations analyze sensor data from CNC machines to identify trends, predict failures, and optimize cutting parameters for improved part quality and reduced downtime. This role involves using software tools to interpret machine data and implement data-driven process improvements.
Hybrid Additive-Subtractive Manufacturing Operator
Additive manufacturing, particularly hybrid systems combining traditional CNC with 3D printing, is an emerging field. This specialization requires Numerical Control Machine Operators to understand both subtractive and additive processes, including material science for various deposition techniques. Operators in this area manage the complex interplay between material addition and removal, producing highly intricate and customized components.
Advanced Materials CNC Specialist
Advanced materials like composites, ceramics, and superalloys require specialized machining techniques due to their unique properties. Operators focusing on advanced materials must understand how these materials react to cutting forces, heat, and tool wear, adapting CNC programs and selecting appropriate tooling. This specialization is crucial for industries like aerospace, medical devices, and high-performance automotive.
In-Process Quality & Metrology Operator
The increasing complexity of CNC machines and the demand for higher precision necessitate specialization in advanced metrology and in-process quality control. This role involves using sophisticated measurement tools like laser trackers, vision systems, and touch probes integrated directly into the CNC process to ensure real-time quality assurance. Operators in this field ensure parts meet ultra-tight tolerances by actively monitoring and adjusting machining parameters.
Pros & Cons of Being a Numerical Control Machine Operator
Making informed career decisions requires understanding both the benefits and challenges of a professional path. Experiences within any career, including that of a Numerical Control Machine Operator, vary significantly based on factors such as company culture, specific industry sector (e.g., aerospace, automotive), specialization area, and individual personality. What one person perceives as an advantage, another might see as a disadvantage. Furthermore, the pros and cons can evolve at different stages of one's career, from an entry-level position to a senior role. This assessment provides an honest, balanced overview to help individuals set realistic expectations before committing to this field.
Pros
- Numerical Control Machine Operators are in consistent demand across various manufacturing industries, providing strong job security and numerous employment opportunities.
- The role offers a hands-on, practical work experience where operators directly contribute to the production of tangible goods, which can be highly satisfying.
- Many employers provide on-the-job training and apprenticeships, allowing individuals to enter this career without a four-year degree and gain valuable skills while earning a wage.
- Operators work with advanced machinery and technology, requiring a blend of technical skill and problem-solving, which can be intellectually stimulating.
- Wages for experienced Numerical Control Machine Operators are competitive, often including opportunities for overtime pay, which can significantly boost earning potential.
- There is a clear path for skill development, as operators can advance by learning more complex machine programming, setup procedures, or moving into quality control or supervisory roles.
- The manufacturing sector is diverse, allowing Numerical Control Machine Operators to work in various fields, from medical devices to automotive parts, offering flexibility in industry choice.
Cons
- The work environment for Numerical Control Machine Operators can be noisy and dusty, requiring consistent use of personal protective equipment and potentially impacting long-term hearing or respiratory health.
- Numerical Control Machine Operators often work shifts, including nights and weekends, to keep machines running continuously, which can disrupt personal life and social schedules.
- The work can be physically demanding, involving prolonged standing, repetitive motions, and occasional lifting of heavy materials or parts, leading to fatigue or musculoskeletal strain.
- While programming skills are valuable, the day-to-day tasks for an operator are often repetitive, loading and unloading parts, monitoring machine cycles, and making minor adjustments, which may lead to monotony.
- Job security for Numerical Control Machine Operators can be sensitive to economic downturns or industry shifts, as manufacturing output directly impacts the demand for their skills.
- A high degree of precision and attention to detail is required, as errors in setup or operation can lead to expensive material waste or machine damage, creating a stressful work environment.
- Despite the advanced machinery, career progression for a Numerical Control Machine Operator can be limited without pursuing further education in programming, engineering, or supervisory roles, potentially plateauing at the operator level.
Frequently Asked Questions
Numerical Control Machine Operators face distinct questions about precision, machine maintenance, and programming. This section addresses common concerns about entering this hands-on field, from mastering complex machinery to understanding safety protocols and career progression within manufacturing.
How long does it take to become job-ready as a Numerical Control Machine Operator if I'm starting from scratch?
You can become an entry-level Numerical Control Machine Operator in 6 to 18 months, depending on your chosen training path. Vocational programs or community college courses typically take 6-12 months to cover machine operation, blueprint reading, and basic G-code. Apprenticeships might extend to 1-2 years but offer valuable on-the-job experience and direct mentorship. Practical machine time is crucial for developing proficiency.
Do I need a specific degree or certification to become a Numerical Control Machine Operator?
No, a four-year degree is not typically required. Most Numerical Control Machine Operators enter the field through vocational training, community college programs, or apprenticeships. Employers value practical skills, certifications like NIMS (National Institute for Metalworking Skills), and hands-on experience over formal academic degrees. Demonstrating mechanical aptitude and a willingness to learn are key qualifications.
What are the typical salary expectations for a Numerical Control Machine Operator, and how does experience affect pay?
Entry-level Numerical Control Machine Operators can expect to earn around $35,000 to $45,000 annually. With a few years of experience and specialized skills, such as advanced programming or operating complex multi-axis machines, salaries can rise to $50,000-$65,000 or more. Location, industry, and shift work can also influence earnings.
What is the typical work-life balance like for a Numerical Control Machine Operator, considering shifts and demands?
The work-life balance for Numerical Control Machine Operators varies but often involves working shifts, including evenings or weekends, especially in facilities with 24/7 production. The work itself is hands-on and requires focus, but it is generally stable and predictable. Overtime can be common during peak production times, which impacts personal time but also increases earning potential.
Is the job outlook for Numerical Control Machine Operators secure, or is automation a threat to this role?
The job market for Numerical Control Machine Operators remains stable and in demand due to ongoing needs in manufacturing, aerospace, and automotive industries. Automation is changing some aspects of the role, but skilled operators who can set up, troubleshoot, and maintain machines are still highly valued. The ability to adapt to new technologies enhances job security.
What are the common career advancement opportunities for a Numerical Control Machine Operator?
Career growth for Numerical Control Machine Operators can lead to roles such as CNC Programmer, Lead Operator, Shop Foreman, or even manufacturing engineering technician. Advancing typically requires gaining expertise in CAM software, advanced G-code programming, and understanding manufacturing processes. Continuous learning and certifications are vital for upward mobility.
What are the biggest challenges or downsides of working as a Numerical Control Machine Operator?
The primary challenges include the need for extreme precision and attention to detail, as errors can be costly. Operators must also stay updated with evolving machine technology and programming languages. The work environment can be noisy and requires adherence to strict safety protocols, and you spend much of your day on your feet.
Is remote work a possibility for a Numerical Control Machine Operator, or is it strictly an on-site role?
Numerical Control Machine Operator roles are almost exclusively on-site because they involve direct interaction with physical machinery. While some programming or planning tasks might occasionally be done remotely, the core responsibilities of machine setup, operation, and maintenance require a physical presence. Therefore, remote work flexibility is very limited in this career.
Related Careers
Explore similar roles that might align with your interests and skills:
CNC Machine Operator
A growing field with similar skill requirements and career progression opportunities.
Explore career guideCnc Machinist
A growing field with similar skill requirements and career progression opportunities.
Explore career guideCnc Operator
A growing field with similar skill requirements and career progression opportunities.
Explore career guideComputer Numerically Controlled (CNC) Machinist
A growing field with similar skill requirements and career progression opportunities.
Explore career guideComputer Numerically Controlled (CNC) Milling Machine Operator
A growing field with similar skill requirements and career progression opportunities.
Explore career guideAssess your Numerical Control Machine Operator readiness
Understanding where you stand today is the first step toward your career goals. Our Career Coach helps identify skill gaps and create personalized plans.
Skills Gap Analysis
Get a detailed assessment of your current skills versus Numerical Control Machine Operator requirements. Our AI Career Coach identifies specific areas for improvement with personalized recommendations.
See your skills gapCareer Readiness Assessment
Evaluate your overall readiness for Numerical Control Machine Operator roles with our AI Career Coach. Receive personalized recommendations for education, projects, and experience to boost your competitiveness.
Assess your readinessSimple pricing, powerful features
Upgrade to Himalayas Plus and turbocharge your job search.
Himalayas
Himalayas Plus
Himalayas Max
Find your dream job
Sign up now and join over 100,000 remote workers who receive personalized job alerts, curated job matches, and more for free!
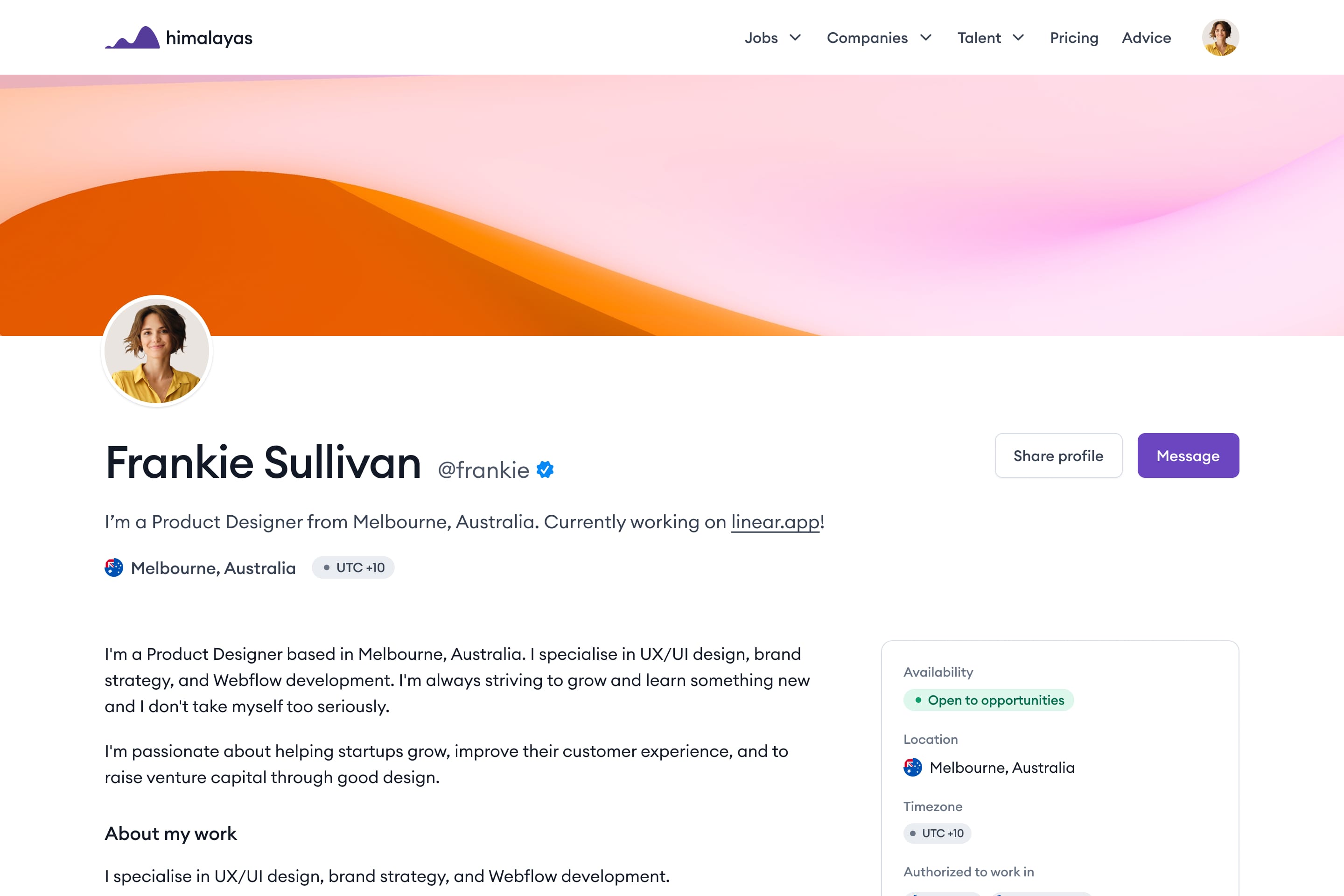