Complete Nickel Plater Career Guide
Nickel platers are skilled artisans who apply a precise layer of nickel onto various materials, protecting them from corrosion, enhancing durability, and improving aesthetics. This specialized trade is vital across manufacturing, ensuring critical components function flawlessly in demanding environments. It is a hands-on career, blending chemistry and craftsmanship, offering stable opportunities for those who master its intricacies.
Key Facts & Statistics
Median Salary
$46,900 USD
(U.S. national median for Platers, Metal and Plastic, U.S. Bureau of Labor Statistics, May 2023)
Range: $35k - $65k+ USD, varying significantly with experience, specialization, and region. Highly experienced platers can earn more.
Growth Outlook
3%
(for Platers, Metal and Plastic), slower than average (U.S. Bureau of Labor Statistics, 2022-2032).
Annual Openings
≈3,800
openings annually (for Platers, Metal and Plastic), including new jobs and replacements.
Top Industries
Typical Education
High school diploma or equivalent; often supplemented by on-the-job training, apprenticeships, or vocational programs focusing on plating and metal finishing.
What is a Nickel Plater?
A Nickel Plater applies a protective or decorative nickel coating to metal parts through an electrochemical process. This professional prepares surfaces, operates plating equipment, and monitors chemical solutions to ensure the precise application of nickel. The primary goal is to enhance the part's corrosion resistance, wear resistance, or aesthetic appeal, depending on the application.
Unlike general metal finishers who might work with various coatings like paint or powder, a Nickel Plater specializes specifically in the intricacies of nickel electroplating. Their expertise lies in understanding the complex chemical reactions and electrical parameters required to achieve a high-quality, durable nickel finish, which is crucial for industries from automotive to electronics.
What does a Nickel Plater do?
Key Responsibilities
- Prepare metal surfaces by cleaning, degreasing, and rinsing parts to ensure optimal adhesion for the nickel coating.
- Operate and monitor electroplating tanks, adjusting voltage, amperage, and temperature settings to maintain precise plating conditions.
- Mix and replenish plating solutions, adding chemicals and brighteners according to established formulas and safety protocols.
- Inspect plated parts for defects such as pitting, blistering, or uneven coating, performing quality checks to meet specifications.
- Maintain accurate records of plating processes, including solution compositions, plating times, and production output.
- Conduct routine maintenance on plating equipment, including filter changes and anode inspections, to ensure continuous operation.
- Adhere to strict safety guidelines, including the proper handling of hazardous chemicals and the use of personal protective equipment (PPE).
Work Environment
Nickel platers typically work in industrial settings such as manufacturing plants, fabrication shops, or specialized plating facilities. The environment can be noisy due to machinery and may involve exposure to chemicals, requiring strict adherence to safety protocols and the use of personal protective equipment.
Work often involves standing for extended periods and handling metal parts, which can be heavy. Collaboration with other production team members, such as quality control technicians and material handlers, is common. The work pace is steady, driven by production schedules, and shifts can vary, sometimes including evenings or weekends, depending on the facility's operational needs.
Tools & Technologies
Nickel platers primarily work with specialized electroplating tanks and power rectifiers that control the electrical current. They use various measuring instruments, including pH meters, hydrometers, and thermometers, to monitor solution chemistry and temperature. Calibration tools ensure the accuracy of these instruments.
For surface preparation, they utilize industrial cleaning agents, abrasive blasting equipment, and specialized cleaning baths. Material handling equipment, such as hoists and forklifts, move parts in and out of plating tanks. Essential safety equipment includes respirators, chemical-resistant gloves, aprons, and eye protection.
Nickel Plater Skills & Qualifications
Becoming a successful Nickel Plater requires a specific blend of practical skills, attention to detail, and a commitment to safety and quality. Qualifications for this role are primarily built upon hands-on experience and vocational training rather than extensive formal education. Employers prioritize demonstrable ability to operate plating equipment, mix chemical solutions accurately, and inspect finished products for adherence to specifications.
Requirements for Nickel Platers vary little by company size or industry, as the core process remains consistent. However, larger manufacturers with automated lines might seek candidates with basic understanding of PLC controls or automation, while smaller job shops emphasize versatility across various plating types. Geographic location can influence demand, with concentrations of manufacturing impacting job availability. The importance of certifications is growing, particularly those related to hazardous materials handling and specific plating standards, which can significantly enhance a candidate's appeal.
Formal education, such as a four-year degree, holds less weight than practical experience in this field. Vocational programs, apprenticeships, and on-the-job training are the most common and effective pathways into this career. The skill landscape for Nickel Platers is relatively stable, though advancements in environmental regulations and material science occasionally introduce new safety protocols or solution formulations. Mastering precision and process control remains paramount throughout a Nickel Plater's career, regardless of seniority.
Education Requirements
Technical Skills
- Chemical Solution Preparation and Maintenance: Accurately mixing plating bath chemicals, performing titrations, and adjusting concentrations to maintain optimal plating performance.
- Electroplating Principles: Understanding the electrochemical process, anode/cathode reactions, voltage, current density, and their impact on plating thickness and adhesion.
- Plating Equipment Operation: Setting up, operating, and monitoring rectifiers, tanks, pumps, filters, and agitation systems used in nickel plating.
- Material Handling and Racking: Safely loading and unloading parts onto plating racks or barrels, ensuring proper contact and minimizing defects.
- Quality Control and Inspection: Using micrometers, calipers, and visual inspection techniques to verify plating thickness, adhesion, uniformity, and surface finish.
- Wastewater Treatment and Environmental Compliance: Knowledge of wastewater treatment processes and adherence to environmental regulations for chemical disposal and emissions.
- Hazardous Materials Handling: Safe handling, storage, and disposal of acids, bases, and other plating chemicals, including understanding Safety Data Sheets (SDS).
- Basic Mechanical Troubleshooting: Identifying and resolving minor issues with pumps, filters, and other mechanical components of plating lines.
- Surface Preparation Techniques: Cleaning, degreasing, and activating metal surfaces prior to plating to ensure proper adhesion and finish.
Soft Skills
- Attention to Detail: Nickel Platers must meticulously follow instructions, measure chemicals precisely, and inspect parts for flaws to ensure high-quality finishes and prevent costly errors.
- Problem-Solving: Identifying and troubleshooting issues with plating baths, equipment malfunctions, or quality defects requires analytical thinking to restore proper operation.
- Safety Consciousness: Working with hazardous chemicals and electrical equipment demands strict adherence to safety protocols, including proper use of PPE and emergency procedures, to protect oneself and others.
- Manual Dexterity: Handling small parts, setting up plating racks, and manipulating equipment requires fine motor skills and steady hands to prevent damage and ensure efficient processing.
- Adherence to Procedures: Strict compliance with written procedures, quality standards, and environmental regulations is critical for consistent results and avoiding non-compliance issues.
- Time Management: Efficiently managing multiple plating cycles, preparing solutions, and cleaning equipment requires strong organizational skills to meet production deadlines.
- Communication: Effectively reporting issues, receiving instructions, and collaborating with team members on production schedules or quality control ensures smooth operations.
How to Become a Nickel Plater
Entering the nickel plating field offers several pathways, from direct entry-level positions to apprenticeships or vocational training. While formal degrees are not typically required, hands-on experience and a strong understanding of chemical processes and safety protocols are paramount. The timeline for entry can range from a few weeks for basic shop helper roles to 1-2 years for comprehensive apprenticeship programs that lead to more skilled positions.
Many plating shops, especially smaller ones, prioritize practical aptitude and a willingness to learn over extensive prior experience. Larger industrial facilities might prefer candidates with some vocational training or certifications in hazardous materials handling. Geographic location plays a role; areas with significant manufacturing industries will have more opportunities. Understanding the specific needs of different industries—like automotive, aerospace, or electronics—can also help tailor your approach.
Breaking into this field often involves starting in a foundational role, such as a production assistant or general laborer, and then progressing through on-the-job training. Networking within local manufacturing or finishing associations can uncover unadvertised openings. Overcoming barriers like a lack of initial experience is best achieved by demonstrating reliability, attention to detail, and a commitment to safety from day one, which are highly valued in this precision-oriented environment.
Step 1
Step 2
Step 3
Step 4
Step 5
Step 6
Education & Training Needed to Become a Nickel Plater
Becoming a skilled Nickel Plater primarily involves hands-on training and specialized certifications rather than traditional four-year degrees. While a high school diploma or GED is usually a prerequisite, the core educational pathway focuses on vocational training, apprenticeships, or on-the-job learning. Formal degree programs are largely irrelevant for direct entry into this role, as the work emphasizes practical application of chemical processes and safety protocols.
Apprenticeships and vocational programs typically cost between $500 and $5,000, often taking 6 months to 2 years to complete. These programs provide a structured curriculum covering electroplating principles, chemical handling, quality control, and safety. Self-study and on-the-job training can range from 3 months to over a year, with minimal direct cost beyond materials, but often require significant personal initiative. Employers generally prefer candidates with formal training or proven experience, as this indicates a foundational understanding of the complex chemical interactions and safety procedures critical to nickel plating.
Continuous learning in nickel plating involves staying updated on new plating technologies, environmental regulations, and safety standards. Specialized workshops and certifications in areas like hazardous waste management or advanced electroplating techniques are valuable for career advancement. These shorter courses may cost a few hundred to a couple thousand dollars and typically last from a few days to several weeks. Practical experience remains paramount; however, combining it with targeted education enhances a plater's versatility and marketability, enabling them to handle diverse plating applications and troubleshoot effectively.
Nickel Plater Salary & Outlook
Compensation for a Nickel Plater varies significantly based on several factors. Geographic location plays a crucial role, as areas with high manufacturing or industrial demand often offer higher wages due to increased cost of living and specialized industry presence. The specific industry, such as aerospace, automotive, or electronics, also influences pay scales, with more niche or high-precision sectors typically offering better compensation.
Years of experience dramatically impact earning potential. Entry-level positions start lower, while experienced platers with specialized skills in complex plating techniques or quality control command higher salaries. Total compensation extends beyond base pay; it often includes overtime opportunities, production bonuses, and comprehensive benefits packages like health insurance, retirement contributions, and paid time off. Some companies may offer profit-sharing or performance incentives.
Negotiation leverage comes from demonstrated expertise, certifications in plating processes, and the ability to maintain stringent quality standards. Remote work is not typically applicable for this hands-on role, so geographic salary arbitrage is not a factor. While these figures focus on the USD market, international markets will have their own distinct wage structures based on local industrial activity and economic conditions.
Salary by Experience Level
Level | US Median | US Average |
---|---|---|
Junior Nickel Plater | $38k USD | $40k USD |
Nickel Plater | $46k USD | $48k USD |
Senior Nickel Plater | $56k USD | $58k USD |
Lead Nickel Plater | $65k USD | $68k USD |
Plating Supervisor | $75k USD | $78k USD |
Market Commentary
The job market for Nickel Platers remains stable, driven by consistent demand in various manufacturing sectors. Industries like automotive, aerospace, defense, and electronics rely heavily on nickel plating for corrosion resistance, wear protection, and aesthetic finishes. This consistent industrial need underpins a steady demand for skilled platers, making it a relatively resilient profession.
Growth in this field is often tied to the broader manufacturing output and technological advancements that require specialized surface finishes. While not experiencing rapid expansion, the market benefits from the ongoing need for durable and high-performance components. Automation and advanced robotics might impact some repetitive tasks, but the intricate nature of plating, quality inspection, and process management still requires human expertise. Future-proofing involves continuous learning in new plating technologies, environmental regulations, and quality assurance protocols.
Supply and demand dynamics for skilled platers are generally balanced, with some regions experiencing a shortage of highly experienced professionals. This can lead to competitive wages in specific industrial hubs. The profession is less susceptible to economic downturns compared to highly cyclical industries, as the need for component durability persists. Geographic hotspots for employment include manufacturing-heavy states and regions with strong aerospace or defense industries, such as the Midwest and parts of the Southeast.
Nickel Plater Career Path
Career progression for a Nickel Plater typically follows a structured path within manufacturing or specialized plating facilities. Advancement relies heavily on mastering technical skills, understanding chemical processes, and ensuring quality control. Professionals can choose an individual contributor (IC) track, focusing on advanced plating techniques and problem-solving, or a management track, leading teams and overseeing operations.
Advancement speed depends on consistent high performance, the complexity of plating projects handled, and a willingness to learn new methods. Specialization in areas like aerospace or medical device plating, which demand tighter tolerances, accelerates progression. Company size also influences paths; larger corporations may offer more formal leadership roles, while smaller shops might see platers take on broader technical responsibilities earlier.
Lateral movement often involves cross-training in other plating types or moving into quality assurance roles. Continuous learning, including certifications in hazardous materials handling or specific plating standards, marks significant milestones. Networking within industry associations and mentorship from experienced platers are crucial for understanding best practices and identifying opportunities. Economic conditions, particularly in manufacturing sectors, can impact demand for skilled platers and influence career opportunities.
Junior Nickel Plater
0-2 yearsKey Focus Areas
Nickel Plater
2-5 yearsKey Focus Areas
Senior Nickel Plater
5-8 yearsKey Focus Areas
Lead Nickel Plater
8-12 yearsKey Focus Areas
Plating Supervisor
12+ years total experienceKey Focus Areas
Junior Nickel Plater
0-2 yearsPerform routine nickel plating operations under direct supervision. Prepare parts for plating, including cleaning and masking. Load and unload plating lines, ensuring proper racking and jigging. Monitor basic bath parameters and record initial data. Assist in quality checks for plated parts, identifying obvious defects.
Key Focus Areas
Develop foundational knowledge of nickel plating baths, rectifiers, and safety protocols. Master precise measurement techniques and basic equipment operation. Focus on understanding material handling, racking, and jigging for various part geometries. Learn to identify common plating defects and their immediate causes. Seek guidance from senior platers and adhere strictly to all safety guidelines.
Nickel Plater
2-5 yearsExecute complex nickel plating jobs independently, adhering to precise specifications. Conduct regular bath analysis and make necessary chemical additions. Troubleshoot common plating issues and implement corrective actions. Maintain detailed process logs and ensure compliance with quality standards. Train and guide junior platers on specific tasks.
Key Focus Areas
Refine skills in bath chemistry adjustments, troubleshooting minor process deviations, and optimizing plating parameters for different specifications. Develop a deeper understanding of various nickel plating types (e.g., bright, dull, electroless) and their applications. Cross-train on different plating lines or equipment. Begin mentoring junior colleagues on basic procedures.
Senior Nickel Plater
5-8 yearsAct as a subject matter expert for all nickel plating processes, leading complex projects and resolving persistent technical challenges. Develop and implement new plating procedures or improve existing ones. Conduct root cause analysis for critical defects and propose long-term solutions. Provide technical training and mentorship to less experienced platers.
Key Focus Areas
Acquire expertise in advanced troubleshooting, process optimization, and defect analysis. Develop a comprehensive understanding of metallurgy and surface science related to plating. Lead continuous improvement initiatives and participate in process development. Mentor and provide technical guidance to platers, fostering skill development.
Lead Nickel Plater
8-12 yearsOversee daily operations for a specific plating line or a small team of platers. Coordinate production schedules, allocate resources, and ensure timely completion of orders. Provide technical leadership and guidance, resolving complex operational issues. Monitor team performance, implement process improvements, and ensure adherence to safety and quality standards.
Key Focus Areas
Develop strong leadership and communication skills, delegating tasks effectively and fostering a collaborative team environment. Master advanced process control, statistical process control (SPC), and lean manufacturing principles. Focus on strategic planning for production schedules and resource allocation. Cultivate problem-solving abilities for systemic operational challenges.
Plating Supervisor
12+ years total experienceManage an entire plating department or multiple plating lines, overseeing all personnel, equipment, and processes. Develop and implement departmental budgets, production goals, and quality objectives. Lead continuous improvement initiatives across the entire plating operation. Ensure compliance with all safety, environmental, and industry regulations. Responsible for staff development, performance reviews, and hiring decisions.
Key Focus Areas
Enhance strategic planning, budgeting, and personnel management capabilities. Develop expertise in regulatory compliance, environmental health and safety (EHS) standards, and quality management systems (e.g., ISO). Focus on cross-functional collaboration with engineering, quality, and supply chain departments. Build strong leadership and motivational skills to manage a diverse workforce.
Job Application Toolkit
Ace your application with our purpose-built resources:
Global Nickel Plater Opportunities
Nickel plating is a specialized skill with consistent global demand, particularly in manufacturing, aerospace, and electronics. This profession translates across countries due to standardized industrial processes, though regulatory differences in environmental compliance and safety exist. International opportunities arise from global supply chains and manufacturing hubs shifting. Professionals often seek overseas roles for better wages or exposure to advanced technologies. No specific international certifications exist; practical experience and adherence to industry standards are key for global mobility.
Global Salaries
Nickel Plater salaries vary significantly by region and industrial demand. In North America, a Nickel Plater in the United States earns between $40,000 and $65,000 USD annually, while in Canada, the range is CAD 45,000 to CAD 70,000. These figures reflect a higher cost of living compared to some other regions. Benefits typically include health insurance and retirement plans.
European salaries for Nickel Platers show a broad spectrum. In Germany, a Nickel Plater might earn between €30,000 and €45,000 (approximately $32,000-$48,000 USD). The UK offers similar ranges, from £25,000 to £38,000 (around $31,000-$47,000 USD). These countries often provide robust social security and generous vacation time, impacting the overall compensation package. Purchasing power parity is crucial; a lower nominal salary in Eastern Europe might offer similar living standards to a higher one in Western Europe.
In Asia-Pacific, particularly in countries like South Korea or Japan, Nickel Platers can expect salaries ranging from KRW 35,000,000 to KRW 55,000,000 (approximately $25,000-$40,000 USD) or JPY 3,500,000 to JPY 5,500,000 (around $22,000-$35,000 USD), respectively. These economies often have lower direct tax burdens, but benefits might be less comprehensive than in European systems. Experience and specialized plating techniques significantly influence compensation across all regions.
Remote Work
Nickel plating is a hands-on, industrial process, making traditional remote work impossible for the core job functions. The role requires physical presence in a manufacturing facility to operate equipment and handle materials. Therefore, digital nomad opportunities do not apply directly to this profession.
However, some peripheral aspects might allow for remote work. For instance, a senior Nickel Plater might remotely consult on process optimization, quality control standards, or training for a multinational company. Such roles are rare and typically reserved for highly experienced individuals. Companies do not generally hire Nickel Platers for international remote work.
Salary expectations for such niche remote consulting roles would depend on the project's scope and the consultant's expertise, often negotiated on a project basis. These roles involve minimal equipment beyond a computer and reliable internet, focusing on knowledge transfer rather than direct plating tasks. Most Nickel Platers should expect to work on-site.
Visa & Immigration
Nickel Platers seeking international work typically apply for skilled worker visas. Countries like Canada, Australia, and Germany often have pathways for tradespeople, including those in manufacturing. Requirements generally include a job offer from an employer, proof of relevant work experience, and sometimes trade skill assessments.
For instance, Canada's Express Entry system or Germany's Skilled Immigration Act can be options. Education credential recognition is less formal for this trade; practical experience and employer sponsorship are more critical. Professional licensing is not common for Nickel Platers, but industry certifications in specific processes or safety may be beneficial.
Visa timelines vary, from a few months to over a year, depending on the country and visa type. Language requirements are usually for general immigration purposes, not specific to the trade itself. Pathways to permanent residency exist in many countries that encourage skilled immigration. Family visas allow dependents to accompany the primary applicant, though specific rights vary by nation.
2025 Market Reality for Nickel Platers
Understanding current market realities for nickel platers is crucial for career longevity and strategic planning. The industry has seen shifts due to technological advancements and evolving economic landscapes.
Post-pandemic, supply chain disruptions initially impacted material availability, but demand has largely stabilized. The broader economic climate, particularly in manufacturing and industrial production, directly influences job availability. Market conditions vary by experience level, with senior platers often finding more stable roles, and by company size, as larger facilities may have more consistent demand. This analysis provides an honest assessment of these dynamics.
Current Challenges
Nickel platers face increasing competition from automated plating lines, which reduce the need for manual labor. Economic downturns impact manufacturing, leading to fewer plating orders and potential layoffs. Maintaining certifications and staying updated on safety regulations adds to the professional burden. The physical demands and exposure to chemicals deter some candidates.
Growth Opportunities
Despite challenges, skilled nickel platers find strong opportunities in niche markets. Precision plating for medical devices, aerospace components, and advanced electronics continues to see demand, often requiring specific expertise. Platers proficient in specialized techniques, such as electroless nickel plating or composite coatings, are particularly sought after.
Opportunities exist in companies that prioritize quality control and adherence to strict industry standards. Developing expertise in automated plating systems or quality assurance roles can provide a competitive edge. Underserved markets might include smaller, specialized fabrication shops that require custom plating solutions rather than high-volume production.
Investing in certifications for new plating technologies or advanced materials can significantly enhance career prospects. Some employers offer apprenticeship programs, providing a pathway for new entrants to gain essential skills. The demand for durable, high-performance coatings ensures a continued, albeit specialized, need for skilled nickel platers.
Current Market Trends
The market for nickel platers is stable but not experiencing rapid growth. Demand primarily comes from specialized manufacturing, aerospace, and electronics sectors needing corrosion resistance and conductivity. Automation continues to influence the plating industry, with many facilities investing in robotic systems for repetitive tasks.
Hiring patterns show a consistent need for skilled platers, especially those with experience in complex geometries or precision applications. Economic conditions, particularly in the automotive and defense industries, directly affect plating volumes. Companies prioritize candidates demonstrating strong safety compliance and problem-solving skills, as mistakes are costly.
Salary trends for experienced nickel platers remain competitive, reflecting the specialized nature of the work. Entry-level positions face more competition, and wages may be lower. Geographic variations are significant; areas with strong manufacturing bases, like the Midwest and Southeast U.S., offer more opportunities. Remote work is not applicable to this hands-on role.
Emerging Specializations
Technological advancements and evolving industry demands continuously reshape career landscapes, creating new specialization opportunities. For nickel platers, understanding these shifts is crucial for securing future-proof career paths. Early positioning in emerging areas, particularly those driven by automation, advanced materials, and environmental regulations, can significantly accelerate career growth beyond 2025.
Specializing in cutting-edge techniques often commands premium compensation and enhanced career prospects compared to traditional plating methods. While established specializations offer stability, emerging fields promise a higher trajectory for innovation and leadership. Many emerging areas, initially niche, are rapidly moving towards mainstream adoption, creating substantial job opportunities within the next 3-5 years.
Embracing these new specializations involves a strategic risk-reward consideration. It requires investing in new skill sets and adapting to evolving processes. However, the potential for significant professional development and increased earning potential typically outweighs the initial investment. Professionals who proactively embrace these shifts will be well-positioned for the next generation of opportunities in the plating industry.
Composite Material Plating Specialist
Sustainable Plating Process Engineer
Automated Plating Systems Technician
Advanced Functional Coating Specialist
Additive Manufacturing Post-Plating Specialist
Pros & Cons of Being a Nickel Plater
Making informed career choices requires a clear understanding of both the potential advantages and genuine challenges of a profession. The experience of a Nickel Plater, like any job, can vary significantly based on the specific company, industry, and the individual's role within the plating operation. Factors such as company culture, the type of products being plated, and the level of automation present can all influence daily tasks and overall job satisfaction. Moreover, the pros and cons may evolve as one progresses from an entry-level position to a more senior or specialized role within the field. What one person considers a benefit, another might view as a drawback, depending on their personal values, work preferences, and long-term career aspirations. This assessment aims to provide a realistic overview to help set appropriate expectations for those considering a career as a Nickel Plater.
Pros
- Nickel Platers gain specialized technical skills in electroplating, chemical handling, and quality control, which are valuable in manufacturing and can be transferred to other finishing processes like chrome or zinc plating.
- There is a consistent demand for skilled Nickel Platers across various manufacturing sectors, including automotive, aerospace, electronics, and decorative finishes, providing good job stability.
- Many entry-level Nickel Plater positions require only a high school diploma, with on-the-job training being common, making it accessible to individuals without extensive prior education or experience.
- The work often involves hands-on problem-solving, such as troubleshooting plating defects or adjusting chemical compositions, providing intellectual engagement and a sense of accomplishment.
- Nickel Platers contribute directly to the quality and durability of products, which can be a source of pride, knowing their work enhances the functionality and appearance of manufactured goods.
- Some companies offer opportunities for skill diversification, allowing platers to learn about different plating materials, surface treatments, or even process automation, expanding their expertise.
- The pay for experienced Nickel Platers is generally competitive within the manufacturing sector, especially for those with a strong safety record and expertise in complex plating operations.
Cons
- Exposure to hazardous chemicals like nickel salts, acids, and bases is a constant concern, requiring strict adherence to safety protocols and the use of personal protective equipment to prevent skin irritation, respiratory issues, and other health problems.
- The work environment often involves high temperatures, humidity, and poor ventilation, making it physically demanding and uncomfortable, particularly during long shifts.
- Precision and attention to detail are critical; even minor errors in chemical concentrations, plating time, or current can lead to defective products, resulting in rework, material waste, and production delays.
- Repetitive tasks, such as loading and unloading parts from plating racks, can lead to musculoskeletal disorders like carpal tunnel syndrome or tendonitis over time.
- Career advancement opportunities for a Nickel Plater can be limited, often requiring further education or cross-training into other electroplating specialties or supervisory roles.
- The job can be monotonous due to the repetitive nature of preparing baths, monitoring processes, and racking parts, which may not appeal to individuals seeking varied daily tasks.
- Maintaining the correct chemical balance in plating baths is complex and requires continuous testing and adjustments, which can be a source of stress and requires specialized knowledge to troubleshoot effectively when issues arise, often under pressure to minimize downtime or rejections from quality control.
Frequently Asked Questions
Nickel Platers face distinct questions about the hands-on nature of the work, safety protocols, and the specific skills required for precise metal finishing. This section addresses common uncertainties about entering this specialized trade, from training pathways to career stability and daily work environments.
What are the typical entry requirements and qualifications to become a Nickel Plater?
Entry into nickel plating often begins with on-the-job training, an apprenticeship, or a vocational program. While a formal degree is not usually required, a strong mechanical aptitude and attention to detail are crucial. Many employers prefer candidates with a high school diploma or GED who can demonstrate basic math and chemistry knowledge, as these are fundamental to understanding plating processes.
How long does it take to become a skilled Nickel Plater if I'm starting from scratch?
Becoming proficient as a Nickel Plater typically takes 1-3 years, depending on the training path. Apprenticeships or vocational programs usually last 1-2 years, combining classroom instruction with practical experience. If starting with only on-the-job training, it might take longer to master the various plating techniques, chemical handling, and quality control necessary for independent work.
What are the salary expectations for a Nickel Plater, both entry-level and experienced?
Salaries for Nickel Platers vary by experience, location, and industry. Entry-level positions might start around $35,000-$45,000 annually. Experienced and highly skilled platers, especially those with specialized certifications or leadership roles, can earn $55,000-$70,000 or more. Overtime opportunities are common in many plating shops, which can significantly boost earnings.
What is the typical work-life balance like for a Nickel Plater, considering the nature of the job?
Work-life balance for Nickel Platers can depend on the specific company and industry. Many plating facilities operate standard day shifts, but some industrial operations might require evening or night shifts, or weekend work to meet production demands. The work involves physical labor and exposure to chemicals, so maintaining safety protocols and a healthy lifestyle is important to mitigate the physical demands of the job.
Is the Nickel Plater role a secure job with good market demand, or is it at risk of automation?
The demand for skilled Nickel Platers remains stable, particularly in industries requiring corrosion protection, aesthetics, or specific material properties, such as aerospace, automotive, and electronics. While automation handles some aspects, the precise and quality-critical nature of nickel plating often requires human expertise, ensuring ongoing job security for skilled professionals. Staying updated on new plating technologies and safety standards enhances long-term career prospects.
What are the potential career growth and advancement opportunities for a Nickel Plater?
Career growth for Nickel Platers can lead to supervisory roles, quality control positions, or specialization in advanced plating techniques. With experience, platers can transition into roles like Plating Supervisor, Process Engineer, or even pursue sales or technical support roles for plating chemical suppliers. Gaining certifications in specific plating methods or chemical handling can also open doors to higher-paying and more responsible positions.
What are the biggest challenges or common difficulties faced by Nickel Platers in their daily work?
The primary challenges in nickel plating include precise chemical management, maintaining safety protocols due to chemical exposure, and ensuring consistent quality in plating thickness and adhesion. Platers must constantly monitor bath chemistry, troubleshoot plating defects, and adapt to varying material specifications. Adherence to strict environmental regulations is also a continuous concern, requiring meticulous record-keeping and waste management practices.
Is there any flexibility for remote work or varied locations as a Nickel Plater?
Nickel plating is a highly hands-on role that requires direct interaction with plating tanks, parts, and chemical solutions. Therefore, remote work is not an option for the core plating responsibilities. However, with significant experience, some platers might transition into roles like process consulting, technical sales, or management, which could involve some remote administrative or advisory tasks, but the actual plating work is always on-site.
Related Careers
Explore similar roles that might align with your interests and skills:
Chrome Plater
A growing field with similar skill requirements and career progression opportunities.
Explore career guideChromium Plater
A growing field with similar skill requirements and career progression opportunities.
Explore career guideElectroplater
A growing field with similar skill requirements and career progression opportunities.
Explore career guideMetal Plater
A growing field with similar skill requirements and career progression opportunities.
Explore career guideTin Plater
A growing field with similar skill requirements and career progression opportunities.
Explore career guideAssess your Nickel Plater readiness
Understanding where you stand today is the first step toward your career goals. Our Career Coach helps identify skill gaps and create personalized plans.
Skills Gap Analysis
Get a detailed assessment of your current skills versus Nickel Plater requirements. Our AI Career Coach identifies specific areas for improvement with personalized recommendations.
See your skills gapCareer Readiness Assessment
Evaluate your overall readiness for Nickel Plater roles with our AI Career Coach. Receive personalized recommendations for education, projects, and experience to boost your competitiveness.
Assess your readinessSimple pricing, powerful features
Upgrade to Himalayas Plus and turbocharge your job search.
Himalayas
Himalayas Plus
Himalayas Max
Find your dream job
Sign up now and join over 100,000 remote workers who receive personalized job alerts, curated job matches, and more for free!
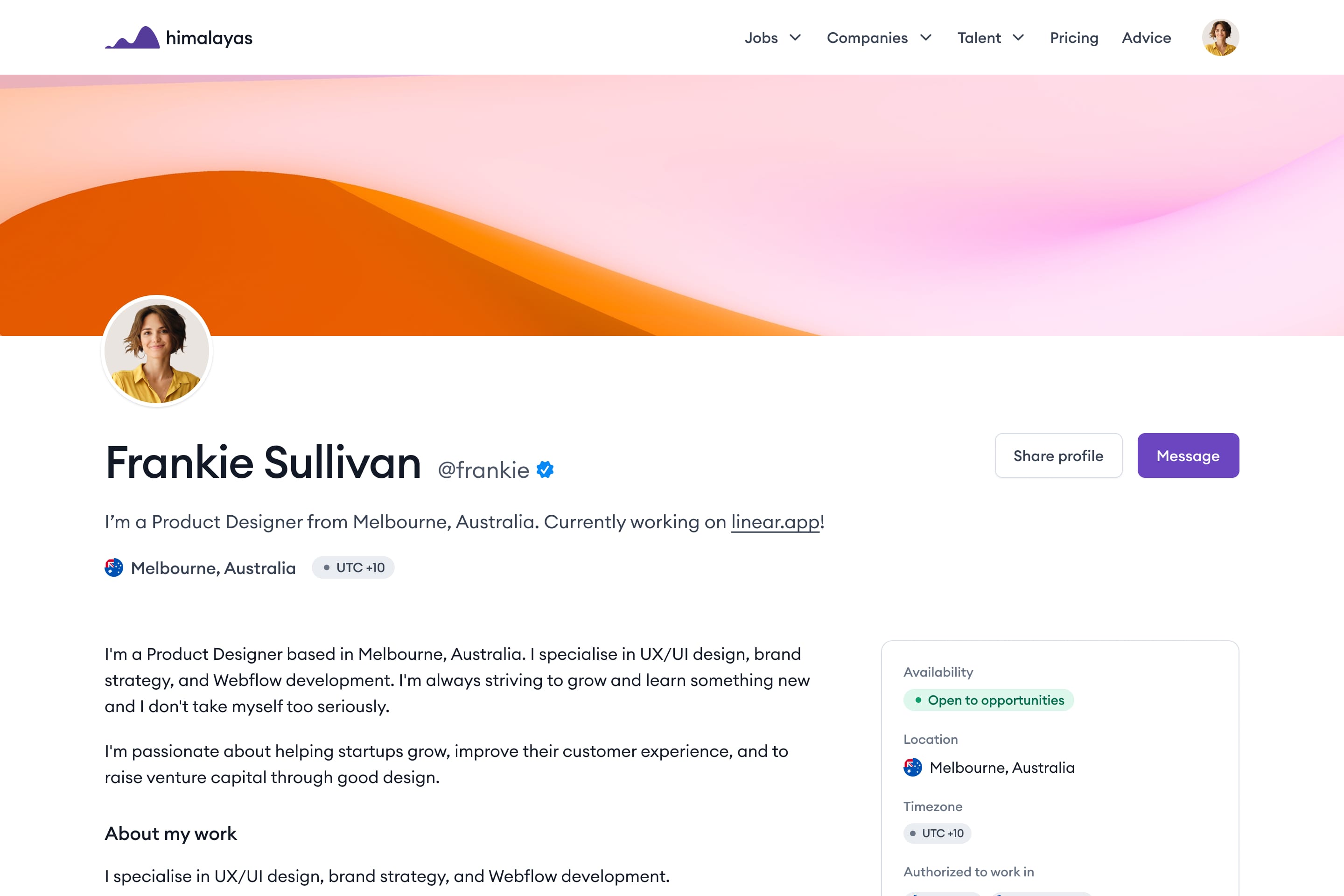