Complete Metal Plater Career Guide
Metal platers are the artisans behind the gleaming surfaces and durable components vital to countless products, applying protective and decorative coatings that enhance material performance. This specialized trade combines precision chemistry with hands-on skill, ensuring everything from aerospace parts to consumer goods meets stringent quality standards. It is a rewarding career path for those who value meticulous work and tangible results, offering stable opportunities in manufacturing and beyond.
Key Facts & Statistics
Median Salary
$44,480 USD
(U.S. Bureau of Labor Statistics, May 2023)
Range: $30k - $60k+ USD
Growth Outlook
Annual Openings
≈3,000
openings annually (U.S. Bureau of Labor Statistics)
Top Industries
Typical Education
High school diploma or equivalent; on-the-job training or vocational school programs often preferred
What is a Metal Plater?
A Metal Plater is a skilled technician responsible for applying thin layers of metal onto the surface of other metal or non-metal objects. This process, known as electroplating or electroless plating, enhances the base material's properties, providing corrosion resistance, improved aesthetics, increased hardness, or better electrical conductivity. Platers meticulously prepare surfaces, manage chemical baths, and control electrical currents to ensure a uniform and durable coating.
This role differs significantly from a Welder, who joins metal pieces together, or a Machinist, who shapes metal through cutting. A Metal Plater's expertise lies in surface engineering, transforming material characteristics without altering its fundamental shape. They play a critical role in industries ranging from automotive and aerospace to electronics and jewelry, ensuring components meet stringent performance and appearance specifications.
What does a Metal Plater do?
Key Responsibilities
- Prepare metal parts for plating by cleaning, degreasing, and etching surfaces using chemical solutions and abrasive techniques.
- Operate and monitor electroplating equipment, including rectifiers, tanks, and filtration systems, ensuring proper voltage and current settings.
- Mix and maintain plating solutions, carefully adding chemicals to achieve the correct concentration and pH levels for optimal deposition.
- Load and unload parts onto racks or into barrels, ensuring proper alignment and contact for uniform plating.
- Inspect plated parts for defects such as blisters, pits, or uneven coating, making adjustments to the plating process as needed.
- Perform quality control checks on finished products, measuring coating thickness and adhesion using specialized instruments.
- Maintain detailed logs of plating processes, including solution compositions, plating times, and quality control results.
Work Environment
Metal platers typically work in manufacturing plants, industrial facilities, or specialized plating shops. The environment can be noisy, with the hum of machinery, and may involve exposure to chemical fumes, requiring excellent ventilation and personal protective equipment. Platers often stand for long periods, handling parts and operating equipment. The work involves a mix of independent tasks and collaboration with team members, particularly for troubleshooting or large batch processing.
Schedules are usually full-time, often during standard business hours, but some facilities operate multiple shifts, including evenings or weekends, to meet production demands. The pace of work is steady, driven by production quotas and quality standards. Safety is paramount, and adherence to strict protocols is a daily requirement due to the use of hazardous chemicals and electrical equipment.
Tools & Technologies
Metal platers frequently use a variety of specialized equipment and chemicals. They operate electroplating tanks, rectifiers, and filtration systems, which are essential for controlling the plating process. Chemical solutions like acids, alkalis, and various metal salts are core to their work, requiring careful handling and knowledge of their properties.
For quality control, platers use micrometers, calipers, and thickness gauges to measure coating uniformity. They also employ pH meters and titration kits to monitor solution chemistry. Safety gear, including respirators, gloves, and eye protection, is crucial due to the hazardous materials involved. Some facilities may use automated plating lines or robotic arms for loading and unloading, requiring familiarity with control panels and basic programming interfaces.
Metal Plater Skills & Qualifications
The role of a Metal Plater requires a precise blend of hands-on technical ability and adherence to safety protocols. Qualifications for this position primarily emphasize practical experience and specialized training over formal academic degrees. Companies often prioritize candidates with direct plating experience, especially those familiar with specific plating processes or materials relevant to their operations.
Requirements for Metal Platers can vary significantly based on the industry sector and the size of the company. Aerospace and medical device manufacturing, for instance, demand extremely high precision and often require certifications in specific plating techniques or quality control standards. In contrast, general manufacturing or automotive plating might focus more on production efficiency and volume. Entry-level positions may accept candidates with vocational training or a strong mechanical aptitude, while senior roles demand extensive experience, troubleshooting skills, and often a proven track record in quality assurance.
Formal education, such as a high school diploma or GED, is a baseline requirement. However, vocational training, apprenticeships, or specialized certifications in electroplating, surface finishing, or chemical handling add significant value. These alternative pathways are highly accepted and often preferred. The skill landscape is continuously evolving with advancements in plating technologies, environmental regulations, and automation. Platers must adapt to new chemical processes, understand advanced machinery, and maintain strict compliance with safety and environmental standards. Continuous learning, especially through industry workshops or supplier training, helps platers stay current and advance their careers.
Education Requirements
Technical Skills
- Electroplating principles and processes (e.g., zinc, nickel, chrome, copper plating)
- Chemical handling and safety procedures (MSDS comprehension)
- Bath analysis and maintenance (pH, concentration, temperature control)
- Rectifier and power supply operation and troubleshooting
- Anode and cathode maintenance and placement
- Surface preparation techniques (cleaning, degreasing, pickling)
- Quality control procedures (adhesion tests, thickness measurement, visual inspection)
- Wastewater treatment and environmental compliance regulations
- Equipment operation and basic maintenance (tanks, pumps, filters)
- Blueprint reading and understanding technical specifications
- Forklift operation (for material handling) and overhead crane operation
- Understanding of material science related to metal substrates and coatings
Soft Skills
- Attention to Detail: Metal Platers must meticulously follow specifications and procedures to ensure uniform coating thickness, adhesion, and appearance, as even minor deviations can compromise product quality and function.
- Problem-Solving: Identifying and troubleshooting issues with plating baths, equipment malfunctions, or coating defects requires analytical thinking to maintain production quality and efficiency.
- Safety Consciousness: Working with hazardous chemicals and machinery demands strict adherence to safety protocols and the consistent use of personal protective equipment to prevent accidents and chemical exposure.
- Manual Dexterity: Precise handling of parts, equipment, and chemicals is crucial for delicate plating processes and to prevent damage to materials or inconsistent finishes.
- Adaptability: Platers often work with various materials, processes, and equipment, requiring them to quickly learn and adjust to new techniques, formulas, and production demands.
- Organizational Skills: Managing multiple plating lines, tracking chemical inventory, and maintaining accurate production records are essential for efficient operations and compliance.
- Team Collaboration: Working effectively with production supervisors, quality control personnel, and maintenance teams ensures smooth workflow, addresses issues promptly, and maintains overall operational efficiency.
- Time Management: Efficiently scheduling and executing plating cycles, preparing solutions, and cleaning equipment to meet production deadlines is vital for throughput and operational success.
How to Become a Metal Plater
Entering the metal plating field offers multiple pathways, ranging from vocational training to on-the-job apprenticeships. A complete beginner might spend 6-12 months gaining foundational knowledge and practical skills, while someone with manufacturing experience could transition within 3-6 months. Different entry routes present unique advantages; vocational programs provide structured learning, while apprenticeships offer direct work experience and often lead to immediate employment.
Entry strategies can vary significantly by company size and industry sector. Larger manufacturing firms might prefer candidates with formal certifications, whereas smaller job shops might prioritize hands-on experience and a strong work ethic. Geographic location also plays a role; areas with a high concentration of industrial manufacturing will have more opportunities. It is a misconception that only a formal degree secures a plating job; often, practical skills and a willingness to learn are more critical.
The hiring landscape for metal platers remains steady, driven by demand across aerospace, automotive, and electronics industries. While formal education is beneficial, many employers value practical experience gained through apprenticeships or entry-level positions. Building a network within local manufacturing communities, attending trade shows, and connecting with experienced platers can open doors to opportunities not advertised publicly. Overcoming initial barriers often involves demonstrating a commitment to safety and precision, key traits for success in this field.
Step 1
Step 2
Step 3
Step 4
Step 5
Step 6
Step 7
Education & Training Needed to Become a Metal Plater
Becoming a Metal Plater primarily involves hands-on training and specialized certifications rather than traditional four-year degrees. Formal university programs are uncommon for this trade, as the skills required are highly practical and process-oriented. Most individuals enter the field through vocational training, apprenticeships, or direct on-the-job training, which typically lasts from a few months to two years depending on complexity.
Vocational schools and community colleges offer certificate or diploma programs in electroplating or surface finishing, often costing between $3,000 and $15,000 with completion times of 6 to 18 months. These programs provide foundational knowledge in chemistry, safety protocols, and plating techniques. Apprenticeships, often sponsored by plating companies or industry associations, provide paid training and extensive practical experience, culminating in a journeyman's status. Apprenticeships can take 2-4 years but offer the benefit of earning while learning, with no upfront tuition costs.
Employer perception strongly favors practical experience and industry-specific certifications, such as those from the National Association for Surface Finishing (NASF). While self-study of plating manuals and online resources can supplement learning, direct supervised practice is crucial for mastering the trade. Continuous learning is essential, as plating technologies and environmental regulations evolve. Advanced certifications or specialized training in areas like precious metal plating or anodizing can significantly enhance career prospects and earning potential. The most effective educational investment for a Metal Plater combines structured technical training with significant hands-on experience, valuing demonstrable skill over academic credentials.
Metal Plater Salary & Outlook
Compensation for a Metal Plater varies significantly based on several factors. Geographic location plays a crucial role, as areas with high industrial demand or a higher cost of living typically offer better wages. For instance, salaries in states like Michigan or Ohio, with strong manufacturing bases, often exceed those in regions with less industrial activity.
Experience, specialized skills, and the type of plating processes mastered also drive salary differences. Platers proficient in niche techniques or working with precious metals can command higher pay. Total compensation extends beyond base salary to include overtime pay, which is common in manufacturing, health benefits, and retirement contributions. Some employers may offer performance bonuses or profit-sharing.
Industry-specific trends, such as the growth in aerospace or automotive manufacturing, directly influence salary growth for Metal Platers. The ability to negotiate based on a strong safety record, efficiency, and specialized certifications can lead to premium compensation. While most Metal Plater roles are on-site, the global demand for skilled trades means that while these figures are USD-centric, international markets also reflect varying compensation based on industrialization and local labor supply.
Salary by Experience Level
Level | US Median | US Average |
---|---|---|
Apprentice Metal Plater | $35k USD | $38k USD |
Metal Plater | $45k USD | $48k USD |
Senior Metal Plater | $55k USD | $58k USD |
Lead Metal Plater | $65k USD | $68k USD |
Metal Plating Supervisor | $75k USD | $78k USD |
Market Commentary
The job market for Metal Platers shows steady demand, driven by the enduring need for corrosion protection, aesthetic finishes, and conductivity in various industries. These industries include automotive, aerospace, electronics, and medical device manufacturing. The Bureau of Labor Statistics projects stable employment for manufacturing production occupations, which includes Metal Platers, though specific growth for platers is tied to the health of these key sectors.
Emerging opportunities for Metal Platers arise from advancements in materials science and environmental regulations. This creates a need for expertise in new plating alloys and environmentally friendly processes. Automation and robotics are increasingly integrated into plating lines, shifting some manual tasks but also creating roles for platers who can operate, maintain, and troubleshoot automated systems. This evolution requires continuous learning and adaptation to new technologies.
Supply and demand dynamics for skilled trades, including Metal Platers, often show a shortage of qualified candidates, particularly for specialized processes. This imbalance can lead to competitive wages for experienced professionals. Geographic hotspots for employment include the industrial Midwest and Southern states with significant manufacturing investments. The role is generally recession-resistant as plating is essential for product durability and functionality across many critical goods.
Metal Plater Career Path
Career progression for a Metal Plater typically follows a clear path from hands-on application to supervisory and leadership roles. This field values practical experience, precision, and adherence to safety and quality standards. Advancement often depends on developing specialized plating techniques and materials knowledge.
Professionals in this field can pursue an individual contributor (IC) track, becoming highly specialized experts in complex plating processes, or transition into a management/leadership track. The management path involves overseeing teams, managing production schedules, and ensuring operational efficiency. Company size and the specific industry (e.g., aerospace, automotive, electronics) can significantly influence available pathways and the pace of advancement.
Advancement speed depends on individual performance, mastery of various plating methods, and continuous learning about new technologies and materials. Lateral moves might involve specializing in a different type of plating (e.g., electroplating, electroless plating, anodizing) or moving into quality assurance roles. Networking within industry associations and pursuing certifications in specific plating techniques or hazardous materials handling can also accelerate career growth and open new opportunities.
Apprentice Metal Plater
0-2 yearsKey Focus Areas
Metal Plater
2-5 yearsKey Focus Areas
Senior Metal Plater
5-8 yearsKey Focus Areas
Lead Metal Plater
8-12 yearsKey Focus Areas
Metal Plating Supervisor
12+ yearsKey Focus Areas
Apprentice Metal Plater
0-2 yearsWorks under direct supervision, assisting experienced platers with basic tasks. Responsibilities include preparing parts for plating, loading and unloading plating racks, and performing initial quality checks. Operates basic plating equipment and maintains work area cleanliness. Decision-making is minimal, primarily following established procedures.
Key Focus Areas
Develop fundamental understanding of plating chemistry, equipment operation, and safety protocols. Focus on mastering basic plating techniques, material handling, and quality inspection. Learn to accurately measure and mix solutions, and maintain a clean work environment. Attention to detail and following instructions are crucial.
Metal Plater
2-5 yearsIndependently performs various metal plating processes according to specifications. Operates and monitors plating lines, conducts quality control tests, and maintains accurate production records. Identifies and resolves minor operational issues. Collaborates with senior platers on complex projects and contributes to process improvements.
Key Focus Areas
Master a wider range of plating processes and materials. Develop troubleshooting skills for common plating issues and learn to adjust parameters for optimal results. Focus on improving efficiency, reducing waste, and understanding the impact of plating on material properties. Pursue certifications in specific plating methods.
Senior Metal Plater
5-8 yearsHandles complex and specialized plating projects, often involving unique materials or stringent specifications. Provides technical guidance to junior platers and assists in training new team members. Troubleshoots advanced plating issues and implements corrective actions. Contributes to process development and quality improvement initiatives.
Key Focus Areas
Deepen expertise in advanced plating techniques, material science, and surface finishing technologies. Develop strong problem-solving skills for complex plating defects and process deviations. Begin mentoring junior platers and contribute to training programs. Focus on process optimization and cost reduction strategies.
Lead Metal Plater
8-12 yearsLeads a team of platers, coordinating daily operations and ensuring production targets are met. Oversees multiple plating lines or complex projects. Responsible for scheduling, quality assurance, and resolving significant operational challenges. Provides technical leadership and drives continuous improvement efforts within the plating department.
Key Focus Areas
Develop strong leadership and communication skills. Focus on project management, resource allocation, and advanced troubleshooting. Gain a comprehensive understanding of production scheduling, inventory management, and lean manufacturing principles. Begin to influence strategic decisions regarding plating processes and technology adoption.
Metal Plating Supervisor
12+ yearsManages the entire metal plating department, overseeing all aspects of operations, including production, quality, safety, and personnel. Develops and implements departmental policies and procedures. Responsible for budgeting, performance reviews, and strategic planning for plating capabilities. Ensures the department meets production goals and quality standards.
Key Focus Areas
Cultivate strategic planning, budget management, and personnel development skills. Focus on optimizing overall departmental performance, implementing new technologies, and ensuring compliance with industry regulations. Develop strong cross-functional collaboration and stakeholder management abilities. Pursue leadership training and industry certifications.
Job Application Toolkit
Ace your application with our purpose-built resources:
Global Metal Plater Opportunities
Metal Platers globally apply protective or decorative coatings to metal objects, a skill crucial across manufacturing, aerospace, and automotive industries. International demand for skilled platers remains consistent, particularly in regions with strong industrial bases. Regulatory differences regarding environmental standards and material specifications impact plating processes worldwide. Professionals consider international roles for higher wages, specialized projects, or better working conditions. Some countries recognize international certifications in surface finishing, aiding global mobility.
Global Salaries
Salaries for Metal Platers vary significantly by region, reflecting industrial output and cost of living. In North America, a Metal Plater earns between $40,000 and $65,000 USD annually in countries like the United States and Canada. This range can increase with specialized skills or experience in aerospace plating. European countries like Germany and the UK offer salaries from €35,000 to €55,000 (approximately $38,000-$60,000 USD), with higher figures in industrial hubs. Scandinavian countries might offer slightly more, but their cost of living is also higher.
Asia-Pacific markets, such as Japan and South Korea, provide salaries ranging from ¥3.5 million to ¥5.5 million (around $23,000-$37,000 USD) and ₩35 million to ₩55 million (about $26,000-$41,000 USD) respectively. While these figures appear lower, purchasing power in these regions often balances the take-home pay. Latin American countries, like Mexico or Brazil, typically offer $15,000-$25,000 USD, often including fewer non-wage benefits compared to developed nations.
International salary structures also differ in benefits. European roles often include more extensive vacation time and robust social security contributions. North American packages might feature private health insurance and retirement plans. Tax implications significantly affect net pay; for example, high-tax European countries might have lower take-home salaries despite similar gross pay. Experience and specific plating expertise, such as electroplating or anodizing, significantly influence compensation across all regions.
Remote Work
International remote work opportunities for Metal Platers are extremely limited, as the role is inherently hands-on and requires specialized on-site equipment. Platers must operate machinery like plating tanks, rectifiers, and ventilation systems within a physical facility. Therefore, digital nomad opportunities or fully remote positions do not apply to this profession.
However, some platers might find rare remote-adjacent roles in technical support, quality control, or process engineering that involve reviewing data or consulting. These roles still often require occasional site visits. Companies generally do not hire Metal Platers for international remote work due to the fundamental need for on-site presence. Any compensation for such roles would be project-based or for highly specialized consulting.
Visa & Immigration
Metal Platers seeking international work typically apply for skilled worker visas. Countries like Canada, Australia, and Germany often have specific pathways for tradespeople, including those in manufacturing. Requirements usually include demonstrating professional experience, often 2-5 years, and holding relevant certifications or diplomas. Educational credential recognition is important; some countries may require an assessment of foreign qualifications to ensure they meet local standards.
Popular destination countries for Metal Platers include Germany, known for its strong industrial sector, and Canada, which often prioritizes skilled trades. Visa application timelines vary, from a few months to over a year. Language proficiency tests, such as IELTS for English-speaking countries or Goethe-Zertifikat for Germany, are frequently required. Some countries may offer expedited processing for occupations in high demand. Pathways to permanent residency often become available after several years of continuous skilled employment.
2025 Market Reality for Metal Platers
Understanding the current market reality for a metal plater is crucial for career planning and success. The industry has seen notable shifts from 2023 to 2025, influenced by post-pandemic supply chain adjustments, increased automation, and evolving environmental standards. Broader economic factors, such as manufacturing output and material costs, directly impact demand for plating services.
Market realities for metal platers also vary considerably by experience level, as highly skilled technicians operating advanced machinery are in different demand than entry-level manual operators. Regional industrial concentrations and the size of plating facilities also shape local opportunities. This analysis provides an honest assessment of these dynamics, helping platers set realistic expectations.
Current Challenges
Metal platers face increased competition for shrinking entry-level roles as automation expands. Economic downturns directly impact manufacturing and, in turn, plating demand. Meeting evolving environmental regulations also requires continuous skill updates and investment from employers, sometimes leading to consolidation or reduced hiring.
Growth Opportunities
Despite challenges, strong demand persists for metal platers skilled in advanced processes like electroforming, anodizing, or specialized coating applications for high-tech industries. Emerging opportunities exist in sectors requiring precision plating for medical devices, defense components, and renewable energy technologies, where quality control and material science knowledge are paramount.
Platers who proactively acquire certifications in automation, robotics, or advanced chemical handling gain a significant competitive edge. Underserved markets in regions with growing aerospace or EV battery manufacturing facilities present better prospects. Furthermore, understanding metallurgy and surface chemistry can lead to roles in process optimization or R&D within plating companies. Strategic career moves involve targeting companies investing in cutting-edge plating technology or those serving niche, high-growth markets, rather than relying solely on traditional manufacturing demand.
Current Market Trends
Hiring for metal platers in 2025 shows a stable but not expansive demand, primarily driven by replacement needs rather than significant growth. The automotive, aerospace, and electronics sectors remain key employers, but their demand fluctuates with economic cycles and supply chain stability. Automation and robotics are increasingly integrated into plating lines, shifting the demand towards platers with strong process control, quality assurance, and equipment maintenance skills.
Employers now prioritize candidates who understand automated systems, can troubleshoot complex machinery, and possess certifications in specialized plating techniques or hazardous material handling. Basic manual plating skills, while still necessary, are no longer sufficient for competitive roles. Wage growth for experienced platers remains modest, largely keeping pace with inflation, but specialized skills in areas like electroless plating or advanced composite coatings command higher rates. Market saturation exists at the entry level, where fewer manual-only roles are available. Geographic variations are pronounced; states with robust manufacturing bases, such as Michigan, Ohio, and North Carolina, offer more opportunities than regions without significant industrial presence.
Emerging Specializations
The metal plating industry, while traditional, is undergoing significant transformation driven by advancements in materials science, environmental regulations, and the demand for enhanced performance characteristics. Understanding these shifts is crucial for Metal Platers seeking to future-proof their careers and capitalize on next-generation opportunities.
Early positioning in emerging specialization areas within metal plating allows professionals to become subject matter experts as these niches expand. This strategic foresight often translates into premium compensation and accelerated career growth, as specialized skills become highly sought after.
While established plating techniques remain vital, focusing on cutting-edge areas ensures relevance in a rapidly evolving market. These emerging specializations are not distant prospects; many are already creating significant job opportunities and are projected to become mainstream within the next three to five years, particularly as industries like aerospace, electronics, and medical devices demand more sophisticated surface finishes.
Pursuing these advanced areas involves a balance of risk and reward. It requires investing in new knowledge and techniques, but the potential for leadership roles and higher earning potential is substantial. Professionals who adapt and specialize will lead the industry's evolution.
Composite Substrate Plating Specialist
Sustainable Plating Process Engineer
Micro/Nano Plating Technician
Additive Manufacturing Post-Processing Plater
EV & Energy Storage Plating Specialist
Pros & Cons of Being a Metal Plater
Understanding both the advantages and challenges of a career is crucial before making any long-term commitments. A career as a Metal Plater, like many professions, offers a unique set of experiences that can vary significantly based on the specific company, industry sector, and individual specialization within the field. Factors such as company culture and equipment technology also play a large role. What one person finds appealing, another might see as a drawback, as personal values and lifestyle preferences heavily influence job satisfaction. Additionally, the nature of pros and cons can evolve at different stages of a career, from entry-level to senior roles. This assessment aims to provide a realistic and balanced perspective to help set appropriate expectations for this particular trade.
Pros
- Consistent demand for skilled Metal Platers exists across various industries, including aerospace, automotive, electronics, and jewelry, ensuring good job security and steady employment opportunities.
- The work provides hands-on engagement with various metals and chemical processes, offering a tangible sense of accomplishment when successfully transforming raw materials into finished, high-quality products.
- Specialized knowledge in plating techniques and chemical solutions can be highly valued, allowing for the development of unique expertise that is not easily replaced by automation.
- Opportunities for skill development and cross-training often exist, allowing platers to learn about different plating materials, surface finishing techniques, and quality control methods, enhancing their versatility.
- Entry into this career often does not require an advanced degree; many learn through apprenticeships, vocational training, or on-the-job experience, making it accessible to a wide range of individuals.
- Metal Platers contribute to the durability and functionality of critical components used in everyday life and advanced technology, providing a sense of contributing to essential manufacturing processes.
- Hourly wages for experienced Metal Platers can be competitive, especially for those with expertise in niche or high-demand plating processes, providing a stable income without significant educational debt.
Cons
- Exposure to hazardous chemicals, including acids, cyanides, and heavy metals, poses significant health risks if safety protocols are not strictly followed, requiring constant vigilance and proper personal protective equipment.
- The work environment often involves high temperatures, humidity, and poor ventilation, which can be physically demanding and uncomfortable, especially during long shifts.
- Repetitive tasks, such as loading and unloading parts, mixing solutions, and monitoring baths, can lead to musculoskeletal strain and boredom over time.
- Strict adherence to precise specifications and quality control is essential; even minor errors in chemical concentrations or plating times can ruin batches of expensive materials, leading to pressure and potential rework.
- Career advancement opportunities may be limited without specialized training in areas like chemical engineering or advanced materials science, often leading to a plateau in the role.
- The job often requires working irregular shifts, including nights and weekends, especially in facilities with continuous production schedules, which can disrupt personal life and routines.
- Disposing of chemical waste requires strict environmental compliance and specialized knowledge; improper handling can lead to severe penalties and environmental damage, adding a layer of responsibility and complexity to the role, which can be stressful.
Frequently Asked Questions
Metal Platers face distinct challenges around material science, safety protocols, and precision application. This section addresses the most common questions about entering this trade, from mastering electroplating techniques to understanding the physical demands and environmental considerations.
What are the common entry requirements to become a Metal Plater?
Entry into metal plating often involves vocational training, an apprenticeship, or on-the-job experience. While a formal degree is not usually required, certifications in hazardous materials handling or specific plating processes can be highly beneficial. Many employers seek candidates with a strong mechanical aptitude and a willingness to learn specialized techniques.
How long does it take to become a skilled Metal Plater if I'm starting fresh?
Becoming proficient as a Metal Plater can take 1-3 years, depending on your learning path. Apprenticeships typically last 2-4 years, combining classroom instruction with extensive on-the-job training. Self-taught individuals or those with less formal training might take longer to gain the necessary experience and confidence in various plating methods.
What are the typical salary expectations for a Metal Plater?
Salaries for Metal Platers vary based on experience, location, and the complexity of the plating work. Entry-level positions might start at $15-$20 per hour, while experienced platers with specialized skills could earn $25-$35 per hour or more. Overtime is often available, which can significantly increase annual income.
What is the work-life balance like for a Metal Plater?
The work-life balance for a Metal Plater is generally stable, often involving regular daytime shifts. However, some facilities operate 24/7, offering evening or night shifts, and overtime might be required to meet production demands. The work can be physically demanding and requires strict adherence to safety protocols, which can impact daily routines.
Is the Metal Plater role a secure job, or is it at risk from automation?
Job security for skilled Metal Platers is generally good, as plating is essential for many manufacturing, aerospace, and defense industries. While automation may impact some tasks, the need for skilled individuals to manage complex plating processes, quality control, and specialized applications remains strong. Demand can fluctuate with economic cycles but often remains consistent.
What are the career growth opportunities for an experienced Metal Plater?
Career growth for a Metal Plater can lead to supervisory roles, quality control management, or specialization in advanced plating techniques like electroforming or electroless plating. Some platers transition into roles in research and development for new plating solutions or become technical trainers. Continuous learning and certifications can open up these advanced opportunities.
What are the biggest challenges or hazards unique to Metal Plating?
Metal Platers frequently encounter challenges related to chemical handling, waste management, and maintaining precise process controls. Ensuring consistent quality and adhesion requires meticulous attention to detail and troubleshooting skills. Exposure to fumes and chemicals necessitates strict adherence to safety procedures and wearing personal protective equipment.
Can Metal Platers work remotely, or is it an on-site job?
Remote work is not feasible for a Metal Plater, as the role requires hands-on work with equipment, chemicals, and materials in a factory or workshop setting. The job is inherently facility-dependent, requiring direct interaction with plating tanks, machinery, and quality testing equipment. Most positions will be on-site, full-time roles.
Related Careers
Explore similar roles that might align with your interests and skills:
Chrome Plater
A growing field with similar skill requirements and career progression opportunities.
Explore career guideCopper Plater
A growing field with similar skill requirements and career progression opportunities.
Explore career guideElectroplater
A growing field with similar skill requirements and career progression opportunities.
Explore career guideNickel Plater
A growing field with similar skill requirements and career progression opportunities.
Explore career guideTin Plater
A growing field with similar skill requirements and career progression opportunities.
Explore career guideAssess your Metal Plater readiness
Understanding where you stand today is the first step toward your career goals. Our Career Coach helps identify skill gaps and create personalized plans.
Skills Gap Analysis
Get a detailed assessment of your current skills versus Metal Plater requirements. Our AI Career Coach identifies specific areas for improvement with personalized recommendations.
See your skills gapCareer Readiness Assessment
Evaluate your overall readiness for Metal Plater roles with our AI Career Coach. Receive personalized recommendations for education, projects, and experience to boost your competitiveness.
Assess your readinessSimple pricing, powerful features
Upgrade to Himalayas Plus and turbocharge your job search.
Himalayas
Himalayas Plus
Himalayas Max
Find your dream job
Sign up now and join over 100,000 remote workers who receive personalized job alerts, curated job matches, and more for free!
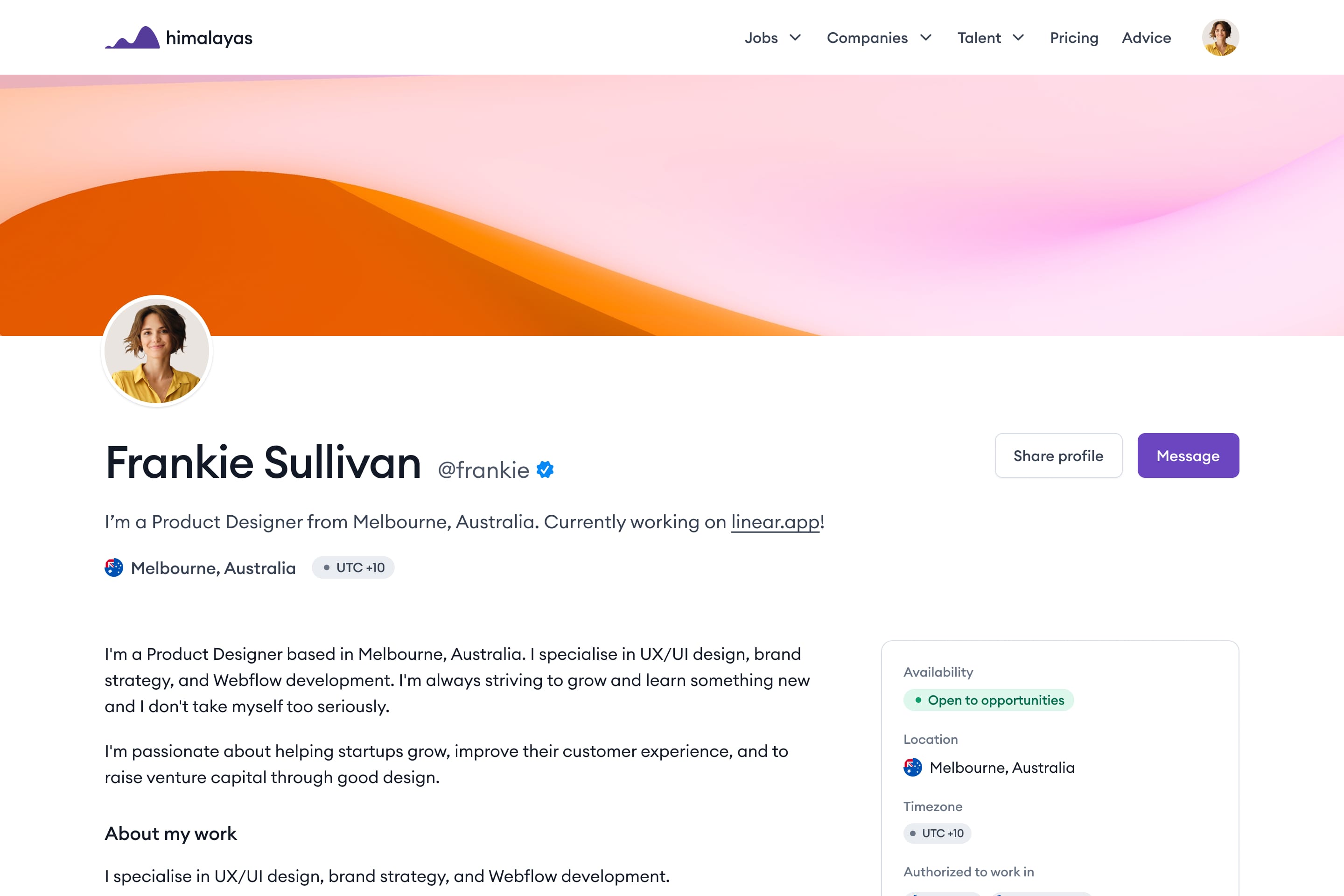