Complete Manufacturing Project Manager Career Guide
Manufacturing Project Managers are the architects of efficiency, orchestrating complex production processes from concept to completion. They ensure products are made on time, within budget, and to exacting quality standards, playing a critical role in a company's profitability and market competitiveness. This demanding yet rewarding career path offers significant opportunities to lead innovation and drive tangible results in diverse industrial sectors.
Key Facts & Statistics
Median Salary
$106,620 USD
(U.S. Bureau of Labor Statistics, May 2023)
Range: $70k - $160k+ USD, varying significantly by experience, industry, and location.
Growth Outlook
6%
as fast as average (U.S. Bureau of Labor Statistics, 2023-2033)
Annual Openings
≈30k
openings annually (U.S. Bureau of Labor Statistics, 2023)
Top Industries
Typical Education
Bachelor's degree in engineering, business, or a related field; PMP or Lean Six Sigma certification often preferred.
What is a Manufacturing Project Manager?
A Manufacturing Project Manager is a specialized professional who orchestrates the planning, execution, and completion of projects within a manufacturing environment. These projects can range from introducing new products and optimizing production lines to implementing new technologies or improving existing processes. They serve as the central hub, ensuring that complex initiatives move forward efficiently, on time, and within budget.
Unlike a general Project Manager who might handle IT or marketing projects, the Manufacturing Project Manager possesses a deep understanding of production processes, supply chains, and quality control. They bridge the gap between design, engineering, and actual production, translating strategic goals into tangible operational changes. Their core purpose is to drive operational excellence and innovation, directly impacting a company's ability to produce goods effectively and competitively.
What does a Manufacturing Project Manager do?
Key Responsibilities
- Develop detailed project plans, including scope, objectives, timelines, and resource allocation for new manufacturing processes or product launches.
- Coordinate cross-functional teams, including engineering, production, supply chain, and quality assurance, to ensure alignment and progress towards project milestones.
- Monitor project progress against the established schedule and budget, identifying potential risks and implementing mitigation strategies proactively.
- Communicate project status, challenges, and successes to stakeholders and senior management, maintaining transparency and managing expectations.
- Manage vendor relationships and procurement activities for necessary materials, equipment, or services, ensuring timely delivery and quality.
- Facilitate problem-solving sessions and drive continuous improvement initiatives within manufacturing operations to optimize efficiency and reduce costs.
- Ensure all project activities comply with regulatory standards, safety protocols, and internal quality management systems.
Work Environment
A Manufacturing Project Manager typically works in a dynamic environment that blends office-based planning with significant time spent on the factory floor. They often divide their time between a corporate office, a dedicated project room, and various production areas or laboratories. Collaboration is constant, involving daily interactions with engineers, production supervisors, quality control specialists, and supply chain personnel. They lead meetings, conduct site visits, and troubleshoot issues directly.
The pace is often fast, driven by production deadlines and new product introduction cycles. While most work occurs during standard business hours, project phases, especially new product launches or critical issue resolution, may require extended hours or occasional weekend work. Travel to supplier sites or other manufacturing facilities might be necessary, though remote work for planning aspects is becoming more common, balanced by the need for on-site presence during critical production phases.
Tools & Technologies
Manufacturing Project Managers rely on a suite of software and systems to orchestrate complex production initiatives. Project management software such as Microsoft Project, Asana, or Jira helps them plan, track, and manage tasks and team collaboration. Enterprise Resource Planning (ERP) systems like SAP or Oracle are crucial for managing inventory, production schedules, and supply chain logistics. They also use statistical process control (SPC) software for quality monitoring and Computer-Aided Design (CAD) viewing tools to review product designs.
Familiarity with lean manufacturing principles, Six Sigma methodologies, and various data analysis tools (e.g., Excel, Minitab) is essential for process optimization and problem-solving. Communication platforms like Microsoft Teams or Slack facilitate daily interactions with diverse teams, while presentation software is vital for stakeholder updates.
Manufacturing Project Manager Skills & Qualifications
A Manufacturing Project Manager guides complex projects from conception to completion within a manufacturing environment. This includes new product introduction, process optimization, facility upgrades, or implementing new machinery. Success hinges on a blend of technical manufacturing knowledge, project management methodologies, and strong leadership capabilities. The role demands an understanding of the entire product lifecycle and supply chain within a production context.
Requirements for this role vary significantly based on the industry, company size, and project complexity. For instance, a project manager in aerospace manufacturing will need deeper regulatory compliance knowledge than one in consumer goods. Entry-level positions may accept candidates with strong engineering backgrounds and foundational project management certifications, while senior roles often demand extensive experience, a PMP certification, and a proven track record of managing multi-million dollar projects. Large corporations often prefer formal degrees and certifications, while smaller firms might prioritize hands-on experience and demonstrated success.
Formal education, practical experience, and certifications all hold significant value. A bachelor's degree in engineering or a related field is almost always a prerequisite. Certifications like the Project Management Professional (PMP) or Certified Associate in Project Management (CAPM) are highly valued and often required for mid-to-senior roles, signaling adherence to best practices. Alternative pathways, such as transitioning from a senior manufacturing engineering role with extensive project exposure, are possible, but usually require supplemental project management training. The skill landscape is evolving, with increasing emphasis on digital transformation, automation, and data-driven decision-making in manufacturing. This role requires a balance of breadth in project management and depth in manufacturing processes.
Education Requirements
Technical Skills
- Project Management Methodologies (Agile, Waterfall, Hybrid): Applying structured approaches to planning, executing, and closing manufacturing projects.
- Manufacturing Processes and Operations: Deep understanding of production workflows, assembly lines, machining, and quality control systems specific to the industry.
- Production Planning and Scheduling Software (e.g., SAP PP, Oracle EBS, MES systems): Proficiency in tools used for managing production schedules, inventory, and resource allocation.
- Process Improvement Methodologies (Lean, Six Sigma): Applying principles to optimize manufacturing efficiency, reduce waste, and improve product quality.
- CAD/CAM Software Comprehension (e.g., AutoCAD, SolidWorks, CATIA): Ability to understand and interpret engineering drawings and designs relevant to manufacturing.
- Enterprise Resource Planning (ERP) Systems (e.g., SAP S/4HANA, Oracle, Microsoft Dynamics): Familiarity with how ERP systems integrate manufacturing, supply chain, and finance.
- Supply Chain Management and Logistics: Knowledge of material sourcing, inventory management, and distribution within a manufacturing context.
- Quality Management Systems (e.g., ISO 9001): Understanding and implementing quality standards and processes in production environments.
- Data Analysis and Reporting Tools (e.g., Excel, Tableau, Power BI): Using data to track project performance, identify trends, and inform decision-making in manufacturing.
- Automation and Industry 4.0 Technologies: Awareness of robotics, IoT, and digital manufacturing trends impacting production lines.
Soft Skills
- Stakeholder Management: Essential for balancing the needs and expectations of diverse groups, including production teams, engineers, suppliers, and senior management.
- Problem-Solving and Decision-Making: Crucial for identifying and resolving complex issues that arise during manufacturing projects, from production bottlenecks to supply chain disruptions.
- Leadership and Motivation: Necessary to guide project teams, foster collaboration, and maintain morale through challenging project phases within a factory setting.
- Communication and Negotiation: Important for clearly conveying project status, risks, and requirements to technical and non-technical audiences, and for negotiating resources or timelines.
- Risk Management Acumen: Vital for proactively identifying potential risks to manufacturing schedules, quality, or budget, and developing mitigation strategies.
- Adaptability and Resilience: Key for navigating the dynamic and often unpredictable nature of manufacturing environments, including unexpected equipment failures or material delays.
- Attention to Detail: Critical for managing complex manufacturing specifications, quality control, and ensuring adherence to safety and regulatory standards.
How to Become a Manufacturing Project Manager
Breaking into Manufacturing Project Management involves several pathways, not just a single route. Aspiring project managers often transition from engineering, operations, or supply chain roles, leveraging their domain expertise. A complete beginner might spend 1.5-2 years building foundational knowledge and gaining practical experience, while someone with manufacturing experience could transition in 6-12 months. Entry strategies vary significantly; larger corporations often prefer candidates with formal project management certifications like PMP, while smaller companies or startups may prioritize hands-on experience and a demonstrated ability to lead initiatives, sometimes even without a specific project management title initially.
Geographic location also plays a role; manufacturing hubs like the Midwest or Southeast in the USA, or industrial regions in Europe and Asia, offer more opportunities. In these areas, networking with industry professionals and attending local manufacturing events becomes crucial for uncovering hidden job prospects and gaining insights. Common misconceptions include believing that only engineers can become manufacturing project managers, or that one must have a PMP certification before even starting; practical experience managing any type of project, even informal ones, proves highly valuable. The current hiring landscape values adaptability, problem-solving skills, and a strong understanding of manufacturing processes as much as, if not more than, formal credentials alone.
Overcoming barriers to entry, such as a lack of direct project management experience, involves strategically framing past roles to highlight project-like responsibilities and outcomes. Emphasize instances where you coordinated tasks, managed timelines, or oversaw cross-functional efforts. Building a portfolio of these 'mini-projects' and seeking mentorship from established manufacturing project managers can significantly accelerate your entry into the field, providing guidance and opening doors to relevant opportunities.
Develop a strong foundation in manufacturing processes and project management principles. Consider online courses in lean manufacturing, Six Sigma, or basic project management. Aim to complete a foundational course within 3-6 months to grasp the core concepts of production, quality control, and project lifecycles relevant to manufacturing.
Gain practical experience by leading or contributing to projects in your current or a related role. Volunteer for initiatives at work, even if they are not formal 'projects,' such as process improvements, new equipment installations, or product launches. Document your contributions, focusing on how you managed scope, timelines, and resources, even for small-scale efforts.
Obtain a recognized project management certification relevant to manufacturing. While PMP is highly regarded, consider CAPM for less experienced individuals, or certifications like Certified Associate in Project Management (CAPM) as a stepping stone. Completing a certification typically takes 3-6 months of dedicated study after meeting the experience requirements.
Build a project portfolio showcasing your ability to manage manufacturing-related initiatives. Include case studies of projects you have worked on, detailing the problem, your role, the actions taken, and the measurable outcomes. Focus on demonstrating your understanding of manufacturing challenges and how you applied project management methodologies to achieve results.
Actively network with manufacturing professionals and project managers in your target industry and region. Attend industry conferences, local manufacturing meetups, and connect with people on LinkedIn. Informational interviews can provide valuable insights into the day-to-day realities of the role and uncover potential job leads that are not publicly advertised.
Tailor your resume and cover letter to highlight manufacturing project management skills and experiences. Use keywords from job descriptions, emphasizing your ability to manage complex production schedules, implement new processes, and drive cross-functional teams to meet manufacturing objectives. Quantify your achievements whenever possible to demonstrate impact.
Prepare thoroughly for interviews by practicing responses to behavioral and technical questions specific to manufacturing project management. Be ready to discuss your experience with risk management, stakeholder communication, and problem-solving within a manufacturing context. Show enthusiasm for the industry and a clear understanding of the role's challenges and rewards.
Step 1
Develop a strong foundation in manufacturing processes and project management principles. Consider online courses in lean manufacturing, Six Sigma, or basic project management. Aim to complete a foundational course within 3-6 months to grasp the core concepts of production, quality control, and project lifecycles relevant to manufacturing.
Step 2
Gain practical experience by leading or contributing to projects in your current or a related role. Volunteer for initiatives at work, even if they are not formal 'projects,' such as process improvements, new equipment installations, or product launches. Document your contributions, focusing on how you managed scope, timelines, and resources, even for small-scale efforts.
Step 3
Obtain a recognized project management certification relevant to manufacturing. While PMP is highly regarded, consider CAPM for less experienced individuals, or certifications like Certified Associate in Project Management (CAPM) as a stepping stone. Completing a certification typically takes 3-6 months of dedicated study after meeting the experience requirements.
Step 4
Build a project portfolio showcasing your ability to manage manufacturing-related initiatives. Include case studies of projects you have worked on, detailing the problem, your role, the actions taken, and the measurable outcomes. Focus on demonstrating your understanding of manufacturing challenges and how you applied project management methodologies to achieve results.
Step 5
Actively network with manufacturing professionals and project managers in your target industry and region. Attend industry conferences, local manufacturing meetups, and connect with people on LinkedIn. Informational interviews can provide valuable insights into the day-to-day realities of the role and uncover potential job leads that are not publicly advertised.
Step 6
Tailor your resume and cover letter to highlight manufacturing project management skills and experiences. Use keywords from job descriptions, emphasizing your ability to manage complex production schedules, implement new processes, and drive cross-functional teams to meet manufacturing objectives. Quantify your achievements whenever possible to demonstrate impact.
Step 7
Prepare thoroughly for interviews by practicing responses to behavioral and technical questions specific to manufacturing project management. Be ready to discuss your experience with risk management, stakeholder communication, and problem-solving within a manufacturing context. Show enthusiasm for the industry and a clear understanding of the role's challenges and rewards.
Education & Training Needed to Become a Manufacturing Project Manager
Becoming a Manufacturing Project Manager involves navigating a diverse educational landscape. Formal four-year degrees in industrial engineering, supply chain management, or business administration with an operations focus are common. These bachelor's degrees typically cost between $40,000 and $100,000+ and take four years to complete. They provide a strong theoretical foundation in manufacturing processes, quality control, and project methodologies.
Alternative pathways, such as specialized bootcamps or professional certifications, offer faster entry. Project Management Professional (PMP) certification, offered by the Project Management Institute (PMI), is highly valued. Bootcamps focused on project management or Lean Six Sigma principles can range from $2,000 to $10,000 and typically last 6 to 12 weeks. While these options provide practical skills quickly, they often require some prior professional experience or a foundational understanding of manufacturing. Employers generally recognize both formal degrees and key certifications, with the latter often preferred for mid-career professionals seeking to validate expertise.
Continuous learning remains crucial for Manufacturing Project Managers. Industry trends like automation, IoT, and sustainable manufacturing constantly evolve, requiring ongoing professional development. Short online courses and workshops from platforms like Coursera or edX, costing $100-$1,000, help bridge skill gaps. Practical experience gained through internships, co-op programs, or entry-level roles is as important as theoretical knowledge. The ideal educational investment combines foundational academic learning with targeted certifications and hands-on experience, adapting to specific industry niches and career advancement goals. Accreditation from bodies like ABET for engineering programs or PMI for project management certifications signifies program quality.
Manufacturing Project Manager Salary & Outlook
Compensation for a Manufacturing Project Manager reflects a blend of specialized skills and strategic impact. Geographic location plays a significant role in earning potential, with higher salaries typically found in regions with dense manufacturing hubs or a higher cost of living, such as the Northeast or California. Conversely, areas with lower living costs may offer comparatively lower base salaries, though purchasing power can be similar.
Years of experience dramatically influence salary progression. Early-career professionals focus on foundational project execution, while seasoned managers command higher pay for their ability to oversee complex initiatives, mitigate risks, and drive efficiency gains. Specialization in areas like lean manufacturing, Six Sigma, or specific industry sectors (e.g., automotive, aerospace, pharmaceuticals) also commands premium compensation due to niche expertise.
Total compensation packages extend beyond base salary. Many Manufacturing Project Managers receive performance bonuses tied to project completion, budget adherence, or operational improvements. Equity compensation is less common in traditional manufacturing but can appear in high-growth or tech-integrated manufacturing firms. Comprehensive benefits, including health insurance, retirement contributions (401k matching), and professional development allowances for certifications like PMP, further enhance the overall value of the role. Salary negotiation leverage comes from a proven track record of successful project delivery, strong leadership skills, and an understanding of a company's specific manufacturing challenges. Remote work's impact on this role is limited given the hands-on nature of manufacturing, but hybrid models can offer some flexibility, potentially influencing local market rates. International markets show significant variations, with figures provided here primarily reflecting the USD context.
Salary by Experience Level
Level | US Median | US Average |
---|---|---|
Junior Manufacturing Project Manager | $70k USD | $75k USD |
Manufacturing Project Manager | $90k USD | $95k USD |
Senior Manufacturing Project Manager | $115k USD | $120k USD |
Lead Manufacturing Project Manager | $135k USD | $140k USD |
Manufacturing Program Manager | $155k USD | $160k USD |
Director of Manufacturing Projects | $180k USD | $190k USD |
Market Commentary
The job market for Manufacturing Project Managers shows consistent demand, driven by ongoing needs for operational efficiency, new product introductions, and supply chain optimization. The sector faces pressures from global competition and technological advancements, requiring skilled project managers to navigate complex production environments. Growth projections for this role remain stable, with the Bureau of Labor Statistics anticipating a modest increase in demand for management occupations across various industries, including manufacturing, through 2032. This growth is linked to the continuous drive for process improvement and the adoption of advanced manufacturing technologies.
Emerging opportunities for Manufacturing Project Managers are found in areas like Industry 4.0 integration, where projects involve implementing automation, IoT, and AI into production lines. The shift towards sustainable manufacturing and circular economy initiatives also creates new project needs focused on resource efficiency and waste reduction. There is a strong demand for professionals who can bridge the gap between traditional manufacturing processes and digital transformation efforts.
Supply and demand dynamics are relatively balanced, though a shortage of candidates with both strong project management acumen and deep manufacturing domain knowledge can exist in specialized sectors. Future-proofing this career involves continuous learning in digital manufacturing, data analytics, and agile methodologies. While automation and AI will transform manufacturing, they also create new project management challenges related to deployment and integration, making the role resilient. Geographic hotspots for these roles align with major industrial corridors in the Midwest, Southeast, and Pacific Northwest, with increasing opportunities in regions investing in advanced manufacturing capabilities.
Manufacturing Project Manager Career Path
Career progression for a Manufacturing Project Manager typically involves a blend of technical mastery, leadership development, and strategic business understanding. Professionals advance by taking on larger, more complex projects, managing diverse teams, and demonstrating consistent success in delivering manufacturing initiatives on time and within budget.
Advancement often involves a critical decision point: specializing further as an individual contributor (IC) on highly complex projects or transitioning into a management track. The IC path might lead to roles like Lead Manufacturing Project Manager, focusing on technical project excellence. The management track evolves into overseeing multiple projects as a Manufacturing Program Manager, then leading entire departments as a Director of Manufacturing Projects. Company size, industry (e.g., automotive, aerospace, consumer goods), and economic conditions significantly influence advancement speed and available opportunities.
Lateral moves are common, allowing professionals to gain experience in different manufacturing processes, product lines, or global regions. This broadens their expertise and prepares them for higher-level strategic roles. Continuous learning, embracing new manufacturing technologies like automation or AI, and cultivating a strong professional network are vital for sustained growth. Certifications in project management (PMP) or lean manufacturing further validate expertise and accelerate progression.
Junior Manufacturing Project Manager
0-2 yearsAssist senior managers in planning and executing smaller, defined manufacturing projects or specific phases of larger projects. Manage project documentation, track progress against timelines, and coordinate resources. Support basic stakeholder communication and issue resolution for designated tasks.
Key Focus Areas
Develop foundational project management skills, including scheduling, budgeting, and risk identification. Learn manufacturing processes, production lifecycles, and quality control standards. Build effective communication with production teams and stakeholders. Understand safety protocols and regulatory compliance.
Manufacturing Project Manager
3-5 yearsLead medium-sized manufacturing projects from inception to completion, managing cross-functional teams and external vendors. Accountable for project budgets, schedules, and quality outcomes. Identify and mitigate project risks. Communicate project status to stakeholders and senior leadership.
Key Focus Areas
Master project planning, execution, monitoring, and closing. Enhance problem-solving skills for production challenges. Develop strong leadership and team motivation abilities. Improve negotiation and conflict resolution with suppliers and internal departments. Pursue PMP certification.
Senior Manufacturing Project Manager
6-9 yearsManage multiple complex, high-impact manufacturing projects simultaneously or a single, large-scale strategic project. Provide mentorship to junior project managers. Drive process improvements within the manufacturing project lifecycle. Influence resource allocation decisions and manage significant budgets.
Key Focus Areas
Refine advanced project management methodologies, including agile or lean manufacturing principles. Cultivate strategic thinking to align projects with business objectives. Develop mentoring skills for junior project managers. Build strong relationships across departments and with key external partners.
Lead Manufacturing Project Manager
10-14 yearsOversee a portfolio of critical manufacturing projects, ensuring alignment with organizational strategy and business goals. Act as a subject matter expert and provide technical leadership for project teams. Implement best practices and standardize project management processes across the manufacturing division. Resolve high-level project impediments.
Key Focus Areas
Focus on driving strategic project initiatives and portfolio management. Develop expertise in new manufacturing technologies and industry trends. Enhance executive communication and presentation skills. Prepare for leadership roles by understanding organizational dynamics and change management.
Manufacturing Program Manager
15-19 yearsDirect a collection of related manufacturing projects (a 'program') to achieve broad strategic objectives. Manage interdependencies between projects and ensure cohesive delivery. Oversee program budgets, resource allocation, and overall program performance. Drive continuous improvement in manufacturing operations and processes.
Key Focus Areas
Master program governance, strategic planning, and cross-program dependencies. Cultivate strong leadership in a multi-project environment. Develop financial acumen for large-scale investments. Build a deep understanding of market dynamics and competitive landscapes.
Director of Manufacturing Projects
20+ yearsProvide executive leadership for all manufacturing project and program initiatives within an organization. Define the strategic direction for manufacturing project management, including methodologies, tools, and talent development. Oversee the entire project portfolio, ensuring alignment with company-wide goals and profitability. Accountable for the overall success of manufacturing project delivery.
Key Focus Areas
Develop executive leadership, strategic vision, and organizational development skills. Drive innovation in manufacturing processes and technology adoption. Cultivate strong stakeholder relationships at the executive level. Focus on talent acquisition and development for the project management function.
Junior Manufacturing Project Manager
0-2 yearsAssist senior managers in planning and executing smaller, defined manufacturing projects or specific phases of larger projects. Manage project documentation, track progress against timelines, and coordinate resources. Support basic stakeholder communication and issue resolution for designated tasks.
Key Focus Areas
Develop foundational project management skills, including scheduling, budgeting, and risk identification. Learn manufacturing processes, production lifecycles, and quality control standards. Build effective communication with production teams and stakeholders. Understand safety protocols and regulatory compliance.
Manufacturing Project Manager
3-5 yearsLead medium-sized manufacturing projects from inception to completion, managing cross-functional teams and external vendors. Accountable for project budgets, schedules, and quality outcomes. Identify and mitigate project risks. Communicate project status to stakeholders and senior leadership.
Key Focus Areas
Master project planning, execution, monitoring, and closing. Enhance problem-solving skills for production challenges. Develop strong leadership and team motivation abilities. Improve negotiation and conflict resolution with suppliers and internal departments. Pursue PMP certification.
Senior Manufacturing Project Manager
6-9 yearsManage multiple complex, high-impact manufacturing projects simultaneously or a single, large-scale strategic project. Provide mentorship to junior project managers. Drive process improvements within the manufacturing project lifecycle. Influence resource allocation decisions and manage significant budgets.
Key Focus Areas
Refine advanced project management methodologies, including agile or lean manufacturing principles. Cultivate strategic thinking to align projects with business objectives. Develop mentoring skills for junior project managers. Build strong relationships across departments and with key external partners.
Lead Manufacturing Project Manager
10-14 yearsOversee a portfolio of critical manufacturing projects, ensuring alignment with organizational strategy and business goals. Act as a subject matter expert and provide technical leadership for project teams. Implement best practices and standardize project management processes across the manufacturing division. Resolve high-level project impediments.
Key Focus Areas
Focus on driving strategic project initiatives and portfolio management. Develop expertise in new manufacturing technologies and industry trends. Enhance executive communication and presentation skills. Prepare for leadership roles by understanding organizational dynamics and change management.
Manufacturing Program Manager
15-19 yearsDirect a collection of related manufacturing projects (a 'program') to achieve broad strategic objectives. Manage interdependencies between projects and ensure cohesive delivery. Oversee program budgets, resource allocation, and overall program performance. Drive continuous improvement in manufacturing operations and processes.
Key Focus Areas
Master program governance, strategic planning, and cross-program dependencies. Cultivate strong leadership in a multi-project environment. Develop financial acumen for large-scale investments. Build a deep understanding of market dynamics and competitive landscapes.
Director of Manufacturing Projects
20+ yearsProvide executive leadership for all manufacturing project and program initiatives within an organization. Define the strategic direction for manufacturing project management, including methodologies, tools, and talent development. Oversee the entire project portfolio, ensuring alignment with company-wide goals and profitability. Accountable for the overall success of manufacturing project delivery.
Key Focus Areas
Develop executive leadership, strategic vision, and organizational development skills. Drive innovation in manufacturing processes and technology adoption. Cultivate strong stakeholder relationships at the executive level. Focus on talent acquisition and development for the project management function.
Job Application Toolkit
Ace your application with our purpose-built resources:
Manufacturing Project Manager Resume Examples
Proven layouts and keywords hiring managers scan for.
View examplesManufacturing Project Manager Cover Letter Examples
Personalizable templates that showcase your impact.
View examplesTop Manufacturing Project Manager Interview Questions
Practice with the questions asked most often.
View examplesManufacturing Project Manager Job Description Template
Ready-to-use JD for recruiters and hiring teams.
View examplesGlobal Manufacturing Project Manager Opportunities
Manufacturing Project Managers globally oversee production initiatives, process improvements, and new product introductions. This role translates consistently across countries, focusing on efficiency, quality, and on-time delivery within factory settings.
Global demand remains strong in 2025, driven by supply chain diversification and automation trends. Professionals often consider international roles for exposure to diverse manufacturing practices and larger-scale operations. Six Sigma and PMP certifications significantly enhance global mobility.
Global Salaries
Salaries for Manufacturing Project Managers vary significantly by region. In North America, particularly the US, annual salaries range from $90,000 to $140,000 USD, with higher figures in industrial hubs like Michigan or Texas. Canadian counterparts typically earn C$80,000 to C$120,000.
European salaries show wide differences. In Germany, a Manufacturing Project Manager can expect €70,000 to €110,000 (approximately $75,000-$118,000 USD), reflecting a high cost of living but strong purchasing power. In the UK, salaries are often £55,000 to £85,000 ($70,000-$108,000 USD). Southern Europe, such as Spain, offers €40,000 to €65,000 ($43,000-$70,000 USD), which provides reasonable purchasing power given lower living costs.
Asia-Pacific markets present diverse compensation. In Singapore, salaries range from S$70,000 to S$120,000 ($52,000-$89,000 USD), while in China, a similar role might pay ¥250,000 to ¥500,000 ($35,000-$70,000 USD), with significant regional variations. These figures must be assessed against local cost of living and tax structures, which can significantly impact take-home pay and overall financial well-being.
Latin American salaries are generally lower, ranging from $40,000 to $70,000 USD in countries like Mexico or Brazil, but with a proportionally lower cost of living. International experience and advanced certifications can significantly boost earning potential across all regions.
Remote Work
International remote work for Manufacturing Project Managers is limited due to the inherent need for on-site presence in factories. However, some roles may involve remote coordination for global projects or supply chain management.
Legal and tax implications of cross-border remote work are complex, requiring careful consideration of permanent establishment risks for employers. Time zone differences pose challenges for international team collaboration, especially with manufacturing sites operating on strict schedules.
Digital nomad opportunities are rare for this specific role, as physical proximity to production facilities is usually essential. Companies with distributed manufacturing operations might offer hybrid roles, where a manager travels frequently but performs administrative tasks remotely. Salary expectations for such roles often align with the employer's base country.
Visa & Immigration
Manufacturing Project Managers commonly use skilled worker visas in popular destinations. Countries like Germany, Canada, and Australia have specific pathways for professionals with engineering and project management expertise.
Requirements typically include recognized educational credentials, often a Bachelor's degree in Engineering or Business, and several years of relevant experience. Some countries, like Canada, may require language proficiency tests like IELTS or CELPIP.
The application process usually involves employer sponsorship, submission of extensive documentation, and can take several months to over a year. Credential recognition by local professional bodies might be necessary in some cases.
Pathways to permanent residency exist in many countries for skilled workers who meet specific criteria, often after a period of employment. Family visas for dependents are usually available alongside the primary applicant's visa.
2025 Market Reality for Manufacturing Project Managers
Understanding the current market realities for Manufacturing Project Managers is crucial for strategic career planning. The landscape has evolved significantly post-pandemic, with supply chain disruptions and rapid technological advancements, especially in AI, reshaping industry needs.
Broader economic factors, such as inflation and fluctuating consumer demand, directly influence investment in new manufacturing projects, impacting job availability. Market realities also vary by experience level; entry-level roles face more competition, while experienced managers with specialized skills are in higher demand. Geographic location and the size of the manufacturing operation further define opportunities, making a precise market assessment essential.
Current Challenges
Manufacturing Project Managers face heightened competition, especially for roles requiring specific industry certifications or advanced automation experience. Economic uncertainty often leads companies to delay or scale back large capital projects, directly impacting demand for these roles. Maintaining project timelines and budgets in a volatile supply chain environment also adds significant pressure.
Growth Opportunities
Despite challenges, strong opportunities exist for Manufacturing Project Managers skilled in digital transformation and advanced automation. Roles focused on implementing AI-powered predictive maintenance, smart factory systems, and robotic process automation are experiencing high demand. Managers who can bridge the gap between IT and operational technology are particularly valuable.
Professionals can gain a competitive edge by pursuing certifications in Lean Six Sigma, Agile methodologies adapted for manufacturing, or specific industrial automation platforms. Underserved markets in emerging industrial hubs or companies undergoing significant modernization present fertile ground for new roles. Expertise in sustainable manufacturing practices and circular economy initiatives also offers a distinct advantage as industries shift towards greener operations. Strategic career moves now involve aligning with companies committed to long-term technological investment and operational resilience.
Current Market Trends
Demand for Manufacturing Project Managers remains steady, driven by ongoing digitalization and automation within the industrial sector. Companies are heavily investing in Industry 4.0 initiatives, requiring skilled managers to oversee complex integrations of AI, IoT, and robotics on factory floors. This shift means a greater emphasis on technical aptitude alongside traditional project management skills.
Economic conditions, while improving, still prompt cautious hiring. Many firms prioritize project managers who can demonstrate clear ROI for new investments, particularly in efficiency and cost reduction. Roles focused on sustainable manufacturing practices and supply chain resilience are seeing increased interest. Salary trends show a premium for those with proven experience in AI-driven process optimization and lean manufacturing methodologies.
Geographically, opportunities are strongest in regions with robust manufacturing bases, such as the Midwest and Southeast in the US, and parts of Europe and Asia. Remote work for these roles is less common due to the hands-on nature of managing physical production sites, though hybrid models for planning and coordination are emerging. Hiring often aligns with capital expenditure cycles, typically peaking after major investment announcements or during periods of facility expansion.
Emerging Specializations
The landscape for manufacturing project managers is rapidly evolving, driven by transformative technologies and shifting global demands. Understanding these emerging trends is crucial for professionals aiming to secure leadership roles and significant career advancement in 2025 and beyond. New specialization opportunities are continually created as advancements like artificial intelligence, sustainable practices, and advanced robotics reshape production processes and supply chains.
Early positioning in these emerging areas provides a distinct competitive advantage. Professionals who develop expertise in cutting-edge specializations often command premium compensation and experience accelerated career growth, as their skills are in high demand but short supply. While established specializations remain vital, focusing on emerging areas allows manufacturing project managers to future-proof their careers and lead innovation.
Many emerging areas, initially niche, are set to become mainstream within the next three to five years, generating a significant number of job opportunities. Investing in these specializations now offers a strong risk-reward profile; the initial effort to acquire new knowledge and skills pays dividends as these fields mature and expand. Strategic career planning involves identifying these nascent yet impactful areas and proactively building the necessary capabilities.
AI & Automation Integration Project Manager
Sustainable Manufacturing Project Manager
Additive Manufacturing Deployment Project Manager
Industrial Cybersecurity Project Manager
Digital Twin Implementation Project Manager
Pros & Cons of Being a Manufacturing Project Manager
Understanding both the advantages and challenges of a career is crucial for making informed decisions. While a role may appear appealing on the surface, the day-to-day realities can vary significantly based on company culture, industry sector, specific specialization, and individual personality. What one person considers a benefit, another might see as a drawback. Furthermore, the nature of pros and cons can evolve at different stages of a career, from entry-level responsibilities to senior leadership. This assessment provides an honest, balanced perspective on the Manufacturing Project Manager role, helping you set realistic expectations for a fulfilling and sustainable career path.
Pros
- Manufacturing Project Managers often see tangible results of their work, such as new products rolling off the assembly line or improved production efficiency, providing a strong sense of accomplishment and direct impact.
- The role offers significant opportunities for leadership and decision-making, as project managers guide cross-functional teams, allocate resources, and resolve complex issues to drive projects to completion.
- This position demands a diverse skill set, including technical knowledge, business acumen, communication, and problem-solving, leading to continuous professional development and a highly transferable skill base across industries.
- Given the critical nature of optimizing production and bringing new products to market, skilled Manufacturing Project Managers are consistently in high demand across various industries, offering strong job security and diverse career opportunities.
- The role involves interacting with a wide array of professionals, from engineers and supply chain specialists to marketing and sales teams, fostering a broad professional network and diverse learning experiences.
- Successful project completion can lead to significant recognition and career advancement, with clear pathways to senior management roles or specialized consulting within the manufacturing sector.
- Many manufacturing companies are investing in advanced technologies like automation, AI, and IoT, allowing Manufacturing Project Managers to work with cutting-edge innovations and contribute to the future of industry.
Cons
- Manufacturing Project Managers often face intense pressure to meet tight deadlines and budget constraints, which can lead to high stress levels and long working hours, especially during critical project phases or unexpected issues.
- Success in this role heavily depends on the performance of diverse teams and external vendors, meaning project managers frequently deal with scope creep, resource conflicts, and communication breakdowns that are often beyond their direct control.
- The role requires constant problem-solving for unexpected production delays, equipment malfunctions, or material shortages, demanding quick, effective decisions under pressure with significant financial implications.
- Travel to different manufacturing sites, supplier locations, or client facilities is frequently required, which can disrupt personal life and lead to significant time away from home.
- Staying current with new manufacturing technologies, lean methodologies, and industry regulations demands continuous learning and professional development, requiring a significant personal time investment outside of core work hours.
- Interacting with a wide range of stakeholders, from engineers and shop floor personnel to executives and clients, can be challenging due to differing priorities, communication styles, and technical understanding.
- Manufacturing environments can sometimes pose safety risks or require adherence to strict safety protocols, adding an additional layer of responsibility and concern for the project manager overseeing operations. There are also specific ISO, OSHA, or EPA compliance requirements that must be met depending on the type of manufacturing being overseen, which creates additional complexity and responsibility for the project manager to manage.
Frequently Asked Questions
Manufacturing Project Managers face unique challenges balancing technical production knowledge with complex project timelines and stakeholder expectations. This section addresses the most pressing questions about entering this specific role, from required skills and certifications to navigating supply chain disruptions and leading diverse teams in a dynamic factory environment.
What educational background and certifications do I need to become a Manufacturing Project Manager?
A bachelor's degree in engineering, supply chain management, or business administration is often the minimum requirement. Many successful Manufacturing Project Managers also hold certifications like PMP (Project Management Professional) or lean manufacturing credentials. Practical experience in a manufacturing environment, even in a non-management role, significantly strengthens your application. Employers prioritize candidates who understand production processes and operational challenges.
How long does it realistically take to become a Manufacturing Project Manager if I'm starting from a different industry?
Transitioning into this role from a related field typically takes 2-5 years of focused effort. This includes gaining foundational manufacturing experience, pursuing project management training, and potentially completing a certification. For someone starting from scratch, expect 5-8 years to build the necessary technical understanding and project leadership skills. Networking within the industry and seeking mentorship can accelerate this timeline.
What are the typical salary expectations for a Manufacturing Project Manager at different career stages?
Entry-level Manufacturing Project Managers can expect a starting salary ranging from $60,000 to $80,000 annually, depending on location and company size. Mid-career professionals with 5-10 years of experience typically earn between $90,000 and $130,000. Senior or specialized roles, especially in complex industries, can command salaries exceeding $150,000. Performance bonuses tied to project success are also common.
What is the typical work-life balance like for a Manufacturing Project Manager, considering project deadlines and travel?
Work-life balance can vary significantly based on project phases and company culture. During critical project launches or problem-solving periods, longer hours are common. However, outside these peak times, a standard 40-50 hour work week is typical. Travel might be required for supplier visits, new facility setups, or client meetings, impacting personal time. Effective project planning and delegation help mitigate excessive overtime.
Is the job market for Manufacturing Project Managers growing, and what is the job security like in this field?
The job market for Manufacturing Project Managers remains strong, driven by continuous innovation, supply chain complexities, and the need for efficiency improvements in production. Companies consistently seek skilled professionals to manage new product introductions, process improvements, and factory expansions. While economic downturns can affect manufacturing, the need for efficient project execution typically persists, making this a relatively stable career path.
What are the common career advancement opportunities for a Manufacturing Project Manager?
Career growth paths include moving into senior project management roles, program management (overseeing multiple projects), or portfolio management. Some Manufacturing Project Managers transition into operations management, plant management, or even executive leadership positions. Specializing in specific manufacturing technologies, such as automation or additive manufacturing, can also open up advanced opportunities and higher compensation.
What are the biggest challenges or frustrations that Manufacturing Project Managers commonly face?
Key challenges include managing scope creep, dealing with unexpected supply chain disruptions, and coordinating diverse teams across different departments. You must also navigate technical issues on the factory floor, ensure quality control, and maintain strict adherence to budgets and timelines. Effective communication and problem-solving skills are crucial for overcoming these daily hurdles.
Can a Manufacturing Project Manager work remotely, or is on-site presence usually required?
While some administrative tasks might be performed remotely, the core responsibilities of a Manufacturing Project Manager often require a significant on-site presence. You need to be physically present at the manufacturing facility to oversee production, troubleshoot issues, and interact directly with production teams, engineers, and quality control staff. Fully remote roles are rare, but hybrid models offering some flexibility are becoming more common.
Related Careers
Explore similar roles that might align with your interests and skills:
Engineering Project Manager
A growing field with similar skill requirements and career progression opportunities.
Explore career guideManufacturing Manager
A growing field with similar skill requirements and career progression opportunities.
Explore career guideManufacturing Operations Manager
A growing field with similar skill requirements and career progression opportunities.
Explore career guideManufacturing Planner
A growing field with similar skill requirements and career progression opportunities.
Explore career guideManufacturing Director
A growing field with similar skill requirements and career progression opportunities.
Explore career guideAssess your Manufacturing Project Manager readiness
Understanding where you stand today is the first step toward your career goals. Our Career Coach helps identify skill gaps and create personalized plans.
Skills Gap Analysis
Get a detailed assessment of your current skills versus Manufacturing Project Manager requirements. Our AI Career Coach identifies specific areas for improvement with personalized recommendations.
See your skills gapCareer Readiness Assessment
Evaluate your overall readiness for Manufacturing Project Manager roles with our AI Career Coach. Receive personalized recommendations for education, projects, and experience to boost your competitiveness.
Assess your readinessSimple pricing, powerful features
Upgrade to Himalayas Plus and turbocharge your job search.
Himalayas
Himalayas Plus
Himalayas Max
Find your dream job
Sign up now and join over 100,000 remote workers who receive personalized job alerts, curated job matches, and more for free!
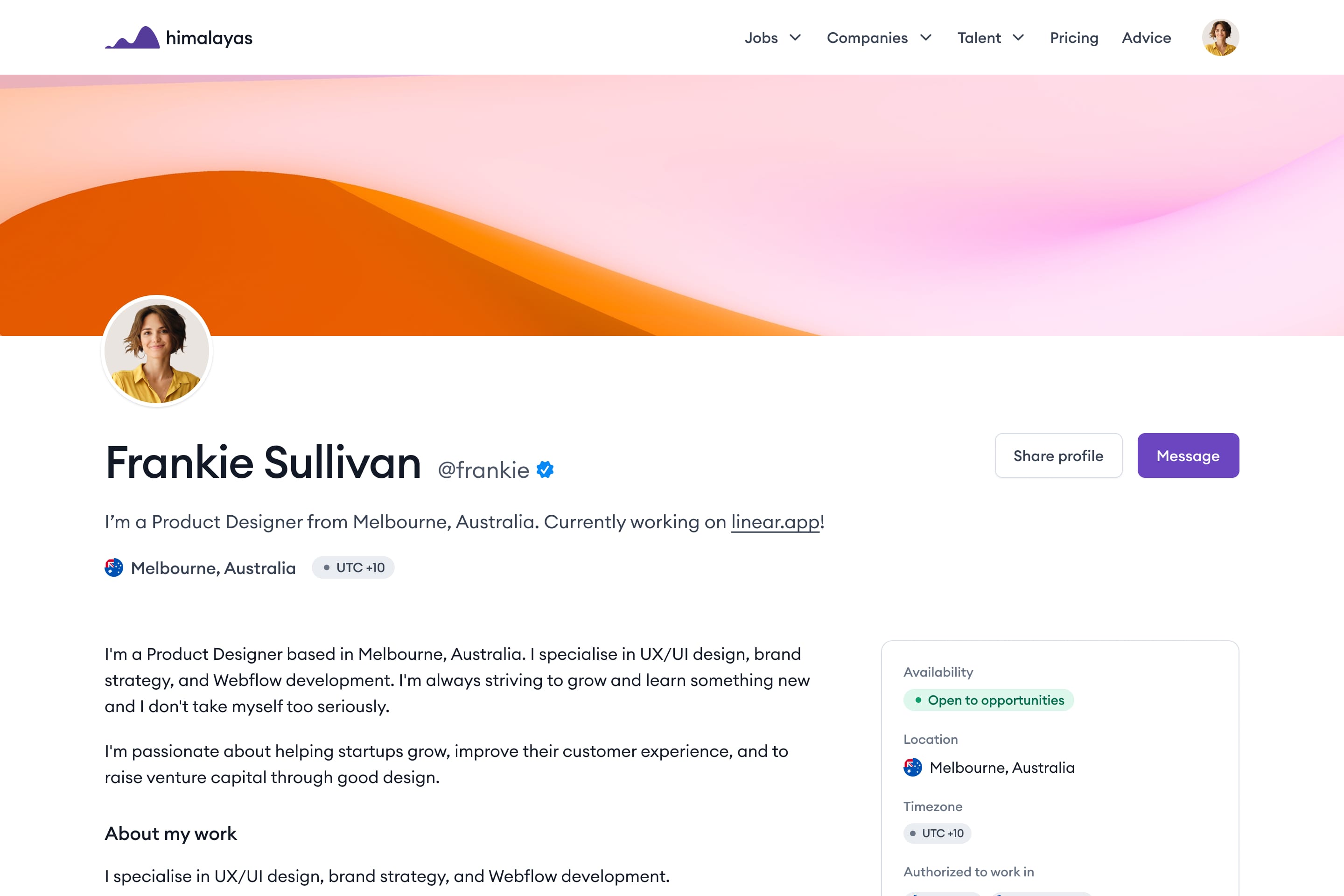