Complete Maintenance Worker Career Guide
Maintenance workers are the unsung heroes who keep buildings and facilities running smoothly, tackling everything from minor repairs to critical system upkeep. They ensure safe, functional environments for businesses, schools, and homes, making this a hands-on career vital to daily operations across every sector. It offers stable opportunities for those who enjoy practical problem-solving and diverse tasks.
Key Facts & Statistics
Median Salary
$45,930 USD
Range: $30k - $70k+ USD
Growth Outlook
5%
as fast as average
Annual Openings
≈180k
openings annually
Top Industries
Typical Education
High school diploma or equivalent, with on-the-job training; some positions may require vocational training or certifications.
What is a Maintenance Worker?
A Maintenance Worker is a skilled individual responsible for the upkeep, repair, and operational efficiency of buildings, facilities, and their integrated systems. This role ensures that physical structures, mechanical equipment, and utility systems function correctly and safely for occupants or operations. They are frontline problem-solvers who address issues ranging from routine wear-and-tear to unexpected malfunctions.
Unlike specialized technicians who focus on a single area like HVAC or plumbing, a Maintenance Worker possesses a broad range of general repair skills across multiple trades. They perform preventative maintenance, respond to repair requests, and conduct minor installations. Their primary value lies in minimizing downtime, extending the life of assets, and providing a safe, functional environment, making them crucial for the smooth operation of any facility.
What does a Maintenance Worker do?
Key Responsibilities
- Inspect building systems, including plumbing, electrical, and HVAC, to identify necessary repairs or maintenance tasks.
- Perform routine preventative maintenance on equipment and machinery to ensure optimal operation and extend asset lifespan.
- Conduct minor repairs on structural elements such as walls, floors, and ceilings, including patching drywall and painting.
- Troubleshoot and resolve issues with building fixtures like lighting, doors, and windows, ensuring they function correctly and safely.
- Respond promptly to maintenance requests from occupants, addressing issues like leaky faucets, clogged drains, or malfunctioning appliances.
- Maintain outdoor areas, including groundskeeping tasks like mowing, trimming, and clearing debris, especially during adverse weather conditions.
- Document all maintenance activities, repairs performed, and materials used, keeping accurate records for future reference and inventory management
Work Environment
Maintenance workers typically operate in a dynamic and varied environment, spending time both indoors and outdoors. They might work in commercial buildings, residential complexes, schools, or industrial facilities. The work often involves physical activity, including lifting, bending, climbing ladders, and working in confined spaces.
Collaboration is common, as they frequently interact with building occupants, other maintenance staff, and external contractors. The schedule is generally full-time, though on-call shifts for emergencies are frequent, especially in residential or critical facility settings. The pace can vary from steady routine tasks to urgent, fast-paced responses during breakdowns or emergencies.
Tools & Technologies
Maintenance workers use a wide array of hand and power tools daily. This includes basic tools like wrenches, screwdrivers, hammers, and saws for general repairs. Power tools such as drills, grinders, circular saws, and pressure washers are essential for more demanding tasks.
Specialized equipment for plumbing (pipe wrenches, drain snakes), electrical work (multimeters, wire strippers), and HVAC systems (refrigerant gauges, vacuum pumps) is also commonly used. They rely on safety gear like gloves, safety glasses, and hard hats. Maintenance tracking software or computerized maintenance management systems (CMMS) help them log tasks, manage work orders, and track inventory efficiently.
Maintenance Worker Skills & Qualifications
A Maintenance Worker's qualifications are primarily practical, focusing on hands-on experience and a diverse skill set rather than advanced academic degrees. Employers prioritize demonstrable competency across various trades. Requirements vary significantly by the type of facility, such as residential, commercial, industrial, or institutional settings, each demanding specific knowledge like HVAC, plumbing, electrical, or carpentry.
For entry-level positions, a high school diploma or GED combined with vocational training or a few years of general labor experience is often sufficient. As workers advance to senior or specialized roles, certifications in specific trades, extensive experience, and a proven track record of independent problem-solving become crucial. Formal education, like an associate's degree in facilities management, can accelerate career progression, particularly in larger organizations or supervisory roles.
While formal degrees are less common, industry-specific certifications in areas like HVAC, electrical, or plumbing add significant value and are often required for specialized tasks. These certifications demonstrate a commitment to safety and adherence to industry standards, which are non-negotiable. The field is evolving with smart building technologies and energy efficiency initiatives, making skills in basic automation and digital diagnostics increasingly important for future success.
Education Requirements
Technical Skills
- Basic electrical wiring and troubleshooting (e.g., outlets, switches, light fixtures)
- Plumbing repairs and installations (e.g., faucets, toilets, drains, minor leaks)
- HVAC system maintenance and filter replacement (e.g., basic troubleshooting, thermostat repair)
- General carpentry (e.g., drywall repair, painting, door/window repair, minor framing)
- Preventative maintenance procedures and scheduling (e.g., equipment checks, lubrication)
- Tool and equipment operation (e.g., power tools, hand tools, ladders, lifts)
- Routine vehicle maintenance (e.g., fluid checks, tire pressure, minor repairs)
- Locksmithing and keying systems (e.g., rekeying locks, repairing door hardware)
- Basic masonry and concrete repair (e.g., patching, crack repair)
- Appliance repair and installation (e.g., refrigerators, washers, dryers)
- Blueprint and schematic reading (e.g., interpreting electrical, plumbing diagrams)
- Safety regulations and protocols (e.g., OSHA standards, hazardous material handling)
Soft Skills
- Problem-solving: Maintenance Workers frequently diagnose and fix issues, requiring logical deduction to identify root causes and implement effective solutions.
- Attention to detail: Meticulous observation prevents overlooked issues, ensuring repairs are thorough and safety standards are met, crucial for preventing repeat failures.
- Adaptability: Facilities present diverse and unpredictable challenges; workers must quickly adjust to new problems, changing priorities, and varied environments.
- Safety consciousness: Adherence to safety protocols protects oneself and others; understanding and implementing lockout/tagout, PPE use, and hazardous material handling is paramount.
- Time management: Efficiently prioritizing and completing multiple repair tasks or preventative maintenance schedules ensures minimal downtime and operational continuity.
- Communication: Clearly explaining issues, repair processes, and preventative measures to supervisors, colleagues, and building occupants ensures everyone understands the situation.
- Customer service orientation: Interacting with tenants or staff requires a helpful and professional demeanor, resolving issues efficiently while maintaining a positive relationship.
- Resourcefulness: Successfully completing tasks often involves improvising solutions with available tools or materials, especially in unexpected situations or during urgent repairs.
How to Become a Maintenance Worker
Breaking into a Maintenance Worker role offers multiple pathways, whether you are a complete beginner or transitioning from a related field. For those new to the trades, a vocational school program or an apprenticeship provides structured learning and hands-on experience, typically taking 6 months to 2 years. Career changers with transferable skills from construction or manufacturing might find direct entry-level positions or shorter certificate courses more suitable, potentially securing a role within 3-6 months.
Entry strategies vary significantly by employer and location. Large corporations or municipalities often prefer candidates with formal certifications or apprenticeship completions due to their standardized training. Smaller businesses or local facilities might prioritize practical experience and a strong work ethic, sometimes offering on-the-job training. Geographic location also plays a role; urban areas may have more specialized roles, while rural areas might require generalist maintenance skills. Understanding these nuances helps in choosing the most effective entry point.
A common misconception is that this field requires only brute strength; instead, it demands problem-solving abilities, attention to detail, and a solid understanding of various systems like plumbing, electrical, and HVAC. While formal degrees are not typically required, obtaining relevant certifications significantly boosts your employability. Networking with other tradespeople, joining local trade associations, and seeking mentorship can open doors to opportunities not publicly advertised, providing crucial insights into the evolving hiring landscape.
Step 1
Step 2
Step 3
Step 4
Step 5
Step 6
Education & Training Needed to Become a Maintenance Worker
Becoming a Maintenance Worker typically involves a blend of practical training and hands-on experience, rather than extensive formal degrees. While some employers prefer candidates with a high school diploma or GED, a bachelor's degree is rarely required. Vocational schools, community colleges, and apprenticeship programs offer the most direct pathways. These programs typically focus on practical skills like plumbing, electrical work, HVAC, and carpentry, costing anywhere from $3,000 to $15,000 and taking 6 months to 2 years to complete.
Alternative learning paths include on-the-job training, often through entry-level positions or assistant roles, which can take 1 to 3 years to gain proficiency. Self-study through online courses or trade manuals, while less structured, can supplement practical experience. Employer acceptance heavily favors candidates with demonstrable practical skills and certifications, such as EPA Section 608 for HVAC or OSHA 10/30-hour cards for safety. These certifications enhance employability and can lead to higher wages.
Continuous learning is vital in this field due to evolving building codes, new technologies, and specialized equipment. Many experienced maintenance workers pursue advanced certifications in specific trades or participate in manufacturer-specific training. The cost-benefit analysis for education in this role strongly favors vocational training and certifications, which offer a high return on investment through immediate applicability and increased earning potential, compared to more expensive, less directly relevant four-year degrees.
Maintenance Worker Salary & Outlook
Compensation for a Maintenance Worker varies significantly, influenced by numerous factors beyond just base pay. Geographic location plays a major role; areas with a higher cost of living or strong industrial presence typically offer higher salaries. For instance, a Maintenance Worker in New York City will likely earn more than one in a rural part of Kansas, reflecting local economic conditions and demand.
Experience, specialized skills, and certifications directly impact earning potential. A worker with expertise in HVAC, plumbing, or electrical systems commands a premium. Total compensation often extends beyond salary, including overtime pay, on-call bonuses, and comprehensive benefits packages. These benefits can encompass health insurance, retirement plans like 401(k)s, paid time off, and allowances for tools or professional development.
Industry also shapes compensation. Maintenance Workers in manufacturing, healthcare, or large commercial facilities often receive better pay and benefits compared to those in residential or smaller institutional settings. Unionized positions frequently offer higher wages and more robust benefits. Remote work is generally not applicable to this hands-on role, but the specific site and employer size can affect the overall compensation structure. Negotiating leverage comes from demonstrating a broad skill set, a strong safety record, and reliability. While figures are presented in USD, international markets have their own distinct pay scales and economic factors.
Salary by Experience Level
Level | US Median | US Average |
---|---|---|
Maintenance Assistant | $36k USD | $38k USD |
Maintenance Worker | $45k USD | $47k USD |
Senior Maintenance Worker | $56k USD | $58k USD |
Maintenance Supervisor | $68k USD | $70k USD |
Maintenance Manager | $82k USD | $85k USD |
Director of Maintenance | $110k USD | $115k USD |
Market Commentary
The job market for Maintenance Workers shows consistent demand, driven by the need to upkeep and repair existing infrastructure across various sectors. The Bureau of Labor Statistics projects a steady growth outlook, with an estimated 4% increase in employment for general maintenance and repair workers from 2022 to 2032. This projection translates to approximately 66,700 new jobs over the decade. Economic factors, such as aging infrastructure and the continuous operation of commercial and industrial facilities, ensure a stable need for these roles.
Emerging opportunities for Maintenance Workers increasingly involve integrating technology. Proficiency with computerized maintenance management systems (CMMS) and smart building technologies is becoming more valuable. The shift towards predictive maintenance, using sensors and data analytics to anticipate equipment failures, creates new specialization areas. While automation can streamline some tasks, the hands-on nature of troubleshooting, repairing, and installing physical systems makes this role largely resistant to full automation.
Supply and demand dynamics vary by region; some areas experience shortages of skilled tradespeople, leading to higher wages and better opportunities. Geographic hotspots for Maintenance Workers include urban centers with extensive commercial properties, large manufacturing hubs, and regions with significant healthcare infrastructure. This profession is relatively recession-resistant, as maintenance is critical regardless of economic cycles. Future-proofing involves continuous learning in new technologies, safety protocols, and specialized mechanical or electrical skills.
Maintenance Worker Career Path
Career progression for a Maintenance Worker typically begins with hands-on technical skill development and evolves towards leadership, strategic planning, and operational management. The path often distinguishes between individual contributor (IC) tracks focused on specialized technical mastery and management tracks that oversee teams and departmental operations. Advancement speed depends on demonstrated technical proficiency, safety adherence, problem-solving abilities, and the capacity to take on greater responsibility.
Factors influencing advancement include continuous learning, obtaining specialized certifications (e.g., HVAC, electrical, plumbing), and consistent high performance. Larger organizations or those with complex infrastructure offer more structured advancement opportunities, while smaller companies might require a broader skill set and fewer distinct hierarchical levels. Lateral movement often involves specializing in a particular trade or moving into a related field like facilities management or construction.
Networking within professional associations and mentorship from experienced colleagues are crucial for identifying opportunities and gaining insights into best practices. Key milestones include mastering complex repairs, leading small projects, and successfully managing preventative maintenance programs. Career pivots might lead to roles in safety management, property management, or even training and development for new maintenance professionals.
Maintenance Assistant
0-2 yearsKey Focus Areas
Maintenance Worker
2-5 yearsKey Focus Areas
Senior Maintenance Worker
5-8 yearsKey Focus Areas
Maintenance Supervisor
8-12 yearsKey Focus Areas
Maintenance Manager
12-18 yearsKey Focus Areas
Director of Maintenance
18+ yearsKey Focus Areas
Maintenance Assistant
0-2 yearsAssists senior technicians with routine maintenance tasks, minor repairs, and preventative maintenance checks. Operates under close supervision, focusing on learning proper techniques and safety procedures. Handles basic tasks like cleaning, organizing tools, and transporting equipment. Has no decision-making authority.
Key Focus Areas
Develop foundational skills in basic repairs, tool usage, and safety protocols. Learn to follow instructions accurately and observe experienced technicians. Focus on understanding common maintenance issues and proper documentation procedures. Building a strong work ethic and attention to detail are key.
Maintenance Worker
2-5 yearsPerforms a variety of general maintenance and repair tasks independently, such as plumbing fixes, electrical troubleshooting, and minor carpentry. Responds to work orders and conducts preventative maintenance checks. Makes routine decisions regarding repair methods and material selection under general supervision. Impacts daily operational efficiency.
Key Focus Areas
Master a broad range of general maintenance skills including basic electrical, plumbing, carpentry, and HVAC. Develop independent problem-solving abilities for common issues. Focus on efficient task completion, accurate record-keeping, and proactive identification of potential problems. Begin understanding system interdependencies.
Senior Maintenance Worker
5-8 yearsHandles complex and specialized maintenance tasks, diagnostics, and repairs requiring advanced technical skills. Acts as a subject matter expert and often provides technical guidance to junior workers. Leads small projects or specific maintenance initiatives, ensuring quality and adherence to schedules. Exercises significant autonomy in problem-solving and task prioritization.
Key Focus Areas
Specialize in one or more complex trades (e.g., advanced HVAC, industrial electrical systems, sophisticated plumbing). Develop diagnostic expertise for intricate issues and train junior staff. Focus on optimizing maintenance processes, implementing best practices, and ensuring compliance with regulations. Certifications in specific trades are highly beneficial.
Maintenance Supervisor
8-12 yearsOversees a team of Maintenance Workers, assigning tasks, monitoring progress, and ensuring quality control. Manages daily operations, schedules preventative maintenance, and responds to urgent repair needs. Conducts performance reviews and provides training to team members. Makes operational decisions influencing team productivity and resource allocation.
Key Focus Areas
Develop leadership and team management skills, including scheduling, delegation, and performance feedback. Focus on effective communication, conflict resolution, and motivating a team. Understand budgeting basics and inventory management. Prioritize safety leadership and continuous improvement initiatives.
Maintenance Manager
12-18 yearsManages the entire maintenance department, including budgeting, staffing, and strategic planning for facility upkeep. Develops and implements preventative maintenance programs, oversees major repair projects, and ensures regulatory compliance. Responsible for departmental performance metrics, resource allocation, and talent development within the team. Impacts organizational operational costs and asset longevity.
Key Focus Areas
Develop strong departmental leadership, strategic planning, and financial management skills. Focus on optimizing maintenance programs, implementing new technologies, and managing vendor relationships. Build capabilities in departmental budgeting, capital expenditure planning, and long-term asset management. Emphasize cross-functional collaboration with other departments.
Director of Maintenance
18+ yearsProvides executive leadership and strategic direction for all maintenance and facilities operations across an organization or multiple sites. Develops long-term maintenance strategies, manages large capital projects, and oversees departmental budgets. Establishes policies, ensures compliance, and drives continuous improvement initiatives that impact the entire organization's infrastructure and operational efficiency. Represents maintenance at the executive level.
Key Focus Areas
Focus on executive leadership, organizational strategy, and enterprise-level asset management. Develop expertise in risk management, long-range capital planning, and integrating maintenance strategy with overall business objectives. Cultivate strong stakeholder management skills and industry thought leadership. Mentorship and succession planning become critical.
Job Application Toolkit
Ace your application with our purpose-built resources:
Maintenance Worker Resume Examples
Proven layouts and keywords hiring managers scan for.
View examplesMaintenance Worker Cover Letter Examples
Personalizable templates that showcase your impact.
View examplesTop Maintenance Worker Interview Questions
Practice with the questions asked most often.
View examplesMaintenance Worker Job Description Template
Ready-to-use JD for recruiters and hiring teams.
View examplesGlobal Maintenance Worker Opportunities
The Maintenance Worker role translates globally, focusing on facility upkeep across residential, commercial, and industrial sectors. International demand remains steady, driven by infrastructure development and aging buildings needing repair. Regulatory differences affect safety standards and building codes, requiring local adaptation. Professionals consider international opportunities for better pay, diverse work environments, or specific project involvement. No specific international certifications are broadly standardized, but trade-specific qualifications from recognized institutions enhance mobility.
Global Salaries
Maintenance Worker salaries vary significantly by region and cost of living. In North America, a Maintenance Worker in the USA typically earns $35,000 to $55,000 USD annually, while in Canada, it ranges from CAD 40,000 to CAD 60,000. These figures reflect solid purchasing power, especially in smaller cities.
European salaries show wide differences. In Germany, a Maintenance Worker might earn €28,000 to €40,000 (approximately $30,000-$43,000 USD), with excellent social benefits. The UK offers £22,000 to £32,000 (around $28,000-$41,000 USD), often with fewer included benefits compared to continental Europe.
Asia-Pacific markets present diverse compensation. Australia offers AUD 50,000 to AUD 70,000 (roughly $33,000-$46,000 USD), reflecting a higher cost of living. In Southeast Asia, like Singapore, salaries could be SGD 24,000 to SGD 36,000 (about $18,000-$27,000 USD), which provides reasonable purchasing power for local goods and services.
Latin America generally has lower nominal salaries but also a lower cost of living. In Mexico, a Maintenance Worker might earn MXN 96,000 to MXN 180,000 (approximately $5,000-$10,000 USD). This allows for local comfort, but international savings can be challenging. Experience and specialized skills, such as HVAC or electrical work, often increase compensation and transferability across borders.
Remote Work
International remote work opportunities for Maintenance Workers are extremely limited. The role inherently requires on-site physical presence to perform repairs, inspections, and upkeep of facilities and equipment. It is not a desk-based profession.
Digital nomad lifestyles are not applicable to this hands-on career. Companies do not typically hire Maintenance Workers for international remote roles because the core duties cannot be performed virtually. All work involves direct interaction with physical infrastructure.
Any 'remote' aspect would only involve administrative tasks or scheduling, which are minor parts of the job. Therefore, a Maintenance Worker seeking international opportunities needs to pursue traditional on-site employment in another country.
Visa & Immigration
Maintenance Workers often qualify for skilled worker visas in countries with demand for trades, like Canada (Express Entry), Australia (Skilled Migration Program), and Germany (Skilled Immigration Act). Requirements usually include a job offer, relevant experience, and sometimes trade certifications or diplomas.
For instance, Canada's Federal Skilled Trades Program requires at least two years of full-time trade experience and a valid job offer or certificate of qualification. Australia's General Skilled Migration program may list maintenance roles on its skilled occupation lists, requiring skills assessment.
Visa timelines vary, typically from 6 to 18 months. Credential recognition is crucial; applicants often need their qualifications assessed by relevant national bodies. Language proficiency, usually English or the local language, is often a requirement for integration and safety.
Some countries offer pathways to permanent residency for skilled trades, recognizing their economic contribution. Family visas for dependents are usually available once the primary applicant secures their work visa.
2025 Market Reality for Maintenance Workers
Understanding current market conditions is crucial for any maintenance worker aiming for career stability or advancement. The landscape for these roles has seen shifts, particularly since 2023, influenced by technological advancements and broader economic forces. Knowing these realities helps job seekers align their skills and expectations.
Post-pandemic, many facilities accelerated upgrades, creating a temporary surge in some maintenance projects. Now, the market has normalized, with a steady demand for upkeep. Broader economic factors, like inflation or interest rates, indirectly affect the sector by influencing new construction or facility expansion, but essential maintenance remains a constant need. Market realities vary significantly; an experienced HVAC technician in a large city will encounter different opportunities than a general maintenance worker in a small town. This analysis provides an honest assessment of these dynamics.
Current Challenges
Maintenance workers face rising expectations for diverse technical skills. Automated systems in facilities require new diagnostic abilities. The job market remains localized, limiting remote work opportunities, and competition for stable, well-paying roles can be intense, especially in urban centers. Economic downturns sometimes lead companies to defer non-essential maintenance, impacting job security.
Growth Opportunities
Despite market challenges, strong opportunities exist for maintenance workers with diverse skill sets. Facilities are increasingly seeking multi-skilled technicians who can handle electrical, plumbing, and HVAC issues, rather than separate specialists. This versatility makes candidates highly valuable.
Emerging roles involve managing smart building technologies, such as integrated security systems or energy management platforms. Maintenance workers who can interpret data from these systems for predictive maintenance are in high demand. Commercial and industrial sectors, including manufacturing plants and large commercial properties, consistently offer robust opportunities due to the complexity and scale of their infrastructure.
Professionals can gain a competitive edge by pursuing certifications in specialized areas like HVAC, electrical codes, or specific equipment operation. Investing in training for new technologies, such as building automation systems or advanced diagnostics, also opens doors. Underserved markets might include specialized facilities like data centers or healthcare institutions, which require specific compliance knowledge and offer stable, often higher-paying, roles. Strategic career moves involve targeting industries less susceptible to economic downturns, focusing on essential services, or seeking roles in companies prioritizing facility longevity.
Current Market Trends
Demand for skilled maintenance workers remains steady across many sectors in 2025. Facilities consistently need upkeep, from residential complexes to industrial plants. The market for general maintenance roles is stable, but specialized skills, such as HVAC, electrical, or plumbing, command higher demand and better compensation.
Technology, particularly smart building systems and IoT devices, is influencing the role. Maintenance workers increasingly troubleshoot automated systems, requiring a blend of traditional hands-on skills and digital literacy. Employers seek candidates who can adapt to new tools and software for scheduling and diagnostics, moving beyond purely manual tasks. Economic conditions like rising interest rates affect new construction less than existing facility maintenance, providing a consistent need for upkeep.
Salary growth for experienced maintenance workers shows a positive trend, especially for those with multiple certifications. Entry-level positions, however, may see slower wage increases due to a larger pool of candidates. Geographic variations are significant; urban areas and industrial hubs often present more job openings and better pay than rural regions. Remote work is generally not applicable to this hands-on role, anchoring opportunities to specific physical locations. Seasonal hiring patterns are minimal, as maintenance needs are year-round, though some outdoor tasks might fluctuate with weather.
Emerging Specializations
The role of a Maintenance Worker is evolving significantly, driven by advancements in smart technologies, sustainable practices, and data analytics. These technological shifts are creating new specialization opportunities that were once uncommon or non-existent. Understanding and positioning oneself early in these emerging areas can provide a substantial advantage for career advancement from 2025 onwards.
Specializing in cutting-edge fields often leads to premium compensation and accelerated career growth. While established maintenance specializations remain crucial, the demand for professionals skilled in next-generation maintenance approaches is rapidly increasing. Early adoption of these skills allows professionals to become subject matter experts as these areas transition from niche to mainstream, typically over a three to five-year period.
Choosing an emerging specialization involves a balance of risk and reward. It requires proactive learning and adaptability, but the payoff includes enhanced employability and leadership opportunities in a rapidly changing industry. Professionals who embrace these evolving areas will be well-prepared to meet future industry demands and drive innovation in maintenance operations.
Predictive Maintenance Technician
Predictive maintenance utilizes sensor data, machine learning, and analytical tools to forecast equipment failures before they occur. This specialization moves beyond traditional reactive or preventive maintenance, enabling Maintenance Workers to schedule interventions precisely when needed. It minimizes downtime, extends asset lifespan, and optimizes resource allocation by shifting from fixed schedules to data-driven insights.
Smart Building Systems Specialist
Maintenance Workers specializing in building automation systems manage and troubleshoot integrated smart building technologies. This includes HVAC controls, lighting systems, security access, and energy management platforms that communicate through a central network. Their expertise ensures optimal building performance, energy efficiency, and occupant comfort by maintaining complex interconnected systems.
Renewable Energy Systems Maintenance Technician
Specialists in renewable energy system maintenance focus on the upkeep of solar panels, wind turbines, and other green energy infrastructure. This involves routine inspections, performance monitoring, and troubleshooting of electrical and mechanical components specific to sustainable power generation. Their work ensures the reliability and efficiency of renewable energy assets.
Industrial Robotics Maintenance Technician
Industrial Robotics Maintenance Technicians are responsible for the installation, programming, repair, and routine servicing of automated robotic systems used in manufacturing and logistics. This specialization demands a deep understanding of robotic mechanics, electronics, and control systems. They ensure the continuous operation and efficiency of automated production lines.
Sustainable HVAC-R Technician
HVAC-R technicians specializing in sustainable climate control systems focus on maintaining and optimizing high-efficiency heating, ventilation, air conditioning, and refrigeration units that utilize environmentally friendly refrigerants and energy recovery technologies. This role is critical for reducing carbon footprints and ensuring compliance with evolving environmental regulations. They troubleshoot complex systems designed for minimal environmental impact.
Pros & Cons of Being a Maintenance Worker
Making informed career choices requires understanding both the benefits and challenges of a profession. The experience of a maintenance worker can vary significantly based on the industry, the specific facility, company culture, and an individual's personal aptitude and preferences. What one person considers a benefit, such as hands-on problem-solving, another might view as a challenge due to the physical demands. Furthermore, the nature of the work can evolve at different career stages, from entry-level tasks to more complex diagnostic and supervisory roles. This assessment provides a realistic overview, helping aspiring maintenance workers set appropriate expectations for this essential career path.
Pros
- High demand for skilled trades ensures consistent job security across various industries, as every building and facility requires ongoing upkeep and repair.
- Tangible results provide immediate satisfaction, as workers can see the direct impact of their efforts in restoring functionality and improving safety or efficiency.
- Diverse work environments offer variety, ranging from schools and hospitals to manufacturing plants and residential complexes, preventing monotony and allowing for different experiences.
- Practical problem-solving is a core aspect, constantly challenging workers to diagnose issues and devise effective solutions using mechanical, electrical, and plumbing knowledge.
- Opportunities for continuous learning exist through on-the-job training and specialized certifications in areas like HVAC, electrical systems, or welding, enhancing skill sets and marketability.
- A sense of essential service is often present, as maintenance workers ensure the safe and efficient operation of vital infrastructure, directly impacting the comfort and productivity of others.
- Entry barriers are relatively low compared to other skilled professions, with many roles accessible through vocational training, apprenticeships, or relevant experience rather than a four-year degree.
Cons
- Exposure to hazardous conditions, including working with dangerous machinery, electrical systems, and chemicals, requires constant vigilance and adherence to strict safety protocols.
- Physical demands are high, often involving heavy lifting, climbing ladders, bending, kneeling, and working in cramped or uncomfortable spaces, which can lead to strain or injury over time.
- Irregular work hours are common, as emergency repairs often require maintenance workers to be on-call or work evenings, weekends, and holidays, disrupting personal time.
- Dealing with unexpected breakdowns and urgent requests can create high-pressure situations and disrupt planned work, leading to stress and the need for quick, effective problem-solving.
- The work can be dirty and unpleasant, often involving contact with grime, dust, waste, and unpleasant odors, which some individuals may find off-putting.
- Career progression can be limited in some organizations, with fewer opportunities for promotion beyond a senior maintenance role without acquiring specialized certifications or management training.
- Public perception may sometimes undervalue the critical role maintenance workers play, despite their essential contribution to safety and operational efficiency.
Frequently Asked Questions
What are the essential qualifications or certifications needed to become a Maintenance Worker?
Entry into a Maintenance Worker role typically requires a high school diploma or GED. Many employers prefer vocational training, an associate's degree in a related field like HVAC or electrical technology, or prior hands-on experience. Certifications in specific trades, such as EPA Section 608 for refrigerants or OSHA 10/30-hour safety training, significantly boost your employability and demonstrate foundational knowledge.
How long does it typically take to become a skilled Maintenance Worker, especially for someone new to the trades?
The timeline to become job-ready as a Maintenance Worker varies. If you pursue a vocational program, it can take 6 months to 2 years. Apprenticeships can last 3-5 years, providing on-the-job training and classroom instruction. If you have some basic mechanical aptitude and are self-taught, you might find entry-level positions quicker, but formal training often leads to better opportunities and higher pay.
What are the typical salary expectations for an entry-level Maintenance Worker, and how does that grow with experience?
Starting salaries for Maintenance Workers can range from $30,000 to $45,000 annually, depending on location, specific industry, and your skill set. Experienced workers with specialized certifications or supervisory roles can earn $50,000 to $70,000 or more. Your earning potential grows with your ability to handle more complex repairs, manage projects, and acquire advanced technical skills.
What is the typical work-life balance and physical demand like for a Maintenance Worker?
Maintenance work often involves a degree of physical activity, including lifting, bending, climbing, and working in various environments. While not always intensely strenuous, you should be prepared for hands-on tasks and being on your feet for extended periods. Most roles are full-time, Monday-Friday, but emergency calls or scheduled weekend work for critical repairs can be common, impacting work-life balance at times.
Is the Maintenance Worker field a stable career with good job security, or is it at risk from automation?
The job market for Maintenance Workers is generally stable and growing. Every building, facility, and piece of equipment requires upkeep, ensuring consistent demand across various sectors like residential, commercial, industrial, and institutional. Automation might change some tasks, but the need for skilled individuals to diagnose, repair, and maintain complex systems remains strong, offering good job security.
What are the career advancement opportunities for a Maintenance Worker?
Career growth for a Maintenance Worker can lead to specialized roles like HVAC Technician, Electrician, Plumber, or Facility Manager. Many advance to supervisory positions, overseeing teams of maintenance staff, or move into roles focused on preventative maintenance planning and asset management. Continuing education and acquiring additional trade certifications are key to upward mobility and increased earning potential.
What are some of the biggest challenges or common frustrations Maintenance Workers face in their daily roles?
A common challenge is managing a diverse range of issues, from minor repairs to urgent breakdowns, often requiring quick problem-solving under pressure. You need to be adaptable and possess a broad skill set, as no two days are exactly alike. Safety is paramount; consistently adhering to protocols and handling hazardous materials or equipment safely is a constant, critical concern in this role.
Is there any flexibility for remote work or is a Maintenance Worker role strictly on-site?
While some administrative or planning tasks might be done remotely, the core work of a Maintenance Worker requires being on-site to inspect, repair, and maintain equipment and facilities. Most roles are therefore location-dependent, involving travel between different sites or within a specific facility. Remote work is generally not a significant aspect of this career path, given its hands-on nature.
Related Careers
Explore similar roles that might align with your interests and skills:
General Maintenance Technician
A growing field with similar skill requirements and career progression opportunities.
Explore career guideMaintenance Assistant
A growing field with similar skill requirements and career progression opportunities.
Explore career guideMaintenance Technician
A growing field with similar skill requirements and career progression opportunities.
Explore career guideFacilities Maintenance Worker
A growing field with similar skill requirements and career progression opportunities.
Explore career guideGeneral Maintenance Worker
A growing field with similar skill requirements and career progression opportunities.
Explore career guideAssess your Maintenance Worker readiness
Understanding where you stand today is the first step toward your career goals. Our Career Coach helps identify skill gaps and create personalized plans.
Skills Gap Analysis
Get a detailed assessment of your current skills versus Maintenance Worker requirements. Our AI Career Coach identifies specific areas for improvement with personalized recommendations.
See your skills gapCareer Readiness Assessment
Evaluate your overall readiness for Maintenance Worker roles with our AI Career Coach. Receive personalized recommendations for education, projects, and experience to boost your competitiveness.
Assess your readinessSimple pricing, powerful features
Upgrade to Himalayas Plus and turbocharge your job search.
Himalayas
Himalayas Plus
Himalayas Max
Find your dream job
Sign up now and join over 100,000 remote workers who receive personalized job alerts, curated job matches, and more for free!
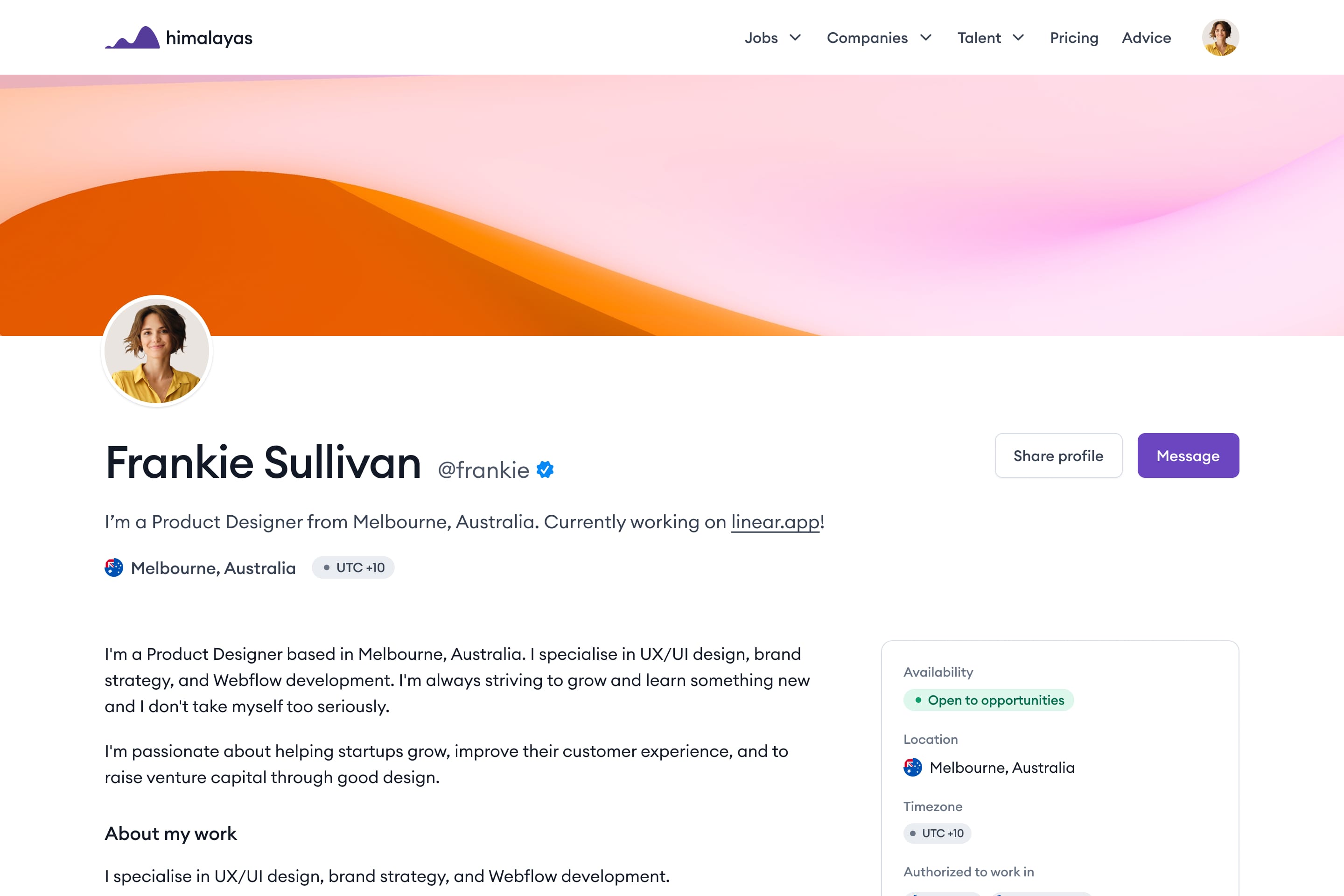