Complete Line Leader Career Guide
Line leaders are crucial in manufacturing and production, ensuring operational efficiency and quality control on the factory floor. They bridge management and frontline staff, optimizing workflows and fostering team productivity to meet demanding production targets. This role offers a direct path to impact output and develop leadership skills within dynamic industrial environments.
Key Facts & Statistics
Median Salary
$62,560 USD
(U.S. Bureau of Labor Statistics, May 2023)
Range: $40k - $85k+ USD
Growth Outlook
1%
slower than average (U.S. Bureau of Labor Statistics, 2022-2032)
Annual Openings
≈34k
openings annually (U.S. Bureau of Labor Statistics, 2022-2032)
Top Industries
Typical Education
High school diploma or equivalent; often requires on-the-job training and leadership experience in a production environment. Some positions may prefer an associate's degree or vocational training.
What is a Line Leader?
A Line Leader is a critical frontline management position in manufacturing and production environments. This professional oversees a specific section or 'line' of the production process, ensuring that operational goals for quality, efficiency, and safety are met. They act as the direct supervisor and mentor for a team of production associates, bridging the gap between management directives and on-the-ground execution.
Unlike a Production Manager who manages multiple lines or a broader department, a Line Leader focuses intensely on the day-to-day performance of their assigned line. They are distinct from a Team Lead, who might focus more on project-based work or a specific task within a team, as a Line Leader is directly responsible for the continuous output and operational integrity of a physical production line. This role is vital for maintaining smooth operations and ensuring product consistency in high-volume manufacturing.
What does a Line Leader do?
Key Responsibilities
- Organize and assign daily tasks to team members on the production line, ensuring efficient workflow and adherence to production schedules.
- Monitor product quality throughout the manufacturing process, identifying and addressing any defects or non-compliance issues promptly.
- Train new team members on standard operating procedures, safety protocols, and proper equipment usage.
- Troubleshoot minor equipment malfunctions or production bottlenecks, escalating complex issues to maintenance or management as needed.
- Maintain accurate production records, including output, waste, and downtime, and report these metrics to supervisors.
- Enforce safety regulations and promote a culture of workplace safety, conducting regular checks to ensure compliance.
- Facilitate communication between the production line and management, relaying feedback and addressing concerns from team members and supervisors alike.
Work Environment
Line leaders typically work in manufacturing plants, warehouses, or production facilities. The environment can be noisy, fast-paced, and may require standing for long periods. They often work in shifts, including evenings, nights, and weekends, to align with continuous production schedules. The role involves constant interaction and collaboration with production associates, quality control personnel, maintenance technicians, and supervisors.
The pace is dynamic, requiring quick decision-making to address immediate production issues. While primarily on-site, some administrative tasks may be performed in a quiet office area. The job requires strong leadership and communication skills to motivate the team and maintain high productivity and quality standards in a structured, often regulated, setting.
Tools & Technologies
Line leaders primarily use the specific machinery and equipment relevant to their production line, which can range from automated assembly robots and conveyor systems to manual tools and specialized instruments. They often interact with Human-Machine Interfaces (HMIs) or Supervisory Control and Data Acquisition (SCADA) systems to monitor production parameters and adjust settings.
For communication and record-keeping, they utilize tablets or industrial PCs running enterprise resource planning (ERP) software like SAP or Oracle, manufacturing execution systems (MES), and quality management software. They also rely on standard office productivity suites for reporting and scheduling. Safety equipment, such as personal protective equipment (PPE) and lockout/tagout devices, are integral to their daily operations.
Line Leader Skills & Qualifications
A Line Leader, often found in manufacturing, production, or assembly environments, requires a blend of operational proficiency and people management skills. Qualifications for this role primarily emphasize practical experience, with formal education often playing a secondary, though sometimes beneficial, role. Companies prioritize demonstrated ability to manage a production line efficiently and ensure quality output.
Requirements for a Line Leader vary significantly based on the industry, company size, and specific product. In highly regulated industries like pharmaceuticals or aerospace, strict adherence to quality control and safety protocols is paramount, demanding detailed procedural knowledge. Smaller companies might expect a Line Leader to be more hands-on with production tasks, while larger organizations often focus more on leadership and process optimization. Seniority levels dictate increasing responsibility for team performance, problem-solving, and potentially cross-functional coordination.
While a high school diploma is usually the minimum educational requirement, practical experience on the production floor holds the most weight. Certifications in lean manufacturing, Six Sigma, or specific equipment operation can significantly enhance a candidate's profile. The skill landscape for Line Leaders is evolving, with an increasing emphasis on data analysis for performance monitoring and digital literacy for operating automated systems. Breadth of understanding across different production stages is crucial, alongside depth in specific operational procedures for the assigned line.
Education Requirements
Technical Skills
- Production Planning and Scheduling
- Quality Control and Assurance (e.g., SPC, visual inspection)
- Equipment Operation and Basic Troubleshooting
- Inventory Management and Material Flow
- Safety Protocols and OSHA Compliance
- Lean Manufacturing Principles (e.g., 5S, Kaizen)
- Data Entry and Production Reporting Software
- Standard Operating Procedure (SOP) Adherence
- Basic Computer Literacy (MS Office Suite)
- Performance Metrics Tracking (e.g., OEE, cycle time)
- Preventative Maintenance Coordination
- Tooling and Fixture Management
Soft Skills
- Leadership and Motivation: Crucial for inspiring and guiding a team to meet production targets and maintain morale.
- Problem-Solving: Essential for quickly identifying and resolving operational bottlenecks, equipment issues, or quality deviations on the line.
- Communication: Vital for clearly conveying instructions, providing feedback, and escalating issues to management or maintenance teams.
- Decision-Making: Important for making swift, effective choices under pressure to maintain production flow and quality standards.
- Attention to Detail: Necessary to ensure product quality, adherence to specifications, and compliance with safety regulations.
- Teamwork and Collaboration: Key for fostering a cooperative environment and coordinating efforts with other line leaders or departments.
- Adaptability: Important for adjusting to changing production schedules, new processes, or unexpected challenges.
- Conflict Resolution: Useful for mediating disputes among team members and maintaining a productive work environment on the line.
How to Become a Line Leader
Becoming a Line Leader typically involves an internal promotion from a production or assembly line role, rather than direct external hiring. Most companies prefer to promote individuals who already understand their specific operational procedures, safety protocols, and team dynamics. This means your entry strategy should focus on gaining initial employment on a production floor, demonstrating strong performance, and actively seeking leadership opportunities.
The timeline for becoming a Line Leader can vary significantly. A highly motivated individual might achieve this within 6-12 months of starting in a general production role by consistently exceeding expectations and showing initiative. For others, it might take 1-3 years as they build a deeper understanding of the processes and company culture. Geographic location and industry sector also play a role; manufacturing hubs might have more opportunities, while highly specialized industries might have a longer promotion cycle.
Overcoming barriers to entry for a Line Leader role involves proving your reliability, attention to detail, and ability to work effectively within a team. Many misconceptions exist about this role, such as believing it only requires technical skill; in reality, strong communication, problem-solving, and interpersonal skills are crucial. Networking within the company, seeking mentorship from existing leaders, and actively participating in continuous improvement initiatives significantly enhance your visibility and readiness for promotion.
Step 1
Step 2
Step 3
Step 4
Step 5
Step 6
Step 7
Education & Training Needed to Become a Line Leader
Becoming a Line Leader typically involves a mix of practical experience and targeted training, rather than traditional multi-year degree programs. While a high school diploma or GED is often a baseline, many employers value vocational certifications and on-the-job training. Formal degrees, like a Bachelor's in Operations Management, are not usually required but can accelerate career progression into higher management roles. They also carry a significant cost, ranging from $40,000 to over $100,000, and take four years to complete, which is a substantial investment for a role primarily focused on direct supervision.
Alternative learning paths, such as professional certifications in lean manufacturing, Six Sigma, or production supervision, are highly effective and much more cost-efficient. These programs can range from a few hundred dollars to $5,000, with completion times from a few weeks to six months. Employers widely accept these credentials, often viewing them as direct indicators of a candidate's readiness for supervisory responsibilities. Many companies also offer internal leadership development programs, which are invaluable for gaining the specific skills needed within their operations. These internal programs are typically free for employees and provide immediate, relevant experience.
Continuous learning is crucial for Line Leaders, especially with evolving manufacturing technologies and process improvements. Regular professional development in areas like team leadership, conflict resolution, and quality control ensures ongoing effectiveness. The balance between theoretical knowledge and practical experience leans heavily towards practical application for this role; direct experience on the production floor is paramount. Educational needs vary by industry; for instance, a Line Leader in pharmaceuticals might need more specialized quality control training than one in general assembly. Investing in short, focused training that directly enhances supervisory and operational efficiency provides the best return for aspiring and current Line Leaders.
Line Leader Salary & Outlook
Compensation for a Line Leader varies significantly based on several key factors. Geographic location plays a crucial role, with higher salaries typically found in regions with a higher cost of living or strong manufacturing sectors. For instance, a Line Leader in California or the Northeast might earn more than one in the Midwest, even within the same company.
Experience levels and specialized skills also directly impact earning potential. A Line Leader with extensive experience managing complex production lines or expertise in lean manufacturing principles can command a higher salary. Total compensation often extends beyond base pay, including performance bonuses, overtime pay, and comprehensive benefits packages. These benefits can include health insurance, paid time off, and retirement contributions like 401(k) matching, significantly increasing the overall value of the compensation package.
Industry-specific trends also influence Line Leader salaries. Industries with high demand for production efficiency, such as automotive, food and beverage, or consumer goods, may offer more competitive wages. Larger companies with more extensive operations often provide better compensation and benefits than smaller businesses. Remote work is generally not applicable for this hands-on role, so geographic arbitrage opportunities are limited. Salary negotiation leverage comes from demonstrating a track record of improving efficiency, reducing waste, and effectively leading production teams. While these figures focus on the USD context, international markets will have their own distinct salary scales based on local economic conditions and labor laws.
Salary by Experience Level
Level | US Median | US Average |
---|---|---|
Line Leader | $52k USD | $55k USD |
Senior Line Leader | $62k USD | $65k USD |
Production Supervisor | $72k USD | $75k USD |
Shift Supervisor | $82k USD | $85k USD |
Operations Manager | $100k USD | $105k USD |
Market Commentary
The job market for Line Leaders remains stable, driven by the continuous need for efficient production and operational oversight across various manufacturing sectors. The U.S. Bureau of Labor Statistics projects a modest growth outlook for production and operations managers, which includes roles like Line Leaders, over the next decade. Demand is particularly strong in industries undergoing expansion or those requiring high levels of precision and quality control.
Emerging opportunities for Line Leaders include roles in facilities adopting advanced automation and smart factory technologies. These roles require a blend of traditional leadership skills and an understanding of integrated production systems. The shift towards greater efficiency and data-driven decision-making means Line Leaders with analytical skills and experience with manufacturing execution systems (MES) are increasingly valued.
Supply and demand dynamics show a consistent need for skilled Line Leaders, particularly those capable of managing diverse teams and adapting to new technologies. While automation may change some aspects of production, the need for human oversight, problem-solving, and team leadership remains critical. This role is generally recession-resistant as essential goods production continues even during economic downturns. Geographic hotspots for Line Leaders align with major manufacturing hubs, though the rise of localized supply chains could create new opportunities in various regions. Future-proofing this career involves continuous learning in areas like industrial automation, supply chain optimization, and advanced leadership techniques.
Line Leader Career Path
Career progression for a Line Leader typically begins with demonstrating strong operational execution and team coordination on the production floor. Advancement hinges on consistent performance, an aptitude for problem-solving, and the ability to mentor and lead others effectively. Professionals can choose an individual contributor (IC) track, deepening their expertise within a specific production process, or transition into a management/leadership track, overseeing broader operational segments.
Advancement speed varies based on factors like the company's size, industry (e.g., manufacturing, food processing), and economic conditions. Larger corporations often have more structured paths and opportunities for specialization. Smaller companies might offer faster progression but require broader skill sets. Lateral moves might involve shifting between different production lines or departments, offering exposure to diverse manufacturing processes.
Continuous learning, especially in lean manufacturing, quality control, and safety protocols, drives progression. Networking within the industry and seeking mentorship from experienced supervisors and managers also accelerate growth. Achieving certifications in areas like Six Sigma or project management enhances a Line Leader's profile, marking significant milestones. Career pivots could lead to roles in quality assurance, logistics, or supply chain management, leveraging their operational expertise.
Line Leader
0-2 yearsKey Focus Areas
Senior Line Leader
2-4 yearsKey Focus Areas
Production Supervisor
4-7 years total experienceKey Focus Areas
Shift Supervisor
7-10 years total experienceKey Focus Areas
Operations Manager
10+ years total experienceKey Focus Areas
Line Leader
0-2 yearsDirect and coordinate a small team of production workers on a specific manufacturing line. Ensure daily production targets are met while maintaining quality standards and adhering to safety regulations. Resolve minor operational issues and report equipment malfunctions. They have limited decision-making authority, primarily focusing on task execution and team coordination.
Key Focus Areas
Develop core skills in production efficiency, quality control, and workplace safety. Understand equipment operation, basic troubleshooting, and material flow. Focus on effective communication with team members and immediate supervisors. Learn to follow standard operating procedures precisely.
Senior Line Leader
2-4 yearsOversee multiple production lines or a more complex single line, guiding a larger team. They are responsible for optimizing line performance, minimizing downtime, and ensuring compliance with advanced quality specifications. Senior Line Leaders act as a primary point of contact for technical issues and assist in training new team members, making more independent operational decisions.
Key Focus Areas
Cultivate strong problem-solving abilities, process optimization, and team motivation techniques. Gain expertise in analyzing production data to identify bottlenecks and implement continuous improvement initiatives. Develop basic leadership skills, including conflict resolution and performance feedback.
Production Supervisor
4-7 years total experienceManage the overall operations of an entire production department or a significant section of the plant during a specific shift. They are responsible for meeting production schedules, managing labor resources, and ensuring adherence to all operational policies. Production Supervisors make critical decisions regarding staffing, quality deviations, and minor equipment issues, impacting departmental output and efficiency.
Key Focus Areas
Acquire skills in resource allocation, scheduling, and performance management. Develop a deeper understanding of production planning, inventory management, and cost control. Focus on coaching and developing line leaders, fostering a culture of accountability and continuous improvement. Seek certifications in lean manufacturing or Six Sigma.
Shift Supervisor
7-10 years total experienceOversee all production activities across several departments or the entire facility during their assigned shift. They ensure seamless transitions between shifts, manage complex operational challenges, and coordinate with other supervisors (e.g., maintenance, logistics). Shift Supervisors have significant autonomy in managing daily operations, resource deployment, and emergency response, directly influencing overall plant productivity.
Key Focus Areas
Master strategic planning, cross-functional collaboration, and advanced leadership skills. Develop capabilities in budgeting, capacity planning, and implementing large-scale operational improvements. Focus on fostering a positive work environment, driving employee engagement, and talent development across multiple production areas.
Operations Manager
10+ years total experienceHold ultimate responsibility for all manufacturing operations within a facility or a major business unit. They develop and implement long-term production strategies, manage large budgets, and drive continuous improvement initiatives across the entire operational footprint. Operations Managers make high-level decisions affecting production capacity, technological investments, and workforce planning, directly impacting the company's profitability and market position.
Key Focus Areas
Develop executive-level leadership, strategic thinking, and P&L management skills. Cultivate expertise in supply chain optimization, capital expenditure planning, and long-term operational strategy. Focus on building high-performing teams, driving organizational change, and representing operations in executive discussions. Pursue advanced business degrees or certifications.
Job Application Toolkit
Ace your application with our purpose-built resources:
Global Line Leader Opportunities
Line Leaders manage production flows and teams across diverse manufacturing sectors globally. International demand for this role remains stable, especially in rapidly industrializing economies and countries with strong export-oriented manufacturing. Cultural differences in team management and regulatory adherence, like safety standards, significantly impact international operations. Professionals seek global roles for career advancement, exposure to new technologies, and higher earning potential in specific markets. No universal international certifications exist, but Six Sigma or Lean Manufacturing certifications enhance global mobility.
Global Salaries
Line Leader salaries vary significantly by region and industry. In North America, a Line Leader typically earns between $45,000 and $65,000 USD annually in the USA or $40,000 to $60,000 CAD in Canada. European salaries range from €30,000 to €50,000 in Germany or France, equivalent to $32,000 to $54,000 USD, while in Eastern Europe, such as Poland, salaries might be €15,000 to €25,000 ($16,000 to $27,000 USD).
Asia-Pacific regions show diverse ranges. In Japan, a Line Leader might earn ¥3,500,000 to ¥5,500,000 ($23,000 to $37,000 USD), while in Australia, salaries are AUD 60,000 to AUD 80,000 ($40,000 to $53,000 USD). Latin American countries like Mexico typically offer MXN 180,000 to MXN 300,000 ($10,000 to $17,000 USD). These figures reflect base salaries and do not include overtime or production bonuses.
Cost of living impacts purchasing power. A higher salary in North America or Western Europe might align with higher expenses for housing and daily necessities. Conversely, lower salaries in parts of Asia or Latin America may offer better purchasing power if local living costs are substantially lower. Salary structures also differ; European countries often include more robust social benefits, like extensive vacation time and public healthcare, which are not always standard in North American compensation packages.
Tax implications vary widely; countries like Germany have higher income tax rates but provide comprehensive social services, while others, like the UAE, have no income tax. Experience and specialized skills, such as Lean Manufacturing or automation expertise, generally command higher compensation globally. Some multinational corporations may have internal pay scales for Line Leaders, ensuring a degree of consistency across their international operations, though local market adjustments always apply.
Remote Work
International remote work for a Line Leader is generally not feasible due to the hands-on nature of the role. Line Leaders must be physically present on the factory floor to oversee production, manage teams, and address immediate operational issues. This role requires direct supervision of machinery and personnel, which cannot be effectively performed remotely.
Some administrative tasks, like data analysis or report generation, could theoretically be done off-site. However, these are minor components of a Line Leader's core responsibilities. Therefore, the concept of a 'digital nomad' or fully remote international work does not apply to this specific profession. Employers hiring Line Leaders internationally expect full on-site presence, aligning with the operational demands of manufacturing environments.
Visa & Immigration
Line Leaders seeking international roles typically apply for skilled worker visas. Popular destination countries for manufacturing roles include Germany, Canada, Australia, and the USA. Each country has specific requirements. For instance, Germany's skilled worker visa often requires a recognized vocational qualification and a job offer. Canada's Express Entry system considers factors like age, education, language proficiency, and work experience. Australia's skilled migration program also assesses points for similar criteria, often requiring a skills assessment.
Education credential recognition is crucial; vocational qualifications or diplomas obtained in one country may need official assessment for equivalency in the target country. Professional licensing is not usually required for Line Leaders, but industry-specific certifications (e.g., in safety or quality control) are beneficial. Visa timelines vary from a few months to over a year, depending on the country and application backlog.
Pathways to permanent residency exist in many countries for skilled workers after a specified period of employment, often ranging from two to five years. Language requirements, such as English for Canada or Australia, or German for Germany, are common and often necessitate official test results. Some countries may offer expedited processing for roles in high-demand sectors, though Line Leader is not typically on such lists. Family visas for spouses and dependents are generally available concurrently with the primary applicant's visa.
2025 Market Reality for Line Leaders
Understanding current market conditions is critical for line leaders. The manufacturing landscape has transformed significantly from 2023 to 2025, driven by post-pandemic shifts and the accelerating integration of AI.
Broader economic factors, such as inflation and supply chain stability, directly influence production volumes and, consequently, the demand for supervisory roles. Market realities for line leaders vary considerably by industry, company size, and geographic location, impacting job availability and career progression.
Current Challenges
Line leaders face increased competition, especially for roles in stable manufacturing sectors. Automation and AI tools improve line efficiency, sometimes reducing the need for multiple supervisory layers. Economic uncertainty can slow production and hiring.
A mismatch exists between traditional line leader skills and the new demands of tech-integrated production environments. Job searches can take longer now, particularly without experience in advanced manufacturing.
Growth Opportunities
Strong opportunities exist for line leaders in advanced manufacturing sectors, including aerospace, medical devices, and specialized electronics. These industries demand precise oversight and technological proficiency.
Emerging roles like 'Automation Line Supervisor' or 'Data-Driven Production Lead' offer growth. Line leaders who develop expertise in robotics, industrial IoT, and predictive maintenance gain a competitive edge. Certifications in these areas or in process optimization are highly valued.
Underserved markets in rural areas with new manufacturing plants may offer less competition. Strategic career moves involve targeting companies investing heavily in smart factory initiatives. Professionals with a blend of traditional leadership and modern tech skills are well-positioned for success.
Sectors like sustainable manufacturing and personalized production are expanding. Investing in specialized training now can lead to better long-term prospects, even amidst broader market challenges.
Current Market Trends
Hiring for line leaders shows stable demand in essential manufacturing sectors like food processing and pharmaceuticals. However, the overall pace of hiring has moderated compared to the post-pandemic surge. Companies prioritize efficiency and cost control, impacting hiring decisions.
Generative AI and automation are redefining production lines. Line leaders now need skills in overseeing automated processes, interpreting data from smart machinery, and troubleshooting advanced systems. Employers increasingly seek candidates who understand Lean manufacturing principles and Six Sigma methodologies.
Salary growth for line leaders remains modest, reflecting a balance between demand and the available talent pool. Market saturation is evident at entry-level supervisory roles without specialized tech or data skills. Remote work normalization does not significantly impact this role, as it requires on-site presence.
Geographic variations are significant; areas with strong manufacturing hubs like the Midwest or Southeast continue to offer more opportunities. Seasonal hiring patterns are less pronounced, but economic downturns can lead to temporary hiring freezes in consumer goods manufacturing.
Emerging Specializations
Technological advancements and evolving industry demands are continuously reshaping the role of a Line Leader, creating new specialization opportunities. Early positioning in these emerging areas is crucial for career advancement in 2025 and beyond. Professionals who proactively adapt their skills to these future-oriented niches often command premium compensation and experience accelerated career growth.
While established specializations remain valuable, focusing on emerging areas offers a strategic advantage. These cutting-edge fields are currently gaining momentum but are not yet oversaturated, providing a chance to become an early expert. Typically, it takes 3-5 years for a truly emerging specialization to become mainstream and generate a significant number of job opportunities, making foresight critical.
Pursuing cutting-edge specializations involves a balance of risk and reward. While they promise higher growth and compensation, they also require commitment to continuous learning and adaptation to rapidly changing environments. However, the potential for impactful contributions and leadership in next-generation operational frameworks often outweighs these considerations.
Smart Automation Line Leader
Circular Economy Line Leader
Predictive Analytics Line Leader
Additive Manufacturing Line Leader
OT Cybersecurity Line Leader
Pros & Cons of Being a Line Leader
Making an informed career choice requires understanding both the positive aspects and the inherent challenges of a profession. A Line Leader's experience varies greatly based on the specific industry, company culture, and the products being handled. What one person considers a benefit, another might see as a drawback, depending on their personal values and work preferences. Furthermore, the demands and opportunities of this role can shift as one gains more experience or moves between different operational settings. This assessment aims to provide a realistic overview, helping individuals set appropriate expectations and determine if this path aligns with their career aspirations.
Pros
Direct impact on production and efficiency provides a sense of accomplishment, as you directly influence the output and quality of the operational line.
Develops strong leadership and team management skills by overseeing a group of workers, delegating tasks, and ensuring smooth collaboration on the production floor.
Hands-on problem-solving opportunities arise daily, allowing you to troubleshoot operational issues, optimize processes, and implement immediate solutions.
Stable employment in various industries, including manufacturing, logistics, and food production, ensures consistent demand for skilled operational leadership.
Offers a clear entry point into management for individuals with strong operational experience, often serving as a stepping stone to higher supervisory roles.
Acquisition of diverse technical knowledge related to specific machinery, production processes, and quality control standards within your particular industry sector.
Regular interaction with different departments, such as quality control, maintenance, and supply chain, provides a holistic view of the business operations and fosters cross-functional understanding.
Cons
High-pressure environment due to direct responsibility for production targets and quality, which can lead to significant stress when deadlines are tight or issues arise.
Irregular and long hours are common, especially in manufacturing or logistics, where shifts may rotate, or overtime is required to meet production demands or fix unexpected problems.
Constant problem-solving for operational glitches, equipment malfunctions, or personnel issues means the role often involves reactive troubleshooting rather than proactive planning.
Limited autonomy in decision-making, as Line Leaders typically operate within strict company policies and procedures, with little room for independent strategic choices.
Exposure to potentially hazardous work environments, depending on the industry, which may involve noise, machinery, or exposure to chemicals, requiring strict adherence to safety protocols.
Managing diverse personalities and skill levels among team members can be challenging, requiring constant mediation, motivation, and disciplinary action when necessary.
Career progression can be slow or limited, as advancement beyond Line Leader often requires significant additional education or a move into a different functional area.
Frequently Asked Questions
What are the typical entry requirements to become a Line Leader?
You typically need a few years of experience in a production or manufacturing environment, understanding the specific processes of the line you will lead. Many companies look for individuals who have demonstrated reliability, a strong work ethic, and an eagerness to learn. While a formal degree is not always required, some roles may prefer a high school diploma or equivalent, and on-the-job training is crucial.
How long does it usually take to transition into a Line Leader position from a production role?
Moving into a Line Leader role often takes 2-5 years of dedicated experience within a production setting. This timeline can vary based on your existing skills, the complexity of the manufacturing process, and opportunities for internal promotion. Developing a reputation for problem-solving and effective communication helps accelerate this transition.
What are the salary expectations for a Line Leader?
Salaries for Line Leaders vary significantly by industry, company size, and location, but generally range from $40,000 to $60,000 annually. This role often includes opportunities for overtime pay, which can increase overall earnings. Experience and demonstrated leadership in a specific sector can push compensation towards the higher end of this range.
What is the typical work-life balance like for a Line Leader, considering shift work?
Line Leader roles often involve shift work, including nights, weekends, or rotating schedules, depending on the production demands of the facility. This can impact work-life balance, requiring careful planning for personal commitments. While the work can be demanding, it also provides a clear structure and often consistent hours once your shift is set.
How secure is the job market for Line Leaders, and what factors influence it?
Job security for Line Leaders is generally stable, as these roles are essential for continuous production and operational efficiency. Demand for skilled leaders in manufacturing and production remains consistent. However, automation and technological advancements can change the nature of the role, requiring continuous learning and adaptation to new processes.
What are the common career advancement opportunities for a Line Leader?
Line Leaders have several avenues for career growth, including advancing to roles like Production Supervisor, Operations Manager, or Quality Control Manager. Developing strong leadership, problem-solving, and process improvement skills are key for advancement. Pursuing additional certifications in lean manufacturing or Six Sigma can also enhance your career trajectory.
What are the biggest day-to-day challenges a Line Leader faces?
A primary challenge for Line Leaders is balancing production targets with maintaining quality and ensuring team safety. You must effectively manage personnel, resolve interpersonal conflicts, and troubleshoot operational issues quickly to minimize downtime. Motivating your team and communicating effectively across different departments are also critical for success.
Is remote work a possibility for Line Leaders?
Line Leader roles are inherently on-site, as they require direct supervision of production lines and immediate problem-solving. Remote work options are extremely rare for this position because of the hands-on nature of managing a physical production process and leading a team in person. Expect to be present at the manufacturing facility for all shifts.
Related Careers
Explore similar roles that might align with your interests and skills:
Line Operator
A growing field with similar skill requirements and career progression opportunities.
Explore career guideProduction Manager
A growing field with similar skill requirements and career progression opportunities.
Explore career guideProduction Supervisor
A growing field with similar skill requirements and career progression opportunities.
Explore career guideProduction Team Leader
A growing field with similar skill requirements and career progression opportunities.
Explore career guidePlant Chief
A growing field with similar skill requirements and career progression opportunities.
Explore career guideAssess your Line Leader readiness
Understanding where you stand today is the first step toward your career goals. Our Career Coach helps identify skill gaps and create personalized plans.
Skills Gap Analysis
Get a detailed assessment of your current skills versus Line Leader requirements. Our AI Career Coach identifies specific areas for improvement with personalized recommendations.
See your skills gapCareer Readiness Assessment
Evaluate your overall readiness for Line Leader roles with our AI Career Coach. Receive personalized recommendations for education, projects, and experience to boost your competitiveness.
Assess your readinessSimple pricing, powerful features
Upgrade to Himalayas Plus and turbocharge your job search.
Himalayas
Himalayas Plus
Himalayas Max
Find your dream job
Sign up now and join over 100,000 remote workers who receive personalized job alerts, curated job matches, and more for free!
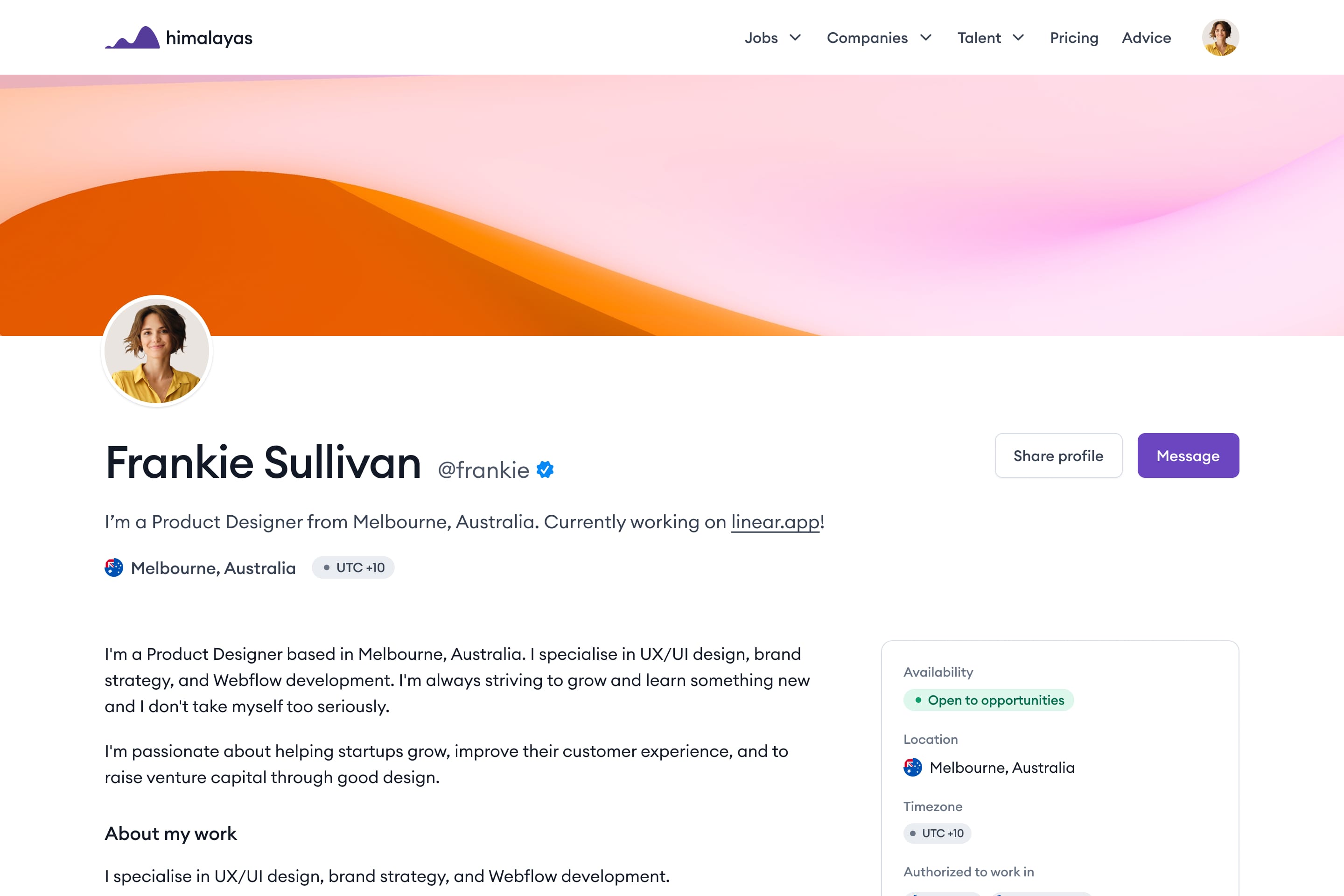