Complete Inventory Coordinator Career Guide
Inventory Coordinators are the unsung heroes of efficient operations, ensuring that businesses have the right products in the right place at the right time. They meticulously manage stock levels, prevent costly overstocking or shortages, and optimize supply chains, directly impacting profitability and customer satisfaction. This role offers a vital entry point into logistics and supply chain management, demanding sharp organizational skills and a keen eye for detail.
Key Facts & Statistics
Median Salary
$47,440 USD
(U.S. national median, May 2023, BLS)
Range: $30k - $65k+ USD
Growth Outlook
1%
as fast as average (2022-2032)
Annual Openings
≈33,000
openings annually
Top Industries
Typical Education
High school diploma or equivalent, though some positions prefer an associate's degree or certificate in logistics or supply chain management
What is an Inventory Coordinator?
An Inventory Coordinator is a specialist responsible for the accurate tracking, management, and control of a company's goods and materials within a warehouse or distribution center. This role ensures that products are properly received, stored, and dispatched, maintaining precise records of stock levels and movements. They are critical to operational efficiency, helping to prevent losses from spoilage, damage, or obsolescence, and ensuring that products are available when needed by customers or production lines.
Unlike a general Warehouse Associate who primarily handles physical movement, or a Supply Chain Manager who focuses on strategic planning, an Inventory Coordinator's core responsibility lies in the data integrity and physical organization of inventory. They serve as the direct link between the physical stock and the digital records, often identifying and resolving discrepancies that impact financial reporting and order fulfillment. Their work directly supports sales, purchasing, and production by providing reliable inventory data.
What does an Inventory Coordinator do?
Key Responsibilities
- Maintain accurate inventory records by performing regular cycle counts and full physical inventories.
- Receive incoming shipments, verify contents against purchase orders, and properly store items in designated locations.
- Prepare outgoing orders for shipment, ensuring correct items and quantities are picked and packaged according to specifications.
- Monitor stock levels to prevent shortages or overstocking, initiating reorder requests as needed.
- Investigate and resolve inventory discrepancies, identifying root causes to improve accuracy.
- Coordinate with purchasing, sales, and warehouse teams to ensure smooth material flow and order fulfillment.
Work Environment
Inventory Coordinators primarily work in a warehouse or distribution center environment, which can range from temperature-controlled facilities to standard industrial settings. The work involves a mix of desk-based tasks for data entry and analysis, and active time on the warehouse floor for counting, receiving, and picking. Collaboration with warehouse staff, purchasing agents, and sales teams is frequent. The pace can be steady with routine tasks, but also fast-paced during peak seasons or when resolving urgent discrepancies. While most work is on-site, some larger organizations might offer hybrid models for administrative aspects. Physical activity, including lifting and moving items, is often required.
Tools & Technologies
Inventory Coordinators regularly use Warehouse Management Systems (WMS) like SAP, Oracle, or NetSuite to track stock, manage orders, and record movements. They also utilize Enterprise Resource Planning (ERP) software for integrated business processes. Handheld barcode scanners and RFID readers are essential for efficient data capture during receiving, picking, and counting processes. Spreadsheets, typically Microsoft Excel, are used for ad-hoc analysis, reporting, and managing smaller inventory sets. Communication tools such as email and internal messaging platforms are vital for coordinating with various departments.
Inventory Coordinator Skills & Qualifications
The Inventory Coordinator role is crucial for maintaining accurate stock levels and ensuring efficient supply chain operations. Qualifications for this position are structured around a blend of practical experience, foundational education, and specific technical competencies. Entry-level roles often prioritize strong organizational skills and a willingness to learn, while senior positions demand a deeper understanding of inventory management systems and supply chain analytics.
Requirements vary significantly by company size and industry. Large corporations with complex supply chains, such as manufacturing or retail giants, often prefer candidates with formal degrees or extensive experience with enterprise resource planning (ERP) systems. Smaller businesses or local distribution centers may place more emphasis on practical experience, attention to detail, and the ability to adapt to less formalized processes. Geographic location can also influence requirements, with certain regions emphasizing specific certifications related to logistics or warehousing.
Formal education, like an associate's or bachelor's degree in supply chain management or business, provides a strong theoretical foundation but is not always a strict prerequisite. Practical experience in a warehouse, logistics, or retail environment often holds equal or greater value, especially for those demonstrating a strong track record of accuracy and efficiency. Certifications from bodies like APICS (now ASCM) or the Council of Supply Chain Management Professionals (CSCMP) significantly enhance a candidate's profile, signaling specialized knowledge and commitment to the field. These certifications are increasingly important as the industry evolves towards more data-driven and automated inventory practices.
The skill landscape for Inventory Coordinators is continuously evolving. There is a growing demand for proficiency in inventory management software, data analysis, and even basic automation tools. Manual tracking and paper-based systems are declining in relevance. The balance between breadth and depth of skills shifts with career stage; entry-level roles require broad foundational understanding, while senior coordinators need deep expertise in specific inventory optimization techniques or system integrations. Common misconceptions include viewing the role as purely administrative; instead, it requires strategic thinking, problem-solving, and a keen eye for process improvement.
Education Requirements
Technical Skills
- Inventory Management Software (e.g., SAP, Oracle, NetSuite, Zoho Inventory)
- Warehouse Management Systems (WMS) proficiency for tracking goods movement
- Data Entry and Accuracy: High proficiency in inputting and verifying inventory data
- Spreadsheet Software (Microsoft Excel): Advanced functions like VLOOKUP, pivot tables for analysis and reporting
- Barcode Scanning and RFID Technology: Operational knowledge and troubleshooting
- Cycle Counting and Physical Inventory Procedures: Practical experience and understanding of methodologies
- Demand Forecasting Basics: Ability to interpret sales data to anticipate future inventory needs
- Logistics and Shipping Procedures: Understanding of inbound/outbound processes and documentation
- Basic Database Querying (SQL): Ability to pull specific inventory reports or troubleshoot data (beneficial for larger systems)
- Safety and Compliance Regulations: Adherence to warehousing and handling standards (e.g., OSHA)
Soft Skills
- Attention to Detail: Critical for accurately tracking inventory, identifying discrepancies, and preventing costly errors.
- Problem-Solving: Essential for resolving inventory discrepancies, optimizing storage, and addressing supply chain bottlenecks.
- Organizational Skills: Necessary for maintaining a structured warehouse, managing documentation, and ensuring efficient retrieval of goods.
- Time Management: Important for prioritizing tasks, meeting deadlines for shipments, and managing multiple inventory counts simultaneously.
- Communication Skills: Crucial for coordinating with suppliers, warehouse staff, sales teams, and management regarding stock levels and issues.
- Adaptability: Key for adjusting to changing inventory demands, new software systems, and unexpected supply chain disruptions.
- Proactive Thinking: Valuable for anticipating future inventory needs, identifying potential stockouts, and suggesting improvements to processes.
- Integrity: Important for handling valuable goods and maintaining accurate records without manipulation, ensuring trust in inventory data.
How to Become an Inventory Coordinator
Becoming an Inventory Coordinator involves various pathways, depending on your background and the industry. Many entry-level positions do not require a bachelor's degree, often preferring a high school diploma or GED coupled with relevant experience or certifications. Career changers from retail, logistics, or administrative roles can often leverage their existing organizational and data management skills.
The timeline for securing an Inventory Coordinator role can range from three months to over a year. A candidate with some relevant experience or a vocational certificate might find a position relatively quickly, while a complete beginner may need more time to acquire foundational skills and build a network. Entry strategies also vary significantly by company size; large corporations often have structured training programs, whereas smaller businesses might offer more hands-on learning from day one.
Networking within supply chain and logistics communities, attending industry webinars, and connecting with professionals on platforms like LinkedIn are crucial. These connections can provide insights into unadvertised roles and mentorship opportunities. Focus on highlighting practical skills in inventory management software, data analysis, and problem-solving, as these are often more valued than a specific degree.
Step 1
Step 2
Step 3
Step 4
Step 5
Step 6
Step 7
Education & Training Needed to Become an Inventory Coordinator
The educational landscape for an Inventory Coordinator emphasizes practical skills and operational knowledge over advanced theoretical degrees. While a bachelor's degree in supply chain management or business administration can be beneficial, it is not always a strict requirement. Many successful Inventory Coordinators start with an associate's degree or a high school diploma combined with relevant certifications and on-the-job training. Four-year degrees typically cost $40,000-$100,000+ and take four years. Associate's degrees range from $10,000-$30,000 and take two years. Certifications often cost $500-$5,000 and can be completed in a few weeks to several months.
Employer acceptance of credentials varies; larger corporations might prefer candidates with a degree, while small to medium-sized businesses often prioritize experience and relevant certifications. Practical experience with inventory management systems (IMS), enterprise resource planning (ERP) software, and strong analytical skills are highly valued. Continuous learning is essential, especially regarding new technologies and industry best practices in logistics and supply chain. Educational needs vary by company size and the complexity of inventory managed. For instance, a coordinator in manufacturing might need more specialized training than one in retail.
The role of practical experience is paramount. Many entry-level positions offer on-the-job training, allowing individuals to gain hands-on experience with inventory tracking, stock rotation, and order fulfillment. Online courses and self-study modules provide flexible, cost-effective ways to acquire specific skills, often ranging from $50 to $500 per course and taking 10-40 hours to complete. These options are excellent for supplementing existing knowledge or preparing for certification exams. Industry-specific accreditations from organizations like APICS (now ASCM) or ISM are widely recognized and can significantly boost career prospects, demonstrating a commitment to professional standards and a strong understanding of supply chain principles.
Inventory Coordinator Salary & Outlook
Compensation for an Inventory Coordinator varies significantly based on several key factors. Geographic location plays a crucial role; major metropolitan areas with high costs of living and significant logistics hubs often offer higher salaries than rural regions. Regional demand for skilled inventory professionals also impacts earning potential.
Experience levels and specialized skills directly influence compensation. A Junior Inventory Coordinator typically focuses on basic stock management, while a Senior Inventory Coordinator handles complex inventory systems, demand forecasting, and vendor relations. Expertise in specific inventory software, supply chain analytics, or lean inventory practices can command premium compensation.
Total compensation packages extend beyond base salary. Many roles include performance bonuses tied to inventory accuracy, cost reduction, or efficiency improvements. Benefits packages, including health insurance, retirement contributions like 401k matching, and paid time off, significantly contribute to overall value. Some companies also offer professional development allowances for certifications in supply chain management.
Industry-specific trends also affect pay. E-commerce and manufacturing sectors, with their complex and high-volume inventory needs, often offer more competitive salaries. Remote work opportunities for Inventory Coordinators are less common due to the hands-on nature of the role, but some planning or analytical positions may offer location flexibility, potentially impacting geographic salary expectations. While the figures provided are for the USD market, international markets will show variations based on local economic conditions and industry maturity.
Salary by Experience Level
Level | US Median | US Average |
---|---|---|
Junior Inventory Coordinator | $42k USD | $45k USD |
Inventory Coordinator | $52k USD | $55k USD |
Senior Inventory Coordinator | $65k USD | $68k USD |
Inventory Supervisor | $75k USD | $78k USD |
Inventory Manager | $90k USD | $95k USD |
Market Commentary
The job market for Inventory Coordinators shows steady demand, driven by the increasing complexity of global supply chains and the growth of e-commerce. Businesses across retail, manufacturing, logistics, and healthcare rely heavily on efficient inventory management to control costs and ensure product availability. The U.S. Bureau of Labor Statistics projects a stable outlook for logistics and supply chain professionals, with inventory management being a core component.
Emerging opportunities for Inventory Coordinators are linked to technological advancements. The adoption of AI, machine learning, and advanced analytics for demand forecasting and inventory optimization is transforming the role. Coordinators who can interpret data, manage automated systems, and adapt to new software platforms will find themselves in higher demand. There is a growing need for professionals skilled in managing omnichannel inventory for seamless online and in-store experiences.
Supply and demand dynamics for this role are generally balanced. While there is consistent demand, the pool of qualified candidates with specialized software skills or analytical capabilities may be smaller, creating opportunities for those with advanced training. Future-proofing this career involves continuous learning in supply chain technology and data analysis. Automation may handle routine tasks, but the need for human oversight, problem-solving, and strategic decision-making in inventory management will remain critical.
Geographic hotspots for Inventory Coordinators often align with major distribution centers, manufacturing hubs, and port cities. The role is relatively recession-resistant as businesses always need to manage their assets efficiently, regardless of economic cycles. However, economic downturns can shift focus towards cost reduction and lean inventory practices, requiring adaptability from professionals in this field.
Inventory Coordinator Career Path
Career progression for an Inventory Coordinator involves developing a deep understanding of supply chain logistics, inventory management systems, and operational efficiency. Professionals can advance along an individual contributor (IC) track, focusing on specialized inventory analytics and optimization, or pursue a management track, leading teams and overseeing broader inventory operations.
Advancement speed depends on performance, the complexity of inventory systems managed, and the size and industry of the company. Larger corporations often have more structured progression paths, while smaller businesses or startups might offer faster advancement but require a broader skillset. Lateral moves into procurement, logistics, or warehouse management are common, expanding an individual's supply chain expertise.
Continuous learning in inventory software, data analysis, and lean principles is crucial. Building a strong professional network and seeking mentorship from experienced supply chain professionals also accelerates growth. Certifications in supply chain management (e.g., APICS) can mark significant milestones and validate expertise, opening doors to higher-level roles and alternative pathways in supply chain consulting or systems implementation.
Junior Inventory Coordinator
0-2 yearsKey Focus Areas
Inventory Coordinator
2-4 yearsKey Focus Areas
Senior Inventory Coordinator
4-7 yearsKey Focus Areas
Inventory Supervisor
7-10 yearsKey Focus Areas
Inventory Manager
10+ yearsKey Focus Areas
Junior Inventory Coordinator
0-2 yearsAssists with daily inventory counts, data entry, and basic reconciliation tasks. Supports the main Inventory Coordinator in maintaining accurate stock levels. Follows established procedures for inventory movement and storage. Works under direct supervision, primarily focusing on task execution.
Key Focus Areas
Develop foundational knowledge of inventory software and warehouse operations. Focus on accuracy in data entry and basic reconciliation tasks. Learn company-specific procedures for receiving, stocking, and shipping. Build strong attention to detail and organizational skills.
Inventory Coordinator
2-4 yearsManages daily inventory counts, conducts regular audits, and investigates discrepancies. Responsible for accurate data entry into inventory management systems. Coordinates with warehouse, purchasing, and sales teams to ensure optimal stock levels. Operates with moderate autonomy, handling routine inventory challenges.
Key Focus Areas
Master inventory control systems and advanced reconciliation techniques. Develop problem-solving skills for discrepancies and stock variances. Improve communication with warehouse staff and other departments. Start understanding the impact of inventory on sales and operations.
Senior Inventory Coordinator
4-7 yearsLeads complex inventory reconciliation projects and resolves significant discrepancies. Analyzes inventory data to identify trends, optimize stock levels, and minimize waste. Proposes and implements process improvements for inventory control. Provides guidance and training to junior team members, acting as a subject matter expert.
Key Focus Areas
Develop analytical skills to identify trends and optimize inventory levels. Focus on process improvement and implementing best practices in inventory management. Start mentoring junior staff and contribute to training materials. Understand demand forecasting principles.
Inventory Supervisor
7-10 yearsOversees a team of Inventory Coordinators, assigning tasks, monitoring performance, and providing coaching. Ensures adherence to inventory policies and procedures across the warehouse. Troubleshoots complex inventory issues and implements corrective actions. Contributes to operational planning and resource allocation for inventory activities.
Key Focus Areas
Cultivate leadership and team management skills. Focus on performance management, scheduling, and workflow optimization for the inventory team. Develop stronger communication and collaboration skills with cross-functional departments. Understand budgeting related to inventory operations.
Inventory Manager
10+ yearsManages the entire inventory department, including budgeting, strategic planning, and performance metrics. Develops and implements inventory control policies and procedures across the organization. Leads initiatives for inventory optimization, demand forecasting, and technology integration. Collaborates with senior leadership on supply chain strategy and vendor relationships, impacting overall business profitability.
Key Focus Areas
Develop strategic planning and budget management capabilities. Focus on advanced analytics, supply chain optimization, and technology adoption for inventory. Build strong stakeholder management and presentation skills. Pursue certifications in supply chain management or logistics.
Job Application Toolkit
Ace your application with our purpose-built resources:
Inventory Coordinator Resume Examples
Proven layouts and keywords hiring managers scan for.
View examplesInventory Coordinator Cover Letter Examples
Personalizable templates that showcase your impact.
View examplesTop Inventory Coordinator Interview Questions
Practice with the questions asked most often.
View examplesInventory Coordinator Job Description Template
Ready-to-use JD for recruiters and hiring teams.
View examplesGlobal Inventory Coordinator Opportunities
An Inventory Coordinator's role involves managing stock levels, optimizing supply chains, and ensuring efficient material flow across diverse industries globally. This profession translates well internationally, with consistent demand in manufacturing, retail, logistics, and e-commerce sectors worldwide. Global job market trends for 2025 show steady growth, driven by expanded international trade and complex supply networks. Professionals often consider international opportunities for career advancement and exposure to different market dynamics. Understanding international logistics standards and enterprise resource planning (ERP) systems aids global mobility in this field.
Global Salaries
Salary ranges for an Inventory Coordinator vary significantly by region and cost of living. In North America, particularly the United States, annual salaries typically range from $45,000 to $65,000 USD. Canadian roles offer CAD 40,000 to CAD 55,000. These figures often include benefits like health insurance and retirement plans. In Western Europe, countries like Germany and the Netherlands offer €35,000 to €50,000 (approximately $38,000 to $54,000 USD). Southern European nations like Spain or Italy might see €25,000 to €35,000 (around $27,000 to $38,000 USD), reflecting lower living costs.
Asia-Pacific markets present diverse compensation. Australia offers AUD 50,000 to AUD 70,000 (around $33,000 to $46,000 USD). Singapore's salaries range from SGD 3,500 to SGD 5,000 per month (approximately $31,000 to $44,000 USD annually), aligning with its higher cost of living. In Latin America, Brazil or Mexico might offer $15,000 to $25,000 USD equivalent annually, where purchasing power parity is crucial for understanding real value. Tax implications and take-home pay differ greatly; for example, European countries often have higher social security contributions, while North America has varying state/provincial taxes.
Experience and specific industry knowledge significantly influence compensation. An Inventory Coordinator with five years of experience and specialized ERP system expertise (e.g., SAP, Oracle) can command salaries at the higher end of these ranges. International pay scales do not typically standardize for this role, but multinational corporations might offer internal compensation frameworks that account for global mobility. Understanding local benefits packages, which can include extensive vacation time in Europe or performance bonuses in Asia, is essential for a complete salary picture.
Remote Work
International remote work for an Inventory Coordinator is limited due to the inherent hands-on nature of the role, which often requires physical presence in warehouses or distribution centers. However, some companies with highly digitized inventory systems or those managing global stock remotely may offer hybrid or occasional remote options for specific tasks like data analysis, reporting, or vendor communication. Such opportunities are more common in larger, multinational logistics or e-commerce firms.
Legal and tax implications for international remote work remain complex. Individuals must understand local labor laws, tax residency rules, and social security obligations in both their home and host countries. Time zone differences can pose challenges for real-time collaboration with on-site teams. Digital nomad visas are generally not suitable for this role given its typical operational requirements.
Companies offering international remote work for similar roles often have specific global hiring policies and provide necessary equipment. Salary expectations for remote roles might adjust based on the employee's location, reflecting a geographic arbitrage model where pay aligns with the cost of living in the remote worker's country. Platforms like LinkedIn or industry-specific job boards occasionally list 'remote' or 'hybrid' inventory roles, though these are typically within a specific country or region.
Visa & Immigration
Common visa categories for Inventory Coordinators typically fall under skilled worker visas. Popular destination countries include Canada, Australia, Germany, and the United Kingdom. These countries often require a job offer from an employer and proof of relevant experience or qualifications. For instance, Canada's Express Entry system or Australia's Skilled Migration program assess points based on age, education, language proficiency, and work experience. The UK's Skilled Worker visa requires sponsorship from a licensed employer.
Education credential recognition is crucial; applicants often need a diploma or degree in supply chain management, logistics, or a related field. Professional licensing is generally not required for Inventory Coordinators, but certifications like APICS (Association for Supply Chain Management) can enhance an application. Visa timelines vary, ranging from a few weeks to several months, depending on the country and application volume. The process typically involves submitting an online application, providing documentation, and attending an interview.
Pathways to permanent residency or citizenship can exist after several years of continuous skilled employment, depending on the country's immigration policies. Language requirements, such as IELTS for English-speaking countries or Goethe-Institut exams for Germany, are often mandatory. Some countries may offer profession-specific immigration advantages if inventory management is listed on their in-demand occupation lists. Practical considerations include securing accommodation and understanding local healthcare systems; family visas for dependents are usually available once the primary applicant's visa is approved.
2025 Market Reality for Inventory Coordinators
Understanding current market conditions is crucial for Inventory Coordinators. The role has transformed significantly since 2023, influenced by post-pandemic supply chain disruptions and the rapid integration of AI and automation.
Broader economic factors, including inflation and consumer spending shifts, directly impact inventory levels and demand for this position. Market realities vary by industry; for instance, e-commerce requires different skills than traditional retail. Geographic location and company size also play a role, with larger corporations often using more advanced systems. This analysis provides an honest assessment of current hiring realities.
Current Challenges
Inventory Coordinators face increased competition, particularly from candidates with stronger data analytics or supply chain software proficiencies. Automation tools are reducing the need for manual tracking, shifting expectations for the role.
Economic uncertainty causes companies to optimize inventory levels more aggressively, leading to fewer new coordinator positions. Companies prioritize efficiency, requiring coordinators to handle more complex tasks with fewer resources.
Growth Opportunities
Despite challenges, strong opportunities exist for Inventory Coordinators who adapt to technological shifts. Roles focusing on inventory analytics, supply chain optimization, or system integration are in high demand.
Emerging specializations include AI-powered inventory forecasting, drone-based inventory management, and blockchain-enabled supply chain transparency. Coordinators who proactively learn these technologies gain a significant competitive edge.
Underserved markets often include smaller manufacturers or specialized distributors who are just beginning to implement advanced inventory systems. These companies need coordinators to help with implementation and initial management.
Certifications in specific inventory management software (e.g., SAP, Oracle, NetSuite) or supply chain analytics are highly valued. Experience with data visualization tools like Tableau or Power BI also provides a competitive advantage. Strategic career moves involve targeting industries undergoing rapid digital transformation, such as advanced manufacturing or specialized e-commerce.
Current Market Trends
Demand for Inventory Coordinators remains stable, but the nature of the role is evolving. Companies are increasingly investing in advanced inventory management systems, including AI-driven forecasting and automated tracking.
This shift means employers seek coordinators who understand data analytics, can troubleshoot system issues, and manage automated workflows. Manual counting and basic data entry skills are less valued.
Economic conditions in 2024-2025 emphasize efficiency and cost reduction across supply chains. This translates to a focus on lean inventory practices, requiring coordinators to minimize stockouts while avoiding overstocking.
Salary growth for traditional Inventory Coordinator roles has slowed. However, those with specialized skills in supply chain software, data visualization, or predictive analytics command higher compensation. Market saturation exists at entry levels for candidates lacking technology proficiency.
Geographically, opportunities are strongest in major logistics hubs and areas with significant manufacturing or distribution centers. Remote work for this role is uncommon due to the hands-on nature of inventory oversight. Seasonal hiring patterns may occur around peak retail or manufacturing cycles, but core demand remains consistent.
Emerging Specializations
The field of inventory management is undergoing significant transformation, driven by advancements in automation, data analytics, and supply chain digitization. These technological shifts are creating entirely new specialization opportunities for Inventory Coordinators, moving beyond traditional stock-taking and order fulfillment.
Positioning oneself early in these emerging areas is crucial for career advancement and securing high-demand roles from 2025 onwards. Professionals who proactively develop expertise in these next-generation inventory practices often command premium compensation and experience accelerated career growth, as businesses prioritize efficiency and resilience in their supply chains.
While established inventory specializations remain relevant, the strategic advantage lies in understanding and adapting to these future-oriented niches. These emerging areas typically take 3-5 years to become mainstream, offering a window for early adopters to build deep expertise. Pursuing cutting-edge specializations carries inherent risks, but the potential for significant professional reward and competitive differentiation outweighs them for forward-thinking individuals.
A balanced approach involves maintaining foundational inventory skills while dedicating effort to mastering the tools and concepts of these nascent fields. This strategy ensures both immediate employability and long-term career resilience in an evolving global supply chain landscape.
Automated Warehouse Inventory Specialist
This specialization focuses on managing inventory within highly automated warehouses and distribution centers, leveraging robotic systems, automated storage and retrieval systems (AS/RS), and IoT sensors. Inventory Coordinators in this role optimize inventory flow in conjunction with automated equipment, troubleshoot system discrepancies, and ensure seamless integration between physical stock and digital control systems. This area is critical as businesses invest heavily in automation to reduce labor costs and improve accuracy.
Predictive Inventory Analyst
This specialization involves using advanced data analytics and machine learning tools to predict demand fluctuations, optimize stock levels, and minimize waste. Inventory Coordinators in this role analyze historical data, market trends, and external factors to forecast future inventory needs with high precision. They develop and refine predictive models to ensure optimal stock availability while reducing carrying costs and preventing obsolescence.
Circular Economy Inventory Coordinator
This area focuses on managing inventory for circular economy models, where products and materials are reused, repaired, or recycled to minimize waste. Inventory Coordinators in this role track reverse logistics, manage returned goods, and ensure materials are effectively re-entered into the supply chain. They play a key role in optimizing inventory for sustainability initiatives and reducing environmental impact.
Inventory Data Security Specialist
This specialization involves ensuring the security and integrity of inventory data across the supply chain, particularly in the context of increasing cyber threats. Inventory Coordinators in this role implement protocols to protect sensitive inventory information, prevent data breaches, and ensure compliance with data privacy regulations. They work to identify vulnerabilities in inventory tracking systems and secure against tampering or unauthorized access, which is vital for maintaining operational trust and preventing financial loss.
Omnichannel Inventory Manager
This specialization focuses on managing inventory across multiple channels, including e-commerce, brick-and-mortar stores, and third-party marketplaces, to provide a seamless customer experience. Inventory Coordinators in this role optimize stock allocation across diverse sales points, manage real-time inventory visibility, and coordinate fulfillment strategies to meet omnichannel demand. They ensure consistent product availability and efficient order processing regardless of the customer's shopping method.
Pros & Cons of Being an Inventory Coordinator
Understanding the advantages and challenges of any career is crucial for making informed decisions. The experience of an Inventory Coordinator can vary significantly based on the company's size, industry, and specific operational demands. What might be a pro for one individual, like predictable routines, could be a con for another who thrives on constant change. Similarly, early career stages might involve more hands-on tasks, while senior roles could shift towards strategic planning. This assessment offers an honest look at both the benefits and realistic challenges of this profession, helping you set appropriate expectations and determine if it aligns with your personal values and long-term aspirations.
Pros
Stable job demand exists across various industries, including retail, manufacturing, and logistics, as every business handling physical goods requires efficient inventory management.
Structured work environment with clear daily tasks provides predictability, which can be beneficial for individuals who prefer routine and organized workflows.
Opportunities for hands-on problem-solving arise regularly, such as identifying discrepancies, optimizing storage layouts, and improving tracking processes to enhance efficiency.
Development of practical skills in logistics and supply chain management is inherent in the role, providing a foundational understanding that is transferable to broader operational positions.
Direct impact on business efficiency and profitability is evident, as effective inventory coordination reduces waste, prevents stockouts, and optimizes cash flow for the company.
Entry-level accessibility makes this a viable career path for individuals with varying educational backgrounds, as many positions prioritize practical skills and a strong work ethic over advanced degrees.
Team collaboration is frequent, as inventory coordinators often work closely with warehouse staff, purchasing, sales, and logistics teams to ensure smooth operations and timely order fulfillment.
Cons
Repetitive tasks can lead to monotony, as daily duties often involve scanning, counting, and organizing items in a similar fashion, which may not appeal to those seeking dynamic intellectual challenges.
Physical demands are common, requiring frequent lifting, bending, and standing for extended periods, especially in warehouse environments, which can be physically taxing over time.
High pressure during peak seasons or unexpected demand spikes can lead to stressful periods, as inventory coordinators must ensure accuracy and timely movement of goods under tight deadlines.
Limited direct career progression within the inventory coordinator role itself means advancement often requires moving into broader supply chain management, logistics, or supervisory positions.
Exposure to varying temperatures and conditions is typical in warehouses or storage facilities, which can be uncomfortable during extreme weather, affecting daily working conditions.
Potential for errors and discrepancies causes stress, as even small mistakes in inventory counts or data entry can lead to significant financial losses or operational disruptions for the company.
Reliance on technology and systems means that system malfunctions or software issues can disrupt workflow and require troubleshooting skills that are not always part of the core job description.
Frequently Asked Questions
Inventory Coordinators face distinct challenges managing stock accuracy and optimizing supply chains. This section addresses common questions about entering this role, from mastering inventory software to ensuring efficient product flow and minimizing waste.
What are the typical educational and experience requirements to become an Inventory Coordinator?
An Inventory Coordinator typically requires a high school diploma or GED, though an associate's degree in logistics, supply chain management, or business administration is often preferred. Practical experience in warehousing, retail, or a related field that involves stock handling is highly valued. Strong computer skills, especially with spreadsheets and inventory management software, are essential for success.
Can I become an Inventory Coordinator without any prior experience in logistics or warehousing?
While you can start as an Inventory Coordinator without prior experience, gaining some exposure to warehouse operations, shipping/receiving, or retail stock management significantly helps. Many entry-level roles provide on-the-job training, but demonstrating basic understanding of inventory principles and strong organizational skills will make you a more competitive candidate. Consider volunteer work or part-time roles in a relevant environment to build foundational experience.
How long does it typically take to become job-ready as an Inventory Coordinator if I'm starting from scratch?
The time it takes to become job-ready for an Inventory Coordinator role varies. If you have relevant experience or a degree, you might be ready immediately. For those starting from scratch, completing an associate's degree could take two years. Alternatively, gaining a few months to a year of experience in a related entry-level position, like a warehouse associate, can build the necessary skills and understanding to transition into a coordinator role.
What are the typical salary expectations for an Inventory Coordinator?
The salary for an Inventory Coordinator can range widely based on location, industry, and experience. Entry-level positions might start around $35,000 to $45,000 annually. With a few years of experience and specialized skills, salaries can increase to $50,000 to $65,000 or more. Companies with complex inventory operations or in high-demand sectors often offer higher compensation.
What is the typical work-life balance and daily routine like for an Inventory Coordinator?
Work-life balance for an Inventory Coordinator varies by employer and industry. Many roles are standard Monday-Friday, 9-5 positions, but some industries like retail or manufacturing may require occasional evening, weekend, or on-call shifts, especially during peak seasons or inventory counts. The role can be desk-based for data entry and analysis, but also involves time on the warehouse floor for physical counts and inspections, requiring a mix of sedentary and active work.
Is the Inventory Coordinator role secure given increasing automation in logistics?
The career outlook for Inventory Coordinators remains stable, driven by the ongoing need for efficient supply chains across all industries. Automation is changing some aspects of the role, but the need for human oversight, problem-solving, and strategic decision-making regarding inventory flow ensures continued demand. Professionals who adapt to new technologies and data analytics tools will find strong job security and growth opportunities.
What are the typical career advancement opportunities for an Inventory Coordinator?
Career growth for an Inventory Coordinator often involves moving into more specialized or supervisory roles. You could advance to an Inventory Manager, Logistics Coordinator, Supply Chain Analyst, or even a Purchasing Agent. Gaining certifications in supply chain management (e.g., APICS CSCP or CPIM) and pursuing further education in logistics or business administration can significantly accelerate your career progression.
Can an Inventory Coordinator typically work remotely, or is it primarily an on-site role?
While some administrative tasks of an Inventory Coordinator can be done remotely, the nature of the role often requires a significant on-site presence. Physical inventory counts, inspecting goods, overseeing shipments, and direct collaboration with warehouse staff usually necessitate being present at the facility. Hybrid models that allow for some remote work for planning and reporting are becoming more common, but fully remote roles are rare for this position.
Related Careers
Explore similar roles that might align with your interests and skills:
Inventory Clerk
A growing field with similar skill requirements and career progression opportunities.
Explore career guideInventory Control Coordinator
A growing field with similar skill requirements and career progression opportunities.
Explore career guideInventory Controller
A growing field with similar skill requirements and career progression opportunities.
Explore career guideInventory Specialist
A growing field with similar skill requirements and career progression opportunities.
Explore career guideInventory Supervisor
A growing field with similar skill requirements and career progression opportunities.
Explore career guideAssess your Inventory Coordinator readiness
Understanding where you stand today is the first step toward your career goals. Our Career Coach helps identify skill gaps and create personalized plans.
Skills Gap Analysis
Get a detailed assessment of your current skills versus Inventory Coordinator requirements. Our AI Career Coach identifies specific areas for improvement with personalized recommendations.
See your skills gapCareer Readiness Assessment
Evaluate your overall readiness for Inventory Coordinator roles with our AI Career Coach. Receive personalized recommendations for education, projects, and experience to boost your competitiveness.
Assess your readinessSimple pricing, powerful features
Upgrade to Himalayas Plus and turbocharge your job search.
Himalayas
Himalayas Plus
Himalayas Max
Find your dream job
Sign up now and join over 100,000 remote workers who receive personalized job alerts, curated job matches, and more for free!
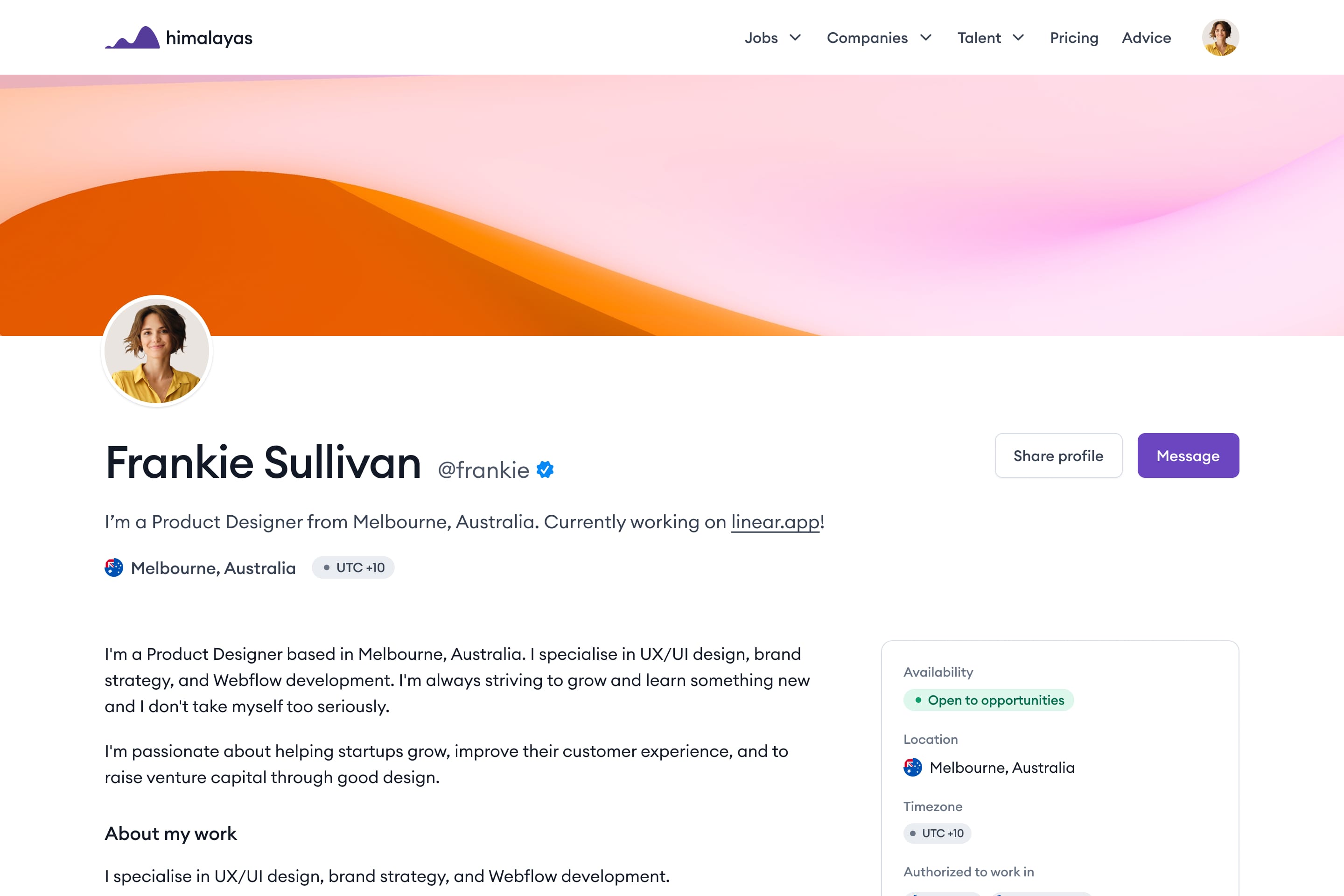