Complete Industrial Robotics Mechanic Career Guide
Industrial Robotics Mechanics are the unsung heroes of modern manufacturing, ensuring the automated systems that build everything from cars to consumer electronics operate flawlessly. This specialized role combines mechanical prowess with advanced diagnostic skills, keeping production lines running efficiently and minimizing costly downtime. It's a hands-on career vital to industrial innovation, offering stable demand and a clear path for skilled technicians.
Key Facts & Statistics
Median Salary
$64,240 USD
Range: $45k - $85k+ USD
Growth Outlook
13%
faster than average
Annual Openings
≈17,400
openings annually
Top Industries
Typical Education
Postsecondary non-degree award or associate's degree in industrial maintenance, robotics, or mechatronics
What is an Industrial Robotics Mechanic?
An Industrial Robotics Mechanic specializes in the installation, maintenance, troubleshooting, and repair of automated robotic systems used in manufacturing and industrial settings. This role ensures that complex robotic arms, automated guided vehicles (AGVs), and other robotic machinery operate efficiently and safely, minimizing downtime in production lines. They possess a deep understanding of mechanical, electrical, pneumatic, and hydraulic systems, often integrating these various components into a cohesive robotic function.
Unlike a general maintenance technician who might handle a wide range of factory equipment, an Industrial Robotics Mechanic focuses specifically on robots and their associated automation. They are distinct from robotics engineers, who design and program new robotic systems, as the mechanic's primary focus is on the physical upkeep, repair, and operational integrity of existing robots. Their expertise is crucial for industries relying on automation for high-volume production, such as automotive, electronics, and food processing.
What does an Industrial Robotics Mechanic do?
Key Responsibilities
- Diagnose and troubleshoot mechanical, electrical, and pneumatic issues in industrial robots using schematics and diagnostic software.
- Perform preventative maintenance on robotic systems, including lubrication, calibration, and inspection of components to prevent breakdowns.
- Repair or replace faulty robotic components such as motors, sensors, actuators, and end-effectors, ensuring proper alignment and function.
- Install and commission new robotic cells, integrating them with existing production lines and ensuring they meet operational specifications.
- Conduct routine safety checks and calibrate robot movements to ensure compliance with industry safety standards and optimal performance.
- Document all maintenance and repair activities, including parts used, time spent, and issues resolved, for future reference and compliance.
Work Environment
Industrial Robotics Mechanics primarily work on factory floors or in manufacturing plants, often in environments that can be noisy, dusty, or temperature-controlled. The role involves a significant amount of hands-on work, requiring the ability to stand, bend, and lift heavy components. They typically work as part of a maintenance or engineering team, collaborating closely with production managers, engineers, and other technicians. The work schedule can vary, often including shifts, on-call duties, and weekend work to minimize production downtime. While some tasks are routine, unexpected breakdowns create a dynamic and often fast-paced environment, demanding quick problem-solving under pressure. Travel is usually minimal, confined to different areas within a single facility or, occasionally, to client sites for specialized installations or repairs.
Tools & Technologies
Industrial Robotics Mechanics regularly use a variety of specialized tools and diagnostic software to perform their duties. They work with standard mechanical tools like wrenches, screwdrivers, and torque wrenches, alongside precision instruments such as multimeters, oscilloscopes, and laser alignment tools. For diagnostics and programming, they interface with robot controllers using proprietary software from manufacturers like FANUC, KUKA, ABB, and Universal Robots. They also use programmable logic controllers (PLCs) like Allen-Bradley and Siemens for automation system integration. Safety equipment, including lockout/tagout devices and personal protective equipment (PPE), is essential for daily operations. Familiarity with CAD software for reviewing robot cell layouts and electrical diagrams is also beneficial.
Industrial Robotics Mechanic Skills & Qualifications
Industrial Robotics Mechanics maintain, troubleshoot, and repair robotic systems used in manufacturing and industrial settings. Their qualifications are primarily structured around hands-on practical experience and specialized technical training. Employers prioritize a demonstrated ability to diagnose complex electromechanical issues and execute precise repairs over theoretical knowledge alone.
Requirements for an Industrial Robotics Mechanic vary significantly based on the industry sector and the complexity of the robotic systems involved. For instance, roles in automotive manufacturing, with highly integrated and specialized robots, often demand deeper expertise in specific robot brands like KUKA, FANUC, or ABB. Smaller manufacturers might require a broader skill set across different automation technologies. Seniority levels also dictate expectations; entry-level positions often focus on preventative maintenance and basic troubleshooting, while senior mechanics handle advanced diagnostics, programming adjustments, and system optimization.
Formal education, such as an associate's degree, provides a strong foundation, but industry certifications and direct experience are often more critical for hiring. Many successful mechanics enter the field through vocational training programs, apprenticeships, or by progressing from general maintenance roles. The skill landscape continuously evolves with advancements in collaborative robots and AI integration, requiring mechanics to adapt and acquire new programming and diagnostic competencies. Prioritizing continuous learning in evolving robotic technologies ensures long-term career success in this dynamic field.
Education Requirements
Technical Skills
- Robotics programming and teach pendant operation (FANUC, KUKA, ABB, Universal Robots)
- Electromechanical troubleshooting and repair (motors, actuators, sensors, gears)
- Industrial control systems (PLCs, HMIs) diagnostics and basic programming (Allen-Bradley, Siemens)
- Hydraulics and pneumatics system maintenance and repair
- Precision measurement tools and calibration (calipers, micrometers, multimeters)
- Electrical systems and wiring diagrams interpretation (schematics, blueprints)
- Preventative maintenance procedures for industrial robots
- Robotic vision systems setup and calibration
- Servo motor and drive system diagnostics
- Welding robot specific maintenance and calibration (if applicable to industry)
- Network connectivity and communication protocols (Ethernet/IP, Profinet)
- Safety system integration and lockout/tagout procedures
Soft Skills
- Problem-solving and Analytical Thinking: Essential for diagnosing complex robotic malfunctions, which often involve interconnected mechanical, electrical, and software issues.
- Attention to Detail: Critical for precise assembly, calibration, and wiring, ensuring robotic systems operate safely and accurately.
- Adaptability and Continuous Learning: The field of robotics evolves rapidly, requiring mechanics to constantly learn new technologies, programming languages, and diagnostic tools.
- Safety Consciousness: Paramount for working with powerful machinery; mechanics must strictly adhere to safety protocols to prevent accidents and injuries.
- Communication Skills: Important for clearly explaining complex technical issues to engineers, production staff, and management, and for documenting work performed.
- Teamwork and Collaboration: Mechanics often work as part of a larger maintenance or production team, requiring effective collaboration to minimize downtime.
- Time Management and Prioritization: Necessary for efficiently handling multiple repair requests and preventative maintenance tasks to keep production lines running.
- Manual Dexterity and Hand-Eye Coordination: Crucial for performing intricate repairs, handling small components, and working with specialized tools in confined spaces on robotic systems and components like circuit boards and sensors.
How to Become an Industrial Robotics Mechanic
Becoming an Industrial Robotics Mechanic involves mastering the repair, maintenance, and troubleshooting of robotic systems in manufacturing and industrial settings. This field offers multiple entry points, from vocational training and apprenticeships to associate's degrees in robotics or mechatronics. The most direct path often involves hands-on technical education, which provides the practical skills employers seek.
Timeline expectations vary; a dedicated vocational program might take 6-12 months, while an associate's degree typically requires two years. Apprenticeships, which combine on-the-job training with classroom instruction, can last 2-4 years. Geographic location significantly impacts opportunities; major manufacturing hubs in the Midwest, Southeast, and certain international regions offer more positions than smaller markets. Companies range from large automotive plants and aerospace manufacturers to smaller automation integrators, each with unique hiring practices and skill demands.
A common misconception is that extensive programming knowledge is always required; while helpful, the core of this role is mechanical and electrical systems, hydraulics, and pneumatics. Practical problem-solving abilities and a strong understanding of safety protocols are paramount. Networking with instructors, industry professionals, and local manufacturers through career fairs or professional organizations can open doors to internships and entry-level positions, helping candidates overcome initial barriers to entry and navigate the evolving hiring landscape.
Complete a specialized technical education program focusing on industrial maintenance, robotics, or mechatronics. Look for programs that offer hands-on training with PLCs, motor controls, hydraulics, pneumatics, and robotic systems, as these foundational skills are crucial for understanding complex machinery.
Obtain relevant industry certifications that validate your skills and knowledge. Certifications from organizations like FANUC, ABB, KUKA, or the Robotic Industries Association (RIA) demonstrate proficiency in specific robotic platforms and significantly enhance your resume, making you a more attractive candidate.
Seek out practical experience through internships, co-op programs, or entry-level technician roles in manufacturing or automation companies. Hands-on experience troubleshooting, performing preventative maintenance, and repairing industrial equipment is invaluable and often a prerequisite for more advanced positions.
Develop a professional network by attending local industry events, joining professional organizations, and connecting with experienced technicians and engineers. Informational interviews can provide insights into the daily realities of the job and potential opportunities, while a strong network can lead to job referrals.
Prepare a targeted resume and cover letter that highlights your technical skills, certifications, and practical experience with industrial robotics. Emphasize your problem-solving abilities, attention to detail, and commitment to safety, tailoring each application to the specific requirements of the job posting.
Practice for technical interviews and hands-on assessments, which are common in this field. Be ready to discuss your experience with specific robotic systems, troubleshoot common mechanical or electrical issues, and demonstrate your ability to read schematics and use diagnostic tools effectively.
Step 1
Complete a specialized technical education program focusing on industrial maintenance, robotics, or mechatronics. Look for programs that offer hands-on training with PLCs, motor controls, hydraulics, pneumatics, and robotic systems, as these foundational skills are crucial for understanding complex machinery.
Step 2
Obtain relevant industry certifications that validate your skills and knowledge. Certifications from organizations like FANUC, ABB, KUKA, or the Robotic Industries Association (RIA) demonstrate proficiency in specific robotic platforms and significantly enhance your resume, making you a more attractive candidate.
Step 3
Seek out practical experience through internships, co-op programs, or entry-level technician roles in manufacturing or automation companies. Hands-on experience troubleshooting, performing preventative maintenance, and repairing industrial equipment is invaluable and often a prerequisite for more advanced positions.
Step 4
Develop a professional network by attending local industry events, joining professional organizations, and connecting with experienced technicians and engineers. Informational interviews can provide insights into the daily realities of the job and potential opportunities, while a strong network can lead to job referrals.
Step 5
Prepare a targeted resume and cover letter that highlights your technical skills, certifications, and practical experience with industrial robotics. Emphasize your problem-solving abilities, attention to detail, and commitment to safety, tailoring each application to the specific requirements of the job posting.
Step 6
Practice for technical interviews and hands-on assessments, which are common in this field. Be ready to discuss your experience with specific robotic systems, troubleshoot common mechanical or electrical issues, and demonstrate your ability to read schematics and use diagnostic tools effectively.
Education & Training Needed to Become an Industrial Robotics Mechanic
Becoming an Industrial Robotics Mechanic requires a blend of theoretical knowledge and hands-on practical skills. Formal degree programs, such as Associate's degrees in Robotics, Automation, or Mechatronics, typically span two years and cost between $10,000 and $30,000 at community colleges or technical institutes. These programs offer a strong foundation in mechanics, electronics, programming, and troubleshooting, often including lab work with industrial robots. They are widely accepted by employers and provide a structured learning environment.
Alternative pathways include vocational training programs, specialized certifications, and manufacturer-specific training. Vocational programs, often 6-12 months long, can range from $5,000 to $15,000 and focus intensely on practical repair and maintenance. Some robot manufacturers, like FANUC or KUKA, offer their own training academies, which are highly valued by employers for specific robot systems. These can vary in cost from a few hundred to several thousand dollars per course module, taking days to weeks. Self-study combined with on-the-job training is possible, but less common for entry-level roles due to the inherent safety risks and complexity of industrial robotics. Employers generally prefer candidates with formal training or certifications that demonstrate competency and safety awareness.
Continuous learning is crucial in this field due to rapid technological advancements. Mechanics often pursue additional certifications in new robot models, programming languages, or specialized maintenance techniques. These ongoing professional development courses can cost hundreds to a few thousand dollars per year. The balance between theoretical understanding and practical experience is critical; while degrees provide the former, direct interaction with robotic systems in labs or apprenticeships builds the latter. The educational needs vary by the type of industry and complexity of robots, with advanced manufacturing often requiring more specialized training. Investing in accredited programs and manufacturer certifications significantly enhances career prospects and earning potential in this specialized trade.
Industrial Robotics Mechanic Salary & Outlook
Compensation for an Industrial Robotics Mechanic reflects a blend of specialized technical skills and hands-on expertise. Geographic location significantly influences earnings; areas with high manufacturing density or advanced automation industries, like the Midwest or parts of the Southeast U.S., often command higher salaries due to demand and cost of living. Conversely, regions with lower industrial presence may offer less.
Years of experience dramatically impact earning potential. Entry-level mechanics begin with foundational knowledge, while senior roles require mastery of complex systems and troubleshooting. Specialization in specific robot brands, programming languages, or advanced diagnostics also creates salary variations. Total compensation packages extend beyond base salary to include overtime pay, which is common in this field due to urgent repair needs, and performance bonuses tied to uptime metrics or project completion.
Benefits typically include health insurance, retirement contributions like 401(k)s, and tool allowances. Companies often provide professional development opportunities, including certifications for new robot technologies, which enhances a mechanic's value. Salary negotiation leverage comes from proven problem-solving abilities and certifications in high-demand robotic platforms. While remote work is limited for hands-on roles, some senior mechanics might offer remote diagnostic support, impacting compensation structures. International markets vary widely, with salary figures in USD providing a benchmark for global comparison.
Salary by Experience Level
Level | US Median | US Average |
---|---|---|
Junior Industrial Robotics Mechanic | $52k USD | $55k USD |
Industrial Robotics Mechanic | $65k USD | $68k USD |
Senior Industrial Robotics Mechanic | $79k USD | $82k USD |
Lead Industrial Robotics Mechanic | $92k USD | $95k USD |
Industrial Robotics Maintenance Supervisor | $105k USD | $110k USD |
Market Commentary
The job market for Industrial Robotics Mechanics shows robust growth, driven by increasing automation across manufacturing, logistics, and other industries. The Bureau of Labor Statistics projects a steady demand for skilled technicians who can install, maintain, and repair robotic systems. Companies are investing heavily in automation to improve efficiency and reduce labor costs, directly fueling the need for these specialized mechanics.
Emerging opportunities include roles focused on collaborative robots (cobots), AI-driven diagnostic systems, and integrated smart factory environments. The skill set for mechanics is evolving to include software diagnostics, network connectivity, and predictive maintenance technologies. This shift requires continuous learning and adaptation to new robot models and control systems. The supply of qualified mechanics often lags behind demand, creating a favorable market for skilled professionals.
Automation and AI, rather than replacing this role, are transforming it, making predictive maintenance and remote troubleshooting more prevalent. This profession is relatively recession-resistant as industries continue to rely on automated processes even during economic downturns. Geographic hotspots for these roles include major manufacturing hubs in Michigan, Ohio, and North Carolina, as well as emerging tech-manufacturing corridors. Future-proofing involves mastering new robot programming languages and understanding data analytics for system optimization.
Industrial Robotics Mechanic Career Path
Career progression for an Industrial Robotics Mechanic typically involves a blend of hands-on technical skill development, increasing problem-solving complexity, and eventually, leadership responsibilities. Professionals in this field advance by mastering the intricacies of robotic systems, including mechanical, electrical, and software components. This path often distinguishes between those who remain individual contributors (IC) with deep technical expertise and those who transition into management, overseeing teams and operations.
Advancement speed depends on several factors: an individual's aptitude for learning new robotic technologies, the specific industry (e.g., automotive, logistics, manufacturing), and the size and complexity of the employer's robotic infrastructure. Larger corporations with diverse robotics fleets often present more structured advancement opportunities. Specialization in certain robot brands or advanced automation techniques can accelerate progression. Lateral movements might involve transitioning to roles like automation technician or controls engineer, leveraging transferable skills.
Continuous learning is paramount, given the rapid evolution of robotics. Certifications from robot manufacturers (e.g., FANUC, KUKA, ABB) significantly boost a mechanic's credentials and open doors to higher-level roles. Networking within the industry, attending trade shows, and engaging with professional organizations also enhance a mechanic's reputation and create mentorship opportunities. Some mechanics may pivot into technical training or field service engineering roles as their careers mature, applying their deep practical knowledge in different capacities.
Junior Industrial Robotics Mechanic
0-2 yearsPerforms routine maintenance tasks, such as lubrication, component replacement, and basic fault diagnosis, under direct supervision. Assists senior mechanics with more complex repairs and installations. Responsible for maintaining a clean and organized workspace and documenting simple tasks.
Key Focus Areas
Develop foundational skills in mechanical assembly, electrical wiring, and basic troubleshooting of robotic cells. Learn to read schematics, understand safety protocols, and use diagnostic tools. Focus on absorbing knowledge from experienced mechanics and following established procedures accurately.
Industrial Robotics Mechanic
2-5 yearsExecutes scheduled preventative maintenance and performs complex diagnostic tests and repairs on industrial robots and associated peripheral equipment. Works independently to resolve most common robotic malfunctions. May provide guidance to junior mechanics on specific tasks and ensure system uptime.
Key Focus Areas
Master advanced troubleshooting techniques for electrical, mechanical, and pneumatic systems. Develop proficiency in robot programming logic for basic tasks and error recovery. Focus on independent problem-solving, efficient repair execution, and adherence to maintenance schedules. Consider specialized training in specific robot brands.
Senior Industrial Robotics Mechanic
5-8 yearsServes as a subject matter expert for complex robotic systems, diagnosing and resolving challenging technical issues that others cannot. Leads repair efforts for major system breakdowns and participates in the commissioning of new robotic installations. Provides technical mentorship to junior and mid-level mechanics.
Key Focus Areas
Cultivate expertise in advanced robot programming, vision systems, and complex PLC integration. Develop strong analytical skills for root cause analysis and predictive maintenance strategies. Focus on optimizing robot performance, reducing downtime, and contributing to system design improvements. Pursue manufacturer-specific advanced certifications.
Lead Industrial Robotics Mechanic
8-12 yearsOversees the daily activities of a team of industrial robotics mechanics, prioritizing work orders and managing resource allocation. Leads complex troubleshooting efforts and ensures compliance with safety and quality standards. Acts as a primary technical liaison with engineering and production teams for system improvements and upgrades.
Key Focus Areas
Develop leadership and project management skills, including work delegation, resource allocation, and team coordination. Focus on strategic planning for maintenance activities, continuous improvement initiatives, and implementing best practices. Enhance communication skills for cross-functional collaboration and reporting.
Industrial Robotics Maintenance Supervisor
12+ years total experience, 2+ years in a lead roleManages the overall maintenance and performance of an entire fleet of industrial robots within a facility or across multiple sites. Develops and implements preventative maintenance programs, manages budgets for parts and services, and oversees the professional development of the robotics maintenance team. Responsible for maximizing robot uptime and operational efficiency.
Key Focus Areas
Acquire strong operational management, budgeting, and personnel development skills. Focus on long-term strategic planning for robotics maintenance, technology adoption, and team training programs. Develop leadership capabilities for performance management, conflict resolution, and fostering a high-performance culture.
Junior Industrial Robotics Mechanic
0-2 yearsPerforms routine maintenance tasks, such as lubrication, component replacement, and basic fault diagnosis, under direct supervision. Assists senior mechanics with more complex repairs and installations. Responsible for maintaining a clean and organized workspace and documenting simple tasks.
Key Focus Areas
Develop foundational skills in mechanical assembly, electrical wiring, and basic troubleshooting of robotic cells. Learn to read schematics, understand safety protocols, and use diagnostic tools. Focus on absorbing knowledge from experienced mechanics and following established procedures accurately.
Industrial Robotics Mechanic
2-5 yearsExecutes scheduled preventative maintenance and performs complex diagnostic tests and repairs on industrial robots and associated peripheral equipment. Works independently to resolve most common robotic malfunctions. May provide guidance to junior mechanics on specific tasks and ensure system uptime.
Key Focus Areas
Master advanced troubleshooting techniques for electrical, mechanical, and pneumatic systems. Develop proficiency in robot programming logic for basic tasks and error recovery. Focus on independent problem-solving, efficient repair execution, and adherence to maintenance schedules. Consider specialized training in specific robot brands.
Senior Industrial Robotics Mechanic
5-8 yearsServes as a subject matter expert for complex robotic systems, diagnosing and resolving challenging technical issues that others cannot. Leads repair efforts for major system breakdowns and participates in the commissioning of new robotic installations. Provides technical mentorship to junior and mid-level mechanics.
Key Focus Areas
Cultivate expertise in advanced robot programming, vision systems, and complex PLC integration. Develop strong analytical skills for root cause analysis and predictive maintenance strategies. Focus on optimizing robot performance, reducing downtime, and contributing to system design improvements. Pursue manufacturer-specific advanced certifications.
Lead Industrial Robotics Mechanic
8-12 yearsOversees the daily activities of a team of industrial robotics mechanics, prioritizing work orders and managing resource allocation. Leads complex troubleshooting efforts and ensures compliance with safety and quality standards. Acts as a primary technical liaison with engineering and production teams for system improvements and upgrades.
Key Focus Areas
Develop leadership and project management skills, including work delegation, resource allocation, and team coordination. Focus on strategic planning for maintenance activities, continuous improvement initiatives, and implementing best practices. Enhance communication skills for cross-functional collaboration and reporting.
Industrial Robotics Maintenance Supervisor
12+ years total experience, 2+ years in a lead roleManages the overall maintenance and performance of an entire fleet of industrial robots within a facility or across multiple sites. Develops and implements preventative maintenance programs, manages budgets for parts and services, and oversees the professional development of the robotics maintenance team. Responsible for maximizing robot uptime and operational efficiency.
Key Focus Areas
Acquire strong operational management, budgeting, and personnel development skills. Focus on long-term strategic planning for robotics maintenance, technology adoption, and team training programs. Develop leadership capabilities for performance management, conflict resolution, and fostering a high-performance culture.
Job Application Toolkit
Ace your application with our purpose-built resources:
Industrial Robotics Mechanic Resume Examples
Proven layouts and keywords hiring managers scan for.
View examplesIndustrial Robotics Mechanic Cover Letter Examples
Personalizable templates that showcase your impact.
View examplesTop Industrial Robotics Mechanic Interview Questions
Practice with the questions asked most often.
View examplesIndustrial Robotics Mechanic Job Description Template
Ready-to-use JD for recruiters and hiring teams.
View examplesGlobal Industrial Robotics Mechanic Opportunities
Industrial Robotics Mechanics maintain and repair automated systems globally. This profession translates consistently across manufacturing sectors worldwide, driven by widespread industrial automation. Global demand for skilled mechanics remains high in 2025 as factories adopt more robotics. Regulatory differences primarily involve safety standards, but core mechanical principles are universal. Professionals seek international roles for higher wages or specialized projects. International certifications like Certified Robotics Technician (CRT) enhance global mobility.
Global Salaries
Salaries for Industrial Robotics Mechanics vary significantly by region and experience. In North America, entry-level mechanics earn $50,000-$70,000 USD annually, while experienced professionals command $80,000-$110,000 USD. For instance, in the US, a skilled mechanic might earn $95,000, while in Canada, it's around CAD 85,000 ($62,000 USD).
European salaries range from €35,000-€60,000 annually. Germany offers €45,000-€70,000 ($48,000-$75,000 USD), reflecting its strong manufacturing base and high cost of living. In contrast, Eastern European countries might offer €25,000-€40,000 ($27,000-$43,000 USD). Purchasing power parity is crucial; a lower nominal salary in a country with a lower cost of living often translates to comparable or better disposable income.
Asia-Pacific regions show diverse ranges. Japan offers JPY 4,500,000-7,500,000 ($30,000-$50,000 USD), while South Korea is similar at KRW 40,000,000-70,000,000 ($29,000-$51,000 USD). China, with its vast manufacturing, offers CNY 120,000-250,000 ($17,000-$35,000 USD), but often includes housing or other benefits. Benefits packages differ, with some countries offering more comprehensive healthcare or vacation time than others. Tax implications vary; some countries have higher income taxes but offer more public services. International pay scales are less standardized for mechanics, but larger multinational corporations may have internal frameworks.
Remote Work
International remote work for Industrial Robotics Mechanics is limited due to the hands-on nature of the role. Most tasks require physical presence for repair, maintenance, and installation of machinery. However, some aspects, like diagnostics, software troubleshooting, or remote monitoring of robotic systems, can be performed remotely.
Digital nomad opportunities are rare for this profession. Companies rarely hire industrial mechanics for fully remote international roles. Instead, international assignments usually involve on-site work or short-term projects abroad. When remote work occurs, it typically involves supporting a local team or a specific client site from a different geographic location within the same company's operational region. Salary expectations for remote diagnostic support might differ, often reflecting a blend of technical expertise and remote accessibility rather than a full on-site mechanic's wage. Companies might provide specialized software or equipment for remote access.
Visa & Immigration
Industrial Robotics Mechanics typically qualify for skilled worker visas in many countries. Popular destinations like Germany, Canada, Australia, and the US often have specific visa categories for trades and technical professions. For example, Canada's Express Entry system or Australia's Skilled Nominated visa (subclass 190) may include this occupation.
Credential recognition is vital. Countries often require educational qualifications and professional experience to be assessed by a recognized body. Some nations, particularly in Europe, demand specific certifications or apprenticeships. The visa application process usually involves submitting educational documents, work experience letters, and sometimes a skills assessment. Timelines vary from a few months to over a year, depending on the country and visa type.
Language requirements are common, especially for non-English speaking countries like Germany, which may require German proficiency. Intra-company transfers are common for large multinational manufacturers moving mechanics between their global facilities. Pathways to permanent residency often exist after several years of skilled employment in a country. Family visas for dependents are usually available alongside the primary applicant's visa. Some countries offer fast-track processing for in-demand occupations, which may include robotics mechanics.
2025 Market Reality for Industrial Robotics Mechanics
Understanding the current market realities for an Industrial Robotics Mechanic is critical for career success. The landscape has evolved significantly since 2023, shaped by rapid advancements in automation and the pervasive influence of AI.
Post-pandemic supply chain recalibrations and the ongoing AI revolution have accelerated robotic adoption, directly impacting the demand for skilled mechanics. Broader economic factors, such as manufacturing output and investment in new technologies, heavily influence job availability. Market realities also vary by experience level, with senior mechanics finding more specialized roles, and by geographic region, depending on industrial concentration. This analysis provides an honest look at today's market to help you navigate your career path effectively.
Current Challenges
Competition for entry-level industrial robotics mechanic roles remains high, especially for those without specialized certifications. Many companies now expect a baseline understanding of AI-driven diagnostic tools, creating a skill gap for some. Economic uncertainties can delay capital expenditures on new robotic systems, directly impacting demand for new maintenance staff.
Growth Opportunities
Strong demand exists for industrial robotics mechanics skilled in advanced diagnostics and predictive maintenance, particularly those familiar with AI-driven systems. Emerging opportunities include specialization in collaborative robot (cobot) maintenance, which requires a blend of mechanical and software expertise, and roles focused on integrating robotic systems with broader IoT networks.
Professionals who pursue certifications in specific robot brands (e.g., FANUC, KUKA, ABB) or gain proficiency in PLC programming (Siemens, Allen-Bradley) hold a significant competitive advantage. Underserved markets often exist in regions where new manufacturing facilities are establishing themselves, creating a localized surge in demand. Strategic career moves involve focusing on continuous learning in areas like machine learning fundamentals for predictive maintenance or advanced sensor technology. The automotive, electronics, and food processing sectors remain robust, consistently seeking skilled robotics mechanics.
Current Market Trends
Demand for industrial robotics mechanics continues to grow steadily in 2025, driven by increasing automation across manufacturing, logistics, and automotive sectors. Companies are investing heavily in advanced robotic systems to boost efficiency and reduce labor costs, directly increasing the need for skilled technicians who can maintain and repair these complex machines. This includes a notable shift towards collaborative robots (cobots) and AI-powered diagnostic systems, which require mechanics to adapt their skill sets.
The integration of generative AI in predictive maintenance platforms is a significant trend. Mechanics are now expected to interpret data from these systems to anticipate failures rather than just react to them. This changes employer requirements, favoring candidates with strong analytical skills alongside mechanical aptitude. Salaries show a moderate upward trend, particularly for those proficient in PLC programming, vision systems, and network troubleshooting, reflecting the specialized nature of the work. Market saturation remains low for highly skilled, experienced mechanics, but entry-level positions can be competitive.
Geographically, demand is strongest in industrial hubs like the Midwest and Southeast United States, as well as parts of Europe and Asia with high manufacturing output. Remote work is generally not applicable to this hands-on role, though some larger companies use remote diagnostics to support on-site teams. Hiring patterns tend to be consistent year-round, reflecting ongoing operational needs rather than seasonal fluctuations.
Emerging Specializations
The field of industrial robotics is undergoing rapid transformation, driven by advancements in artificial intelligence, machine learning, and sensor technologies. These innovations are not only enhancing the capabilities of robotic systems but also creating entirely new specialization opportunities for Industrial Robotics Mechanics.
Early positioning in these emerging areas is crucial for career advancement from 2025 onwards. Professionals who proactively develop skills in these cutting-edge niches will find themselves in high demand, often commanding premium compensation and experiencing accelerated career growth. While established specializations remain vital, focusing on emerging areas provides a strategic advantage, preparing mechanics for the next generation of industrial automation.
Many emerging areas, particularly those involving advanced AI integration or collaborative robotics, are rapidly transitioning from niche applications to mainstream adoption. This shift creates significant job opportunities within a relatively short timeframe, often within the next three to five years. Pursuing these specializations involves a balance of risk and reward; while they require investment in new skills, the potential for career differentiation and long-term stability is substantial.
Robotics Cybersecurity Specialist
As industrial robots become more sophisticated and interconnected, their vulnerability to cyber threats increases. Industrial Robotics Mechanics specializing in cybersecurity ensure the integrity and operational safety of these complex systems. This involves implementing secure network protocols, monitoring for malicious activity, and developing rapid response plans to neutralize cyberattacks that could disrupt production or compromise proprietary data.
Collaborative Robotics (Cobot) Technician
Cobots, or collaborative robots, are designed to work alongside human operators, requiring mechanics who understand human-robot interaction and safety protocols. This specialization focuses on the installation, programming, and maintenance of cobots, ensuring their seamless integration into human-centric workspaces. Mechanics in this area optimize cobot performance for tasks requiring close human collaboration, such as assembly or quality control.
AI-Integrated Robotics Mechanic
The integration of AI and machine learning is transforming industrial robotics, enabling robots to learn, adapt, and make autonomous decisions. Mechanics in this specialization troubleshoot and maintain AI-driven robotic systems, focusing on the software and hardware interfaces that facilitate machine learning. This includes diagnosing issues with neural networks, sensor data processing, and predictive maintenance algorithms.
Robotic Additive Manufacturing Specialist
Additive manufacturing, particularly 3D printing, is increasingly integrated with robotic arms for complex, large-scale production. Industrial Robotics Mechanics specializing in robotic additive manufacturing maintain and optimize robotic systems used for precise material deposition. This involves understanding advanced printing materials, robotic path planning for 3D structures, and calibration for high-precision layering.
Sustainable Robotics Maintenance Technician
The demand for sustainable manufacturing practices is driving the adoption of energy-efficient and environmentally conscious robotic systems. Mechanics in this area specialize in optimizing robot performance for reduced energy consumption and waste. This involves implementing predictive maintenance to extend component life, retrofitting older systems for efficiency, and managing the responsible disposal or recycling of robotic components.
Pros & Cons of Being an Industrial Robotics Mechanic
Making informed career decisions requires a clear understanding of both the benefits and challenges associated with a specific profession. The experience within any career, including that of an Industrial Robotics Mechanic, can vary significantly based on the company culture, the industry sector (e.g., automotive, aerospace, food processing), and the specific type of robotic systems involved.
Furthermore, the pros and cons may shift at different stages of a career; early-career mechanics might focus on learning and skill acquisition, while senior mechanics may prioritize problem-solving and system optimization. It is also important to acknowledge that what one person considers an advantage, another might see as a disadvantage, depending on individual values, lifestyle preferences, and tolerance for certain work conditions. This assessment provides an honest, balanced perspective to help individuals set realistic expectations for a career as an Industrial Robotics Mechanic.
Pros
- High demand for skilled professionals ensures strong job security and consistent employment opportunities across various manufacturing and logistics industries.
- Offers intellectually stimulating work involving complex problem-solving, as diagnosing and repairing advanced robotic systems requires a blend of mechanical, electrical, and programming knowledge.
- Competitive compensation packages are common due to the specialized skills required, often including good hourly wages, overtime pay, and comprehensive benefits.
- Provides opportunities for continuous skill development and learning, as the field of robotics constantly evolves, allowing mechanics to stay at the forefront of automation technology.
- Directly contributes to efficient production and innovation, offering a sense of accomplishment in keeping sophisticated automated systems operational and improving manufacturing processes.
- Offers a tangible and hands-on work experience, appealing to individuals who enjoy practical application of technical knowledge and seeing immediate results from their work.
- Career advancement opportunities exist, allowing mechanics to progress into roles such as robotics engineers, automation specialists, team leads, or trainers with additional experience and certifications.
Cons
- Frequent exposure to loud machinery, heavy equipment, and potential electrical hazards requires constant vigilance and adherence to strict safety protocols, which can be mentally taxing over time.
- Requires continuous learning and adaptation to new robotic technologies, software updates, and manufacturing processes, demanding ongoing training and skill development to remain effective.
- Irregular work hours and on-call duties are common, especially in production environments where robot malfunctions can occur at any time, leading to unexpected shifts or weekend work.
- The work can be physically demanding, involving lifting heavy components, working in confined spaces, and standing for long periods, which may lead to physical strain or injuries over a career.
- Troubleshooting complex, interconnected robotic systems can be frustrating and time-consuming, as diagnosing issues often requires intricate knowledge of mechanical, electrical, and programming components.
- Job opportunities may be concentrated in specific industrial hubs or manufacturing regions, potentially requiring relocation for the best career prospects and limiting options in other areas.
- The repetitive nature of some maintenance tasks, such as routine inspections or parts replacement, can lead to monotony despite the overall technical complexity of the role at times, impacting job satisfaction for some individuals and companies with predictable production schedules and fewer unique challenges often experience this more.
Frequently Asked Questions
Industrial Robotics Mechanics face distinct challenges maintaining complex automated systems crucial for manufacturing. This section addresses key questions about entering this hands-on field, from required technical skills and training paths to job stability and career progression within the evolving automation industry.
What are the essential qualifications and training needed to become an Industrial Robotics Mechanic?
Becoming an Industrial Robotics Mechanic typically requires a post-secondary education, such as an associate's degree in robotics, automation, mechatronics, or industrial maintenance. Many also benefit from vocational training programs focusing on hydraulics, pneumatics, electrical systems, and PLC programming. Hands-on experience through internships or apprenticeships is crucial for developing practical troubleshooting skills.
How long does it typically take to become job-ready as an Industrial Robotics Mechanic if I'm starting from scratch?
From starting with no prior experience, it generally takes 2-4 years to become job-ready. This includes completing a two-year associate's degree or vocational program and then gaining 1-2 years of entry-level experience or apprenticeship. Specialized certifications in robotics brands or specific control systems can accelerate your readiness for more complex roles.
What are the realistic salary expectations for an Industrial Robotics Mechanic?
The salary for Industrial Robotics Mechanics varies by experience, location, and industry. Entry-level positions might start around $45,000-$55,000 annually. Experienced mechanics with specialized skills or certifications can earn $60,000-$80,000 or more. Overtime pay is often available due to the critical nature of maintaining production lines.
What is the typical work-life balance and work environment like for this role?
Work-life balance can vary. Mechanics often work standard shifts, but on-call duties or irregular hours are common, especially in manufacturing environments that operate 24/7. This includes responding to breakdowns during nights, weekends, or holidays to minimize production downtime. The work is physically demanding, requiring standing, lifting, and working in various industrial settings.
Is the job market for Industrial Robotics Mechanics stable, or is it at risk of automation itself?
Job security for Industrial Robotics Mechanics is strong and growing. As industries increasingly automate, the demand for skilled professionals to install, maintain, and repair these complex systems rises. This role is difficult to automate itself, ensuring ongoing need. Continuous learning and adapting to new technologies are key to long-term stability.
What are the potential career growth and advancement opportunities for an Industrial Robotics Mechanic?
Career growth paths include specializing in specific robot brands, advanced programming, or becoming a field service engineer traveling to client sites. You could also advance to lead mechanic, maintenance supervisor, or even move into robotics design and integration roles with further education. Continuous professional development through certifications is crucial for advancement.
Can Industrial Robotics Mechanics work remotely, or is it strictly an on-site position?
While some roles might involve regional travel to different plant locations, Industrial Robotics Mechanics primarily work on-site at manufacturing facilities. Remote work is generally not feasible given the hands-on nature of repairing and maintaining physical machinery. Your work location will usually be a factory floor, requiring adherence to safety protocols.
What are the most challenging aspects of being an Industrial Robotics Mechanic?
The biggest challenge is keeping up with rapidly evolving technology and complex troubleshooting. Robotics systems integrate mechanical, electrical, and software components, requiring a broad skill set. You must continuously learn new programming languages, diagnostic tools, and robot models to effectively diagnose and repair issues under pressure to minimize costly production downtime.
Related Careers
Explore similar roles that might align with your interests and skills:
Industrial Maintenance Mechanic
A growing field with similar skill requirements and career progression opportunities.
Explore career guideIndustrial Mechanic
A growing field with similar skill requirements and career progression opportunities.
Explore career guideMechatronics Technician
A growing field with similar skill requirements and career progression opportunities.
Explore career guideRobotics Testing Technician
A growing field with similar skill requirements and career progression opportunities.
Explore career guideWelding Robot Operator
A growing field with similar skill requirements and career progression opportunities.
Explore career guideAssess your Industrial Robotics Mechanic readiness
Understanding where you stand today is the first step toward your career goals. Our Career Coach helps identify skill gaps and create personalized plans.
Skills Gap Analysis
Get a detailed assessment of your current skills versus Industrial Robotics Mechanic requirements. Our AI Career Coach identifies specific areas for improvement with personalized recommendations.
See your skills gapCareer Readiness Assessment
Evaluate your overall readiness for Industrial Robotics Mechanic roles with our AI Career Coach. Receive personalized recommendations for education, projects, and experience to boost your competitiveness.
Assess your readinessSimple pricing, powerful features
Upgrade to Himalayas Plus and turbocharge your job search.
Himalayas
Himalayas Plus
Himalayas Max
Find your dream job
Sign up now and join over 100,000 remote workers who receive personalized job alerts, curated job matches, and more for free!
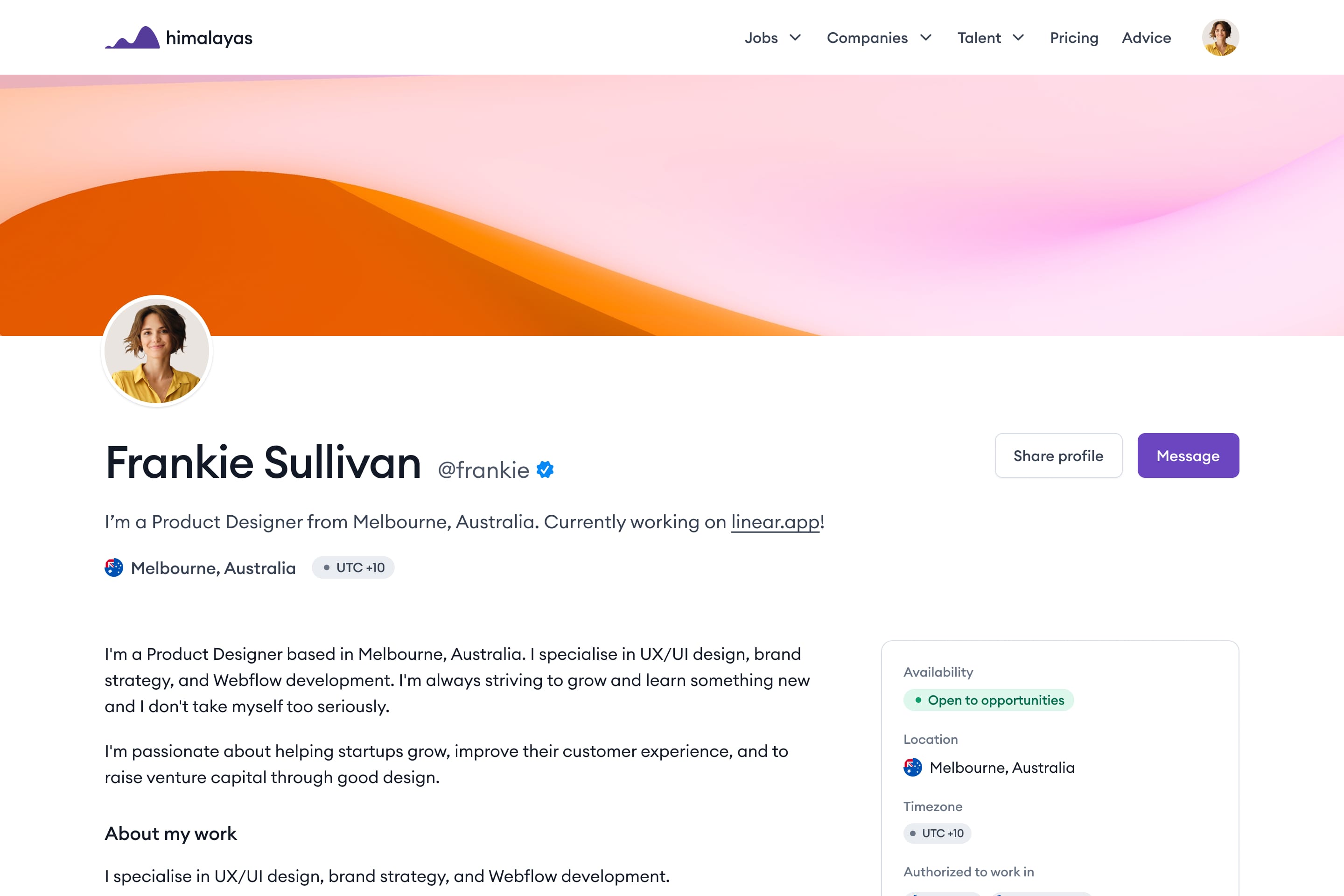