Complete Industrial Engineering Technologist Career Guide
Industrial Engineering Technologists are the efficiency experts on the ground, directly implementing and optimizing processes to boost productivity and quality in manufacturing and service industries. They bridge the gap between theoretical engineering designs and practical application, ensuring systems run smoothly and cost-effectively. This hands-on role offers a direct path to impacting operational success, making it a vital career for those who enjoy problem-solving and tangible results.
Key Facts & Statistics
Median Salary
$66,800 USD
(U.S. Bureau of Labor Statistics, May 2023)
Range: $45k - $95k+ USD
Growth Outlook
3%
as fast as average (U.S. Bureau of Labor Statistics, 2022-2032)
Annual Openings
≈1,300
openings annually (U.S. Bureau of Labor Statistics)
Top Industries
Typical Education
Associate's degree in industrial engineering technology or a related engineering technology field
What is an Industrial Engineering Technologist?
An Industrial Engineering Technologist is a skilled professional who applies engineering principles and analytical methods to improve efficiency, productivity, quality, and safety within organizational systems. They focus on optimizing complex processes, workflows, and resource utilization in manufacturing, logistics, healthcare, and service industries. Their primary goal involves streamlining operations to reduce waste and enhance overall performance.
Unlike a traditional Industrial Engineer who might focus more on theoretical research or complex system design, the Technologist emphasizes the practical application and implementation of these designs. They bridge the gap between engineering theory and shop-floor reality, translating high-level strategies into actionable, measurable improvements. They are instrumental in putting efficiency concepts into practice, working directly with operational teams to implement changes and monitor their effectiveness.
What does an Industrial Engineering Technologist do?
Key Responsibilities
- Analyze production processes and workflows to identify inefficiencies and bottlenecks.
- Design and implement new layouts for manufacturing facilities or service operations to optimize space and material flow.
- Develop and update standard operating procedures (SOPs) to ensure consistent quality and efficiency across tasks.
- Conduct time studies and motion studies to establish accurate work standards and improve productivity.
- Utilize statistical methods to collect and interpret data, supporting decisions for process improvements.
- Collaborate with engineers and production staff to test and refine new systems, equipment, or process changes.
- Prepare detailed reports and presentations summarizing findings, recommendations, and the impact of implemented changes on operational performance.
Work Environment
Industrial Engineering Technologists primarily work in manufacturing plants, production facilities, or large service organizations. Their work environment blends office time for analysis and report generation with significant time spent on the factory floor or in operational areas observing processes. Collaboration is frequent, involving engineers, production managers, line workers, and quality assurance personnel.
The pace of work can be dynamic, often driven by production schedules and improvement initiatives. They typically work standard business hours, but may occasionally adjust their schedule to observe different shifts or respond to urgent operational issues. The role requires a hands-on approach and the ability to adapt to diverse operational settings, sometimes involving noisy or active environments.
Tools & Technologies
Industrial Engineering Technologists regularly use specialized software for simulation, statistical analysis, and Computer-Aided Design (CAD). Tools like Arena or FlexSim are common for process simulation, while Minitab or JMP assist with statistical process control and data analysis. They also frequently work with Microsoft Excel for data management and analysis, along with PowerPoint for presenting findings.
Beyond software, they utilize various measurement tools such as stopwatches, video cameras, and data loggers for time and motion studies. Knowledge of Enterprise Resource Planning (ERP) systems like SAP or Oracle is beneficial for understanding operational data. They often work with lean manufacturing tools, including value stream mapping, Kaizen, and 5S principles, applying these methodologies to drive continuous improvement.
Industrial Engineering Technologist Skills & Qualifications
Industrial Engineering Technologists bridge the gap between theoretical industrial engineering principles and practical application. Their role involves implementing, optimizing, and maintaining systems in manufacturing, logistics, and service industries. They focus on improving efficiency, productivity, quality, and safety within operational environments. Qualifications for this role emphasize a blend of technical knowledge and hands-on experience, often prioritizing practical application over advanced theoretical research.
Requirements for Industrial Engineering Technologists vary significantly by industry sector, company size, and specific operational focus. In large manufacturing plants, the role might center on Lean Six Sigma implementation and automation integration. In logistics, it could involve supply chain optimization and warehouse layout design. Smaller companies might expect a broader skill set, with technologists handling multiple aspects of process improvement. Geographic location also plays a role, as some regions have stronger manufacturing bases that demand more technologists.
While formal education provides foundational knowledge, practical experience and industry-recognized certifications significantly enhance a candidate's profile. Many technologists enter the field with an associate's degree or a bachelor's in a technology-focused discipline, demonstrating a strong emphasis on applied learning. Certifications in Lean, Six Sigma, or project management are highly valued, indicating a commitment to continuous improvement methodologies. The skill landscape for this role is continuously evolving, with increasing importance placed on data analytics, automation technologies, and sustainable practices. Professionals must balance a broad understanding of industrial processes with deep expertise in specific tools or methodologies to remain competitive.
Education Requirements
Technical Skills
- Process Mapping and Analysis (e.g., Value Stream Mapping, Flow Charts)
- Lean Manufacturing Principles and Tools (e.g., 5S, Kaizen, Kanban)
- Six Sigma Methodologies (e.g., DMAIC framework, statistical process control)
- Data Collection and Analysis (e.g., Minitab, Excel for statistical analysis)
- CAD Software (e.g., AutoCAD, SolidWorks for layout and design)
- Work Measurement and Time Studies (e.g., MOST, stopwatch studies)
- Ergonomics and Workplace Design Principles
- Production Planning and Control Systems (e.g., MRP, ERP basics)
- Quality Management Systems (e.g., ISO 9001, quality assurance techniques)
- Automation and Robotics Fundamentals (understanding of PLC, HMI basics)
- Supply Chain and Logistics Optimization Concepts
- Project Management Software (e.g., Microsoft Project, Asana for tracking tasks)
Soft Skills
- Problem-solving and Analytical Thinking: Essential for identifying inefficiencies, root causes of issues, and developing effective solutions within complex operational systems.
- Attention to Detail: Crucial for accurate data collection, precise process mapping, and ensuring the correct implementation of improvements to avoid errors.
- Communication and Presentation Skills: Important for clearly explaining technical concepts, proposed changes, and project outcomes to both technical and non-technical stakeholders.
- Collaboration and Teamwork: Necessary for working effectively with production teams, engineers, management, and other departments to implement process improvements.
- Adaptability and Flexibility: Valued for adjusting to changing production demands, new technologies, and unexpected challenges in dynamic industrial environments.
- Time Management and Prioritization: Key for managing multiple improvement projects simultaneously, meeting deadlines, and optimizing personal productivity.
How to Become an Industrial Engineering Technologist
Breaking into the Industrial Engineering Technologist field involves several pathways, each with its own timeline and advantages. Many enter with an Associate's degree in Industrial Engineering Technology, Manufacturing Technology, or a related engineering discipline, providing a solid theoretical and practical foundation. Others transition from skilled trades or manufacturing roles, leveraging their hands-on experience and then acquiring specific IE tech skills through certifications or focused coursework. A complete beginner might expect a 2-year timeline to acquire an Associate's degree, while those with existing manufacturing experience could potentially pivot in 6-12 months with targeted training.
Entry strategies vary significantly by company size and industry. Larger corporations often seek candidates with formal degrees and internship experience, valuing structured problem-solving skills. Smaller businesses and startups may prioritize practical experience and a demonstrated ability to implement efficiency improvements, sometimes being more open to self-taught individuals or those with vocational training. Geographic location also plays a role; manufacturing hubs will have more opportunities, but also more competition. It is important to understand that while an Industrial Engineer designs systems, an Industrial Engineering Technologist implements, optimizes, and maintains these systems, requiring a strong blend of technical knowledge and hands-on ability.
A common misconception is that this role is purely theoretical; in reality, it demands significant time on the shop floor, interacting with production teams and equipment. Networking within local manufacturing associations, attending industry trade shows, and seeking mentorship from experienced technologists or engineers can significantly accelerate career entry. Building a portfolio that showcases practical projects, even from academic settings or personal initiatives, proves capability more effectively than a resume alone. The hiring landscape values adaptability and a continuous learning mindset, as manufacturing processes and technologies constantly evolve.
Step 1
Step 2
Step 3
Step 4
Step 5
Step 6
Education & Training Needed to Become an Industrial Engineering Technologist
Becoming an Industrial Engineering Technologist involves a blend of theoretical knowledge and practical application, with several educational pathways available. Formal degree programs, typically associate's or bachelor's degrees in Industrial Engineering Technology or a related field, provide a strong foundational understanding of process optimization, quality control, and systems integration. A two-year associate's degree often costs between $8,000 and $25,000, while a four-year bachelor's degree can range from $40,000 to over $100,000, depending on the institution and location. Completion times are generally 2 years for an associate's and 4 years for a bachelor's, assuming full-time study. These degrees are highly regarded by employers for entry-level and mid-level positions, providing a structured curriculum and often including valuable internship opportunities.
Alternative learning paths, such as specialized certification programs or online courses, can supplement a degree or provide focused skills for those with prior technical backgrounds. These options typically range from a few hundred dollars for individual online courses to $5,000-$15,000 for comprehensive certification programs, with completion times varying from a few weeks to 6-12 months. While these alternatives may not replace a formal degree for all roles, they are excellent for skill enhancement or for transitioning into the field from a related discipline. Employers value practical experience and demonstrated problem-solving abilities; therefore, internships, co-op programs, and hands-on projects are critical components of any educational journey in this field.
Continuous learning is essential for Industrial Engineering Technologists due to evolving technologies and industry standards. Professional development often involves specialized training in areas like Lean Manufacturing, Six Sigma, CAD/CAM software, or supply chain analytics. These programs enhance marketability and can lead to career advancement. The cost-benefit analysis for educational investments should consider the specific career goals: a formal degree offers a broader foundation and more career mobility, while targeted certifications can provide quicker entry or specialization. Industry-specific accreditations, such as those from ABET (Accreditation Board for Engineering and Technology) for degree programs, signal quality and relevance to employers.
Industrial Engineering Technologist Salary & Outlook
Compensation for an Industrial Engineering Technologist varies significantly based on several key factors. Geographic location plays a crucial role, with higher salaries typically found in major industrial hubs and areas with a higher cost of living, such as California, Texas, and the Northeast. Conversely, regions with lower living costs may offer lower base salaries.
Experience, specialized skills, and the specific industry dramatically influence earning potential. Technologists with expertise in automation, lean manufacturing, or supply chain optimization often command higher salaries. Total compensation packages frequently extend beyond base salary to include performance bonuses, profit sharing, and comprehensive benefits such as health insurance, retirement plans, and paid time off. Some roles may also offer allowances for professional development or certifications.
Industry-specific trends, like the growth in advanced manufacturing or logistics, drive salary growth for this role. Larger companies with more complex operations or those in high-demand sectors may offer more competitive compensation. Remote work opportunities for Industrial Engineering Technologists are less common due to the hands-on nature of the role, but some consultative positions may offer location flexibility, potentially impacting salary based on the employer's geographic base. International markets present different salary scales, with the provided figures reflecting the U.S. dollar context.
Salary by Experience Level
Level | US Median | US Average |
---|---|---|
Junior Industrial Engineering Technologist | $55k USD | $60k USD |
Industrial Engineering Technologist | $70k USD | $75k USD |
Senior Industrial Engineering Technologist | $90k USD | $95k USD |
Lead Industrial Engineering Technologist | $110k USD | $115k USD |
Market Commentary
The job market for Industrial Engineering Technologists shows steady demand, driven by industries focused on efficiency, productivity, and cost reduction. Manufacturing, logistics, healthcare, and consulting sectors consistently seek these professionals to optimize processes and improve operational performance. The increasing complexity of global supply chains and the push for automation across industries further fuel this demand.
Technological advancements, including AI, robotics, and data analytics, are reshaping the role, creating new opportunities for technologists proficient in these areas. The emphasis on Industry 4.0 and smart factories ensures a continuous need for individuals who can implement and manage advanced systems. While automation streamlines processes, it also elevates the complexity of the technologist's responsibilities, requiring continuous skill development.
Demand for Industrial Engineering Technologists is relatively stable, as their expertise remains vital for operational efficiency regardless of economic cycles. Geographic hotspots for these roles align with manufacturing corridors and major distribution centers, though remote work is not typical given the hands-on nature. Future-proofing this career involves embracing new technologies and specializing in areas like predictive maintenance, digital twins, or sustainable operations. The market is not overly saturated, with a consistent need for skilled professionals who can drive tangible improvements in efficiency and productivity.
Industrial Engineering Technologist Career Path
Career progression for an Industrial Engineering Technologist typically involves a blend of technical skill refinement, project management, and leadership development. Initial stages focus on mastering core methodologies and data analysis, while later stages emphasize optimizing complex systems and guiding teams. Advancement paths often diverge into individual contributor (IC) tracks, focusing on specialized technical expertise, or management tracks, which involve leading teams and strategic initiatives. Performance, the ability to deliver measurable improvements, and continuous learning significantly influence advancement speed.
Company size and industry heavily impact an Industrial Engineering Technologist's career path. In large corporations, opportunities for specialization and formal leadership roles are more prevalent, often requiring expertise in specific manufacturing processes or supply chain components. Startups or smaller firms might offer broader responsibilities, allowing technologists to contribute across various operational areas, though formal progression might be less structured. Lateral movement to related fields like quality assurance, logistics management, or operations analysis is common, leveraging transferable skills in process optimization and efficiency.
Networking within professional organizations, pursuing relevant certifications (e.g., Lean Six Sigma), and securing mentorship are crucial for accelerating career growth. These activities enhance professional reputation, provide access to advanced knowledge, and open doors to new opportunities. Economic conditions and specific industry trends also play a role, influencing the demand for efficiency experts and the availability of resources for process improvement projects. Continuous skill development, particularly in data analytics, automation, and project management, remains vital for sustained progression.
Junior Industrial Engineering Technologist
0-2 yearsKey Focus Areas
Industrial Engineering Technologist
2-4 yearsKey Focus Areas
Senior Industrial Engineering Technologist
4-7 yearsKey Focus Areas
Lead Industrial Engineering Technologist
7+ years total experienceKey Focus Areas
Junior Industrial Engineering Technologist
0-2 yearsAssist senior technologists with data collection, analysis, and basic process documentation. Support smaller projects or specific components of larger initiatives under direct supervision. Follow established procedures to identify inefficiencies and suggest minor improvements. Work primarily within a defined scope, contributing to team goals.
Key Focus Areas
Develop foundational skills in process mapping, time and motion studies, and basic data collection. Master industrial engineering software and tools. Learn to interpret technical drawings and specifications. Focus on understanding operational workflows and safety protocols. Begin building problem-solving and analytical abilities.
Industrial Engineering Technologist
2-4 yearsConduct independent analysis of operational processes, identifying areas for improvement in efficiency, quality, and cost. Design and implement process changes, often leading smaller projects from conception to completion. Prepare detailed reports and present findings to department managers. Provide technical support and guidance to production teams.
Key Focus Areas
Strengthen analytical skills, including statistical process control and root cause analysis. Develop proficiency in implementing Lean and Six Sigma principles. Enhance project management skills for smaller-scale initiatives. Improve communication skills for presenting findings and recommendations. Focus on independent problem-solving.
Senior Industrial Engineering Technologist
4-7 yearsLead complex process improvement projects with significant impact on organizational efficiency and profitability. Design and optimize entire operational systems or production lines. Mentor and guide junior technologists, reviewing their work and providing technical direction. Serve as a subject matter expert, making key technical decisions and influencing strategic operational planning.
Key Focus Areas
Master advanced optimization techniques, simulation modeling, and facility layout planning. Develop strong leadership and mentoring skills for junior team members. Cultivate cross-functional collaboration abilities, working with diverse departments. Focus on strategic planning for process improvements and change management. Pursue relevant certifications.
Lead Industrial Engineering Technologist
7+ years total experienceOversee multiple industrial engineering projects and initiatives across different departments or business units. Define the strategic direction for process optimization and efficiency programs. Lead and manage a team of industrial engineering technologists, responsible for their development and performance. Serve as a key advisor to senior leadership on operational excellence and strategic planning.
Key Focus Areas
Develop strategic leadership and program management capabilities. Focus on innovation, researching and integrating new technologies and methodologies. Cultivate advanced stakeholder management and negotiation skills. Drive organizational change and foster a culture of continuous improvement. Shape the long-term industrial engineering strategy.
Job Application Toolkit
Ace your application with our purpose-built resources:
Industrial Engineering Technologist Resume Examples
Proven layouts and keywords hiring managers scan for.
View examplesIndustrial Engineering Technologist Cover Letter Examples
Personalizable templates that showcase your impact.
View examplesTop Industrial Engineering Technologist Interview Questions
Practice with the questions asked most often.
View examplesIndustrial Engineering Technologist Job Description Template
Ready-to-use JD for recruiters and hiring teams.
View examplesGlobal Industrial Engineering Technologist Opportunities
Industrial Engineering Technologists apply engineering principles to optimize processes and systems globally. They enhance efficiency and productivity across manufacturing, logistics, and service industries worldwide. International demand for process improvement drives opportunities in diverse markets, from automotive in Germany to supply chains in Southeast Asia. Regulatory frameworks and industry standards vary by region, impacting project execution. Professionals pursue international roles for diverse experiences and higher earning potential, often benefiting from certifications like Lean Six Sigma.
Global Salaries
Salaries for Industrial Engineering Technologists vary significantly by region, reflecting economic conditions and industry maturity. In North America, particularly the US, annual salaries range from $60,000 to $95,000 USD, with higher figures in major industrial hubs like Michigan or Texas. Canadian technologists can expect $55,000 to $85,000 CAD (approximately $40,000-$62,000 USD).
European compensation sees a wide spectrum. Germany offers €45,000 to €70,000 ($48,000-$75,000 USD), while the UK ranges from £35,000 to £55,000 ($44,000-$69,000 USD). Eastern European countries like Poland might offer €20,000 to €35,000 ($21,000-$37,000 USD), reflecting lower costs of living. In Asia-Pacific, Australia provides AUD 70,000 to AUD 100,000 ($46,000-$66,000 USD). Singapore typically offers SGD 45,000 to SGD 75,000 ($33,000-$55,000 USD), often with attractive benefits due to high demand in manufacturing.
Latin American salaries are generally lower, ranging from $25,000 to $45,000 USD in countries like Mexico or Brazil, though purchasing power can be higher. Tax implications and social benefits, such as healthcare and pension contributions, differ substantially. For instance, European countries often have higher social security deductions but provide comprehensive public healthcare. Experience and specialized certifications, like supply chain management or quality control, significantly impact international compensation. Some multinational corporations use standardized internal pay scales, but local market adjustments are common.
Remote Work
International remote work for Industrial Engineering Technologists is less common than for software roles, given the hands-on nature of process optimization. However, some aspects, like data analysis, simulation, and report generation, are performed remotely. Industry trends show an increase in hybrid models, allowing technologists to work from home for part of the week.
Legal and tax implications for international remote work require careful consideration; technologists must understand their tax residency and host country labor laws. Time zone differences pose challenges for global team collaboration, especially when coordinating with manufacturing sites. Digital nomad opportunities for this role are limited but exist for consultants or those focusing on theoretical process design. Companies with global operations sometimes hire technologists for remote oversight of international projects, provided they can travel for site visits. Salary expectations for remote roles often align with the employer's country of origin, not the technologist's location.
Visa & Immigration
Industrial Engineering Technologists commonly utilize skilled worker visas for international employment. Popular destinations include Germany, Canada, Australia, and the US, due to their robust manufacturing sectors. Germany's Blue Card requires a recognized degree and a job offer meeting a specific salary threshold. Canada's Express Entry system assesses points for age, education, language proficiency, and work experience, often leading to permanent residency.
Australia offers various skilled migration visas, including the Skilled Independent visa (subclass 189) or employer-sponsored visas (subclass 482). Credential recognition is crucial; professional bodies in each country may require assessments of foreign degrees. For example, Engineers Australia or the German Chamber of Industry and Commerce might evaluate qualifications. Visa processing times vary, from a few months to over a year, depending on the country and visa type. Language proficiency, typically English or the local language, is often a requirement, demonstrated by standardized tests. Some countries offer fast-track options for highly sought-after engineering roles. Family members can usually accompany the primary visa holder on dependent visas.
2025 Market Reality for Industrial Engineering Technologists
Understanding the current market realities for industrial engineering technologists is crucial for strategic career development. The landscape has evolved significantly since 2023, driven by post-pandemic supply chain recalibrations and the accelerating impact of AI.
Broader economic factors, such as inflation and global trade shifts, directly influence manufacturing investments and, consequently, the demand for efficiency roles. Market realities for this profession vary considerably by experience level—entry-level positions face different challenges than senior roles—and by geographic region, with industrial clusters showing stronger demand. Company size also plays a role, as larger enterprises often have more established industrial engineering departments compared to smaller firms.
Current Challenges
Significant challenges for industrial engineering technologists include increased competition from automation and AI tools that streamline processes, potentially reducing the need for human oversight in routine tasks. Market saturation at entry-level positions is a concern as more graduates enter the field, leading to longer job search timelines.
Economic uncertainty can slow down manufacturing and logistics investments, directly impacting demand for process optimization roles. A skills gap exists where employers seek technologists proficient in advanced data analytics and AI integration, which many traditional programs do not fully cover.
Growth Opportunities
Despite challenges, strong opportunities exist for industrial engineering technologists in specific areas. Emerging roles in smart manufacturing, digital twin simulation, and AI-driven predictive maintenance are experiencing high demand. Technologists who specialize in integrating AI into supply chain optimization or production scheduling can find significant advantages.
Professionals can position themselves by acquiring certifications in advanced data analytics platforms, machine learning fundamentals, or specific industrial automation software. Underserved markets include small to medium-sized manufacturers looking to modernize their operations but lacking in-house expertise. Certain sectors, such as renewable energy manufacturing, medical device production, and advanced logistics, show consistent growth and resilience.
Developing a strong portfolio demonstrating successful implementation of efficiency projects using modern tools provides a competitive edge. This includes showing proficiency in process automation, data visualization, and root cause analysis. Strategic career moves involve targeting companies investing heavily in Industry 4.0 technologies or pursuing roles that blend operational expertise with data science skills.
Current Market Trends
The market for industrial engineering technologists in 2025 shows a nuanced demand. While core manufacturing and logistics sectors continue to seek efficiency gains, the emphasis has shifted dramatically towards technologists proficient in data analytics, automation integration, and AI-driven process optimization. Traditional roles focused solely on time-and-motion studies are less prevalent; instead, employers prioritize those who can implement and manage smart factory solutions.
Economic conditions, particularly in industries like automotive and consumer electronics, influence hiring. Some companies face market corrections and cautious investment, leading to selective hiring for critical, high-impact efficiency projects. However, the overall drive for cost reduction and productivity improvement keeps demand steady for skilled technologists.
Generative AI and advanced automation directly impact this profession. Technologists now use AI-powered simulation tools and predictive analytics to optimize workflows, inventory management, and supply chain logistics. This necessitates a strong understanding of data interpretation and system integration, moving beyond basic CAD or statistical analysis. Employer requirements increasingly include certifications in specific automation platforms or data science tools.
Salary trends are stable for experienced professionals, especially those with AI and automation expertise, reflecting the value they bring in a highly competitive global market. Entry-level salaries face pressure due to increased candidate pools and the evolving skill set demands. Geographically, demand remains strongest in established manufacturing hubs like the Midwest and Southeast United States, as well as parts of Europe and Asia, where large-scale production facilities operate. Remote work opportunities are limited for roles requiring direct site presence for process observation and physical system implementation, though some data analysis and simulation work can be done remotely.
Emerging Specializations
The industrial engineering technologist role is evolving significantly, driven by rapid advancements in automation, data analytics, and sustainable practices. These technological shifts are not merely optimizing existing processes; they are creating entirely new domains where technologists can apply their expertise in efficiency, system design, and process improvement. Understanding these emerging areas allows professionals to strategically position themselves for future career growth and leadership opportunities.
Early positioning in these cutting-edge fields can command premium compensation and accelerate career progression well into 2025 and beyond. While established specializations remain vital, focusing on emerging niches provides a distinct competitive advantage. These nascent areas often transition from specialized roles to mainstream demand within three to five years, creating a surge in job opportunities for those with relevant skills.
Pursuing emerging specializations involves a balance of risk and reward. While the initial demand might be lower, the long-term potential for impact and career advancement is substantial. Professionals who proactively develop skills in these forward-looking areas become indispensable as industries adapt to new paradigms, securing roles at the forefront of innovation.
Human-Robot Collaboration Technologist
This specialization focuses on designing, implementing, and optimizing human-robot collaboration systems within manufacturing and logistics environments. As collaborative robots (cobots) become more prevalent, technologists are needed to ensure seamless interaction between human workers and autonomous systems, improving safety, efficiency, and productivity. This involves optimizing workflows where humans and robots share tasks, ensuring ergonomic design, and integrating advanced sensors and AI for adaptive operations.
Predictive Analytics & IoT Integration Specialist
This area involves leveraging advanced data analytics and machine learning to predict equipment failures, optimize production schedules, and improve quality control in real-time. Industrial engineering technologists in this field analyze vast datasets from IoT sensors, production lines, and supply chains to identify patterns, build predictive models, and recommend proactive interventions. Their work ensures higher operational uptime, reduced waste, and more resilient systems.
Sustainable Operations & Circular Economy Technologist
This specialization applies industrial engineering principles to design and implement sustainable and circular economy models within industrial operations. Technologists focus on optimizing resource utilization, minimizing waste generation, and developing closed-loop systems for materials and energy. This includes process redesign for waste reduction, energy efficiency improvements, and the integration of renewable energy sources, aligning operations with environmental stewardship goals.
Additive Manufacturing Process Optimizer
This emerging field focuses on the design, optimization, and management of additive manufacturing (3D printing) processes for industrial production. Industrial engineering technologists ensure that 3D printing workflows are efficient, cost-effective, and integrated seamlessly into existing supply chains. They optimize material usage, print parameters, and post-processing steps to achieve desired product quality and production throughput for custom or complex components.
Digital Twin & Immersive Simulation Technologist
This specialization involves using virtual reality (VR) and augmented reality (AR) technologies to simulate, visualize, and optimize industrial processes and facility layouts. Technologists create immersive digital twins of factories, warehouses, or assembly lines to test different configurations, train workers, and identify bottlenecks before physical implementation. This reduces design errors, accelerates deployment, and enhances operational efficiency.
Pros & Cons of Being an Industrial Engineering Technologist
Making an informed career decision requires understanding both the positive aspects and the inherent challenges of a profession. The experience of an Industrial Engineering Technologist can vary significantly based on the company's culture, the specific industry sector, and the technologist's area of specialization. Furthermore, the pros and cons may shift at different career stages, with early roles focusing on data collection and senior roles on strategic implementation. It is also important to remember that what one person considers an advantage, another might see as a disadvantage, depending on individual preferences and work style. This assessment aims to provide a realistic overview to help set appropriate expectations for this career path.
Pros
Industrial Engineering Technologists play a direct role in improving operational efficiency, often seeing tangible results from their work, such as reduced waste or increased productivity.
This role offers diverse work environments, from manufacturing plants to logistics centers, providing exposure to various industrial processes and challenges.
The demand for efficiency and cost reduction ensures consistent job security and a steady need for professionals who can optimize systems and processes.
Technologists develop strong analytical and problem-solving skills, utilizing data to identify bottlenecks and design innovative solutions, which are highly transferable across industries.
The work often involves a blend of technical analysis and practical application, allowing technologists to move between desk-based analysis and hands-on observation of operations.
There are ample opportunities for continuous learning, as technologists must stay updated with new technologies, lean methodologies, and automation tools to remain effective.
The role frequently requires collaboration with various departments, including production, quality control, and management, fostering strong teamwork and communication abilities.
Cons
The role often involves meticulous data analysis and process mapping, which can be repetitive and mentally taxing for those who prefer dynamic, less detail-oriented work.
Industrial Engineering Technologists frequently face pressure to deliver measurable efficiency improvements, leading to stress if targets are aggressive or resources are limited.
Career progression can sometimes be slower compared to degreed industrial engineers, as technologists may hit a ceiling without further education or certifications.
Implementing changes can be challenging due to resistance from employees or management who are comfortable with existing processes, requiring strong negotiation and communication skills.
The work environment may involve spending significant time on factory floors or in industrial settings, which can be noisy, require safety gear, and be less comfortable than an office.
While problem-solving is a pro, the solutions often involve complex statistical analysis and software tools, requiring continuous learning and adaptation to new methodologies.
Budget constraints or limited access to advanced tools can hinder the ability to implement optimal solutions, leading to frustration when ideal improvements are not feasible.
Frequently Asked Questions
Industrial Engineering Technologists combine technical skills with process improvement. Professionals considering this role often wonder about the specific technical skills needed, the hands-on nature of the work, and how this role differs from a full Industrial Engineer. This section addresses common uncertainties about entry, daily tasks, and career progression.
What are the typical educational requirements to become an Industrial Engineering Technologist?
Becoming an Industrial Engineering Technologist typically requires an associate's degree in industrial engineering technology, manufacturing technology, or a related field. Some entry-level positions might accept candidates with a certificate and relevant hands-on experience. Practical skills in CAD software, lean manufacturing principles, and statistical process control are highly valued.
How long does it take to become job-ready as an Industrial Engineering Technologist?
The timeline to become job-ready as an Industrial Engineering Technologist usually ranges from two to four years, depending on your educational path. An associate's degree program is generally two years. If you pursue a bachelor's degree, it would take four years, though some technologists enter the field with an associate's and gain experience before potentially pursuing further education.
What is the typical work-life balance like for an Industrial Engineering Technologist?
Industrial Engineering Technologists often work full-time, standard business hours, generally 40 hours per week. However, project deadlines, system implementations, or troubleshooting production issues can sometimes require extended hours. The work-life balance is generally stable, but adaptability to production demands is important in manufacturing environments.
Is the job market for Industrial Engineering Technologists stable, or is it at risk from automation?
The job market for Industrial Engineering Technologists is stable, driven by the ongoing need for efficiency and cost reduction in manufacturing and logistics. Industries are constantly looking for ways to optimize processes and reduce waste, ensuring a consistent demand for professionals with these skills. Automation and technological advancements may change the nature of the work but are unlikely to diminish the need for human oversight and improvement.
What are the common career growth paths for an Industrial Engineering Technologist?
Industrial Engineering Technologists can advance their careers by specializing in areas like quality control, supply chain optimization, or process automation. Opportunities for promotion often include lead technologist, project manager, or even transitioning into a full Industrial Engineer role with further education. Continuous learning and certifications in new technologies are key for career progression.
Can Industrial Engineering Technologists work remotely, or is it primarily an on-site role?
While some tasks might involve remote analysis or data work, the role of an Industrial Engineering Technologist is largely hands-on and often requires presence on the production floor or in a facility. This means remote work options are less common compared to purely office-based roles. Most positions will involve on-site work to directly observe, analyze, and implement process improvements.
How does an Industrial Engineering Technologist differ from an Industrial Engineer?
The primary difference lies in scope and depth of theoretical knowledge. Industrial Engineering Technologists focus more on the practical application, implementation, and maintenance of engineered systems and processes. Industrial Engineers, with a bachelor's or master's degree, typically handle more complex design, research, and high-level strategic planning, often requiring advanced mathematical and statistical modeling.
Related Careers
Explore similar roles that might align with your interests and skills:
Engineering Technologist
A growing field with similar skill requirements and career progression opportunities.
Explore career guideIndustrial Engineer
A growing field with similar skill requirements and career progression opportunities.
Explore career guideProcess Improvement Engineer
A growing field with similar skill requirements and career progression opportunities.
Explore career guideProduction Engineer
A growing field with similar skill requirements and career progression opportunities.
Explore career guideIndustrial Engineering Technician
A growing field with similar skill requirements and career progression opportunities.
Explore career guideAssess your Industrial Engineering Technologist readiness
Understanding where you stand today is the first step toward your career goals. Our Career Coach helps identify skill gaps and create personalized plans.
Skills Gap Analysis
Get a detailed assessment of your current skills versus Industrial Engineering Technologist requirements. Our AI Career Coach identifies specific areas for improvement with personalized recommendations.
See your skills gapCareer Readiness Assessment
Evaluate your overall readiness for Industrial Engineering Technologist roles with our AI Career Coach. Receive personalized recommendations for education, projects, and experience to boost your competitiveness.
Assess your readinessSimple pricing, powerful features
Upgrade to Himalayas Plus and turbocharge your job search.
Himalayas
Himalayas Plus
Himalayas Max
Find your dream job
Sign up now and join over 100,000 remote workers who receive personalized job alerts, curated job matches, and more for free!
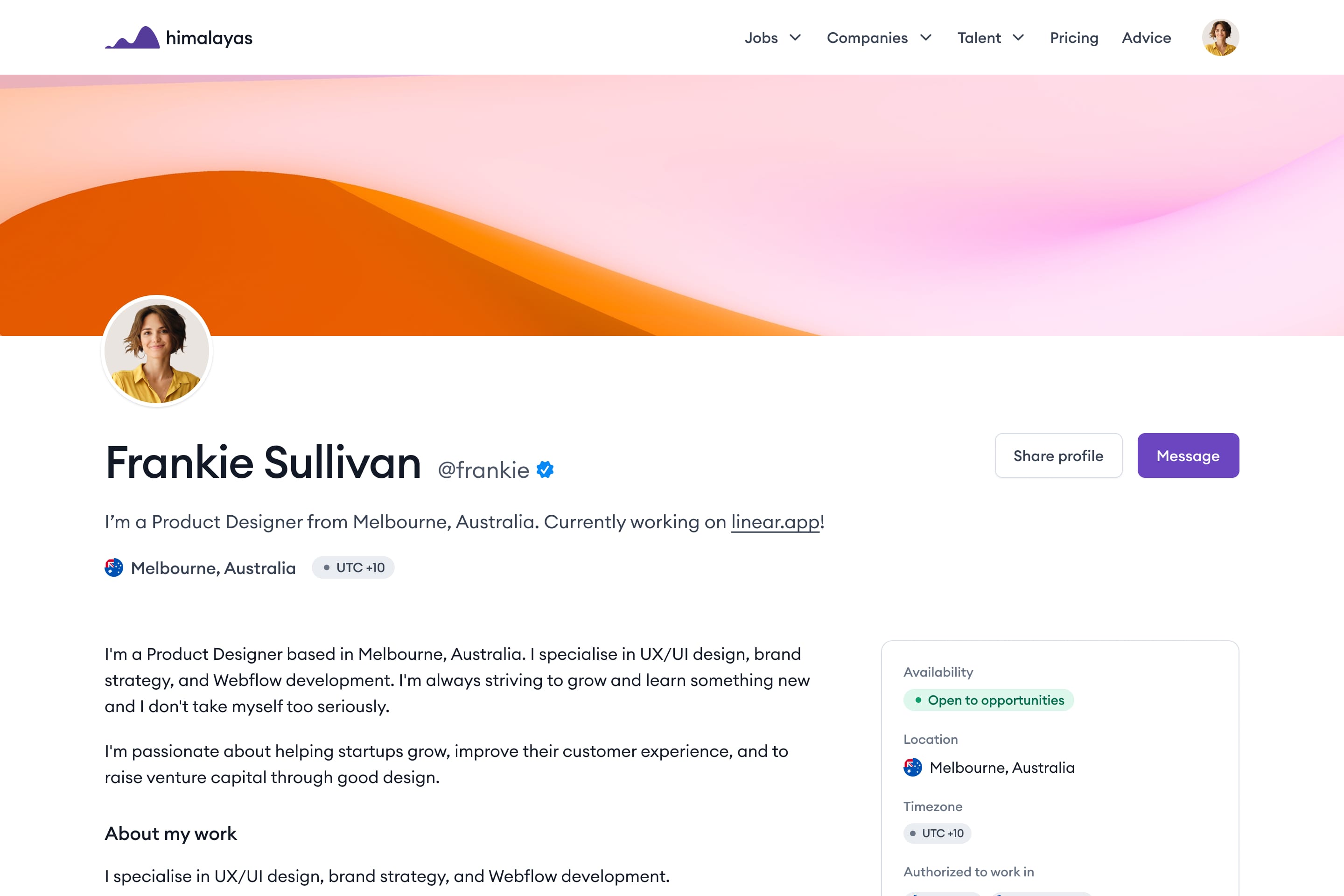