Complete Hse Engineer Career Guide
HSE Engineers are vital guardians of workplace safety and environmental compliance, designing and implementing systems that protect people, property, and the planet. They blend engineering principles with a deep understanding of regulations to prevent incidents and ensure operational sustainability, offering a career path with significant impact and demand across diverse industries.
Key Facts & Statistics
Median Salary
$100,530 USD
(U.S. Bureau of Labor Statistics, May 2023)
Range: $60k - $150k+ USD
Growth Outlook
6%
as fast as average (U.S. Bureau of Labor Statistics, 2022-2032)
Annual Openings
≈15,500
openings annually (U.S. Bureau of Labor Statistics, 2022-2032)
Top Industries
Typical Education
Bachelor's degree in engineering (e.g., environmental, chemical, mechanical) or occupational health and safety. Certifications like CSP (Certified Safety Professional) are highly valued.
What is a Hse Engineer?
An HSE Engineer specializes in safeguarding health, safety, and environmental standards within an organization, particularly in industrial, construction, or manufacturing settings. This role focuses on preventing accidents, minimizing risks, and ensuring compliance with all relevant health, safety, and environmental regulations. They are crucial for creating a safe workplace and promoting sustainable operational practices.
Unlike an HSE Manager, who typically oversees a team and sets strategic direction, an HSE Engineer is often more hands-on, focusing on the technical implementation of safety systems, conducting detailed risk assessments, and investigating incidents. They translate regulatory requirements and corporate policies into practical, actionable engineering solutions and operational procedures. Their primary value lies in systematically identifying hazards and engineering controls to mitigate them, ensuring the well-being of personnel and the protection of the environment.
What does a Hse Engineer do?
Key Responsibilities
- Conduct regular site inspections and audits to identify potential hazards and ensure compliance with HSE regulations and company policies.
- Develop and implement HSE management systems, procedures, and training programs to promote a strong safety culture among employees and contractors.
- Investigate incidents, accidents, and near-misses, determining root causes and recommending corrective actions to prevent recurrence.
- Prepare detailed HSE reports, including performance metrics, incident summaries, and compliance status, for management and regulatory bodies.
- Collaborate with project teams, contractors, and regulatory agencies to integrate HSE considerations into project planning, design, and execution phases.
- Assess and manage risks associated with operational activities, proposing mitigation strategies and emergency response plans.
- Maintain up-to-date knowledge of local and international HSE laws, standards, and best practices, ensuring organizational adherence.
Work Environment
HSE Engineers typically work in a hybrid environment, splitting their time between an office setting for planning and reporting, and various field locations such as construction sites, manufacturing plants, or industrial facilities. The work involves significant on-site presence, often in dynamic and sometimes hazardous conditions, requiring strict adherence to safety protocols.
Collaboration is constant, working closely with project managers, site supervisors, workers, and regulatory inspectors. The pace can be fast, especially during incidents or critical project phases. While a standard workweek is common, emergency situations or critical deadlines may require extended hours. Travel to different project sites is a regular part of the role, and remote work is generally limited due to the hands-on nature of site inspections and audits.
Tools & Technologies
HSE Engineers utilize a range of tools and technologies to manage safety. This includes specialized HSE management software (e.g., Intelex, Cority, Enablon) for incident tracking, audit management, and compliance reporting. They also use risk assessment matrixes, safety checklists, and permit-to-work systems.
Common productivity software like Microsoft Office Suite (Excel, PowerPoint, Word) is essential for data analysis and report generation. Depending on the industry, they might also work with environmental monitoring equipment, gas detectors, noise meters, and personal protective equipment (PPE) to conduct assessments and ensure worker safety. Familiarity with Computerized Maintenance Management Systems (CMMS) can also be beneficial for tracking equipment safety.
Hse Engineer Skills & Qualifications
HSE Engineer qualifications are structured around a core understanding of safety regulations, environmental protection, and occupational health principles. Companies prioritize candidates who can integrate these principles into engineering design and operational processes. Requirements vary significantly by industry sector; for instance, oil and gas demands deep knowledge of process safety and hazardous waste management, while manufacturing focuses on machinery safety and ergonomics. Seniority levels dictate the depth of experience and leadership capabilities expected, with entry-level roles emphasizing foundational knowledge and compliance, and senior roles requiring strategic planning and risk management expertise.
The balance between formal education, practical experience, and certifications shifts as a career progresses. A bachelor's degree provides the theoretical foundation, but hands-on experience in implementing HSE management systems and conducting risk assessments is crucial. Certifications like NEBOSH or CSP are often 'must-haves' for mid-career and senior roles, demonstrating a commitment to professional standards and specialized knowledge. While traditional degrees are common, individuals with strong technical backgrounds in engineering disciplines who acquire HSE certifications can also succeed. The skill landscape is evolving, with increasing emphasis on data analytics for predictive safety, digital tools for incident reporting, and a broader understanding of sustainability principles.
Geographic regions also influence requirements due to varying regulatory frameworks; for example, European roles often require familiarity with ISO standards and EU directives, while North American roles focus on OSHA and EPA regulations. Breadth of skills in different HSE domains is valuable early on, while depth in specific areas like process safety or environmental impact assessment becomes more critical for specialized or senior positions. A common misconception is that HSE is solely about compliance; instead, it involves proactive risk mitigation, continuous improvement, and fostering a strong safety culture.
Education Requirements
Technical Skills
- HSE Management Systems (ISO 45001, ISO 14001, OHSAS 18001)
- Risk Assessment and Hazard Identification (HAZOP, FMEA, JSA, What-If Analysis)
- Process Safety Management (PSM) and Mechanical Integrity principles
- Environmental Regulations and Compliance (EPA, local environmental laws, waste management)
- Occupational Health and Industrial Hygiene principles
- Incident Investigation and Root Cause Analysis (RCA methodologies like TapRoot, BowTie)
- Emergency Preparedness and Response Planning
- Safety Auditing and Inspection Techniques
- Data Analysis and Reporting Tools (e.g., Excel, specialized HSE software)
- Permit-to-Work (PTW) Systems and Safe Work Procedures
- Ergonomics and Human Factors Engineering
- Contractor HSE Management
Soft Skills
- Analytical Thinking: HSE Engineers must analyze complex data, incident reports, and risk assessments to identify root causes and develop effective preventive measures.
- Problem-Solving: This role requires developing practical and innovative solutions to complex safety and environmental challenges, often under operational constraints.
- Communication Skills: HSE Engineers need to clearly articulate complex technical information, safety procedures, and risk assessments to diverse audiences, including workers, management, and regulatory bodies.
- Attention to Detail: Meticulousness is critical for reviewing regulations, conducting inspections, and documenting processes to ensure compliance and prevent errors.
- Influence and Persuasion: Successfully implementing HSE initiatives often requires convincing stakeholders, from frontline workers to senior leadership, to adopt new practices or invest in safety improvements.
- Adaptability: The regulatory landscape and operational environments are constantly changing, requiring HSE Engineers to quickly adapt to new requirements and emerging risks.
- Ethical Judgment: Upholding safety and environmental standards requires strong ethical judgment, especially when balancing operational demands with compliance and risk mitigation.
- Collaboration and Teamwork: HSE Engineers frequently work with multi-disciplinary teams, including operations, maintenance, and project management, to integrate safety into all aspects of work.
How to Become a Hse Engineer
Breaking into the HSE (Health, Safety, and Environment) Engineer field involves diverse pathways, from traditional engineering degrees to specialized certifications. A common misconception is that only environmental or chemical engineering degrees qualify; however, mechanical, industrial, or even civil engineering backgrounds can be strong foundations with supplementary HSE knowledge. The timeline for entry varies significantly: a recent engineering graduate might find a junior role within 3-6 months, while a career changer from a different field might need 1-2 years to acquire necessary certifications and practical experience.
Entry strategies differ by industry and company size. Large corporations in oil & gas, manufacturing, or construction often prefer candidates with formal engineering degrees and multiple certifications, while smaller firms or consultancies might prioritize hands-on experience and a strong understanding of specific regulations. Geographic location also plays a role; regions with heavy industries like the Gulf Coast or certain parts of Europe have more concentrated opportunities. Networking with professionals in industry associations like ASSP or IOSH is crucial; these connections often open doors to mentorship and unadvertised job opportunities.
The hiring landscape increasingly values practical application of safety principles and a proactive approach to risk management, beyond just compliance. Barriers to entry can include the need for specific industry certifications (e.g., CSP, NEBOSH) and limited entry-level roles that do not require prior HSE experience. Overcoming these barriers involves strategic education, targeted internships, and demonstrating a genuine passion for safety culture through volunteer work or relevant projects.
Step 1
Step 2
Step 3
Step 4
Step 5
Step 6
Step 7
Education & Training Needed to Become a Hse Engineer
Becoming an HSE (Health, Safety, and Environment) Engineer requires a blend of formal education and specialized certifications. A bachelor's degree in engineering, environmental science, or occupational safety and health typically forms the foundational knowledge. These 4-year programs can cost between $40,000 and $100,000+ at public universities and significantly more at private institutions. They provide theoretical knowledge in areas like risk assessment, regulatory compliance, and environmental management. While a degree is often preferred, some roles, particularly in specific industries, may accept candidates with extensive experience combined with relevant certifications.
Alternative learning paths, such as professional certifications and online courses, offer more focused and time-efficient training. Certifications like the Certified Safety Professional (CSP) or Associate Safety Professional (ASP) are highly valued in the industry and require specific educational and experience prerequisites. These certification prep courses range from $1,000 to $5,000, and self-study for exams can take 6-12 months. Bootcamps specifically for HSE are less common; instead, professionals often pursue individual modules or specialized short courses in areas like hazardous waste management or industrial hygiene, typically costing $500-$2,000 per course and lasting a few days to weeks. Employers generally perceive formal degrees and nationally recognized certifications as strong indicators of a candidate's foundational knowledge and commitment to the field.
Continuous learning is crucial for HSE Engineers due to evolving regulations and technologies. Professional development often includes specialized training in new safety protocols, environmental impact assessment techniques, or specific industry standards. The cost-benefit analysis for educational investments should consider the employer's industry; for instance, oil and gas or manufacturing may prioritize specific certifications more than other sectors. Practical experience, often gained through internships or entry-level roles, complements theoretical knowledge by providing real-world application of safety and environmental principles. Educational needs also vary by seniority; entry-level roles might focus on general safety principles, while senior roles demand expertise in complex regulatory frameworks and strategic environmental planning.
Hse Engineer Salary & Outlook
Compensation for an HSE Engineer varies significantly, shaped by numerous factors beyond just base salary. Geographic location is a primary driver; high-cost-of-living areas or regions with dense industrial activity, such as the Gulf Coast in the U.S. or major European industrial hubs, typically offer higher pay due to demand and economic conditions. Conversely, salaries may adjust downward in areas with lower living costs or less industrial concentration.
Experience, specialized certifications (e.g., CSP, CIH), and specific industry expertise (e.g., oil & gas, manufacturing, construction) dramatically influence earning potential. An HSE Engineer with a niche in process safety management for chemical plants will likely command a premium over a generalist. Total compensation packages often include performance bonuses, which can be substantial, along with comprehensive benefits like health insurance, retirement plans (401k matching), and professional development allowances for certifications or advanced degrees. Some companies also offer equity options, particularly in rapidly expanding sectors.
Industry-specific trends, such as increased regulatory scrutiny or a company's commitment to sustainability, can drive salary growth. Engineers adept at navigating complex regulatory frameworks or implementing innovative safety technologies gain significant negotiation leverage. Remote work can impact salary ranges, with some companies adjusting pay based on the employee's location, while others maintain a standard rate, opening opportunities for geographic arbitrage. International markets also present varied compensation structures, with U.S. dollar figures providing a benchmark against global standards.
Salary by Experience Level
Level | US Median | US Average |
---|---|---|
Junior HSE Engineer | $70k USD | $75k USD |
HSE Engineer | $90k USD | $95k USD |
Senior HSE Engineer | $115k USD | $120k USD |
Lead HSE Engineer | $140k USD | $145k USD |
HSE Manager | $160k USD | $165k USD |
HSE Director | $190k USD | $200k USD |
Market Commentary
The job market for HSE Engineers shows consistent demand, driven by stringent regulatory environments and an increasing corporate focus on sustainability and worker well-being. Projections indicate a steady growth outlook, with the Bureau of Labor Statistics forecasting a 5-7% increase in related occupations over the next decade. This growth is fueled by ongoing industrial activity, infrastructure development, and the need to comply with evolving environmental and safety standards.
Emerging opportunities for HSE Engineers include roles focused on environmental compliance for renewable energy projects, digital safety management systems, and the integration of AI and IoT for predictive hazard analysis. Automation and AI are not expected to displace HSE Engineers but rather to enhance their capabilities by automating routine data collection and analysis, allowing them to focus on strategic risk management and proactive safety measures. This shift requires continuous learning in data analytics and technology integration.
Supply and demand dynamics are relatively balanced, though specialized areas like process safety or environmental remediation may experience shortages of qualified candidates. Geographic hotspots for HSE Engineers include industrial corridors in Texas, Louisiana, and Pennsylvania, as well as states with significant manufacturing and construction sectors. The profession is generally recession-resistant, as safety and environmental compliance remain critical regardless of economic cycles. Future-proofing involves embracing digital transformation, understanding global regulatory frameworks, and developing strong communication skills to drive a safety culture within organizations.
Hse Engineer Career Path
Career progression for an HSE Engineer typically involves a gradual increase in responsibility, technical depth, and leadership. Professionals can advance along an individual contributor (IC) track, focusing on deep technical expertise, or transition into a management track, leading teams and strategic initiatives. Both paths require continuous learning and adapting to evolving safety regulations and environmental standards.
Advancement speed depends on performance, the complexity of projects handled, and a willingness to specialize in areas like process safety, environmental compliance, or occupational health. Company size significantly influences progression; larger corporations often have more structured paths and specialized roles, while smaller firms may offer broader exposure but fewer formal steps. Networking within industry associations and pursuing advanced certifications are crucial for visibility and opening new opportunities.
Lateral moves between different industries, such as manufacturing, oil and gas, or construction, are common, allowing engineers to broaden their experience. This field also sees professionals pivot into roles like risk management or sustainability consulting. Industry reputation, built through consistent performance and contributions to safety best practices, plays a vital role in career trajectory and leadership opportunities.
Junior HSE Engineer
0-2 yearsKey Focus Areas
HSE Engineer
2-5 yearsKey Focus Areas
Senior HSE Engineer
5-8 yearsKey Focus Areas
Lead HSE Engineer
8-12 yearsKey Focus Areas
HSE Manager
12-18 yearsKey Focus Areas
HSE Director
18+ yearsKey Focus Areas
Junior HSE Engineer
0-2 yearsSupport senior engineers in conducting routine safety inspections, environmental audits, and risk assessments. Assist with incident investigations, data collection, and report preparation. Participate in safety training sessions and contribute to developing basic HSE documentation. Work under direct supervision, focusing on learning and executing defined tasks.
Key Focus Areas
Develop foundational knowledge of HSE regulations and standards (OSHA, EPA, ISO 14001, ISO 45001). Master basic risk assessment techniques and incident investigation protocols. Focus on understanding site-specific safety procedures and environmental permits. Build strong communication skills for effective reporting and basic training delivery.
HSE Engineer
2-5 yearsConduct independent HSE inspections, audits, and risk assessments for specific processes or departments. Lead incident investigations, analyze data, and recommend corrective actions. Develop and deliver safety training programs. Ensure compliance with regulatory requirements and internal HSE policies. Manage smaller HSE projects with moderate supervision.
Key Focus Areas
Deepen expertise in specific HSE areas like chemical safety, ergonomics, or waste management. Enhance analytical skills for identifying root causes of incidents and developing preventive measures. Improve project management capabilities for implementing HSE programs. Begin developing strong stakeholder engagement and persuasive communication skills.
Senior HSE Engineer
5-8 yearsLead complex HSE projects and initiatives, often across multiple departments or sites. Serve as a technical expert, providing guidance on regulatory compliance and best practices. Oversee incident management processes, ensuring thorough investigation and effective corrective actions. Develop and implement comprehensive HSE programs, contributing to policy development. Provide mentorship to junior engineers.
Key Focus Areas
Cultivate advanced risk management and hazard identification skills. Develop a strategic understanding of HSE management systems and their integration into business operations. Mentor junior team members and provide technical guidance. Pursue specialized certifications relevant to the industry (e.g., CSP, CIH, REM). Enhance negotiation and conflict resolution abilities.
Lead HSE Engineer
8-12 yearsCoordinate and oversee HSE activities for a major project, facility, or a specific functional area. Guide a team of HSE engineers, assigning tasks and reviewing their work. Develop and implement HSE strategies aligned with organizational goals. Act as a primary point of contact for regulatory bodies and external audits. Drive continuous improvement in HSE performance.
Key Focus Areas
Master strategic planning for HSE initiatives and resource allocation. Develop strong leadership and team coordination skills. Focus on influencing organizational culture towards a proactive safety mindset. Build expertise in change management and implementing new HSE technologies. Enhance presentation skills for executive-level communication.
HSE Manager
12-18 yearsManage the overall HSE function for a significant business unit or a large facility. Develop and execute long-term HSE strategies, policies, and budgets. Lead, mentor, and develop a team of HSE professionals. Ensure regulatory compliance and manage relationships with governmental agencies. Drive significant improvements in safety performance and environmental sustainability across the organization.
Key Focus Areas
Develop robust financial management skills related to HSE budgets and investments. Cultivate executive leadership, strategic thinking, and organizational development capabilities. Focus on building high-performing teams and fostering a strong safety culture. Enhance cross-functional collaboration and external stakeholder management. Pursue advanced business or leadership training.
HSE Director
18+ yearsProvide executive leadership for the entire organization's HSE strategy and performance. Set the vision, direction, and strategic objectives for all HSE programs globally or nationally. Oversee compliance with all applicable laws and regulations. Represent the company in high-level industry forums and with regulatory authorities. Responsible for fostering a world-class safety culture and achieving industry-leading HSE results.
Key Focus Areas
Master enterprise-wide risk management and global HSE governance. Develop expertise in corporate social responsibility and sustainability reporting. Focus on board-level communication and influencing C-suite decisions. Cultivate strategic partnerships with industry leaders and regulatory bodies. Drive innovation in HSE practices and technologies.
Job Application Toolkit
Ace your application with our purpose-built resources:
Global Hse Engineer Opportunities
HSE Engineers are globally essential for ensuring workplace safety, environmental compliance, and health standards across industries. Their expertise is highly transferable, with strong demand in manufacturing, oil and gas, construction, and renewable energy sectors worldwide. Regulatory frameworks vary by country, requiring engineers to adapt to local laws and international standards like ISO 45001. Professionals often seek international roles for career growth, diverse project experience, and exposure to different industrial practices.
Global Salaries
HSE Engineer salaries vary significantly by region, industry, and experience. In North America, particularly the U.S. and Canada, salaries range from $70,000 to $120,000 USD annually for experienced professionals. European salaries typically fall between €45,000 and €85,000 (approximately $48,000-$90,000 USD), with higher compensation in Scandinavia and Western Europe. For instance, in Germany, an HSE Engineer might earn €55,000-€90,000, while in the UK, it could be £40,000-£75,000.
Asia-Pacific markets, such as Australia and Singapore, offer strong salaries from AUD 80,000 to AUD 140,000 (approx. $53,000-$93,000 USD) and SGD 60,000 to SGD 110,000 (approx. $44,000-$81,000 USD), respectively. The Middle East, especially UAE and Saudi Arabia, provides competitive, often tax-free, compensation ranging from $60,000 to $100,000 USD due to robust oil and gas and construction sectors. Latin America and emerging markets generally offer lower base salaries, perhaps $30,000 to $60,000 USD, but these must be weighed against lower living costs.
Purchasing power parity is crucial; a lower nominal salary in one country might offer a comparable or better quality of life than a higher salary in a high-cost region. International roles often include additional benefits like housing allowances, relocation packages, and health insurance, which significantly boost the overall compensation package. Tax implications also differ, with some countries having higher income taxes but more social benefits. Experience and specialized certifications, such as NEBOSH or OSHA, enhance earning potential globally.
Remote Work
True remote work for HSE Engineers is limited given the hands-on nature of site inspections, audits, and incident investigations. However, hybrid models are becoming more common, allowing for remote work on documentation, policy development, training material creation, and data analysis. Some roles might involve extensive travel to various sites rather than a fixed office.
Legal and tax implications for international remote work are complex, often requiring the employer to have a legal entity in the remote worker's country. Time zone differences can pose challenges for global team collaboration. Digital nomad visas are generally not suitable for this role due to the need for physical presence. Companies in consulting or large multinational corporations might offer more flexible arrangements. Remote work typically impacts salary expectations, often aligning with the cost of living in the employee's location rather than the company's base. Equipment and a reliable internet connection are essential for any remote component of the role.
Visa & Immigration
HSE Engineers often qualify for skilled worker visas in many countries due to their specialized technical expertise. Popular destinations include Canada (Express Entry), Australia (Skilled Nominated/Independent visas), the UK (Skilled Worker visa), and Germany (EU Blue Card). Requirements typically include a relevant engineering degree, professional experience, and sometimes English or local language proficiency (e.g., German for Germany).
Credential recognition is vital; engineering degrees usually require assessment by professional bodies like Engineers Australia or the UK Engineering Council. Visa processing times vary, from a few months to over a year, depending on the country and visa type. Many skilled worker visas offer pathways to permanent residency after several years of employment. Some countries prioritize professionals in high-demand fields, potentially offering faster processing. Family visas for spouses and dependents are generally available, contingent on the primary applicant's visa approval. Understanding specific country immigration points systems and occupation lists is crucial for a successful application.
2025 Market Reality for Hse Engineers
Understanding current market conditions is vital for any HSE Engineer seeking career advancement or new opportunities. The landscape for this profession has evolved significantly from 2023 to 2025, shaped by post-pandemic shifts and the accelerating integration of AI.
Broader economic factors, such as industrial growth rates and regulatory changes, directly influence demand for safety professionals. Market realities also vary by experience level, with senior engineers often finding more specialized roles, and by geographic region, where industrial activity dictates job availability. Company size also matters; large corporations often have structured HSE departments, while smaller firms might seek multifaceted engineers. This analysis provides an honest assessment of these dynamics, helping set realistic expectations.
Current Challenges
HSE Engineers face increased competition, particularly for entry-level roles, as automation and AI tools improve hazard identification, allowing some companies to maintain safety oversight with fewer personnel. Economic slowdowns in heavy industries can directly reduce project starts, impacting hiring. Employers demand a broader skill set, including data analytics and AI tool proficiency, creating a gap for candidates without these updated capabilities.
Growth Opportunities
Strong demand for HSE Engineers persists in the renewable energy sector, including wind farms and solar installations, due to new safety challenges and regulatory needs. Infrastructure development projects, such as smart cities and transportation networks, also offer significant opportunities, particularly for engineers who can integrate digital safety systems.
Emerging specializations like AI-driven predictive safety analytics, cybersecurity for industrial control systems, and environmental compliance for novel materials present growing opportunities. Professionals who upskill in data science, machine learning applications for risk assessment, and advanced sensor technologies will gain a strong competitive edge. Underserved markets, such as developing economies investing heavily in infrastructure, or remote industrial sites, can offer unique roles.
Market corrections may create opportunities for strategic career moves, as companies re-evaluate their safety protocols and invest in long-term resilience. Sectors focused on critical national infrastructure and advanced manufacturing remain resilient. Timing educational investments in areas like industrial hygiene, occupational health, or specific industry certifications can position engineers favorably. Focusing on niche areas like process safety management in chemical plants or complex construction site safety also provides a distinct advantage in a crowded market.
Current Market Trends
HSE Engineer hiring in 2025 shows steady demand in sectors like renewable energy and infrastructure development, while traditional oil & gas and manufacturing see more selective hiring. Companies prioritize roles that can integrate digital safety solutions and data analytics for predictive risk management. The drive for sustainability and ESG compliance boosts the need for engineers who can implement robust environmental and safety frameworks.
Economic conditions influence project investments, directly affecting the number of HSE Engineer positions. Layoffs in some traditional industries have shifted talent towards growth sectors like clean energy. Generative AI and advanced analytics are transforming the field, enabling more efficient risk assessments and compliance monitoring. Employers now seek candidates who can leverage these technologies, moving beyond manual inspections to proactive, data-driven safety strategies.
Salary trends for experienced HSE Engineers remain strong, especially for those with specialized certifications or expertise in emerging technologies. However, market saturation exists at the junior level, making differentiation crucial. Remote work for HSE roles is less common due to the hands-on nature of site safety, but some design and compliance aspects can be managed remotely. Geographic variations are significant; strong demand persists in industrial hubs and regions with major infrastructure projects, such as the Gulf Coast in the U.S. or rapidly developing Asian markets. Hiring often aligns with project lifecycles, leading to cyclical demand rather than constant, linear growth.
Emerging Specializations
The field of Health, Safety, and Environment (HSE) engineering is undergoing significant transformation, driven by rapid technological advancements and evolving global standards. As industries embrace digital transformation, automation, and sustainable practices, new specialization opportunities are emerging for HSE engineers. These shifts are creating distinct career paths that demand a forward-looking perspective.
Early positioning in these emerging areas is crucial for career advancement in 2025 and beyond. Professionals who develop expertise in cutting-edge domains like AI-driven safety analytics or sustainable energy safety will find themselves at the forefront of the industry. This proactive approach often leads to premium compensation and accelerated career growth, as demand for these specialized skills outpaces supply.
While established HSE specializations remain vital, a strategic balance involves understanding where future growth lies. Emerging areas, though sometimes requiring initial investment in new skills, promise substantial long-term returns. Many of these niche areas are currently gaining traction and are projected to become mainstream within the next three to five years, creating a significant number of job opportunities. Evaluating the risk and reward of specializing in these cutting-edge fields involves assessing the pace of technological adoption and regulatory evolution within specific industries.
AI-Driven Safety Analytics Engineer
This specialization focuses on integrating artificial intelligence and machine learning tools to predict and prevent workplace incidents. It involves developing algorithms that analyze vast datasets from sensors, incident reports, and operational logs to identify hidden patterns and potential hazards. HSE engineers in this area design predictive models, implement smart monitoring systems, and create AI-driven risk assessment frameworks, moving safety management from reactive to proactive. This shift enhances operational efficiency and significantly reduces accident rates.
Sustainable Energy Safety Engineer
This area concentrates on ensuring the safety and environmental compliance of renewable energy infrastructure, including solar farms, wind turbines, and hydrogen production facilities. It involves developing specialized safety protocols for energy storage systems, high-voltage equipment, and unique environmental impacts associated with clean energy generation. Professionals in this field address emerging hazards in green technologies, contributing to the safe expansion of sustainable energy. Their work is critical for the global transition to a low-carbon economy.
Digital Twin for HSE Engineer
This specialization applies advanced digital twin technology to create virtual models of industrial facilities for comprehensive safety simulations and environmental impact assessments. HSE engineers build and manage these digital replicas, simulating potential hazards, testing emergency response plans, and optimizing environmental controls in a risk-free virtual environment. This allows for proactive identification of design flaws and operational risks before physical implementation, significantly enhancing safety and regulatory compliance. It represents a paradigm shift in risk management.
Autonomous Systems Safety Engineer
This emerging field addresses the unique safety and environmental challenges posed by autonomous systems, robotics, and drone operations in industrial settings. HSE engineers in this area develop safety standards and operational guidelines for human-robot collaboration, autonomous vehicle navigation in hazardous environments, and drone-based inspections. They ensure that the integration of these technologies enhances safety without introducing new, unforeseen risks. Their expertise is critical for industries adopting advanced automation.
Cyber-Physical Safety Engineer
This specialization focuses on the intersection of cybersecurity and operational technology (OT) within industrial control systems (ICS) to protect critical infrastructure from cyber-physical threats. HSE engineers in this role assess cyber risks to safety-critical systems, develop protocols to prevent cyber-attacks that could lead to physical harm or environmental damage, and ensure compliance with emerging cybersecurity regulations. They bridge the gap between IT security and industrial safety, safeguarding complex operational environments. Their work is vital for protecting modern industrial plants.
Pros & Cons of Being a Hse Engineer
Making informed career decisions requires a clear understanding of both the benefits and challenges associated with a profession. The experience of an HSE Engineer can vary significantly based on the specific industry, company culture, project scale, and geographical location. What one individual perceives as an advantage, another might see as a challenge, depending on personal values, lifestyle preferences, and career stage. For instance, extensive travel might appeal to some but be a major drawback for others. This assessment provides a realistic overview of the typical pros and cons to help set appropriate expectations.
Pros
- HSE Engineers play a crucial role in preventing accidents and ensuring worker well-being, providing a strong sense of purpose and direct impact on safety outcomes.
- The demand for HSE professionals remains consistent across diverse industries, including oil and gas, construction, manufacturing, and energy, offering strong job security and varied career paths.
- HSE Engineers develop a broad skill set encompassing risk assessment, regulatory compliance, incident investigation, and training, which are highly transferable across different sectors and roles.
- The role often involves working on complex projects and interacting with various stakeholders, including management, engineers, and site workers, offering continuous intellectual stimulation and problem-solving opportunities.
- Salaries for experienced HSE Engineers are generally competitive, especially in high-risk industries, reflecting the critical nature of their responsibilities and specialized expertise.
- HSE Engineers gain deep insights into operational processes and management systems, which can open doors to broader management roles or specialized consulting opportunities.
- The profession offers a dynamic work environment where no two days are exactly alike, involving a mix of field visits, office work, training sessions, and strategic planning, which avoids monotony.
Cons
- HSE Engineers often face significant pressure, especially during incident investigations or regulatory audits, where mistakes can have severe legal and safety consequences.
- The role requires extensive travel to various project sites, often in remote or challenging environments, which can disrupt personal life and lead to prolonged periods away from home.
- HSE Engineers must constantly update their knowledge of evolving local and international safety regulations, standards, and best practices, which demands continuous learning and certification.
- Dealing with non-compliance or resistance from management or workers regarding safety protocols can be frustrating, requiring strong negotiation and communication skills to enforce standards.
- The job can expose individuals to hazardous conditions, such as construction sites or industrial facilities, requiring strict adherence to personal protective equipment and safety procedures.
- Career progression can sometimes feel slow or limited within a single organization, often requiring moves between companies or industries to advance to higher-level management roles.
- HSE Engineers frequently handle distressing situations, including accident investigations and fatality reviews, which can take a significant emotional and psychological toll over time and require strong resilience and coping mechanisms to manage.
Frequently Asked Questions
HSE Engineers face distinct challenges balancing regulatory compliance with operational efficiency and workforce safety. This section addresses common questions about transitioning into this vital role, from required qualifications and daily responsibilities to career growth and the impact of technological advancements on safety practices.
What are the essential educational qualifications and certifications needed to become an HSE Engineer?
Becoming an HSE Engineer typically requires a bachelor's degree in engineering (e.g., chemical, environmental, industrial) or a related scientific field. Many professionals also pursue certifications like the Certified Safety Professional (CSP) or Associate Safety Professional (ASP) to enhance their credentials. Practical experience through internships or entry-level safety roles is also crucial for demonstrating competence.
How long does it typically take to become job-ready as an HSE Engineer if I'm starting from scratch?
The timeline varies significantly based on your starting point. If you have an engineering degree, you might gain entry-level positions within 1-2 years of graduation, often after completing an internship. For those transitioning from other fields, acquiring a relevant degree or certifications, along with practical experience, can take 3-5 years. Continuous learning is also vital throughout your career.
What is the job market outlook and security like for HSE Engineers?
HSE Engineers are critical across various industries, including oil and gas, manufacturing, construction, and consulting. The job market remains stable due to increasing regulatory requirements and a growing emphasis on workplace safety. Demand is particularly strong in industries with high operational risks, ensuring good job security for qualified professionals.
What can I expect regarding work-life balance and potential travel requirements in this role?
Work-life balance for an HSE Engineer can vary. While many roles are standard 9-to-5, project-based work or incident response might require longer hours, especially in industries like construction or oil and gas. Travel to different sites is also common, which impacts personal time. However, many companies prioritize employee well-being, offering flexible arrangements when possible.
What are the typical salary expectations for an HSE Engineer at different career stages?
The salary for an HSE Engineer varies based on experience, industry, location, and certifications. Entry-level positions might start around $60,000-$75,000 annually. Mid-career professionals with 5-10 years of experience can earn $80,000-$120,000, while senior or specialized roles can exceed $150,000. Certifications and a strong track record significantly boost earning potential.
What are the common career growth paths and advancement opportunities for an HSE Engineer?
Career growth for an HSE Engineer is robust. You can advance to senior HSE Engineer, HSE Manager, or Director of HSE roles, overseeing larger teams and strategic initiatives. Specialization in areas like industrial hygiene, ergonomics, or environmental compliance also opens new pathways. Consulting or moving into regulatory bodies are also viable long-term options.
Do I need a computer science degree to succeed as an HSE Engineer, or are there alternative educational paths?
No, a computer science degree is not a prerequisite. While some roles benefit from data analysis skills, the core of HSE Engineering lies in applying engineering principles to safety and environmental management. Degrees in chemical, environmental, industrial, or mechanical engineering are more common and directly relevant. You can acquire necessary data skills through short courses or certifications.
What are the biggest challenges and common misconceptions about being an HSE Engineer?
Key challenges include staying updated with evolving regulations, managing complex risks across diverse operations, and fostering a strong safety culture among all employees. You will also need to effectively communicate technical safety information to non-technical stakeholders and balance safety priorities with production demands. Continuous learning and strong interpersonal skills are essential.
Related Careers
Explore similar roles that might align with your interests and skills:
Hse Advisor
A growing field with similar skill requirements and career progression opportunities.
Explore career guideHse Coordinator
A growing field with similar skill requirements and career progression opportunities.
Explore career guideHse Manager
A growing field with similar skill requirements and career progression opportunities.
Explore career guideHse Specialist
A growing field with similar skill requirements and career progression opportunities.
Explore career guideSafety Engineer
A growing field with similar skill requirements and career progression opportunities.
Explore career guideAssess your Hse Engineer readiness
Understanding where you stand today is the first step toward your career goals. Our Career Coach helps identify skill gaps and create personalized plans.
Skills Gap Analysis
Get a detailed assessment of your current skills versus Hse Engineer requirements. Our AI Career Coach identifies specific areas for improvement with personalized recommendations.
See your skills gapCareer Readiness Assessment
Evaluate your overall readiness for Hse Engineer roles with our AI Career Coach. Receive personalized recommendations for education, projects, and experience to boost your competitiveness.
Assess your readinessSimple pricing, powerful features
Upgrade to Himalayas Plus and turbocharge your job search.
Himalayas
Himalayas Plus
Himalayas Max
Find your dream job
Sign up now and join over 100,000 remote workers who receive personalized job alerts, curated job matches, and more for free!
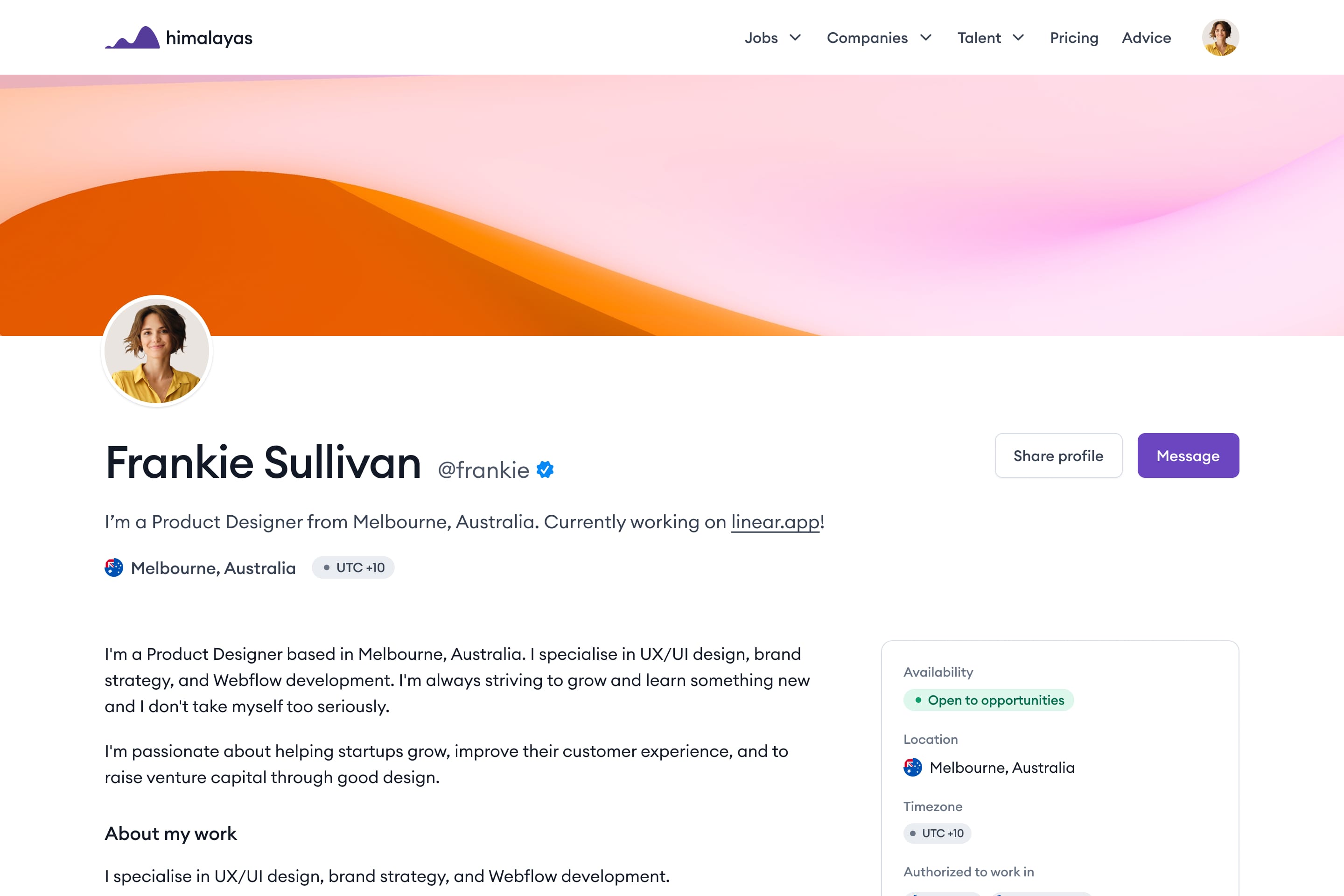