Complete Equipment Engineer Career Guide
Equipment engineers are the backbone of high-tech manufacturing, ensuring complex machinery operates at peak efficiency and precision. They design, develop, and maintain the specialized tools and systems critical for producing everything from semiconductors to pharmaceuticals, directly impacting product quality and production costs. This role offers a unique blend of mechanical, electrical, and process engineering challenges, making it ideal for those who thrive on hands-on problem-solving and continuous improvement in dynamic industrial environments.
Key Facts & Statistics
Median Salary
$99,570 USD
(U.S. national median, BLS May 2023)
Range: $65k - $150k+ USD
Growth Outlook
6%
as fast as average (BLS)
Annual Openings
≈21,000
openings annually (BLS)
Top Industries
Typical Education
Bachelor's degree in Mechanical, Electrical, or Industrial Engineering
What is an Equipment Engineer?
An Equipment Engineer is a specialized professional focused on the design, installation, maintenance, and optimization of machinery and systems used in manufacturing and production processes. They ensure that complex equipment operates at peak efficiency, reliability, and safety, playing a critical role in minimizing downtime and maximizing output. This role bridges the gap between mechanical engineering principles and practical application in a production environment.
Unlike a general Mechanical Engineer who might focus on product design, or a Maintenance Technician who primarily executes repairs, an Equipment Engineer takes a holistic view of equipment lifecycle management. They are responsible for strategic planning, continuous improvement, and advanced troubleshooting, ensuring the equipment not only functions but contributes effectively to business goals. Their expertise is crucial in industries ranging from semiconductors and pharmaceuticals to automotive and food processing, where precision and consistent operation of machinery are paramount.
What does an Equipment Engineer do?
Key Responsibilities
- Develop and implement preventative maintenance programs for complex manufacturing equipment to minimize downtime and extend asset lifespan.
- Diagnose and troubleshoot intricate mechanical, electrical, and pneumatic issues on production machinery, often requiring specialized diagnostic tools.
- Design and execute equipment upgrades or modifications to improve efficiency, yield, and safety in manufacturing processes.
- Collaborate with cross-functional teams, including production, quality, and R&D, to integrate new equipment and optimize existing systems.
- Analyze equipment performance data and maintenance records to identify trends and propose continuous improvement initiatives.
- Manage spare parts inventory and procurement, ensuring critical components are available to support ongoing operations without excessive stock.
- Conduct root cause analysis for equipment failures, implementing corrective actions to prevent recurrence and enhance reliability.
Work Environment
Equipment engineers primarily work in manufacturing plants, production facilities, or laboratories. The environment can range from cleanroom settings in semiconductor or pharmaceutical industries to more robust factory floors. They spend a significant portion of their time directly on the production line, interacting with machinery, and collaborating with operators and technicians.
The role often involves a mix of hands-on troubleshooting and desk-based analysis, documentation, and planning. Work hours are typically standard business hours, but on-call duties or irregular shifts may be necessary to address critical equipment breakdowns that impact production. The pace is often dynamic, responding to urgent issues while also driving long-term improvement projects. Collaboration with various teams, including production, quality, and R&D, is constant.
Tools & Technologies
Equipment engineers routinely use a variety of specialized tools and software to manage and maintain complex machinery. They utilize Computerized Maintenance Management Systems (CMMS) such as SAP PM, Maximo, or Oracle EAM for scheduling maintenance, tracking work orders, and managing inventory. For diagnostics, they employ multimeters, oscilloscopes, thermal imaging cameras, and vibration analysis tools.
They also work with Programmable Logic Controllers (PLCs) and Human-Machine Interfaces (HMIs), often requiring knowledge of programming languages like Ladder Logic or Structured Text for troubleshooting and optimizing machine control. CAD software like AutoCAD or SolidWorks helps them design modifications or analyze equipment schematics. Furthermore, they use statistical analysis software like JMP or Minitab to interpret equipment performance data and identify areas for improvement.
Equipment Engineer Skills & Qualifications
Equipment Engineers play a critical role in the lifecycle of manufacturing and industrial machinery, ensuring optimal performance, reliability, and safety. Their qualifications are structured around a strong foundation in engineering principles, coupled with hands-on experience in specific equipment types. Requirements for this role vary significantly based on the industry, company size, and the complexity of the machinery involved.
For instance, an Equipment Engineer in the semiconductor industry needs deep knowledge of ultra-precision tools and vacuum systems, while one in a food processing plant focuses on hygiene, automation, and material handling systems. Entry-level positions often require a bachelor's degree and some internship experience. Senior roles, especially in R&D or highly specialized fields, might prefer a master's degree or extensive practical experience combined with a strong track record.
Practical experience and certifications often outweigh formal education beyond a bachelor's degree. Many companies value candidates who have completed industry-specific training or hold certifications in areas like Lean Six Sigma, robotics, or specific PLC programming. The skill landscape for Equipment Engineers is evolving rapidly with the advent of Industry 4.0, predictive maintenance, and advanced automation. This means a continuous learning mindset and adaptability to new technologies are becoming crucial. While breadth in various equipment types is beneficial for generalists, depth in specific, high-value machinery is often preferred for specialized roles. Misconceptions include believing the job is solely about repair; it encompasses design, optimization, and strategic asset management.
Education Requirements
Technical Skills
- PLC Programming (e.g., Siemens, Allen-Bradley, Rockwell Automation) for automation control
- SCADA/HMI systems for data acquisition and process visualization
- CAD software (e.g., SolidWorks, AutoCAD) for equipment design and layout
- Predictive Maintenance Technologies (e.g., vibration analysis, thermal imaging, acoustic analysis)
- Robotics and Automated Systems integration and troubleshooting
- Hydraulic and Pneumatic Systems design and maintenance
- Control Systems troubleshooting and calibration
- Process Instrumentation and Sensor technologies
- Material Science principles and selection for machinery components
- Statistical Process Control (SPC) for quality and performance monitoring
- Lean Manufacturing and Six Sigma methodologies for process optimization
- Reliability Engineering principles (e.g., FMEA, RCM) for asset management
Soft Skills
- Problem-solving and Root Cause Analysis: Equipment Engineers frequently diagnose complex machinery malfunctions, requiring systematic problem-solving to identify root causes and implement effective solutions.
- Attention to Detail and Precision: Working with intricate machinery and technical specifications demands meticulous attention to detail to ensure proper installation, calibration, and maintenance, preventing costly errors.
- Technical Communication and Documentation: Engineers must clearly articulate complex technical issues and solutions to diverse audiences, including technicians, management, and vendors, and accurately document procedures and findings.
- Adaptability and Continuous Learning: The rapid evolution of industrial technology requires Equipment Engineers to continuously learn new systems, software, and methodologies, adapting to changing equipment and industry standards.
- Safety Consciousness: A paramount soft skill, ensuring all operations, maintenance, and design considerations prioritize safety for personnel and equipment, adhering to strict industry regulations.
- Collaboration and Interdisciplinary Teamwork: Equipment Engineers often work with production, R&D, and quality control teams, requiring strong collaborative skills to integrate equipment solutions into broader operational goals.
- Time Management and Prioritization: Managing multiple equipment projects, maintenance schedules, and unexpected breakdowns demands effective time management and the ability to prioritize tasks under pressure.
- Analytical Thinking and Data Interpretation: Utilizing performance data, sensor readings, and historical maintenance logs to analyze equipment trends, predict failures, and optimize operational efficiency.
How to Become an Equipment Engineer
Breaking into the Equipment Engineer field offers multiple pathways, typically requiring a strong technical foundation. Traditional routes involve a bachelor's degree in engineering, often mechanical, electrical, or industrial engineering. Non-traditional entry points exist for those with extensive hands-on experience in equipment maintenance or technician roles, who then pursue certifications or associate degrees to bridge knowledge gaps.
Timeline expectations vary significantly; a complete beginner pursuing a four-year degree might take 4-5 years, plus internship experience. A career changer with a related technical background could transition in 1-2 years by focusing on specialized certifications and practical projects. Entry strategies also depend on company size and industry sector; large manufacturing firms or semiconductor companies often prefer candidates with formal degrees, while smaller operations or startups might value demonstrated problem-solving skills and hands-on experience over specific academic credentials. Geographic location plays a role, with more opportunities in industrial or tech hubs.
A common misconception is that all Equipment Engineer roles are identical; in reality, responsibilities vary widely from designing new machinery to optimizing existing production lines or managing maintenance schedules. Building a strong project portfolio and networking within relevant industries, such as manufacturing, aerospace, or semiconductors, is crucial. The hiring landscape values adaptability, problem-solving, and a blend of theoretical knowledge with practical application. Overcoming barriers often involves showcasing relevant projects and internships to compensate for limited direct experience.
Obtain a foundational engineering degree, ideally a Bachelor of Science in Mechanical, Electrical, Industrial, or Manufacturing Engineering. This academic background provides the essential theoretical knowledge in thermodynamics, materials science, control systems, and process optimization that forms the core of an Equipment Engineer's expertise. Aim for a program accredited by ABET or an equivalent international body.
Gain practical experience through internships, co-op programs, or entry-level technician roles within manufacturing, automation, or industrial settings. Seek opportunities where you can work directly with machinery, troubleshoot issues, perform maintenance, and learn about production processes. This hands-on exposure is invaluable for developing practical skills and understanding real-world equipment challenges.
Develop proficiency in relevant software and technical skills crucial for equipment engineering, such as CAD software (e.g., SolidWorks, AutoCAD), PLC programming, SCADA systems, and data analysis tools (e.g., Python, MATLAB for performance monitoring). Consider online courses or certifications in these areas to supplement your formal education and showcase specialized expertise to potential employers.
Build a project portfolio that demonstrates your problem-solving abilities and practical application of engineering principles. This could include academic capstone projects, personal projects where you designed or improved a mechanical or electrical system, or contributions to equipment-related initiatives during internships. Focus on projects that highlight your ability to analyze, design, troubleshoot, and optimize equipment performance.
Network with professionals in the equipment engineering field by attending industry conferences, joining professional organizations (e.g., ASME, IEEE, SME), and connecting with engineers on platforms like LinkedIn. Informational interviews can provide insights into specific industry needs and potential job opportunities. Many roles are filled through referrals, so building a strong professional network is highly beneficial.
Prepare a targeted resume and cover letter that highlights your specific skills, projects, and experiences relevant to equipment engineering roles. Tailor each application to the job description, emphasizing your understanding of equipment design, maintenance, process improvement, and safety protocols. Practice answering technical interview questions related to machine design, troubleshooting, and system integration.
Actively apply for entry-level Equipment Engineer, Junior Manufacturing Engineer, or Process Engineer roles, and be open to contract or technician positions that offer a clear path for advancement. During interviews, articulate how your academic knowledge and practical experiences equip you to analyze equipment performance, identify root causes of failures, and implement effective solutions, demonstrating your readiness to contribute to a production environment.
Step 1
Obtain a foundational engineering degree, ideally a Bachelor of Science in Mechanical, Electrical, Industrial, or Manufacturing Engineering. This academic background provides the essential theoretical knowledge in thermodynamics, materials science, control systems, and process optimization that forms the core of an Equipment Engineer's expertise. Aim for a program accredited by ABET or an equivalent international body.
Step 2
Gain practical experience through internships, co-op programs, or entry-level technician roles within manufacturing, automation, or industrial settings. Seek opportunities where you can work directly with machinery, troubleshoot issues, perform maintenance, and learn about production processes. This hands-on exposure is invaluable for developing practical skills and understanding real-world equipment challenges.
Step 3
Develop proficiency in relevant software and technical skills crucial for equipment engineering, such as CAD software (e.g., SolidWorks, AutoCAD), PLC programming, SCADA systems, and data analysis tools (e.g., Python, MATLAB for performance monitoring). Consider online courses or certifications in these areas to supplement your formal education and showcase specialized expertise to potential employers.
Step 4
Build a project portfolio that demonstrates your problem-solving abilities and practical application of engineering principles. This could include academic capstone projects, personal projects where you designed or improved a mechanical or electrical system, or contributions to equipment-related initiatives during internships. Focus on projects that highlight your ability to analyze, design, troubleshoot, and optimize equipment performance.
Step 5
Network with professionals in the equipment engineering field by attending industry conferences, joining professional organizations (e.g., ASME, IEEE, SME), and connecting with engineers on platforms like LinkedIn. Informational interviews can provide insights into specific industry needs and potential job opportunities. Many roles are filled through referrals, so building a strong professional network is highly beneficial.
Step 6
Prepare a targeted resume and cover letter that highlights your specific skills, projects, and experiences relevant to equipment engineering roles. Tailor each application to the job description, emphasizing your understanding of equipment design, maintenance, process improvement, and safety protocols. Practice answering technical interview questions related to machine design, troubleshooting, and system integration.
Step 7
Actively apply for entry-level Equipment Engineer, Junior Manufacturing Engineer, or Process Engineer roles, and be open to contract or technician positions that offer a clear path for advancement. During interviews, articulate how your academic knowledge and practical experiences equip you to analyze equipment performance, identify root causes of failures, and implement effective solutions, demonstrating your readiness to contribute to a production environment.
Education & Training Needed to Become an Equipment Engineer
Becoming an Equipment Engineer typically requires a strong foundation in engineering principles. Most employers prefer candidates with a Bachelor's degree in Mechanical, Electrical, Industrial, or Manufacturing Engineering. These 4-year degrees often cost between $40,000 and $120,000 or more at public universities, and significantly higher at private institutions, taking four years to complete. They provide the theoretical knowledge in mechanics, electronics, and system design crucial for this role.
While formal degrees are standard, some specialized certifications or master's degrees can enhance career prospects, especially for senior roles or specific equipment types. Master's degrees, often costing $20,000 to $60,000, take 1-2 years. Online courses and professional development seminars from industry associations offer continuing education, ranging from a few hundred to a few thousand dollars, completed in weeks or months. These alternatives often complement a foundational degree rather than replacing it. Employers value hands-on experience, often gained through internships or co-op programs during degree studies.
The market generally perceives a bachelor's degree as the entry-level standard, with advanced degrees signaling deeper specialization. Continuous learning remains vital, as equipment technology evolves rapidly. Industry-specific training, such as certifications in automation systems or specific machinery operation, further enhances an Equipment Engineer's value. The cost-benefit analysis favors a bachelor's degree as the primary investment, providing broad career applicability, while specialized training offers targeted skill enhancement for specific industries or equipment.
Equipment Engineer Salary & Outlook
Compensation for an Equipment Engineer varies significantly based on several factors. Geographic location plays a crucial role; major industrial hubs and areas with high demand for manufacturing or R&D often command higher salaries due to increased cost of living and specialized industry presence. For example, salaries in California or Massachusetts typically exceed those in less industrially dense states.
Years of experience, specific engineering specializations, and the breadth of technical skills directly impact earning potential. Expertise in advanced automation, robotics, or specific industrial processes can lead to premium compensation. Total compensation packages frequently extend beyond base salary, including performance bonuses, stock options in publicly traded companies, and comprehensive benefits such such as health insurance, retirement contributions, and professional development allowances.
Industry-specific trends, particularly in semiconductors, aerospace, or pharmaceuticals, drive salary growth for Equipment Engineers. Companies with cutting-edge technology or high-volume production often offer more competitive packages. Remote work opportunities are less common for this hands-on role, but some companies may offer location-flexible roles for design or analytical tasks, which can affect salary expectations based on the employee's chosen location versus the company's headquarters. While these figures focus on the US market, international compensation can differ widely based on local economic conditions and industry maturity.
Salary by Experience Level
Level | US Median | US Average |
---|---|---|
Junior Equipment Engineer | $70k USD | $75k USD |
Equipment Engineer | $90k USD | $95k USD |
Senior Equipment Engineer | $115k USD | $120k USD |
Lead Equipment Engineer | $140k USD | $145k USD |
Principal Equipment Engineer | $165k USD | $170k USD |
Market Commentary
The job market for Equipment Engineers shows consistent demand, driven by ongoing advancements in manufacturing, automation, and industrial processes. Industries like semiconductor manufacturing, aerospace, automotive, and biotechnology continuously seek skilled professionals to design, maintain, and optimize complex machinery. Current trends indicate a strong emphasis on automation integration, predictive maintenance, and smart factory initiatives, creating new opportunities for engineers proficient in these areas.
Growth projections for Equipment Engineers are stable, often tied to the expansion of manufacturing and high-tech sectors. The Bureau of Labor Statistics projects a steady outlook for mechanical engineers, a broader category that includes Equipment Engineers, with growth influenced by reshoring efforts and increased investment in domestic production capabilities. There is a particular demand for engineers who can bridge the gap between mechanical systems and software, contributing to the Internet of Things (IoT) and Industry 4.0 initiatives.
The supply of highly specialized Equipment Engineers, especially those with expertise in cutting-edge technologies like advanced robotics or nanotechnology equipment, remains a key challenge for many industries. This supply-demand imbalance can lead to competitive salaries and benefits for qualified candidates. Future-proofing this career involves continuous learning in areas like data analytics for equipment performance, AI for predictive maintenance, and new materials science. While not entirely recession-proof, the essential nature of maintaining production lines provides a degree of stability, particularly in critical infrastructure or defense sectors. Geographic hotspots for this role include Silicon Valley, Texas, Arizona, and the Midwest's manufacturing belt.
Equipment Engineer Career Path
Career progression for an Equipment Engineer typically unfolds through increasing technical specialization and leadership responsibilities. Professionals often begin by mastering specific machinery and processes, then advance to optimizing complex systems and eventually leading strategic initiatives. This field offers distinct pathways, with some engineers focusing on deep technical expertise as individual contributors (IC track) while others transition into managing teams and projects (management track).
Advancement speed depends on several factors, including individual performance, the complexity of equipment managed, and the industry sector. For instance, semiconductor or aerospace industries often present more intricate challenges and specialized equipment, potentially accelerating development for those who master them. Company size also plays a role; larger corporations may offer more structured career paths and opportunities for diverse project exposure, whereas smaller firms might provide broader responsibilities earlier in a career.
Lateral movement is common, allowing Equipment Engineers to pivot into related fields like process engineering, manufacturing engineering, or even supply chain management, leveraging their understanding of operational efficiency. Continuous learning, including certifications in Six Sigma, Lean Manufacturing, or specific equipment technologies, marks significant milestones. Networking within industry associations and mentorship from experienced engineers are crucial for identifying opportunities and gaining insights into emerging technologies and best practices.
Junior Equipment Engineer
0-2 yearsWorks under direct supervision to assist with equipment installation, routine maintenance, and basic repairs. Learns to operate and monitor various machinery. Documents observations and assists senior engineers in identifying equipment issues. Supports production lines by ensuring basic equipment functionality.
Key Focus Areas
Develop foundational knowledge of equipment operation, maintenance, and troubleshooting. Focus on understanding safety protocols, standard operating procedures, and basic diagnostic tools. Build proficiency in reading schematics and technical manuals. Seek mentorship to accelerate learning about specific machinery.
Equipment Engineer
2-5 yearsManages scheduled and unscheduled maintenance activities for assigned equipment. Diagnoses complex equipment malfunctions and implements solutions. Participates in equipment upgrade projects and performs calibration. Provides technical support to production teams to minimize downtime and improve output.
Key Focus Areas
Enhance problem-solving skills through root cause analysis and corrective action implementation. Develop expertise in preventive and predictive maintenance techniques. Focus on optimizing equipment performance, efficiency, and reliability. Begin to understand equipment lifecycle management and cost-benefit analysis for repairs/upgrades.
Senior Equipment Engineer
5-8 yearsLeads complex equipment improvement projects, from conception to implementation. Conducts detailed analyses to identify systemic equipment issues and proposes innovative solutions. Serves as a subject matter expert for specific equipment types or processes. Mentors junior engineers and contributes to departmental best practices.
Key Focus Areas
Master advanced troubleshooting and diagnostic techniques. Focus on project management skills for equipment modifications and new installations. Develop strong communication and collaboration abilities for cross-functional teamwork. Begin mentoring junior engineers and contributing to training materials.
Lead Equipment Engineer
8-12 yearsOversees a team of Equipment Engineers, assigning tasks and managing project portfolios. Develops and implements department-wide maintenance strategies and reliability programs. Drives continuous improvement initiatives across multiple equipment lines or production areas. Manages budgets related to equipment maintenance and capital expenditures.
Key Focus Areas
Cultivate leadership and team management skills, including delegation and performance feedback. Focus on strategic planning for equipment lifecycle, including procurement and retirement. Develop business acumen to assess the financial impact of equipment decisions. Build strong vendor relationships and negotiate contracts.
Principal Equipment Engineer
12+ yearsProvides strategic direction and technical leadership for the entire equipment engineering function. Defines long-term equipment technology roadmaps and capital investment strategies. Drives major organizational initiatives for operational excellence and technological advancement. Represents the company as a top technical authority in equipment-related matters.
Key Focus Areas
Develop executive leadership and strategic thinking skills. Focus on long-term technological roadmapping and innovation within equipment engineering. Cultivate a broad understanding of business operations, market trends, and regulatory compliance. Engage in industry thought leadership and external collaborations.
Junior Equipment Engineer
0-2 yearsWorks under direct supervision to assist with equipment installation, routine maintenance, and basic repairs. Learns to operate and monitor various machinery. Documents observations and assists senior engineers in identifying equipment issues. Supports production lines by ensuring basic equipment functionality.
Key Focus Areas
Develop foundational knowledge of equipment operation, maintenance, and troubleshooting. Focus on understanding safety protocols, standard operating procedures, and basic diagnostic tools. Build proficiency in reading schematics and technical manuals. Seek mentorship to accelerate learning about specific machinery.
Equipment Engineer
2-5 yearsManages scheduled and unscheduled maintenance activities for assigned equipment. Diagnoses complex equipment malfunctions and implements solutions. Participates in equipment upgrade projects and performs calibration. Provides technical support to production teams to minimize downtime and improve output.
Key Focus Areas
Enhance problem-solving skills through root cause analysis and corrective action implementation. Develop expertise in preventive and predictive maintenance techniques. Focus on optimizing equipment performance, efficiency, and reliability. Begin to understand equipment lifecycle management and cost-benefit analysis for repairs/upgrades.
Senior Equipment Engineer
5-8 yearsLeads complex equipment improvement projects, from conception to implementation. Conducts detailed analyses to identify systemic equipment issues and proposes innovative solutions. Serves as a subject matter expert for specific equipment types or processes. Mentors junior engineers and contributes to departmental best practices.
Key Focus Areas
Master advanced troubleshooting and diagnostic techniques. Focus on project management skills for equipment modifications and new installations. Develop strong communication and collaboration abilities for cross-functional teamwork. Begin mentoring junior engineers and contributing to training materials.
Lead Equipment Engineer
8-12 yearsOversees a team of Equipment Engineers, assigning tasks and managing project portfolios. Develops and implements department-wide maintenance strategies and reliability programs. Drives continuous improvement initiatives across multiple equipment lines or production areas. Manages budgets related to equipment maintenance and capital expenditures.
Key Focus Areas
Cultivate leadership and team management skills, including delegation and performance feedback. Focus on strategic planning for equipment lifecycle, including procurement and retirement. Develop business acumen to assess the financial impact of equipment decisions. Build strong vendor relationships and negotiate contracts.
Principal Equipment Engineer
12+ yearsProvides strategic direction and technical leadership for the entire equipment engineering function. Defines long-term equipment technology roadmaps and capital investment strategies. Drives major organizational initiatives for operational excellence and technological advancement. Represents the company as a top technical authority in equipment-related matters.
Key Focus Areas
Develop executive leadership and strategic thinking skills. Focus on long-term technological roadmapping and innovation within equipment engineering. Cultivate a broad understanding of business operations, market trends, and regulatory compliance. Engage in industry thought leadership and external collaborations.
Job Application Toolkit
Ace your application with our purpose-built resources:
Equipment Engineer Resume Examples
Proven layouts and keywords hiring managers scan for.
View examplesEquipment Engineer Cover Letter Examples
Personalizable templates that showcase your impact.
View examplesTop Equipment Engineer Interview Questions
Practice with the questions asked most often.
View examplesEquipment Engineer Job Description Template
Ready-to-use JD for recruiters and hiring teams.
View examplesGlobal Equipment Engineer Opportunities
Equipment Engineers analyze, design, and optimize manufacturing equipment globally. This role is crucial in high-tech, semiconductor, and automotive industries, which operate internationally. Global demand remains strong as companies expand production and automate processes. Cultural differences impact safety standards and operational procedures, requiring adaptable professionals. International certifications, like Six Sigma or specific machinery accreditations, enhance global mobility. Professionals seek international roles for advanced projects and diverse industry exposure.
Global Salaries
Salaries for Equipment Engineers vary significantly by region and industry. In North America, particularly the USA, an Equipment Engineer typically earns between $80,000 and $120,000 USD annually. California or Texas often see higher ranges, sometimes exceeding $130,000, but with a higher cost of living. Benefits packages in the US often include comprehensive health insurance and retirement plans.
Europe offers diverse salary landscapes. In Germany, a leading manufacturing hub, salaries range from €55,000 to €85,000 ($60,000-$92,000 USD). Northern European countries like Sweden or Finland offer similar ranges, often with more generous vacation time and social benefits. Southern Europe, such as Spain or Italy, might see lower figures, around €35,000 to €60,000 ($38,000-$65,000 USD), reflecting lower living costs.
Asia-Pacific markets present competitive compensation. In Singapore, salaries often range from S$60,000 to S$95,000 ($45,000-$70,000 USD), with lower tax burdens. South Korea, a semiconductor powerhouse, offers ₩50,000,000 to ₩80,000,000 ($37,000-$59,000 USD) annually, with strong company benefits. China's rapidly growing manufacturing sector offers ¥200,000 to ¥400,000 ($28,000-$56,000 USD), but local purchasing power can be strong in some cities. Experience and specialized skills, like robotics or automation, significantly boost earning potential across all regions.
Remote Work
International remote work opportunities for Equipment Engineers are limited due to the hands-on nature of the role. Most tasks involve direct interaction with machinery on a factory floor or in a lab. However, some aspects, like design, simulation, data analysis, or project management, can be performed remotely. This often applies to senior or principal engineers managing global teams or equipment lifecycles.
Companies with distributed manufacturing sites may offer hybrid roles, combining remote work with occasional site visits. Digital nomad visas are generally not suitable for this role due to the need for physical presence. When remote work is possible, tax implications vary by country of residence and employer location. Employers typically provide necessary software and secure network access. Time zone differences require flexible scheduling for international collaboration.
Visa & Immigration
Equipment Engineers often qualify for skilled worker visas in many countries. Popular destinations include Germany (EU Blue Card), the USA (H-1B visa, though competitive), Canada (Express Entry), and Singapore (Employment Pass). These visas typically require a relevant bachelor's degree in engineering and several years of experience. Credential recognition is crucial; engineers may need to have their degrees evaluated by local authorities or professional bodies.
The application process for skilled worker visas generally takes several months, involving employer sponsorship, documentation submission, and sometimes interviews. Language requirements vary; English is often sufficient for many roles in multinational companies, but local language proficiency can be an advantage. Pathways to permanent residency exist in countries like Canada and Australia, often linked to continuous skilled employment. Intra-company transfers are common for engineers moving within a global corporation.
2025 Market Reality for Equipment Engineers
Understanding current market realities is crucial for Equipment Engineers navigating their careers. The field has evolved significantly from 2023 to 2025, driven by post-pandemic reshoring efforts and the accelerating integration of AI into manufacturing processes.
Broader economic factors, such as supply chain stability and industrial investment cycles, directly influence job availability. Market conditions also vary by experience level, with senior roles often more insulated from economic shifts, and by company size, as large corporations may have more structured equipment teams than smaller firms. This analysis provides an honest assessment of current hiring conditions and strategic considerations.
Current Challenges
Equipment Engineers face increased competition, especially at junior levels, as companies seek more experienced hires to manage complex, automated systems. Economic uncertainty in manufacturing sectors, particularly semiconductors and automotive, can slow hiring. A mismatch often exists between traditional engineering curricula and the rapid evolution of AI-driven predictive maintenance and smart factory integration, requiring continuous upskskilling.
Growth Opportunities
Despite challenges, strong opportunities exist for Equipment Engineers specializing in advanced manufacturing and automation. Roles focused on semiconductor fabrication equipment, electric vehicle battery production lines, and pharmaceutical manufacturing show robust demand. These sectors require highly specialized engineers to manage complex, high-precision machinery.
Emerging opportunities lie in roles combining traditional equipment knowledge with data science and AI. This includes positions like 'Predictive Maintenance Engineer' or 'Smart Factory Integration Specialist.' Engineers who can develop and implement AI-powered diagnostic tools or optimize equipment performance through machine learning algorithms are highly sought after.
Professionals can gain a competitive advantage by acquiring certifications in industrial automation platforms (e.g., Siemens, Rockwell), robotics programming, or data analytics tools like Python for sensor data processing. Underserved markets might include regions with new factory investments or specialized manufacturing niches experiencing growth. Market corrections could create opportunities as companies streamline operations, increasing the need for efficiency-focused equipment optimization.
Current Market Trends
The market for Equipment Engineers in 2025 shows nuanced demand. While core manufacturing sectors maintain steady requirements for maintaining production lines, the strongest growth comes from industries investing heavily in automation and advanced robotics. This includes the semiconductor industry, which continues to expand globally, and specialized battery manufacturing.
Generative AI and machine learning are increasingly influencing job requirements. Employers now prioritize engineers who can not only troubleshoot but also implement predictive maintenance systems, analyze sensor data for efficiency gains, and integrate smart factory technologies. This shifts the role from purely reactive repair to proactive optimization and data-driven decision-making.
Economic conditions, while stable in some manufacturing niches, still cause caution in capital expenditure, impacting new equipment installations in others. This can lead to slower hiring for projects requiring extensive new equipment setup versus ongoing maintenance roles. Salary trends remain positive for those with advanced automation, data analytics, and AI integration skills, creating a premium for specialized expertise. Market saturation affects entry-level roles more, as companies prefer engineers who can immediately contribute to high-tech environments.
Geographically, demand concentrates in established manufacturing hubs like the US Midwest, parts of Asia (especially for semiconductors), and Germany. Remote work is less common for this hands-on role, though some senior positions involve remote oversight of global equipment fleets. Seasonal hiring is minimal, driven more by project cycles and factory expansions.
Emerging Specializations
Technological advancement and industry evolution consistently create new specialization opportunities for Equipment Engineers. As manufacturing processes become more complex and integrated, the demand for highly specialized engineering expertise grows significantly. Understanding these shifts allows professionals to position themselves strategically for future career paths.
Early positioning in emerging areas is crucial for career advancement in 2025 and beyond. These cutting-edge specializations often command premium compensation and accelerate career growth, offering distinct advantages over more established paths. While foundational engineering skills remain essential, adapting to new technologies and methodologies unlocks significant value.
The timeline for emerging areas to become mainstream and create substantial job opportunities varies, typically spanning three to five years. Early adopters gain a competitive edge, becoming experts as the market matures. However, specializing in cutting-edge areas involves a balance of risk and reward. While the potential for high demand and compensation is strong, these fields require continuous learning and adaptability as technologies evolve rapidly.
Additive Manufacturing Equipment Engineer
Robotics and Automation Equipment Engineer
Sustainable Manufacturing Equipment Engineer
Smart Factory Equipment Engineer
Advanced Materials Processing Equipment Engineer
Pros & Cons of Being an Equipment Engineer
Making informed career decisions requires understanding both the benefits and challenges of a professional path. An Equipment Engineer's experience can vary significantly based on the industry, company culture, specific equipment managed, and individual aptitude. The pros and cons may also shift as one progresses from an entry-level position to a senior or specialized role. What one person views as a challenge, another might see as an engaging opportunity, depending on their personal values and career aspirations. This assessment aims to provide a realistic overview to help set appropriate expectations for this particular engineering discipline.
Pros
- High demand across diverse industries, including manufacturing, semiconductors, aerospace, and pharmaceuticals, ensures strong job security and a wide range of employment opportunities.
- The role offers significant intellectual stimulation through problem-solving complex mechanical, electrical, and control system issues, requiring analytical thinking and diagnostic skills.
- Opportunities for continuous learning are abundant, as engineers regularly work with cutting-edge technologies and must stay updated on new equipment, automation, and maintenance techniques.
- Direct impact on production efficiency and quality is a core aspect, allowing engineers to see tangible results of their work in improving operational flow and reducing costs.
- Competitive salaries and benefits packages are common due to the specialized technical expertise required and the critical nature of maintaining expensive, high-volume production machinery.
- Career advancement paths are clear, often leading to senior engineering roles, project management, or even leadership positions within operations or maintenance departments.
- The work often involves a blend of hands-on technical work and theoretical analysis, appealing to individuals who enjoy both practical application and intellectual challenges.
Cons
- Regular exposure to hazardous materials or environments, such as chemicals, high voltage, or extreme temperatures, requires strict adherence to safety protocols and can pose health risks if not managed properly.
- The role often demands on-call availability or irregular hours, especially when critical equipment malfunctions occur outside of standard working times, impacting personal life and work-life balance.
- Dealing with complex, often proprietary equipment means a steep and continuous learning curve, as new technologies and specialized machinery are constantly introduced.
- Budgetary constraints can limit access to optimal tools or necessary upgrades, forcing engineers to find creative, sometimes less efficient, solutions or work with outdated systems.
- High-pressure situations arise during equipment breakdowns or production line stoppages, requiring immediate, accurate diagnosis and repair to minimize costly downtime.
- The work environment can be physically demanding, involving lifting heavy components, working in confined spaces, or standing for extended periods, which can lead to fatigue or injury.
- Limited opportunities for creative design work exist, as the primary focus is on maintaining, troubleshooting, and improving existing equipment rather than inventing new systems from scratch, which can be less appealing to those seeking innovative roles.
Frequently Asked Questions
Equipment Engineers face unique challenges balancing technical expertise with operational efficiency and safety. This section addresses common questions about entering this role, from the necessary educational background to managing maintenance schedules and ensuring regulatory compliance.
What educational background do I need to become an Equipment Engineer?
Most Equipment Engineer roles require a Bachelor's degree in engineering, typically mechanical, electrical, industrial, or manufacturing engineering. Some specialized positions may prefer a Master's degree. Practical experience through internships or co-op programs during your studies significantly enhances your job prospects and understanding of real-world equipment.
What is the typical salary range for an Equipment Engineer?
Entry-level Equipment Engineers can expect a starting salary ranging from $60,000 to $80,000 annually, depending on the industry, location, and specific company. With 5-10 years of experience, salaries can climb to $90,000 - $120,000, and senior or specialized roles can exceed $130,000. Factors like certifications and project management experience also influence earning potential.
What are the common career advancement opportunities for an Equipment Engineer?
The career path for an Equipment Engineer often involves progressing from entry-level roles to senior engineer positions, where you take on more complex projects and mentorship responsibilities. Many move into management roles like Engineering Manager or Operations Manager, overseeing teams and larger departmental functions. Specialization in areas like automation, reliability, or specific equipment types also opens advanced opportunities.
Is there strong job security and market demand for Equipment Engineers?
The demand for Equipment Engineers remains stable, driven by industries reliant on complex machinery, such as manufacturing, aerospace, automotive, semiconductors, and energy. As technology advances and automation increases, the need for engineers who can design, maintain, and optimize sophisticated equipment continues. Job security is generally good, especially for those with specialized skills or experience in critical industries.
What is the typical work-life balance like for an Equipment Engineer?
Work-life balance for an Equipment Engineer can vary. During normal operations, it's often a standard 40-hour week. However, project deadlines, equipment breakdowns, or installation phases can sometimes require extended hours, including evenings or weekends. Roles in 24/7 manufacturing environments might involve on-call rotations. Overall, it's a role that requires flexibility to respond to operational needs.
What are the biggest challenges Equipment Engineers face in their daily work?
Key challenges include troubleshooting complex mechanical and electrical systems, ensuring equipment uptime, and managing maintenance budgets effectively. You also need to stay current with rapidly evolving technologies and adapt to new regulations. Balancing cost efficiency with performance and safety requirements is a constant challenge. Effective communication with technicians and management is also crucial.
Can Equipment Engineers work remotely, or is it primarily an on-site role?
While some Equipment Engineer roles, particularly those focused on design or analysis, might offer hybrid or remote options, many positions require a significant on-site presence. This is because you need to directly interact with, inspect, and troubleshoot physical equipment on the production floor or in a lab. Travel may also be required for vendor visits, new equipment installations, or multi-site responsibilities.
Related Careers
Explore similar roles that might align with your interests and skills:
Equipment Specialist
A growing field with similar skill requirements and career progression opportunities.
Explore career guideEquipment Technician
A growing field with similar skill requirements and career progression opportunities.
Explore career guideMaintenance Engineer
A growing field with similar skill requirements and career progression opportunities.
Explore career guideRotating Equipment Engineer
A growing field with similar skill requirements and career progression opportunities.
Explore career guideMarine Equipment Engineer
A growing field with similar skill requirements and career progression opportunities.
Explore career guideAssess your Equipment Engineer readiness
Understanding where you stand today is the first step toward your career goals. Our Career Coach helps identify skill gaps and create personalized plans.
Skills Gap Analysis
Get a detailed assessment of your current skills versus Equipment Engineer requirements. Our AI Career Coach identifies specific areas for improvement with personalized recommendations.
See your skills gapCareer Readiness Assessment
Evaluate your overall readiness for Equipment Engineer roles with our AI Career Coach. Receive personalized recommendations for education, projects, and experience to boost your competitiveness.
Assess your readinessLand your dream job with Himalayas Plus
Upgrade to unlock Himalayas' premium features and turbocharge your job search.
Himalayas
Himalayas Plus
Himalayas Max
Find your dream job
Sign up now and join over 100,000 remote workers who receive personalized job alerts, curated job matches, and more for free!
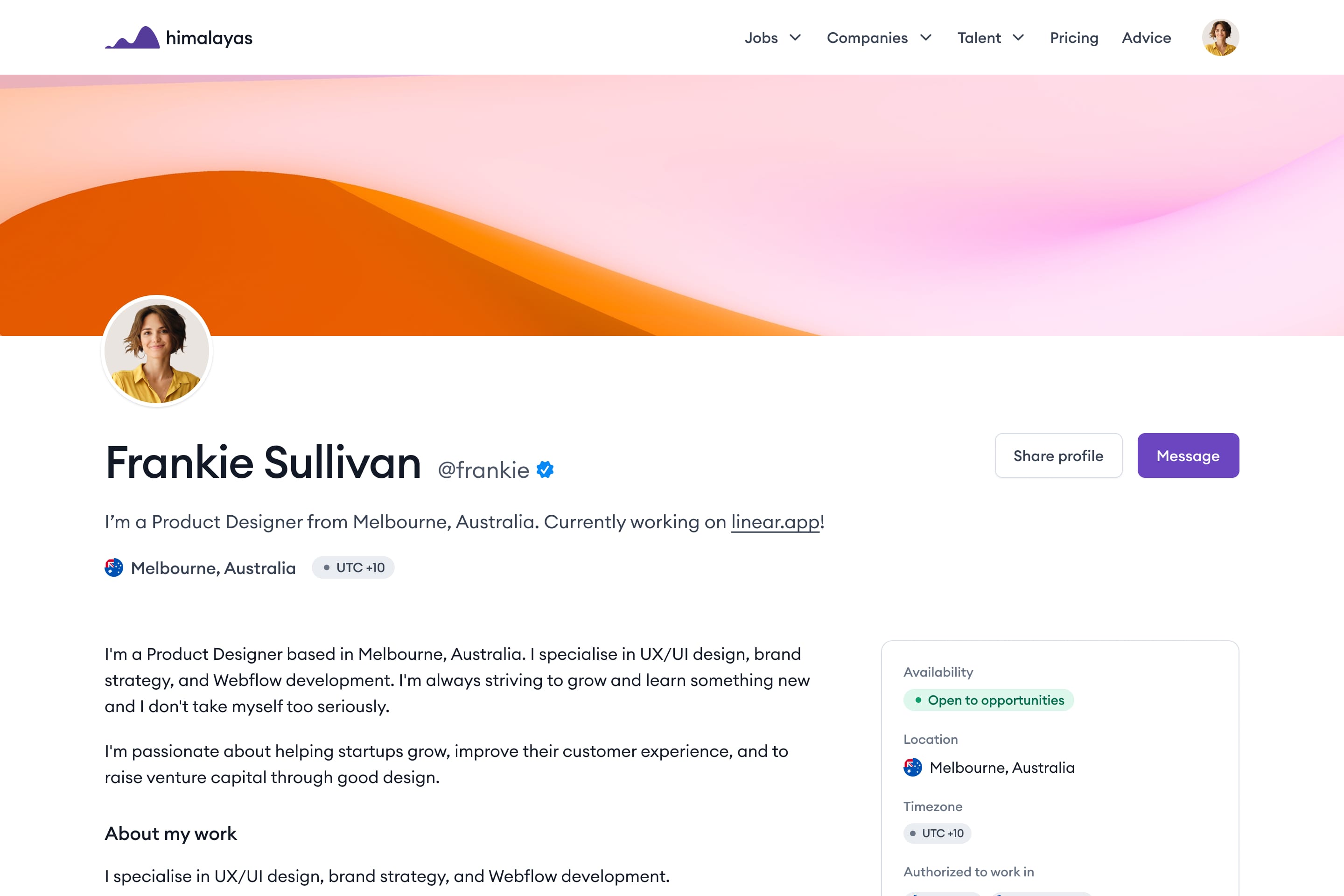