Complete Aluminum Polisher Career Guide
Aluminum polishers are skilled artisans who transform raw or fabricated aluminum into highly reflective, aesthetically pleasing, and corrosion-resistant surfaces. This specialized role demands precision and an eye for detail, directly impacting the quality and finish of products ranging from automotive parts to architectural elements. It offers a tangible career path for those who enjoy hands-on work and seeing immediate results, contributing to the final look and durability of countless industrial and consumer goods.
Key Facts & Statistics
Median Salary
$41,040 USD
(BLS, May 2023)
Range: $30k - $60k+ USD (BLS, May 2023)
Growth Outlook
0%
as fast as average (BLS, 2022-2032)
Annual Openings
≈17k
openings annually (BLS, 2022-2032)
Top Industries
Typical Education
High school diploma or equivalent; often on-the-job training or vocational school
What is an Aluminum Polisher?
An aluminum polisher specializes in refining the surface of aluminum components to achieve a desired aesthetic finish, ranging from a matte sheen to a mirror-like brilliance. This role involves meticulously removing imperfections, oxidation, and scratches through a process of grinding, sanding, and buffing. They enhance the visual appeal and often the corrosion resistance of aluminum parts used in diverse industries like automotive, aerospace, marine, and architectural design.
This role differs significantly from a general metal fabricator or welder, as their primary focus is on surface aesthetics and precision finishing rather than the structural formation or joining of metal. Unlike a painter or coater who applies a surface layer, an aluminum polisher physically alters the metal's surface to create its final look and feel.
What does an Aluminum Polisher do?
Key Responsibilities
- Inspect aluminum surfaces for imperfections such as scratches, oxidation, and dullness before polishing begins.
- Select appropriate abrasive compounds and buffing wheels based on the aluminum alloy and desired finish.
- Operate various types of polishing equipment, including stationary buffing machines and handheld grinders.
- Apply polishing compounds evenly to the surface, ensuring consistent pressure and movement to achieve a uniform shine.
- Clean and degrease polished aluminum components to remove residue and prepare them for subsequent processes or packaging.
- Perform routine maintenance on polishing machinery, including changing buffing pads and ensuring safety guards are in place.
- Adhere to safety protocols, wearing personal protective equipment such as gloves, eye protection, and respirators to prevent injury and exposure to dust and fumes.
Work Environment
An aluminum polisher typically works in a manufacturing plant, fabrication shop, or a specialized metal finishing facility. The environment can be noisy due to machinery and may involve exposure to metal dust, fumes, and polishing compounds, necessitating strict adherence to safety protocols and the use of personal protective equipment. The work often involves standing for extended periods and requires repetitive motions.
Collaboration is usually with a small team of fellow polishers, fabricators, or quality control personnel. The pace of work can be steady, driven by production schedules, and may involve shift work depending on the facility's operational hours. Overtime might be necessary to meet deadlines.
Tools & Technologies
Aluminum polishers primarily use a range of specialized tools and equipment to achieve a high-quality finish. This includes stationary buffing machines with various motor speeds and abrasive wheels, as well as handheld orbital polishers and grinders for more intricate or hard-to-reach areas. They select specific polishing compounds and rouges, which come in different grits and formulations for cutting, coloring, and finishing aluminum surfaces. Essential personal protective equipment includes safety glasses, ear protection, respirators for dust and fume protection, and heavy-duty gloves.
Other tools include degreasing agents, microfiber cloths, and compressed air for cleaning the finished product. Experience with different types of aluminum alloys and their unique polishing characteristics is also crucial for success in this role.
Aluminum Polisher Skills & Qualifications
The Aluminum Polisher role demands a precise blend of manual dexterity, technical understanding of abrasive materials, and a keen eye for detail. This position focuses on achieving specific surface finishes on aluminum components, ranging from mirror-like sheens to satin or brushed textures. Qualifications for this role emphasize practical experience and demonstrated skill over formal academic degrees.
Requirements for an Aluminum Polisher vary significantly based on the industry and the specific application of the polished parts. For instance, aerospace or medical device manufacturing demands extremely high precision and adherence to strict quality control standards, often requiring certifications in specific polishing techniques or materials. In contrast, roles in automotive aftermarkets or architectural finishes might prioritize efficiency and aesthetic consistency over microscopic tolerances.
Formal education is rarely a prerequisite for this role; vocational training, apprenticeships, or on-the-job experience are the most common pathways. Many successful polishers start as production assistants or in general fabrication roles, learning the craft through mentorship. The field is evolving with advancements in automated polishing equipment, yet the demand for skilled manual polishers remains high for intricate or custom work. A strong portfolio showcasing various finishes and materials can often outweigh traditional credentials.
Education Requirements
Technical Skills
- Knowledge of various aluminum alloys and their polishing characteristics (e.g., 6061, 7075, cast aluminum)
- Proficiency with hand-held power tools (e.g., rotary buffers, orbital sanders, die grinders)
- Expertise in selecting and applying appropriate abrasive compounds and wheels (e.g., rouges, compounds, buffing pads, felt wheels)
- Understanding of grit progression from coarse to fine for material removal and surface refinement
- Ability to achieve specific surface finishes (e.g., mirror, satin, brushed, matte) consistently
- Skill in inspecting finished surfaces for defects (e.g., swirls, hazing, pitting, scratches) using visual and tactile methods
- Familiarity with safety protocols for polishing operations (e.g., PPE, ventilation, dust collection)
- Maintenance and cleaning of polishing equipment and work areas
- Basic knowledge of metal cleaning and degreasing agents suitable for aluminum
- Understanding of material removal rates and how they affect part dimensions and tolerances
- Ability to read and interpret technical drawings or finish specifications
- Experience with wet sanding techniques for fine finishes
Soft Skills
- Attention to Detail: Essential for identifying imperfections and achieving consistent surface finishes, ensuring every part meets exact specifications.
- Manual Dexterity: Crucial for controlling polishing tools, applying even pressure, and navigating complex part geometries with precision.
- Patience: Polishing often requires repetitive motions and meticulous work over extended periods to achieve desired results, demanding a calm and focused approach.
- Problem-Solving: Important for troubleshooting issues like uneven finishes, material inconsistencies, or tool marks, requiring adjustments to technique or materials.
- Work Ethic: The ability to maintain focus and productivity through repetitive tasks, ensuring high-volume output while upholding quality standards.
- Safety Consciousness: Paramount for handling power tools, abrasive materials, and chemicals safely, protecting oneself and others in the workshop.
- Adaptability: Necessary for switching between different types of aluminum alloys, varying part shapes, and diverse finish requirements, adjusting techniques accordingly.
- Self-Discipline: The capacity to maintain consistent quality and output without constant supervision, adhering to production schedules and quality benchmarks independently.
How to Become an Aluminum Polisher
Entering the aluminum polishing field offers various pathways, from hands-on apprenticeships to direct entry for those with relevant mechanical aptitude. The timeline to become proficient can range from a few months for basic polishing tasks to a year or more for advanced finishes, depending on the complexity of the work and the industry. Some roles focus on decorative finishes for consumer goods, while others involve precision polishing for aerospace or automotive components.
Entry strategies vary significantly by geographic region and industry. In areas with strong manufacturing or automotive sectors, opportunities for on-the-job training or apprenticeships are more common. Smaller shops might prioritize a strong work ethic and willingness to learn, while larger corporations or specialized industries may prefer candidates with some vocational training or prior experience with power tools and metal finishing processes. Misconceptions often include believing this is a purely manual labor job; it requires a keen eye for detail, patience, and a deep understanding of different abrasives and techniques.
Networking within local manufacturing or fabrication communities, attending industry trade shows, or even visiting local machine shops can uncover opportunities not publicly advertised. While a formal degree is not typically required, demonstrating a strong portfolio of finished pieces or practical experience with metalworking equipment significantly enhances a candidate's appeal. The hiring landscape values precision and reliability, making hands-on demonstrations of skill crucial for securing a position.
Step 1
Step 2
Step 3
Step 4
Step 5
Step 6
Step 7
Education & Training Needed to Become an Aluminum Polisher
Becoming an Aluminum Polisher primarily involves acquiring hands-on skills rather than formal academic degrees. Traditional 4-year university programs are generally not relevant for this trade. Instead, vocational training, apprenticeships, and specialized workshops form the core educational pathways. These programs typically focus on practical techniques, safety protocols, and the use of specific tools and materials, which are crucial for achieving the high-quality finishes required in industries like automotive, aerospace, and decorative arts.
Vocational schools or community colleges may offer certificate programs in metal finishing or auto body repair that include polishing techniques. These can range from 6 to 18 months and cost between $3,000 to $10,000, depending on the institution and program depth. Apprenticeships, often offered by polishing shops or manufacturing companies, provide on-the-job training and can last from one to three years, with apprentices earning a wage while learning. Self-study through online tutorials and practice with personal equipment is also an option, costing minimal amounts for materials but requiring significant self-discipline and time, potentially 6-12 months to gain proficiency.
Employers highly value practical experience and a demonstrated portfolio of work over academic credentials. While a formal certificate might offer a structured learning environment, an apprenticeship directly integrates learners into the professional workflow, often leading to immediate employment upon completion. Continuous learning in this field involves staying updated on new polishing compounds, equipment, and safety standards, often through vendor-specific training or industry workshops. The specific needs for an Aluminum Polisher vary little by specialization, as the core skills remain consistent across different applications, though high-end decorative work might demand finer attention to detail.
Aluminum Polisher Salary & Outlook
Compensation for an Aluminum Polisher varies significantly based on several factors beyond just base salary. Geographic location plays a crucial role, with higher wages typically found in regions with a strong manufacturing base or specialized industries requiring precision finishing, often correlating with higher costs of living. Conversely, areas with lower demand or a surplus of skilled polishers may offer more modest wages.
Years of experience dramatically influence earning potential. Entry-level polishers earn less than those with a decade of expertise in intricate polishing techniques or specialized materials. Total compensation often extends beyond hourly wages to include overtime pay, production bonuses for meeting output targets, and benefits packages such as health insurance, paid time off, and retirement contributions. Some employers may offer professional development allowances for certifications in new polishing technologies or safety protocols.
Industry-specific trends also affect pay. Aerospace, automotive, and high-end consumer goods manufacturing often command higher rates due to the precision and quality required. Unionization can also influence compensation, providing structured pay scales and benefits. Negotiating leverage comes from demonstrating expertise in specialized finishes, efficiency, and a proven track record of quality work. While remote work is not applicable for this hands-on role, demand in international markets can influence domestic wages, as U.S. figures are often a benchmark for skilled trades.
Salary by Experience Level
Level | US Median | US Average |
---|---|---|
Aluminum Polisher | $40k USD | $42k USD |
Senior Aluminum Polisher | $52k USD | $55k USD |
Lead Aluminum Polisher | $65k USD | $68k USD |
Market Commentary
The job market for Aluminum Polishers is stable, driven by consistent demand from manufacturing sectors that require high-quality metal finishes. Industries like aerospace, automotive, marine, and consumer electronics rely heavily on skilled polishers for both aesthetic appeal and functional precision. While overall manufacturing employment may fluctuate, the specialized nature of polishing often creates a steady need for trained individuals.
Future growth in this field is projected to be modest but consistent, aligning with the general outlook for production occupations. Automation and robotic polishing technologies are emerging, particularly for repetitive tasks or large-volume production. However, complex geometries, intricate designs, and high-precision finishes still require the nuanced touch and critical eye of a human polisher. This human element ensures a degree of recession resistance for highly skilled professionals.
The supply of experienced Aluminum Polishers is often limited, creating a demand-supply imbalance that can favor skilled candidates. This scarcity is partly due to a declining emphasis on vocational training in some regions. Emerging opportunities may lie in specialized niche markets, such as custom fabrication, restoration work, or industries utilizing new aluminum alloys that require specific polishing techniques. Geographic hotspots for this role typically include industrial centers in the Midwest, Southeast, and Pacific Northwest, where manufacturing facilities are concentrated. Continuous learning in new materials and advanced polishing techniques will be crucial for long-term career viability.
Aluminum Polisher Career Path
Career progression for an Aluminum Polisher typically involves a gradual increase in skill, precision, and autonomy. Professionals in this field advance by mastering various polishing techniques, handling more complex parts, and demonstrating consistent high-quality work. The pathway often distinguishes between individual contributor (IC) tracks, where polishers become master craftspeople, and leadership tracks, where they manage teams and operations.
Advancement speed depends on several factors, including individual performance, the complexity of projects undertaken, and the company's size and specialization. Larger manufacturing facilities or those dealing with intricate aerospace or automotive components might offer more structured progression. Lateral movement opportunities exist in related metal finishing roles, such as grinding or deburring, or transitioning into quality control or specialized fabrication.
Continuous learning through hands-on experience, mastering new tools, and understanding different aluminum alloys is crucial. Networking within the industry, attending trade shows, and seeking mentorship from experienced polishers can accelerate growth. Developing a reputation for exceptional quality and efficiency marks significant progression. Some polishers may eventually pivot into roles such as quality assurance inspectors, specialized metal fabricators, or even start their own custom polishing businesses.
Aluminum Polisher
0-2 yearsKey Focus Areas
Senior Aluminum Polisher
2-5 yearsKey Focus Areas
Lead Aluminum Polisher
5-8 years total experienceKey Focus Areas
Aluminum Polisher
0-2 yearsPerform basic polishing tasks on aluminum parts under direct supervision. Follow detailed instructions to achieve specified surface finishes. Work with standard tools and materials for routine components. Contribute to maintaining a clean and organized work area. Identify and report minor imperfections to senior staff.
Key Focus Areas
Develop proficiency with various polishing tools, including rotary polishers, orbital sanders, and hand tools. Focus on achieving consistent finishes on simpler aluminum components. Understand different abrasive types and their applications. Begin to learn about surface preparation and quality inspection for basic parts. Adhere strictly to safety protocols and material handling guidelines.
Senior Aluminum Polisher
2-5 yearsIndependently polish a wide range of aluminum components, including complex or high-value parts. Make decisions on appropriate tools and abrasives for specific finishes. Conduct quality checks on finished products, ensuring adherence to strict specifications. Provide guidance and initial training to entry-level polishers. Troubleshoot minor issues with equipment and materials.
Key Focus Areas
Master advanced polishing techniques for intricate and contoured aluminum surfaces. Develop expertise in identifying and correcting various surface defects, such as scratches, swirls, and oxidation. Cultivate a deep understanding of different aluminum alloys and their unique polishing requirements. Begin to mentor junior polishers on fundamental techniques and safety. Focus on optimizing workflow and efficiency.
Lead Aluminum Polisher
5-8 years total experienceOversee a team of aluminum polishers, assigning tasks and managing daily operations. Ensure all polishing work meets quality standards and production deadlines. Provide expert technical guidance and hands-on training to the team. Manage equipment maintenance schedules and material inventory for the polishing department. Act as a primary point of contact for complex polishing projects or client specifications.
Key Focus Areas
Develop strong leadership and team coordination skills. Focus on optimizing production schedules and managing material flow. Master advanced problem-solving for complex polishing challenges and equipment malfunctions. Cultivate excellent communication abilities to liaise with production managers, quality control, and clients. Gain expertise in estimating project timelines and material needs.
Job Application Toolkit
Ace your application with our purpose-built resources:
Aluminum Polisher Cover Letter Examples
Personalizable templates that showcase your impact.
View examplesAluminum Polisher Job Description Template
Ready-to-use JD for recruiters and hiring teams.
View examplesGlobal Aluminum Polisher Opportunities
Aluminum Polishers find global demand in manufacturing, automotive, and aerospace industries. This role involves precise surface finishing, a skill valued worldwide for product aesthetics and functionality. International opportunities exist where advanced manufacturing flourishes, such as in Germany, Japan, and the United States. Cultural differences affect workplace safety standards and precision expectations. Professionals considering international moves should highlight specialized skills in their portfolios.
Global Salaries
Salaries for Aluminum Polishers vary significantly by region and industrial sector. In North America, particularly the United States, an Aluminum Polisher earns between $35,000 and $55,000 USD annually. Canadian salaries are comparable, ranging from $40,000 to $60,000 CAD ($29,000-$44,000 USD), often with good benefits.
European salaries for this role differ across countries. In Germany, a skilled Aluminum Polisher can expect €30,000 to €45,000 ($32,000-$48,000 USD) per year, with strong social security benefits. The UK offers £25,000 to £35,000 ($31,000-$44,000 USD). These figures reflect higher living costs in Western Europe. Eastern European nations like Poland might offer lower nominal salaries, around PLN 40,000-60,000 ($10,000-$15,000 USD), but purchasing power can be similar due to much lower expenses.
Asia-Pacific markets, especially in developed industrial hubs like Japan and Australia, provide competitive compensation. In Japan, salaries range from ¥3.5 million to ¥5 million ($23,000-$33,000 USD), often with performance bonuses. Australian polishers earn between AUD 50,000 and AUD 70,000 ($33,000-$46,000 USD). Latin American countries typically offer lower wages, with Brazil paying around BRL 30,000-50,000 ($6,000-$10,000 USD) annually. Experience and specific industry (e.g., aerospace vs. general manufacturing) heavily influence compensation globally.
Remote Work
Aluminum Polishing is a hands-on, physically demanding role requiring specialized machinery. Therefore, international remote work opportunities are virtually non-existent for this specific position. The core function involves direct interaction with materials and equipment on a factory floor or workshop. This means the job cannot be performed from a different country or even off-site.
Digital nomad opportunities or countries with favorable remote work policies do not apply to an Aluminum Polisher. Companies hiring for this role require on-site presence. Any discussion of international remote work for this profession would be inaccurate. The nature of the work necessitates a physical location and specialized tools.
Visa & Immigration
Immigration pathways for Aluminum Polishers typically fall under skilled worker visa categories. Popular destination countries like Germany, Canada, and Australia have specific requirements for trades. For instance, Canada's Express Entry system or Provincial Nominee Programs may consider skilled tradespersons. Germany's skilled immigration law requires a recognized qualification and a job offer. Credential recognition for vocational training is crucial; applicants often need their qualifications assessed.
Visa timelines vary, from a few months to over a year, depending on the country and application volume. Language requirements might apply, particularly for direct employer-sponsored visas; German or French proficiency helps in respective countries. English proficiency tests are common for immigration to English-speaking nations. Some countries offer fast-track programs for in-demand trades, though Aluminum Polisher is not universally considered a critical shortage occupation. Family visas for dependents are usually part of skilled worker programs, allowing spouses and children to accompany the primary applicant. Permanent residency can be a long-term goal, often requiring several years of work and tax contributions in the host country.
2025 Market Reality for Aluminum Polishers
Understanding current market conditions for an aluminum polisher is crucial for career success. The landscape has shifted significantly between 2023 and 2025, influenced by post-pandemic supply chain adjustments and the accelerating integration of automation. Broader economic factors, particularly in manufacturing and automotive sectors, directly impact job availability.
Market realities for polishers vary considerably by experience level, with highly skilled specialists finding more stable work than entry-level candidates. Geographic location, particularly proximity to industrial hubs, also plays a critical role. This analysis provides an honest assessment of these evolving market realities.
Current Challenges
Aluminum polishers face several challenges. Automation and robotic polishing systems reduce demand for manual labor, increasing competition for remaining roles. Economic slowdowns impact manufacturing and automotive sectors, directly cutting polishing needs. Skill gaps emerge as employers seek multi-skilled technicians capable of operating advanced machinery alongside traditional hand-polishing techniques. Entry-level positions are particularly scarce due to these shifts.
Growth Opportunities
Despite challenges, strong demand exists for highly skilled aluminum polishers in specific niches. The aerospace industry consistently seeks polishers for critical components requiring flawless finishes. Custom fabrication shops, luxury goods manufacturers, and restoration projects also present stable opportunities, valuing precision and artistry over speed.
Emerging opportunities include roles that combine traditional polishing with machine operation or quality control. Professionals who can program and maintain robotic polishing systems, or those specializing in post-automation finishing, gain a significant advantage. Developing expertise in materials science, particularly different aluminum alloys and their unique polishing requirements, also creates a competitive edge.
Underserved markets often involve specialized, low-volume production or repair work where automation is not cost-effective. Investing in certifications for advanced polishing techniques or cross-training in related metal finishing processes can open doors. Strategic career moves involve targeting companies focused on high-value, low-volume production rather than mass manufacturing. The market values adaptability and a willingness to learn new technologies alongside traditional craftsmanship.
Current Market Trends
Hiring for aluminum polishers in 2025 shows a nuanced picture. Demand remains steady in specialized, high-precision sectors like aerospace and custom fabrication where human touch offers superior finish. However, large-scale automotive and consumer goods manufacturing increasingly integrates robotic polishing, reducing the need for numerous manual polishers. This shift impacts job availability and skill requirements.
Economic conditions directly influence this field. A downturn in manufacturing or construction reduces demand for polished aluminum components, leading to fewer openings. Conversely, a strong economy can boost production, creating more opportunities, especially in niche markets or for custom work. The rise of automation in larger facilities means companies seek polishers who can manage automated systems, perform quality control, and handle intricate, non-standard parts that robots cannot yet master.
Employer requirements are evolving. While traditional hand-polishing expertise remains vital, a growing preference exists for candidates with mechanical aptitude, experience with CNC polishing machines, and a basic understanding of quality assurance software. Salaries for manual polishers remain stable but do not show significant growth, reflecting the increased efficiency from automation. Geographic variations are significant; areas with strong aerospace or luxury goods manufacturing hubs offer more consistent demand than regions dominated by mass-production industries. Remote work is not applicable for this hands-on role. Seasonal trends are minimal, but economic cycles in manufacturing dictate overall demand.
Emerging Specializations
The field of aluminum polishing, while traditional in its core function, stands on the cusp of significant evolution driven by advancements in material science, automation, and aesthetic demands across industries. Understanding these shifts is crucial for professionals seeking to advance their careers and secure future opportunities. New specialization areas are emerging from the intersection of precision finishing, sustainable practices, and advanced manufacturing techniques.
Early positioning in these emerging areas, particularly for 2025 and beyond, offers substantial career advantages. Professionals who acquire specialized skills in these cutting-edge niches often command premium compensation and experience accelerated career growth. This strategic focus allows them to become indispensable assets as industries adopt new production methods and quality standards.
While established polishing techniques remain valuable, focusing on emerging areas balances foundational expertise with future-oriented skills. These new specializations typically take several years to mature from nascent trends into widespread industry demands, creating significant job opportunities. This timeline offers a window for skilled polishers to acquire and refine the necessary expertise. Pursuing these cutting-edge areas involves a calculated risk, but the potential for higher earnings and leadership roles in a transforming industry often outweighs the initial investment in new skill acquisition.
Automated Polishing Cell Technician
As industries increasingly adopt robotic systems for repetitive tasks, the demand for aluminum polishers skilled in programming and overseeing automated polishing cells is rising. This specialization involves setting up robotic arms, selecting appropriate abrasives and compounds for different aluminum alloys, and fine-tuning robot paths to achieve precise, consistent finishes. It combines traditional polishing knowledge with advanced manufacturing technology, ensuring high-volume production with superior quality control.
Precision Surface Finishing Specialist
The aerospace, automotive, and medical device sectors increasingly require ultra-smooth, defect-free aluminum surfaces for performance and safety. This specialization focuses on achieving finishes with nanometer-level precision, often using advanced abrasive materials, controlled environments, and metrology instruments. It goes beyond cosmetic appeal, ensuring material integrity and optimal functionality for critical components where surface quality directly impacts product lifespan and performance.
Eco-Friendly Polishing & Waste Reduction Expert
With growing emphasis on environmental responsibility, aluminum polishers specializing in sustainable and eco-friendly practices are becoming highly sought after. This involves expertise in using biodegradable compounds, minimizing waste generation, optimizing water usage, and implementing closed-loop systems for polishing slurry. Professionals in this area help companies reduce their environmental footprint while maintaining high-quality finishes, addressing both regulatory compliance and corporate sustainability goals.
Hybrid Material Polishing Technician
Advanced composite materials often incorporate aluminum elements that require specific polishing techniques to maintain structural integrity and aesthetic appeal. This specialization involves working with hybrid materials where aluminum is bonded or integrated with other substances like carbon fiber or ceramics. It requires an understanding of how different materials react to polishing processes and the ability to prevent delamination or damage to the composite structure while achieving a flawless aluminum finish.
Additive Manufacturing Post-Processing Polisher
The increasing use of additive manufacturing (3D printing) for aluminum parts creates a unique demand for post-processing specialists. 3D-printed aluminum components often have rough surface finishes that require precise polishing to meet functional and aesthetic specifications. This specialization focuses on techniques to smooth and refine these unique surfaces, often involving a combination of traditional hand polishing and specialized automated or chemical-mechanical processes to achieve desired textures and tolerances.
Pros & Cons of Being an Aluminum Polisher
Making informed career decisions requires a clear understanding of both the benefits and challenges of any profession. The experience of an aluminum polisher, like many roles, can vary significantly depending on the specific industry, the size of the company, and the type of aluminum products being processed. What one person considers a benefit, another might view as a challenge, based on their personal values, physical capabilities, and career aspirations. For instance, the hands-on nature of the work might be a pro for some and a con for others. Moreover, the demands and opportunities within this role can evolve as one gains experience, shifting from early career focus on basic techniques to mid-career emphasis on efficiency and quality. This assessment aims to provide a realistic overview to help set appropriate expectations for those considering a career as an aluminum polisher.
Pros
- There is a consistent demand for skilled aluminum polishers across various industries, including automotive, aerospace, marine, and architectural fabrication, ensuring relatively stable employment opportunities.
- The role requires a strong sense of craftsmanship and attention to detail, providing a sense of satisfaction from transforming raw or dull aluminum into a highly finished, aesthetically pleasing product.
- Entry into this career often requires vocational training or on-the-job experience rather than a four-year degree, making it accessible to individuals seeking practical, hands-on work without extensive formal education.
- Aluminum polishing is a tangible skill that can be applied in diverse settings, from large manufacturing plants to small custom workshops, offering flexibility in work environments.
- The work is often focused and hands-on, appealing to individuals who prefer physical tasks and seeing immediate, visible results of their efforts.
- Developing expertise in specific polishing techniques, such as mirror finishing or satin brushing, can lead to specialization and increased value in niche markets, potentially commanding better compensation for unique skills.
- The job typically offers a predictable work schedule, often during regular business hours, which can contribute to a stable work-life balance compared to roles with unpredictable shifts or on-call requirements.
Cons
- The work environment for an aluminum polisher can be noisy and dusty, requiring constant use of personal protective equipment (PPE) like respirators and hearing protection, which can be uncomfortable for long shifts.
- This role often involves repetitive motions and standing for extended periods, leading to potential issues like carpal tunnel syndrome, back pain, or other musculoskeletal disorders over time.
- Exposure to aluminum dust and polishing compounds can pose respiratory risks if ventilation is inadequate or PPE is not properly worn, leading to potential long-term health concerns.
- Opportunities for significant career advancement within a polishing role itself are often limited; progression usually involves moving into supervisory roles or transitioning to different manufacturing specializations.
- The work can be monotonous due to the repetitive nature of the polishing process, which may not suit individuals who thrive on varied tasks or intellectual stimulation.
- Meeting tight production deadlines can lead to increased pressure and a fast-paced work environment, especially when there is high demand for polished parts.
- The pay scale for aluminum polishers, while stable, may not offer the high earning potential found in more technical or specialized manufacturing roles, often remaining within a moderate wage bracket for experienced workers, unless working on highly specialized or artistic pieces where skill commands a premium, which is rare.
Frequently Asked Questions
Aluminum Polishers face distinct challenges around mastering precision techniques and managing physical demands. This section addresses the most common questions about entering this trade, from required skills and safety protocols to career progression and earning potential in a specialized niche.
What are the entry requirements and typical training paths to become an Aluminum Polisher?
Becoming an Aluminum Polisher typically starts with on-the-job training or an apprenticeship, which can last from a few months to two years. Most employers seek candidates with good manual dexterity, attention to detail, and a willingness to learn. While no specific degree is usually required, vocational training in metal finishing or auto body repair can be beneficial.
How long does it take to become proficient and secure a stable job as an Aluminum Polisher?
The timeline to become proficient as an Aluminum Polisher varies. Entry-level positions can be secured relatively quickly with basic mechanical aptitude. However, achieving true mastery and efficiency in complex polishing tasks often takes 1-3 years of consistent practice and exposure to different types of aluminum products. Your progress depends on the training quality and your dedication to honing the craft.
What are the typical salary expectations for an Aluminum Polisher at different experience levels?
Starting salaries for Aluminum Polishers can range from $15-$20 per hour, depending on location and industry. Experienced polishers with specialized skills or those working on high-value products like custom vehicles or aerospace components can earn $25-$35 per hour or more. Overtime opportunities are common, which can significantly boost overall earnings.
What is the typical work-life balance like, considering the physical demands of the job?
The work-life balance for an Aluminum Polisher can vary. Many positions are full-time, often with standard day shifts. However, depending on project deadlines or production demands, overtime, including evenings or weekends, may be required. The work is physically demanding, involving standing for long periods, repetitive motions, and exposure to dust and noise, which can impact daily energy levels.
Is there good job security and market demand for Aluminum Polishers?
Job security for Aluminum Polishers is generally stable, particularly in industries that rely heavily on polished aluminum, such as automotive, aerospace, and manufacturing. While automation can impact some manual roles, the precision and artistry required for high-quality aluminum polishing often necessitate human skill. Demand for skilled tradespeople remains consistent, especially for those with a strong work ethic.
What are the potential career growth and advancement opportunities for an Aluminum Polisher?
Career growth for an Aluminum Polisher can involve becoming a lead polisher, supervisor, or moving into quality control or training roles within a manufacturing or finishing company. Some polishers also transition into related trades like metal fabrication or welding, or they may start their own specialized polishing businesses. Continuous learning and mastering new techniques can open up more opportunities.
What are the main health and safety concerns associated with this job, and how are they managed?
The primary health and safety concerns for Aluminum Polishers include respiratory issues from dust inhalation, hearing damage from noise exposure, and repetitive strain injuries. Proper personal protective equipment (PPE) such as respirators, hearing protection, and gloves are essential. Employers must provide adequate ventilation and training to mitigate these risks effectively.
Can Aluminum Polishers work remotely, or is it strictly an on-site role?
Remote work is generally not possible for an Aluminum Polisher, as the job requires direct hands-on work with machinery and materials in a workshop or factory setting. The need for specialized equipment, ventilation systems, and direct supervision means the work must be performed on-site. Therefore, location flexibility is limited to commuting to a physical workplace.
Related Careers
Explore similar roles that might align with your interests and skills:
Aluminum Pourer
A growing field with similar skill requirements and career progression opportunities.
Explore career guideAluminum Welder
A growing field with similar skill requirements and career progression opportunities.
Explore career guideAnodizer
A growing field with similar skill requirements and career progression opportunities.
Explore career guideMetal Die Finisher
A growing field with similar skill requirements and career progression opportunities.
Explore career guideTool Polishing Machine Operator
A growing field with similar skill requirements and career progression opportunities.
Explore career guideAssess your Aluminum Polisher readiness
Understanding where you stand today is the first step toward your career goals. Our Career Coach helps identify skill gaps and create personalized plans.
Skills Gap Analysis
Get a detailed assessment of your current skills versus Aluminum Polisher requirements. Our AI Career Coach identifies specific areas for improvement with personalized recommendations.
See your skills gapCareer Readiness Assessment
Evaluate your overall readiness for Aluminum Polisher roles with our AI Career Coach. Receive personalized recommendations for education, projects, and experience to boost your competitiveness.
Assess your readinessSimple pricing, powerful features
Upgrade to Himalayas Plus and turbocharge your job search.
Himalayas
Himalayas Plus
Himalayas Max
Find your dream job
Sign up now and join over 100,000 remote workers who receive personalized job alerts, curated job matches, and more for free!
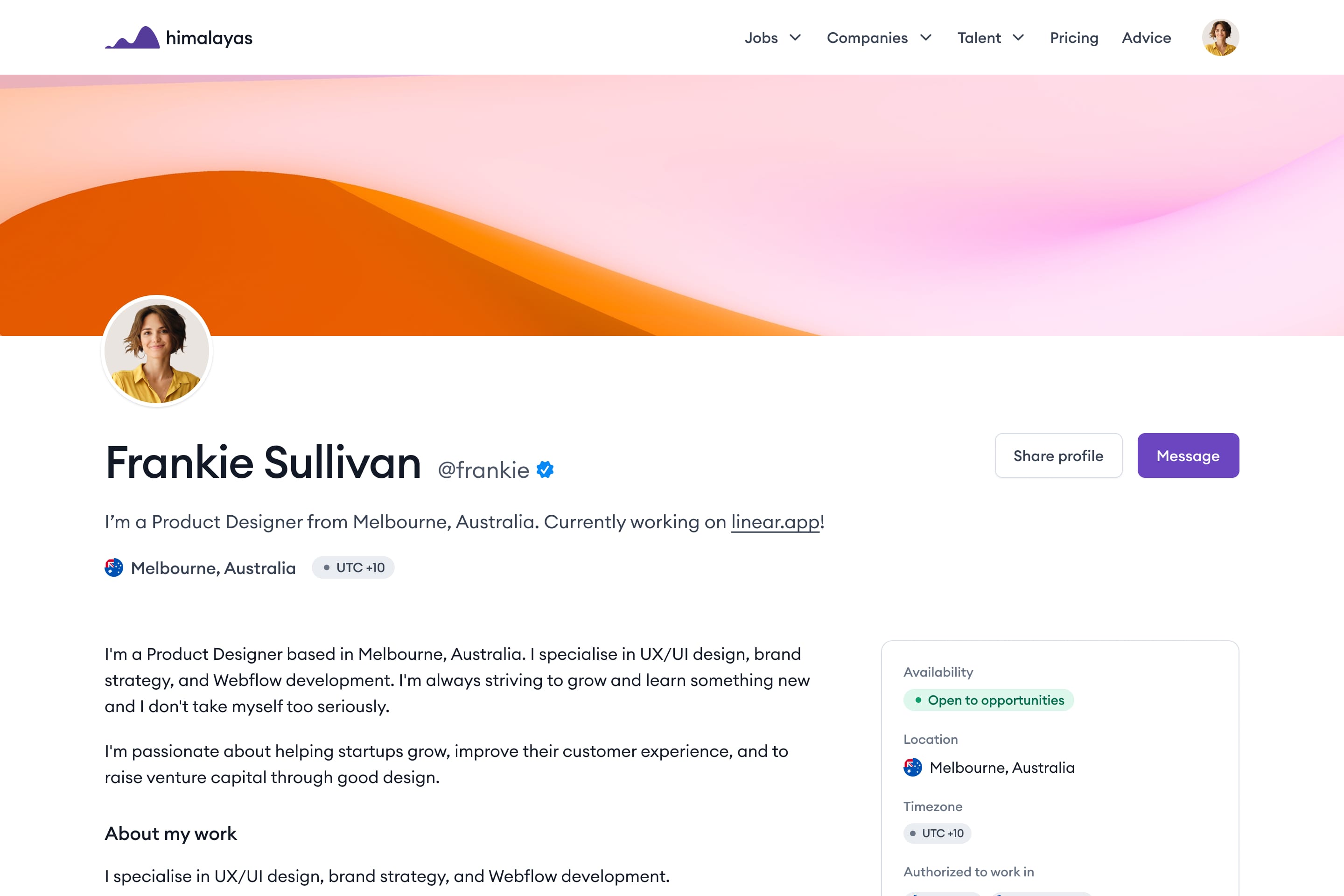