5 Warehouse Technician Interview Questions and Answers
Warehouse Technicians are responsible for the efficient handling, storage, and distribution of goods within a warehouse. They ensure inventory accuracy, maintain safety standards, and operate equipment such as forklifts. Junior technicians focus on basic tasks like organizing and labeling, while senior technicians may oversee operations, train staff, and implement process improvements. Supervisors and managers take on leadership roles, ensuring the warehouse runs smoothly and meets organizational goals. Need to practice for an interview? Try our AI interview practice for free then unlock unlimited access for just $9/month.
Unlimited interview practice for $9 / month
Improve your confidence with an AI mock interviewer.
No credit card required
1. Junior Warehouse Technician Interview Questions and Answers
1.1. Can you describe a time when you identified a potential safety hazard in the warehouse and how you addressed it?
Introduction
This question is crucial as it assesses your awareness of safety protocols and your proactive approach to maintaining a safe working environment, which is vital in warehouse operations.
How to answer
- Start by outlining the specific safety hazard you identified
- Explain the context of the situation and why it was concerning
- Detail the steps you took to address the hazard, including any communication with supervisors or team members
- Highlight the outcome of your actions and any improvements made to safety protocols
- Emphasize the importance of safety in warehouse operations
What not to say
- Failing to recognize the importance of safety procedures
- Describing a situation where you did nothing to address a hazard
- Minimizing the impact of the hazard or treating it lightly
- Not involving supervisors or failing to follow proper reporting procedures
Example answer
“While working at a local distribution center, I noticed that some pallets were stacked too high, creating a potential risk of them toppling over. I immediately reported this to my supervisor and suggested we implement a maximum height limit for stacking. As a result, we revised our stacking procedures, which improved overall safety and reduced the number of near-miss incidents by 30%.”
Skills tested
Question type
1.2. What strategies would you use to prioritize tasks during a busy shipping season?
Introduction
This question evaluates your time management and organizational skills, which are essential for a warehouse technician during peak operational periods.
How to answer
- Discuss your approach to assessing workload and identifying urgent tasks
- Explain how you would prioritize tasks based on deadlines and importance
- Mention any tools or systems you might use to stay organized
- Describe how you would communicate with team members to ensure coordination
- Highlight the importance of flexibility to adapt as situations change
What not to say
- Suggesting that you would tackle tasks randomly or without a plan
- Failing to recognize the need for teamwork and communication
- Ignoring the importance of deadlines and urgency
- Not addressing the need for adaptability during busy periods
Example answer
“During peak shipping seasons, I would first evaluate the daily workload and identify tasks that are time-sensitive, such as order fulfillment deadlines. I would create a prioritized list, using tools like checklists or warehouse management software for tracking. I would also communicate closely with my team to ensure we are aligned and able to assist each other as needed, allowing us to handle the increased volume efficiently.”
Skills tested
Question type
2. Warehouse Technician Interview Questions and Answers
2.1. Can you describe a time when you identified a safety hazard in the warehouse and how you addressed it?
Introduction
This question is crucial for evaluating your commitment to safety and your proactive approach in a warehouse environment, which is essential for a Warehouse Technician.
How to answer
- Use the STAR method (Situation, Task, Action, Result) to structure your response
- Clearly describe the specific safety hazard you identified
- Explain the actions you took to address the hazard, including any collaboration with your team
- Discuss the outcome of your actions and the impact on your colleagues and the warehouse operations
- Emphasize any changes or improvements made to prevent future hazards
What not to say
- Downplaying the importance of safety in the workplace
- Failing to provide a specific example or being vague
- Blaming others for the hazard instead of focusing on your actions
- Neglecting to mention the follow-up actions taken after addressing the hazard
Example answer
“At Amazon, I noticed that the storage shelves were overstocked, creating a potential risk for items falling. I immediately reported it to my supervisor and worked with the team to reorganize the shelves, ensuring that heavier items were stored lower down. As a result, we significantly reduced the risk of accidents, and my actions led to a new policy for shelf stocking that improved overall safety in the warehouse.”
Skills tested
Question type
2.2. How do you handle high-pressure situations, especially during peak seasons or when deadlines are tight?
Introduction
This question assesses your ability to perform under pressure, which is a critical skill for Warehouse Technicians, especially during busy times.
How to answer
- Describe your strategies for managing stress and staying organized
- Provide an example of a high-pressure situation you faced and how you handled it
- Explain how you prioritize tasks during busy periods
- Discuss any tools or methods you use to maintain efficiency and accuracy
- Highlight the importance of teamwork and communication in stressful situations
What not to say
- Claiming you never feel stressed or that pressure doesn't affect you
- Providing a vague or unrelated example
- Ignoring the role of teamwork and support from colleagues
- Suggesting that you often make mistakes under pressure without learning from them
Example answer
“During the holiday season at DHL, we experienced a surge in shipments, which created intense pressure. I focused on staying organized by breaking tasks into manageable parts and prioritizing urgent orders. I communicated closely with my team to ensure everyone was on the same page. This approach helped us meet our deadlines, and we managed to process 20% more packages than the previous year without compromising quality.”
Skills tested
Question type
3. Senior Warehouse Technician Interview Questions and Answers
3.1. Can you describe a time when you identified a significant safety hazard in the warehouse? What actions did you take?
Introduction
This question is crucial as it assesses your awareness of safety protocols and your proactive approach to ensuring a safe working environment, which is vital for a Senior Warehouse Technician.
How to answer
- Use the STAR method (Situation, Task, Action, Result) to structure your response.
- Clearly describe the situation, including the specific safety hazard you identified.
- Explain the potential risks associated with the hazard and how it could impact operations.
- Detail the actions you took to address the issue, including any communication with team members or management.
- Share the positive outcomes resulting from your actions, such as improved safety protocols or reduced incidents.
What not to say
- Ignoring the importance of safety protocols or regulations.
- Failing to take responsibility or initiative in addressing safety issues.
- Describing a situation without detailing the actions taken.
- Overemphasizing the problem without highlighting the resolution.
Example answer
“At my previous job at Flipkart, I noticed that several pallets were stacked too high, creating a potential tipping hazard. I immediately reported it to my supervisor and initiated a review of our stacking protocols. We implemented new guidelines and conducted a training session for the team. As a result, we significantly reduced near-miss incidents related to stacking hazards over the following months.”
Skills tested
Question type
3.2. How do you ensure accurate inventory management in a high-volume warehouse?
Introduction
This question evaluates your technical skills and methods for maintaining inventory accuracy, which are essential for efficient warehouse operations.
How to answer
- Describe the tools and technologies you use for inventory management, such as warehouse management systems (WMS).
- Explain your process for conducting regular inventory counts and reconciliations.
- Detail how you train and supervise team members to follow inventory protocols.
- Share any specific metrics or improvements you've achieved in inventory accuracy.
- Discuss your approach to handling discrepancies or errors in inventory.
What not to say
- Suggesting that inventory management isn't a priority.
- Failing to mention the use of technology or software.
- Providing vague answers without specific examples or metrics.
- Neglecting to acknowledge the importance of teamwork in inventory management.
Example answer
“In my role at Amazon, I utilized the WMS to track inventory levels and automate reorder points. I conducted weekly inventory audits and trained my team on proper scanning techniques. As a result, we improved our inventory accuracy from 85% to 98%, significantly reducing stock discrepancies and improving order fulfillment times.”
Skills tested
Question type
4. Warehouse Supervisor Interview Questions and Answers
4.1. Can you describe a time when you had to improve the efficiency of a warehouse operation?
Introduction
This question is crucial for understanding your problem-solving skills and ability to implement process improvements, both of which are essential for a Warehouse Supervisor.
How to answer
- Use the STAR method (Situation, Task, Action, Result) to structure your response.
- Clearly describe the inefficiency you identified and its impact on operations.
- Detail the specific actions you took to address the issue, including any tools or systems you implemented.
- Quantify the results to demonstrate the effectiveness of your solution.
- Discuss any feedback received from team members or upper management after the changes were made.
What not to say
- Failing to provide specific examples or results.
- Overemphasizing team members' faults without taking responsibility.
- Being vague about the steps taken to improve efficiency.
- Neglecting to mention any challenges faced during implementation.
Example answer
“At XYZ Logistics, I noticed that order picking was taking too long, leading to delays in dispatch. I conducted a time study and reorganized the layout to minimize travel distance for pickers. We implemented a batch picking system, which reduced picking time by 30%. This change not only improved efficiency but also increased team morale as they felt more productive.”
Skills tested
Question type
4.2. How do you handle conflicts between team members in a warehouse setting?
Introduction
This question assesses your conflict resolution and leadership skills, which are key in managing a diverse team in a fast-paced environment.
How to answer
- Describe your approach to conflict resolution, emphasizing communication and understanding.
- Provide an example of a specific conflict and how you addressed it.
- Explain how you ensure that all parties feel heard and valued.
- Discuss the outcome and any long-term changes that resulted from the resolution.
- Highlight the importance of maintaining a positive work environment.
What not to say
- Avoiding conflicts instead of addressing them.
- Taking sides without hearing all perspectives.
- Not providing a concrete example of conflict resolution.
- Suggesting that conflicts are rare or unimportant in a warehouse setting.
Example answer
“In my previous role at ABC Warehousing, two team members had a disagreement about task responsibilities which affected the workflow. I arranged a meeting where both could express their concerns. We discussed their viewpoints and reached a compromise where responsibilities were shared more equally. This not only resolved the conflict but also fostered better teamwork moving forward.”
Skills tested
Question type
4.3. What strategies would you implement to ensure safety compliance in the warehouse?
Introduction
Safety compliance is vital in warehouse operations, making this question essential to evaluate your understanding of safety protocols and your ability to enforce them effectively.
How to answer
- Outline specific safety regulations relevant to warehouse operations.
- Discuss strategies such as regular training sessions, safety audits, and employee engagement initiatives.
- Emphasize the importance of fostering a safety-first culture among team members.
- Provide an example of how you previously improved safety compliance in a warehouse.
- Mention how you would handle non-compliance issues if they arise.
What not to say
- Ignoring the importance of safety regulations.
- Suggesting that safety training is unnecessary once employees are onboarded.
- Failing to provide examples of previous safety initiatives.
- Neglecting to mention the role of communication in safety compliance.
Example answer
“At my last job with DEF Distribution, I implemented a monthly safety training program that included hands-on demonstrations of safe equipment usage. We also conducted quarterly safety audits and encouraged team members to report hazards proactively. As a result, we reduced workplace accidents by 40% within a year, demonstrating a strong commitment to safety compliance.”
Skills tested
Question type
5. Warehouse Manager Interview Questions and Answers
5.1. Can you describe a time when you optimized warehouse operations to improve efficiency?
Introduction
This question evaluates your ability to analyze and enhance operational processes, which is critical for a Warehouse Manager tasked with maximizing productivity.
How to answer
- Use the STAR method (Situation, Task, Action, Result) to structure your response.
- Clearly outline the initial inefficiencies you identified in the warehouse.
- Describe the specific strategies or technologies you implemented to address those inefficiencies.
- Quantify the results achieved in terms of time saved, cost reduction, or increased throughput.
- Highlight any team involvement or training you initiated during the process.
What not to say
- Focusing on minor changes that had little impact.
- Failing to provide measurable outcomes or results.
- Neglecting to mention the team's role in the process.
- Blaming others for existing inefficiencies without taking ownership.
Example answer
“At my previous role with Bidvest, I noticed our order picking process was taking too long, leading to delays. I implemented a new layout that utilized a zone picking method, which reduced travel time. As a result, we improved order processing speed by 30% and increased overall warehouse efficiency, leading to a 15% reduction in labor costs. This experience taught me the importance of continuous improvement and teamwork in operational success.”
Skills tested
Question type
5.2. How do you handle conflicts or disagreements among warehouse staff?
Introduction
This question assesses your conflict resolution skills and ability to maintain a positive work environment, which is essential for team cohesion in a warehouse setting.
How to answer
- Describe your approach to addressing conflicts promptly and fairly.
- Share examples of specific conflict situations and how you resolved them.
- Emphasize the importance of communication and active listening in your resolution process.
- Discuss how you ensure that all parties feel heard and valued.
- Highlight any follow-up actions to prevent similar conflicts in the future.
What not to say
- Avoiding conflict instead of addressing it.
- Taking sides without understanding all perspectives.
- Describing situations where you escalated conflicts rather than resolving them.
- Neglecting to mention follow-up or prevention strategies.
Example answer
“In my previous role at Massmart, I encountered a situation where two team members disagreed over their responsibilities during a peak season. I invited both employees to a private discussion to understand their viewpoints. By facilitating a conversation and clarifying roles, we reached a consensus that improved collaboration. This not only resolved the conflict but also strengthened their working relationship, and I continued to check in with them to ensure smooth operations going forward.”
Skills tested
Question type
Similar Interview Questions and Sample Answers
Simple pricing, powerful features
Upgrade to Himalayas Plus and turbocharge your job search.
Himalayas
Himalayas Plus
Himalayas Max
Find your dream job
Sign up now and join over 100,000 remote workers who receive personalized job alerts, curated job matches, and more for free!
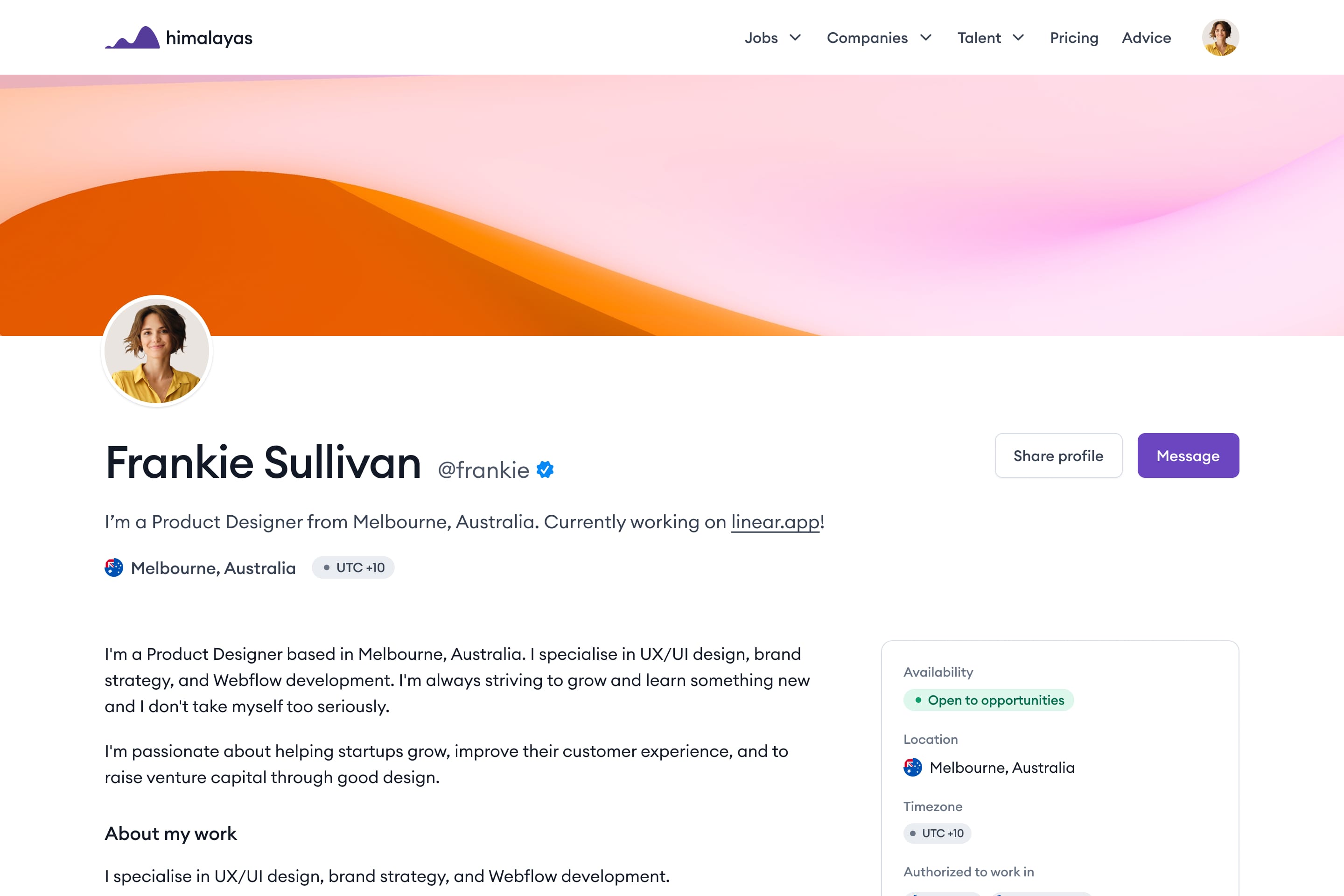