6 Warehouse Operations Manager Interview Questions and Answers
Warehouse Operations Managers oversee the daily operations of a warehouse, ensuring efficient storage, inventory management, and distribution of goods. They are responsible for maintaining safety standards, optimizing workflows, and managing staff to meet organizational goals. Junior roles may assist in supervising specific tasks, while senior roles involve strategic planning, managing multiple facilities, and leading large teams. Need to practice for an interview? Try our AI interview practice for free then unlock unlimited access for just $9/month.
Unlimited interview practice for $9 / month
Improve your confidence with an AI mock interviewer.
No credit card required
1. Assistant Warehouse Operations Manager Interview Questions and Answers
1.1. Can you describe a time when you improved warehouse efficiency? What steps did you take?
Introduction
This question assesses your ability to identify inefficiencies and implement improvements in warehouse operations, which is critical for an Assistant Warehouse Operations Manager.
How to answer
- Use the STAR method to structure your response: Situation, Task, Action, Result.
- Clearly outline the inefficiency you identified and its impact on operations.
- Detail the specific actions you took to address the issue, including any tools or methodologies used.
- Quantify the results achieved, such as time saved or increased throughput.
- Highlight any collaboration with team members or other departments.
What not to say
- Avoid vague answers without specific examples.
- Do not focus on individual contributions without mentioning teamwork.
- Refrain from discussing improvements that did not yield positive results without learnings.
- Avoid using jargon without explaining its relevance.
Example answer
“At my previous role at Woolworths, I noticed that our picking process was causing significant delays. I conducted a time-motion study and identified that reorganizing our storage layout would streamline the process. After implementing a new layout, we reduced order picking time by 20%, which improved overall efficiency and allowed us to handle 15% more orders during peak times.”
Skills tested
Question type
1.2. How do you handle conflicts between team members in a warehouse setting?
Introduction
This question evaluates your conflict resolution skills and ability to maintain a positive working environment, essential for effective warehouse management.
How to answer
- Describe your approach to understanding the root cause of the conflict.
- Explain how you facilitate communication between the parties involved.
- Detail any steps you take to mediate the situation and find a resolution.
- Share examples of how you’ve successfully resolved conflicts in the past.
- Highlight the importance of maintaining team morale and productivity.
What not to say
- Avoid discussing conflicts that escalated without resolution.
- Do not suggest ignoring conflicts or hoping they resolve on their own.
- Refrain from placing blame on team members without taking accountability.
- Avoid vague or generic conflict resolution strategies.
Example answer
“In my role at Coles, I encountered a situation where two team members had a disagreement over shift responsibilities. I brought them together in a private meeting to discuss their concerns. By facilitating open dialogue, we identified misunderstandings about workload expectations. We reached an agreement on responsibilities that satisfied both parties, which not only resolved the conflict but also strengthened their collaboration moving forward.”
Skills tested
Question type
2. Warehouse Operations Manager Interview Questions and Answers
2.1. Can you describe a time when you successfully improved warehouse efficiency?
Introduction
This question assesses your ability to analyze operations and implement improvements, which is crucial for a Warehouse Operations Manager.
How to answer
- Use the STAR method to structure your response: Situation, Task, Action, Result.
- Clearly describe the initial state of efficiency and the specific challenges faced.
- Detail the steps you took to analyze the situation and identify areas for improvement.
- Explain the solutions you implemented and how you engaged your team in the process.
- Quantify the results, such as improved turnaround times or cost savings.
What not to say
- Focusing only on minor changes without significant impact.
- Neglecting to mention teamwork or collaboration.
- Providing vague examples without specific metrics.
- Failing to discuss any challenges faced during the process.
Example answer
“At Amazon, I noticed our order picking process was taking longer than industry standards. I conducted a time and motion study and found that reorganizing the layout of frequently picked items could save time. After implementing a new layout and training the team on best practices, we improved our picking efficiency by 30%, significantly reducing order fulfillment times.”
Skills tested
Question type
2.2. How do you handle conflicts among team members in a warehouse environment?
Introduction
This question evaluates your conflict resolution skills and your ability to maintain a positive working environment, which is essential in managing warehouse operations.
How to answer
- Describe your approach to identifying the root cause of conflicts.
- Discuss your communication strategies for addressing issues with team members.
- Explain how you facilitate discussions to reach a resolution.
- Highlight the importance of maintaining morale and team cohesion.
- Provide examples of successful conflict resolution in previous roles.
What not to say
- Avoiding conflict or ignoring issues.
- Using authoritarian methods to resolve disputes.
- Not having a systematic approach to conflict resolution.
- Focusing only on the negative aspects without highlighting positive outcomes.
Example answer
“In my role at DHL, I encountered a situation where two team members disagreed over task responsibilities, leading to tension. I organized a meeting where both could express their concerns. By facilitating open communication and clarifying roles, we reached a mutual understanding, leading to improved collaboration. The resolution not only alleviated the conflict but also increased productivity as the team worked more effectively together afterward.”
Skills tested
Question type
3. Senior Warehouse Operations Manager Interview Questions and Answers
3.1. Can you describe a time when you implemented a process improvement in warehouse operations? What was the impact?
Introduction
This question assesses your ability to drive efficiency and enhance operations, which is crucial for a Senior Warehouse Operations Manager.
How to answer
- Use the STAR method (Situation, Task, Action, Result) to structure your answer
- Clearly define the process that needed improvement and why it was essential to address it
- Detail the steps you took to analyze the situation and implement the improvement
- Quantify the results, such as time saved, cost reductions, or increased accuracy
- Reflect on any challenges faced and how you overcame them
What not to say
- Describing a minor change that had little impact
- Failing to provide specific metrics or outcomes
- Taking sole credit without acknowledging team contributions
- Not mentioning how you measured the success of the improvement
Example answer
“At a distribution center for Grupo Pão de Açúcar, we faced issues with order picking accuracy. I analyzed our picking process and identified that implementing a zone picking system would streamline operations. After training the team and adjusting our layout, we improved accuracy from 85% to 97% within three months, reducing returns and increasing customer satisfaction significantly.”
Skills tested
Question type
3.2. How do you ensure safety and compliance in warehouse operations?
Introduction
This question evaluates your knowledge of safety regulations and your commitment to maintaining a compliant and safe working environment.
How to answer
- Discuss relevant safety regulations in Brazil, such as NR-11 for handling materials
- Explain how you conduct regular safety audits and training programs
- Describe your approach to fostering a safety culture among employees
- Provide examples of how you've successfully handled compliance issues
- Mention how you stay updated on changes in regulations
What not to say
- Ignoring the importance of safety culture and training
- Failing to mention specific safety regulations
- Providing vague responses without concrete examples
- Suggesting that safety compliance is solely the responsibility of safety officers
Example answer
“In my previous position at Magazine Luiza, I prioritized safety by implementing monthly safety audits and training sessions focused on proper equipment use and hazard awareness. We achieved a 30% reduction in workplace accidents within a year. I also established a safety committee to encourage employee feedback on safety practices, ensuring compliance with NR-11 and other regulations.”
Skills tested
Question type
3.3. How would you handle a situation where there is a significant inventory discrepancy?
Introduction
This question tests your problem-solving and analytical skills in managing inventory, a critical aspect of warehouse operations.
How to answer
- Describe your initial steps in investigating the discrepancy
- Discuss how you would engage with team members to gather insights
- Explain the methods you would use to reconcile inventory records
- Outline how you would prevent future discrepancies through process improvements
- Mention the importance of communication with stakeholders about the situation
What not to say
- Assuming that discrepancies are always due to employee error
- Neglecting the need for a thorough investigation
- Failing to mention preventative measures for the future
- Downplaying the significance of inventory accuracy
Example answer
“At a previous role with Carrefour, we discovered a significant inventory discrepancy during a monthly audit. I immediately initiated an investigation, involving team members who handled the stock. We traced the issue back to a mislabeling error in our inventory management system. After rectifying the records, I implemented a double-check system for incoming stock, which greatly improved our accuracy rates moving forward.”
Skills tested
Question type
4. Regional Warehouse Operations Manager Interview Questions and Answers
4.1. Can you describe a time when you improved efficiency in warehouse operations?
Introduction
This question assesses your ability to identify inefficiencies and implement effective solutions, which is crucial for a Regional Warehouse Operations Manager.
How to answer
- Start with the specific inefficiency you identified in the warehouse operations
- Explain the analysis process you undertook to understand the root causes
- Detail the steps you took to implement changes and improvements
- Quantify the results achieved post-implementation, such as time saved or cost reduced
- Discuss any feedback received from the team or superiors about the changes
What not to say
- Not providing specific metrics or outcomes from the improvements
- Focusing solely on the problem without detailing the solution
- Neglecting to mention how you involved your team in the process
- Giving an example that lacks clear relevance to warehouse operations
Example answer
“At Alibaba, I identified that our order picking process was taking too long, causing delays in shipments. I analyzed the picking paths and implemented a new layout based on product demand frequency, which reduced travel time by 30%. This change not only improved our order fulfillment times but also increased team morale as employees found the new system easier to navigate.”
Skills tested
Question type
4.2. How do you handle conflicts between warehouse staff and management regarding operational procedures?
Introduction
This question evaluates your conflict resolution and communication skills, essential for maintaining a productive warehouse environment.
How to answer
- Describe your approach to understanding different perspectives in a conflict
- Emphasize the importance of open communication and active listening
- Detail how you would mediate discussions to find a common ground
- Provide an example of a past conflict and how you resolved it
- Highlight any changes you made to prevent similar conflicts in the future
What not to say
- Avoiding addressing the conflict directly
- Suggesting that conflicts are not a concern in operations
- Failing to acknowledge the importance of team dynamics
- Providing a vague answer without specific examples
Example answer
“When conflicts arise between staff and management, I advocate for open discussions. For instance, at JD.com, a disagreement occurred over the implementation of new safety protocols. I facilitated a meeting where both sides could voice their concerns. By actively listening and finding a compromise that ensured safety while addressing staff workload, we reached a solution that satisfied everyone, and I later introduced regular check-ins to keep communication open.”
Skills tested
Question type
5. Director of Warehouse Operations Interview Questions and Answers
5.1. Can you describe a time when you improved warehouse efficiency? What steps did you take?
Introduction
This question assesses your ability to analyze operational processes and implement improvements, which is crucial for a Director of Warehouse Operations.
How to answer
- Use the STAR method to structure your response: Situation, Task, Action, Result.
- Clearly define the inefficiency issue you identified.
- Detail the methods you used to analyze the process (e.g., data analysis, team feedback).
- Explain the solution you implemented and the rationale behind it.
- Quantify the results to showcase the impact of your actions.
What not to say
- Providing vague descriptions without specific examples.
- Failing to quantify results or impact.
- Not mentioning team involvement or collaboration.
- Blaming others for inefficiencies instead of focusing on your contributions.
Example answer
“At my previous role with DHL, I noticed that our order picking process was causing delays. I analyzed the workflow and implemented a zone picking system that divided the warehouse into sections. This change reduced picking time by 30% and improved order accuracy by 15%. The success of this initiative highlighted the importance of operational analysis and teamwork in driving efficiency.”
Skills tested
Question type
5.2. How do you ensure safety compliance in warehouse operations?
Introduction
Safety compliance is critical in warehouse operations to protect employees and reduce liability. This question evaluates your knowledge and approach to safety management.
How to answer
- Discuss your understanding of relevant safety regulations and standards.
- Explain how you conduct safety training and ensure all staff are informed.
- Describe your strategies for regular safety audits and inspections.
- Share how you promote a culture of safety within the team.
- Provide examples of past initiatives that improved safety metrics.
What not to say
- Neglecting to mention specific safety regulations.
- Suggesting safety is solely the responsibility of the safety officer.
- Failing to provide examples of proactive safety measures.
- Overlooking the importance of employee engagement in safety practices.
Example answer
“At my last position with DB Schenker, I implemented a comprehensive safety training program that included regular workshops and hands-on drills. We conducted quarterly safety audits, resulting in a 20% reduction in workplace incidents within a year. I believe fostering a culture of accountability and open communication about safety is key to ensuring compliance and protecting our employees.”
Skills tested
Question type
6. VP of Warehouse Operations Interview Questions and Answers
6.1. Can you describe a time when you implemented a process improvement in warehouse operations that significantly increased efficiency?
Introduction
This question is crucial for understanding your ability to drive operational improvements and enhance efficiency in warehouse environments, which is a key responsibility for a VP of Warehouse Operations.
How to answer
- Use the STAR method (Situation, Task, Action, Result) to structure your response.
- Clearly define the specific problem or inefficiency you identified.
- Explain the steps you took to analyze the situation and develop a solution.
- Detail the implementation process, including team involvement and any challenges faced.
- Quantify the improvements achieved, such as reductions in labor costs, time savings, or increased order accuracy.
What not to say
- Avoid vague descriptions without specific metrics or outcomes.
- Don't focus solely on the problem without discussing your solution.
- Refrain from taking sole credit for team efforts.
- Do not neglect to mention how you managed resistance to change, if applicable.
Example answer
“At Amazon, I noticed our order picking process was causing delays and increasing labor costs. I led a cross-functional team to analyze the workflow and implemented a new pick-to-light system. This change reduced our picking time by 30%, resulting in a 15% decrease in labor costs over six months. The experience reinforced the importance of data-driven decision-making and teamwork in operational success.”
Skills tested
Question type
6.2. How do you ensure compliance with safety regulations and standards in warehouse operations?
Introduction
This question assesses your knowledge and commitment to safety standards, which are critical in warehouse operations to protect employees and maintain operational integrity.
How to answer
- Describe your approach to keeping up-to-date with safety regulations and industry standards.
- Explain the training programs you’ve implemented for staff regarding safety practices.
- Discuss how you conduct regular audits or inspections to ensure compliance.
- Share examples of how you've addressed safety issues in the past.
- Highlight your strategies for fostering a culture of safety within the organization.
What not to say
- Neglecting to mention the importance of safety training for employees.
- Downplaying the significance of safety audits and compliance checks.
- Using vague statements without specific examples of safety initiatives.
- Avoiding discussion on how you handle safety violations.
Example answer
“At DHL, I prioritized safety by implementing a comprehensive training program that included regular workshops and simulations for all warehouse staff. I established a safety committee that conducted monthly audits to identify potential hazards. When we had a minor incident, I led a root cause analysis, resulting in new safety protocols that decreased incidents by 40% over the next year. My commitment to safety is rooted in fostering a culture where employees feel responsible for their own and each other’s safety.”
Skills tested
Question type
Similar Interview Questions and Sample Answers
Simple pricing, powerful features
Upgrade to Himalayas Plus and turbocharge your job search.
Himalayas
Himalayas Plus
Himalayas Max
Find your dream job
Sign up now and join over 100,000 remote workers who receive personalized job alerts, curated job matches, and more for free!
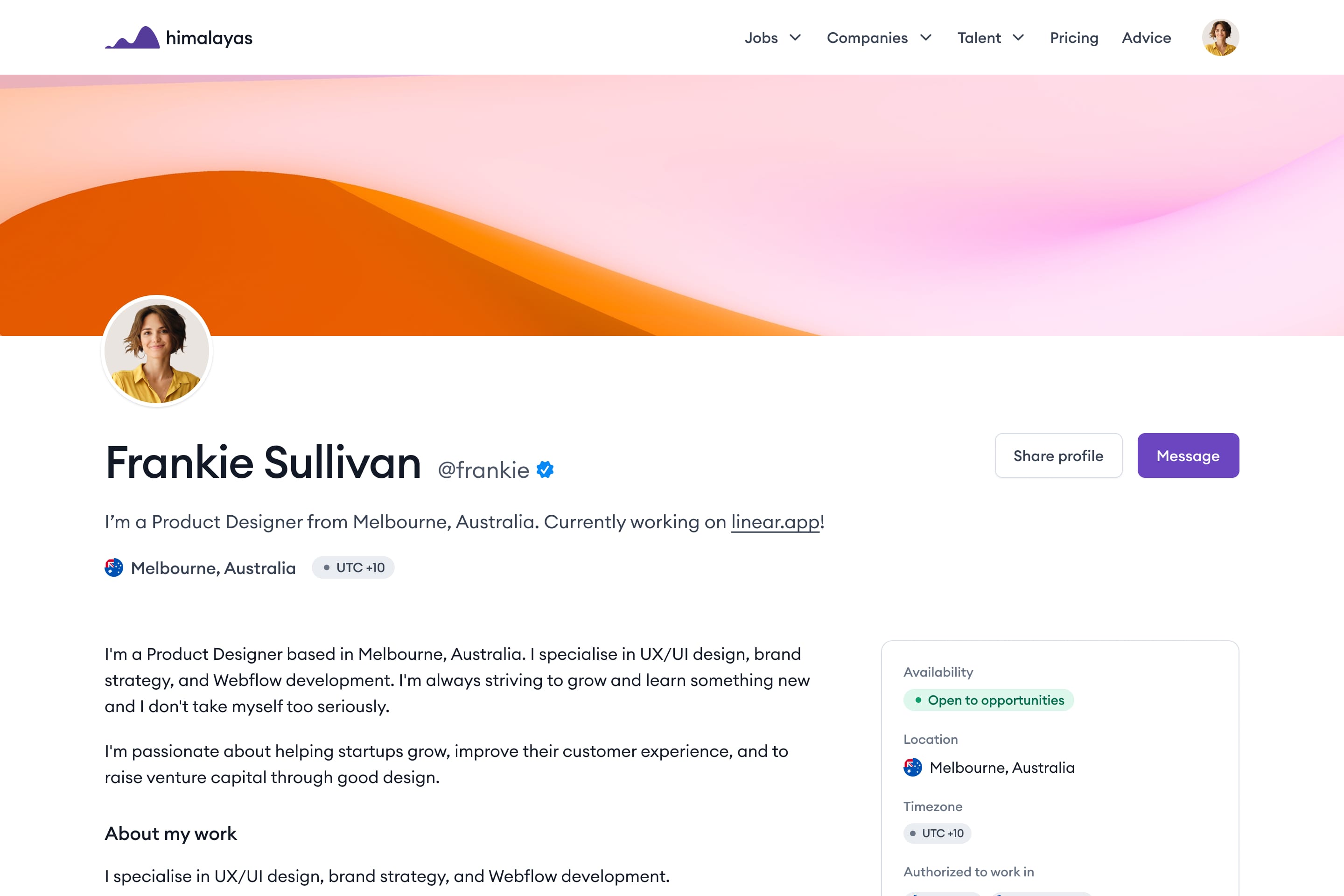