3 Tobacco Drier Operator Interview Questions and Answers
Tobacco Drier Operators are responsible for overseeing the drying process of tobacco leaves to ensure quality and consistency. They monitor and adjust equipment, maintain optimal drying conditions, and ensure the final product meets industry standards. Junior operators focus on operating machinery under supervision, while senior and lead operators take on responsibilities such as troubleshooting, process optimization, and training new staff. Need to practice for an interview? Try our AI interview practice for free then unlock unlimited access for just $9/month.
Unlimited interview practice for $9 / month
Improve your confidence with an AI mock interviewer.
No credit card required
1. Tobacco Drier Operator Interview Questions and Answers
1.1. Can you describe your experience with managing the drying process of tobacco leaves?
Introduction
This question is vital as it evaluates your technical knowledge and hands-on experience with the drying process, which is crucial for maintaining the quality of tobacco.
How to answer
- Begin with an overview of your experience in tobacco processing, specifying your roles and responsibilities.
- Detail the specific methods and equipment you've used for drying tobacco leaves.
- Discuss how you ensure optimal moisture content and quality during the drying process.
- Mention any challenges you faced and how you overcame them.
- Quantify your achievements, such as improvements in drying efficiency or quality control.
What not to say
- Providing vague details about the drying process without specific examples.
- Neglecting to mention the importance of quality control.
- Focusing too much on theory without practical examples.
- Failing to acknowledge any challenges faced in the process.
Example answer
“In my role at Philip Morris, I managed the drying process for Virginia tobacco. I utilized both air and heated drying methods, carefully monitoring humidity levels to ensure we achieved a moisture content of around 12%. This not only maintained the quality of the tobacco but also improved our drying efficiency by 15%. I faced challenges during a humid season, but by adjusting our airflow and drying times, we minimized quality loss significantly.”
Skills tested
Question type
1.2. Describe a time when you had to troubleshoot a problem with the drying equipment.
Introduction
This question assesses your problem-solving skills and ability to think critically under pressure, both of which are essential for a Tobacco Drier Operator.
How to answer
- Use the STAR method to structure your response: Situation, Task, Action, Result.
- Describe the specific problem you encountered with the equipment.
- Explain the steps you took to diagnose and resolve the issue.
- Highlight the outcome and any long-term improvements made as a result.
- Mention any collaboration with maintenance teams or other operators.
What not to say
- Avoid blaming others for the equipment failure.
- Do not provide a solution that lacks detail or clarity.
- Steer clear of overly technical jargon that may not be understood.
- Neglecting to mention the importance of safety protocols.
Example answer
“While operating the drying system at Reynolds American, I noticed the moisture levels were not decreasing as expected. I assessed the air circulation and discovered a blockage in the exhaust duct. I collaborated with the maintenance team to clear the duct and recalibrated the drying controls. As a result, we restored normal drying operations within hours, and I implemented a routine check to prevent future blockages.”
Skills tested
Question type
2. Senior Tobacco Drier Operator Interview Questions and Answers
2.1. Can you describe your experience with operating and maintaining tobacco drying equipment?
Introduction
This question is crucial for assessing your hands-on experience and technical expertise in operating specialized machinery, which is vital for ensuring product quality in tobacco processing.
How to answer
- Begin by summarizing your experience with different types of tobacco drying equipment.
- Discuss specific maintenance tasks you performed regularly to ensure optimal performance.
- Highlight any troubleshooting methods you used to resolve equipment issues.
- Mention safety protocols you followed while operating machinery.
- Include any improvements you made to enhance efficiency or quality.
What not to say
- Vague descriptions of experience without specific details.
- Failing to mention safety practices or compliance with regulations.
- Neglecting to discuss the importance of quality control.
- Providing a list of tasks without demonstrating understanding of the equipment.
Example answer
“In my previous role at a tobacco processing facility, I operated several types of drying equipment, including convection and vacuum dryers. I regularly performed maintenance checks, replacing worn-out components to prevent breakdowns. Once, I identified a humidity control issue that was affecting product quality, and I adjusted the settings, resulting in a 15% reduction in moisture content, which improved the final product. Safety was always my priority, ensuring compliance with all operational protocols.”
Skills tested
Question type
2.2. Tell me about a time when you had to troubleshoot a problem during the drying process.
Introduction
This question evaluates your critical thinking and problem-solving skills, essential for quickly addressing issues that may arise during the tobacco drying process.
How to answer
- Use the STAR method to structure your answer: Situation, Task, Action, Result.
- Clearly describe the problem and its potential impact on production.
- Explain the steps you took to diagnose and resolve the issue.
- Highlight any teamwork or communication involved in finding a solution.
- Share the outcome and any lessons learned from the experience.
What not to say
- Failing to take ownership of the problem or blaming others.
- Describing a situation without outlining your specific actions.
- Neglecting to mention how you communicated with your team during the issue.
- Giving an example that lacks a clear resolution or outcome.
Example answer
“At my last job at a tobacco plant, we experienced an unexpected drop in drying efficiency. I noticed that the airflow was lower than normal. I gathered my team, and we conducted a quick inspection, discovering a blockage in the air duct. After clearing it, we monitored the system and restored efficiency. This incident taught me the importance of teamwork and proactive communication in troubleshooting.”
Skills tested
Question type
3. Lead Tobacco Drier Operator Interview Questions and Answers
3.1. Can you describe your experience with managing and operating tobacco drying equipment?
Introduction
This question is crucial as it assesses your technical proficiency and hands-on experience with the specific machinery used in tobacco processing, which is vital for maintaining product quality and operational efficiency.
How to answer
- Begin with your specific roles and responsibilities related to tobacco drying equipment.
- Discuss the types of equipment you have operated and any relevant certifications or training.
- Explain how you ensure the equipment operates efficiently and safely.
- Include examples of troubleshooting issues or optimizing drying processes.
- Highlight any improvements you implemented that enhanced productivity or quality.
What not to say
- Claiming to have experience without specific details or examples.
- Ignoring safety protocols and procedures related to equipment operation.
- Failing to mention your role in maintaining or troubleshooting the equipment.
- Being vague about the types of equipment you have experience with.
Example answer
“In my previous role at a tobacco processing plant, I was responsible for managing the drying process for Virginia tobacco. I operated several types of drying equipment, including continuous flow driers. I implemented a maintenance schedule that reduced downtime by 20% and ensured compliance with safety regulations. Additionally, I worked closely with the quality control team to adjust drying parameters based on moisture content, which improved the final product's quality significantly.”
Skills tested
Question type
3.2. Describe a time when you had to train new staff on the drying processes and equipment.
Introduction
This question evaluates your leadership and communication skills, particularly in training and mentoring new team members, which is essential for a lead operator.
How to answer
- Use the STAR method to structure your response.
- Clearly explain the training objectives and the new staff's initial skill levels.
- Describe your training approach and any materials or resources used.
- Share specific outcomes from the training, such as improved performance or safety compliance.
- Reflect on what you learned from the experience and how you adapted your training methods.
What not to say
- Indicating that training is not part of your responsibilities.
- Providing vague descriptions of the training process without specific examples.
- Focusing solely on the technical aspects without mentioning engagement or support.
- Neglecting to highlight any positive results from the training.
Example answer
“When I joined my previous company, I was tasked with training two new operators on our tobacco drying equipment. I developed a hands-on training program that included shadowing experienced staff, interactive sessions, and safety drills. By the end of the training, both operators were able to run the equipment independently, and we saw a 15% increase in productivity within their first month. This experience taught me the importance of patience and adaptability in training methods.”
Skills tested
Question type
Similar Interview Questions and Sample Answers
Simple pricing, powerful features
Upgrade to Himalayas Plus and turbocharge your job search.
Himalayas
Himalayas Plus
Himalayas Max
Find your dream job
Sign up now and join over 100,000 remote workers who receive personalized job alerts, curated job matches, and more for free!
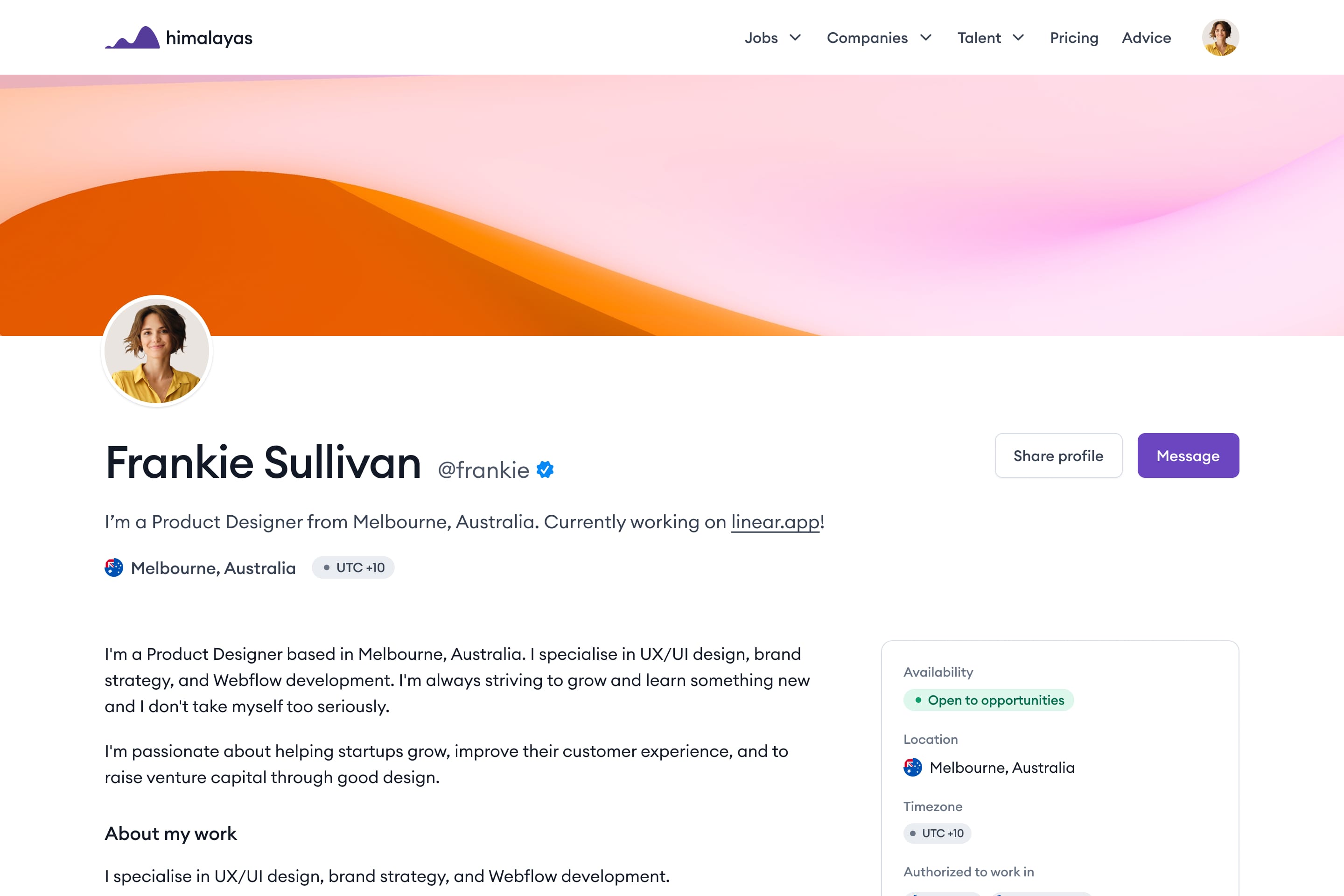