5 Switchbox Assembler Interview Questions and Answers
Switchbox Assemblers are responsible for assembling, wiring, and testing electrical switchboxes used in various industrial and commercial applications. They follow technical diagrams and specifications to ensure accurate and safe assembly. Junior assemblers focus on basic tasks and learning processes, while senior and lead roles involve overseeing complex assemblies, ensuring quality control, and mentoring team members. Need to practice for an interview? Try our AI interview practice for free then unlock unlimited access for just $9/month.
Unlimited interview practice for $9 / month
Improve your confidence with an AI mock interviewer.
No credit card required
1. Junior Switchbox Assembler Interview Questions and Answers
1.1. Can you describe your experience with assembling electronic components and what tools you are familiar with?
Introduction
This question is crucial for a Junior Switchbox Assembler role as it assesses your hands-on experience, familiarity with tools, and understanding of assembly processes, which are essential for ensuring quality and efficiency.
How to answer
- List specific electronic components you have worked with in previous roles or projects.
- Mention the tools and equipment you are proficient in, such as soldering irons, wire strippers, and multimeters.
- Provide examples of past assembly tasks and how you ensured precision and quality.
- Discuss any training or certifications related to electronics assembly.
- Highlight your ability to follow technical drawings and specifications accurately.
What not to say
- Claiming to have no experience with electronic assembly.
- Being vague about the tools you have used.
- Failing to mention any quality control measures you take.
- Overlooking the importance of safety protocols in assembly work.
Example answer
“In my previous role at a local electronics manufacturer, I assembled various electronic components including circuit boards and connectors. I am proficient with tools such as soldering irons, wire strippers, and multimeters. I always ensure that I follow technical drawings meticulously, which helped me achieve a 99% quality rate in assembled products. Additionally, I completed a certification course in electronics assembly that reinforced my knowledge of best practices and safety protocols.”
Skills tested
Question type
1.2. Describe a situation where you encountered a problem during assembly. How did you resolve it?
Introduction
This question evaluates your problem-solving skills and your ability to work under pressure, both of which are critical in a hands-on assembly role.
How to answer
- Use the STAR method (Situation, Task, Action, Result) to structure your response.
- Clearly explain the problem you faced during the assembly process.
- Detail the steps you took to investigate and resolve the issue.
- Share the outcome of your actions and any lessons learned.
- Mention any collaboration with team members if applicable.
What not to say
- Blaming others for the problem without taking responsibility.
- Focusing solely on the negative aspects without highlighting a solution.
- Failing to provide a specific example.
- Describing a situation where no action was taken to resolve the issue.
Example answer
“During my internship at a manufacturing facility, I encountered a situation where a batch of assembled switchboxes was not functioning due to a soldering error. I quickly assessed the situation and identified the faulty connections. I collaborated with a senior technician to rework the affected units and implemented a checklist for future assemblies to prevent similar issues. This experience taught me the importance of thorough inspections during the assembly process, and we achieved a 20% decrease in rework rates afterward.”
Skills tested
Question type
2. Switchbox Assembler Interview Questions and Answers
2.1. Can you describe your experience with assembling electronic components, specifically in a production environment?
Introduction
This question is important as it evaluates your hands-on experience and familiarity with assembly processes, which are critical for a Switchbox Assembler role.
How to answer
- Begin with your previous roles that involved electronic assembly, mentioning specific products or components.
- Detail the specific tools and equipment you used, such as soldering irons, multimeters, or assembly jigs.
- Explain your understanding of assembly instructions and quality control processes.
- Highlight any relevant safety protocols you followed.
- Mention any certifications or training you have received related to electronic assembly.
What not to say
- Avoid vague descriptions without mentioning specific tools or processes.
- Don’t focus on unrelated experiences outside of assembly or electronics.
- Refrain from discussing negative experiences without explaining how you overcame challenges.
- Avoid claiming experience with components you are not familiar with.
Example answer
“In my previous role at a local electronics manufacturer, I assembled various electronic devices, including circuit boards and switchboxes. I regularly used soldering irons and multimeters to ensure precision in my work. I adhered to strict assembly instructions and quality control measures, which resulted in a 98% first-pass yield. Additionally, I completed a certification in electronic assembly, reinforcing my commitment to safety and quality.”
Skills tested
Question type
2.2. Describe a time when you encountered a problem during assembly and how you resolved it.
Introduction
This behavioral question assesses your problem-solving skills and your ability to handle challenges in a production environment.
How to answer
- Use the STAR method to structure your answer (Situation, Task, Action, Result).
- Clearly describe the specific problem you faced during assembly.
- Explain the steps you took to investigate and resolve the issue.
- Highlight any collaboration with team members or supervisors.
- Share the positive outcome, including any impact on production efficiency or quality.
What not to say
- Avoid blaming others for the problem or not taking responsibility.
- Don’t provide vague answers without specific details.
- Refrain from discussing problems that you did not resolve.
- Avoid focusing solely on the negative aspects without a resolution.
Example answer
“During my time at XYZ Electronics, I noticed that several assembled switchboxes were failing quality checks due to inconsistent soldering. I investigated and found that the soldering iron temperature was set incorrectly. I raised the issue with my supervisor and proposed a team training session on proper soldering techniques. After implementing the training, we reduced defects by 40%, significantly improving our production quality.”
Skills tested
Question type
3. Senior Switchbox Assembler Interview Questions and Answers
3.1. Can you describe your experience with electronic assembly and the specific tools you have used?
Introduction
Understanding the tools and techniques you've used in electronic assembly is crucial for a Senior Switchbox Assembler role, as it showcases your technical expertise and familiarity with industry standards.
How to answer
- Detail the specific types of electronic components you've worked with, such as switches, circuit boards, or connectors.
- Mention the tools and equipment you are proficient in, such as soldering irons, multimeters, and assembly jigs.
- Explain any safety standards or quality control measures you have adhered to during assembly processes.
- Share any relevant certifications or training that enhance your technical capabilities.
- Provide examples of complex assembly tasks you have completed successfully.
What not to say
- Claiming to have experience with tools you are not familiar with.
- Being vague about your past roles and responsibilities.
- Ignoring safety protocols or quality control in your response.
- Overlooking the importance of teamwork in assembly processes.
Example answer
“In my previous role at Schneider Electric, I worked extensively with both analog and digital components, using tools such as soldering irons and oscilloscopes. I completed assembly tasks for switchboxes while adhering to IPC-A-610 standards, ensuring both quality and safety. Additionally, I received training in ESD safety, which I applied daily to protect sensitive components. This experience has equipped me with a strong foundation in electronic assembly techniques.”
Skills tested
Question type
3.2. Describe a challenging assembly problem you faced and how you resolved it.
Introduction
This question assesses your problem-solving abilities and how you approach challenges in the assembly process, which are critical for a senior role.
How to answer
- Use the STAR method (Situation, Task, Action, Result) to structure your response.
- Clearly identify the challenge you encountered and its impact on the assembly line.
- Explain the steps you took to troubleshoot and resolve the issue.
- Highlight the outcome and any improvements made to prevent similar issues in the future.
- Discuss how you communicated with your team during the process.
What not to say
- Focusing solely on the problem without discussing the solution.
- Blaming others for the challenge without taking responsibility.
- Using jargon that may not be understood by all interviewers.
- Failing to mention any proactive measures taken afterward.
Example answer
“At my previous job, we encountered a recurring issue with a specific switchbox design that caused intermittent failures. I conducted a thorough analysis and discovered that a certain soldering technique was leading to weak connections. I introduced a new soldering method and trained the team on it. This not only resolved the issue but also improved the overall quality of our assemblies, reducing failure rates by 30%. Communication with my team was key throughout this process, ensuring everyone was onboard with the changes.”
Skills tested
Question type
4. Lead Switchbox Assembler Interview Questions and Answers
4.1. Can you describe a time when you identified a quality issue in the assembly process and how you addressed it?
Introduction
This question evaluates your attention to detail and problem-solving skills, which are critical in ensuring product quality in assembly roles.
How to answer
- Use the STAR method to structure your response: Situation, Task, Action, Result.
- Clearly describe the quality issue you encountered and its potential impact on the product.
- Explain the steps you took to investigate and identify the root cause of the issue.
- Detail the corrective actions you implemented and how you communicated these to your team.
- Share the outcome, including any measurable improvements in quality or efficiency.
What not to say
- Downplaying the importance of quality control in the assembly process.
- Failing to take responsibility for addressing the issue.
- Providing vague answers without specific examples.
- Not mentioning any collaboration with team members or supervisors.
Example answer
“While working at Siemens, I noticed a recurring issue with incorrect wiring in our switchboxes. I took the initiative to conduct a thorough review of the assembly process and found that the issue stemmed from unclear labeling on the wiring diagrams. I organized a meeting with the team to discuss this and proposed a revised labeling system. After implementing this change, we reduced wiring errors by 40% in the following month, significantly improving our quality metrics.”
Skills tested
Question type
4.2. How do you prioritize your tasks when working on multiple assembly projects with tight deadlines?
Introduction
This question assesses your time management and organizational skills, which are essential for a lead assembler managing multiple projects.
How to answer
- Describe your approach to task prioritization, including any specific methods you use (e.g., to-do lists, project management tools).
- Explain how you assess the urgency and importance of different tasks.
- Share an example of a time you effectively managed competing deadlines.
- Discuss how you communicate with your team to ensure everyone is aligned on priorities.
- Mention any tools or techniques you use to track progress and maintain quality.
What not to say
- Claiming that you do not have a structured method for prioritizing tasks.
- Focusing solely on personal work without considering team dynamics.
- Overlooking the importance of deadlines and quality in your response.
- Failing to provide a specific example to illustrate your approach.
Example answer
“At my previous role with ABB, I was often required to manage several switchbox assembly projects simultaneously. I prioritized my tasks using a project management tool that flagged deadlines and dependencies. I assessed each task's urgency and communicated with my team daily to ensure alignment. For example, during a peak production period, I successfully delivered two major projects on time by reallocating resources and focusing on the highest-impact tasks. This proactive approach helped us meet our deadlines without compromising quality.”
Skills tested
Question type
5. Assembly Supervisor Interview Questions and Answers
5.1. Can you describe a time when you had to manage a conflict within your assembly team?
Introduction
This question is crucial for understanding your conflict resolution skills and ability to maintain team cohesion, which are essential for an Assembly Supervisor role.
How to answer
- Use the STAR method to structure your response: Situation, Task, Action, Result.
- Clearly describe the conflict, including the individuals involved and the context.
- Explain your approach to addressing the conflict, including communication strategies and mediation techniques.
- Detail the outcome and any positive changes that resulted from your intervention.
- Share lessons learned and how you applied them in future situations.
What not to say
- Blaming team members without taking responsibility for the management approach.
- Not providing a clear resolution or outcome from the conflict.
- Suggesting you avoid conflict rather than addressing it head-on.
- Focusing too much on the negative aspects of the conflict without highlighting solutions.
Example answer
“In my previous role at BMW, there was a situation where two assembly line workers had a disagreement over task responsibilities that was affecting productivity. I arranged a meeting to facilitate open communication, allowing each person to express their concerns. By fostering collaboration, we agreed on a shared approach to responsibilities. This not only resolved the conflict but also improved team dynamics and productivity by 15% in the following weeks.”
Skills tested
Question type
5.2. How do you ensure quality control in the assembly process?
Introduction
Quality control is vital in assembly roles to ensure products meet standards, and this question evaluates your knowledge and approach to maintaining high-quality output.
How to answer
- Outline specific quality control methodologies you have used, such as Six Sigma or Lean Manufacturing.
- Explain how you train and motivate your team to adhere to quality standards.
- Describe how you monitor the assembly process and the metrics you use to measure quality.
- Discuss your approach to addressing quality issues when they arise.
- Provide examples of how your efforts have led to improved quality outcomes.
What not to say
- Suggesting that quality control is solely the responsibility of the quality assurance team.
- Failing to mention specific quality control tools or processes.
- Ignoring the importance of team training and engagement in quality control.
- Being vague about how you handle quality issues.
Example answer
“At Volkswagen, I implemented a Lean Manufacturing approach that included regular training for my team on quality standards and best practices. We used real-time monitoring tools to track defect rates, and I established a feedback loop for immediate reporting of quality issues. This led to a 20% reduction in defects over six months, as the team became more proactive in identifying and resolving potential quality concerns.”
Skills tested
Question type
Similar Interview Questions and Sample Answers
Simple pricing, powerful features
Upgrade to Himalayas Plus and turbocharge your job search.
Himalayas
Himalayas Plus
Himalayas Max
Find your dream job
Sign up now and join over 100,000 remote workers who receive personalized job alerts, curated job matches, and more for free!
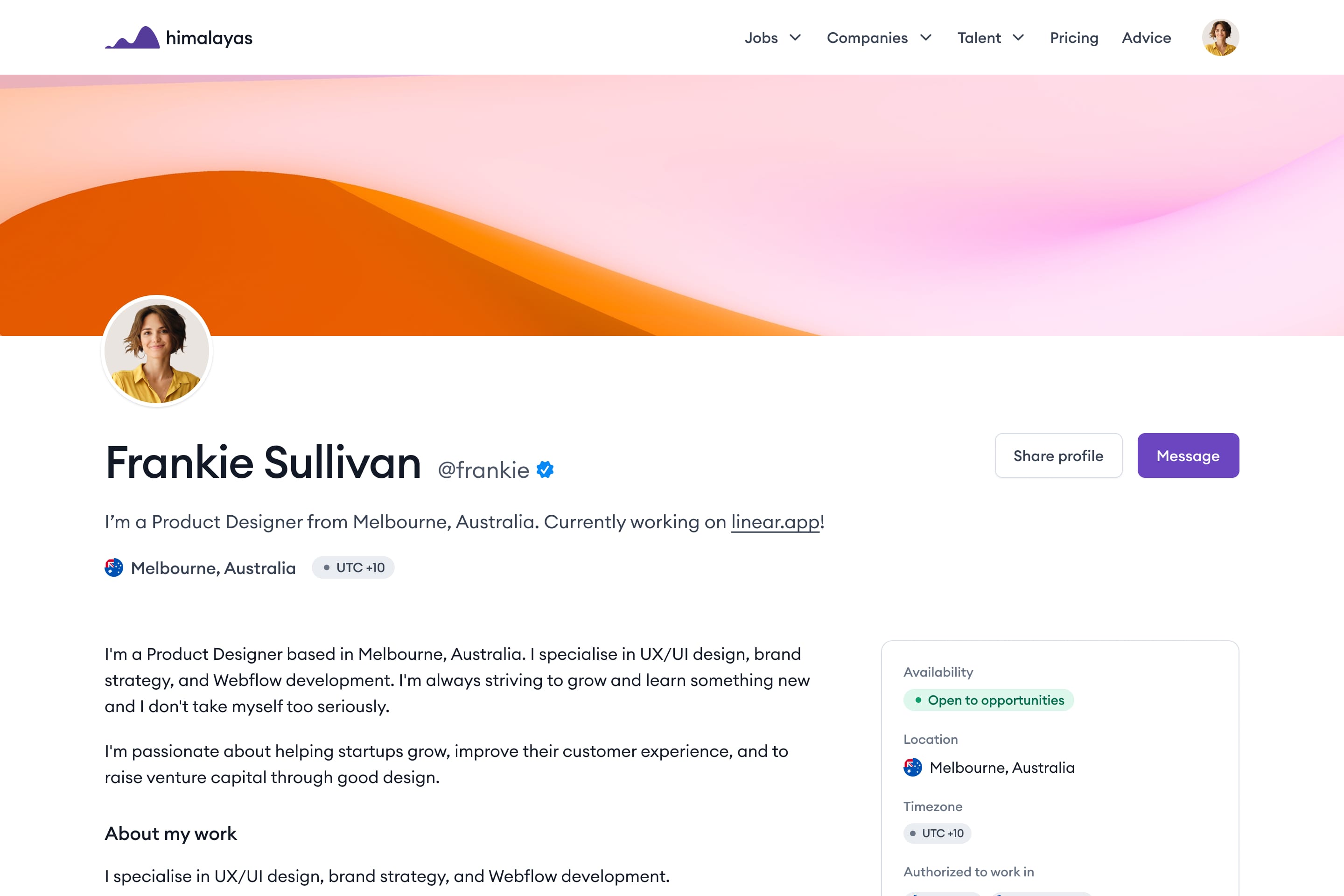