5 Subway Car Repairer Interview Questions and Answers
Subway Car Repairers are responsible for maintaining, diagnosing, and repairing subway cars to ensure their safe and efficient operation. They inspect mechanical, electrical, and hydraulic systems, troubleshoot issues, and perform necessary repairs or replacements. Junior roles focus on learning and assisting with basic tasks, while senior and lead positions involve overseeing repairs, mentoring junior staff, and ensuring compliance with safety standards and operational guidelines. Need to practice for an interview? Try our AI interview practice for free then unlock unlimited access for just $9/month.
Unlimited interview practice for $9 / month
Improve your confidence with an AI mock interviewer.
No credit card required
1. Apprentice Subway Car Repairer Interview Questions and Answers
1.1. Can you describe a time when you successfully diagnosed and repaired a mechanical issue?
Introduction
This question evaluates your problem-solving skills and technical knowledge, which are essential for an Apprentice Subway Car Repairer.
How to answer
- Use the STAR method to structure your response: Situation, Task, Action, Result.
- Clearly describe the mechanical issue you encountered.
- Explain how you diagnosed the problem, including any tools or methods you used.
- Detail the steps you took to repair the issue and any challenges faced.
- Quantify the results of your repair, such as improved performance or safety outcomes.
What not to say
- Providing vague descriptions without specific details.
- Failing to mention the methods or tools used for diagnosis.
- Taking sole credit without acknowledging any team support.
- Neglecting to discuss the impact of your repair work.
Example answer
“During my training at a local workshop, I encountered a subway car with a malfunctioning braking system. After checking the brake pads and fluid levels, I used diagnostic tools to identify a faulty sensor. I replaced it, tested the system, and confirmed it operated within safety standards. This experience taught me the importance of thorough diagnostics and teamwork, as my mentor provided vital guidance.”
Skills tested
Question type
1.2. How would you handle a situation where you are unsure about a repair procedure?
Introduction
This question assesses your willingness to seek help and your approach to learning in a practical environment.
How to answer
- Explain your thought process when facing uncertainty.
- Emphasize the importance of safety and accuracy in repair work.
- Discuss your willingness to consult manuals, experienced colleagues, or supervisors.
- Describe how you would document the situation for future reference.
- Highlight your commitment to continuous learning and improvement.
What not to say
- Suggesting you would attempt the repair without adequate knowledge.
- Failing to acknowledge the importance of safety.
- Ignoring the value of asking for help or clarification.
- Being dismissive about learning from mistakes.
Example answer
“If I encounter uncertainty about a repair procedure, I would first consult the service manual for guidance. If I still have questions, I would ask an experienced colleague or supervisor for assistance. Safety is my top priority, so I would never proceed without being sure of the correct method. I believe in learning from every experience, so I would document what I learned for future reference.”
Skills tested
Question type
2. Subway Car Repairer Interview Questions and Answers
2.1. Can you describe a specific time when you diagnosed and repaired a complex issue in a subway car?
Introduction
This question assesses your technical expertise and problem-solving skills, which are critical for a Subway Car Repairer as they directly impact safety and service reliability.
How to answer
- Use the STAR method to structure your answer: Situation, Task, Action, Result
- Clearly describe the issue you encountered and its implications for the service
- Detail the diagnostic steps you took to identify the root cause
- Explain the repair process you followed, including any tools or techniques used
- Quantify the results, such as time saved, cost efficiency, or improved performance
What not to say
- Failing to provide a concrete example or using a vague response
- Overly technical jargon that doesn't clarify your actions
- Not addressing the impact of your repair on the overall operation
- Neglecting to mention teamwork if applicable, as collaboration is often key
Example answer
“While working at ATAC in Rome, I encountered a subway car that frequently stalled. After conducting a series of diagnostic tests, I identified a failing traction motor. I replaced the motor, recalibrated the system, and performed thorough testing. This not only resolved the stalling issue but also improved the car's acceleration by 20%, significantly enhancing passenger experience.”
Skills tested
Question type
2.2. How do you ensure safety and compliance while performing repairs on subway cars?
Introduction
This question is crucial as safety is the top priority in any maintenance role, especially in public transport. It evaluates your understanding of safety protocols and regulatory compliance.
How to answer
- Discuss your familiarity with safety regulations and standards in the industry
- Explain the specific safety procedures you follow during repairs
- Detail how you stay updated on compliance requirements
- Mention any training or certifications relevant to safety in the workplace
- Describe a situation where you had to prioritize safety and the outcome of that decision
What not to say
- Implying that safety checks are optional or can be overlooked
- Providing a generic answer without specific procedures or examples
- Neglecting to mention teamwork in ensuring safety
- Failing to recognize the importance of compliance in your role
Example answer
“In my role at Trenitalia, I follow strict safety protocols outlined in our company guidelines. Before starting any repair, I conduct a risk assessment and ensure all personal protective equipment (PPE) is in place. I also participate in monthly safety training sessions to stay current on regulations. For instance, during a maintenance overhaul, I identified a potential safety hazard and halted work until it was addressed, preventing any risk to my colleagues and the public.”
Skills tested
Question type
3. Senior Subway Car Repairer Interview Questions and Answers
3.1. Can you describe a complex repair you handled on a subway car and how you approached the problem?
Introduction
This question assesses your technical expertise, problem-solving skills, and ability to work under pressure, which are crucial for a Senior Subway Car Repairer.
How to answer
- Begin with a brief description of the issue you encountered with the subway car.
- Explain the steps you took to diagnose the problem, including any tools or techniques used.
- Detail the repair process, including any collaboration with team members or other departments.
- Discuss the outcome and any impact on operations, such as reducing downtime.
- Highlight any lessons learned from the experience that you can apply to future repairs.
What not to say
- Oversimplifying the repair process without mentioning specific challenges.
- Failing to illustrate collaboration or communication with other team members.
- Neglecting to mention safety protocols or regulations adhered to during repairs.
- Not providing a clear outcome or metrics related to the repair work.
Example answer
“At the Mexico City Metro, I encountered a recurring issue with the braking system on one of the older subway cars. I used diagnostic tools to pinpoint the root cause, which was a malfunction in the hydraulic system. Collaborating with the electrical team, we replaced critical components and tested the system thoroughly. This repair reduced the car's downtime by 30%, ensuring it was back in service quickly. This experience taught me the importance of cross-department collaboration and thorough testing.”
Skills tested
Question type
3.2. How do you ensure safety and compliance with regulations while repairing subway cars?
Introduction
This question evaluates your knowledge of safety regulations and how you prioritize safety in your repair work, which is essential in this role.
How to answer
- Discuss your understanding of relevant safety regulations and standards.
- Explain how you incorporate safety checks into your daily repair routines.
- Describe any training or certifications you have related to safety procedures.
- Provide examples of how you have handled safety concerns in past repairs.
- Emphasize the importance of maintaining a safety-first culture among your team.
What not to say
- Underestimating the importance of safety regulations in repair work.
- Failing to mention specific safety protocols or training you've received.
- Ignoring the impact of safety culture on team performance.
- Only discussing safety in hypothetical terms without real examples.
Example answer
“I am well-versed in the safety regulations mandated by the Mexican government for public transport. Before any repair, I conduct a thorough risk assessment and ensure all team members are briefed on safety protocols. For instance, during a major overhaul of a subway car, I initiated a safety audit, which led to identifying and mitigating potential hazards. Creating a safety-first culture is vital, and I encourage open dialogue about safety concerns within my team.”
Skills tested
Question type
4. Lead Subway Car Repairer Interview Questions and Answers
4.1. Can you describe a challenging repair issue you encountered and how you resolved it?
Introduction
This question is important for assessing your technical expertise and problem-solving skills in the context of subway car repair, where issues can be complex and time-sensitive.
How to answer
- Use the STAR method to structure your response (Situation, Task, Action, Result)
- Clearly explain the nature of the repair issue and its potential impact on safety or service
- Detail the steps you took to diagnose the problem
- Describe the specific actions you implemented to resolve it
- Quantify the results, such as time saved or improvements in performance
What not to say
- Describing a situation without a clear resolution
- Focusing too much on technical jargon without explaining it simply
- Taking sole credit without acknowledging teamwork
- Failing to highlight the importance of safety and compliance
Example answer
“At my previous job with the MTA, we faced an issue with a subway car that had persistent brake failures. I led a team to conduct a thorough inspection, identifying a faulty valve. After replacing it, we tested the system and ensured it met safety standards. This proactive approach not only resolved the immediate issue but also enhanced our preventative maintenance schedule, reducing similar issues by 30% over the next year.”
Skills tested
Question type
4.2. How do you ensure safety protocols are followed during repairs?
Introduction
This question assesses your commitment to safety and your ability to enforce protocols, which is crucial in a role that involves heavy machinery and public transportation.
How to answer
- Discuss specific safety protocols you follow and how you communicate them to your team
- Explain the training processes you implement for new team members
- Share examples of how you handle safety violations or near misses
- Describe how you maintain a culture of safety within the team
- Highlight any previous experiences that contributed to improved safety outcomes
What not to say
- Ignoring the importance of safety in the workplace
- Providing vague answers without specific examples
- Neglecting to mention teamwork and communication
- Indicating a lack of experience in implementing safety protocols
Example answer
“In my current role, I ensure that all team members undergo rigorous safety training before starting any repair work. I hold weekly safety meetings to review protocols and encourage open discussions about potential hazards. Last year, after a near miss incident, I initiated a safety audit that led to a 50% reduction in safety violations on our team. Creating a proactive safety culture is my top priority.”
Skills tested
Question type
5. Supervisor of Subway Car Repairs Interview Questions and Answers
5.1. Can you describe a time when you had to manage a significant repair project under a tight deadline?
Introduction
This question assesses your project management skills and ability to work under pressure, which are critical in a supervisory role overseeing subway car repairs.
How to answer
- Use the STAR method to structure your response
- Clearly outline the project scope and the specific deadline
- Detail the steps you took to plan and execute the repairs
- Discuss how you coordinated with your team and handled any challenges
- Quantify the results and the impact on service continuity
What not to say
- Focusing too much on the technical aspects without discussing leadership
- Being vague about the challenges faced and how you resolved them
- Neglecting to mention team coordination and communication
- Failing to provide measurable outcomes from the project
Example answer
“At the Mexico City Metro, I led a team tasked with repairing a fleet of subway cars after a major incident. We had just two weeks to complete the repairs. I organized a detailed action plan, allocating tasks based on team strengths. Despite facing unexpected delays due to parts shortages, I arranged for expedited shipping and regular check-ins with the team. We completed the repairs on time, which minimized service disruption and maintained passenger trust.”
Skills tested
Question type
5.2. How do you ensure safety and quality standards are met during subway car repairs?
Introduction
This question evaluates your understanding of safety protocols and quality assurance processes, which are vital in the transportation industry.
How to answer
- Describe specific safety protocols you implement in your team
- Discuss how you train staff on safety and quality standards
- Detail your approach to monitoring compliance during repairs
- Share examples of how you handle safety incidents or quality issues
- Highlight the importance of a safety-first culture in your team
What not to say
- Underestimating the importance of safety and quality standards
- Providing generic responses without specific protocols
- Failing to mention ongoing training or staff engagement
- Ignoring past incidents or lessons learned in safety management
Example answer
“I prioritize safety and quality by implementing rigorous training programs for my team on standards outlined by the National Safety Council. I conduct weekly safety audits and encourage open communication about any risks. Last year, we encountered a quality issue with brakes that I addressed by retraining staff and revising our inspection checklist, resulting in a 30% reduction in defects. This proactive approach has fostered a culture of accountability and safety awareness.”
Skills tested
Question type
Similar Interview Questions and Sample Answers
Simple pricing, powerful features
Upgrade to Himalayas Plus and turbocharge your job search.
Himalayas
Himalayas Plus
Himalayas Max
Find your dream job
Sign up now and join over 100,000 remote workers who receive personalized job alerts, curated job matches, and more for free!
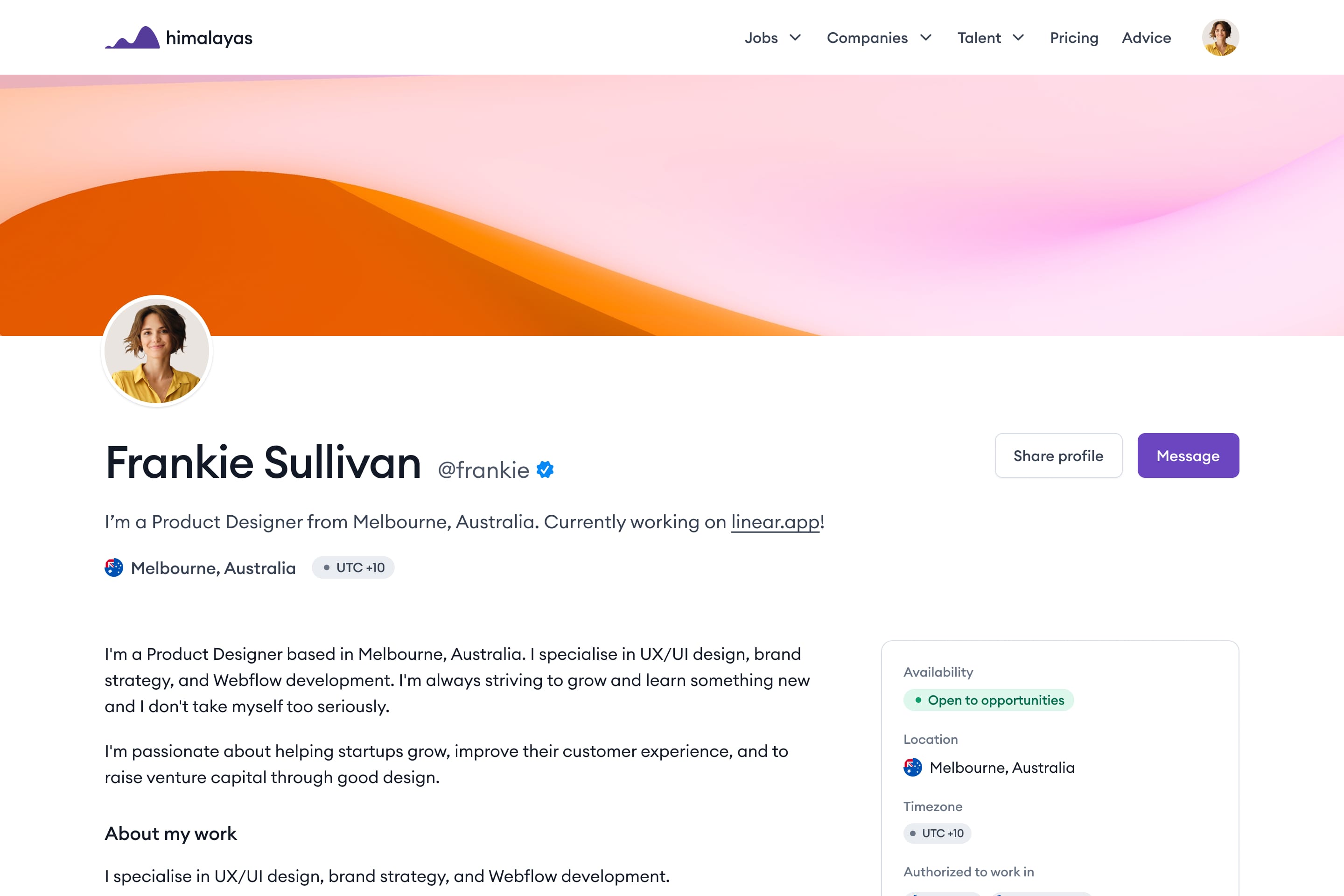