5 Steel Roller Interview Questions and Answers
Steel Rollers operate machinery to shape and form steel into desired dimensions and specifications. They monitor the rolling process, ensure quality standards are met, and maintain equipment. At junior levels, they assist in operations and learn the trade, while senior roles involve overseeing processes, troubleshooting issues, and mentoring junior workers. Need to practice for an interview? Try our AI interview practice for free then unlock unlimited access for just $9/month.
Unlimited interview practice for $9 / month
Improve your confidence with an AI mock interviewer.
No credit card required
1. Apprentice Steel Roller Interview Questions and Answers
1.1. Can you describe a time when you had to learn a new skill or technique quickly on the job?
Introduction
This question is important for assessing your adaptability and willingness to learn, which are crucial traits for an apprentice in a hands-on role like steel rolling.
How to answer
- Use the STAR method to structure your response: Situation, Task, Action, Result.
- Clearly describe the new skill or technique you had to learn.
- Explain why it was necessary to learn this skill quickly.
- Detail the steps you took to acquire the skill, including any resources you utilized.
- Share the outcome of your efforts and what you learned from the experience.
What not to say
- Avoid vague responses that lack detail about the skill or situation.
- Do not focus solely on the challenges without discussing the actions taken.
- Refrain from claiming that you never struggle with learning new skills.
- Avoid underselling the importance of teamwork or guidance from others.
Example answer
“At a previous job, I had to quickly learn the operation of a new hydraulic press due to a sudden staff shortage. I observed an experienced colleague for a couple of shifts, then practiced under supervision. Within a week, I was operating the press independently and increased production efficiency by 15%. This experience taught me the importance of hands-on learning and asking questions.”
Skills tested
Question type
1.2. What safety protocols do you think are essential when working in a steel rolling environment?
Introduction
Safety is paramount in manufacturing environments. This question tests your awareness of safety practices and your commitment to maintaining a safe workplace.
How to answer
- List key safety protocols relevant to steel rolling processes.
- Explain why each protocol is important for worker safety.
- Share any personal experiences where safety protocols helped prevent accidents.
- Demonstrate your understanding of the consequences of neglecting safety measures.
- Discuss how you would contribute to fostering a safety-first culture in the workplace.
What not to say
- Avoid generic answers that do not reflect specific protocols.
- Do not downplay the importance of safety or suggest shortcuts.
- Refrain from ignoring the role of teamwork in maintaining safety.
- Avoid only mentioning personal safety without regard to others.
Example answer
“Essential safety protocols in steel rolling include wearing PPE like helmets and gloves, following lockout/tagout procedures, and maintaining clear communication during operations. In my previous role, we had a near-miss incident that highlighted the importance of these protocols, leading to enhanced training sessions. I believe fostering a safety-first culture is crucial for everyone's well-being.”
Skills tested
Question type
1.3. How do you handle constructive criticism from supervisors or colleagues?
Introduction
This question is designed to evaluate your openness to feedback, which is essential for growth and development as an apprentice.
How to answer
- Acknowledge the importance of constructive criticism for personal and professional growth.
- Share a specific instance where you received feedback and how you responded.
- Explain how you applied the feedback to improve your skills or performance.
- Discuss your attitude towards ongoing learning and development.
- Highlight your willingness to seek feedback proactively.
What not to say
- Avoid defensive responses or blaming others for feedback.
- Do not suggest you avoid criticism or find it unhelpful.
- Refrain from generalizing negative experiences without learning outcomes.
- Avoid implying that you know everything already or don’t need feedback.
Example answer
“I view constructive criticism as an opportunity for growth. Once, my supervisor pointed out that my technique for operating the rolling machine was inefficient. I took this feedback seriously, sought additional training, and practiced regularly. As a result, my efficiency improved significantly, and I even assisted others in learning the correct technique. This experience reinforced my belief in the value of mentorship and feedback.”
Skills tested
Question type
2. Steel Roller Interview Questions and Answers
2.1. Can you describe a challenging project you worked on as a steel roller, and how you overcame any obstacles?
Introduction
This question assesses your problem-solving skills and ability to handle challenges in a technical role. As a steel roller, you need to navigate various obstacles that can arise during production.
How to answer
- Use the STAR method (Situation, Task, Action, Result) to structure your response
- Clearly outline the specifics of the project and the challenges faced
- Explain the steps you took to overcome these obstacles, emphasizing technical skills and collaboration
- Highlight the outcome of your efforts and any improvements made to processes
- Reflect on what you learned from the experience and how it can be applied to future projects
What not to say
- Avoid vague descriptions of the project without specific challenges
- Refrain from focusing solely on technical aspects without mentioning teamwork
- Do not downplay the difficulties faced or provide overly simplistic solutions
- Avoid taking all the credit; acknowledge contributions from others
Example answer
“In my role at ArcelorMittal, I worked on a project to streamline the steel rolling process. We encountered a significant issue with temperature control, which was causing defects in the final product. I collaborated with the engineering team to analyze the data and adjust our heating methods. As a result, we improved product quality by 20% and reduced waste by 15%. This experience taught me the importance of cross-team communication in resolving technical issues.”
Skills tested
Question type
2.2. How do you ensure safety and quality standards are met during the steel rolling process?
Introduction
Safety and quality are critical in the steel industry. This question evaluates your understanding of industry standards and your commitment to maintaining them in your work.
How to answer
- Discuss your knowledge of relevant safety regulations and quality control measures
- Explain the specific practices you implement to uphold these standards in your daily tasks
- Provide examples of how you have contributed to safety improvements or quality audits
- Mention any training or certifications you have received related to safety and quality
- Emphasize the importance of culture in ensuring safety and quality within the team
What not to say
- Avoid claiming that safety is not a priority in your work
- Refrain from mentioning practices that could compromise safety or quality
- Do not suggest that you work independently without collaboration on safety measures
- Avoid vague responses about quality without specific examples
Example answer
“At Vallourec, I strictly adhere to ISO safety standards and regularly participate in safety training sessions. I conduct daily inspections of machinery and ensure that all team members wear appropriate protective gear. Additionally, I implemented a quality control checklist that has helped us reduce defects by 25%. I believe that fostering a culture of safety and quality among team members is essential for our success.”
Skills tested
Question type
3. Senior Steel Roller Interview Questions and Answers
3.1. Can you describe a challenging project where you had to ensure the quality and efficiency of steel rolling operations?
Introduction
This question assesses your technical expertise and problem-solving abilities in managing complex steel rolling processes, which are critical for a Senior Steel Roller.
How to answer
- Use the STAR method to structure your response: Situation, Task, Action, Result.
- Clearly outline the specifics of the project, including any challenges faced related to equipment, materials, or team dynamics.
- Detail the steps you took to address the challenges, focusing on your technical skills and decision-making processes.
- Quantify the results achieved, such as improvements in quality, efficiency, or cost savings.
- Discuss any lessons learned and how they can be applied to future projects.
What not to say
- Avoid being vague about your role and contributions.
- Don't focus only on the problems without explaining how you solved them.
- Refrain from using jargon without explaining it to ensure clarity.
- Neglecting to mention team collaboration or support can undermine your leadership skills.
Example answer
“At ArcelorMittal, I led a project to improve the rolling efficiency of our steel beams. We faced issues with inconsistent thickness causing production delays. I implemented a new monitoring system for the rollers that collected real-time data on thickness variations. This allowed us to adjust parameters on the fly. As a result, we improved our production efficiency by 20% and reduced waste by 15%. This experience taught me the importance of data-driven decision-making in steel rolling operations.”
Skills tested
Question type
3.2. How do you ensure safety and compliance in steel rolling operations?
Introduction
This question evaluates your understanding of safety protocols and compliance standards, which are crucial in the steel industry to prevent accidents and ensure operational integrity.
How to answer
- Explain your approach to fostering a safety-first culture within the team.
- Detail specific safety protocols you follow and how you ensure compliance with industry regulations.
- Provide examples of training or initiatives you have led to promote safety.
- Discuss how you handle incidents or near misses and the importance of reporting.
- Mention how you keep up with changes in safety regulations and standards.
What not to say
- Avoid suggesting that safety is someone else's responsibility.
- Don't downplay the importance of compliance or safety training.
- Refrain from giving examples where safety protocols were ignored.
- Neglecting to discuss proactive measures can indicate a lack of commitment to safety.
Example answer
“In my previous role at Sappi, I prioritized safety by implementing a comprehensive training program for all new operators, emphasizing hands-on learning about equipment and safety protocols. I also established regular safety audits and encouraged open discussions about safety concerns. When an incident occurred involving equipment malfunction, I led a root cause analysis and revised our procedures, which led to a 30% reduction in incidents over the following year. This experience reinforced my belief that safety is a continuous commitment.”
Skills tested
Question type
4. Lead Steel Roller Interview Questions and Answers
4.1. Can you describe your experience with rolling steel and the specific techniques you employ to ensure quality and efficiency?
Introduction
This question is crucial as it assesses your technical expertise in steel rolling processes and your ability to produce high-quality outputs while optimizing efficiency.
How to answer
- Start by outlining your relevant experience in steel rolling, including years of experience and types of steel you've worked with.
- Discuss specific techniques or machinery you are proficient in and how they contribute to quality and efficiency.
- Mention any quality control measures you implement to ensure the final product meets specifications.
- Highlight any improvements or innovations you introduced in past roles that enhanced productivity.
- Provide examples of challenges faced in rolling processes and how you overcame them.
What not to say
- Vague descriptions of experience without specific techniques or machinery mentioned.
- Failing to mention quality control measures or how you ensure product integrity.
- Avoiding discussion of challenges or presenting a one-sided view of your experience.
- Overlooking the importance of teamwork and collaboration in the rolling process.
Example answer
“In my previous role at Ternium, I worked as a lead steel roller for 8 years, primarily using a hot rolling mill. I employed techniques such as controlled cooling and precise temperature management to ensure the steel met our stringent quality standards. I implemented a new quality control protocol that reduced defects by 15% and increased overall efficiency by optimizing the rolling speed. Challenges like inconsistent steel quality were addressed by collaborating closely with the metallurgical team to adjust our rolling parameters based on real-time feedback.”
Skills tested
Question type
4.2. Describe a situation where you had to lead a team through a challenging production issue. What was your approach?
Introduction
This question evaluates your leadership and team management skills, particularly in high-pressure situations that are common in manufacturing environments.
How to answer
- Use the STAR method to structure your response: Situation, Task, Action, Result.
- Clearly describe the production issue and its impact on operations.
- Detail your role as a leader and how you communicated with your team during the crisis.
- Explain the actions you took to resolve the issue and any collaboration with other departments.
- Highlight the outcome and any lessons learned that improved future practices.
What not to say
- Blaming team members or external factors without taking responsibility.
- Providing a response that lacks specific actions you took to resolve the issue.
- Ignoring the importance of communication and teamwork in crisis management.
- Failing to demonstrate how the experience contributed to your growth as a leader.
Example answer
“At my previous job with Grupo Villacero, we faced a significant production delay due to a mechanical failure in the rolling mill. As the lead, I organized an emergency meeting with my team to assess the issue. We developed a plan to reallocate resources and prioritized tasks to minimize downtime. By coordinating with maintenance and implementing immediate fixes, we managed to reduce the downtime by 30%. This experience underscored the importance of transparent communication and proactive leadership in overcoming production challenges.”
Skills tested
Question type
5. Steel Rolling Supervisor Interview Questions and Answers
5.1. Can you describe a time when you had to resolve a safety issue in the steel rolling process?
Introduction
Safety is paramount in steel manufacturing, and this question assesses your ability to identify, address, and communicate safety concerns effectively.
How to answer
- Use the STAR method to structure your response: Situation, Task, Action, Result.
- Clearly describe the safety issue you encountered and its potential impact.
- Explain the steps you took to resolve the issue, including any collaboration with safety teams.
- Detail the outcome of your actions, referencing any changes made to improve safety procedures.
- Mention how you communicated the issue and resolution to your team to ensure future compliance.
What not to say
- Downplaying the seriousness of the safety issue.
- Focusing solely on the technical aspects without addressing safety protocols.
- Failing to mention any follow-up measures taken to prevent recurrence.
- Avoiding responsibility or blaming others without demonstrating your role in the solution.
Example answer
“In my previous role at Gerdau, we faced a situation where a machine showed signs of wear that could lead to a safety hazard. I gathered the team to assess the risk and halted production to ensure safety. We collaborated with the maintenance department to conduct a thorough inspection and replaced the faulty parts. As a result, we not only avoided an accident but also developed a more rigorous inspection schedule that improved overall safety compliance by 30%.”
Skills tested
Question type
5.2. How do you ensure the quality of the steel produced during the rolling process?
Introduction
Quality control in steel rolling is critical for product reliability. This question evaluates your understanding of quality assurance processes and methodologies.
How to answer
- Describe the specific quality control measures you implement during the rolling process.
- Explain how you monitor the production process for deviations from quality standards.
- Discuss how you handle quality issues when they arise.
- Mention any tools or technologies you use to enhance quality assurance.
- Provide examples of how your quality initiatives have led to measurable improvements.
What not to say
- Suggesting quality is solely the responsibility of the quality control team.
- Neglecting to mention any specific quality metrics or standards.
- Providing vague answers without concrete examples.
- Ignoring the importance of team training on quality standards.
Example answer
“At Companhia Siderúrgica Nacional, I implemented a quality assurance program that included continuous monitoring of temperature and thickness during the rolling process. We utilized real-time data analytics to detect deviations immediately. When a batch failed to meet specifications, I led a root cause analysis that uncovered a calibration issue. By rectifying this and conducting training sessions, we reduced our defect rate by 15% over the following quarter.”
Skills tested
Question type
Similar Interview Questions and Sample Answers
Simple pricing, powerful features
Upgrade to Himalayas Plus and turbocharge your job search.
Himalayas
Himalayas Plus
Himalayas Max
Find your dream job
Sign up now and join over 100,000 remote workers who receive personalized job alerts, curated job matches, and more for free!
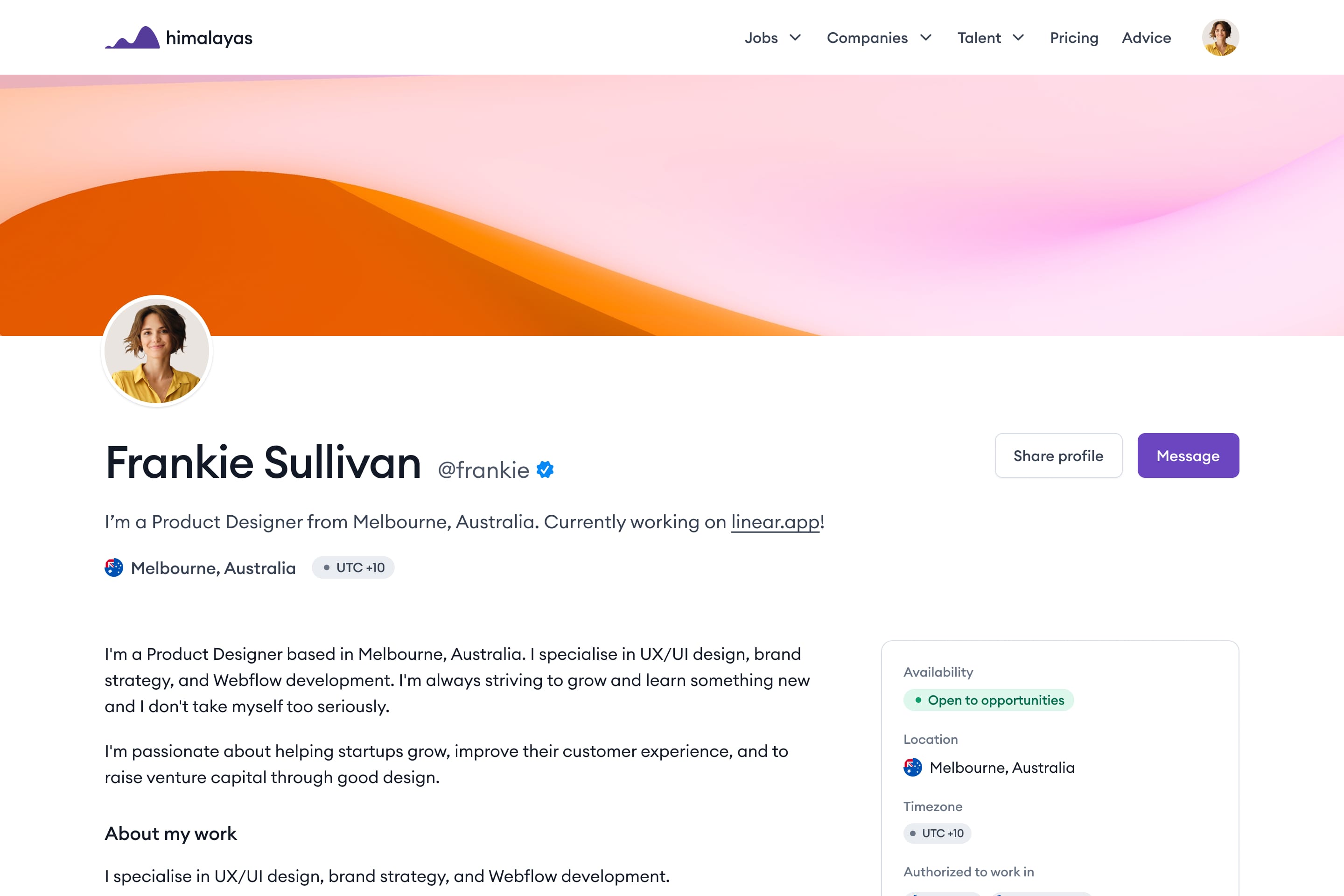