6 Shipping and Receiving Material Handler Interview Questions and Answers
Shipping and Receiving Material Handlers are responsible for managing the movement of goods within a warehouse or distribution center. They handle tasks such as loading and unloading shipments, verifying inventory, and ensuring materials are stored and distributed efficiently. Junior roles focus on basic tasks and learning processes, while senior and lead roles involve overseeing operations, mentoring team members, and ensuring compliance with safety and quality standards. Need to practice for an interview? Try our AI interview practice for free then unlock unlimited access for just $9/month.
Unlimited interview practice for $9 / month
Improve your confidence with an AI mock interviewer.
No credit card required
1. Junior Material Handler Interview Questions and Answers
1.1. Can you describe a situation where you had to manage multiple tasks in a fast-paced environment?
Introduction
This question assesses your ability to prioritize and manage time effectively, which is crucial for a Junior Material Handler who often deals with various tasks simultaneously.
How to answer
- Use the STAR method to structure your response (Situation, Task, Action, Result).
- Clearly describe the tasks you were juggling and the workplace setting.
- Explain your thought process in prioritizing tasks.
- Share specific actions you took to manage time and resources efficiently.
- Quantify the results or improvements achieved due to your actions.
What not to say
- Focusing on one task and neglecting to mention multitasking.
- Providing an answer that lacks a clear structure or outcome.
- Failing to demonstrate any specific strategies for prioritization.
- Overlooking the importance of teamwork or communication with others.
Example answer
“At my previous job at Amazon, I often had to manage receiving shipments while preparing orders for delivery. During peak hours, I used a checklist to prioritize tasks based on urgency, which helped me complete orders 20% faster without compromising accuracy. This experience taught me the importance of staying organized under pressure.”
Skills tested
Question type
1.2. What safety protocols do you think are essential when handling materials and equipment?
Introduction
This question evaluates your understanding of safety standards and practices, which is vital for ensuring a safe working environment in material handling roles.
How to answer
- List key safety protocols relevant to material handling.
- Explain why each protocol is important for workplace safety.
- Share any personal experiences or training you have received related to safety.
- Demonstrate your commitment to following safety regulations.
- Mention how you would encourage others to adhere to safety practices.
What not to say
- Ignoring the importance of safety and providing vague answers.
- Suggesting that safety protocols are unnecessary or can be overlooked.
- Failing to acknowledge specific safety training or certifications.
- Not mentioning the importance of teamwork in maintaining safety.
Example answer
“I believe essential safety protocols include wearing appropriate personal protective equipment (PPE), following equipment operation guidelines, and conducting regular safety checks. In my previous role at Walmart, I completed safety training which emphasized these protocols. I always encourage my team to report any unsafe conditions immediately to prevent accidents.”
Skills tested
Question type
2. Material Handler Interview Questions and Answers
2.1. Can you describe a time when you had to handle a difficult situation while managing materials or inventory?
Introduction
This question evaluates your problem-solving skills and ability to manage stress while working in a fast-paced environment, which is crucial for a Material Handler.
How to answer
- Use the STAR method (Situation, Task, Action, Result) to structure your response.
- Clearly describe the situation and the specific challenge you faced.
- Explain the actions you took to resolve the issue, focusing on your decision-making process.
- Highlight the results of your actions, ideally with measurable outcomes.
- Discuss any lessons learned that could apply to future situations.
What not to say
- Avoid blaming others for the situation without taking responsibility.
- Do not focus on negative outcomes without discussing how you improved the situation.
- Refrain from giving vague responses that lack detail.
- Do not ignore the importance of teamwork in resolving challenges.
Example answer
“In my previous role at a logistics company, we faced a sudden shortage of critical materials due to a supplier issue. I quickly assessed our inventory levels and identified alternative materials that could be used. I communicated with my team to implement a temporary solution while negotiating with the supplier for expedited delivery. As a result, we were able to maintain production schedules without significant delays, improving our response time by 30%. This experience taught me the importance of flexibility and proactive communication in material handling.”
Skills tested
Question type
2.2. How do you ensure safety and compliance while handling materials in a warehouse environment?
Introduction
This question assesses your understanding of safety protocols and regulations, which are essential for a Material Handler to prevent accidents and ensure compliance.
How to answer
- Discuss your knowledge of safety regulations relevant to material handling in France.
- Explain the steps you take to comply with safety standards when handling materials.
- Share examples of how you have promoted a safety culture in the workplace.
- Mention any specific training or certifications you have received related to safety.
- Describe how you stay updated on changes in safety regulations.
What not to say
- Do not downplay the importance of safety protocols.
- Avoid vague statements without specific examples or actions.
- Refrain from mentioning non-compliance as a norm in any situation.
- Do not ignore the role of teamwork in maintaining a safe environment.
Example answer
“I prioritize safety by strictly adhering to the safety protocols set forth by our company and applicable French regulations. For instance, I always wear the necessary personal protective equipment (PPE) and ensure that my colleagues do the same. I also conduct regular safety audits within my team and lead training sessions to highlight best practices. Recently, I identified a potential hazard in our material storage area and worked with management to implement corrective measures, reducing near-misses by 40%. Staying informed about the latest safety regulations is crucial, and I regularly participate in safety workshops to enhance my knowledge.”
Skills tested
Question type
3. Senior Material Handler Interview Questions and Answers
3.1. Can you describe a situation where you had to manage a conflict within your team during a busy period?
Introduction
This question assesses your conflict resolution and teamwork skills, which are vital in a fast-paced warehouse environment where collaboration is essential.
How to answer
- Use the STAR method to structure your response
- Clearly outline the conflict, including the people involved and circumstances
- Explain how you approached the situation and your role in resolving it
- Discuss the outcome and any lessons learned
- Emphasize the importance of communication and teamwork
What not to say
- Blaming others without taking responsibility
- Describing a situation that escalated without resolution
- Failing to mention the steps taken to resolve the conflict
- Neglecting to highlight the importance of teamwork
Example answer
“During peak season at a logistics company, two team members had a disagreement over task responsibilities. I facilitated a meeting where both could voice their concerns. By clarifying roles and setting priorities, we reached a compromise. This not only eased tensions but improved our workflow, resulting in a 20% increase in productivity during that busy period.”
Skills tested
Question type
3.2. How do you ensure safety and compliance in your handling of materials?
Introduction
This question evaluates your knowledge of safety protocols and compliance regulations, which are crucial in preventing accidents and ensuring a safe working environment.
How to answer
- Detail your understanding of safety regulations relevant to material handling
- Describe specific safety practices you follow or implement
- Share examples of how you have trained or guided others on safety
- Explain how you monitor compliance and address safety issues
- Discuss the importance of a safety-first culture in the workplace
What not to say
- Ignoring specific safety protocols or regulations
- Failing to provide real-world examples of safety practices
- Suggesting that safety is solely the responsibility of management
- Neglecting the importance of continuous safety training
Example answer
“At a previous role in a manufacturing facility, I conducted daily safety checks and ensured that all team members were up-to-date on material handling protocols. I initiated a training program that focused on proper lifting techniques and equipment use, which reduced workplace accidents by over 30%. Maintaining a safety-first culture is essential, and I regularly encourage team discussions about safety improvements.”
Skills tested
Question type
4. Lead Material Handler Interview Questions and Answers
4.1. Can you describe a time when you improved the efficiency of a warehouse process?
Introduction
This question assesses your ability to identify inefficiencies and implement effective solutions, which are critical skills for a Lead Material Handler.
How to answer
- Use the STAR method to structure your response: Situation, Task, Action, Result.
- Clearly describe the process that needed improvement and why it was inefficient.
- Detail the specific actions you took to implement changes, including any tools or methodologies used.
- Quantify the results of your improvements, such as time savings or cost reductions.
- Highlight any collaboration with team members or cross-departmental communication that facilitated the change.
What not to say
- Vaguely mentioning improvements without specific details or metrics.
- Focusing solely on the problem without explaining your solution.
- Taking full credit for improvements without acknowledging team contributions.
- Neglecting to mention any challenges faced during the process.
Example answer
“At Woolworths, I noticed our inventory restocking process was taking too long, leading to stockouts. I analyzed the workflow and identified that we could streamline our picking process by implementing a zone picking strategy. After training the team, we reduced restocking time by 30%, significantly decreasing stockouts and improving customer satisfaction.”
Skills tested
Question type
4.2. How do you ensure safety and compliance in a fast-paced warehouse environment?
Introduction
This question focuses on your knowledge and management of safety protocols, which are crucial in preventing accidents and ensuring regulatory compliance in material handling.
How to answer
- Discuss your understanding of relevant safety regulations and standards applicable in Australia, such as WHS (Work Health and Safety) guidelines.
- Explain how you conduct safety training and ensure all team members are aware of safety protocols.
- Describe methods you use to monitor compliance, such as regular audits or safety drills.
- Share how you handle safety incidents and what preventive measures you implement to avoid future occurrences.
- Mention any initiatives you've led to promote a culture of safety in the workplace.
What not to say
- Ignoring the importance of safety protocols or suggesting they are burdensome.
- Failing to provide specific examples of safety measures you've implemented.
- Claiming that accidents are unavoidable without discussing prevention strategies.
- Neglecting to mention team involvement or training in safety practices.
Example answer
“In my previous role at Coles, I prioritized safety by conducting weekly safety briefings and ensuring compliance with WHS regulations. I initiated a buddy system for new hires to learn safety protocols from experienced staff. After implementing regular safety audits, we reduced incidents by 40% over the year, fostering a culture of safety among our team.”
Skills tested
Question type
5. Shipping and Receiving Coordinator Interview Questions and Answers
5.1. Can you describe a time when you had to resolve a significant issue with a shipment?
Introduction
This question assesses your problem-solving skills and ability to handle logistics challenges, which are crucial for a Shipping and Receiving Coordinator.
How to answer
- Use the STAR method (Situation, Task, Action, Result) to structure your response
- Clearly explain the nature of the shipment issue and its implications
- Detail the steps you took to investigate and resolve the problem
- Highlight any collaboration with other teams or stakeholders
- Describe the outcome and any improvements made to prevent future issues
What not to say
- Blaming external factors without taking responsibility
- Providing vague examples without specific actions or results
- Neglecting to mention teamwork or communication with other departments
- Failing to demonstrate learning or process improvements from the incident
Example answer
“At a previous role with a logistics company, we faced a significant delay in a shipment due to a customs hold. I quickly coordinated with our customs broker to understand the issue and worked with our supplier to provide the necessary documentation. By maintaining clear communication with our clients, we mitigated dissatisfaction. The shipment was released within 48 hours, and I implemented a checklist to streamline future customs processes, reducing similar delays by 30%.”
Skills tested
Question type
5.2. How do you ensure accuracy in inventory management?
Introduction
This question tests your attention to detail and methods for maintaining accurate inventory records, which is vital for effective shipping and receiving operations.
How to answer
- Describe your approach to inventory tracking and data entry
- Explain how you conduct regular audits or counts
- Detail any software or tools you use for inventory management
- Discuss how you address discrepancies when they arise
- Highlight your experience with training others on inventory accuracy
What not to say
- Implying that accuracy is not a priority in your role
- Providing generic answers without mentioning specific processes
- Neglecting the importance of technology in inventory management
- Failing to acknowledge the consequences of inaccurate inventory
Example answer
“I prioritize accuracy by implementing a systematic approach to inventory management. I utilize software like SAP for real-time tracking and conduct monthly physical counts to verify records. When discrepancies arise, I investigate promptly, often tracing back through shipping logs to identify issues. Additionally, I trained my team on best practices, which improved our inventory accuracy rate by 15% in six months.”
Skills tested
Question type
6. Warehouse Supervisor Interview Questions and Answers
6.1. Can you describe a time when you improved the efficiency of warehouse operations?
Introduction
This question assesses your ability to identify inefficiencies and implement changes that enhance productivity, which is essential for a Warehouse Supervisor role.
How to answer
- Use the STAR method (Situation, Task, Action, Result) to structure your response
- Clearly describe the initial inefficiency and its impact on operations
- Detail the specific steps you took to analyze and address the issue
- Explain the results of your actions, including any metrics or improvements
- Share any lessons learned from the experience that can be applied to future situations
What not to say
- Providing vague examples without specific actions or results
- Focusing solely on the problem without discussing solutions
- Claiming success without backing it up with data or evidence
- Ignoring the role of team collaboration in the improvement process
Example answer
“At a previous role in a logistics company, I noticed that our picking process was leading to delays. I implemented a new layout for the shelves based on item popularity, which minimized travel time. As a result, we increased order fulfillment speed by 25% within three months, significantly improving overall operations and customer satisfaction.”
Skills tested
Question type
6.2. How would you handle a conflict between team members in the warehouse?
Introduction
This situational question evaluates your conflict resolution skills and ability to maintain a positive team environment, crucial for a supervisory position.
How to answer
- Describe your approach to understanding the root cause of the conflict
- Explain how you would facilitate communication between the parties involved
- Detail any specific strategies you would use to mediate the situation
- Emphasize the importance of maintaining team morale and productivity
- Share a relevant example if possible, showcasing your conflict resolution experience
What not to say
- Avoiding the issue or suggesting ignoring the conflict
- Focusing solely on disciplinary action without mediation
- Claiming that conflict resolution is not part of your role
- Not considering the perspectives of all parties involved
Example answer
“In my previous role, two team members had a disagreement over task responsibilities. I called for a private meeting to hear both sides and encouraged open communication. By clarifying roles and finding common ground, we reached a resolution that improved their collaboration and reduced misunderstandings. This experience reinforced my belief in proactive conflict resolution to maintain a harmonious work environment.”
Skills tested
Question type
Similar Interview Questions and Sample Answers
Simple pricing, powerful features
Upgrade to Himalayas Plus and turbocharge your job search.
Himalayas
Himalayas Plus
Himalayas Max
Find your dream job
Sign up now and join over 100,000 remote workers who receive personalized job alerts, curated job matches, and more for free!
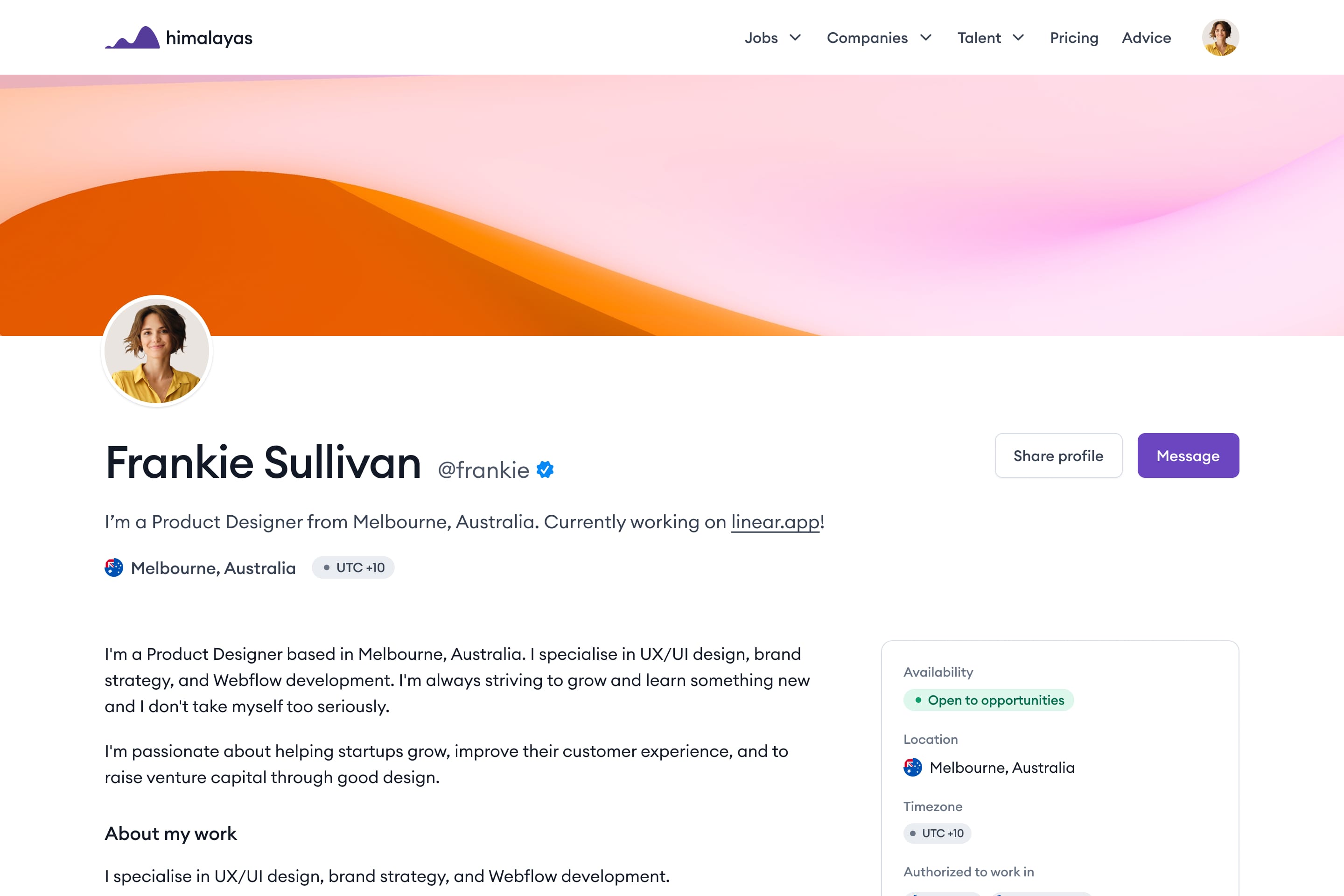