6 Quality Control Analyst Interview Questions and Answers
Quality Control Analysts ensure that products and processes meet established standards of quality and safety. They perform inspections, tests, and evaluations to identify defects or deviations, and work to resolve quality issues. Junior analysts focus on routine testing and data collection, while senior analysts and managers oversee quality assurance programs, lead teams, and implement process improvements to maintain high standards. Need to practice for an interview? Try our AI interview practice for free then unlock unlimited access for just $9/month.
Unlimited interview practice for $9 / month
Improve your confidence with an AI mock interviewer.
No credit card required
1. Junior Quality Control Analyst Interview Questions and Answers
1.1. Can you describe a time when you identified a defect in a product during quality control testing?
Introduction
This question is crucial for a Junior Quality Control Analyst as it assesses your attention to detail and problem-solving skills in identifying issues before they reach customers.
How to answer
- Use the STAR method (Situation, Task, Action, Result) to structure your answer
- Clearly describe the context of the testing environment
- Explain the specific defect you identified and its potential impact
- Detail the steps you took to report and address the defect
- Share the outcome and any improvements made as a result
What not to say
- Providing examples that lack detail or clarity
- Neglecting to mention how you communicated the issue to the team
- Focusing solely on the defect without discussing the resolution process
- Overlooking the importance of teamwork in quality control
Example answer
“While working on a product line at a manufacturing company, I identified a recurring defect in the packaging that could compromise the product's integrity. I documented the issue, collaborated with the production team to trace its origin, and recommended changes in the wrapping process. This led to a 15% reduction in packaging defects over the following month, ensuring better product quality and customer satisfaction.”
Skills tested
Question type
1.2. How do you ensure that you stay updated with the latest quality control standards and best practices?
Introduction
This question evaluates your commitment to continuous learning and professional development, which is essential in the ever-evolving field of quality control.
How to answer
- Discuss specific resources you use, such as industry publications, webinars, and professional organizations
- Mention any relevant certifications or training you've pursued or plan to pursue
- Share how you apply new knowledge or techniques in your work
- Explain your approach to networking with other professionals in the field
- Highlight your proactive attitude toward learning and growth
What not to say
- Indicating a lack of interest in ongoing learning
- Only mentioning casual or informal sources of information
- Failing to connect learning to practical application
- Being vague about your strategies for staying updated
Example answer
“I prioritize staying updated by subscribing to industry journals like the Journal of Quality in Maintenance Engineering and attending relevant webinars. Recently, I completed a certification in Six Sigma, which provided me with valuable tools and methodologies that I've already started implementing in my current role. Additionally, I engage with a network of quality control professionals through LinkedIn, which helps me exchange ideas and experiences.”
Skills tested
Question type
2. Quality Control Analyst Interview Questions and Answers
2.1. Can you describe a situation where you identified a quality issue during the testing process? How did you address it?
Introduction
This question assesses your attention to detail and problem-solving abilities, which are crucial for a Quality Control Analyst.
How to answer
- Use the STAR method to structure your response: Situation, Task, Action, Result.
- Clearly explain the context of the testing process and the specific quality issue you encountered.
- Detail the steps you took to investigate and resolve the issue, including any tools or methodologies you used.
- Discuss the outcome of your actions, emphasizing any improvements in product quality or team processes.
- Reflect on what you learned from the experience and how it has influenced your approach to quality control.
What not to say
- Failing to provide a specific example and speaking in generalities.
- Not taking responsibility or blaming others for the quality issue.
- Overlooking the importance of documenting the issue and the resolution process.
- Neglecting to mention the impact of your actions on the overall project or product.
Example answer
“While working at Toyota, I discovered a recurring defect in a batch of parts during my quality testing. I immediately documented the issue and collaborated with the production team to trace the defect to a malfunctioning machine. By implementing a recalibration process and additional training for operators, we reduced the defect rate by 25%. This experience taught me the importance of cross-team communication and proactive issue resolution.”
Skills tested
Question type
2.2. What quality assurance tools and methodologies are you familiar with, and how have you applied them in your previous roles?
Introduction
This question evaluates your technical proficiency with quality assurance practices and tools that are essential for a Quality Control Analyst.
How to answer
- List specific tools and methodologies you have experience with, such as Six Sigma, ISO standards, or specific QA software.
- Provide examples of how you have successfully implemented these tools in past projects.
- Discuss any certifications or training you have completed related to these methodologies.
- Mention how you stay updated with the latest trends and tools in the quality control field.
- Highlight any measurable impacts these methodologies have had on the quality of products or processes.
What not to say
- Vague references to tools without specific examples of use.
- Claiming familiarity with tools without demonstrating how you have applied them.
- Ignoring the importance of continuous learning in quality control methodologies.
- Failing to connect your experience with the needs of the company or role.
Example answer
“I am well-versed in Six Sigma and have utilized tools like Minitab for data analysis to measure process performance. At Sony, I led a team project where we applied Six Sigma principles to reduce defects in a product line by 30%. I also hold a Six Sigma Green Belt certification, which has helped me deepen my understanding of quality metrics and process improvement. I continually seek out webinars and workshops to enhance my knowledge in this area.”
Skills tested
Question type
3. Senior Quality Control Analyst Interview Questions and Answers
3.1. Can you describe a situation where you identified a significant quality issue in a product? What steps did you take to address it?
Introduction
This question assesses your analytical skills and ability to take initiative in maintaining quality standards, which are critical for a Senior Quality Control Analyst.
How to answer
- Use the STAR method to structure your response: Situation, Task, Action, Result.
- Clearly explain the quality issue you identified and its potential impact on the business or customers.
- Detail the specific steps you took to investigate and address the issue, including any testing methods or tools used.
- Discuss how you collaborated with other teams (e.g., production, engineering) to resolve the issue.
- Share the measurable outcomes that resulted from your actions, reflecting on how this improved the product quality.
What not to say
- Blaming others for the quality issue without taking responsibility.
- Providing vague descriptions of the problem without specific details.
- Failing to mention the importance of effective communication with stakeholders.
- Ignoring the follow-up actions taken to ensure the issue wouldn't recur.
Example answer
“At a previous role with Nestlé, I discovered a batch of products that did not meet our quality standards due to a machinery malfunction. I immediately initiated a thorough investigation using our internal testing protocols. Collaborating closely with the production team, we identified the root cause and implemented corrective actions. This not only resolved the quality issue but also led to a 20% reduction in similar incidents over the next quarter, emphasizing the importance of proactive quality control.”
Skills tested
Question type
3.2. How do you stay updated with industry standards and regulatory requirements related to quality control?
Introduction
This question evaluates your commitment to continuous learning and adaptability, which are essential for maintaining high quality standards in a dynamic regulatory environment.
How to answer
- Discuss specific resources or platforms you use to stay informed, such as professional organizations, webinars, or industry publications.
- Mention any relevant certifications or training programs you have completed.
- Explain how you apply the knowledge gained from these resources to your work.
- Share examples of how staying updated has positively impacted your role or organization.
- Highlight your proactive approach to sharing knowledge with team members.
What not to say
- Claiming you do not follow industry updates or standards.
- Providing generic answers without specifics on resources or methods.
- Focusing only on past knowledge without discussing ongoing learning.
- Neglecting to mention the importance of compliance in your role.
Example answer
“I actively engage with the South African Bureau of Standards and subscribe to industry newsletters. I recently completed a certification in ISO 9001:2015, which deepened my understanding of current quality management systems. I regularly share insights from these resources with my team and have implemented best practices that align with new regulations, enhancing our quality assurance processes significantly.”
Skills tested
Question type
4. Quality Control Specialist Interview Questions and Answers
4.1. Can you describe a time when you identified a significant quality issue and how you handled it?
Introduction
This question is crucial for assessing your problem-solving skills and your ability to implement effective quality control measures. Identifying and resolving quality issues is a core responsibility for a Quality Control Specialist.
How to answer
- Use the STAR method to structure your response (Situation, Task, Action, Result)
- Clearly describe the quality issue, including its context and impact on the product or process
- Explain the steps you took to investigate and address the issue
- Highlight any collaboration with other team members or departments
- Quantify the results of your actions, such as reduced defects or improved processes
What not to say
- Avoid vague descriptions of the issue without specific details
- Don't take sole credit for team efforts; acknowledge collaboration
- Refrain from discussing issues you did not resolve or take action on
- Do not gloss over the importance of quality control in your response
Example answer
“At Johnson & Johnson, I identified a recurring defect in our packaging line that resulted in product damage. I led an investigation that involved analyzing production data and conducting root cause analysis. By collaborating with the engineering team, we redesigned the packaging process, which ultimately reduced product return rates by 30%. This experience reinforced the importance of thorough investigation and cross-department collaboration in quality control.”
Skills tested
Question type
4.2. How do you stay updated on quality standards and regulations relevant to our industry?
Introduction
This question assesses your commitment to continuous learning and your knowledge of industry standards, which is vital for ensuring compliance and maintaining high-quality outputs.
How to answer
- Mention specific resources or organizations you follow (e.g., ISO, ASTM, FDA)
- Discuss any professional certifications or training programs you've completed
- Explain how you apply this knowledge in your role to improve quality control processes
- Highlight any active participation in industry groups or forums
- Describe how you share relevant updates with your team or organization
What not to say
- Claiming you don't follow any standards or updates
- Providing outdated information or resources
- Focusing only on personal benefits of staying updated without mentioning team impact
- Neglecting to mention any formal training or certifications
Example answer
“I regularly follow updates from the American Society for Quality (ASQ) and participate in webinars on ISO standards. Last year, I completed a Six Sigma certification, which has enhanced my understanding of quality control processes. I actively share insights with my team during weekly meetings, ensuring everyone is aligned with current standards and best practices.”
Skills tested
Question type
5. Quality Assurance Analyst Interview Questions and Answers
5.1. Can you describe a time when you identified a critical bug in a software application before it reached production?
Introduction
This question is crucial for evaluating your attention to detail and problem-solving skills, which are essential for a Quality Assurance Analyst.
How to answer
- Begin by setting the context of the project and the application being tested.
- Describe the testing methods you employed to discover the bug.
- Explain the severity of the bug and its potential impact on the end users.
- Detail the steps you took to report the bug and how you collaborated with the development team to resolve it.
- Highlight any positive outcomes resulting from your actions, such as improved product quality or enhanced team processes.
What not to say
- Avoid vague descriptions without specific details about the bug or testing process.
- Don't take sole credit; acknowledge the collaborative effort with the development team.
- Refrain from discussing minor bugs that would not have significant impacts.
- Do not omit the follow-up actions taken to ensure the bug was fixed.
Example answer
“While working at Shopify, I was testing a new feature when I discovered a critical bug that caused payment processing failures. I used exploratory testing techniques and detailed logs to identify the issue. Reporting it immediately, I collaborated with developers to implement a fix, which prevented a potential financial loss for users. This experience underscored the importance of thorough testing and communication.”
Skills tested
Question type
5.2. How do you prioritize your testing tasks when you have multiple projects with tight deadlines?
Introduction
This question assesses your time management and prioritization skills, which are critical for handling multiple projects effectively.
How to answer
- Explain your criteria for prioritizing tasks, such as risk assessment and business impact.
- Discuss any tools or frameworks you use to manage your workload.
- Share how you communicate priorities with your team and stakeholders.
- Provide an example of a situation where you successfully managed competing deadlines.
- Mention the importance of flexibility and adaptability in your approach.
What not to say
- Avoid suggesting that you can handle everything without prioritization.
- Do not ignore the importance of team communication in managing priorities.
- Refrain from giving examples where you missed deadlines due to poor prioritization.
- Don't imply that you only focus on the most urgent tasks at the expense of quality.
Example answer
“At my previous job with Telus, I faced multiple project deadlines. I prioritized testing based on the risk associated with each feature and its impact on users. I used a project management tool to visualize tasks and communicated priorities during daily stand-ups. This approach allowed me to complete testing for a high-risk feature ahead of schedule, ensuring a smooth release. Flexibility was key, as I adjusted my focus when new high-priority issues arose.”
Skills tested
Question type
6. Quality Control Manager Interview Questions and Answers
6.1. Can you describe a time when you identified a quality issue in the production process and how you resolved it?
Introduction
This question is crucial as it evaluates your ability to identify quality issues proactively and implement effective solutions, which is a key responsibility of a Quality Control Manager.
How to answer
- Use the STAR method to structure your response: Situation, Task, Action, Result.
- Clearly outline the quality issue you identified and its implications for production.
- Detail the steps you took to investigate the issue and gather data.
- Explain the actions you implemented to resolve the issue and improve processes.
- Share the results, focusing on metrics that demonstrate improvement in quality.
What not to say
- Failing to take responsibility for the quality issue.
- Not discussing specific metrics or results from your actions.
- Overlooking the importance of teamwork in resolving issues.
- Providing a vague or unrelated example without clear relevance to quality control.
Example answer
“At Toyota, I noticed an increase in defects during the assembly process. I initiated a root cause analysis, which revealed a misalignment in the machinery. I coordinated with the engineering team to recalibrate the equipment and provided training to the assembly line workers. As a result, our defect rate dropped by 30% within a month, significantly improving product quality and customer satisfaction.”
Skills tested
Question type
6.2. How do you ensure that your quality control team remains compliant with industry standards and regulations?
Introduction
This question assesses your knowledge of industry standards and your capability to lead a team in maintaining compliance, which is vital for a Quality Control Manager.
How to answer
- Discuss your familiarity with relevant industry standards, such as ISO 9001.
- Explain the training programs you implement for your team regarding compliance.
- Describe how you conduct regular audits and assessments to ensure adherence.
- Detail your approach to staying updated with regulatory changes and disseminating this information to your team.
- Highlight any past experiences where you successfully ensured compliance in your team.
What not to say
- Indicating that compliance is not a priority for your team.
- Failing to mention specific industry standards or regulations.
- Overlooking the importance of continuous training and education.
- Neglecting to discuss the consequences of non-compliance.
Example answer
“At Canon, I ensured our team remained compliant with ISO 9001 by implementing a structured training program that updated staff on quality standards and regulations. I scheduled quarterly audits and created a checklist for our processes. When new regulations were introduced, I organized a workshop to educate the team. This proactive approach helped us maintain compliance and avoid any penalties.”
Skills tested
Question type
Similar Interview Questions and Sample Answers
Simple pricing, powerful features
Upgrade to Himalayas Plus and turbocharge your job search.
Himalayas
Himalayas Plus
Himalayas Max
Find your dream job
Sign up now and join over 100,000 remote workers who receive personalized job alerts, curated job matches, and more for free!
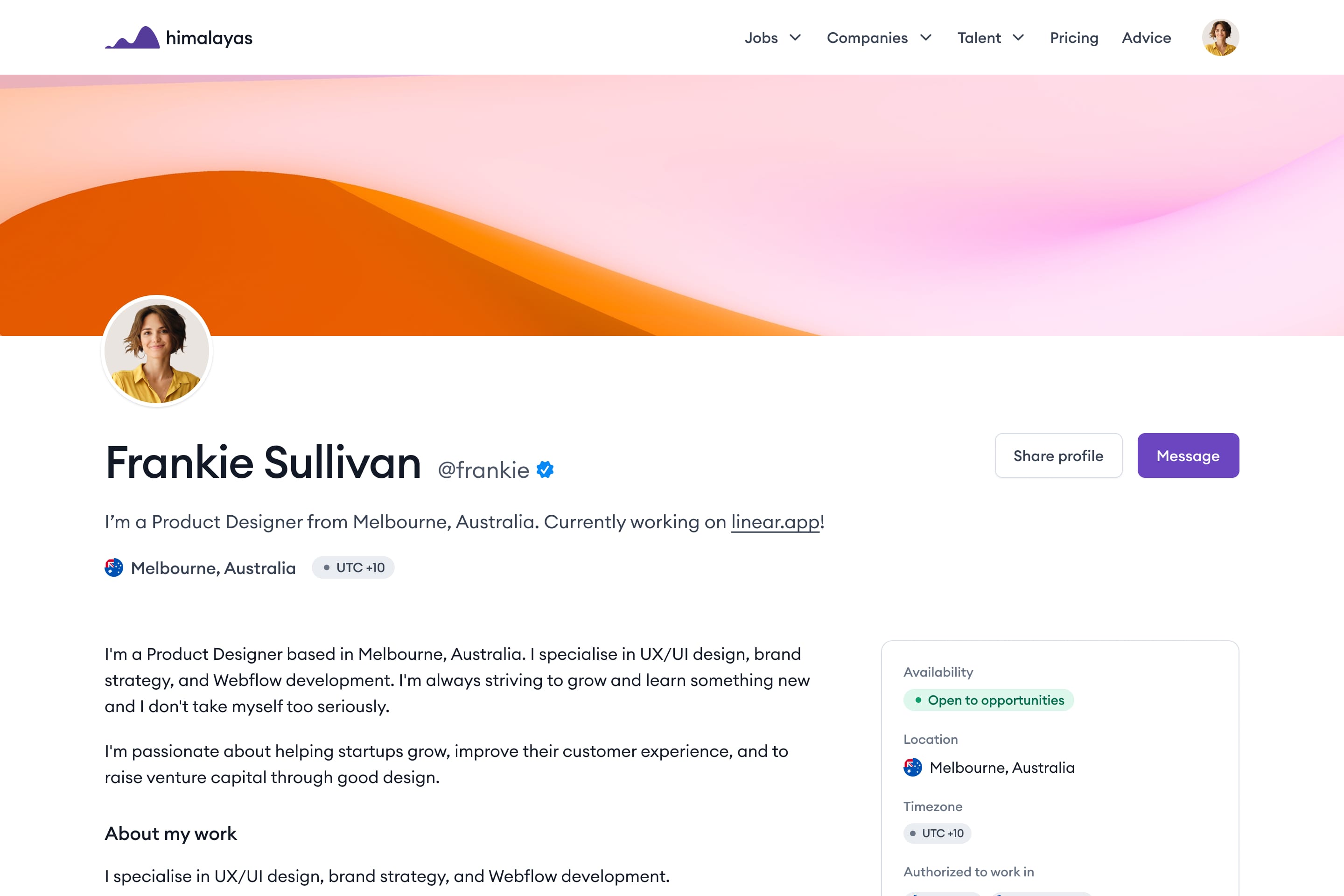