6 Plant Superintendent Interview Questions and Answers
Plant Superintendents oversee the daily operations of manufacturing or production facilities, ensuring that processes run efficiently, safely, and within budget. They manage staff, coordinate production schedules, and enforce compliance with safety and quality standards. Junior roles may involve assisting in operations and learning the intricacies of plant management, while senior roles focus on strategic planning, team leadership, and optimizing plant performance. Need to practice for an interview? Try our AI interview practice for free then unlock unlimited access for just $9/month.
Unlimited interview practice for $9 / month
Improve your confidence with an AI mock interviewer.
No credit card required
1. Assistant Plant Superintendent Interview Questions and Answers
1.1. Can you describe a time when you had to deal with a significant operational challenge in a manufacturing environment?
Introduction
This question assesses your problem-solving skills and ability to manage operational challenges, which are vital for an Assistant Plant Superintendent role.
How to answer
- Use the STAR method (Situation, Task, Action, Result) to structure your response.
- Clearly outline the operational challenge and its implications on production.
- Discuss the specific actions you took to address the challenge.
- Highlight any collaboration with team members and departments.
- Quantify the results to demonstrate the impact of your actions, such as improved efficiency or reduced downtime.
What not to say
- Focusing solely on the problem without discussing your solution.
- Neglecting to mention teamwork or collaboration.
- Providing vague answers without measurable outcomes.
- Avoiding responsibility or blaming others for the challenge.
Example answer
“At a manufacturing plant in Valencia, we faced a critical equipment failure that halted production. I quickly organized a cross-functional team to diagnose the issue. We implemented a temporary workaround that allowed us to resume operations within 48 hours while simultaneously working with the maintenance team to repair the equipment. As a result, we minimized downtime to only 5% of our production schedule, maintaining our output targets.”
Skills tested
Question type
1.2. How do you ensure safety compliance and promote a culture of safety within the plant?
Introduction
Safety is paramount in manufacturing. This question evaluates your knowledge of safety protocols and your ability to foster a safe working environment.
How to answer
- Discuss your familiarity with safety regulations and standards relevant to the industry.
- Explain your strategies for training employees and ensuring compliance.
- Provide examples of initiatives you have implemented to enhance safety culture.
- Mention how you monitor and assess safety performance metrics.
- Highlight any past experiences where you successfully improved safety outcomes.
What not to say
- Implying safety is solely the responsibility of the safety officer.
- Providing generic answers without personal involvement.
- Ignoring the importance of employee engagement in safety.
- Failing to mention specific safety protocols or metrics.
Example answer
“In my previous role at a manufacturing facility, I implemented a comprehensive safety training program that included regular workshops and hazard recognition drills. I also established a safety committee that included employees from all levels to foster ownership of safety practices. Over the course of a year, our incident rate decreased by 30%, demonstrating the positive impact of a proactive safety culture.”
Skills tested
Question type
2. Plant Superintendent Interview Questions and Answers
2.1. Can you describe a time when you improved operational efficiency in a plant?
Introduction
This question is important as it evaluates your ability to identify inefficiencies and implement effective solutions, a critical skill for a Plant Superintendent.
How to answer
- Use the STAR method to structure your response (Situation, Task, Action, Result)
- Clearly outline the specific inefficiency you identified
- Explain the steps you took to analyze the situation and develop a solution
- Detail how you implemented the changes, including any team collaboration
- Quantify the results in terms of efficiency gains, cost savings, or production increases
What not to say
- Focusing on minor improvements without substantial impact
- Taking sole credit without acknowledging team contributions
- Neglecting to mention any challenges faced during implementation
- Providing vague answers without specific metrics or examples
Example answer
“At Fiat Chrysler, I noticed that our assembly line was experiencing delays due to inefficient material handling. I led a team to redesign the workflow and introduced a new inventory management system. As a result, we reduced assembly time by 20% and cut down on material waste by 15%. This experience taught me the value of proactive problem-solving and teamwork.”
Skills tested
Question type
2.2. How do you ensure compliance with safety regulations in the plant?
Introduction
This question assesses your knowledge and commitment to safety standards, which are critical in a manufacturing environment.
How to answer
- Describe your approach to developing and enforcing safety policies
- Share specific examples of safety initiatives you've implemented
- Explain how you conduct training and regular safety audits
- Discuss how you encourage a culture of safety among employees
- Highlight any measurable improvements in safety metrics
What not to say
- Saying that safety compliance is solely the responsibility of the safety officer
- Providing generic answers without specific examples
- Not mentioning employee involvement in safety practices
- Ignoring the importance of continuous safety training and updates
Example answer
“At Pirelli, I implemented a comprehensive safety program that included weekly training sessions and monthly safety audits. I also established a safety committee that included employees from all levels to encourage input on safety practices. As a result, we saw a 30% reduction in workplace accidents over two years, reinforcing a culture of safety and accountability.”
Skills tested
Question type
3. Senior Plant Superintendent Interview Questions and Answers
3.1. Can you describe a time when you improved the efficiency of a plant operation?
Introduction
This question assesses your ability to drive operational improvements and efficiency in a manufacturing environment, which is crucial for a Senior Plant Superintendent's role.
How to answer
- Use the STAR method to structure your response: Situation, Task, Action, Result.
- Clearly define the operational inefficiency you faced and its impact on production.
- Detail the specific actions you took to address the issue, including any methodologies or tools used.
- Quantify the improvements achieved (e.g., percentage increase in efficiency, cost savings).
- Discuss any lessons learned and how you applied them to future operations.
What not to say
- Vague statements without clear metrics or outcomes.
- Attributing all success to external factors without personal contribution.
- Focusing solely on technical details without mentioning team involvement.
- Neglecting to mention ongoing monitoring or sustainability of improvements.
Example answer
“At BHP, we faced a significant slowdown in our processing line, impacting our production targets. I initiated a thorough review using Lean Six Sigma methodologies, identifying bottlenecks that caused delays. By implementing process restructuring and training staff on new protocols, we increased efficiency by 30%, which saved the company $200,000 annually. This experience taught me the importance of continuous improvement and team engagement.”
Skills tested
Question type
3.2. How do you ensure safety compliance within the plant?
Introduction
Safety compliance is paramount in plant operations. This question evaluates your knowledge of safety protocols and your ability to foster a safety-first culture.
How to answer
- Discuss your understanding of relevant safety regulations (e.g., Work Health and Safety Act in Australia).
- Explain how you conduct safety audits and ensure compliance with regulations.
- Share examples of how you promote a safety culture among employees.
- Detail your approach to training staff and addressing non-compliance issues.
- Highlight any specific safety initiatives you have led and their outcomes.
What not to say
- Implying safety regulations are unimportant or secondary to production goals.
- Neglecting to mention proactive measures or just focusing on reactive solutions.
- Failing to provide specific examples or results from safety initiatives.
- Suggesting that safety is solely the responsibility of the safety officer.
Example answer
“At Rio Tinto, I implemented a comprehensive safety program that included regular audits, safety training, and employee engagement sessions. We established clear safety protocols and a reporting system for hazards. As a result, our incident rate dropped by 40% over two years. I believe a strong safety culture is built on open communication and accountability at all levels.”
Skills tested
Question type
4. Plant Manager Interview Questions and Answers
4.1. Can you describe a time when you improved a manufacturing process and what the outcome was?
Introduction
This question assesses your ability to analyze and improve processes, which is crucial for a Plant Manager to enhance operational efficiency and reduce costs.
How to answer
- Use the STAR method to structure your answer: Situation, Task, Action, Result.
- Clearly describe the specific manufacturing process you focused on.
- Explain the challenges you identified and the rationale behind your improvements.
- Detail the steps you took to implement the changes, including any team involvement.
- Quantify the results achieved, such as increased productivity or cost savings.
What not to say
- Focusing solely on technical aspects without discussing team engagement.
- Failing to provide concrete metrics or outcomes.
- Not mentioning the challenges faced during the improvement process.
- Taking credit for the results without acknowledging team contributions.
Example answer
“At a previous role with Siemens, I identified that our assembly line was experiencing significant downtime due to inefficient machine setups. I led a cross-functional team to analyze the process, and we implemented a standardized setup protocol that reduced machine changeover time by 30%. As a result, we increased our overall production efficiency by 20%, which saved the company approximately €200,000 annually.”
Skills tested
Question type
4.2. How do you ensure safety standards are met in your plant?
Introduction
This question evaluates your commitment to safety, regulatory compliance, and the ability to foster a safe working environment, which is a top priority for any Plant Manager.
How to answer
- Discuss the specific safety standards and regulations relevant to the industry.
- Explain your approach to training employees on safety practices.
- Detail how you monitor compliance and address any safety violations.
- Share examples of initiatives you’ve implemented to enhance safety culture.
- Highlight any measurable improvements in safety performance metrics.
What not to say
- Suggesting safety is someone else's responsibility.
- Failing to provide specific examples of safety initiatives.
- Ignoring the role of training in maintaining safety standards.
- Underestimating the importance of regular safety audits.
Example answer
“In my role at Nestlé, I implemented a comprehensive safety training program that included regular workshops and on-site drills. I also introduced a safety audit system that allowed us to identify and mitigate risks proactively. As a result, we achieved a 50% reduction in workplace accidents over two years, significantly improving our safety compliance scores.”
Skills tested
Question type
5. Operations Manager (Plant) Interview Questions and Answers
5.1. Can you describe a time when you improved operational efficiency in a plant setting?
Introduction
This question assesses your ability to identify inefficiencies and implement effective solutions, which is crucial for an Operations Manager in a manufacturing environment.
How to answer
- Use the STAR method (Situation, Task, Action, Result) to structure your response.
- Clearly outline the initial inefficiencies you identified and their impact on operations.
- Detail the specific actions you took to address these issues.
- Quantify the improvements achieved in terms of efficiency, cost savings, or production output.
- Discuss any challenges faced during the implementation and how you overcame them.
What not to say
- Focusing on theoretical improvements without real examples.
- Providing vague descriptions without measurable outcomes.
- Neglecting to mention teamwork or collaboration with other departments.
- Avoiding discussion of setbacks or failures during the process.
Example answer
“At my previous position with a manufacturing company in Ontario, I identified that our assembly line had a 20% downtime due to equipment failures. I initiated a predictive maintenance program by analyzing machine data and scheduled regular check-ups. As a result, we reduced downtime by 35%, which increased our production output by 15% within six months. This experience taught me the importance of proactive maintenance and data utilization.”
Skills tested
Question type
5.2. How do you handle conflicts between team members on the production floor?
Introduction
This question evaluates your conflict resolution skills and ability to maintain a positive work environment, which are essential for an Operations Manager overseeing plant staff.
How to answer
- Explain your approach to understanding the root cause of conflicts.
- Discuss specific strategies you employ to facilitate communication between conflicting parties.
- Provide an example of a conflict you successfully resolved and the skills you utilized.
- Emphasize the importance of maintaining team morale and productivity.
- Mention any follow-up actions you take to prevent future conflicts.
What not to say
- Dismissing conflicts as unimportant or irrelevant.
- Suggesting that you avoid dealing with conflicts altogether.
- Failing to provide a specific example of conflict resolution.
- Blaming one party without acknowledging the perspectives of both sides.
Example answer
“In my role at a manufacturing plant, I encountered a conflict between two team leaders over resource allocation. I organized a meeting where both could express their concerns, facilitating a discussion that focused on our shared goals. By encouraging collaboration, we devised a resource-sharing plan that improved overall productivity by 10%. This reinforced my belief in the value of open communication.”
Skills tested
Question type
6. Director of Plant Operations Interview Questions and Answers
6.1. Can you describe a time when you had to implement a significant operational change in a plant setting? What steps did you take?
Introduction
This question assesses your experience with change management and operational efficiency, which are critical skills for a Director of Plant Operations.
How to answer
- Use the STAR method (Situation, Task, Action, Result) to structure your response
- Clearly define the operational change needed and its context
- Discuss the steps you took to communicate and implement the change
- Highlight any challenges faced and how you overcame them
- Quantify the results to show the impact of the change on plant performance
What not to say
- Focusing on the change itself without discussing your leadership role
- Failing to mention specific metrics or measurable outcomes
- Avoiding discussion of challenges faced during implementation
- Not acknowledging team involvement in the change process
Example answer
“At BHP, we needed to reduce our production downtime by 20%. I led a cross-functional team to implement a predictive maintenance program. After analyzing historical data, we identified critical machinery needing more attention. By introducing regular maintenance schedules and training staff on new protocols, we achieved a 30% reduction in downtime within six months, significantly improving overall productivity.”
Skills tested
Question type
6.2. How do you ensure safety and compliance in plant operations, especially in a highly regulated industry?
Introduction
This question evaluates your knowledge of safety regulations and your ability to foster a culture of compliance and safety in plant operations.
How to answer
- Discuss the specific safety regulations relevant to the industry
- Explain your approach to training staff on safety protocols
- Describe how you conduct regular safety audits and compliance checks
- Share examples of how you have improved safety metrics in previous roles
- Highlight the importance of a safety-first culture among the workforce
What not to say
- Suggesting that safety is someone else's responsibility
- Failing to mention specific safety regulations or standards
- Neglecting to discuss the importance of training and audits
- Not providing examples of past safety improvements
Example answer
“In my previous role at Rio Tinto, I prioritized safety by implementing a comprehensive training program for all employees on workplace safety standards. We conducted quarterly safety audits and established a reward system for teams that excelled in compliance. This initiative led to a 40% reduction in workplace incidents over two years, reinforcing our commitment to a safety-first culture.”
Skills tested
Question type
Similar Interview Questions and Sample Answers
Simple pricing, powerful features
Upgrade to Himalayas Plus and turbocharge your job search.
Himalayas
Himalayas Plus
Himalayas Max
Find your dream job
Sign up now and join over 100,000 remote workers who receive personalized job alerts, curated job matches, and more for free!
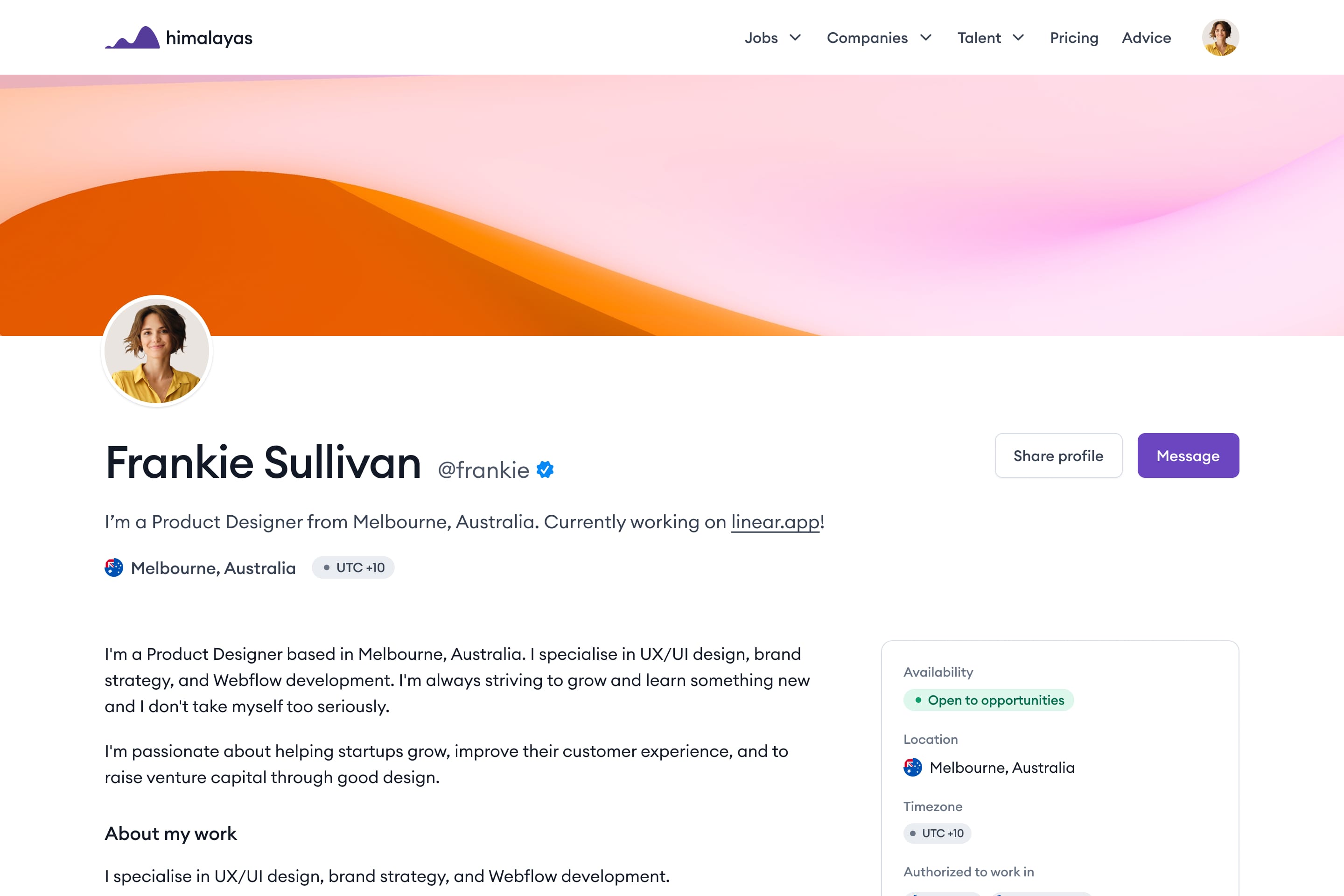