4 Orthotic Fabricator Technician Interview Questions and Answers
Orthotic Fabricator Technicians are skilled professionals who design, construct, and repair orthotic devices to assist individuals with mobility or structural challenges. They work closely with orthotists and healthcare professionals to create custom devices that meet patients' specific needs. Junior technicians focus on learning fabrication techniques and assisting with basic tasks, while senior and lead technicians oversee complex projects, ensure quality standards, and may train or mentor junior staff. Need to practice for an interview? Try our AI interview practice for free then unlock unlimited access for just $9/month.
Unlimited interview practice for $9 / month
Improve your confidence with an AI mock interviewer.
No credit card required
1. Junior Orthotic Fabricator Technician Interview Questions and Answers
1.1. Can you describe your experience with different materials used in orthotic fabrication?
Introduction
This question is essential to understanding your technical knowledge and practical experience with the materials that are critical in orthotic fabrication.
How to answer
- Identify specific materials you have worked with (e.g., thermoplastics, carbon fiber, etc.)
- Explain the properties of each material and why they are suitable for certain applications
- Share any techniques you use for cutting, shaping, or molding these materials
- Discuss how you ensure quality and precision in your work with these materials
- Include any experiences with troubleshooting material-related issues
What not to say
- Claiming to have experience without mentioning specific materials or techniques
- Providing vague or superficial knowledge about materials
- Ignoring safety or quality control practices
- Not acknowledging the importance of selecting the right material for specific patient needs
Example answer
“In my previous role at a local clinic, I worked extensively with thermoplastics such as PETG and polypropylene. I learned to mold these materials using a vacuum forming technique, which allowed me to create custom orthotic devices. I ensured precision by using calibrated tools and verifying dimensions against patient casts. Additionally, when we faced issues with material brittleness, I researched and suggested using a carbon fiber composite for more durable outcomes. This experience highlighted the importance of material selection in patient comfort and device longevity.”
Skills tested
Question type
1.2. Describe a challenging project you worked on in orthotic fabrication and how you overcame obstacles.
Introduction
This question assesses your problem-solving skills and ability to adapt under pressure, which are vital in a hands-on technical role like this.
How to answer
- Use the STAR method to structure your response
- Clearly describe the project and the specific challenges you faced
- Explain the steps you took to address these challenges
- Highlight any collaboration with colleagues or other departments
- Share the outcome and what you learned from the experience
What not to say
- Focusing on the negative aspects without discussing the resolution
- Not mentioning teamwork or collaboration if applicable
- Giving an overly simplistic account of the challenge
- Failing to reflect on lessons learned or personal growth
Example answer
“While working on a custom foot orthotic for a patient with complex foot deformities, we faced issues with initial fit and comfort. I collaborated with the physiotherapist to gather detailed feedback from the patient. After several iterations, I adjusted the design and used a softer material for the areas causing discomfort. The final product not only fit well but also significantly improved the patient's mobility. This experience taught me the importance of listening to feedback and collaborating closely with healthcare professionals.”
Skills tested
Question type
2. Orthotic Fabricator Technician Interview Questions and Answers
2.1. Can you describe your experience with different orthotic materials and how you choose the right one for specific patient needs?
Introduction
This question is crucial for understanding your technical knowledge and decision-making process in selecting materials, which directly impacts patient outcomes.
How to answer
- Discuss your familiarity with various orthotic materials (e.g., thermoplastics, composites, foams)
- Explain the criteria you consider when selecting materials (durability, flexibility, patient comfort)
- Provide examples of specific cases where you chose a particular material and the reasoning behind it
- Mention any collaborations with clinicians or other professionals to ensure the best material choice
- Highlight the importance of staying updated on new materials and techniques in the field
What not to say
- Claiming to have no experience with certain materials
- Focusing only on one type of material without considering patient needs
- Being vague about the selection process without specific examples
- Underestimating the importance of patient comfort and fit
Example answer
“In my role at a local clinic, I often work with various materials like polypropylene for its rigidity and thermoplastics for their moldability. For a patient needing a lightweight AFO for mobility, I chose a thin polypropylene due to its balance of strength and comfort. Collaborating closely with the prescribing clinician ensured we met the patient’s specific needs while considering their lifestyle.”
Skills tested
Question type
2.2. Describe a challenging case where you had to troubleshoot an issue with an orthotic device you fabricated.
Introduction
This question assesses your problem-solving skills and ability to adapt to unforeseen challenges in the fabrication process.
How to answer
- Use the STAR method to structure your response
- Clearly describe the problem, including any patient feedback or functional issues
- Explain the steps you took to identify the root cause of the issue
- Detail the solutions you implemented and their outcomes
- Discuss what you learned from the experience and how it improved your future work
What not to say
- Blaming the patient or external factors without taking responsibility
- Providing a solution that didn't work without explaining the learning process
- Being too technical without relating it back to patient impact
- Failing to mention collaboration with others when resolving the issue
Example answer
“I once fabricated a custom foot orthotic that initially caused discomfort for the patient. After receiving their feedback, I conducted a thorough assessment and realized I had not accounted for their arch height properly. I adjusted the design, using a softer material for cushioning. This not only resolved the discomfort but also improved their overall mobility. This experience taught me the importance of patient feedback in refining my work.”
Skills tested
Question type
3. Senior Orthotic Fabricator Technician Interview Questions and Answers
3.1. Can you describe a challenging case where you had to create a custom orthotic device for a patient with unique needs?
Introduction
This question assesses your technical expertise and problem-solving skills in a field where customization is key to patient care.
How to answer
- Begin by outlining the patient's specific needs and the challenges associated with them.
- Explain the steps you took to gather necessary information and collaborate with the healthcare team.
- Detail the fabrication process you used to create the custom orthotic device.
- Discuss how you evaluated the effectiveness of the device post-fitting.
- Highlight any feedback received from the patient or healthcare professionals that illustrates the success of your solution.
What not to say
- Avoid vague descriptions that lack detail about the case or the fabrication process.
- Do not focus solely on the technical aspects without discussing patient impact.
- Refrain from taking sole credit; mention collaboration with others.
- Steer clear of examples that ended in failure without discussing learnings.
Example answer
“I worked with a patient who had a rare foot deformity requiring a highly customized orthotic. I collaborated closely with the physiotherapist to understand the patient's mobility needs and conducted a thorough assessment. Using a CAD program, I designed an orthotic that provided the necessary support while considering comfort. After fitting, the patient reported a significant improvement in mobility and pain reduction, which was incredibly rewarding. This experience reinforced my belief in the importance of a patient-centered approach in orthotic fabrication.”
Skills tested
Question type
3.2. How do you ensure that your orthotic devices comply with industry standards and regulations?
Introduction
This question evaluates your understanding of compliance and quality assurance in orthotic fabrication, which is crucial for patient safety and legal adherence.
How to answer
- Discuss your knowledge of relevant industry standards and regulations, such as ISO or local health regulations.
- Explain your process for staying updated on changes in regulations.
- Detail how you implement quality control measures during fabrication.
- Describe any training or certifications you have that enhance your compliance knowledge.
- Mention how you document processes and maintain records for audits.
What not to say
- Neglecting to mention specific standards or regulations.
- Claiming compliance is not a significant part of your job.
- Providing examples of non-compliance without discussing corrective actions taken.
- Avoiding discussion on the importance of patient safety.
Example answer
“I stay informed about the latest ISO standards and local regulations through continuous education and attending relevant workshops. During fabrication, I follow a strict quality control checklist to ensure each device meets compliance criteria. Recently, I implemented a new documentation system that tracks every step of the fabrication process, which has streamlined our audit readiness. Ensuring compliance is not just about following rules; it’s about guaranteeing patient safety and the effectiveness of our devices.”
Skills tested
Question type
4. Lead Orthotic Fabricator Technician Interview Questions and Answers
4.1. Can you describe a time when you had to troubleshoot a problem with an orthotic device that you fabricated?
Introduction
This question is crucial as it assesses your technical problem-solving skills and your ability to ensure the quality of orthotic devices, which is vital in this role.
How to answer
- Begin with a clear description of the issue encountered with the orthotic device.
- Explain the steps you took to identify the root cause of the problem.
- Detail the corrective actions you implemented and the rationale behind them.
- Discuss the outcome of your troubleshooting efforts and any feedback received.
- Highlight the importance of precision and quality in orthotic fabrication.
What not to say
- Avoid vague descriptions of the problem without specifics.
- Don’t focus on the problem without discussing the solution.
- Refrain from taking sole credit; acknowledge collaboration if applicable.
- Avoid mentioning a lack of follow-up on the issue.
Example answer
“At Hanger Clinic, I encountered a situation where a custom foot orthotic was causing discomfort for the patient. I first reviewed the measurements and made adjustments to the mold based on patient feedback. After remaking the orthotic with the correct contours, the patient reported significant improvements. This experience reinforced my attention to detail and the critical nature of patient feedback in orthotic fabrication.”
Skills tested
Question type
4.2. How do you ensure that the orthotic devices you fabricate meet both patient needs and industry standards?
Introduction
This question evaluates your understanding of patient-centric care and regulatory compliance, which are essential for producing effective orthotic devices.
How to answer
- Explain your process for gathering patient needs and preferences.
- Discuss how you incorporate industry standards and best practices into your work.
- Share examples of how you have balanced patient requirements with technical specifications.
- Highlight any quality assurance measures you implement in your fabrication process.
- Mention ongoing education or training you pursue to stay updated on industry standards.
What not to say
- Failing to mention the importance of patient communication.
- Neglecting to discuss any standards or regulations.
- Suggesting that quality assurance is not part of your role.
- Providing a generic response that lacks specific examples.
Example answer
“In my role at Orthotic Solutions, I always start by conducting a thorough assessment of the patient’s needs through direct communication with them and their healthcare provider. I ensure my designs comply with both the American Orthotic and Prosthetic Association (AOPA) standards and the latest fabrication technologies. I regularly participate in workshops to stay informed on best practices, which helps me deliver orthotics that not only meet patient satisfaction but also uphold industry standards.”
Skills tested
Question type
Similar Interview Questions and Sample Answers
Simple pricing, powerful features
Upgrade to Himalayas Plus and turbocharge your job search.
Himalayas
Himalayas Plus
Himalayas Max
Find your dream job
Sign up now and join over 100,000 remote workers who receive personalized job alerts, curated job matches, and more for free!
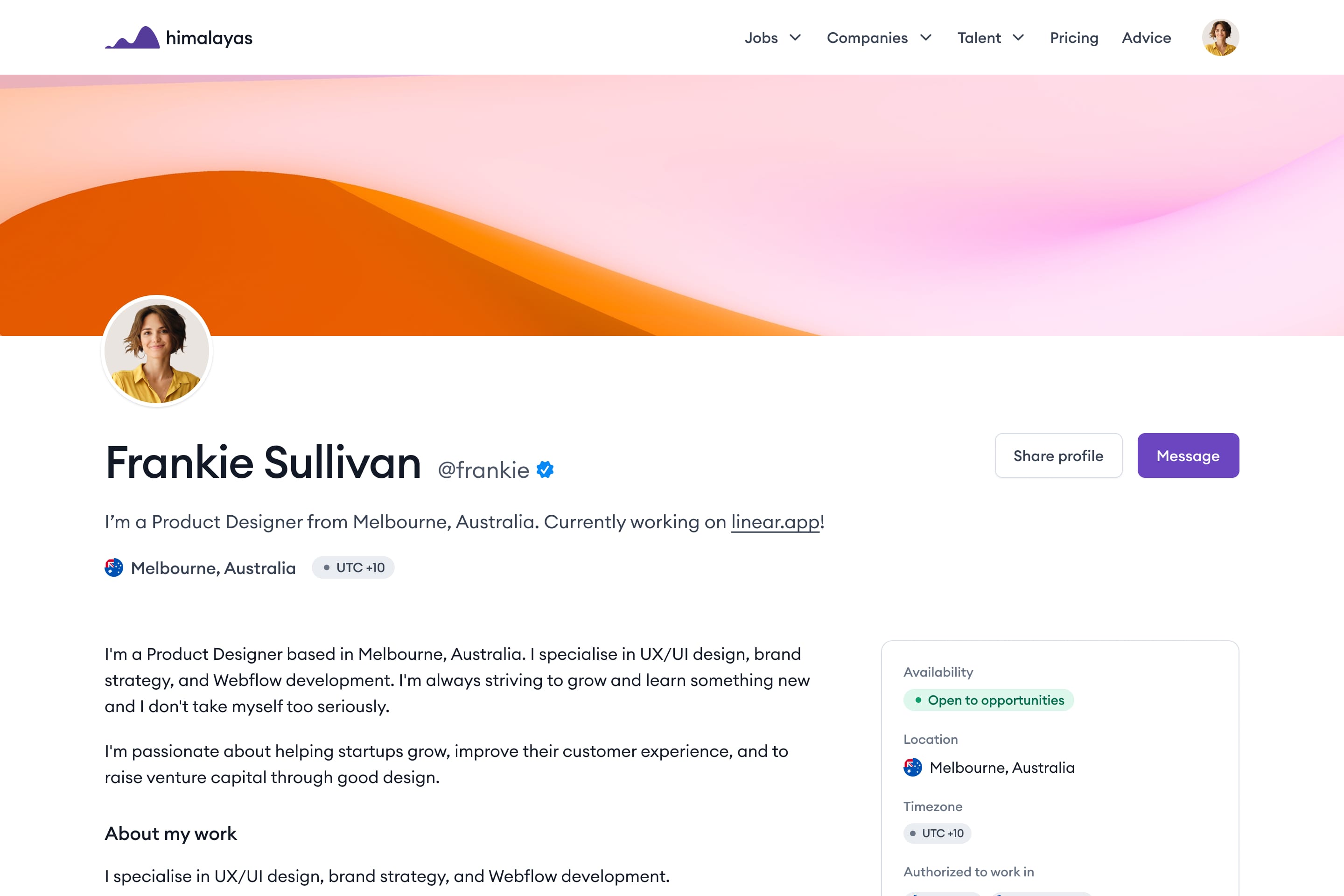