6 Maintenance Specialist Interview Questions and Answers
Maintenance Specialists are responsible for ensuring the proper functioning and upkeep of equipment, machinery, and facilities. They perform routine inspections, troubleshoot issues, and carry out repairs to minimize downtime and maintain operational efficiency. Junior specialists focus on basic tasks and learning the trade, while senior specialists and leads take on more complex responsibilities, oversee projects, and mentor team members. Supervisors and managers handle team coordination, planning, and strategic maintenance initiatives. Need to practice for an interview? Try our AI interview practice for free then unlock unlimited access for just $9/month.
Unlimited interview practice for $9 / month
Improve your confidence with an AI mock interviewer.
No credit card required
1. Junior Maintenance Specialist Interview Questions and Answers
1.1. Can you describe a time when you identified a maintenance issue before it became a major problem?
Introduction
This question assesses your proactive problem-solving abilities and attention to detail, which are crucial for a Junior Maintenance Specialist role.
How to answer
- Use the STAR method to structure your response: Situation, Task, Action, Result.
- Begin by describing the context of the environment where you worked.
- Clearly state the maintenance issue you identified.
- Explain the steps you took to address the issue before it escalated.
- Highlight the positive outcome and any metrics that demonstrate your impact.
What not to say
- Focusing on a situation where you failed to identify an issue.
- Providing vague details that don't clearly demonstrate your role.
- Neglecting to explain the actions you took to solve the problem.
- Downplaying the importance of preventive maintenance.
Example answer
“While working as an intern at a manufacturing facility, I noticed unusual vibrations in one of the machines during routine inspections. Recognizing that this could lead to significant downtime, I immediately reported it to my supervisor. We conducted a thorough inspection and identified a worn-out bearing that needed replacement. By addressing this issue proactively, we avoided a potential breakdown that could have halted production for days. This experience taught me the value of vigilance in maintenance work.”
Skills tested
Question type
1.2. How do you prioritize your maintenance tasks when faced with multiple requests?
Introduction
This question evaluates your organizational skills and ability to manage time effectively, which are essential for maintaining operational efficiency.
How to answer
- Describe your method for assessing the urgency and importance of each task.
- Mention any tools or systems you use to keep track of tasks.
- Explain how you communicate with your team or supervisors regarding priorities.
- Share an example of how you successfully managed competing priorities in the past.
- Discuss how you ensure that critical issues are addressed promptly.
What not to say
- Claiming that you simply tackle tasks as they come without any system.
- Ignoring the importance of communication with team members.
- Failing to provide a specific example of prioritization.
- Suggesting that all tasks are equally important.
Example answer
“In my previous role, I maintained a task list that ranked requests based on urgency and impact on operations. For instance, when I received multiple requests, I would quickly assess which tasks could lead to safety issues or significant downtime. I prioritized a request for a failing safety system over routine checks. By keeping my team informed about priorities, we managed to resolve the critical issue promptly, ensuring safety and operational continuity.”
Skills tested
Question type
2. Maintenance Specialist Interview Questions and Answers
2.1. Can you describe a time when you identified a potential maintenance issue before it became a problem?
Introduction
This question is important as it assesses your proactive approach to maintenance and your ability to foresee potential issues, which is crucial for ensuring operational efficiency.
How to answer
- Use the STAR method to structure your response: Situation, Task, Action, Result.
- Clearly describe the environment and the equipment involved.
- Explain how you identified the issue through observation or data analysis.
- Detail the steps you took to address the issue before it escalated.
- Highlight the positive outcome and impact on operations or safety.
What not to say
- Describing a reactive approach without mentioning proactive measures.
- Failing to specify the tools or methods used for identification.
- Not discussing the impact of the preventive action taken.
- Overlooking team collaboration if applicable.
Example answer
“At a mining site in Queensland, I noticed unusual vibrations in a conveyor belt during routine checks. I used vibration analysis tools to assess the issue and discovered a misalignment. I scheduled immediate maintenance, which prevented a breakdown that could have halted operations for days. This proactive approach saved the company significant downtime costs and ensured safety for all workers.”
Skills tested
Question type
2.2. What maintenance management software are you familiar with, and how have you used it to improve maintenance operations?
Introduction
This question evaluates your technical skills and familiarity with tools essential for effective maintenance management, which is increasingly important in modern facilities.
How to answer
- Name specific software you have experience with, such as CMMS (Computerized Maintenance Management Systems).
- Describe how you utilized the software to track maintenance schedules, inventory, or work orders.
- Share examples of improvements you made or efficiencies gained through the software.
- Discuss how you trained others or promoted the use of the software in your team.
- Highlight any metrics or results achieved as a direct outcome of using the software.
What not to say
- Being vague about the software or not naming specific tools.
- Overlooking the benefits or any measurable results from using the software.
- Saying you haven't used any software but claiming to be tech-savvy.
- Ignoring the collaborative aspects of using software with team members.
Example answer
“I have extensive experience with Maximo and CMMS platforms. At my previous job, I implemented Maximo to manage our maintenance schedules. By automating work orders and tracking asset performance, we reduced downtime by 30% and improved our response time to issues. I also conducted training sessions for my team to ensure everyone was comfortable using the system, which boosted overall productivity.”
Skills tested
Question type
2.3. How do you prioritize maintenance tasks when you have multiple urgent issues to address?
Introduction
This question assesses your prioritization and decision-making skills, which are vital in a maintenance role where urgent issues can arise unexpectedly.
How to answer
- Explain your criteria for prioritizing tasks (e.g., safety, production impact, equipment criticality).
- Describe a systematic approach you follow, such as using a priority matrix.
- Share an example of a time you successfully managed multiple urgent tasks.
- Discuss how you communicate prioritization to your team and stakeholders.
- Highlight how you ensure that urgent tasks do not compromise overall maintenance quality.
What not to say
- Saying you handle tasks as they come without a structured approach.
- Ignoring the importance of communication with team members.
- Failing to consider safety as a top priority.
- Not providing a specific example of past experiences.
Example answer
“When faced with multiple urgent maintenance requests, I first assess each situation based on safety implications and production impact. For instance, during my time at a manufacturing plant, we had a critical machine failure alongside a leaking boiler. I prioritized the boiler repair as it posed a safety risk while delegating the machine issue to a capable technician. This approach minimized downtime and ensured a safe working environment for all staff.”
Skills tested
Question type
3. Senior Maintenance Specialist Interview Questions and Answers
3.1. Can you describe a time when you identified a potential maintenance issue before it became a problem?
Introduction
This question assesses your proactive approach to maintenance and your ability to foresee and mitigate issues, which is critical for a Senior Maintenance Specialist.
How to answer
- Use the STAR method to structure your response: Situation, Task, Action, Result.
- Describe the context of the equipment or system you were monitoring.
- Explain how you identified the issue and the indicators you observed.
- Detail the steps you took to address the potential problem before it escalated.
- Quantify the impact of your actions on safety, cost savings, or equipment longevity.
What not to say
- Focusing solely on reactive maintenance without mentioning proactive measures.
- Neglecting to provide specific details about the issue or your actions.
- Not discussing the outcomes or improvements resulting from your actions.
- Avoiding acknowledgment of team collaboration if applicable.
Example answer
“At a manufacturing facility, I noticed unusual vibrations in a conveyor system during routine checks. I analyzed the data and recognized it was a sign of potential bearing failure. I scheduled an immediate inspection, which confirmed my suspicion. By replacing the bearings proactively, we avoided a costly breakdown that would have halted production for days. This intervention saved the company approximately $10,000 in downtime costs.”
Skills tested
Question type
3.2. How do you prioritize maintenance tasks when faced with multiple urgent issues?
Introduction
This question evaluates your prioritization and decision-making skills, which are essential for managing maintenance tasks effectively.
How to answer
- Discuss the criteria you use for prioritization, such as safety, operational impact, and resource availability.
- Explain how you communicate with team members and stakeholders to assess urgency.
- Describe any tools or methods you use to organize and track maintenance tasks.
- Provide an example of a time you successfully managed competing priorities.
- Highlight the importance of flexibility and adaptability in your approach.
What not to say
- Saying you handle tasks on a first-come, first-served basis without considering impact.
- Failing to mention collaboration or communication with the team.
- Ignoring the importance of safety in prioritization.
- Describing a rigid approach that lacks adaptability.
Example answer
“When faced with multiple urgent maintenance requests, I first assess the safety risks and operational impact of each issue. For instance, if a critical piece of equipment is down, I prioritize that over minor repairs. I also consult with my team to gather insights on task urgency. Recently, we had simultaneous requests for a generator failure and a minor HVAC issue. I addressed the generator first, as its failure would halt operations, while delegating the HVAC task to a technician. This approach allowed us to minimize downtime effectively.”
Skills tested
Question type
4. Lead Maintenance Specialist Interview Questions and Answers
4.1. Can you describe a situation where you identified a recurring maintenance issue and how you addressed it?
Introduction
This question is important to evaluate your problem-solving skills and ability to implement effective maintenance strategies. As a Lead Maintenance Specialist, identifying and resolving ongoing issues is key to ensuring operational efficiency.
How to answer
- Use the STAR method (Situation, Task, Action, Result) to structure your response
- Clearly describe the recurring issue you faced and its impact on the operations
- Explain the analysis you conducted to identify the root cause
- Detail the corrective actions you implemented and how you communicated these to the team
- Share the measurable outcomes of your actions, such as reduced downtime or cost savings
What not to say
- Focusing solely on the technical aspects without discussing the broader impacts
- Avoiding specifics and giving vague answers about 'fixing problems'
- Not mentioning collaboration with team members or stakeholders
- Failing to discuss the follow-up measures taken after the initial solution
Example answer
“At Tata Power, I noticed a recurring issue with the conveyor belt failing every few weeks. I led a team to conduct a thorough analysis and discovered that the lubrication schedule was inadequate. I implemented a new preventive maintenance schedule and trained the team on proper lubrication techniques. As a result, we reduced conveyor downtime by 60% over six months, significantly improving our production efficiency.”
Skills tested
Question type
4.2. How do you prioritize maintenance tasks when faced with multiple urgent requests?
Introduction
This question assesses your prioritization skills and ability to manage time effectively in a fast-paced environment. As a Lead Maintenance Specialist, you will often need to balance multiple tasks and make quick decisions.
How to answer
- Explain your method for assessing and categorizing maintenance requests based on urgency and impact
- Discuss tools or systems you use to manage tasks, such as CMMS (Computerized Maintenance Management System)
- Describe how you communicate priorities to your team and stakeholders
- Provide an example of a past experience where you successfully managed competing priorities
- Mention how you ensure that critical tasks are completed while maintaining team morale
What not to say
- Suggesting you handle tasks randomly or without a system
- Ignoring the importance of team input in prioritization
- Failing to provide an example of effective prioritization
- Claiming to always work late to manage tasks instead of improving processes
Example answer
“In my role at Larsen & Toubro, I used a priority matrix to categorize requests based on urgency and operational impact. When multiple issues arose, I would first address those affecting safety and production. For example, when a critical pump failure occurred simultaneously with routine maintenance requests, I quickly assessed the situation and prioritized the pump repair. I communicated with my team to ensure they understood the shift in focus, which helped us resolve the issue within hours without delaying other tasks significantly.”
Skills tested
Question type
5. Maintenance Supervisor Interview Questions and Answers
5.1. Can you describe a situation where you had to handle a significant equipment failure? What steps did you take to resolve it?
Introduction
This question assesses your problem-solving skills and ability to manage crises, which are crucial for a Maintenance Supervisor role. Equipment failures can lead to downtime and financial loss, so demonstrating effective management in such situations is vital.
How to answer
- Use the STAR method to structure your response: Situation, Task, Action, Result.
- Clearly describe the equipment failure and its impact on operations.
- Detail the steps you took to diagnose the issue and implement a solution.
- Highlight collaboration with team members and any external contractors involved.
- Share the outcome, including any metrics related to downtime reduction or cost savings.
What not to say
- Blaming others for the equipment failure without taking accountability.
- Providing vague responses without specific actions taken.
- Failing to mention teamwork or collaboration.
- Overemphasizing the problem rather than the solution.
Example answer
“At a manufacturing facility, we faced a major breakdown of our conveyor system that halted production. I quickly assessed the situation, gathered my maintenance team, and we conducted a root cause analysis. Within two hours, we identified a faulty motor and sourced a replacement from a local supplier. We managed to get the system running again within six hours, reducing potential downtime from two days to just half a day. This experience reinforced the importance of quick thinking and teamwork in crisis situations.”
Skills tested
Question type
5.2. How do you ensure compliance with safety regulations in your maintenance operations?
Introduction
This question evaluates your knowledge and commitment to workplace safety, a critical aspect of the Maintenance Supervisor role. Compliance with safety regulations is paramount to protect employees and equipment.
How to answer
- Discuss your understanding of relevant safety regulations and standards.
- Explain your approach to training team members on safety protocols.
- Describe how you conduct regular safety audits and inspections.
- Share examples of how you've improved safety practices in past roles.
- Mention any certifications or training you have related to safety compliance.
What not to say
- Suggesting that safety is not a priority in maintenance operations.
- Providing generic answers without specific safety practices.
- Failing to mention the importance of ongoing training and education.
- Overlooking the role of documentation and reporting in safety compliance.
Example answer
“I prioritize safety by ensuring that all team members are trained in the latest safety regulations, including those set by Safe Work Australia. I conduct monthly safety audits to identify potential hazards and address them proactively. In my previous role, I implemented a new training program that reduced workplace incidents by 30% within a year. Additionally, I maintain meticulous records of safety checks and compliance to ensure transparency and accountability.”
Skills tested
Question type
6. Maintenance Manager Interview Questions and Answers
6.1. Can you describe a time when you implemented a new maintenance strategy that improved operational efficiency?
Introduction
This question evaluates your ability to innovate and improve processes, which is crucial for a Maintenance Manager responsible for optimizing equipment performance and reducing downtime.
How to answer
- Use the STAR method to structure your response, focusing on the Situation, Task, Action, and Result.
- Clearly outline the previous maintenance strategy and its limitations.
- Describe the new strategy you implemented and why you chose it.
- Discuss the steps you took to implement the strategy and how you engaged your team.
- Quantify the results in terms of efficiency improvements, cost savings, or reduced downtime.
What not to say
- Focusing only on the technical aspects without mentioning the impact on the team or operations.
- Providing vague results without specific metrics.
- Not acknowledging the challenges faced during implementation.
- Taking sole credit for the success without recognizing team efforts.
Example answer
“At XYZ Manufacturing, I noticed our equipment downtime was significantly high due to reactive maintenance. I implemented a predictive maintenance strategy using data analytics to foresee equipment failures. By training my team on new software and processes, we reduced unplanned downtime by 30% and saved the company around $150,000 in repair costs over the first year.”
Skills tested
Question type
6.2. How do you prioritize maintenance tasks when faced with multiple urgent requests?
Introduction
This question assesses your decision-making and prioritization skills, which are essential for managing resources effectively and ensuring critical operations continue smoothly.
How to answer
- Describe your prioritization criteria, such as safety, operational impact, and resource availability.
- Explain how you communicate with your team and stakeholders to assess urgency.
- Detail how you balance long-term projects with immediate needs.
- Provide an example of a specific situation where you effectively managed competing priorities.
- Discuss any tools or methods you use to track and manage tasks.
What not to say
- Suggesting you handle all requests on a first-come, first-served basis without proper assessment.
- Failing to mention collaboration with your team or stakeholders.
- Ignoring the importance of safety and operational continuity in decision-making.
- Neglecting to discuss how you handle conflicts or pushback from team members.
Example answer
“In my previous role at ABC Corp, we often faced multiple urgent requests due to equipment failures. I prioritize tasks based on a risk assessment model that considers safety, impact on production, and resource availability. For instance, when our main conveyor system broke down, I coordinated with my team to temporarily redirect resources while also planning a fix for a less critical issue. This approach ensured we minimized production loss while addressing urgent needs effectively.”
Skills tested
Question type
Similar Interview Questions and Sample Answers
Simple pricing, powerful features
Upgrade to Himalayas Plus and turbocharge your job search.
Himalayas
Himalayas Plus
Himalayas Max
Find your dream job
Sign up now and join over 100,000 remote workers who receive personalized job alerts, curated job matches, and more for free!
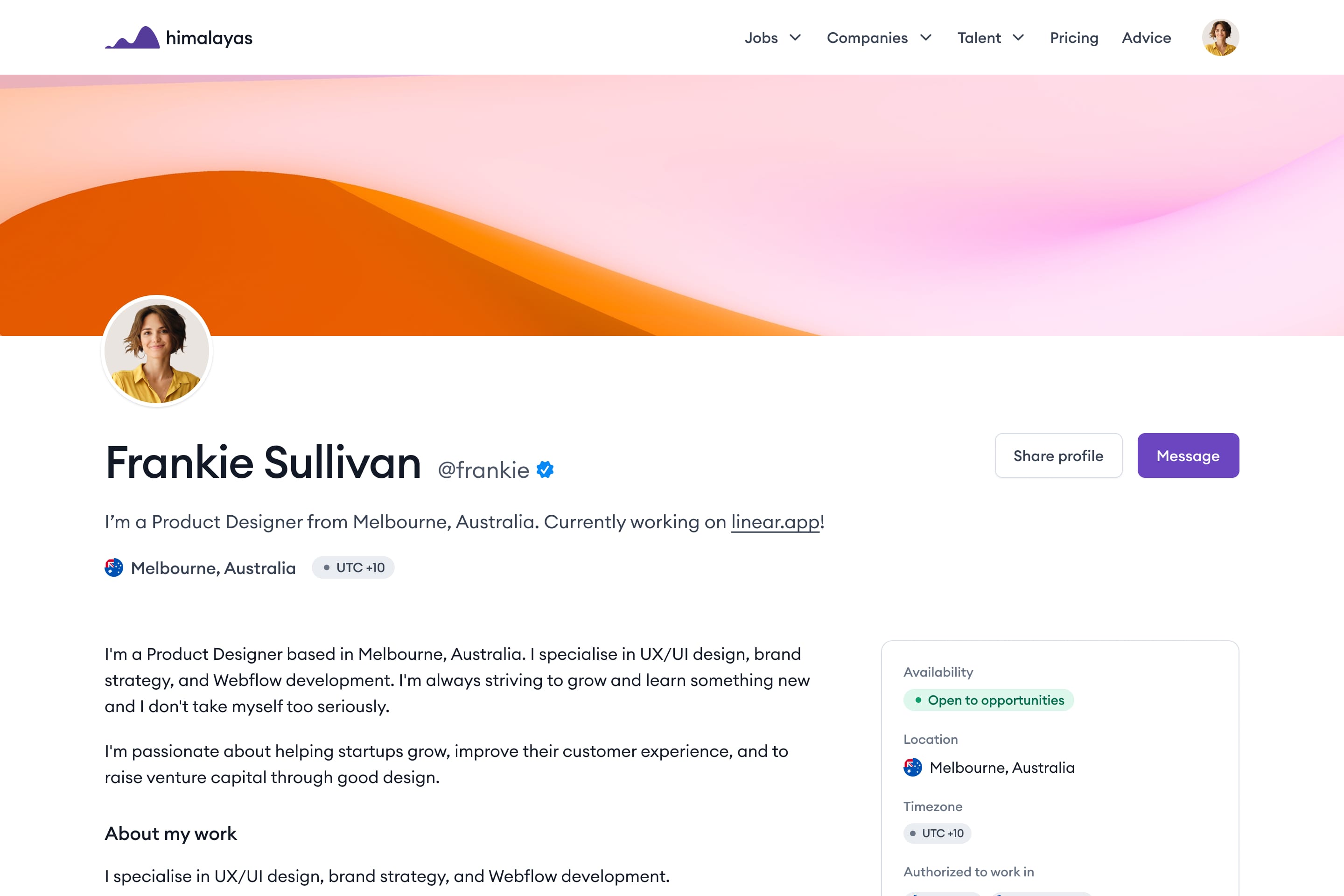